整车尺寸缺陷分析方法
缺陷是指在零件、分总成或整车上本身存在的或客户可见的不满足车辆功能的现象。对所有已确认的缺陷都需进行分析,根据其出现的频率及对客户的影响来划分缺陷的优先性 。 不符合性主要针对与合同协议不符的状况,合同协议有以下内容定义:
- 数模和图纸
- 公差表:零件、分总成、条件图(美学或功能)
- 装配工艺标准
- 设备工装标准和工序能力
- 工序特性,产品功能特性清单和目标
一、缺陷和不符合项分析解决方法
缺陷和不符合项分析解决方法”是一种严密的思维方式,它能有效地解决各种类型的问题。每个部门在需要时都可以应用它,并同时运用更合适的工具和专业知识。
尺寸工程运用这一方法并根据我们的专业来解决整车的缺陷和不符合项。
解决问题需要一个精确的事实分析和原因追寻过程,这样才能找到有效的解决方法。
工作目标:
- 精确描述待解决的问题
- 确定造成问题的缘由
- 提出并应用解决方法,它既能消除起因也能解决问题
成功条件:
- 不要急于寻求解决方法,原因必须要辨认确定以便完全被解决掉
- 采取漏斗式的方法(由多到少,去粗取精)
- 全面而彻底的寻找(数量上)
- 分类以便一目了然(类别)
- 鉴别并保留最恰当最贴切的,能够经常被质疑
缺陷和不符合项分析解决方法的步骤:
1.1 描述缺陷或不符合项
把所有必需信息汇总得出可能性最大的结果以便很好的提出问题,分析问题,解决问题。
为了全面细致描述缺陷,反映客观事实(缺陷),我们将使用下面的描述方法:
1.2 列出并鉴别可能的影响因素
有可能的因素列成一张表并分类,然后挑选出很可能的原因,鉴别它们是否是缺陷产生的源头。
1.3 确定缺陷产生原因
a.原因的找寻和归类
分析员要在现场确定的可能的原因,而不应该重新开始整个进程
b.挑选原因
- 从分析报告中有影响的矢量(测量数据)开始,选出尺寸链环中影响和风险最大的链环
- 分析可能的工装工序能力原因
- 分析人员操作和环境的影响
c.鉴别原因
- 确认监控报告的符合性
- 调研相关联的尺寸
- 开展试验验证可能的原因
“漏斗法”筛选缺陷原因
1.4 制定解决方案
制定恢复符合性的行动计划
- 所有影响的不符合项因素被确定后,制定能解决缺陷的方案。
- 分析质量、成本、周期、风险,选出最有效最合适的解决方法,若需要,要进行确认。
例如:调整夹具、操作工艺、监控计划上是最有效的。
- 产品定义、制造工艺和工序、工装设备的更改,与相关部门一起评审整改方案
- 综合对比评估方案风险
- 确认方案实施优先性
- 制定方案的验证试验(如果需要)
- 制定整改方案详细计划
- 制定临时方案
1.5 缺陷和不符合项关闭
- 确认缺陷消除,符合性达标
- 更新零件/总成和工序监控计划以及所有相关工艺文件
- 跟踪积累数据保证缺陷被纳入监控计划
- 总结形成经验反馈
二、实车尺寸缺陷分析案例
2.1 实车缺陷的分析流程
(1)确认缺陷: 必须看到实车缺陷或跟质检人员确认缺陷现象,确认责任归属
- 了解清楚缺陷表现,相关零件和偏差方向/数量/频次
- 初步判定缺陷为批量缺陷或是偶发缺陷
- 初步判断是零件问题或是车身问题或是装配问题
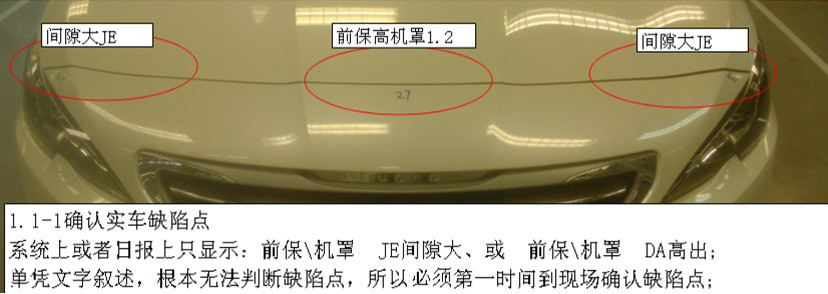
通过以下方法可以依据经验快速分析出部分可能原因:
1 .装配螺钉或螺目有无偏孔或者错孔
2. 零件之间距离有无异常变化
3. 零件之间有无干涉
4. 零件孔和表面有无异常变形
…
(2)列入清单: 将新缺陷增加到总装缺陷唯一性清单里,建立可追溯性跟踪内容
(3)确定尺寸偏差比: 利用缺陷和不符合项的分析解决方法,确认零件尺寸偏差比率
“观察法”识别异常缺陷原因
观察法: 实车缺陷中,有部分是由于来件尺寸突变或者工艺装配异常造成,这类缺陷往往会在实车上表现明显的异常,可以通过观察快速锁定原因。
缺陷原因: 零件干涉
缺陷原因: 涂胶过厚导致角窗与侧围不贴合
“模拟法”确认部分装配环节影响
模拟法: 分析缺陷时,可采取手工或者工装模拟现场操作人员的正常操作和可能的失误操作,来分析尺寸偏差是否有可能由操作带来。
“互换法”确认零件和车身的尺寸偏差
互换法: 将正常车辆和缺陷车辆在CUBing上检测以后再进行互换装车,可以判定出那个零件还是车身是缺陷的主要来源。
“排除法”快速解决简单尺寸链缺陷
排除法: 在分析尺寸链构成比较简单(零件-车身-装配)的尺寸缺陷时,直接将零件在车身的装配结果与CUBing装车结果对比可通过排除快速鉴别车身偏差和零件偏差。
缺陷车零件CUBing测量
(4)制定临时措施:制定临时措施保证生产(尽快完成)
通常通过以下临时措施保证:
1 .临时调整工装
2. 返修零件或采取加垫片/海绵等措施
3. 临时总装返修
..
(5)过程控制数据分析: a.确认相关零件和总成的尺寸偏差和稳定性是否出现异常
b.确认对应的车身总成/开启件UCF/调整线末检测数据是否合格和存在异常
总装件检测报告
冲压件检测报告
UCF检测报告
调整线下检测报告
尺寸验证试验
(6)手工调整验证:手工试验或临时调整将异常点调整到中值状态,观察缺陷是否改善?
(7)批量确认和制定最终方案 :批量验证试验结果是否稳定有效数据收集,如果缺陷稳定消失则最终改善方案
通过批量验证后,确认措施有效的情况下,制定最终的改善方案并跟踪实施,确保效果良好
缺陷数据 验证数量
共7台 共7台
要求间隙<=1.5 要求间隙<=1.5
实测平均1.8 实测平均1.8
结论:方案稳定有效,可以正式实施
三、经验反馈
对于缺陷分析完成后确认的设计问题,应以经验反馈的形式提交分析结果和改进建议,以便设计改进方案。
改善建议: 前保打紧点设计距离前部边缘建议<=80mm
整车尺寸缺陷分析方法的相关知识就先介绍到这里,如果各位有什么问题可以后台留言沟通,希望能给各位带来提高!