电动汽车动力电池系统加热方法研究进展
1 内部加热方式
电池内部加热不受电池箱尺寸和空间以及安装方式限制,同一类型电芯,每个电芯的加热功率基本相同,热量从内部产生,加热均匀,但须配套高低频加载控制电路装置或者外控电路。
1.1 高/低频交流电加热
TA.Stuart和A.Hande等最早提出利用低频或高频交流电对氢镍或铅酸电池进行内部加热,其中低频交流电的频率是60Hz,高频交流电的频率是10~20kHz。主要原理是通过电池自身的电阻进行加热,在电池组通交流电的同时可以对电池进行充电和放电。低频交流电的装置体积相对于高频交流电体积较为庞大,较难实现装车,并且有人指出,低频交流电会使电池内部发生电离,电池寿命降低,但未有数据证实。针对锂离子动力电池系统,有多项类似加热的专利出现,由于涉及到交流电产生装置的成本、质量、安装空间等限制,目前该种方法还没有在电动汽车上批量应用。
1.2 电池内部放电加热
Wang等开发出一种具有快速自发热功能的锂离子电池。在电池中设计了镍箔作为第三极,只要环境温度低于0℃,正极和第三极就会形成放电回路,产生热量对电池进行加热;电池内部温度超过0℃,第三极断开,电池回到工作状态。电池从-30℃加热到0℃,只要30s,同时消耗5.5%的电量,效率高,时间短,有望应用于电动汽车上解决低温严寒应用,加热结构和原理见图1。
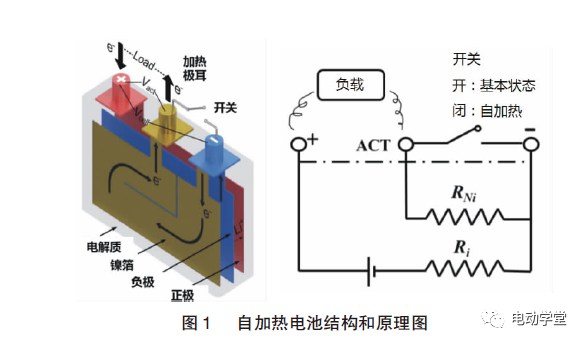
但在电动汽车应用中,由于为数百上千只电池串并联,电池包内部各电池温度存在差异,由于加热为电池内部自行控制,会造成有些电池加热时间长,有些电池加热时间短,从而加大单体电池之间荷电量的不一致性,所以对电池组内部的温度一致性、电池系统的均衡等方面提出了更高的要求。在电池组低温贮存和车辆驻停期间,还有可能造成电池组电量完全放空甚至过放电,影响电池组性能和寿命。
1.3 其他
某些情况下,有利用低温下电芯内阻较高的特点,通过负载以小电流对电池组进行放电的形式产生热量加热,但通常加热效率较低,加热时间长,实际应用较少。
2 外部加热系统
外部加热方式相对比较多,结构设计也有比较大的差别,但总体上应当满足:
(1)成本低;(2)能效高;(3)安全可靠;(4)寿命长;(5)温度一致性好,小于5℃,最佳小于3℃;(6)与车辆设计匹配,包括与电芯结构、电池箱结构、系统参数及车载充电机等参数的匹配性等。
外部加热相对安全,容易实现,但能效低,加热时间长。部分外部加热还需与电池组在高温下的散热、低温下的保温等结合起来设计。外部加热按热量传导介质分,主要有以下几种方法:热风加热、液体加热、加热板或加热膜加热等。
2.1 热风加热
热风加热有两种方式:一是引入外部热风,这种方式对电池箱及管道等的密封性要求比较高,而且热量散失比较大,能量效率直接与气体流速、进出风口温度等有关,但这种方式电池箱内若产生有害气体可以直接排出,并且可以同时作为散热系统;二是在电池箱内部热风循环,配合其他加热装置(如PTC加热器),加热器通电产生热量,风扇将吹向散热器形成热气流,在电池箱内部形成热空气内循环。王发成等试验了用空气进行电加热电池组的试验,证明是一种有效方法,从-15℃加热到电池表面0℃,仅用了21min。
热风加热方式结构简单、质量轻、成本低,但由于电池包中气流速度及通道限制等原因,空气将热量传导到电池上效率较低,且各处流速不均匀,很难保证均匀传热,加热效率相对最低。气体加热相对来说温差较大,所以对电池箱内部安全性、气流通道等设计要求较高,必须对流场进行专门设计,电池箱内部不能形成死角,各区域传热、电池箱体对外散热要基本一致,才能较好地控制温差,在环境极冷情况下,容易产生更大的不均匀。
热风加热适合于圆柱、方形结构的电池,其组成模块或模组时电池之间自然形成或留出有气体通道,变更与加热或散热的结构设计,对于软包电池,由于组合体积、方式、成本等方面的限制,应用较少。
2.2 液体加热
液体加热方法是在外部或电池箱内将液体加热,使其流经电池周围实现对电池加热。通常液体加热方式电池组的加热与散热两者功能是做在一起的。通用的VOLT、TELSA等采用此方式进行加热和散热。液体加热对电池箱的密封和绝缘要求较高,电池模块、电池箱的设计复杂,可靠性要求高。使用液体作为传热介质,需要考虑绝缘性、安全性、密封性,以及电池组的维护方便性,还应考虑电池包的整体质量。其主要优点包括:
(1)加热或冷却的效率比较高;
(2)液体有较好的保温作用,电池组充电或放电一段时间后液体温度已经上升到足够高的温度,车辆运行中停驻几小时,不会由于电池组温度很快下降而影响再次行驶,但加热时要首先将液体进行加热,会多消耗能量;
(3)电池组温度一致性高,一般可以控制在3℃以内。液体加热或散热的情况下,电芯产生的热量或液体热量传递到电芯的速度,受传热路径和传热方式影响较大,液体管道或导热部件最好直接和电芯接触,但电池系统通常为高压系统,管道或导热部件与电芯之间的绝缘、耐压要求很高,需满足相关标准要求。导热一般采用金属铝板等,可用导热硅胶等对其进行绝缘;
(4)适宜于各种不同结构和类型的电池。液体加热/冷却是目前主要研究和应用的方式之一。
液体加热要避免液体的泄露,电池箱内接口越少越好,同时要考虑泄露后液体的存在不能产生电池包的安全性问题;成本相对比较高,包括液体的加热/冷却装置、管道、导热板等;质量高,对电池系统的比能量影响比较大。储液槽、加热/冷却装置、泵等一般安装在电池箱外部。
2.3 PTC加热
PTC加热器由PTC陶瓷发热元件与铝管组成。PTC发热体热阻小、换热效率高达99%,安全性好,任何应用情况下均不会产生过热现象。与风扇结合使用,即遇风机故障停转时,PTC加热器因得不到充分散热,其功率会自动急剧下降,不会导致持续大功率发热而出现的安全性问题。PTC使用寿命长;电压使用范围宽,根据电池系统电压需要设计;功率可根据需求设计;阻燃。
使用时,可在电池模块中不同单体之间加铝制加热板,加热板和PTC加热器连接,对电池组进行加热,但要注意加热板和电池之间的绝缘问题,在加热器不工作时,加热板还可用于电池的散热。PTC加热器可以作为单独加热装置与风扇结合使用形成热风循环,也可以做成板状对电池组进行加热,其成本较低,已在电池组中广泛使用。
但PTC加热器体积较大,做成板状厚度超过10mm,不能直接夹在电池或电池模块之间。通常做成板状安装在电池箱底部或电池模组之间;多个PTC加热片一起使用时,应并联,不可串联,要注意与电池组/充电机的电压、电流匹配;不同散热条件使得PTC加热片的发热功率差别很大,稳定功率与使用条件有关,同一件PTC发热器,使用条件不同,则功率可能相差几倍,散热越快则稳定功率越大,PTC的表面温度越高则功率越高,所以采用导热快的铝板,或者在热风循环中直接用风扇对加热器吹风进行对流散热。
2.4 加热膜加热
加热膜有两种组成方式,一种是采用金属箔作为发热元件,通常覆以绝缘、耐压高、耐高温、强度好的聚亚酰胺膜,厚度只有0.1mm左右,也可以与其他导热材料(如导热硅胶等)组合使用,做成厚度较大、更可靠的加热膜;另一种则是以合金丝等作为发热元件,涂覆由硅橡胶与玻璃纤维布等组成的绝缘层,厚度相对较大,有几毫米左右。图2为不同形状的加热膜/板。
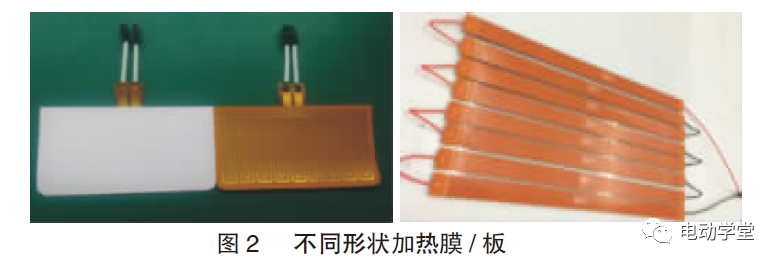
加热膜成型性好,厚度薄、质量轻、柔性好,可贴在电池壳体上,传热效率更高而且能量损失更小;通电发热迅速、温升快、发热面大、发热均匀,有利于电池箱内部温度一致性;耐腐蚀、环保、阻燃、安装方便、寿命长、绝缘强度高、击穿电压高,并且不受尺寸限制,可以根据电池或模块的结构任意弯曲,确保紧密接触,保证最大的热能传递,也可以做成板状替代PTC加热板。发热功率可以根据设计要求进行设计,对金属箔的宽度、长度或金属丝的直径和长度等予以调整,加热膜可以串并联使用。
刘存山等根据传热学原理,对比分析两种PTC 加热和加热膜加热两种方式,选用了电热膜的低温加热方法。其成本接近于PTC加热板,是电池组目前应用的主要加热方式之一。
但使用该类电热器件必须注意,其持续使用工作温度应小于240℃,瞬时不超过300℃;粘贴式安装工作温度应小于150℃;空中干烧受材料耐温限制;工作电压的选取以大功率-高电压、小功率-低电压为原则;加热膜引出端点处容易出现温度过高等现象。加热膜适用于各种类型电芯组成的电池组。
2.5 其他加热方式
(1)加热套加热
加热套加热是在每一个电池单体加上一个加热套,加热套由电阻材料制成,外部通电对电池组进行加热,加热速度快,并且单体受热均匀,能量损失小,但高温情况下电池散热较慢。
(2)珀尔贴效应加热
珀尔贴效应指电流流过两种不同导体界面时,将从外界吸收热量,或者向外界放出热量。利用此性质,通过改变电流方向,可以实现加热和制冷两种功能,强度可以通过电流大小进行精确控制。ALAOUIC等做出了利用珀尔贴效应对电池组进行加热和冷却的装置,该装置还可以替代汽车空调。
(3)相变材料保温与加热
相变材料蓄热能力强,在达到相变温度时可以大量吸热或放热而温度不变。选用合适的相变材料能够使电池单体有效地达到热平衡,可以很好地控制电池温度上下限,避免产生温度过高或过低现象,但是成本较高。相变材料本身不能产热,但在车辆行驶过程中或电池组充电过程中,温度在上升,相变材料能储存部分热量,可以在低温环境下延缓电池组搁置温度的下降速度,解决车辆低温停驻问题,降低能耗。
3 电池组的保温
如果电池箱内各部位散热条件不一致,即使加热效果很好,也有可能造成较大的温差,影响电池组使用寿命和加热效果。如在金属电池箱底部直接安装加热板,上面放置电池模组,在温度较低情况下,由于电池箱底部散热本身比较快,造成热损耗较大,实际电池组会很难加热到所要求的温度。
对电池箱体进行保温设计可以有效提高加热效能和温度一致性,适用于动力电池组的保温材料主要有高分子改性泡沫材料、气凝胶等。保温材料应满足下列性能指标:
(1)导热系数小;(2)阻燃,达到UL94-V0级,且在温度较高时不会产生有毒气体;(3)吸水率低;(4)抗老化,与电池组同寿命甚至更长;(5)应用在电池箱底部时,抗压缩性要好。其他还有如密度、抗化学性能、尺寸稳定性等。
保温材料多为有机绝缘材料,如聚氨酯、聚苯乙烯、聚乙烯等,其中聚氨酯泡沫塑料是保温性能较好的一种保温材料。硬质聚氨酯的导热系数为0.023W/(m·K),材料密度约40kg/m3(可调整),比热容为2380J/kg,作为电池组的保温和结构材料已成功应用。
新型的气凝胶是另一种保温材料,其孔隙率高,密度低,室温导热系数可达0.013W/(m·K)。但由于抗压性差,不能直接被电池模块压迫,需要对模块的安装方式进行特殊设计。图3为几种隔热材料导热系数对比。几种加热方法的特点比较如表1所示。
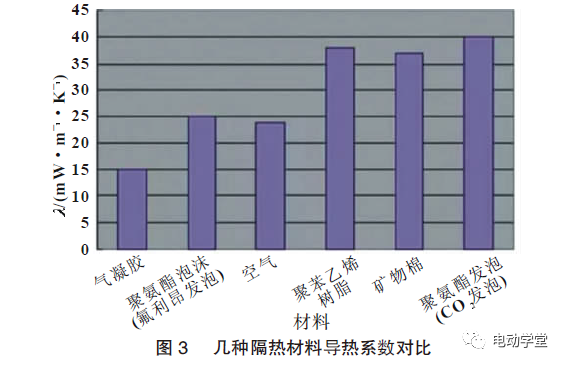
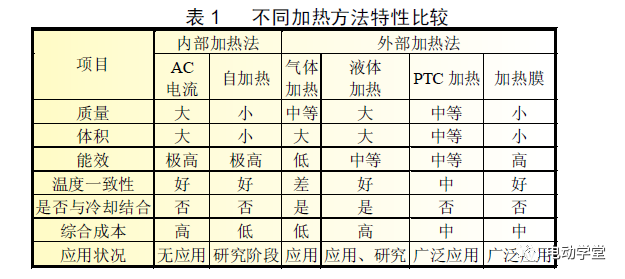
4 热控设计细节或者应考虑的其他因素
除了选择合适的加热方法外,还需考虑温度采集点的位置以及温度控制策略。内部加热,采集点布置在电池极柱、汇流板等上面,采集温度低于电池内部温度;外部加热时热量最先传递到的是电池外壳,采集温度高于电池内部温度,不同电芯其滞后时间不同,还与加热方式、加热速度、传热情况等有关。采用外部加热时,通常将加热的控制温度比所需求的温度高5~10℃。随着新材料、新技术的发展,更经济实用的加热方式和加热技术将会不断涌现。
最新资讯
-
推荐性国家标准《乘/商用车电子机械制动卡
2025-04-30 11:13
-
载荷分解
2025-04-30 10:46
-
布雷博在上海开设亚洲首个灵感实验室
2025-04-30 10:25
-
组分性能对锂离子电池卷芯挤压力学响应的影
2025-04-30 09:00
-
美国发布自动驾驶新框架,放宽报告要求+扩
2025-04-30 08:59