高强钢材料车身轻量化研究
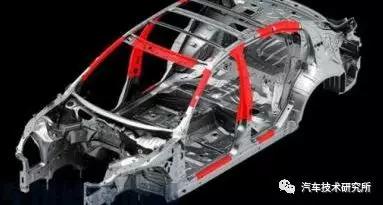
本文以某高强钢材料车身模型为研究对象,结合国内外高强钢材料应用现状,制定白车身高强钢材料方案,同时对车身部件进行料厚优化、安全性分析、冲压工艺研究,探究高强钢材料在车身轻量化应用中的若干问题。
2 基于车身安全的高强钢材料方案
高强钢材料车身的轻量化技术路线主要是通过提升车身钢板的强度和塑性,配合先进成型与连接工艺,在保证性能(主要是安全性能、结构性能)的前提下,减薄车身部件料厚,进而实现减重。
2.1 高强钢材料分类
目前,高强钢材料主要有两种分类方式:按照材料强度分类,普通高强钢屈服强度一般为210~550 MPa,先进高强钢抗拉强度一般为500~1 500 MPa;按照钢中的金相组织和冶金类型分类,欧洲车身会议按照此方法分类,并有相应的车身材料配色标准,如表1所示。
2.2 基于安全理念的高强钢材料应用
安全性是车身最重要的性能,各大汽车集团有各自的安全设计理念和方案,但主要遵循的设计原则均为“前、后碰撞区变形吸能+乘员舱高强度”(见图1),即车身前、后区域既要能吸收碰撞能量,又要将剩余能量进行分流和传导,减少对乘员的冲击力,而乘员舱要保持高强度,在碰撞时将变形控制在有限范围内,保证乘员生存空间[3]。
表1 按照冶金类型分类的车身钢种类别
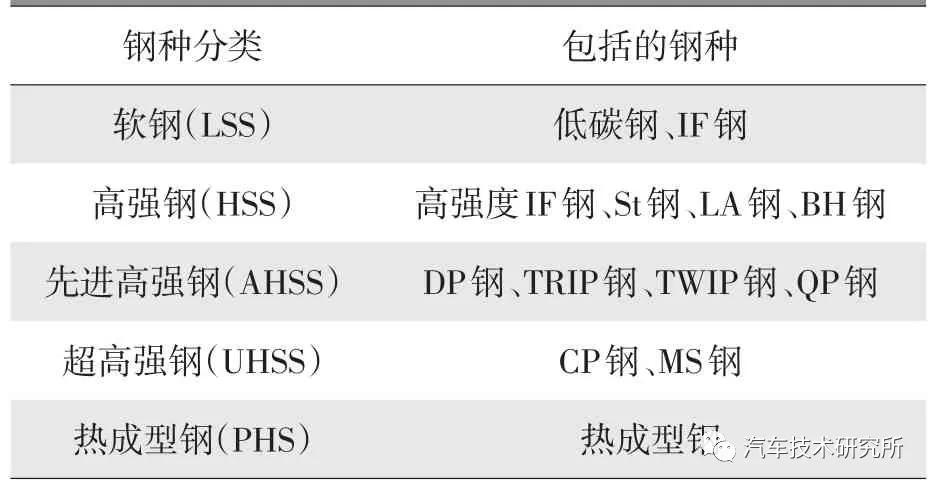
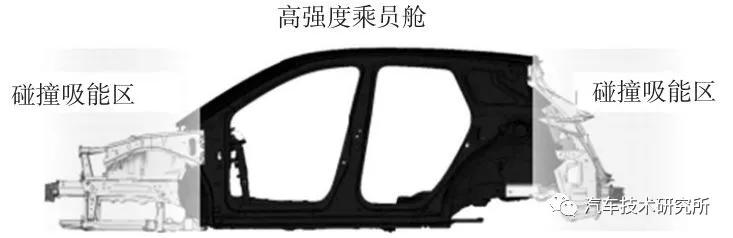
高强钢兼具高强度和良好的塑性,有利于碰撞过程中的能量吸收,在保证安全的前提下,能够最大程度实现轻量化。不可否认的是,热成型钢应用的比例越来越高,在第三代高强钢冷冲压应用技术全面突破前,热成型钢仍是车身安全用材的主流趋势,并衍生出补丁板热成型、拼焊板热成型、差厚板热成型、分段强化热成型等多种新技术,进一步实现轻量化。图2所示为沃尔沃车型热成型钢用量统计,其新一代车型热成型钢应用比例均在30%以上,许多自主车型也逐渐加大热成型钢应用量。
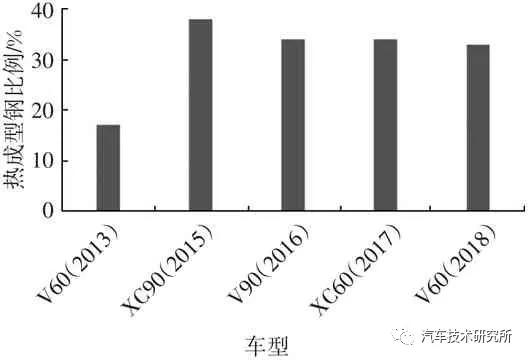
高强度钢与普通钢板相比,泊松比和弹性模量几乎一致,进行等强度设计时保持结构形式一致,仅将部件料厚进行等效计算。等效替代后的部件料厚可大致确定为:

式中,t1、t2分别为等强度替换前、后的部件厚度;σs1、σs2分别为等强度替换前、后部件材料的屈服强度。
安全性是后续材料方案制定、料厚优化等工作的前提。
2.3 高强钢车身材料方案
通过分析自身情况、车型定位以及对标分析,本文在某轿车白车身模型基础上,提出一种较为前瞻的高强钢车身材料方案,如图3所示。
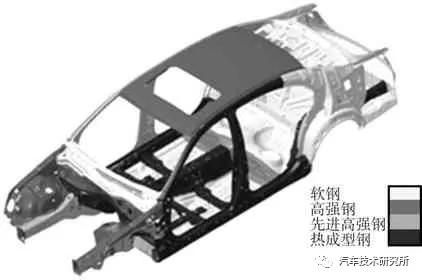
该车身材料方案制定遵循以下指导性原则:
a.乘员舱重点考虑安全性,在门环、地板横梁、中通道、前围挡板等处采用热成型钢,控制乘员舱侵入量,保证驾乘人员安全。
b.碰撞吸能区既要有的良好塑性以保证碰撞能量吸收,又要有一定的刚度来传递碰撞冲击力。前纵梁采用先进高强钢,前悬支撑座采用高强钢,后纵梁根据强度要求,可采用先进高强钢或者热成型钢。
c.结构框架/节点重点考虑结构刚度,地板连接梁、顶梁、侧围加强板和搭接结构等选择成本适中的高强钢或先进高强钢,采用合理的结构和料厚,提升车身框架刚度。
d.钣金件综合考虑性能、成本、工艺性、NVH性能等,前地板、顶盖选择软钢或高强钢,中/后地板、前围内板、流水槽、轮罩内外板、侧围外板等选择成型性好的软钢。
应当说明的是,该方案为高强钢车身用材的指导性原则,具体车型开发时,应结合车型级别、目标成本、性能要求、生产资源、平台化战略等诸多条件平衡,进行具体材料选择。材料选择后还要结合结构设计、CAE仿真优化,才能最大化发挥材料的轻量化潜力。
3 基于车身灵敏度的高强钢料厚优化
长期以来,高强钢“高强、减薄”这一轻量化技术路线较为明确,但车身是一个庞大的系统,减薄位置、减薄程度、料厚变化对车身性能的影响等问题尚未清晰。
3.1 白车身有限元模型建立
在前处理软件中完成白车身的有限元建模,车身材料见图3,各零部件初始厚度为原型车相应零部件的厚度,白车身模型信息如表2所示。
表2 白车身网格模型
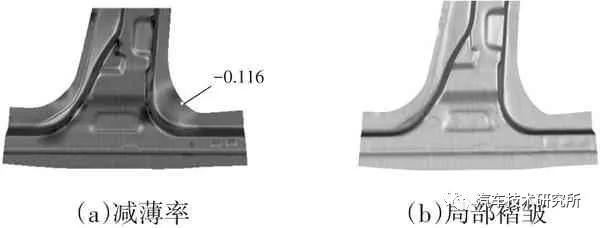
3.2 车身灵敏度分析
3.2.1 原型车性能分析
车身模态、刚度等是评价车身性能的重要指标。经计算,料厚优化前原白车身模型的模态、弯曲刚度、扭转刚度如表3所示,振型如图4所示。
表3 白车身性能计算结果
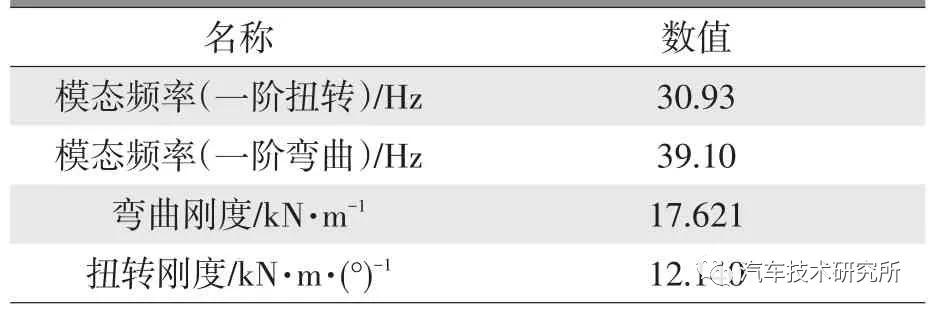
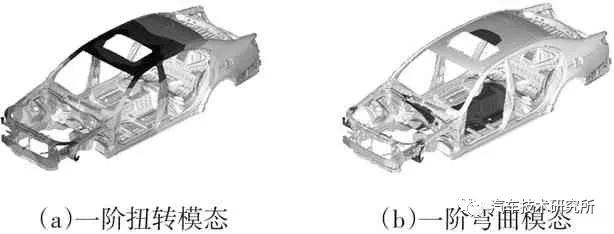
3.2.2 车身灵敏度计算模型建立
3.2.2.1 建立设计变量
根据筛选原则,选择88对(个)可变厚度的部件料厚作为设计变量,控制料厚变化范围为±20%以内,以不影响装配。其中前15个质量灵敏度较大的变量如表4所示。
表4 白车身钣金设计变量
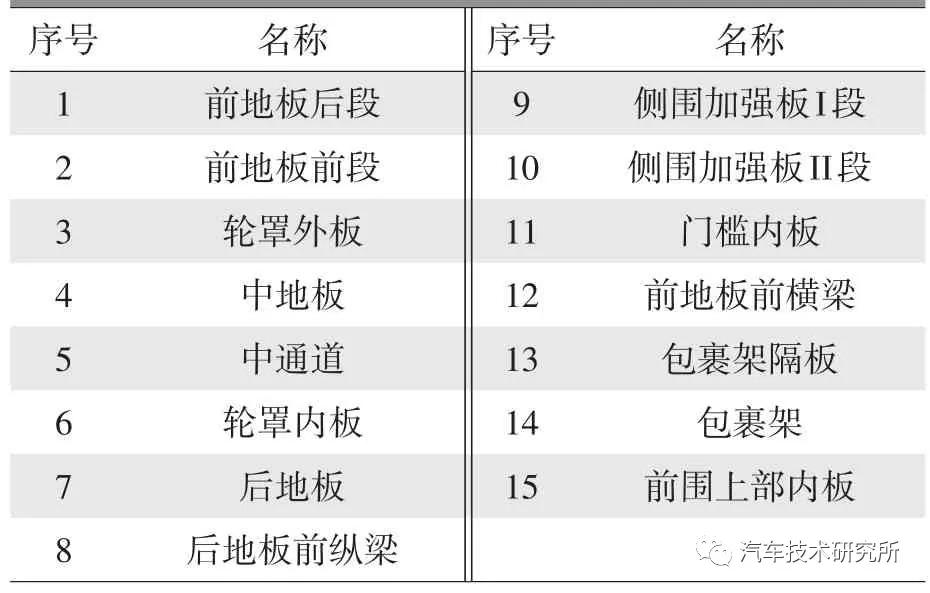
3.2.2.2 设定约束条件
优化后整车性能应不低于或稍高于目前水平,设定模态频率(一阶扭转)不小于31 Hz,模态频率(一阶弯曲)不小于39 Hz,弯曲刚度不小于17 kN/m,扭转刚度不小于12.5 kN·m/(°)。
3.2.2.3 优化目标
优化目标为白车身质量最小。
3.2.3 车身灵敏度计算模型求解
本文应用OptiStruct软件进行灵敏度计算。软件采用最小步长迭代法,是目前工程上通用、稳定、快速的求解方法[4]。该白车身灵敏度计算模型求解后得到如下结论:对模态频率(一阶扭转)影响较大的前5个零件是侧围加强板I段、前围上部内板、前围上部内板加强板、前围挡板、侧围加强板II段,见图5;对弯曲刚度影响较大的前5个零件依次是轮罩内板、轮罩外板、门槛内板、前围上部内板、门槛外板,见图6;对扭转刚度影响较大的前5个零件依次是顶盖外板、侧围内板I段、前围上部内板、前围挡板、轮罩外板,见图7。
3.2.4 车身料厚优化结果
根据灵敏度计算结果、式(1)和常用板材供货规格等条件,对88对(个)变量料厚重新赋值并计算,结果如表5所示。在保证车身模态、刚度稍有提升的前提下,仅靠料厚减薄实现降重11.7 kg,降重3.4%,白车身平均料厚下降0.04 mm。若各部件配合相应的轻量化结构设计和先进制造工艺,轻量化潜力更大。
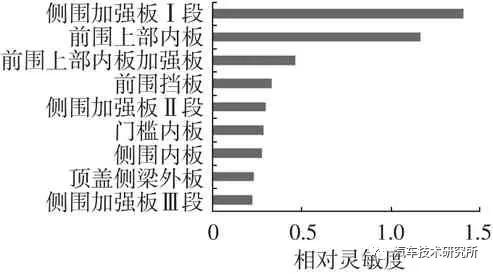
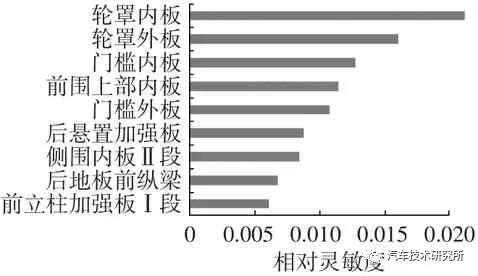
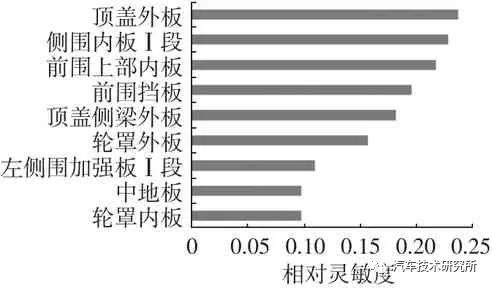
表5 优化前后结果对比
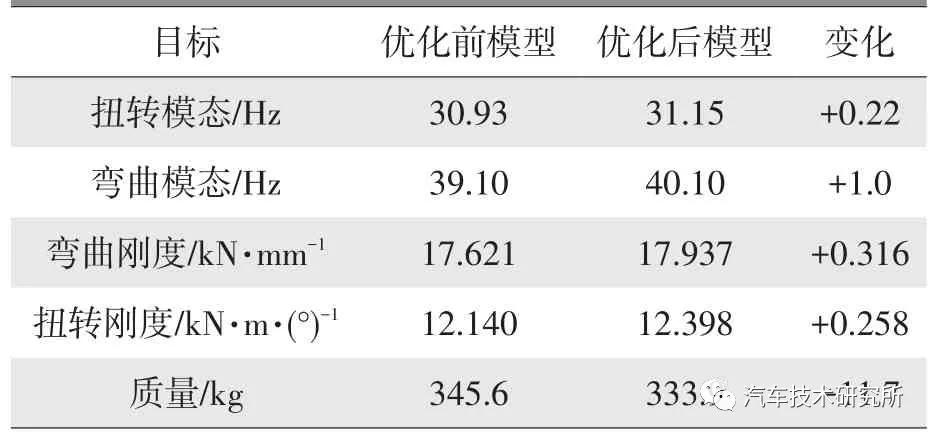
4 安全性能验证
B柱是汽车侧碰中重要的承载部件,也是车身材料应用强度最高的位置之一,目前,热成型方案是比较主流的应用方案。本文以B柱为例,对料厚优化结果进行安全性能验证。
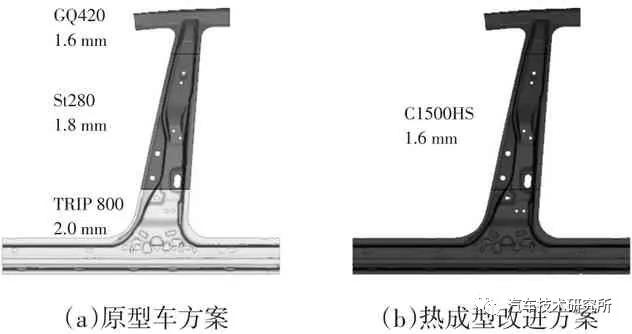
表6 高强钢材料性能对比
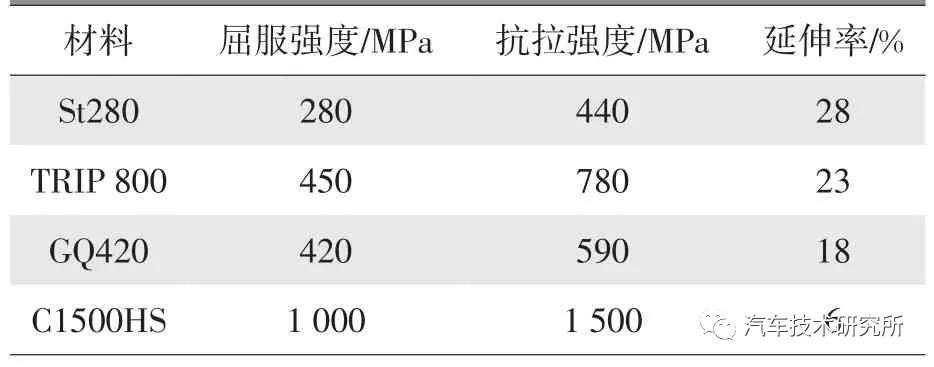
参考C-NCAP标准,采用简化B柱侧碰模型进行计算,对B柱优化前、后方案的安全性能进行对比。侧面壁障的移动速度为50 km/h,模拟碰撞时间为80 ms,B柱侧碰计算模型及失效模式如图9所示,碰撞过程变形区域主要位于B柱底部与门槛交界处。
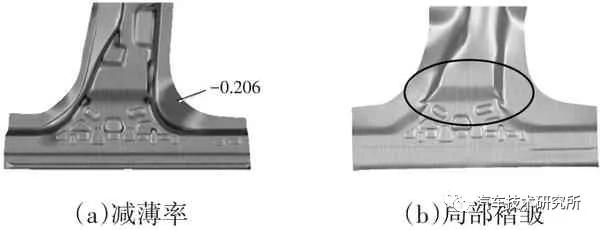
图10 和图11分别为碰撞过程中两种方案的最大侵入量、侵入速度随时间的变化曲线,80 ms内最大侵入量分别为75.2 mm和69.1 mm,最大侵入速度分别为2.4 m/s和2.3 m/s,热成型方案的最大侵入量、最大侵入速度均有所降低。由对比结果可知,采用更高强度级别的钢种,合理减薄料厚,安全性能有一定提升,在轻量化的同时,仍可有效保护乘员安全。
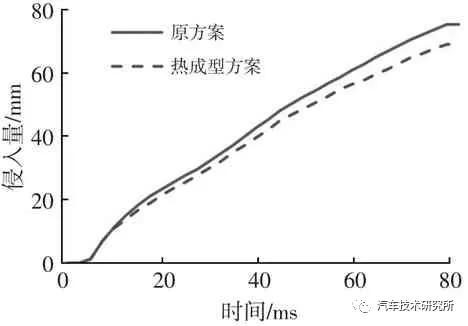
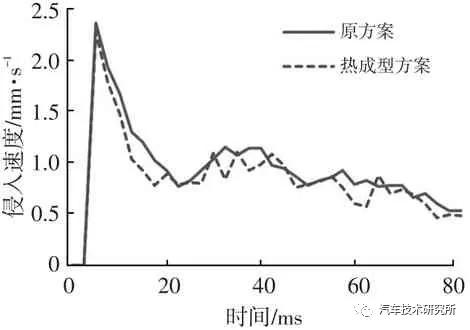
原型车B柱通过热成型方案的实施,料厚降低,性能略有提升,实现降重1.314 kg,若结合补丁板热成型、差厚板热成型等先进工艺,还有更大轻量化空间。
5 成型性能优化
目前,国内外各大钢厂已经开发了800~1 500 MPa的先进高强钢,进一步追求轻量化,但高强、减薄却是限制冲压工艺的两大因素[5]。一方面,高强钢屈服强度提升,成型极限变小,冲压过程易出现起皱、开裂等缺陷;另一方面,冲压过程中产生较大的残余应力和回弹,零部件的几何尺寸不确定性增强。在满足车身强度、刚度、轻量化的条件下,如何保证冲压工艺可行是高强钢应用实践的一大难点。
随着计算机技术的发展和冲压理论的不断完善,可以通过计算机模拟,较为准确地预测零部件在冲压过程中的所有问题,国外在预测冲压件缺陷方面已达到很高精度,并实现产品设计、模具开发的同步。本文以B柱为例,对高强钢材料替换、料厚减薄后的方案进行冲压工艺可行性研究,力求设计方案和成型工艺同步实现。
图12所示为提取的B柱模型冲压分析结果,材料为热成型钢,料厚1.6 mm。若按照原结构进行设计并冲压,由于B柱底部型面复杂,两侧翻边处减薄率达-0.206,有开裂风险,同时,吸皱筋不足,会出现褶皱。
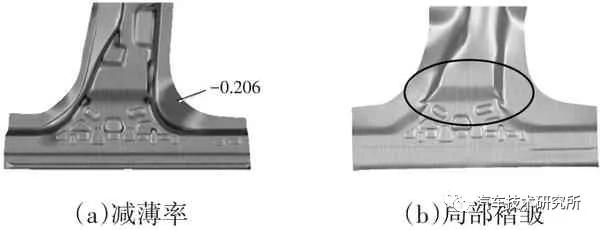
根据热成型工艺特点,采取以下改进方法:采用开放式设计,尽可能采取弯曲成型,减少翻边边产生起皱、减薄以及拉裂的风险;有起皱倾向的区域(如B柱零件底部)应该设置吸皱筋。改进后的结构及成型分析结果如图13所示,成型性良好,无开裂和起皱风险。
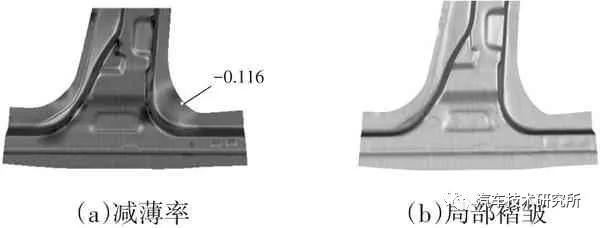
相对于冷冲压,热成型应尽量采取规则的形状,不规则的结构会增加板料定位差,在成型过程中,模具与板料冷却效果差,影响材料流动和淬火冷却,导致强度分布不均。
工程实践证明,成型性优化涉及的结构改动多为微调,不涉及大的结构断面调整,对零件整体的安全性能的影响极为有限,可以认为前文的安全性能分析仍然有效。
6 结论
高强钢的应用主要考虑车辆的安全性能,其中,热成型是目前技术条件下,基于车身安全的材料首选。通过灵敏度分析,可优化车身各部件的料厚,实现材料和结构的合理化匹配,尽可能实现车身轻量化。通过安全性分析,可以验证采用更高强度级别的钢种,在轻量化的同时,仍可有效保护乘员安全。通过冲压工艺分析,可预测高强钢冲压成型的可行性,使得设计方案和工艺同步实现。
编辑推荐
最新资讯
-
奇石乐推出用于DAQ数据采集系统的KiStudio
2025-04-28 17:51
-
全球首次!IVISTA 2023版修订版引入带灯光
2025-04-28 09:59
-
我国首批5G毫米波行业标准送审稿审查通过
2025-04-28 08:56
-
5/16 厦门- 新能源汽车电驱测试技术的创新
2025-04-28 08:53
-
国内首个汽车电磁防护技术验证体系EMTA正式
2025-04-28 08:49