电动汽车驱动桥桥壳有限元分析
1 驱动桥三维模型的建立
根据某低速电动汽车驱动桥桥壳设计图纸在CATIA零件设计模块中建立法兰部件、半轴套管部件、弹簧座部件、桥壳本体部件及主减速器壳部件的三维实体模型,并在CATIA装配设计模块中进行各部件间的装配,装配好的驱动桥桥壳三维实体模型如图1所示。为了提高有限元分析效率,在建立各零部件三维模型时,将对分析结果影响较小的油管支架、纵摆臂支架、减震器支架删除,同时为了保证有限元分析精度,保留驱动桥壳各部件的倒圆角。某低速电动汽车相关参数见表1。
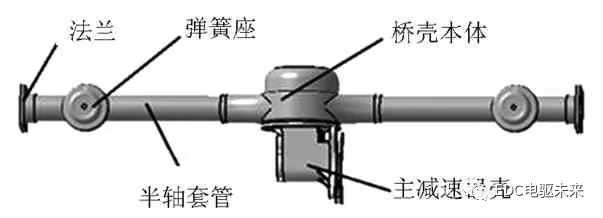
图1 驱动桥桥壳三维实体模型
Fig.1 The 3D solid model of drive axle housing
表1 某低速电动汽车相关参数
Tab.1 Relevant parameters of an electric vehicle
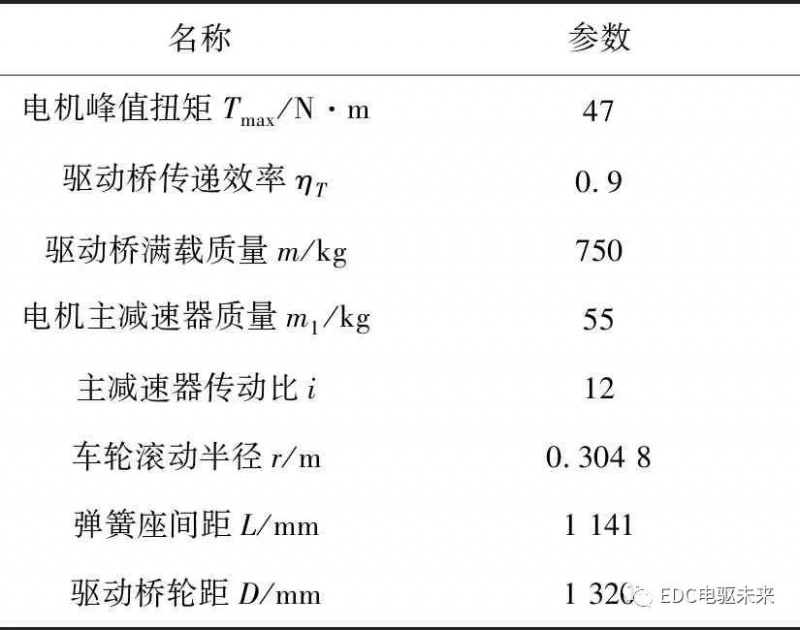
2 驱动桥极限工况分析
汽车实际受力情况较为复杂,一般按最大冲击载荷工况、最大驱动力工况、最大制动工况以及最大侧向力工况进行分析。如果该低速电动汽车后驱动桥桥壳在上述4种极限工况下满足强度、刚度要求,则认为该桥壳满足汽车各种使用工况要求[4]。为了方便理论计算及有限元分析,需要确定三维坐标系,现以汽车前进方向为Z轴正向,汽车前进方向的驱动桥轴向左侧为X轴正向,竖直向上方向为Y轴正向,理论分析和有限元分析过程中均采用该坐标系。
2.1 最大冲击载荷工况
当汽车满载行驶在不平路面时,桥壳除需要承受来自电机主减速器的重力作用外,还需要承受来自不平路面的冲击载荷,该冲击载荷通过车轮-半轴-支承轴承-桥壳的传递方式由地面传递到桥壳,一般最大冲击载荷的值以1.75倍满载轴荷代替,该工况下驱动桥桥壳不受其它力和弯矩的作用[5-6]。冲击载荷工况受力分析如图2所示。
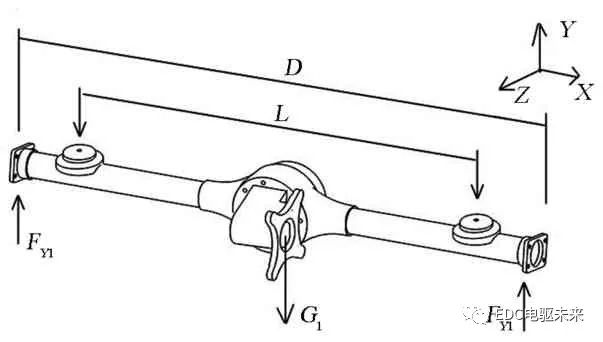
图2 冲击载荷工况受力分析图
Fig.2 The force analysis diagram of impact load condition
结合表1和图2可知,最大冲击载荷工况下电机主减速器重力为
G1=Kdm1g=943.25 N (1)
单侧法兰内安装支承轴承处受到的垂向力为
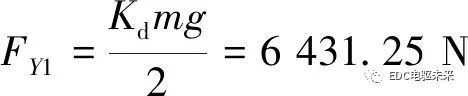
式中:Kd为动载荷系数,取1.75;g为重力加速度,取9.8 m/s2。
2.2 最大驱动力工况
汽车以最大驱动力行驶时,驱动桥桥壳需要承受电机主减速器的重力、驱动桥满载重力和最大驱动力作用。其中最大驱动力可由电机最大转矩或地面附着力求得。最大驱动力工况受力分析如图3所示。
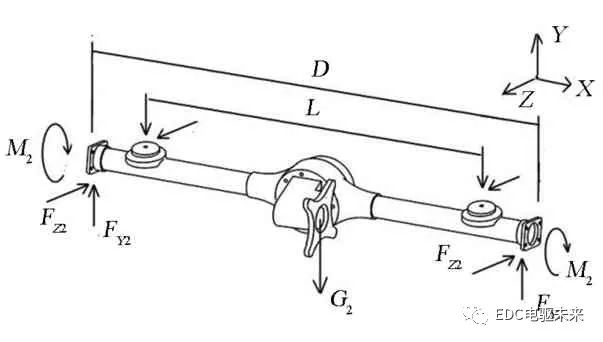
图3 最大驱动力工况受力分析图
Fig.3 The force analysis diagram of maximum driving force condition
结合表1和图3可知,最大驱动力工况下电机主减速器重力为
G2=m2″m1g=646.8 N (3)
单侧法兰内安装支承轴承处受到的垂向力为
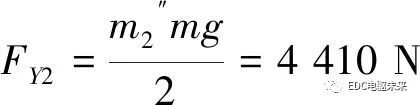
通过地面附着力计算,单侧法兰内安装支承轴承处的最大驱动力为
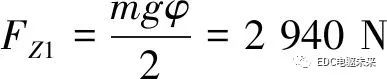
通过电机最大扭矩计算,单侧法兰内安装支承轴承处的最大驱动力为
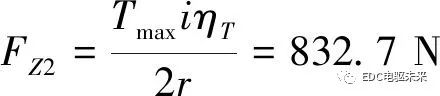
式中:m″为最大驱动力工况下驱动桥载荷转移系数,取1.2;φ为地面附着系数,取0.8。由于地面附着力大于电机产生的最大驱动力,因此以电机产生的驱动力为最大驱动力。
单侧法兰内安装支承轴承处受到的力矩为

2.3 最大制动力工况
当汽车紧急制动时,不考虑侧向力,此时驱动桥桥壳主要承受电机主减速器的重力、驱动桥满载重力和制动力的作用。最大制动力工况受力分析如图4所示。
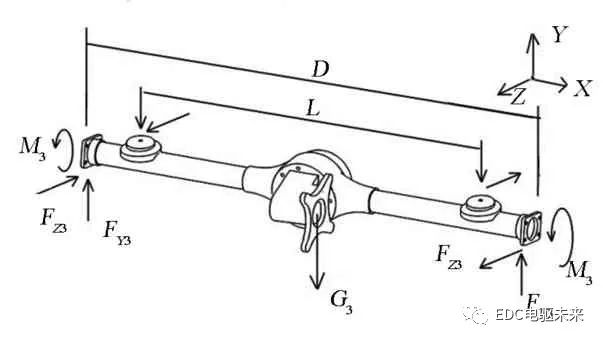
图4 最大制动力工况受力分析图
Fig.4 The force analysis diagram of maximum braking force condition
结合表1和图4可知,最大制动力工况下电机主减速器重力为
G3=m3″m1g=431.2 N (8)
单侧法兰内安装支承轴承处受到的垂向力为
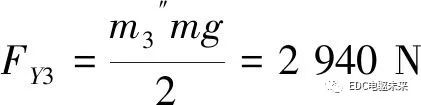
单侧法兰内安装支承轴承处受到的最大制动力为
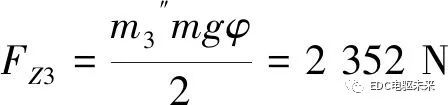
制动鼓与法兰相连,最大制动力时的力矩作用在法兰上,且每个法兰上有4个螺栓孔。
单侧法兰每个螺栓孔制动力矩为

式中:m3″为最大制动力工况下的驱动桥载荷转移系数,取0.8。
2.4 最大侧向力工况
当汽车极限转弯、处于侧滑状态时,发生侧滑一侧的垂向力和侧向力达到最大值,另一侧受力为零。假设汽车向右极限转弯(有向左侧翻趋势)时,最大侧向力工况受力分析如图5所示。
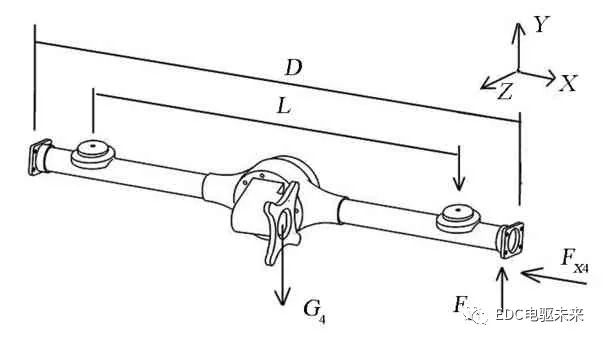
图5 最大侧向力工况受力分析图
Fig.5 The force analysis diagram of maximum lateral force condition
结合表1和图5可知,最大侧向力工况下电机主减速器重力为
G4=m1g=539 N (12)
侧滑一侧(汽车前进方向左侧)的法兰内安装支承轴承处受到的垂向力为
FY4=mg=7 350 N (13)
侧滑一侧(汽车前进方向左侧)的法兰内安装支承轴承处受到的侧向力为
FX4=mgφ,=7 350 N (14)
式中:φ,为侧滑附着系数,取1.0。
3 有限元分析
3.1 定义材料属性
该电动汽车驱动桥桥壳包括法兰、半轴套管、弹簧座及桥壳本体,其中法兰及弹簧座所用材料为40Cr,半轴套管及桥壳本体的材料为45号钢,主减速器壳的材料为铸铝,各材料性能参数见表2。
表2 各材料性能参数
Tab.2 Performance parameters of various materials
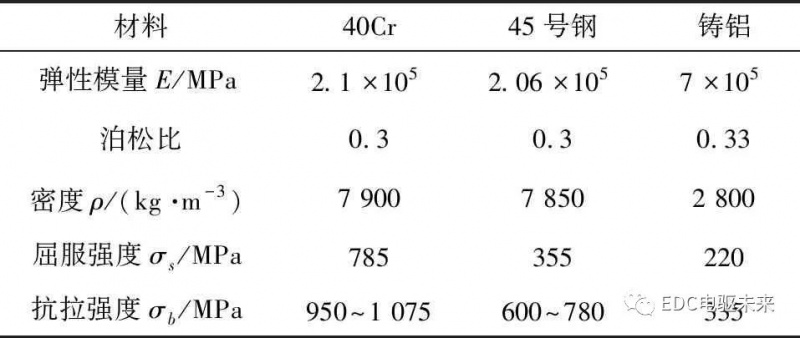
3.2 定义连接关系和网格划分
主减速器壳体和桥壳本体之间采用共节点的连接方法,半轴套管与法兰、半轴套管与弹簧座、半轴套管与桥壳本体之间均采用绑定连接的方法。为了保证网格质量,同时为了减少计算量,对驱动桥壳不同部件采用不同类型的网格进行划分。半轴套管采用实体壳单元网格划分方法进行划分,网格形状为四边形,单元尺寸8 mm;两侧法兰及弹簧座结构和受力情况比较复杂,采用四面体进行网格划分,单元尺寸3 mm;主减速器壳体和桥壳本体也采用四面体进行网格划分,单元尺寸6 mm。得出节点数246 185个,单元数143 144个。驱动桥桥壳有限元网格划分如图6所示。
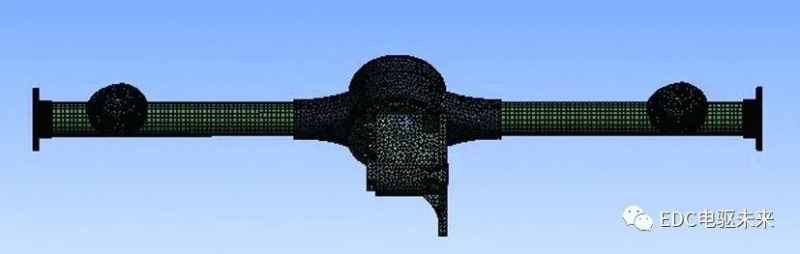
图6 驱动桥桥壳有限元网格划分图
Fig.6 Finite element mesh division diagram of drive axle housing
3.3 边界条件及结果分析
本文采用弹簧座处添加约束条件、法兰内侧轴承支承处添加载荷的方式进行边界条件添加,各种工况下的弹簧座处约束条件见表3,其中“Free”表示该自由度是释放的,“0”表示该自由度是约束的,根据上文分析的各工况下的载荷进行载荷添加。经过网格划分和有限元计算得出各工况下等效应力、剪切应力和变形云图如图7—图18所示,其中图7、图8、图10、图11、图13、图14、图16及图17的上半部分为整体应力云图,下半部分为去除弹簧座后的应力云图。
表3 各种工况下的弹簧座处约束条件
Tab.3 Constraints on spring seats under various working conditions

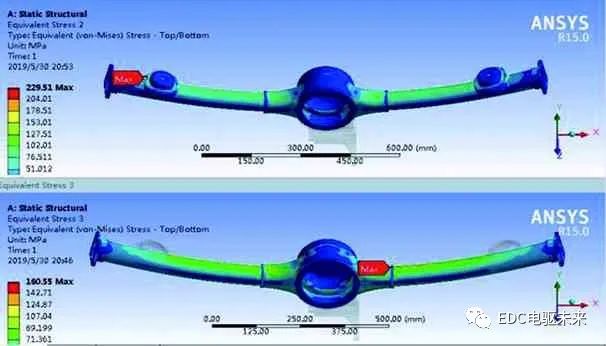
图7 冲击载荷等效应力云图
Fig.7 Equivalent stress nephogram of impact load
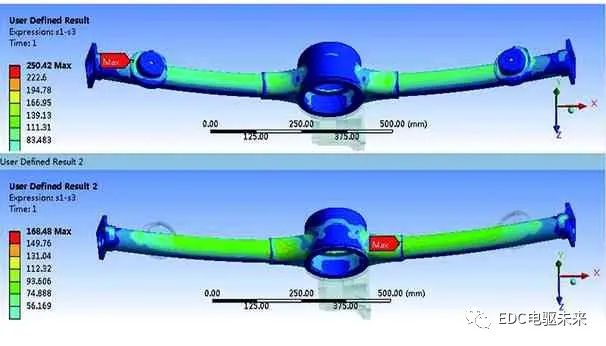
图8 冲击载荷剪切应力云图
Fig.8 Shear stress nephogram of impact load
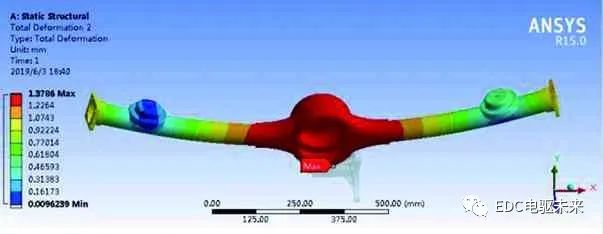
图9 冲击载荷变形云图
Fig.9 Deformation nephogram of impact load
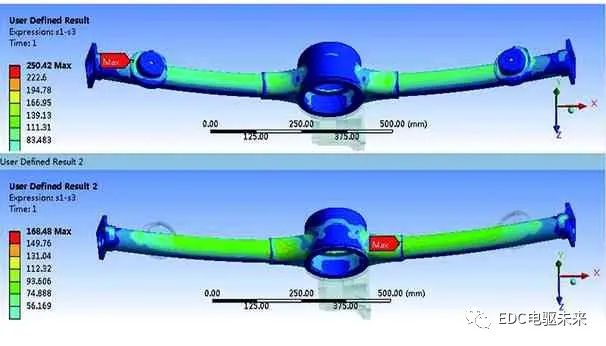
图10 最大驱动力等效应力云图
Fig.10 Equivalent stress nephogram of maximum driving force

图11 最大驱动力剪切应力云图
Fig.11 Shear stress nephogram of maximum driving force
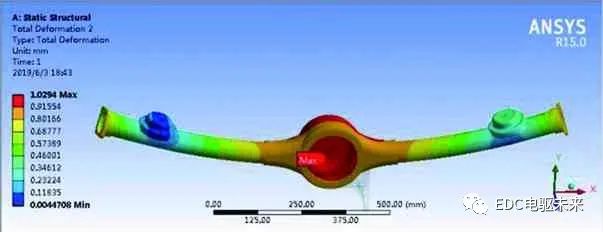
图12 最大驱动力变形云图
Fig.12 Deformation nephogram of maximum driving force
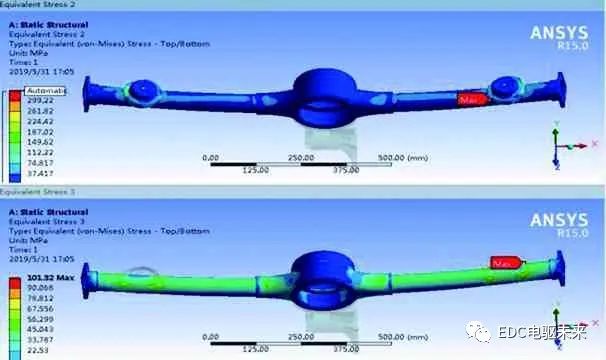
图13 最大制动力等效应力云图
Fig.13 Equivalent stress nephogram of maximum braking force
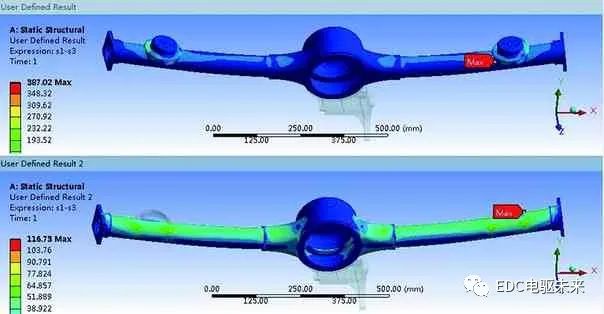
图14 最大制动力剪切应力云图
Fig.14 Shear stress nephogram of maximum braking force
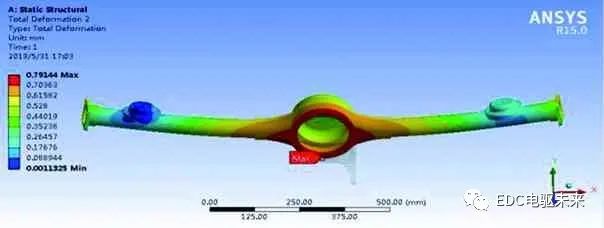
图15 最大制动力变形云图
Fig.15 Deformation nephogram of maximum braking force
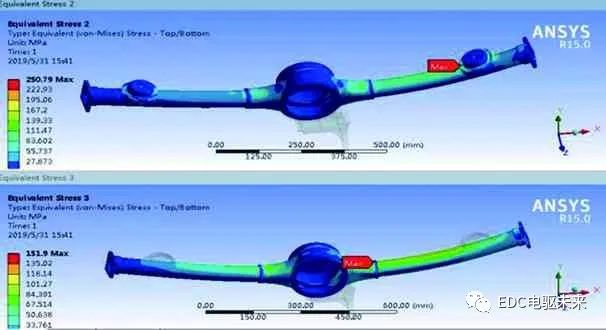
图16 最大侧向力等效应力云图
Fig.16 Equivalent stress nephogram of maximum lateral force
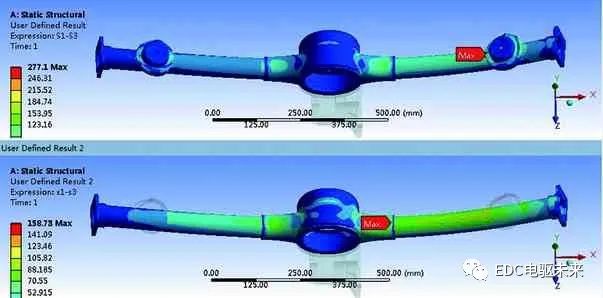
图17 最大侧向力剪切应力云图
Fig.17 Shear stress nephogram of maximum lateral force
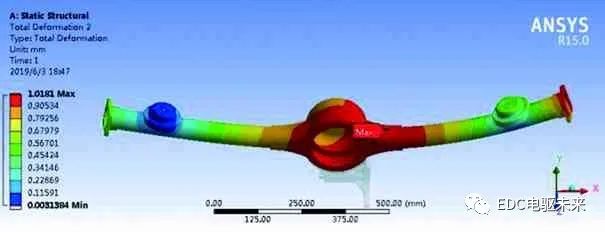
图18 最大侧向力变形云图
Fig.18 Deformation nephogram of maximum lateral force
由图7—图18云图可以得出不同工况下的最大应力及变形情况,见表4。结合云图和表4可知,4种工况下桥壳最大应力为最大制动力工况时的剪切应力387.02 MPa,小于40Cr屈服极限785 MPa,安全系数为2.03(785 MPa/387.02 MPa),具有一定的强度储备。去除弹簧座后的最大应力为最大冲击载荷工况时的剪切应力168.48 MPa,小于45号钢的屈服极限355 MPa,安全系数为2.11(355 MPa/168.48 MPa),同样具有一定的强度储备,因此整个驱动桥桥壳满足刚度、强度要求。4种工况下桥壳最大变形量为1.378 6 mm,该车轮距1.32 m,故每米轮距的最大变形量为1.04 mm,小于《汽车驱动桥台架试验评价指标》规定的1.5 mm,满足变形量要求。
表4 不同工况下的应力及变形
Tab.4 Stresses and deformations under different working conditions
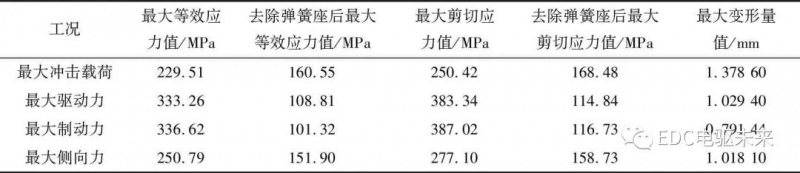
4 结束语
通过对该半浮式半轴结构驱动桥桥壳在4种典型工况下的有限元分析可知,各工况下桥壳的最大剪切应力均大于最大等效应力,因此在校核桥壳刚度及强度时应当以最大剪切应力为参考。当法兰及弹簧座采用40Cr为材料,半轴套管及桥壳本体采用45号钢为材料时,该驱动桥桥壳满足刚度、强度及变形量要求。分析可知,该桥壳潜在的应力集中处为桥壳本体与半轴套管连接处以及弹簧座处,这一结论为后续驱动桥桥壳的优化设计提供了参考,也为提高产品设计效率打下了良好的基础。
最新资讯
-
推荐性国家标准《乘/商用车电子机械制动卡
2025-04-30 11:13
-
载荷分解
2025-04-30 10:46
-
布雷博在上海开设亚洲首个灵感实验室
2025-04-30 10:25
-
组分性能对锂离子电池卷芯挤压力学响应的影
2025-04-30 09:00
-
美国发布自动驾驶新框架,放宽报告要求+扩
2025-04-30 08:59