基于有限元技术的发动机悬置支架拓扑优化设计研究
通过建立悬置系统的动力学模型,进行动力学仿真并获得载荷数据。
进而应用有限元方法对发动机悬置支架进行分析;
根据分析结果,使用连续体结构拓扑优化技术对支架模型进行优化设计;
减轻了悬置支架的质量,指出了拓扑优化在轻量化设计中的重要意义。
关键词:悬置支架 运动学仿真 有限元分析拓扑优化轻量化
前言
随着汽车工业的快速发展及日益突出的能源问题,对汽车设计提出的新要求是降低其制造成本及提高整车燃油经济性,通过对零部件和整车进行材料优化配置和结构优化设计,可以在不影响其强度和性能的基础上达到产品的轻量化,以期实现降低制造成本和节能的目标。
拓扑优化技术是一项新兴的设计方法,它可以在方案设计阶段给出零部件甚至车身原型合理的材料布局,减轻结构重量. 通过这项技术,企业能缩短设计周期,提高产品性能,减少昂贵的样件生产和整车测试的次数。目前,均匀化法、变厚度法、变密度法等方法对于处理平面问题的拓扑优化已日趋成熟。
变密度法的基本思想是引入一种假想的密度可变材料,对结构中每个有限单元赋予内部伪密度(pseudo-density),然后通过内部伪密度来确定目标函数。设单元密度为0到1之间的某一值,如某些单元所受应力较小,可相应减小密度;如某些单元是关键单元,则可相应增加密度。最后根据单元密度,通过设定门槛值来调整材料的分配。当某处单元的相对密度为1,则表示该单元为有材料,应保留或增加该单元(实体),如果相对密度为0,表示该处单元无材料,单元可以删除。这样,优化时就以材料密度为设计变量,使结构的拓扑优化问题转换为材料的最优分布问题[1] [2]。
变速器悬置支架(见图1)是动力总成悬置系统中的安全件和功能件,它的作用是支撑悬置、连接变速器以及传递作用在动力总成上的一切力和力矩,另外,悬置支架的一阶固有频率对车内噪声的影响很大,因此,在动力总成悬置系统设计时,应对支架的强度和固有频率进行优化设计和试验验证。本文使用了Hypermesh及其Optistruct模块,对变速器悬置支架进行了前处理和拓扑优化,并对优化前后的悬置支架在各载荷工况下所受应力和前三阶的约束模态进行了比较,验证了优化方案的有效性和可靠性。各工况的载荷数据通过ADAMS软件建立悬置系统动力学仿真模型进行仿真分析来获得。
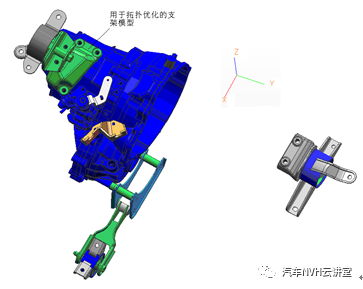
1 悬置系统动力学仿真
1.1 动力学仿真模型建立
Lagrange乘子方法是多体系统动力学建模中经常使用的方法,根据所研究的动力总成悬置系统特点,悬置每个刚体质心的笛卡儿坐标作为系统的广义坐标。
根据拉格朗日法建立运动方程[3][4],即
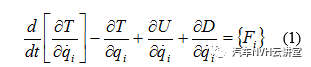
式中T ———系统振动时的动能
U ———系统振动时的势能
D ———系统振动时产生耗散能
Fi ———发动机的激振力
可建立系统的动力学方程。动力总成悬置系统的动力学方程表示为:

其中:为系统质量矩阵,为系统阻尼矩阵,为系统刚度矩阵,为激振力。
不考虑阻尼和外力作用,可得到系统的自由振动的微分方程,也即系统六自由度固有特性的分析方程:

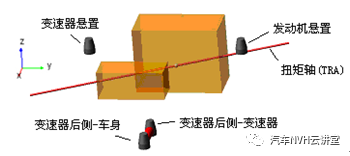
关系的发动机和变速器组合为一体。输入零部件惯性特性参数、悬置的阻尼特性、刚度特性、悬置的安装角度和安装位置。在ADAMS环境中把表1、2和表3的数据输入进行悬置系统的动力学仿真。
表1 动力总成惯性特性参数
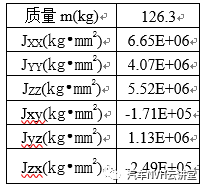
表2 悬置的安装位置
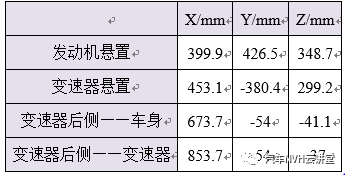
表3 悬置件的主轴刚度
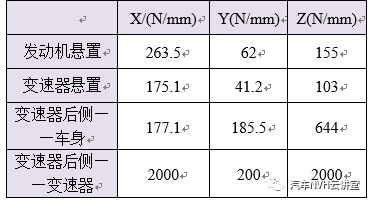
1.2 仿真结果及载荷输出
根据动力学仿真分析的结果,在载荷的作用点设置坐标标记以获得作用点的载荷值。在仿真中对悬置系统的28中工况进行了分析。得到变速器悬置支架各工况(通用汽车公司规定的28种工况)的载荷数据如表4。
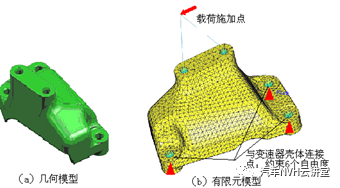
表4 变速器悬置支架在各种工况下的载荷数据
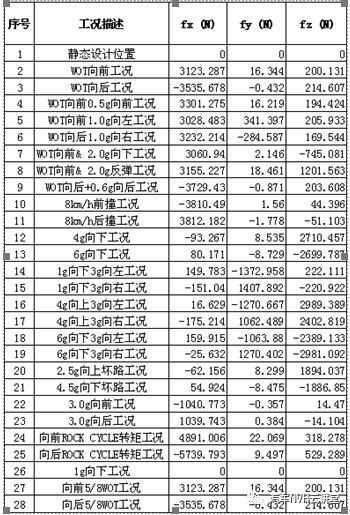
2 悬置支架有限元分析及拓扑优化
2.1 悬置支架的概念设计及有限元建模
变速器悬置支架原设计几何结构(见图3),几何模型由球墨铸铁直接铸造成型。该支架主要承受来自发动机的垂直载荷。此外,在车辆的行驶过程中还承受由于前撞、后撞和转矩工况等引起的前后方向载荷。本文将对此支架在行驶过程中受到的28种不同工况进行应力和模态分析,确保其所有工况条件下所受应力不大于200MPa,一阶模态大于600HZ。
变速器悬置支架的有限元模型及边界条件见图3,有限元模型采用线性四面体网格,节点数为19968,单元数为11039。杨氏模量、泊松比、和材料的密度分别为:E=1.70GPa、μ=0.3、ρ=7.35g/cm3 。
与变速器连接的三个孔采用固定约束。加载点与零件之间使用刚性单元(REB2)连接,以模拟悬置安装的真实位置,载荷点为发动机悬置硬点位置,载荷见表4。
2.2悬置支架概念模型预分析。
对变速器悬置支架进行有限元计算,初步了解悬置支架的应力、变形的分布特点。得到各种工况下支架的所受应力情况如表5。由计算结果可以得知,最大应力出现在4g向上3g向右工况,该工况的应力分布云图见图4。从云图上看,大部分区域所受的应力很小(深黑色区域),可以通过改变悬置支架的结构,提高支架的应力水平,使材料的利用率得到提高,同时降低变速器悬置支架的质量。

2.3 悬置支架概念模型结构拓扑优化过程
一般情况下,在进行结构拓扑优化前,首先要根据要求设计结构特点定义结构的初始区域,然后根据结构所要满足的功能选择合适的目标函数。目前结构拓扑优化的目标函数一般是结构的变形能、模态频率和由两者共同组成的多目标函数。
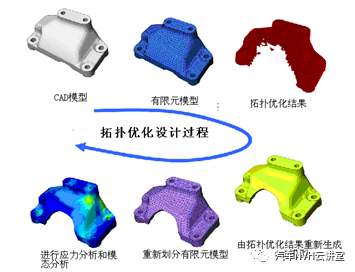
3 悬置支架拓扑优化结果分析
3.1力学指标分析
为了对优化后的设计方案与原设计方案进行全面的比较,需对各种工况条件下的应力和模态进行对比。对拓扑优化结果重新生成的CAD模型重新划分有限元模型见图6。与变速器连接的三个孔采用全约束。加载点与零件之间使用刚性单元(REB2)连接,以模拟悬置安装的真实位置,载荷点为发动机悬置硬点位置,载荷见表4.
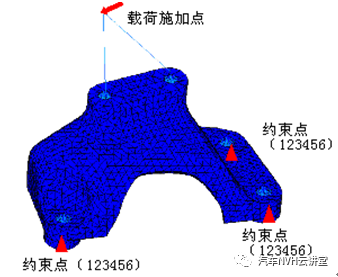
对拓扑优化后变速器悬置支架进行有限元分析计算,得到各工况下的最大应力,并与原方案的应力分析结果进行比较,可以发现原来应力大的工况最大应力有所下降,而原来最大应力小的工况,所受最大应力有所提高,使得应力的分布更趋合理,如表5所示。同时对前三阶模态的频率进行了比较(见表6),拓扑优化后的支架第一和第二阶模态频率虽然稍有降低,但还是远远大于600HZ,完全能够满足设计要求。
表5原方案与优化方案应力分析结果比较
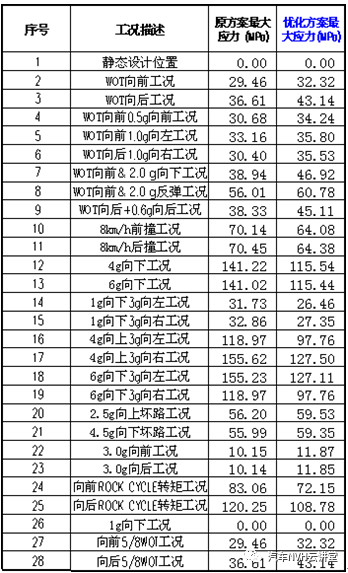
表6原方案与优化方案模态分析结果比较
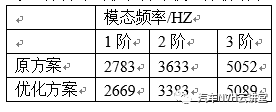
3.2 轻量化指标分析
对拓扑优化前后的质量进行比较,原方案零件质量为1.396kg,优化方案零件质量为1.27kg,重量降低率为9.4%。可见拓扑优化设计对结构轻量化的效果是很明显的。拓扑优化结果见图7。
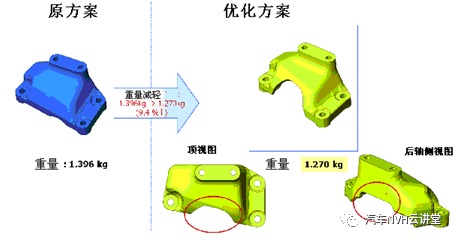
3.3 试验验证
优化后的方案进行了零件的制造和海南试验场38000公里的整车耐久性试验,没有出现试验故障,证明了上述优化方案的可靠性。
4 结论
在悬置系统动力学仿真分析的基础上,进行了变速器悬置支架所受应力和模态频率的预分析。结合预分析的实际情况,采用变密度法对零件进行了结构拓扑优化,通过拓扑优化前后的应力分布及模态频率情况的对比。说明了拓扑优化对于变速器悬置的轻量化和力学性能的改善有着显著的效果。本文建立的优化设计方法和设计思路也可用于汽车上其他零部件的设计。
拓扑优化技术这一新兴优化设计方法非常适合于汽车工业中车身整体和单个零件的设计. 尽管有一些困难,但世界范围内的汽车业已有大量成功应用的案例,专门的拓扑优化软件现也已相对成熟. 目前国内汽车工业的相关研究和应用还不多,因此需要加强这一方面的研究工作,推广拓扑优化技术的使用,从而促进汽车设计水平与国际接轨。
最新资讯
-
全球首次!IVISTA 2023版修订版引入带灯光
2025-04-28 09:59
-
我国首批5G毫米波行业标准送审稿审查通过
2025-04-28 08:56
-
5/16 厦门- 新能源汽车电驱测试技术的创新
2025-04-28 08:53
-
国内首个汽车电磁防护技术验证体系EMTA正式
2025-04-28 08:49
-
一文带你了解滤波器
2025-04-28 08:35