Mahle augments its RDE test capabilities
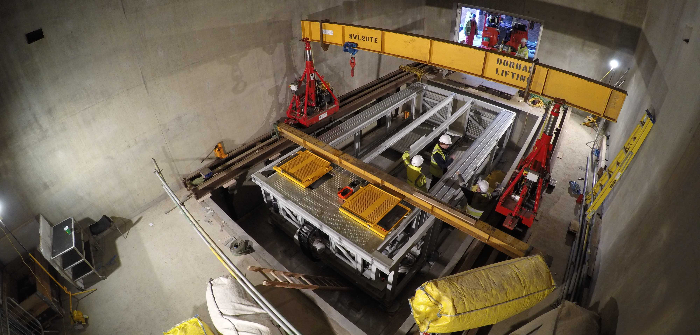
The first chamber housed inside Mahle’s new state-of-the-art, Real Driving Emissions test center in Northampton, UK is nearing completion.
At a cost of around £8m (US$11.2m), the cutting-edge facility is said to be the first of its kind in the UK, enabling simulation of altitudes up to 5,000m as well as extreme temperature and humidity. Such a capability will enable OEMs to eliminate traditional, expensive field trips from their programs.
Weiss altitude and environmental simulation equipment was successfully installed and the company has also now taken delivery of the Horiba 4WD chassis dynamometer.
Construction began in May 2017 and is on track to be completed by June this year.
“We’ve built on a car park adjacent to the existing facility and it’s all been knocked into one area. This will enable the new and old facilities to share the warm soak area and any other equipment that is needed,” explains Derek Wise, chief engineer, build and test, at Mahle Powertrain.
To put in the foundations for the chamber, workers had to pile down to around 20m. “The area used to be an old slag heap for a power station, which meant the soil contained a lot of heavy metal contamination.
“This has been the biggest challenge for us during the construction process – the soil had to be removed and carefully processed to clean it up.”
The facility measures 1,550m², including two test chambers, 50m² of office space, six meeting rooms, and a large reception area.
The new Horiba Vulcan II XtraCold 4WD chassis dyno will enable analysis of vehicles weighing up to 5 tonnes, with a power rating of up to 450kW and speeds of up to 190km/h.
The Weiss system meanwhile comprises three core functions including: a circulatory air conditioning unit which controls air temperature, humidity, and distribution inside the test chamber; a refrigeration system to reduce air temperature; and a blower system.
Within the latter is an exhaust blower to evacuate air from the test cell to simulate low air pressure at altitude, and an outer air blower, which can pressurize the facility to a maximum of 1,050mbar (abs).
Altitudes of up to 5,000m can be replicated by reducing the air pressure in the whole chamber to approximately 50% of standard sea level air pressure.
Temperatures of between -40°C to +60°C can also be simulated, as well as a humidity range of 10-80% relative humidity, with an air circulation capability of 70,000m³/hr.
To withstand the semi-vacuum conditions, the facility walls are made of 500mm thick reinforced concrete. The vehicles will enter via a reinforced steel door, which weighs 3.5 tonnes. The test cell will also have an airlock system that allows personnel to enter and leave the facility without having to return to atmospheric pressure.
Now, with the implementation of the new RDE center, engineers will be able to use the Mahle Vehicle Certification Agency approved RDE test routes to their full potential as well as simulating them in the chamber.
Plans are to begin purchasing systems for the second test chamber within the next two years. “once the first one is up and running, we will then look at equipping the second. In future, we may also look at converting one of the older facilities for other purposes,” Wise notes.
More generally, the company is working to increase the amount of simulation conducted in order to speed up development cycles, as Wise comments, “When testing for RDE there are a lot of extra parameters. We’re going through the process on the production program at the moment and it’s added cost and time. The OEMs are only just coming to terms with that and simulation is helping reduce the permutations.”
编辑推荐
最新资讯
-
奇石乐推出用于DAQ数据采集系统的KiStudio
2025-04-28 17:51
-
全球首次!IVISTA 2023版修订版引入带灯光
2025-04-28 09:59
-
我国首批5G毫米波行业标准送审稿审查通过
2025-04-28 08:56
-
5/16 厦门- 新能源汽车电驱测试技术的创新
2025-04-28 08:53
-
国内首个汽车电磁防护技术验证体系EMTA正式
2025-04-28 08:49