负游隙对轮毂轴承摩擦力矩的影响
1 引言
负游隙是第三代汽车轮毂轴承单元的重要参数之一,负游隙影响着轮毂轴承的载荷分布、振动、噪声、摩擦力矩及寿命等[1],其中,摩擦力矩直接影响着轮毂轴承的效率。为了降低摩擦力矩,减小轮毂轴承的功率损失,进而提升汽车传动系统的效率,对轮毂轴承负游隙的研究就显得尤为重要。虽然对轮毂轴承负游隙作出了很多研究,但对负游隙如何影响摩擦力矩方面的研究却较少,因此主要针对某前置前驱车型第三代轮毂轴承,研究负游隙对其摩擦力矩的影响。
2 轮毂轴承的摩擦力矩
摩擦特性是轮毂轴承的一项重要性能指标,摩擦不仅会造成大量的能量损失,摩擦引起的磨损还会使轴承精度下降,产生过高的温升,导致工作表面烧伤或润滑剂失效等。轮毂轴承的摩擦力矩是一个十分复杂的问题,与其结构、几何精度、材料性能、工作载荷、装配精度、润滑条件及加工工艺等多种因素相关。
2.1 摩擦力矩的计算
根据轮毂轴承内部的摩擦特点,其摩擦力矩由多方面的因素共同决定,本次研究主要考虑由滚动材料的弹性滞后、差动滑动及自旋滑动引起的摩擦力矩。
2.1.1 弹性滞后引起的摩擦力矩MT
滚动体在滚道上滚动时由于材料的弹性滞后,产生的摩擦力矩MT为:

式中:dm—轴承节圆直径,m;γ=DW cosα/d m,DW—钢球直径,mm;α—接触角,rad;Z—钢球数;Qi(o)j—接触载荷,N;KT—与材料弹性模量、第一、二类椭圆积分、主曲率函数等相关的系数;β—弹性滞后系数,轴承钢取0.007。
受载后滚动体与内滚道会发生接触变形,由于两物体在接触面上各点的线速度不同,产生的差动滑动摩擦力矩为:
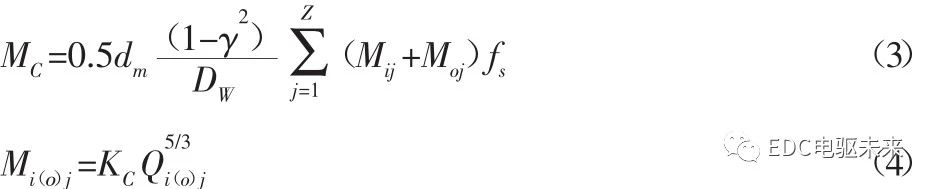
式中:fs—滑动摩擦系数,轴承钢取0.08;KC—与材料弹性模量、第二类椭圆积分、主曲率函数及沟曲率等相关的系数。
2.1.3 自旋滑动引起的摩擦力矩MZ
在双列角接触球轮毂轴承中,由于接触角的存在,在滚动体相对滚道绕接触面法线自旋滑动时产生了摩擦力矩:

式中:Fi(ο)j—第二类椭圆积分;
ai(ο)j—接触椭圆长半轴,mm。
则轮毂轴承中与载荷相关总的摩擦力矩为:

由计算公式可知,以上摩擦力矩均与轮毂轴承所受的载荷Q呈正相关,随着载荷Q的增大,摩擦力矩增大。
3 轮毂轴承负游隙
3.1 负游隙的设计
汽车轮毂轴承的游隙设计一般依据轴承寿命最大化原则,寿命的最大化与轴承的游隙直接相关。
当轮毂轴承在较大正游隙下工作时,载荷集中作用于受力方向的滚动体上,这部分滚动体和内外圈沟道接触处将会产生很大的集中应力,导致轴承的寿命缩短;而当工作在负游隙下时,滚动体工作条件得到改善,各个滚动体将会更加均匀的受力,从而保证了轴承的使用寿命。
轴承寿命理论分析与大量的寿命试验表明:轮毂轴承的工作游隙设计在(-0.01~-0.06)mm范围内时,轴承会有更长的寿命。如图1所示[10],当轮毂轴承的工作游隙>(-0.01)mm时,由于沟道预载荷变小,随着工作游隙的增加,轴承寿命呈平缓下降的趋势;当工作游隙<(-0.06)mm时,沟道预载荷过大,运转过程中轴承内部温升高且轴承内圈挤压变形,随着工作游隙的减小,轴承寿命呈急剧下降趋势,同时也会增大摩擦力矩,降低轴承效率。
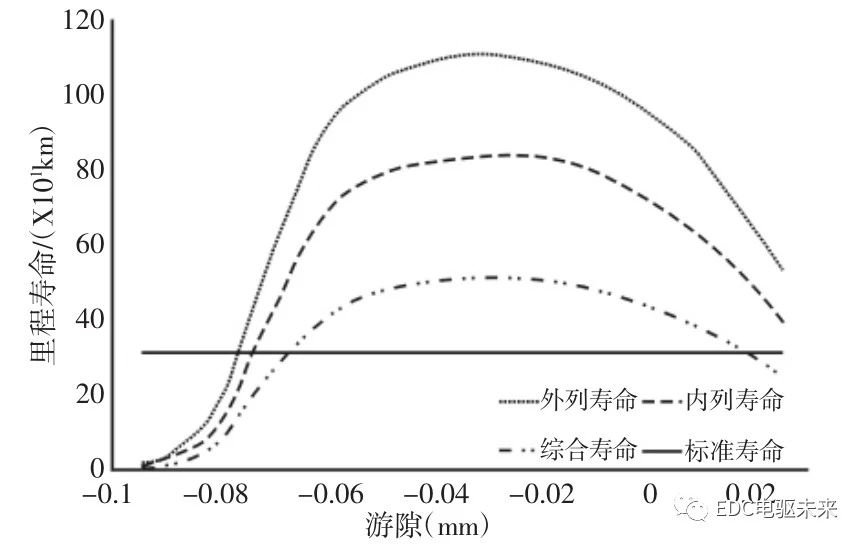
Fig.1 Relation Between Hub Bearing Work Clearance and Life
为了使轮毂轴承有更长的使用寿命,目前第三代汽车轮毂轴承普遍设计为极小的负游隙,因此,主要针对负游隙在(0~-0.06)mm范围内的轮毂轴承进行研究。
3.2 负游隙接触理论模型
第三代汽车轮毂轴承装配件为负游隙状态,轴承空载时钢球与滚道已经发生弹性变形。为研究负游隙对轮毂轴承摩擦力矩的影响,建立了轮毂轴承负游隙的接触理论模型。
两接触体的赫兹接触理论模型,如图2所示。则对于轮毂轴承:
内、外滚道曲率和:

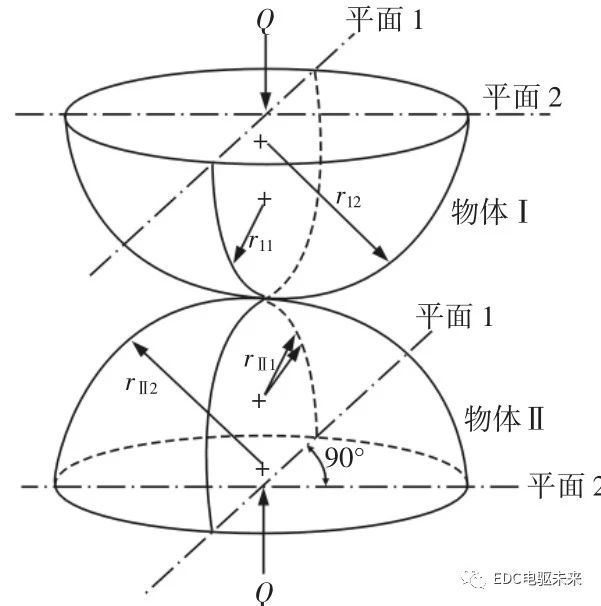
Fig.2 Geometry Model of Contact Bodies
内、外滚道曲率差:

轮毂轴承装配前径向负游隙理论值:

由于轮毂轴承的两种材料属性接近,可得到简化计算公式:
接触区域投影椭圆长半轴:

接触区域投影椭圆短半轴:

接触位移:

式中:a*—接触椭圆量纲为1的长半轴,mm;b*—接触椭圆量纲为1 的短半轴,mm;δ*—量纲为 1 的接触位移,mm(a*、b*与 δ*均为F(ρi(o))的函数,通过查相关资料得到);Q—轮毂轴承载荷,N。

3.3 轮毂轴承接触载荷的计算
某车型轮毂轴承参数:钢球D=13.494mm,内圈滚道曲率半径Ri=6.950mm,外圈滚道曲率半径Ro=7.084 mm,内圈滚道沟径Di=47.928 mm,外圈滚道沟径Do=75.190 mm。
轮毂轴承装配时,通常设有一定的压装量,从而使轮毂轴承产生一个很小的负游隙。假设钢球直径为D=13.494mm时,压装后的游隙值为0,此时轴承为零游隙状态,钢球与滚道恰好没有接触应力,假定轴承其他尺寸不变,通过钢球直径的增大而得到负游隙。计算得到的空载时不同负游隙轮毂轴承的接触载荷,如表1所示。
表1 不同负游隙轮毂轴承的接触载荷
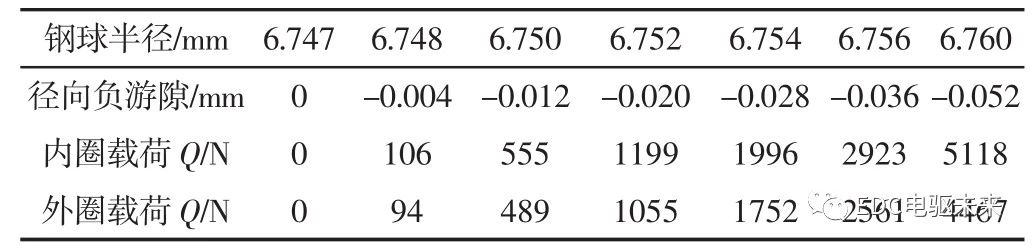
轮毂轴承负游隙与接触载荷的关系曲线,如图3所示。由图可知,随着负游隙的增大,轴承内外滚道的接触载荷呈逐渐增大的趋势,负游隙的增大将导致轴承摩擦力矩的增大,当负游隙超过一定的范围时,将对轮毂轴承效率的提升产生不利影响。
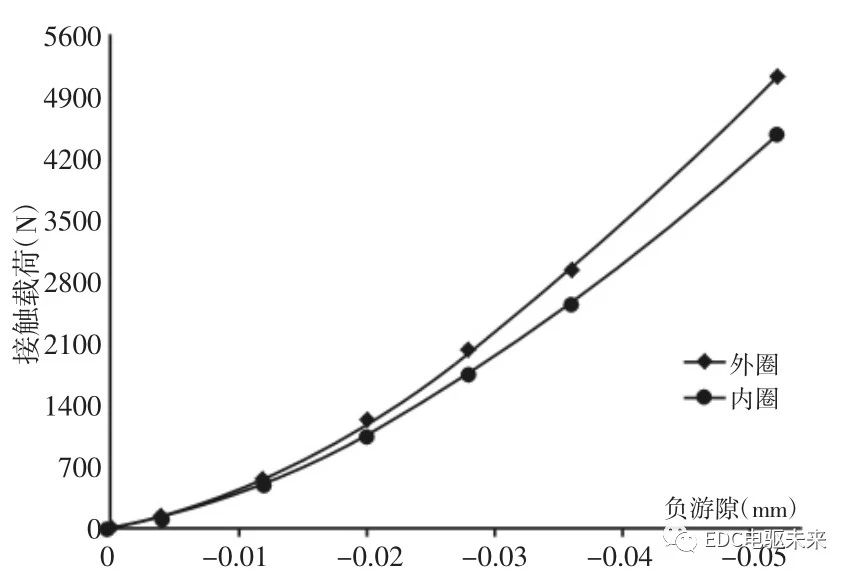
4 试验方案
4.1 试验原理
试验采用汽车轮毂轴承摩擦力矩试验机测试轮毂轴承的摩擦力矩。试验机结构主要包括:主轴部件、测试部件、径向加载部件、轴向加载部件、电气控制系统及工业计算机等。
轮毂轴承安装到芯轴上,芯轴固定在传动主轴上,伺服电机通过传动主轴、轮毂轴承连接,各部件通过对测试部件进行径向和轴向加载,产生的旋转扭矩传递到外圈和衬套,再由连杆传递到扭矩传感器,然后通过扭矩传感器测出相应的数值,从而得到轮毂轴承的摩擦力矩。轮毂轴承的摩擦力矩测试设备,如图4所示。
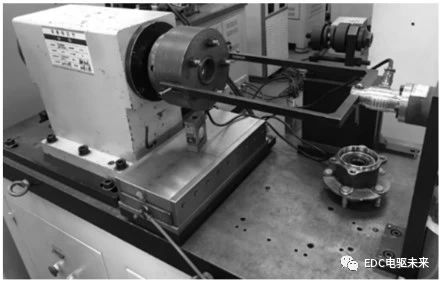
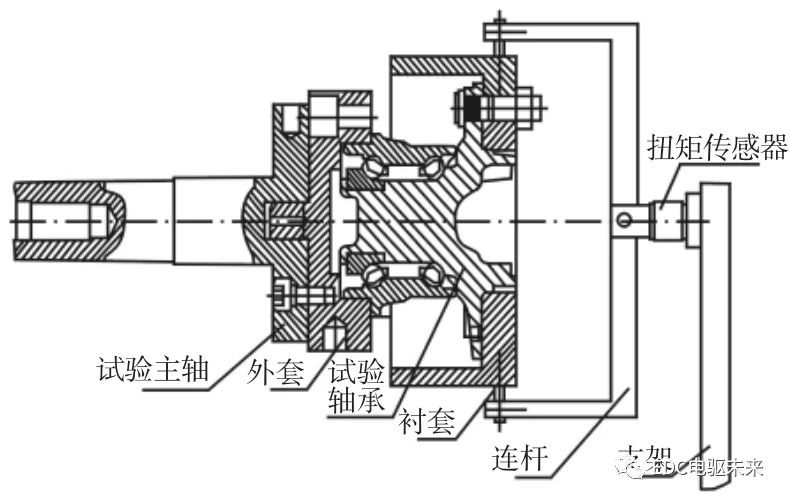
试验中按照图5的检测原理图将汽车轮毂轴承装上工装,一侧连接旋转主轴,主轴通过电机转动,另一侧连接连杆,轴承选装后通过连杆传导力矩至力矩传感器,进而输出力矩值。
4.2 试验工况
本试验的测试对象为某车型第三代汽车双列角接触球轮毂轴承。在生产线上挑选出不同负游隙的轮毂轴承作为试验测试样件,在实际生产过程中,由于各种误差的存在,且轮毂轴承铆接后的负游隙目前还难以准确检测,因此试验中的负游隙为根据铆接前游隙得到的理论计算值,并且轴承的负游隙值比较随机,不能保证等范围选取,试验选取的测试样本负游隙值分别为(-0.036)mm、(-0.030)mm、(-0.023)mm、(-0.020)mm、(-0.014)mm 及(-0.010)mm。试验过程中,首先使轮毂轴承以10r/min的转速转动,以测量其启动力矩,然后以500r/min的转速,磨合10min后,分别以100r/min、200r/min、…900r/min、1000r/min的转速运转,不加载测试摩擦力矩,转速控制精度保证在(±5)r/min以内,每种转速下稳定运转60s后,测量摩擦力矩值,记录不同转速下的摩擦力矩。按照以上提出的试验工况要求,参照汽车轮毂轴承摩擦力矩的相关测试标准,即可测得各种转速下不同负游隙轮毂轴承的摩擦力矩值。
5 结果
通过对不同负游隙的轮毂轴承进行测试,所得到的负游隙与摩擦力矩的关系曲线,如图6所示。
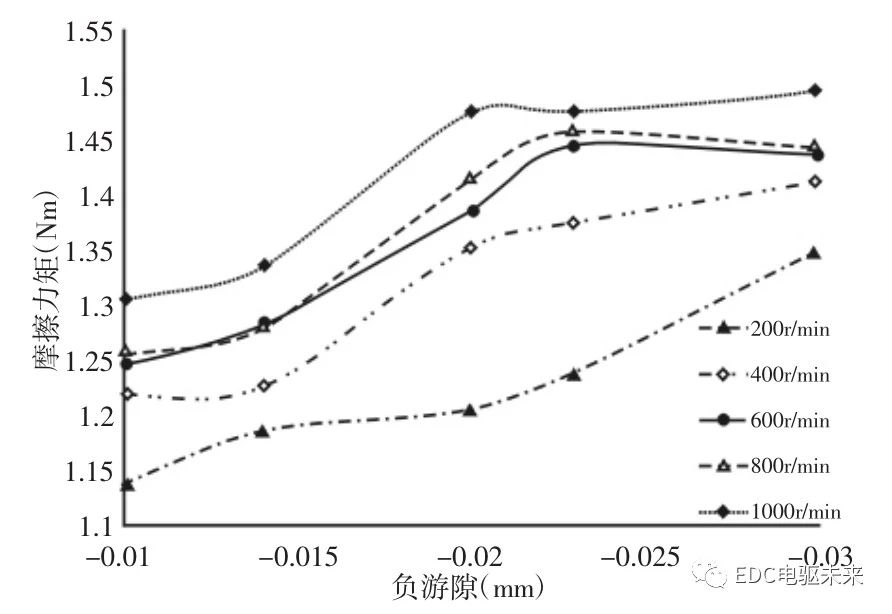
由图6中可知,负游隙对轮毂轴承的摩擦力矩影响较为明显,其摩擦力矩差值达到了0.2Nm左右。试验结果表明:负游隙在(-0.010~-0.025)mm范围内时,随着轮毂轴承负游隙绝对值的增大,其摩擦力矩增大,且增加趋势较为明显,当负游隙值超过一定值后,随着负游隙绝对值的继续增大,摩擦力矩增加,但增幅趋于平缓。因此,适当的减小负游隙绝对值对提升传动系统效率具有一定的实际意义。
6 结束语
主要针对汽车轮毂轴承负游隙对其摩擦力矩的影响进行了理论分析及试验研究,可以得到如下结论:
(1)对轮毂轴承的摩擦力矩进行了理论分析,明确了载荷对其摩擦力矩的重要影响;
(2)建立了轮毂轴承负游隙的接触理论模型,分析了负游隙的变化对钢球与内外圈滚道间接触载荷的影响,分析结果表明,随着负游隙绝对值的增大,钢球与滚道的接触载荷逐渐增大;
(3)对不同负游隙轮毂轴承的摩擦力矩进行试验测试,结果表明:随着负游隙绝对值的减小,其摩擦力矩呈逐渐减小的趋势,这将为轮毂轴承的减摩设计以及效率的提升提供了指导依据。
- 下一篇:轮毂电机驱动平台的转矩矢量分配技术
- 上一篇:液压悬置在整车上的放置位置及作用
编辑推荐
最新资讯
-
奇石乐推出用于DAQ数据采集系统的KiStudio
2025-04-28 17:51
-
全球首次!IVISTA 2023版修订版引入带灯光
2025-04-28 09:59
-
我国首批5G毫米波行业标准送审稿审查通过
2025-04-28 08:56
-
5/16 厦门- 新能源汽车电驱测试技术的创新
2025-04-28 08:53
-
国内首个汽车电磁防护技术验证体系EMTA正式
2025-04-28 08:49