ISG双电机PHEV混合动力系统匹配
ISG双电机架构PHEV系统结构和原理如图1 所示。该系统架构有两条能量传递路径:第一条路径(L1)是1-2-4-3,主要通过电能实现能量传递,实际上是一种APU(Auxiliary Power Unit)架构驱动模式[1];第二条路径(L2)是1-2-3,是通过离合结合实现机械传递发动机直驱。这两条路径通过一定的控制逻辑关联,最终可以实现PHEV串、并联驱动模式的切换。

表1为ISG双电机架构PHEV系统不同运行工况各系统参与工作情况。
概括地讲,ISG双电机架构PHEV混合动力系统工作基本逻辑是:低速或市区工况采用串联纯电驱动模式,中、高速工况时机械驱动介入,高速等速巡航时采取发动机直驱为主。
下面以某款MPV混合动力车辆设计为例,通过系统对比来论证这种系统架构的基本特点。
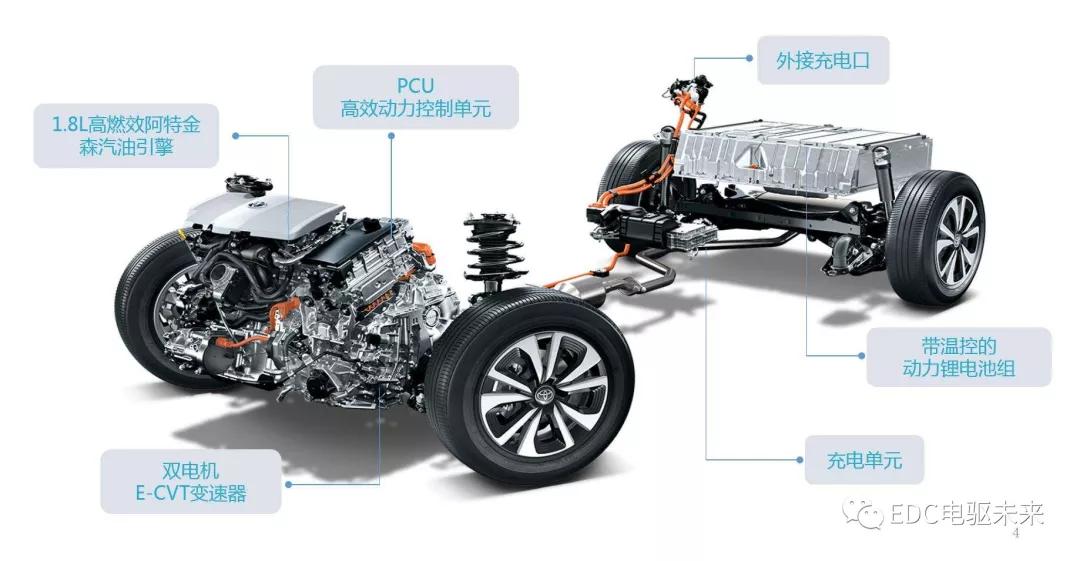
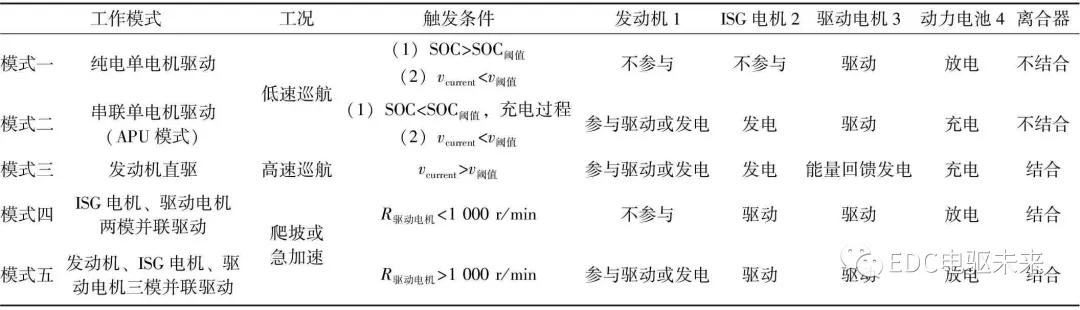
2 动力系统参数设计
整车及设计目标参数见表2。
表2 整车及设计目标参数
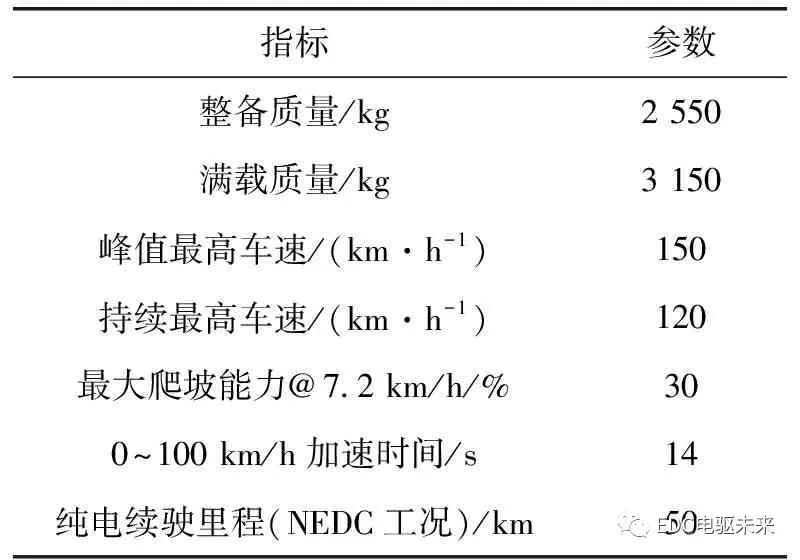
(1)驱动电机峰值功率
驱动电机峰值功率的设计,需要考虑表1中各工况的整车实际运行功率的需要。由于并联驱动时ISG系统需要直接为整车提供驱动功率参与驱动整车运行,因此,驱动电机峰值功率首先要由NEDC工况纯电或串联驱动模式下对驱动电机的需求功率决定。
由公式(1)[2]

可求得NEDC工况纯电驱动模式整车对驱动电机的峰值功率需求为68 kW。其中NDEC工况各速段驱动电机峰值功率需求如图2所示。
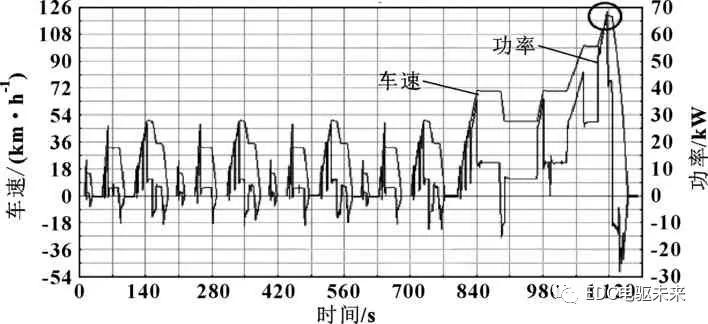
(2)驱动电机额定功率
根据电机特性,取功率因子eP=Pt/Pe=0.6,则与上述峰值功率相对应的电机额定功率为:Pt=68×0.6=40.8 kW。
(3)根据永磁电机特性,取电机峰值扭矩、峰值功率拐点转速1 000 r/min,已知电机峰值功率68 kW,由式(2)得拐点转速时电机峰值扭矩650 N·m。驱动电机特性见图3。
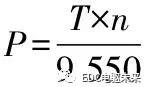
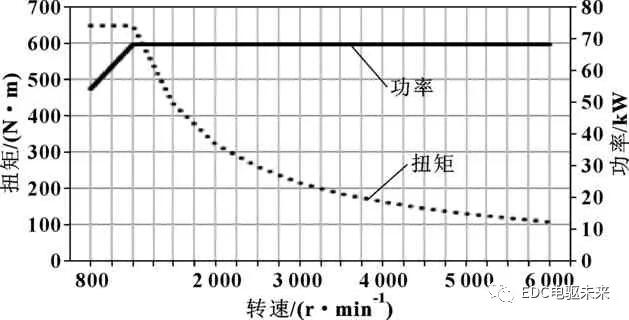
2.2 系统速比的初步确定
(1)整车以120 km/h等速巡航模式持续运行时,发动机以直驱方式参与整车驱动,可以减少能量的二次转化和实现系统功率应用的最大化。考虑到系统NVH因素,定义此时系统最高需求转速不高于3 500 r/min,则变速器速比应不高于:


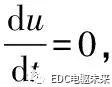
(3)

式中:ig为变速器速比;i0为主减速器速比;i为坡度,取i=0.2;
根据求得的轮边驱动扭矩3 440 N·m、电机峰值扭矩650 N·m,可求得系统总变速需求应不低于5.3。
综上,初步考虑为系统提供两速比AMT方案,两级速比分别为:3.74,5.3。
2.3 动力电池电量需求计算
已知:续驶里程按半载NEDC计算;SOC放电深度按100%~20%计算;电机平均效率:EPT系统95%。借助Cruise系统建模仿真不难得出, NEDC工况能耗率:27.4 kW·h/100 km,若按50 km续驶里程计算,所需工作电量为50/100×27.4=13.7 kW·h,按放电深度80%考虑,动力电池的最大荷电量需求为13.7/(1-20%)≈18 kW·h。
2.4 ISG系统功率需求
整车对ISG系统的需求,主要考虑其功率输出。表3列出了在考虑系统传递效率的条件下,混合动力各极限功率工况功率总需求及各工况条件下对系统的最小功率需求。
表3 各运行工况基本功率需求
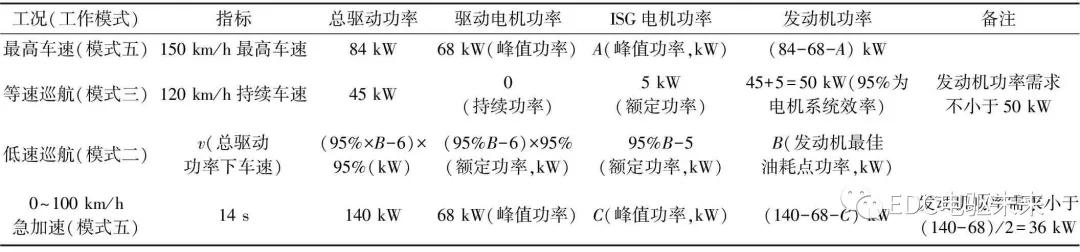
上述,采纳模式三120 km/h持续巡航,发动机对应转速3 500 r/min条件下发动机输出功率需达到50 kW,此时处于发动机直驱模式。
2.5 发动机选型
为规避由于发动机工作转速过高可能引起的系统过疲劳和NVH风险,初步确定工作转速为3 500 r/min、功率为50 kW的发动机为理想的发动机。
2.6 ISG电机功率的确定
图4为根据架构布置初选的PHEV系统发动机万有特性。可以看出:在相对经济的油耗-功率线上,发动机转速4 000 r/min以下最大峰值功率可达55 kW,基本满足整车120 km/h持续巡航的功率需求。
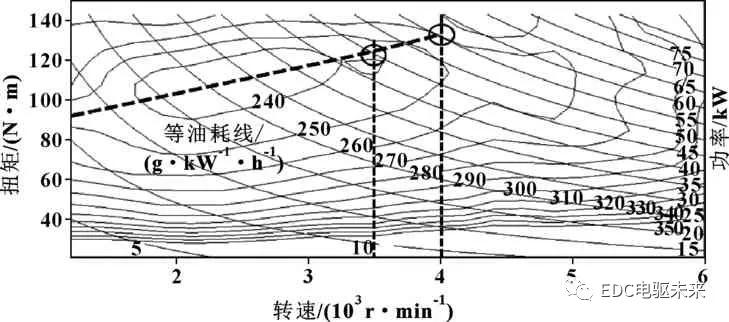
结合发动机特性,v′=100 km/h时,发动机转速2 918 r/min,此时发动机功率36 kW,不难求得急加速工况下ISG电机峰值C′=140-68-36=36 kW。相应地ISG电机额定功率为36×60%=21.6 kW。
2.7 动力系统匹配的结果
动力系统匹配结果如表4所示。
表4 动力系统匹配结果
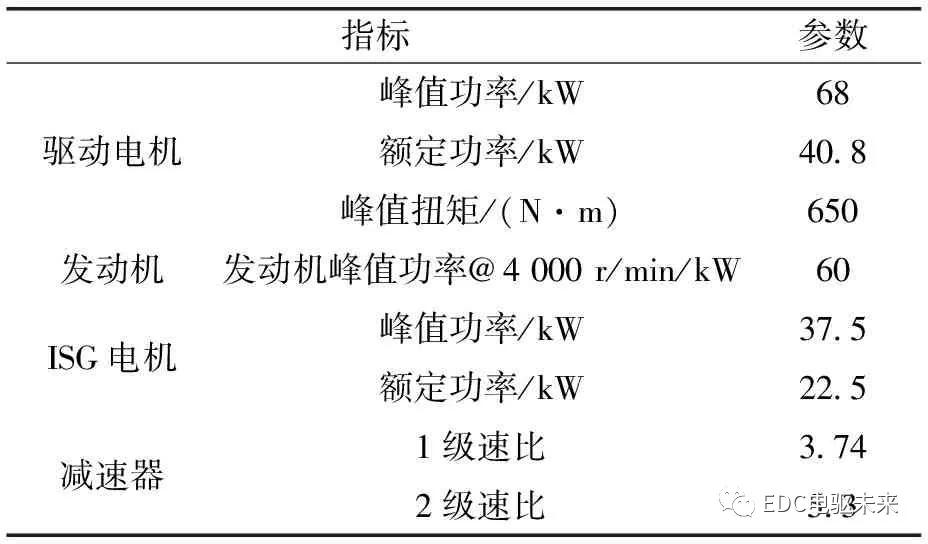
由于PHEV系统的匹配主要围绕高速工况时降低能耗为出发点展开,其着眼点在于通过离合结合实现发动机直驱以减少能量二次转化效率低的问题。
3.1 系统工作模式定义
(1)为最大限度减少油电二次转换带来的效率损失,设定系统工作过程中电池荷电量(SOC)变化范围为30%~40%。当SOC<30%时,启动发动机以串联或直驱模式驱动车辆并将动力电池充电至40% soc="">40%时,在需求功率充足的条件下关闭发动机以纯电模式放电至30% SOC。图5中数据已通过效率折算等效发动机输出功率为整车需求功率,并均考虑计入了整车附件功率和系统损耗。可看出:当发动机转速低于3 250 r/min时,串联模式整车功率需求曲线较发动机直驱时整车功率需求曲线更靠近发动机工作最佳经济区,高于3 250 r/min时反之。据此得出两种驱动模式切换阈值v阈值=110 km/h。
(2)在油耗性能最大化前提下,为避免发动机转速过高引起NVH问题,取巡航车速120 km/h所对应的发动机转速3 760 r/min作为发动机直驱模式下发动机转速的上限(实践中,如果发动机外特性好,可以进一步降低上限转速)。而在整车从120 km/h至150 km/h最高车速急加速过程中,为保证高速段较好的加速性能,可以设定临界转速为4 500 r/min、整车车速为140 km/h时离合器再脱开,使得当发动机转速达到4 500 r/min时ISG系统和动力电池以并联纯电功率输入的方式为驱动电机提供功率驱动车辆运行。
(3)急加速和爬坡、坡起工况时,离合结合,ISG电机和驱动电机同时提供扭矩驱动车辆运行。当电机转速高于1 000 r/min时,此时发动机转速已被ISG电机拖动到怠速转速以上,开始参与急加速和爬坡、坡起工况扭矩的输出。
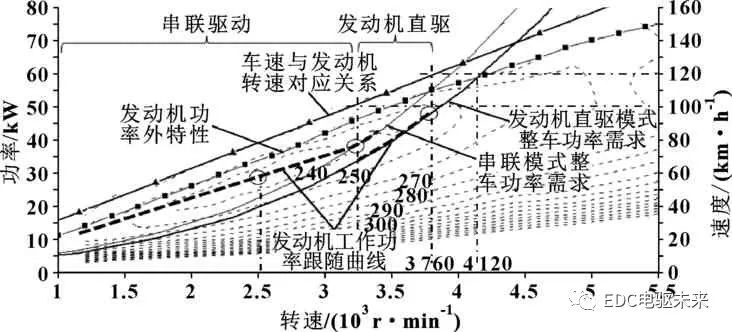
3.2 系统建模
根据发动机外特性,在输出功率充分条件下,当系统以串联模式工作时可采用发动机定转速以2 500 r/min工作从而实现经济性的最大化。而当整车需求功率较大时,发动机工况点以功率伴随方式沿经济曲线上移,直至发动机以直驱模式工作。
应用MATLAB/Simulink建立一个Demo(如图6—图7所示)使发动机始终以相对经济的工况运行,并通过AVL.Cruise自带的策略控制模块进行设定实现上述设计构想。发动机运行工况控制是由整车需求功率通过查表法求得对应发动机转速,通过油门开度来控制。Demo文件通过Cruise接口程序转换为.dll文件,最终代入图8的 Cruise程序模型进行整车性能计算。
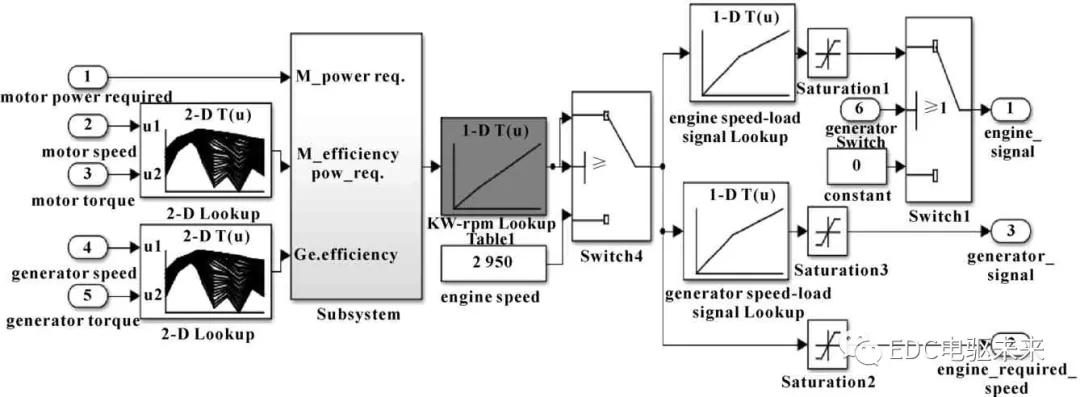
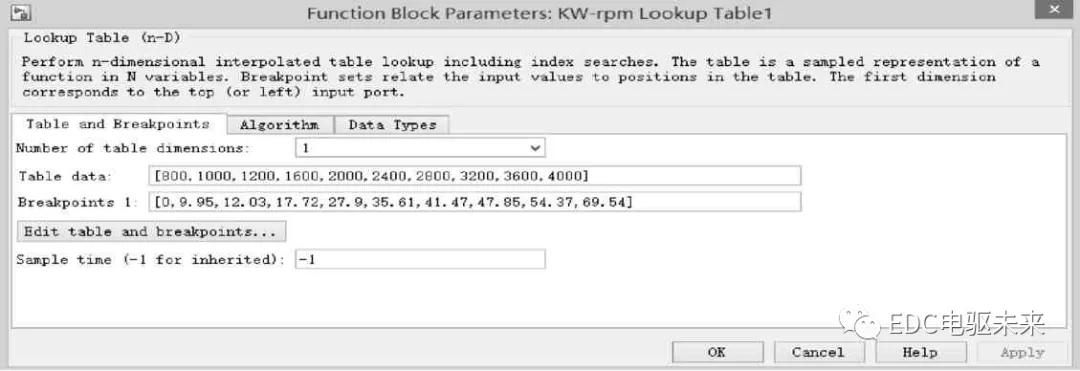
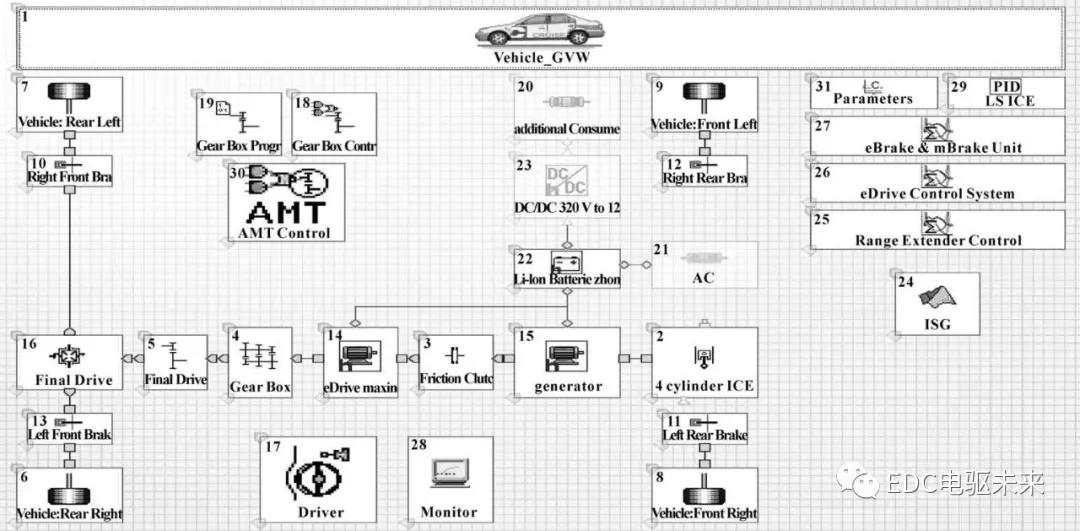
3.3 仿真结果分析
将各系统参数代入上述模型,根据表1定义设定系统工作模式,结合系统架构确定能量回收策略为制动踏板非解耦设计。通过仿真得出结果见表5,满足设定目标。
表5 仿真结果

3.3.1 NEDC工况发动机工作时间分布
从图9可看出:在整个NEDC工况运行过程中,发动机始终工作在经济油耗区。
表6为同款车型ISG架构PHEV混合动力与发动机直驱内燃机车辆燃油消耗率的对比。
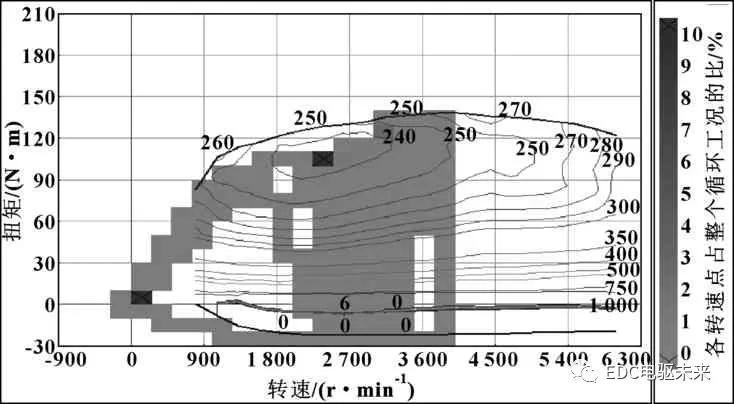
表6 同款车型ISG架构PHEV混合动力与发动机直驱车辆燃油消耗率对比L·10-2·km-1
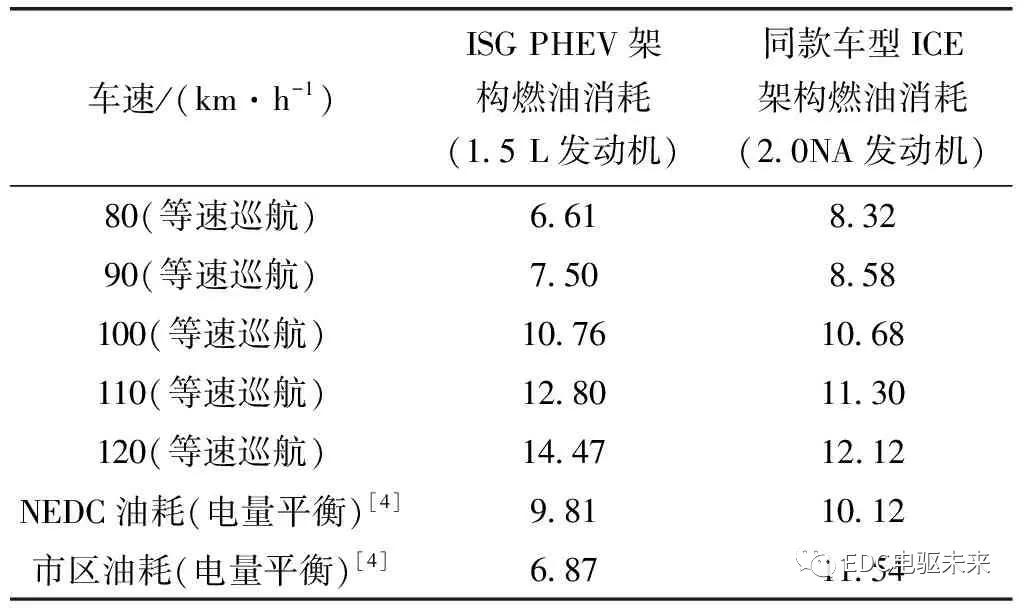
(1)110 km/h及以下时ISG串架构较省油。110 km/h以上时速时尽管ISG架构也为发动机直驱,如果ISG架构所选用发动机排量小,高功率输出时将偏离油耗经济区,导致油耗偏高。
(2)市区工况,ISG架构PHEV系统整车油耗仅为传统发动机直驱内燃机车辆燃油消耗率的59.5%,系统节油率40.5%。
3.3.2 最大爬坡度及整车急加速工况仿真结果
图10为整车最大爬坡度仿真结果,图11为整车急加速工况仿真结果。
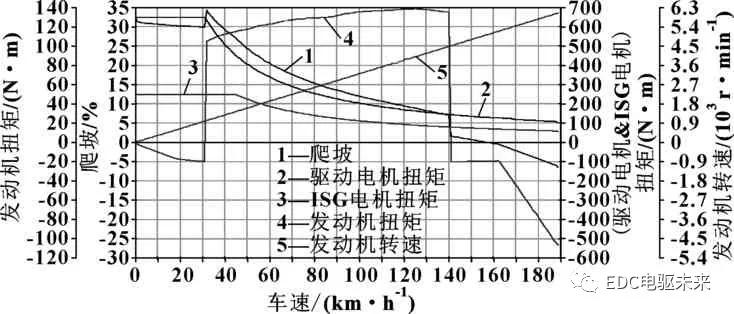
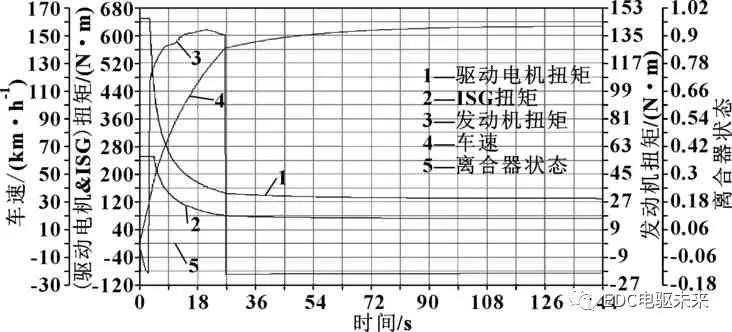
从图10、图11可以看出:低车速时ISG电机以驱动电机方式参与工作,同时反拖发动机运转,此时发动机对整个系统以负扭矩输出;当电机转速达到和高于1 000 r/min时,发动机开始参与扭矩输出,此时整车爬坡、坡起能力和整车最大加速能力达到最大值(仿真结果见表5)。
4 结论
(1)ISG双电机架构PHEV混合动力系统匹配的重点,是结合整车运行工况,根据选定系统尤其是发动机系统的特性,合理设定各串并联驱动模式的切换工况,预设好临界阈值。
(2)ISG双电机架构属于混联式混合动力的一种[5],其完美地实现了混联混合动力系统所具备的所有特性,与单一APU架构系统相比大大地扩展了经济工况下巡航车速。由于该类架构系统具有两个电机并且ISG电机与驱动电机通过离合器硬连接,项目实践中可能对系统布置空间造成较大的压力,造成只能选用有限排量的发动机,导致高速巡航段油耗偏离经济油耗区,致使油耗偏高。这一点需要在项目预研前期做好规划。
(3)ISG双电机架构PHEV混合动力系统相对传统发动机直驱内燃机车辆,综合经济性能突出。因其同时具备APU怠速发电和相对高速时发动机并联直驱的特性,既照顾了客户的实际需要,又优化了燃油的经济性。该架构形式具有较高的实用价值。
- 下一篇:中国汽研检测事业部下属的安全中心引入家THOR假人
- 上一篇:排放法规概述
编辑推荐
最新资讯
-
大卓智能端到端直播实测,16公里复杂路段挑
2025-04-25 17:16
-
《汽车轮胎耐撞击性能试验方法-车辆法》等
2025-04-25 11:45
-
“真实”而精确的能量流测试:电动汽车能效
2025-04-25 11:44
-
GRAS助力中国高校科研升级
2025-04-25 10:25
-
梅赛德斯-AMG使用VI-CarRealTime开发其控制
2025-04-25 10:21