高速电机设计重点与发展综述
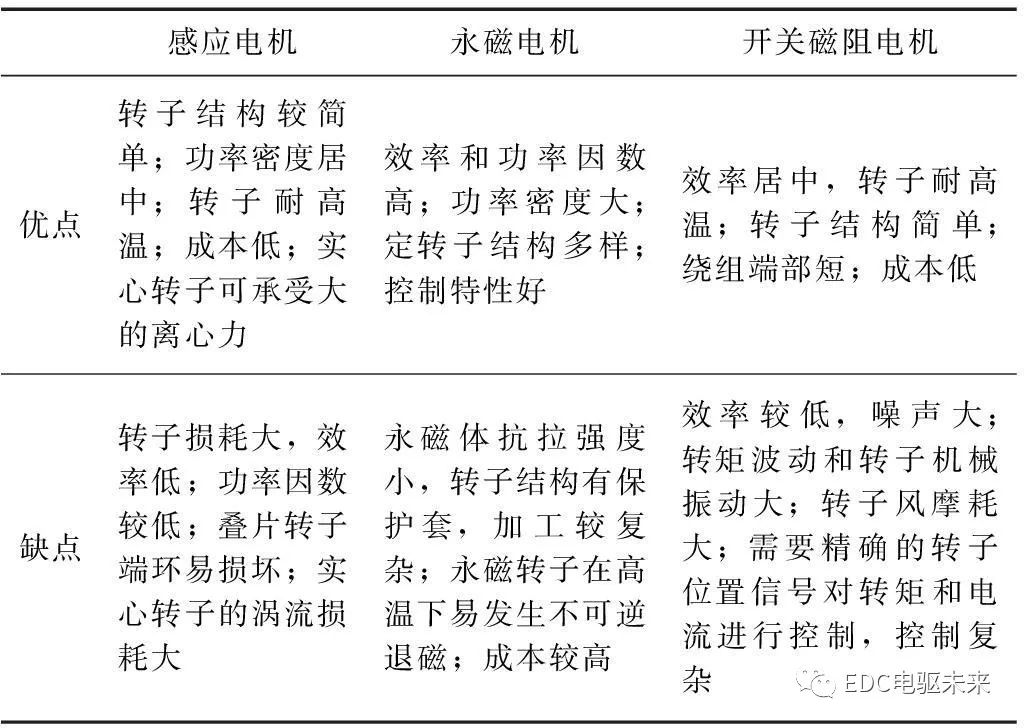
高速电机的主要特点是转子速度高、定子绕组电流和铁心中磁通频率高、功率密度和损耗密度大。这些特点决定了高速电机具有不同于常速电机特有的关键技术与设计方法。
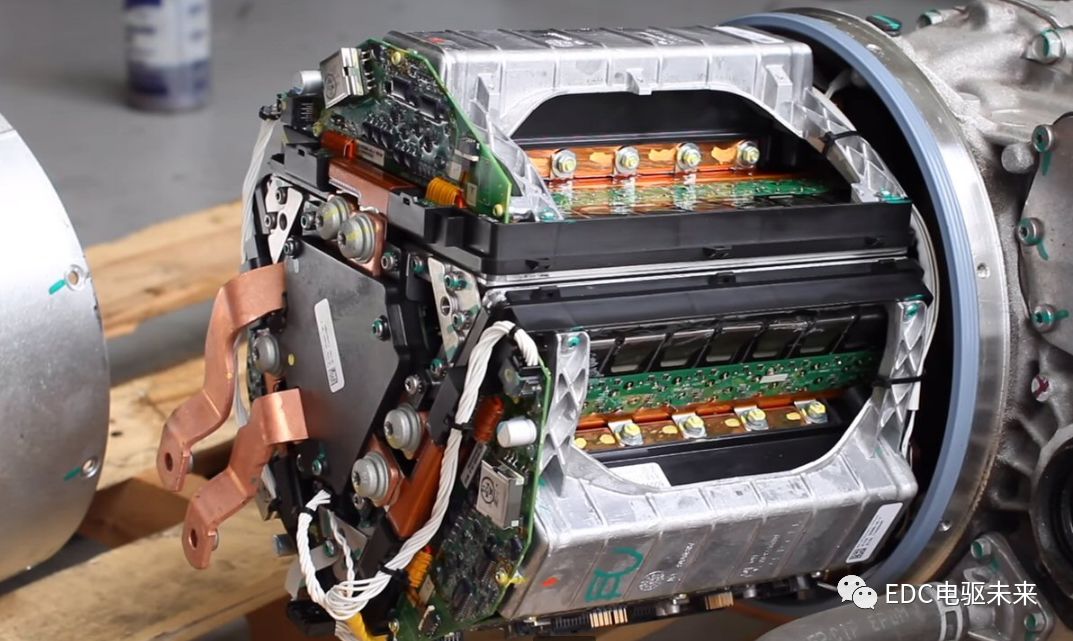
高速电机的转子速度通常高于10 000 r/min,在高速旋转时,常规叠片转子难以承受巨大的离心力,需要采用特殊的高强度叠片或实心转子结构;对于永磁电机来说,转子强度问题更为突出,因为烧结而成的永磁材料不能承受转子高速旋转产生的拉应力,必须对永磁体采取保护措施;转子与气隙高速摩擦,在转子表面造成的摩擦损耗远大于常速电机,给转子散热带来很大困难;为了保证转子有足够的强度,高速电机转子多为细长型,因此与常速电机相比,高速电机转子系统接近临界转速的可能性大大增加,为了避免发生弯曲共振,必须准确预测转子系统的临界转速;普通电机轴承无法在高速下可靠运行,必须采用高速轴承系统。
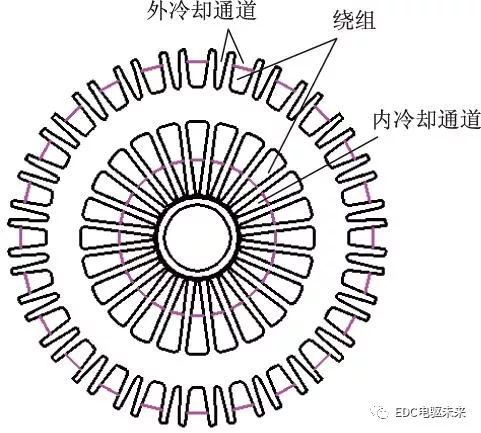
高速电机绕组电流和铁心中磁通交变频率很高,会在电机绕组、定子铁心以及转子中产生较大的高频附加损耗。定子电流频率较低时,通常可以忽略趋肤效应和邻近效应对绕组损耗的影响,但在高频情况下,定子绕组会产生明显的趋肤效应和邻近效应,增大绕组附加损耗;高速电机定子铁心中磁通频率高,趋肤效应的影响不能忽略,常规的计算方法会带来较大误差,为了准确计算高速电机的定子铁心损耗,需要探索高频工况下的铁耗计算模型;定子开槽与绕组非正弦分布引起的空间谐波以及PWM供电产生的电流时间谐波均会在转子中产生较大的涡流损耗,由于转子体积小、散热条件差,会给转子散热带来极大困难,因此转子涡流损耗的准确计算以及探索有效降低转子涡流损耗的措施,对高速电机可靠运行具有重要意义;同时,高频电压或电流也给大功率高速电机的控制器设计带来了挑战。
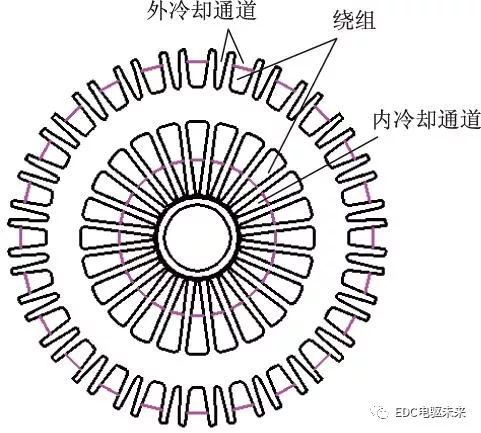
高速电机的体积远小于同等功率的常速电机,不仅功率密度和损耗密度大,而且散热困难,如果不采用特殊散热措施,会使电机温升过高,从而缩短绕组寿命,特别对于永磁电机,在转子温升过高的情况下,永磁体易发生不可逆退磁。设计良好的冷却系统,能有效降低定转子温升,是大功率高速电机长期稳定运行的关键。
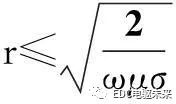
综上所述,高速电机在转子强度、转子系统动力学、电磁设计、冷却系统设计与温升计算、高速轴承以及控制器的研制等方面存在许多常规电机所不具有的特殊关键问题,因此高速电机的设计是一个集电磁场-转子强度-转子动力学-流体场与温度场等多物理场多次迭代的综合设计过程。目前应用于高速领域的电机类型主要有感应电机、永磁电机、开关磁阻电机以及爪极电机,每种电机类型又有不同的拓扑结构。
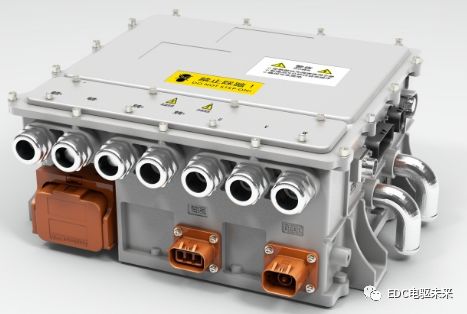
本文对国内外不同类型高速电机的发展现状进行了分析,总结了现有不同类型高速电机的极限指标;详细分析了高速电机结构与设计特点,包括定子设计、不同类型转子结构设计、转子系统动力学分析与轴承选取以及冷却系统的设计等,最后分析了高速电机发展所面临的主要问题,展望了高速电机的发展趋势与前景。
1 高速电机的发展现状
高速电机通常指转速超过10 000 r/min或难度值(转速和功率平方根的乘积)超过1×105的电机,现有的各类电机中,成功实现高速化的主要有感应电机、内转子永磁电机、开关磁阻电机以及少数外转子永磁电机和爪极电机等。为了分析各类型高速电机的特点,在文献[17]的基础上,本文对国内外各类型高速电机的发展现状进行了进一步的总结和扩展,并按照难度值进行了排列。
1.1 高速感应电机
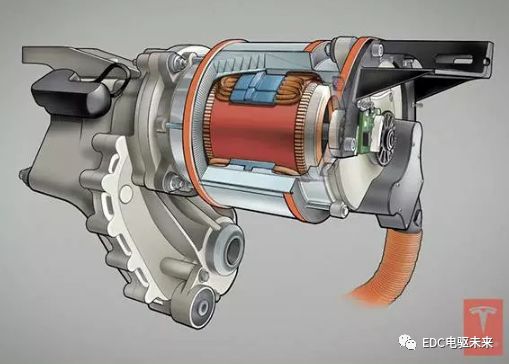
感应电机转子结构简单、转动惯量低,并能在高温和高速的条件下长时间运行,因此感应电机在高速领域应用比较广泛。表1给出了国内外高速感应电机的发展现状。国内外最大功率的高速感应电机为15 MW,转速为20 000 r/min,为ABB公司2002年研制,采用实心转子结构;高速感应电机最大速度为180 000 r/min,功率为10 kW,采用磁悬浮轴承,实心转子结构,线速度为219 m/s,电机的效率约为85%。国内对高速感应电机的研究相对滞后,其中重庆德马电机研制了一系列高速感应电机,海军工程大学、沈阳工业大学、哈尔滨工业大学以及浙江大学等针对高速感应电机开展了许多研究工作,海军工程大学对2.5 MW高速感应电机开展了研究,重庆德马电机研制了100 kW、25 000 r/min高速感应电机,国内高速感应电机的发展水平远低于国外。
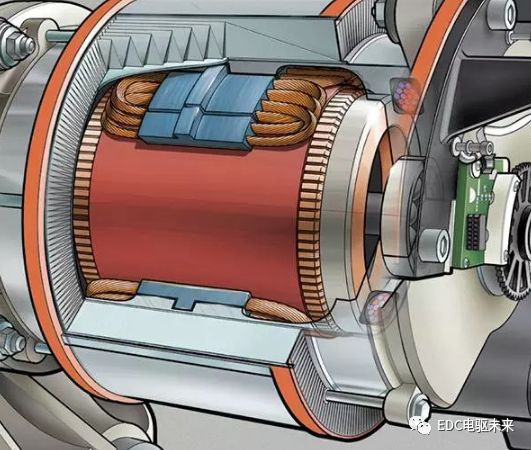
从表1可看出,采用实心转子结构的高速感应电机最大难度值高达24.49×105,转子表面线速度可达367 m/s,而采用常规叠片转子结构的高速感应电机最大难度值仅为3×105,转子表面线速度最高为185 m/s;在难度值大于3×105或转子表面线速度大于185 m/s的高速感应电机多采用实心转子结构或高强度叠片转子结构。文献[24]介绍的一台2 000 kW、15 000 r/min、转子表面线速度为290 m/s的高速感应电机转子采用了AISI4130合金钢铸成的高强度叠片结构,文献[36]介绍的一台5 kW、92 500 r/min、转子表面线速度为240 m/s的高速感应电机转子也采用了高强度合金铸成的叠片转子结构。
1.2 内转子高速永磁电机
永磁电机具有效率和功率因数高及转速范围大等优点,因此其在高速应用领域倍受青睐。相对于外永磁转子电机,内转子永磁电机具有转子半径小及可靠性强的优点,成为高速电机的首选。
内转子高速永磁电机的发展现状如表2所示。可以看出,内转子高速永磁电机的最大功率已达8 MW,转速15 000 r/min,为面贴式永磁转子,采用碳纤维保护套捆扎;最高转速的永磁电机为500 000 r/min,功率为1 kW,转子表面线速度为261 m/s,采用合金保护套。国内对高速永磁电机的研究主要集中在浙江大学、沈阳工业大学、哈尔滨理工大学、哈尔滨工业大学、西安交通大学、南京航空航天电机、东南大学、北京航空航天大学、江苏大学、北京交通大学、广东工业大学、南车株洲电机有限公司等,他们对高速永磁电机有面贴式(SPM)和内置式(IPM)两种转子结构。从表2可看出,除少数采用内置式转子结构外,其余多采用面贴式永磁转子结构。文献[89]对一台11 kW、50 000 r/min的高速永磁电机设计了内置式转子结构,该电机转子表面线速度为233 m/s,转子采用高强度叠片材料。采用常规叠片材料的高速内置式永磁电机,最大难度值为1.13×105,最大转子表面线速度为135 m/s。
表1 高速感应电机的发展
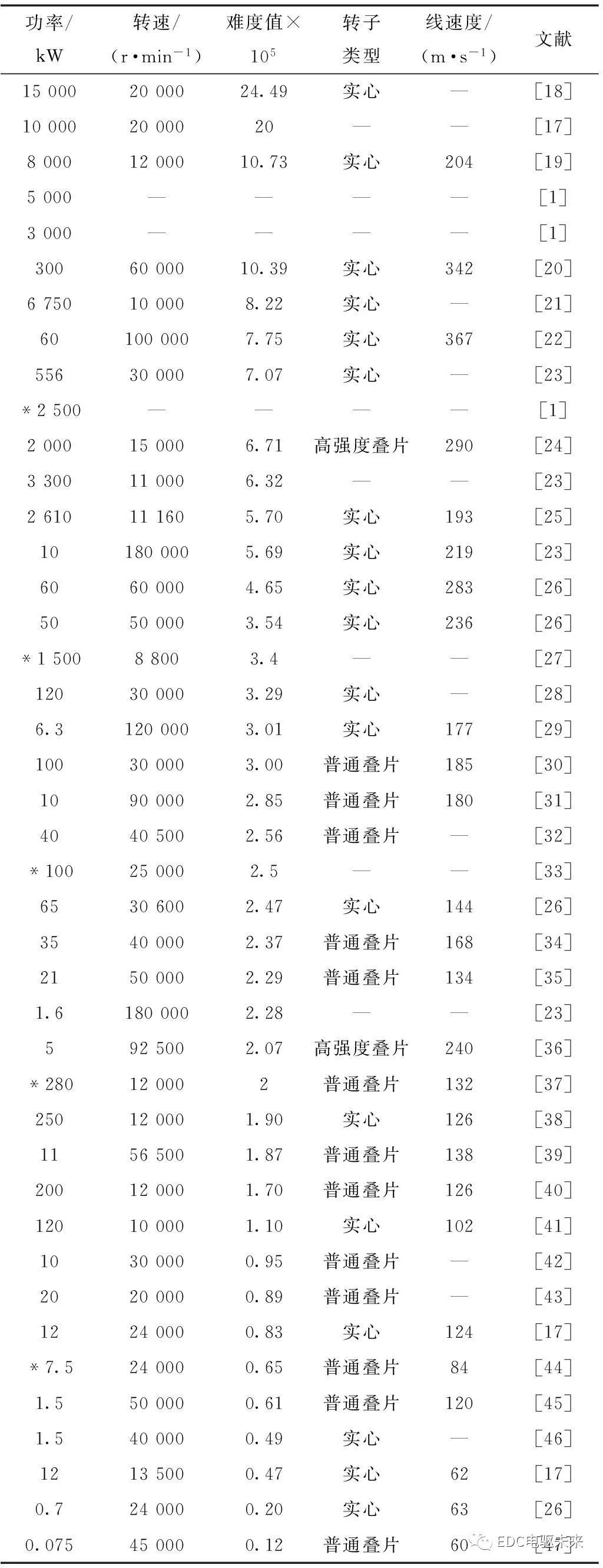
表2 内转子高速永磁电机的发展
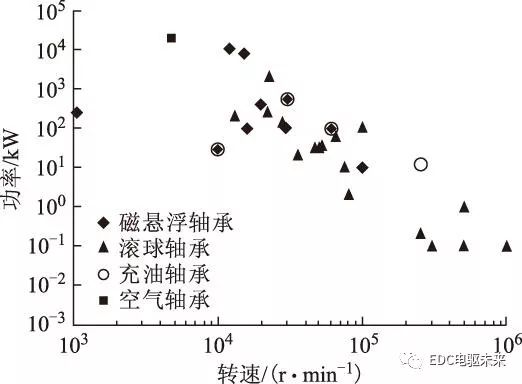
续表2
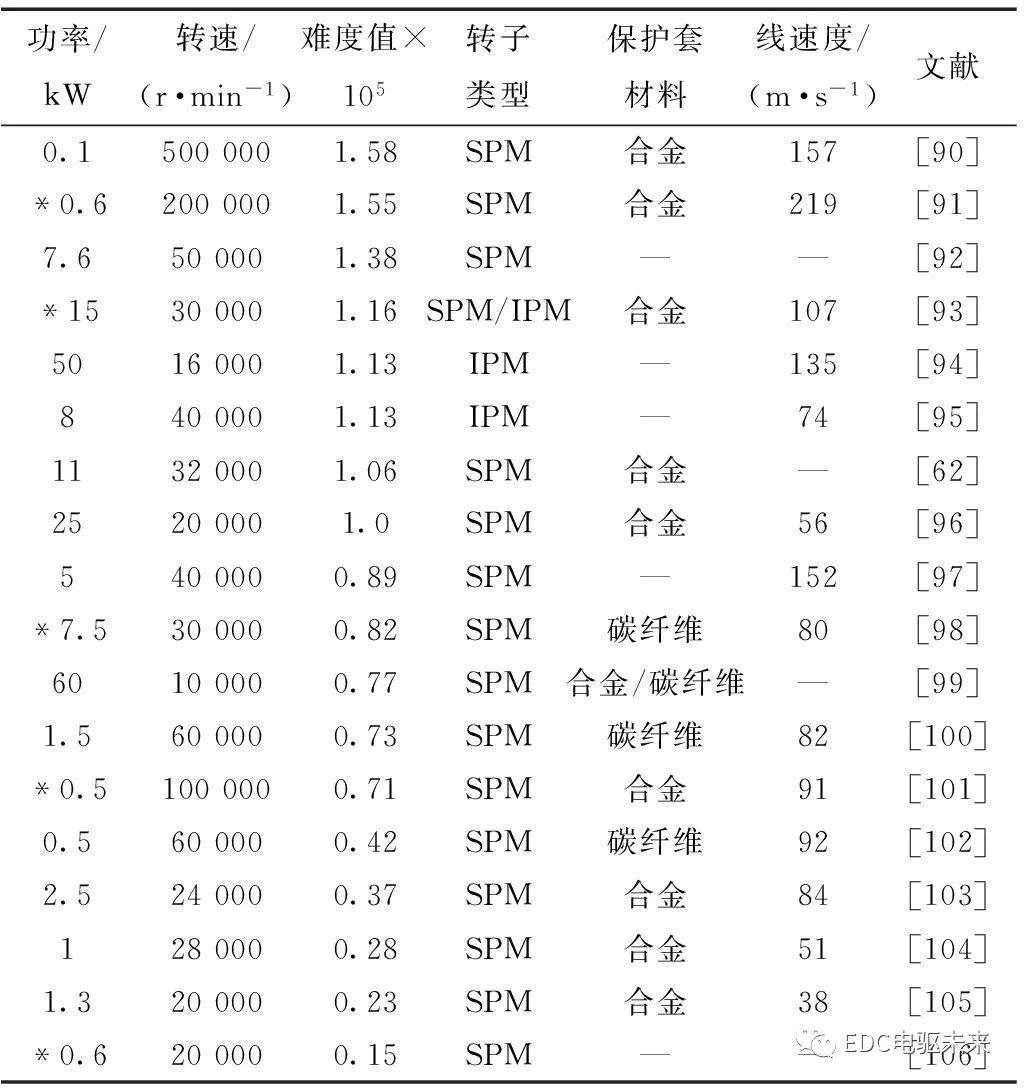
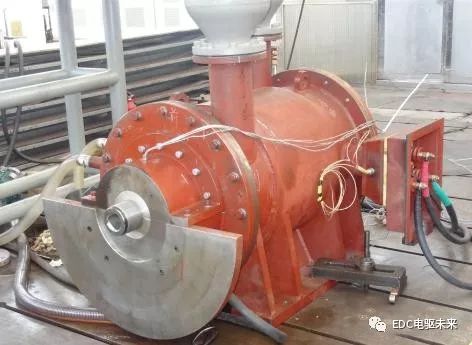
表贴式永磁转子主要有两种保护措施,一种是采用碳纤维捆扎,一种是采用合金护套。从表2可看出,采用合金护套时,高速电机的最大难度值为6.49×105,最大功率为135 kW,最大转子表面线速度为294 m/s。而采用碳纤维捆扎的高速电机最大功率高达8 000 kW,最大表面线速度为314 m/s。
1.3 高速开关磁阻电机
开关磁阻电机以结构简单、坚固耐用、成本低廉以及耐高温等优点而备受瞩目,在高速领域的应用日益广泛,国内外高速开关磁阻电机的发展现状如表3所示。高速开关磁阻电机目前可达的最大难度值为3.51×105,最大功率为250 kW(转速22 000 r/min),最高转速为200 000 r/min(功率1 kW)。南京航空航天大学、北京交通大学、湖南工业大学、华中科技大学等对高速开关磁阻电机开展了相关研究工作,其中南京航空航天大学研制了1 kW、130 000 r/min的开关磁阻电机。
表3 高速开关磁阻电机的发展
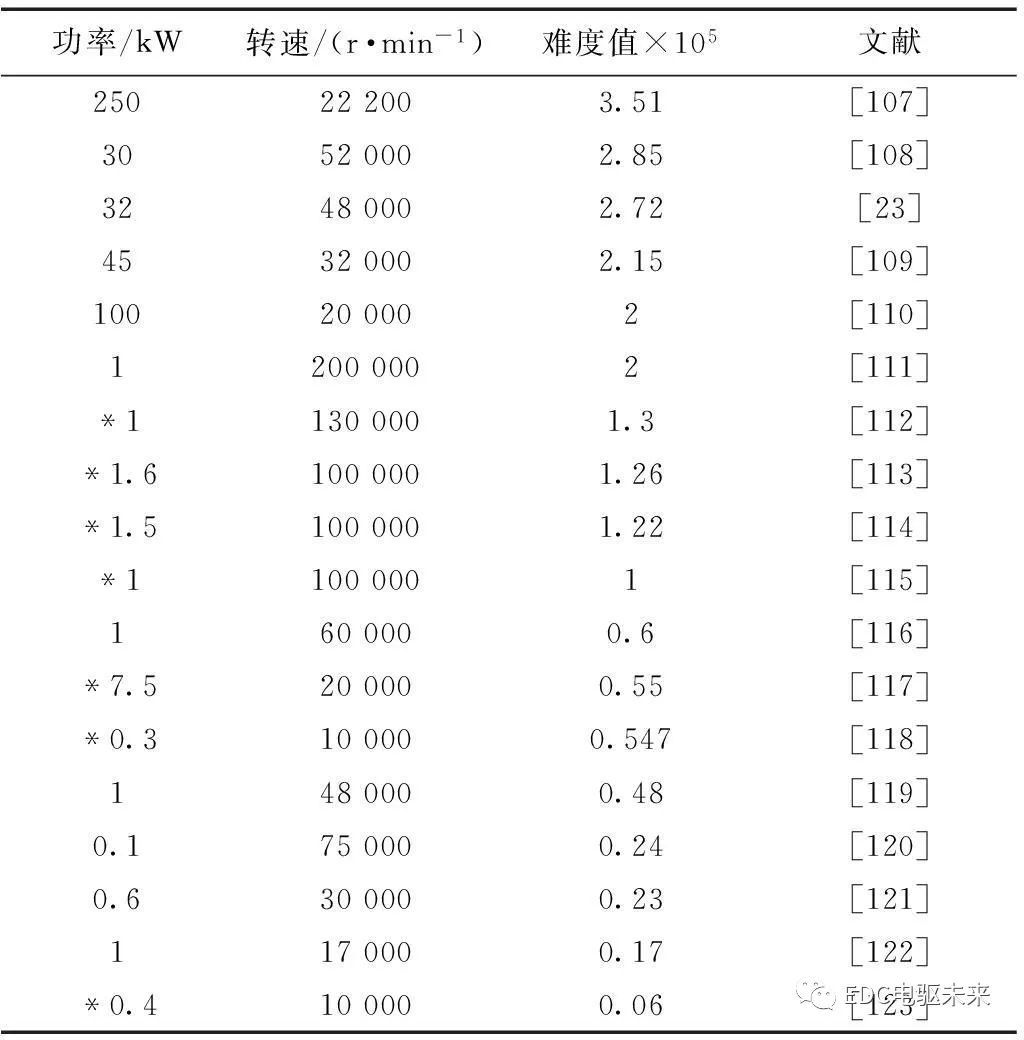
1.4 其他类型高速电机
高速电机除上述3种类型的电机外,还有少数外转子永磁电机与爪极电机。本文对国内外其他类型的高速电机进行的不完全统计如表4所示。外转子高速永磁电机最高难度值为3.17×105(28 kW、60 000 r/min),最大功率为100 kW,最高转速为60 000 r/min。哈尔滨工业大学、山东大学、浙江大学针对外转子高速永磁电机开展了相关的研究工作,沈阳工业大学对双定子单转子轴向磁通电机和外转子爪极高速电机进行了一定研究。
表4 其他类型高速电机的发展
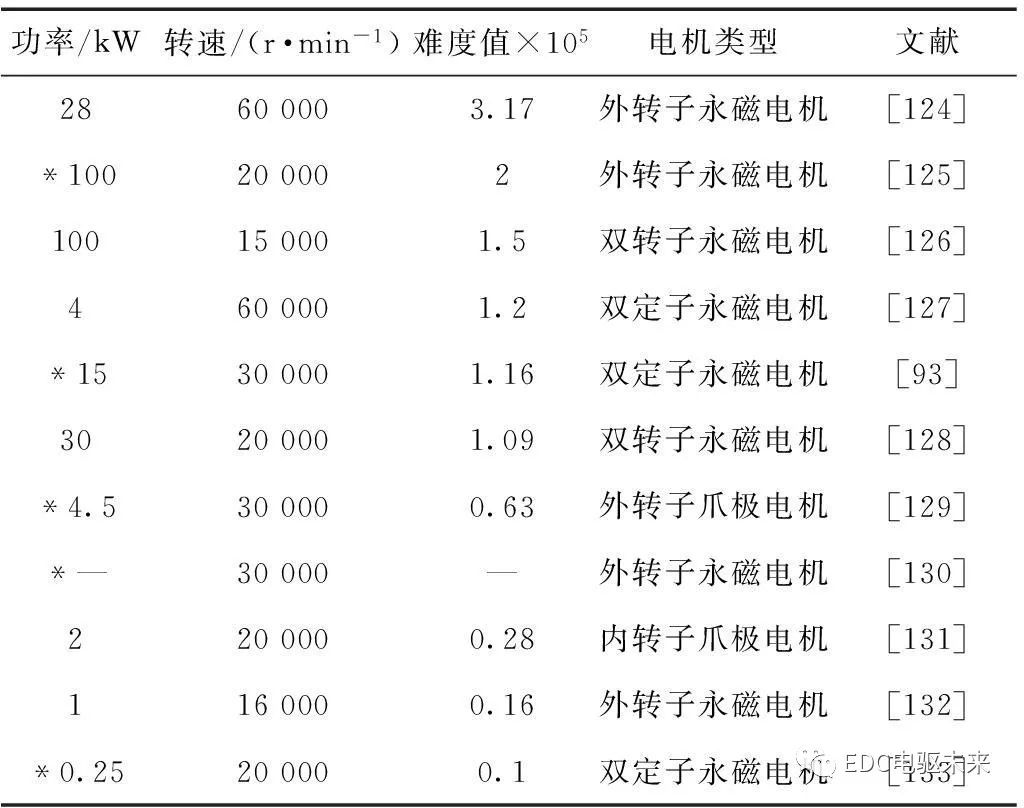
1.5 不同类型高速电机的比较分析
基于国内外高速电机的发展现状和相关文献,本文在文献[17]的基础上,对现有不同类型和结构高速电机的极限指标进行了统计,如表5所示。实心转子感应电机可达到的难度值和转子表面线速度最大,采用碳纤维保护措施的内转子永磁电机次之。这两种结构高速电机的难度值均超过了10×105、转子表面线速度超过了300 m/s。兆瓦级以上的高速电机类型多为实心转子感应电机和碳纤维保护措施的内转子永磁电机,也有少数高强度叠片感应电机。高强度叠片感应电机的最大难度值和转子表面线速度与采用合金护套的内转子永磁电机接近,分别为6.5×105和290 m/s,但采用合金护套的内转子高速永磁电机目前达到的最大功率仅为135 kW,因为合金护套中会产生大量的涡流损耗,不宜用于较大功率的高速永磁电机。高速开关磁阻电机、常规叠片高速感应电机、外转子高速永磁电机的最大难度值相近,约为3×105~3.5×105,目前阶段的最大功率均在300 kW以下,最大转子表面线速度在185~210 m/s之间。内置式高速永磁电机的最大难度值低于1.2×105,高强度叠片内置式永磁电机的最大表面线速度可达233 m/s,但采用常规叠片时仅为135 m/s。爪极电机所能承受的难度值最低,小于1×105。
表5 现有不同类型高速电机的极限指标
表6 不同类型高速电机的对比
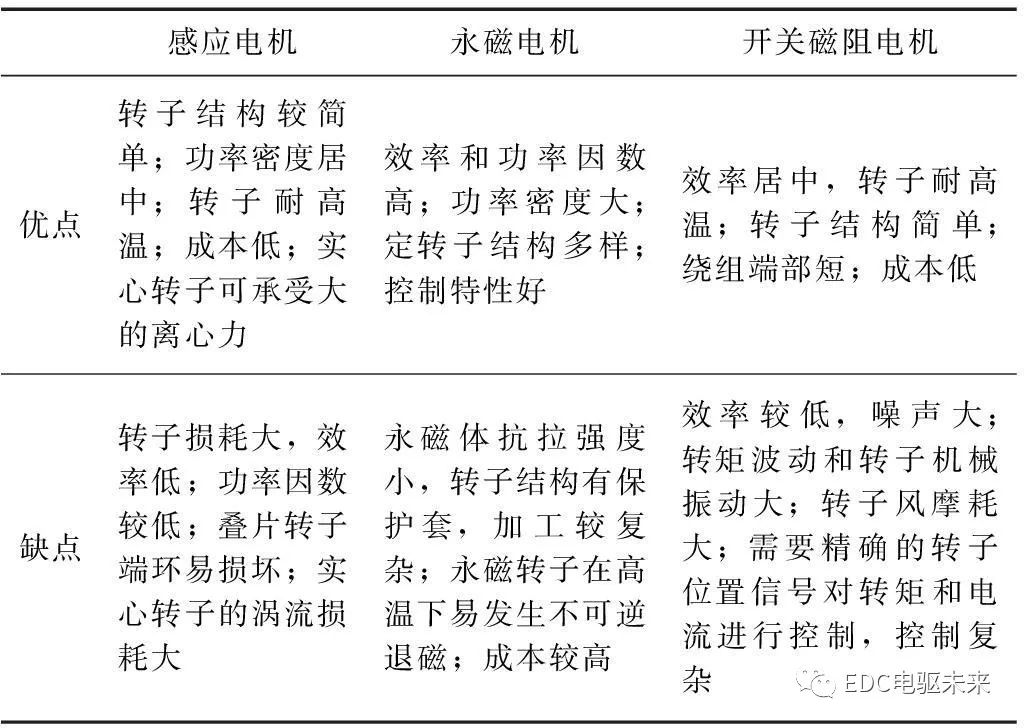
2 定子结构的设计
2.1 极数
高速电机一般设计为2极或4极。对于2极电机,永磁体可采用整体结构,定子电流和铁心中磁场的交变频率较低,有利于降低高频附加损耗,但2极电机的定子绕组端部较长、铁心轭部较厚。4极电机与2极电机相反,定子绕组端部较短,铁心轭部较薄,但定子绕组电流和铁心中磁场的交变频率较高。
2.2 槽数
2.3 铁心材料
高速电机频率高,高频下的定子铁心将产生较大的铁耗,通过合理选取定子铁心材料,可有效降低定子损耗,提高电机的电磁性能。图2为不同定子材料单位重量铁耗随频率的变化曲线。其中,B20AT1500、B27AH1500、B35AH300分别为0.2 mm、0.27 mm和0.35 mm的硅钢片材料,Vacoflux50为0.2 mm的钴钢片,Somaloy700为软磁复合(SMC)材料,Metglas2605SA1为非晶合金材料。从图2可看出,非晶合金材料的单位铁耗远小于其他材料,但该种材料的饱和磁感应强度较低(为1.2~1.3 T),适用于铁心磁通密度较低的高速电机。当电机的工作频率低于1 000 Hz时,SMC材料单位铁耗值高于普通硅钢片,当工作频率高于2 000 Hz时,SMC材料才能有效减小高速电机的铁心损耗。单位钴钢片的损耗值小于硅钢片,但钴钢片的抗拉强度较小,约为硅钢片的一半。
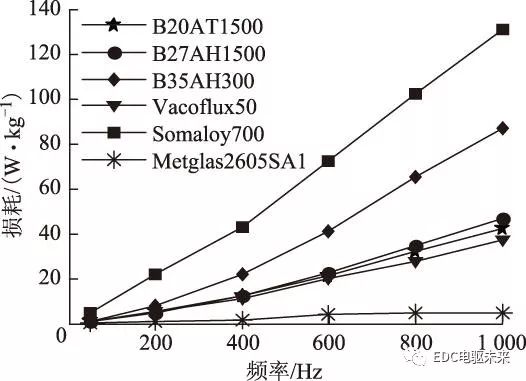
2.4 定子绕组
传统定子绕组端部较长,增加了转子的轴向长度,从而降低了转子系统的刚度。环型绕组结构可有效缩短定子绕组端部长度,其不利之处是线圈嵌线工艺较复杂。
高速电机频率较高,会在定子绕组的导体中产生较大的趋肤效应和邻近效应,从而造成附加损耗,为了降低定子绕组中的损耗,定子绕组须采用许多根较小直径的细导线并联绕制,绕组的导体半径r一般要小于磁场在导体中的透入深度,即为
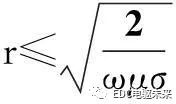
式中,μ为导体的磁导率;σ为导体的电导率;ω为交变磁场角频率。
文献[11]对圆铜线绕组的交直流损耗进行了分析,当电机频率在1 kHz以下时,定子绕组的交、直流损耗比约为1,可忽略趋肤效应和邻近效应的影响;文献[49]对一台5 MW、6.3 kV的高速永磁电机采用了扁铜线绕组结构,并对定子绕组损耗进行了分析,分析结果显示,当频率为400 Hz时,定子绕组的交流损耗约为直流损耗的3倍,因此扁铜线绕组的交、直流损耗比受频率影响非常明显,在进行高频铜耗计算时,必须考虑趋肤效应和邻近效应的影响。
3 转子结构的设计
3.1 笼型转子
3.1.1 转子槽型
高速叠片式笼型转子通常采用闭口槽,闭口槽类型主要有圆形槽、水滴槽、平行槽3种,如图3所示。圆形槽的优势为对转子铁心上应力的分布影响较小,可保证转子具有较高的机械强度,工艺简单、成本低,而缺点为转子齿磁通密度易产生局部过大,导条电流密度过高,转子铜耗较大。水滴槽和平行槽是在圆形槽之上改良的,可有效减小转子齿磁通密度,同时增大了导条面积,减小了导条上的电流密度,具有较小的转子铜耗,但机械强度低于圆形槽。
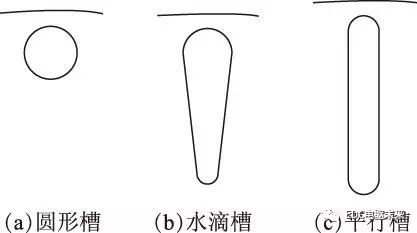
3.1.2 转子铜条材料
纯铜在温度较高的情况下会发生软化现象,因此在高速感应电机的设计中,主要采用铜合金作为转子导条材料。表7列出了几种常用的铜合金材料属性,在选择导条材料时,要综合考虑机械强度和转子铜耗,在保证机械强度的情况下,应选择电导率较大的铜合金。
表7 不同导体材料属性
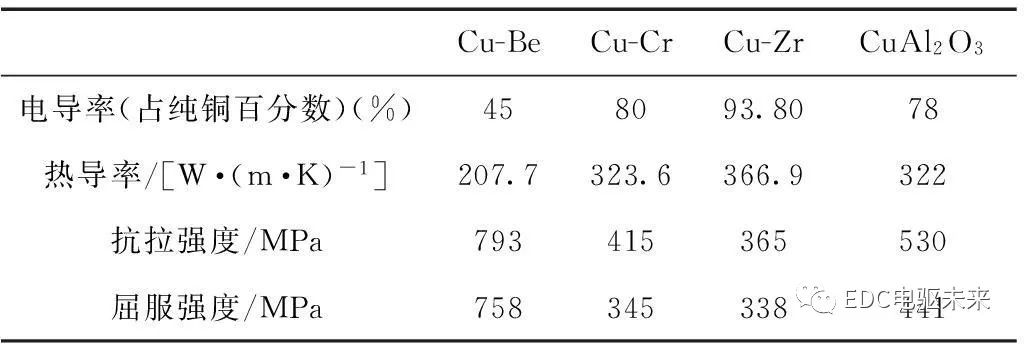
3.1.3 端环的保护
感应电机的端环与铜条是焊接而成的,当高速旋转时,焊接处易发生损坏,因此必须对端环进行保护,目前最常用的保护措施是用铆钉将端环与转子铁心固定在一起以增加转子整体的机械强度,如图4所示。
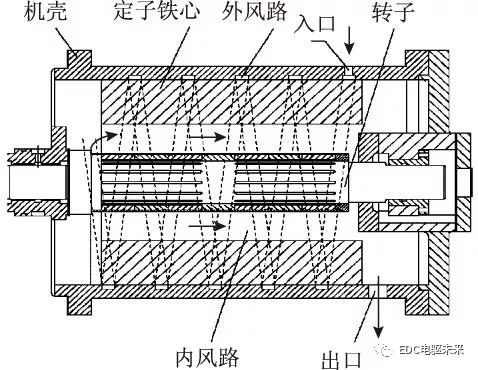
3.2 实心转子
实心转子高速感应电机有如图5所示的4种转子结构。文献基于一台75 kW、60 000 r/min的高速感应电机,对4种转子结构的应力和损耗进行了比较分析,如图6所示。可以看出,实心钢转子结构和铜屏蔽转子结构的转子强度较好,开槽实心转子的转子应力远大于其他3种转子结构,但实心钢转子结构的转子涡流损耗最大,开槽实心转子次之;铜屏蔽转子和笼型实心转子因为在转子材料中有铜导体,这些铜导体为电流提供了通路,能够减小一部分涡流,所以这两种转子的损耗比另外两种转子损耗低。
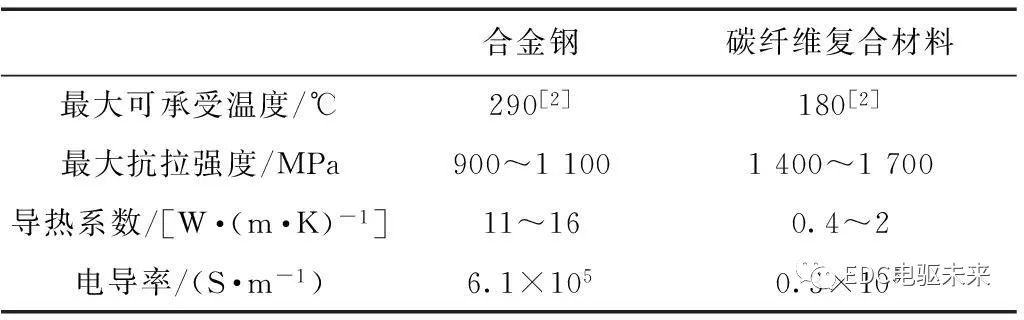
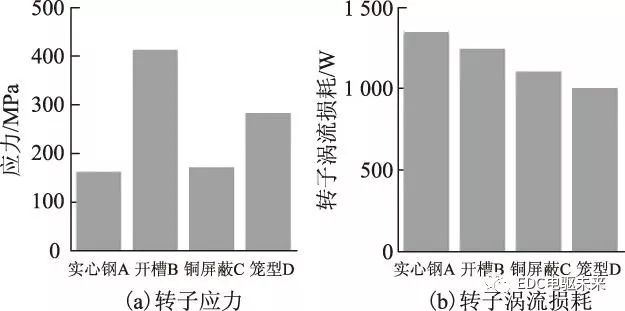
3.3 永磁转子
3.3.1 永磁材料
常用的永磁体材料主要有NdFeB和SmCo。NdFeB材料的剩磁密度和矫顽力较大,但易受温度影响,最大可承受温度约为220 ℃,抗拉强度约为80~140 MPa,SmCo材料的剩磁密度较小,受温度影响较小,可承受的温度高达350 ℃,但抗拉强度小,约为25~35 MPa,使用SmCo永磁材料时会增加保护套厚度和等效气隙长度。
3.3.2 内置式永磁转子
为了改善传统内置式永磁转子结构在高速运行时易在隔磁桥处应力过大的问题,内置式高速永磁转子多采用永磁体分段,并在永磁体段间设置加强筋的结构。图7列举了几种常用的内置式高速永磁转子结构。图7a为一字形永磁体分段结构,该种分段结构也可采用V形和W形等结构型式。文献[95]在8 kW、40 000 r/min的高速永磁电机中采用了2极结构,分析了永磁体层数及每层加强筋数量等对电磁特性和转子应力的影响,永磁体层数对转子应力的影响很小,可忽略不计,最终样机采用了图7d所示的转子结构,该种结构具有较小的漏磁系数。文献[5]介绍了一种新型切向式高速永磁电机转子结构,如图7e所示,C形硅钢片挂在高强度的不导磁轴上,永磁体为不等厚结构,靠近转轴处较厚,沿半径方向逐渐减小,这种结构即可降低硅钢片应力,又拥有较小的漏磁系数。
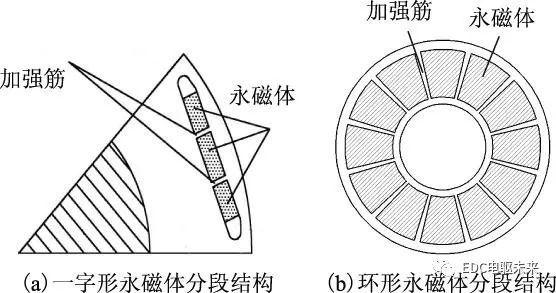
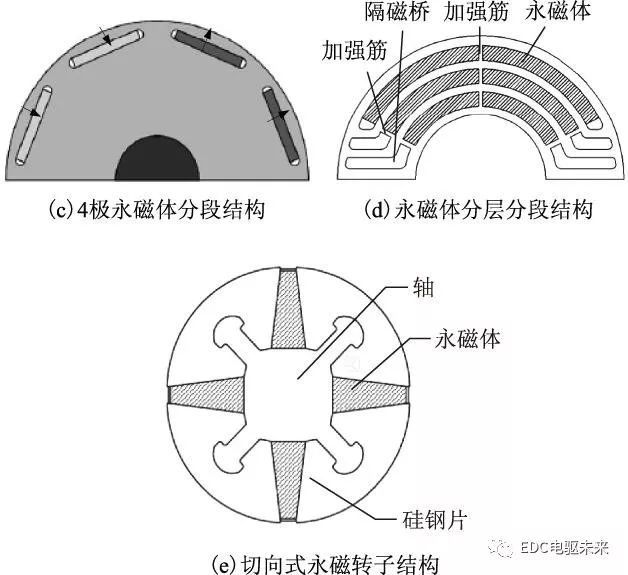
3.3.3 表贴式永磁转子结构及其保护措施
表贴式高速永磁电机的转子结构如图8所示。图8a为实心永磁体结构,该转子结构为2极,永磁体采用平行充磁的方式。查阅到的相关文献中介绍的75 kW、60 000 r/min,150 kW、24 000 r/min,0.5 kW、400 000 r/min和0.1 kW、500 000 r/min的高速永磁电机均采用了该种转子结构。图8b为2极环形永磁体结构,采用了平行充磁方式和永磁体不分块技术,该种转子结构即为2极Halbach结构,加工较简单,多用于转子外径较小的高速永磁电机,2.3 kW、150 000 r/min和10 kW、70 000 r/min等高速电机均采用了该种结构。图8c为面包式永磁转子结构,该结构的气隙磁通密度更接近正弦波,谐波较小,但所需永磁体较厚,文献[52,53]分别介绍的1.5 MW、20 000 r/min和120 kW、70 000 r/min的高速永磁电机均采用该种转子结构。图8d为永磁体分段转子结构,极间间隙可由高温塑料、环氧树脂、碳纤维、合金等材料填充,从而降低保护套在极间间隙处的弯曲应力,提高转子可靠性,该种转子结构为高速永磁电机最常用的转子结构。为了降低转子涡流损耗,Halbach充磁转子结构越来越多的在高速电机中应用,图8e给出了3种Halbach充磁结构,30 kW、20 000 r/min和640 kW、10 000 r/min的高速永磁电机均采用了该种转子结构。
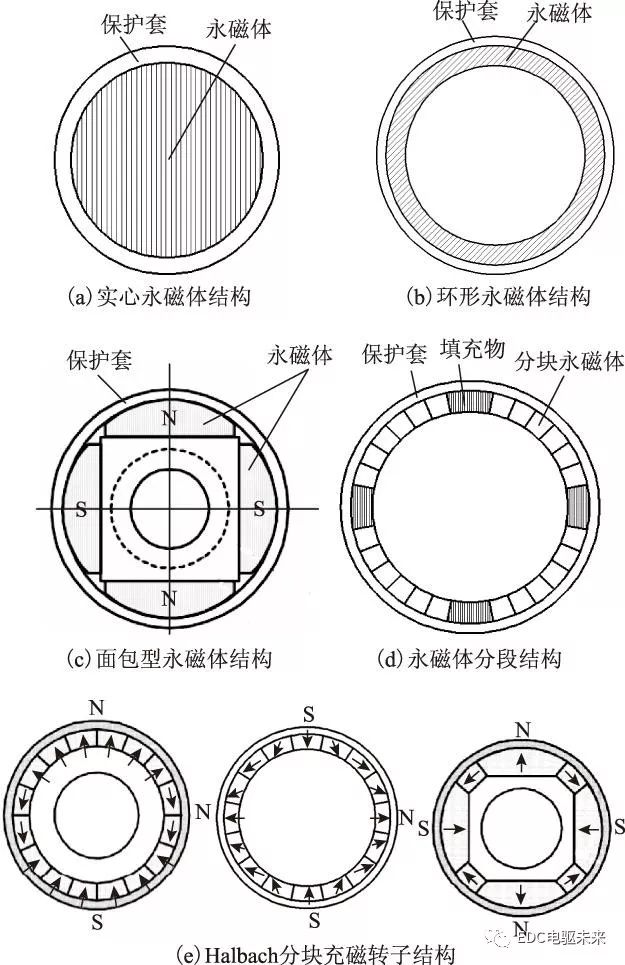
对于表贴式永磁转子,必须对永磁体采取保护措施:一种保护方法是在永磁体外面用高强度非导磁护套(如Inconel718、钛合金等),另一种保护方法是采用碳纤维等高强度纤维捆扎。两种材料的特性如表8所示。考虑温度和弯曲应力时碳纤维护套的最大可承受应力约为1 400~1 700 MPa,大于合金钢护套最大抗拉强度,但合金护套可承受的最大温度(290 ℃)远高于碳纤维护套(180 ℃)。合金钢材料的电导率较高,电机空间谐波和时间谐波会在合金保护套中产生较大的涡流损耗。采用碳纤维捆扎时保护套厚度和高频涡流损耗较小,但碳纤维是热的不良导体,不利于永磁转子的散热。文献[138]介绍的在合金保护套内层加入铜屏蔽层可有效抑制转子涡流损耗,但对碳纤维保护措施抑制效果并不明显。文献[82]在合金保护套上开设轴向和周向浅槽来降低转子涡流损耗,周向浅槽结构如图9所示。
表8 不同保护套材料属性
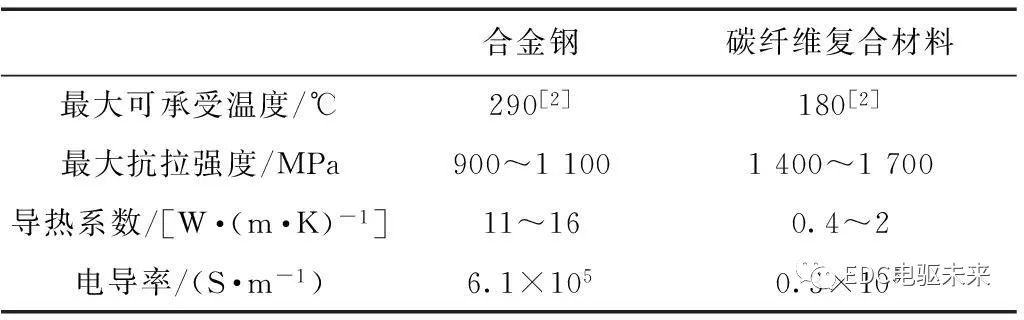
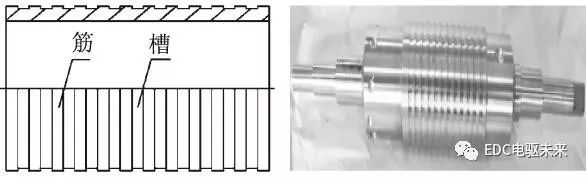
针对高速永磁电机,文献[139]提出了一种半导磁的合金保护套,相对磁导率为7.2,与非导磁合金保护套相比,采用半导磁保护套可明显改善电机的空载反电动势波形。文献[140]介绍了一台75 kW、60 000 r/min的高速永磁电机,该文从电磁特性、转子应力、转子温度等方面综合比较了碳纤维保护套、非导磁合金护套以及半导磁合金护套的性能。采用碳纤维护套所需保护套厚度、转子损耗、转子温度均最小,采用半导磁合金护套所需永磁体厚度最小,保护套厚度小于非导磁合金护套,但转子涡流损耗远大于非导磁合金护套和碳纤维保护套。
文献[141]对一台1 120 kW、18 000 r/min的高速永磁电机设计了两种保护措施:一种采用纯碳纤维保护措施,一种采用合金钢和碳纤维共同组成的混合保护措施,如图10所示。其中纯碳纤维保护套与永磁体采用过盈配合,混合保护措施与永磁体采用间隙配合,间隙处填充高强度粘合剂,混合保护措施可降低纯碳纤维保护套的弯曲应力。实验表明采用上述保护措施的两种转子样机均能在22 000 r/min安全运行。
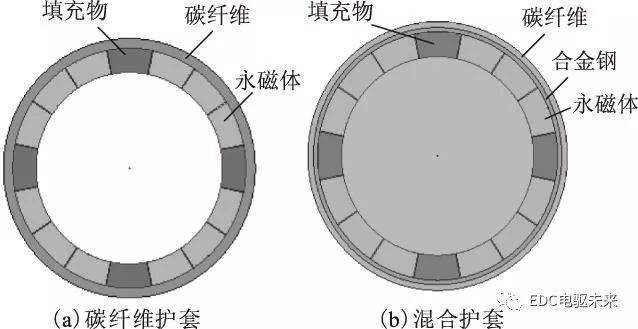
文献[71,142]中介绍的转速分别为200 000 r/min和60 000 r/min的两台高速永磁电机,在碳纤维保护套内层均缠绕了一层较薄的玻璃丝纤维,目的在于有效抑制在永磁体弯曲处和永磁体分块对碳纤维护套造成的弯曲应力,提高保护套可靠性。
4 转子系统的动力学设计与轴承设计
4.1 转子系统动力学设计
转子动力学设计是高速旋转机械设计的重要内容,转子旋转时,转子的质量中心和回转中心总会有一定的偏差,使转子产生周期性的离心干扰力,使得转子的偏心进一步增加,转子振动的幅度进一步增大,当转子的转速与转子的临界转速接近时,转子将会发生剧烈的弯曲振动,引起整个机组振动,严重时甚至使得转子遭到破坏。对于刚性转子,工作转速n应低于一阶临界转速nc1,即n<0.7nc1;对于挠性转子,应使工作转速在一阶临界转速nc1和二阶临界转速nc 2之间,即1.4nc1
编辑推荐
最新资讯
-
风噪测试在电动汽车时代的关键作用
2025-04-29 11:34
-
汉航车辆性能测试系列之操纵稳定性测试--汉
2025-04-29 11:09
-
新能源汽车热管理系统验证体系PITMS正式发
2025-04-29 11:09
-
试验载荷谱采集
2025-04-29 11:07
-
APx500 软件演示模式 (Demo Mode) 竟有这些
2025-04-29 08:37