车用高性能永磁电机驱动系统的研发
本文重点介绍高性能车用永磁电机驱动系统中的高功率密度车用电机控制器、广域高效混合励磁电机和全数字化高性能电机控制软件平台3 项关键技术,提出了在功率密度、全范围效率、可靠性、维护性和成本等方面均优于传统的车用永磁电机驱动系统的解决方案。在此基础上开发出高功率密度车用电机驱动系统样机,成功应用于力帆LF620纯电动警务车。
关键词: 永磁电机驱动系统; 电机控制器; 混合励磁电机; 全数字化控制
前言
车用电机驱动系统是电动汽车的关键和共性技术。因受到车辆空间限制和使用环境的约束,车用电机驱动系统不同于普通的电传动系统,它要求具有更高的运行性能( 如全速度范围的高效率)、更高的比功率(不低于1. 2k W/kg) 以及更严酷的工作环境(环境温度达到105℃) 等等[1],为满足这些要求,车用电机驱动系统的技术发展趋势基本上可以归纳为电机永磁化、控制数字化和系统集成化。
与国际先进水平相比,我国在面向车辆工况的电机系统优化设计能力,满足产业化需求的全数字化电机控制软件平台建设,机电一体化系统集成设计能力,以及高集成度功率电子模块研制与生产、产品可靠性、耐久性和成熟度的考核与分析等方面,仍存在较大差距。随着我国电动汽车产业化进程的推进,这些技术差距必将影响相关行业的市场竞争力。
本文中重点介绍了高性能车用永磁电机驱动系统中高功率密度、高效率与低成本的车用电机控制器、广域高效混合励磁电机和满足可重复性、可移植性和易使用性要求的全数字化高性能电机控制软件平台3项关键技术,提出了在功率密度、全范围效率、可靠性、维护性及成本等方面均优于传统的车用永磁电机驱动系统的解决方案。并开发出新型混合励磁电机驱动系统和高功率密度、高效与低成本的车用电机控制器样机,后者已成功应用于力帆LF620纯电动警务车,服务于2010年上海世博会。
1 高功率密度车用电机控制器
电动汽车中主驱动电机控制器一般采用典型的三相桥式电压源逆变电路,其主要部件包括功率模块、直流侧支撑电容和叠层母线排[2]。根据车辆对控制器的功率等级需求,功率模块大多采用绝缘栅双极型晶体管(insulated gate bipolar transistor,IG-BT) ,其成本一般占到电机控制器总成本的30% 以上,功率模块的性能、可靠性与成本直接影响电机控制器产业化的实现; 直流侧支撑电容是控制器中最重要的无源器件,主要作用是吸收功率模块开关造成的直流侧脉动电流,稳定直流侧输出电压电流,从而提高蓄电池使用寿命,其体积和质量对控制器的功率密度有很大影响。因此,IGBT功率模块和直流侧支撑电容是提高控制器性能和控制成本的关键。
1. 1 智能IGBT功率模块的研发
为提高IGBT功率模块的运行性能和可靠性,降低成本,中国科学院电工研究所联合国内功率模块封装企业进行具备自主知识产权的国产智能IGBT功率模块的研发。在IGBT设计方面进行了大量分析优化和工艺设计工作。
首先,借助计算机仿真分析技术,优化模块内部芯片布局和布线,从而减少了模块内部的杂散电感; 优化底板设计、控制底板弧度,降低了芯片应力; 采用氮化铝DBC基板,降低了热阻。
其次,应用专有干法大面积焊接免清洗技术,减少了焊接空洞率,减少热阻; 研究应力控制的压焊技术,提高了电流浪涌能力,减少了引线的杂散电感。研发出的智能IGBT功率模块内部布局及实物见图1(a) 和图1(b) 。
同时,进一步提高系统集成度,在智能IGBT功率模块内部集成了驱动保护电路。在驱动技术方面,采用分段驱动方式,在常规推挽驱动原理电路中加入可控辅助充放电电流源,在缩短器件开关时间的同时,降低开通过程中集电极电流尖峰和关断过程中集射电压尖峰,减小开关应力、损耗和噪声; 在保护技术方面,采用了集射电压检测方式和短路保护实现电路,在短路发生后无延时地箝制由米勒效应造成的门电压抬升,避免误导通。
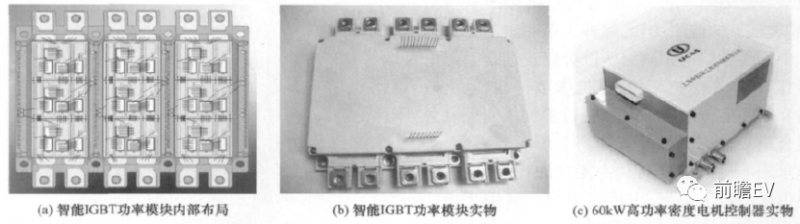
图1智能IGBT功率模块及60k W高功率密度电机控制器
1. 2 直流侧支撑电容的选择
在由蓄电池储能的电动汽车中,由于蓄电池组内部等效电容很大,一般在法拉量级[3],对直流电压的滤波可主要由蓄电池组实现,支撑电容并不独自承担电压滤波的功能。由于平稳的输出电流有利于提高蓄电池组的使用寿命,因而在正常工况下,希望蓄电池组输出电流Iin接近于理想直流,此时直流侧电容须吸收因IGBT不停开关所造成的脉动电流,导致直流侧电容电流Icap不断脉动,因此在蓄电池组供电的条件下,直流侧电容的选取主要考虑其能提供的纹波电流有效值的大小,而电容值可相对选取较小。
直流侧支撑电容的传统设计方法是采用一组串并联的电解电容,体积大而且可靠性不高,难以进一步提升功率密度。采用聚合物膜( 金属聚丙烯膜) 作为电介质的金属膜电容体积小、高频特性好具有更大的电流提供能力和更低的等效电阻; 寿命可达到100 000h,而 普 通电解电容只有5 000 ~10 000h。这些特征使金属膜电容非常适合电动汽车的应用条件[4 - 5]。高功率密度的车用电机控制器采用新型220μF/600V金属膜电容作为直流侧支撑电容。该电容采用金属聚丙烯膜作为电介质,工作温度可达到105℃。10k Hz时能够提供有效值为100A的峰值纹波电流,开关频率即使在20k Hz时,也仍保持容性阻抗特性,同时电容值可随开关频率增加而增加。很明显,膜电容具有低感、高频特性好和大电流提供能力等优点,非常适合较高频率条件下应用。
1. 3高功率密度电机控制器的研发
应用智能IGBT功率模块和金属膜电容技术所研制的60k W 高功率密度电机控制器如图1(c) 所示,该控制器的质量比功率为4k W/kg,体积比功率为6k W/L。
2 广域高效混合励磁电机
无刷永磁电机具有高能量密度、体积小、质量轻和效率高等优点,在电动汽车中具有极好的应用前景,已应用于国内外多种电动车辆。但其永磁磁链无法调节的缺点在恒定供电电压下会带来弱磁控制问题: 车辆动力性能要求电机系统在高转速下具有较宽的恒功率调速范围以保证车辆的高速性能。由于受到电池电压的限制,目前大部分永磁电机系统采用增加定子绕组去磁电流的方法来抵消永磁磁场,从而达到恒定供电电压下弱磁调速的目的,但这种方法降低了系统效率和功率因数,增加了控制器成本,同时还存在深度弱磁控制时稳定性差和高速失控时的电压安全问题。混合励磁电机能解决以上问题。
2. 1 旁路式混合励磁电机的基本原理
混合励磁电机是在永磁电机与电励磁电机的基础上演变而来,通过在永磁电机中引入电励磁绕组使电机获得励磁可控的性能,电机更适合于宽速度范围、高弱磁比的应用场合,弥补了单一励磁方式的不足。中国科学院电工研究所以旁路式混合励磁电机为研究对象,在电机结构、电机参数特性、电机数学模型和励磁电流规划等方面进行了深入研究。旁路式混合励磁电机工作原理如图2 所示,为最大程度继承永磁电机高效和高功率密度的优点,电机励磁主要由永磁磁势提供,电励磁磁势主要用于增强或削弱主磁路磁通,通过调节电励磁电流大小实现电励磁助磁与弱磁功能。
(1) 助磁工况
电励磁助磁工况下的磁路如图2( a) 所示。N 极侧的电励磁磁力线从电励磁端盖通过轴向气隙进入电机转子N 极,与永磁体磁力线一同通过主气隙与电枢绕组交链,一部分磁力线通过端盖闭合,另一部分磁力线通过电机轭部与主气隙进入转子S极,通过S极侧轴向气隙进入电励磁旁路闭合。
(2) 弱磁工况
电励磁弱磁通过励磁电流反向实现,反向的电励磁磁势与永磁体磁势建立与助磁工况下电励磁旁路中相反的磁力线方向,部分永磁体磁力线不经过主气隙与电枢绕组交链,实现电机弱磁运行。
2. 2 样机与实验结果
目前已完成的原理样机最大输出功率为4k W,电励磁磁势为 ± 1 200A·T。图 3 为采用最优励磁图2旁路式混合励磁电机工作原理电流规划后的电机效率和恒定4A 励磁电流下实验结果的对比。由图可见,混合励磁电机高效区范围及转速范围均有拓宽。
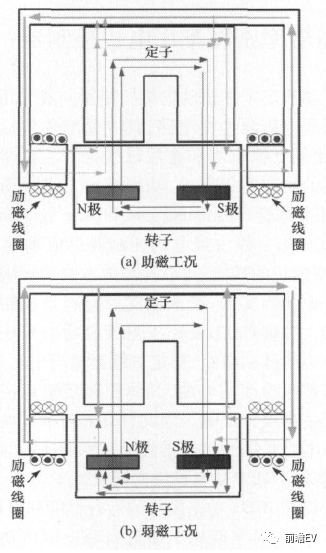
图2旁路式混合励磁电机工作原理
综合来看,与传统无刷永磁电机相比,旁路式混合励磁电机具有显著优点: 如低速时增大励磁以提高输出转矩; 高速运行时减小或反向励磁从而拓宽电机的恒功率弱磁区; 降低电机在高速运行下的铁损,提高效率; 动态调节励磁电流大小,提高负载变化时发电电压动态性能; 减小电枢反应弱磁磁势,降低永磁体高温运行时的失磁风险等。混合励磁是未来车用永磁电机的重要发展趋势。
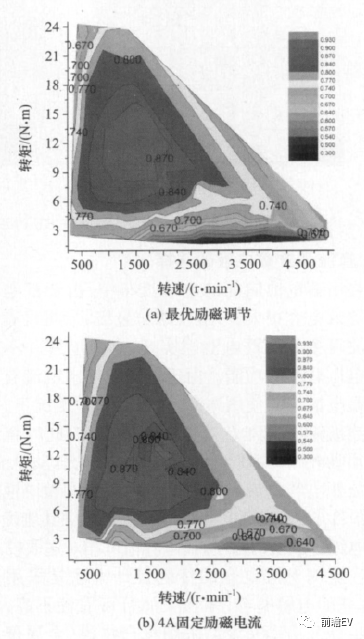
图3 混合励磁电机效率对比
3 全数字化高性能电机控制软件平台
电动车辆的大批量标准化生产,要求其驱动电机系统所采用的控制软件满足可重复性、可移植性和易使用性的要求,具有这些特点的全数字化电机驱动控制系统是其重要发展方向之一。除永磁同步电机控制所需的核心控制策略———包括深度弱磁技术、死区补偿技术、抗积分饱和PI技术、解耦技术等磁场定向控制技术外,为满足电动车辆的高度可靠性和安全要求,数字化车用驱动控制系统还要求具有故障监控、故障保护和自诊断等功能。
3. 1 软件平台主要功能
为达到保证可靠性的前提下满足软件系统可重复性、可移植性和易使用性的目的,根据电动汽车对电机驱动系统的要求以及开发使用人员的需求对电机驱动软件系统按照系列化、平台化和服务化的目标进行规划。软件平台拓扑如图4所示。该全数字电机驱动软件平台实现了以下主要功能: ( 1) 软件硬件分离 为方便软件开发人员,并实现软硬件的解耦,把软件从硬件中剥离出来,形成软件算法文件和硬件配置文件; ( 2) 算法功能模块化 按最小功能化把所有的算法模块化,实现算法间解耦; ( 3) 参数分类提取 对系统平台中出现的所有参数进行提取并分类,方便参数配置; (4) 快速开发模式 采用功能模块串联的方式,实现系统平台的快速升级和第三方开发; (5) 产权保护功能以IP核的方式灵活实现核心算法的产权保护。
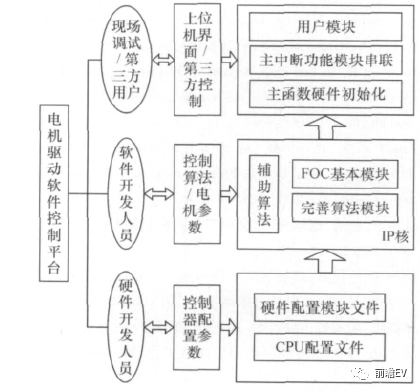
图4电机驱动软件控制平台
3. 2 关键技术
电机驱动软件控制平台的核心算法采用全数字化的磁场定向控制(field oriented control) ,结合上位机控制,集成如下控制技术。
(1) 具有转速控制、转矩控制及功率控制3种模式,并可实现自由切换[6]。在全速度范围恒转速控制误差≤10r/min; 恒转矩控制误差≤5% Tn(Tn为额定转矩) ,转矩响应时间< 0. 3ms。
(2) 具有沿最大转矩电流(maximum torque perampere,MTPA) 曲线开始控制到沿电流圆弱磁进入弱磁二区,再沿最大转矩电压( maximum torque pervolt,MTPV) 曲线进入弱磁三区的深度弱磁控制技术,如图5所示。
(3) 采用死区补偿技术有效抑制电压源逆变器零电流箝位效应,如图6 所示,有效改善电机的低速性能[7]; 采用一种具有预测功能的抗积分饱和速度PI 控制器,电流调节更加快速、无超调; 实现了电压解耦,高速性能更加稳定[8]。
此外,还具备系统自检、参数在线整定、故障诊断、软件保护、CAN通信和上位机功能。
实验用电机参数如表1所示,实验中基速为600r / min,进入三区弱磁最高转速4 000r / min。
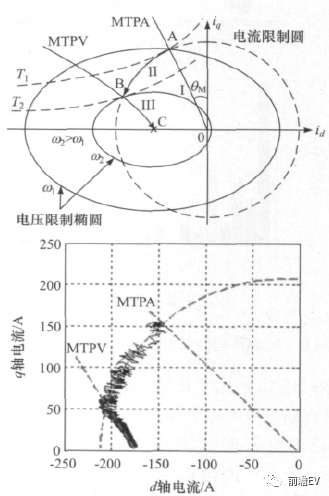
图5永磁同步电机工作区域和全区控制实验结果
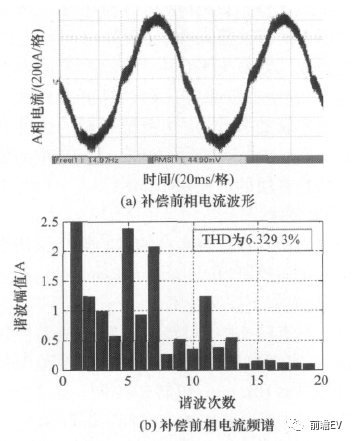
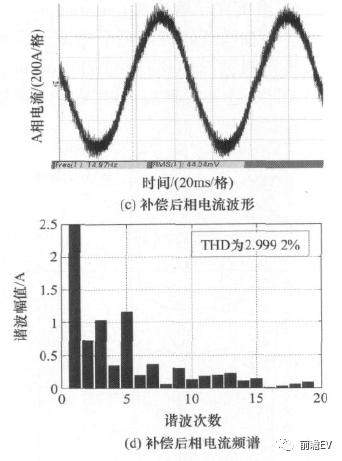
图6 死区补偿前后电机相电流波形和频谱
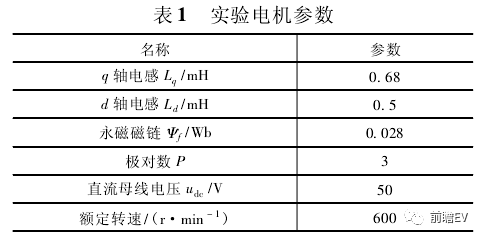
全数字化高性能电机控制软件平台通过实验验证和工程应用证明,能满足电动汽车起动加速、低速爬坡和高速运行等复杂工况的需求,并以IP核的形式进行产权保护,具有良好的可重复性、可移植性、易使用性、友好的升级维护和第三方开发功能,具备了体系化、平台化和服务化的特点。
4 结论
本文中研究了高功率密度车用电机控制器、广域高效混合励磁电机和全数字化高性能电机控制软件平台3项关键技术,所提出的技术方案在功率密度、全范围效率、可靠性、维护性和成本等方面均优于传统的车用永磁电机驱动系统,具有广泛的应用前景。
- 下一篇:氢能源汽车动力系统集成研究
- 上一篇:悬架对汽车盘式制动器制动抖动的影响分析
编辑推荐
最新资讯
-
全国汽车标准化技术委员会汽车节能分技术委
2025-04-18 17:34
-
我国联合牵头由DC/DC变换器供电的低压电气
2025-04-18 17:33
-
中国汽研牵头的首个ITU-T国际标准正式立项
2025-04-18 17:32
-
为什么要进行汽车以太网接收测试?汽车以太
2025-04-18 17:26
-
产品手册下载 | NI 全新USB数据采集-NI mio
2025-04-18 16:39