1、概述
托底工况指的是汽车底盘在行驶中碰到地面或者地面突出物。汽车过减速带、撞击路沿、上坡顶、走坑洼路以及压过路面上的石头或砖块,都可能发生托底。车轮带起石子击打车底的情况也可归属到托底工况。
对于传统燃油车,托底的危害主要是油底壳变形、排气管变形、悬架部件变形和传动机构损伤,通常不会对乘员造成人身伤害。所以传统燃油车的碰撞安全性能开发中一般不考虑托底工况,最多是将托底作为气囊标定的误作用工况来研究。
图1 蔚来ES8底盘受撞数日后电池包自燃
但对于在地板下布置动力电池的纯电动汽车,托底的后果要严重的多。动力电池底面不受车身结构的保护,而且面积大,更容易受到剐蹭和撞击。托底工况易造成电池损伤,严重时会起火爆炸。而且托底造成的损伤在电池底部,不易察觉,具有隐蔽性。有些托底事故虽然当时未发生短路起火,车辆还能继续行驶,但电池包已经严重变形。如果用户未及时发现处理,电池芯体和高压器件持续处于挤压状态,电池包可能在一段时间后发生自燃。
2、托底工况的试验模拟
托底对动力电池结构的破坏主要有两种模式。一种是刮底模式,即动力电池的前端和底部受到前后方向的剐蹭,载荷以水平方向为主,也有一些垂向成分。通常会造成电池前边框和电池底壳前半部变形,严重时甚至会将电池壳体从前到后划开。
另一种是撞底模式,即动力电池底面受到向上的挤压或撞击。载荷以垂直方向为主,可使车轮一轮或多轮离地。通常会造成电池底壳垂向变形,严重时会将电池底壳顶穿后进而刺破内部芯体。
针对以上两种电池破坏模式,可以用两个标准工况来模拟托底。
第一种是整车刮底工况:
地面固定一楔形刚性块,如图2。楔形块斜面为45度,高度设置为与电池壳体在Z向有35mm左右的重叠量。
整车以每小时10公里的速度驶过楔形块。
共进行三次刮底试验,楔形块分别对应电池包的左侧、右侧和中心线。
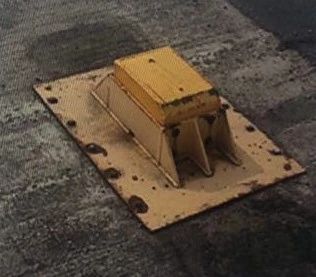
图2 刮底工况用的楔形块
第二种是车底球击工况:
车辆按满载状态静止于地面。用直径75mm的刚性圆球,从车底沿Z向顶起动力电池底面,如图3。
采用准静态加载,载荷从0逐渐增加至整车满载质量的一半。
刚性圆球加载点选择电池底部最薄弱或者最危险的数个位置,逐个进行考察。
图3 底部球击工况
托底是可能多次发生的情况,所以我们将整车刮底和车底球击定义为整车耐久工况而不是整车安全工况。对于整车安全工况,要求电芯不受撞击和挤压以避免起火爆炸,但并不要求动力电池还能继续使用,动力电池允许损坏甚至报废。对于整车耐久工况,则要求这种工况发生多次后动力电池都能保证功能正常,且无安全隐患。
基于以上考虑,可以将整车刮底和车底球击工况的考察指标设定如下:
- 加载后电池包壳体结构不破碎、无可见裂纹。
- 电池包壳体无明显变形(建议加载过程中壳体最大侵入量小于4mm,加载后壳体永久变形量小于1mm)。
- 内部冷却系统和管线、插接件和芯体等无损伤。
- 动力电池功能正常,可继续使用。
要达到以上指标,电池包下壳体要非常强壮,通常只有厚度足够且设计有大量加强筋的铸造壳体才能达标。对于挤压铝、钢板或者铝板材质的下壳体,在大载荷下容易发生较大变形,要通过整车刮底和车底球击工况考察,需考虑增加电池包防护梁和电池包底护板。
3、电池包防护梁设计
整车刮底工况导致的电池包损伤主要集中在电池包前部区域,在动力电池包前布置一道防护梁能够有效保护电池。
目前已经有多款量产车型应用了电池包防护梁,如图4。防护梁有圆管截面、矩形截面、三角形截面和平板型等多种形式。其中圆管型梁工艺简单,成本低廉,刚强度好,应当是电池包防护梁的首选。
图4 各种电池包防护梁
防护梁的安装布置要注意以下三点:
- 防护梁应装在车身上,不要直接装在电池包上,以避免防护梁将载荷传递到电池包。
- 防护梁最下缘应比电池包底面至少低10mm,保证防护梁先于电池包与地面突起物接触。
- 防护梁距离电池包前端的X向距离应控制在100-150mm左右。如果距离太远,影响防护效果;如果距离太近,防护梁受力变形后有可能撞击到电池包。
电池防护梁的防护功能实际有三种:
- 对于类似图2的楔形固定物,车辆向前行驶,防护梁刮过楔形物,如图5。防护梁能够保护电池前端不受直接撞击,仅电池底面的中后部会受到楔形物刮蹭。此种情况最大的风险是电池包底面刮蹭破坏。
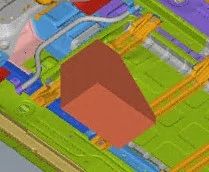
- 图5 电池包防护梁刮过楔形块
- 对于石块砖块等地面异物,车辆向前行驶时,防护梁将异物撞飞或者击碎,避免电池包前端与突起物撞击。此种工况下最大的风险是飞溅的异物碎片击坏电池包下壳体。
- 对于柱状地面障碍物,车辆向前行驶,防护梁被障碍物阻挡,如图6。车辆无法继续前进,电池包不会与障碍物接触。此种情况最大的风险是防护梁变形过大撞击电池包前端。
图6 电池包防护梁被障碍物阻挡
本文所介绍的整车刮底工况实际只考察了第一种防护功能,如果只考虑整车刮底工况,较细的电池防护梁即可满足。但要实现第二种和第三种防护功能,则要求电池防护梁足够强壮。所以在空间和重量允许的情况下,我们应尽量将电池防护梁截面做大,厚度适当增加,与车身的连接点也尽量增多,建议采用4处连接点。
4、电池包底护板设计
整车刮底和车底球击工况下,电池底面都有可能受力损坏,增加底护板是相当有效的防护手段。
电池包底护板应满足以下指标要求:
给动力电池足够防护,使电池包通过车底球击工况考察。
与电池包防护梁配合,使电池包通过整车刮底工况考察。
整车刮底和车底球击工况下,电池包护板不破碎,不出现可见裂纹,但允许有可见变形。
底护板安装后的约束模态频率大于30Hz。
上海市强制性地方标准BD31T634-2012规定的整车涉水工况下,底护板不破裂不脱落。
底护板可考虑采用2mm左右厚度的铝板或者1.2mm左右厚度的钢板,需要涂装防石击涂层。也可采用非金属材料,例如改性塑料和玻纤复合材料等,料厚通常需要在3mm以上。
底护板应采用螺栓与电池包连接,不能使用胶粘连接。这是因为螺接的底护板可归属车身,其重量不会影响电池包能量密度测算。如果底护板与电池包粘接,底护板的重量只能归属到电池包,将会降低电池包能量密度值,影响补贴金额。
为保证防护效果和模态频率达标,底护板需要设计合理的加强筋。底护板两侧和前后都应有固定点,中部还应有多个固定点与电池底壳相连接,如图7所示。底护板中间连接点的数目不应低于4个,且应分布均匀,避免出现局部受力集中点。
图7 一种底护板方案
为保证在涉水工况下不发生破坏,底护板应设计多个泄水孔。底护板螺栓安装点处必须有足够的压紧面,即在每个安装点处,护板与电池包压紧配合面的直径不小于20mm,否则在涉水时安装点处极有可能发生撕裂。
5、小结
对于纯电动汽车,托底工况容易造成动力电池包损坏,可能引发严重事故。托底工况包含刮底和撞底两种载荷模式,可采用整车刮底和车底球击两个标准工况来分别模拟。
当前大多数动力电池壳体很难直接通过整车刮底和车底球击工况考察。电池包防护梁和电池包底护板是有效的加强方案。可明显缓解托底造成的电池损坏。
电池包防护梁应设计得尽量粗壮,应装在车身上而不是电池包壳体上。其最下缘应比电池包底面至少低10mm,距离电池包前端的X向距离应控制在100-150mm左右。
电池包底护板要有足够的厚度,需要设计合理的加强筋,中部还应有多个固定点与电池底壳相连接。其约束模态应大于30Hz,还须保证在涉水工况下的强度。
作者简介
王朋波,清华大学力学博士,汽车结构CAE分析专家。重庆市科协成员、《计算机辅助工程》期刊审稿人、交通运输部项目评审专家。专业领域为整车疲劳耐久/NVH/碰撞安全性能开发与仿真计算,车体结构优化与轻量化,CAE分析流程自动化等。王朋波私人微信:poplewang。