汽车内饰塑料尾门性能验证
典型的塑料尾门如下图2所示,主要有塑料尾门内板、塑料尾门.上部外板(或扰流板)、塑料尾门下板、尾门玻璃、铰链金属加强板、气撑金属加强板、锁扣加强板及尾门其它附件组成。其中尾门内板和上部外板(或扰流板)的常用材料为SMC或PP+LGF,通过强力胶水分别和尾门玻璃和尾门下部外板连接。由于尾门下部外板是外观零件,要求塑料材料外观喷涂性能好,一般用PP材料。与金属尾门(如下图2所示)相比,塑料尾门的优势主要有质量轻、零件少、集成度高、不易生锈、成本较低。
塑料材料的一些性能暂时无法和钢板材料相比(如拉伸模量、断裂强度),因而塑料化尾门挑战之一是在保证在产品重量降低的前提下仍能满足金属尾门的技术要求。从大的方面来说尾门技术要求主要包括强度、刚度、模态、NVH、碰撞、疲劳寿命等要求。
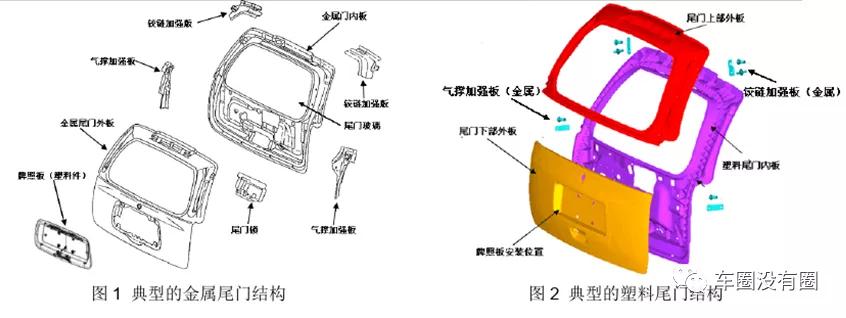
使用HyperMesh软件的ABAQUS模板建立塑料尾门的有限元模型,其中金属加强版使用实体单元,单元尺寸2mm;橡胶缓冲块与橡胶密封等使用Spring单元模拟,其刚度值可以通过物理试验测得;雨刮器总成、尾灯、锁扣等使用Mass单元模拟,分别在其重心处赋予实际的质量:螺栓连接使用Beam单元模拟,并释放螺栓轴旋转方向自由度;胶水连接使用实体单元;铰链使用Equation模拟,释放尾门旋转方向的自由度,保证尾门能自由旋转;尾门内板、外板、玻璃等薄壁大面的零件均使用Shell单元模拟,平均尺为6mm,可能产生应力集中的区域进行细化到2mm。完成后的塑料尾门的有限元模型见图3。
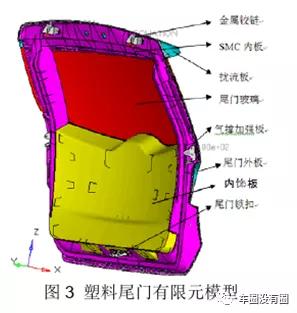
为了确保塑料尾门的性能,对其定义了多达十几种不同工况的技术要求,这些工况分别涵盖了塑料尾门的刚度要求、强度要求及模态要求。对尾门的优化分析主要包括四步:
1)建立有限元模型,分别对每一种工况进行计算,确定最难满足设计要求的工况:
2)运用OptiStruct 软件进行拓扑优化计算。由于每种工况的边界条件有所差异,网格模型也不尽相同,不适合在同一个拓扑优化模中定义所有的分析工况,本文是针对每一种工况分别进行拓扑优化计算。综合所有的拓扑优化计算结果,再结合装配、工艺等实际情况,初步确定尾门SMC内板的壁厚分布、加强筋分布与采用的断面形状。
3)针对最难满足技术要求的典型工况,运用HyperStudy软件的优化功能对尾门SMC内板各区域进行详细的壁厚优化,获得合理的壁厚分布:
4)重新验算所有工况,检查结果是否满足设计要求。优化分析流程图如图4所示。
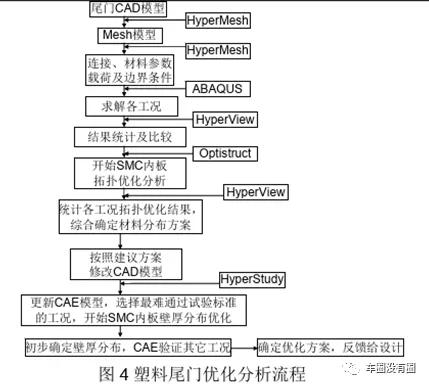
2.1 拓扑优化分析
图5是塑料尾门某工况(Wiper motor mounting surface stiffness)的CAE模型。将与铰链、尾门锁相连接的车身简化成刚性体,进行全约束。金属铰链需释放Y方向的旋转自由度,以确保尾门能绕车身自由旋转。
在雨刮器总成的重心位置沿整车X方向施加100N的载荷,要求变形量小于0.2mm。
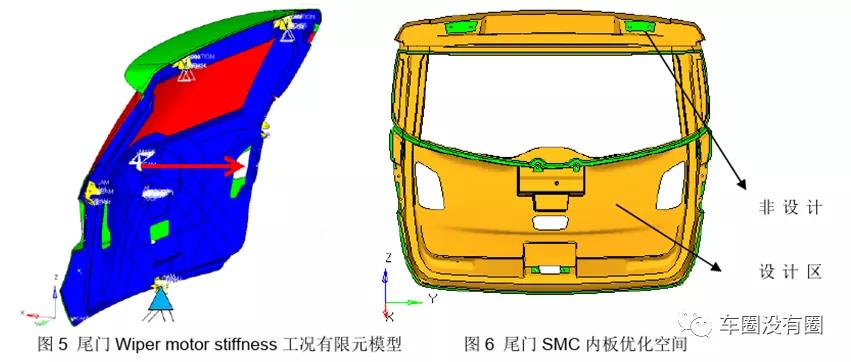
塑料尾门SMC内板是结构优化的重点,将胶粘、螺栓等连接区域应定为非设计区域,其它定位为设计区域。如图6所示,棕黄色区域为设计区域,定义为设计变量,绿色为非设计区域,即在拓扑优化过程中壁厚保持不变。
2.1 2 约束函数的设置
定义响应:
1)定义设计变量区域的总体积(Volume)为响应Vol;
2)在尾门雨刮器总成的重心位置定义一个节点,用RBE2连接至雨刮器电机在尾门的安装孔,将这一节点的X向位移(Static Displacement)定义为响应Disp。
定义约束条件和目标函数:目标是材料的最优分布,故目标函数为响应Vol的最小化;约束条件为响应Disp的上限为0. 20mm。
2.1 3 优化结果分析
使用OptiStruct拓扑优化分析功能进行优化,经过多步迭代后得出优化模型,在HyperVeiw中查看计算结果,图7为上述工况拓扑优化结果后的材料分布云图。其中,图中红色和绿色表示该区域需要分配更多的材料,蓝色表示需要分配较少的材料。
限于篇幅,图8给出比较典型分析工况的拓扑优化分析结果。综合所有分析工况拓扑优化分析的结果,确认尾门SMC内板以下区域需要重点加强,如图8所示。
内板与金属铰链连接区域(区域1)
内板与雨刮器总成连接区域(区域2)
内板与气撑支架连接区域(区域3)
内板与锁扣连接区域(区域4)
尾门玻璃左右两侧的内板区域(区域5)
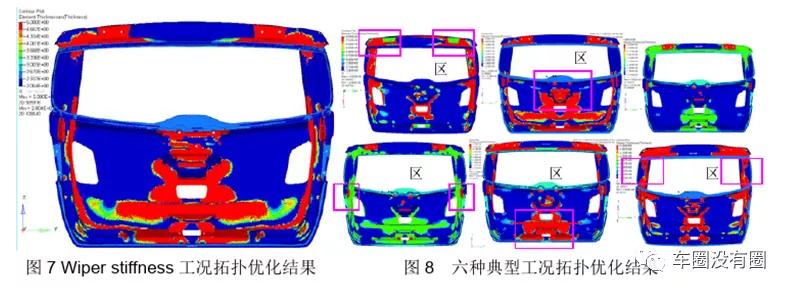
1)局部区域壁厚增加;
2)增加加强筋;
3)改变结构断面,增加抗弯模量。更改后的尾门内板结构与初步的壁厚分布分别如下图9于图10所示。对于Wipersifness工况经过重新验算,当位于雨刮器总成质心施加100N,施力点X向的最大位移为0.162mm(见图11) , 虽然满足技术要求(S0. 2mm),但SMC内板偏重(13.5Kg), 有进一步优化的空间。
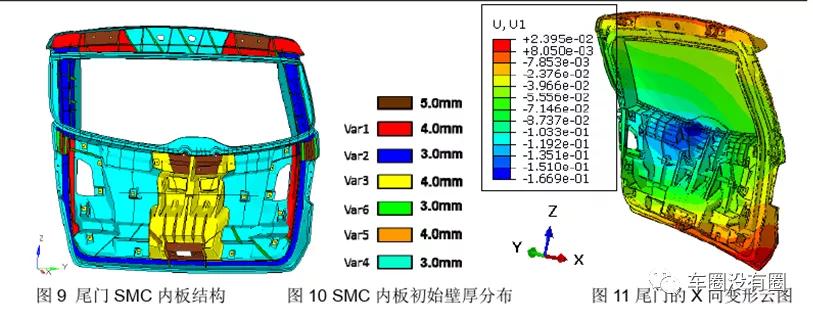
HyperStudy是AltairHyperWorks软件包中的一款主要产品,它主要用于CAE环境下DOE(试验设计),优化及随机分析研究,可与各种外部求解器(如Abaqus, Radioss等)合并使用。
2.2 1 优化数学模型
利用HyperStudy对SMC尾门内板进行尺寸优化,取图12所示的六个壁厚为设计变量,雨刮器总成质心的X向位移为约束条件,整个产品的质量为优化目标,优化的数学模型如下:
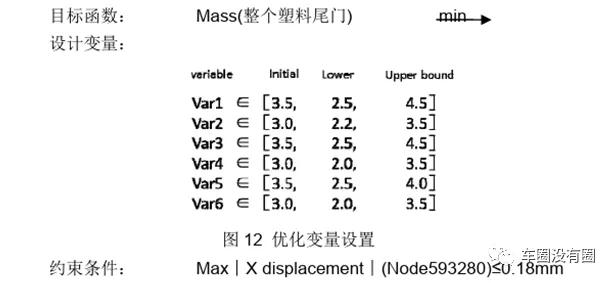
Max | X displacement | (Node593280)≤0. 18mm
2.2 2 优化结果
整个优化过程进行了150次迭代,即相当于软件自动对150次不同壁厚的组合方案进行了计算。目标函数和约束条件的变化分别如图13和图14与所示。从图13可以看出,当迭代进行到第150次
整个尾门的质量为30.97Kg,对应的雨刮器中心X向最大变形为0.183mm。
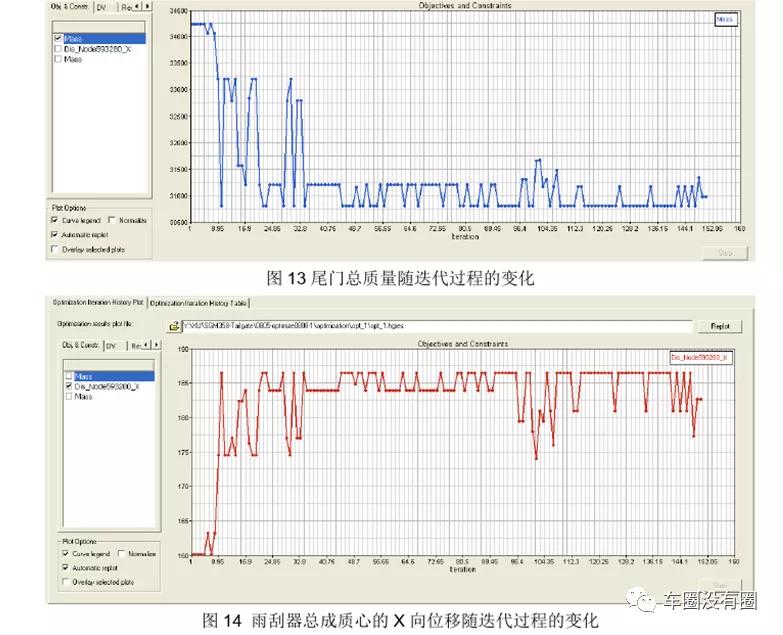
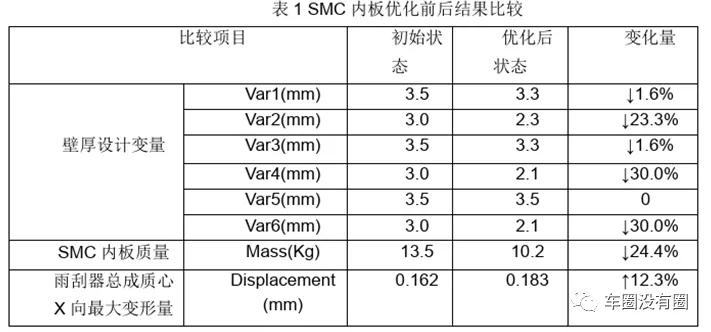
虽然没有满足约束条件(Max X displacement≤0. 18mm)
但仍满足技术要求(X向最大变形量不大于0.2mm)。
3 结论
使用OptiStruct的拓扑优化分析功能,能快速发现产品结构的载荷传递路径,从而针对性的进行结构加强与材料分配;HyperStudy的优化功能则能快速确定产品壁厚的合理分配。壁厚优化后的SMC内板质量为10.2Kg,比初始壁厚的内板质量下降了3.3Kg。通过拓扑优化和壁厚优化,使得产品结构在满足技术要求的前提下,达到产品轻量化的目的。
与金属尾门总成质量相比,在产品刚度、强度、模态的技术要求不降低的前提下,优化后塑料尾门总成质量下降了7.1Kg,下降幅度达27%。
编辑推荐
最新资讯
-
漫说信息智能 · 电动车防晕车大作战
2025-04-27 16:28
-
R171.01对DCAS的要求⑨
2025-04-27 15:29
-
智驾标准法规体系大全
2025-04-27 15:28
-
国内最大汽车创作者大会开幕,懂车帝投入5
2025-04-27 13:18
-
大卓智能端到端直播实测,16公里复杂路段挑
2025-04-25 17:16