如何通过仿真优化电动汽车的电能消耗
随着智能电动车的普及,运行中的车辆对电的消耗更增。制造商需要优化电动汽车的能源消耗,保证行驶里程。一种方法是通过减少车身和装饰来减轻整体重量。ARRK通过采取不同的方法,节省了30%的质量。是如何做到的呢?
为什么复合材料对电动汽车市场很重要?
车身整体减重是优化电动汽车能耗、减少运营消耗的关键。可以通过多种措施使结构、车身和内饰降低总量,但研发人员很少针对动力总成减重。
在ARRK,我们致力于减轻动力总成的重量。我们研究了用低密度材料代替铝外壳材料来优化典型的两级电传动的重量。碳纤维增强热塑性材料提供了机械性能和快速制造工艺的良好组合,但要达到齿轮箱的耐久性和声学预期所需的刚度(尤其是在高于100°C的温度下),对复合材料来说是一项挑战。
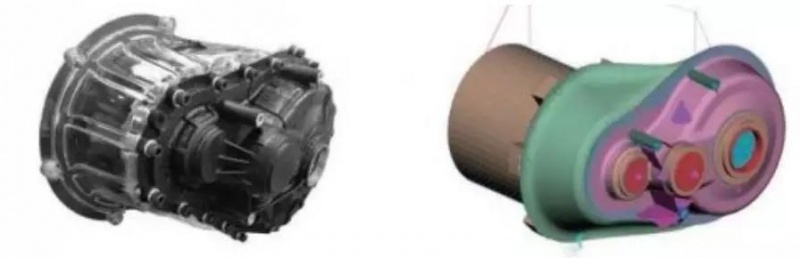
电动汽车动力传动系统面临哪些挑战?
电齿轮箱的功能复杂性比传统变速箱低,因为齿轮的数量现在要低得多。传统车辆有多达7个传动比,而电动车辆只有一到两个。
对电动变速箱来说,最具挑战性的是舱内声环境控制。燃油车的内燃机会淹没变速箱的工作噪音,而现在的电动引擎是静音的。这使得变速箱声学占主导地位,尤其是在低速情况下。变速器本身的声音,通常带有低沉的呜呜声,需要控制以降低乘客的不适。
理想的变速箱,不会因传递的载荷而变形。但在现实中,轴承会发生位移,导致轴上齿轮的运行位置发生变化。用新的外壳材料替换原来的铝变速箱,而维持相同或更好的刚度,这是一个挑战。中间轴和输出轴的轴偏差和轴倾斜误差必须保持在铝壳的同一水平或更低。
ARRK是如何解决这一挑战的?
在本次项目中我们用纤维增强热塑性材料取代了电动变速器的铝外壳材料,不会对内部零件有其他变动。
使用短纤维增强热塑性材料(含短切玻璃纤维的PPA材料)以及复合材料片材(双轴碳纤维织物和聚酰胺热塑性基体)进行过模压。铝嵌件作为轴承座,确保将轴承载荷传递到奥尔加诺板中,并减少齿轮啮合的偏差。附加的注塑肋和单向带保证了刚度要求。
通过ARRK P+Z(德国实体)和ARRK Shapers(法国实体)共同努力,展示了ARRK产品开发小组开发零部件、制造工具、建立生产流程和批量生产的能力。德国实体负责研发,法国实体建立生产流程,搭建工具和样机。
ARRK产品研发由CAE仿真驱动。不同工艺的有限元仿真,复材仿真、冲压仿真,迭代优化至采纳。通过ESI的复合材料制造解决方案,优化后的变速箱重量为4kg,而最初的铝合金的变速箱重量为5.8kg,实现了近30%的减重。ESI帮助ARRK构建性能优于标准铝齿轮箱的复合材料变速箱,大大提升研发能力。
编辑推荐
最新资讯
-
中汽中心工程院能量流测试设备上线全新专家
2025-04-03 08:46
-
上新|AutoHawk Extreme 横空出世-新一代实
2025-04-03 08:42
-
「智能座椅」东风日产N7为何敢称“百万级大
2025-04-03 08:31
-
基于加速度计补偿的俯仰角和路面坡度角估计
2025-04-03 08:30
-
《北京市自动驾驶汽车条例》正式实施 L3级
2025-04-02 20:23