乘用车模块化电驱动后桥设计原则研究
本文基于电动汽车特点及某SUV整车平台的开发需求,提出一种乘用车电驱动后桥底盘架构模型,基于该架构模型,研究了电驱动后桥悬架结构选型原则、后桥模块布置原则与模块化平台化设计原则,且完成了具有较高平台拓展性的模块化电驱动后桥概念设计。
1 电驱动后桥底盘架构设计
1.1 设计目标
根据某SUV整车平台车型规划,需开发一套电驱动后桥底盘模块,兼顾纯电动后驱车型及PHEV混动四驱车型需求。表1所示为该SUV平台车型基本参数。表2所示为后桥电驱动总成基本参数。
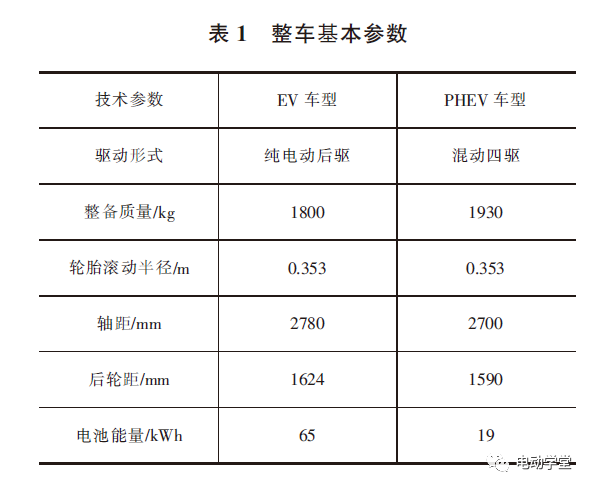
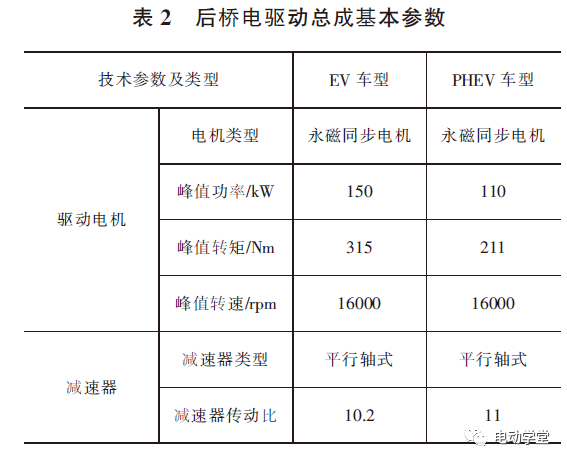
1.2 电驱动后桥底盘架构设计
根据开发需求,结合纯电动汽车及混合动力汽车整车特点,建立模块化电驱动后桥底盘架构模型,如图1所示。
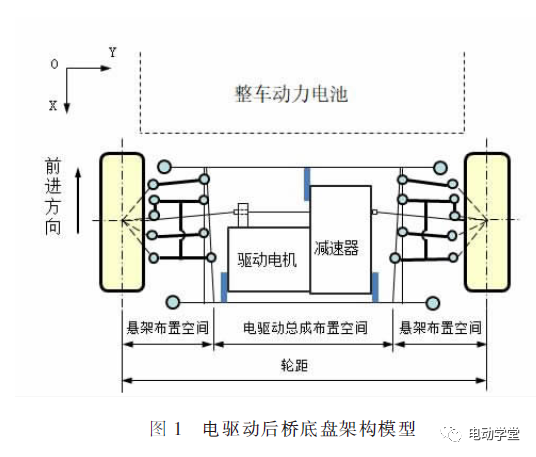
基于该底盘架构模型,模块化电驱动后桥由电驱动总成、后副车架、后悬架、电驱动总成悬置、后桥驱动轴、后制动器带转向节总成组成,其设计要点分析如下。
1)燃油汽车总布置时主要围绕乘员和动力总成进行设计,而电动汽车总布置时除了关注乘员和动力总成,还需要考虑整车动力电池[1]1,电驱动后桥关键系统及零部件选型与布置需要适应这几个部分的空间。
2)纯电动汽车增加了动力电池的重量,整车质心位置向下和向后移动,后悬架负荷增大,需选择承载能力更强、操控性能更好的悬架结构形式。
3)相比于燃油发动机,电驱动总成更为紧凑,体积小扭矩大,且扭矩响应快[2],对电驱动总成悬置系统抵抗扭矩的要求更高;且相比于前舱车身结构,后部车身的局部刚度偏小,后桥电驱动总成悬置的布置需考虑电驱动总成刚体模态与周边子系统模态频率避开。
4)相比于内燃机的低频点火、机械和燃烧噪声,电动汽车的主要噪声变为电磁力和齿轮啮合产生的高频啸叫声,且由于没有内燃机工作噪声的掩蔽,这些高频单调噪声在特定工况下会比较显著,需从后桥模块的结构设计上加以控制。
5)根据底盘电动化和平台化发展的趋势,电驱动后桥的设计应具有一定的平台拓展性和兼容性,以匹配不同车型的轮距和轴距需求,兼容不同结构尺寸的电驱动总成。
2 悬架结构选型
作为驱动车桥,对后桥悬架结构及性能提出了更高的需求。本章基于常见独立后悬架结构及其在整车上的布置特点,分析与选择适合于纯电动汽车后驱动桥的悬架结构形式。
2.1 连杆支柱式悬架
连杆支柱式悬架是由麦弗逊悬架演变而来的一种后悬架形式,主要由两根横向连杆、一根纵向拖曳臂以及滑柱总成构成。其中一根横向连杆与纵向拖曳臂组合,起到控制臂的作用,且和滑柱总成一起控制车轮外倾角;另一根横向连杆主要用于调节与控制车轮前束角;拖曳臂同时还能控制车辆的纵向稳定性。连杆支柱式悬架结构及其在整车上的布置特点如图2所示。
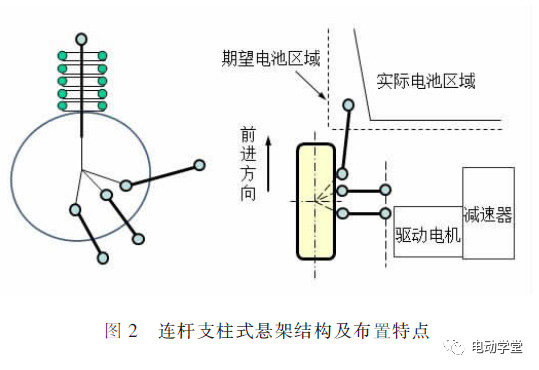
连杆支柱式悬架的结构特性与麦弗逊悬架基本相同,虽然对车轮外倾角的控制有些先天不足,侧向支撑能力也相对差一些,但通过横向稳定杆的设计和弹性元件的匹配调整,可以改善其侧向支撑能力不足的情况。
连杆支柱式悬架结构简单,重量轻,其横向连杆的布置特点有利于电驱动总成的拓展空间;但其纵向拖曳臂的布置特点,对动力电池的宽度限制较大,通常动力电池包只能设计成滑板形状。
2.2 拖曳臂多连杆式悬架
拖曳臂多连杆式悬架是中级轿车较为常见的一种后悬架形式,主要由纵向拖曳臂、下控制臂、上控制臂、前束拉杆、螺旋弹簧和减振器构成。其中,悬架的承载主要由下控制臂承担,其余拉杆主要起导向作用;车轮外倾角和前束角分别有一根连杆独立控制,其悬架性能的实现更少依赖于衬套的调教;纵向拖曳臂主要控制车辆纵向稳定性,其前衬套起纵向弹性和振动过滤的作用。拖曳臂多连杆式悬架结构及其在整车上的布置特点如图3所示。
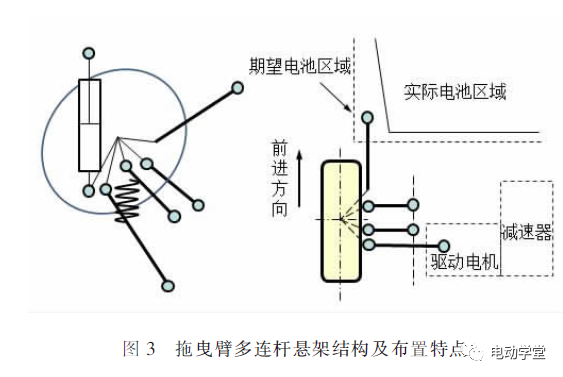
通过各连杆布置及衬套刚度设计,拖曳臂多连杆式悬架可精确地控制车轮定位角的变化规律,获得良好的操纵稳定性和行驶平顺性。
为控制悬架侧倾变化率,其下控制臂一般设计相对较长,对电驱动总成横向布置空间产生较大的限制,不利于大功率电驱动总成的布置;且其纵向拖曳臂的布置特点,对动力电池的宽度限制较大,因此,基于布置的角度,拖曳臂多连杆悬架不适合于纯电动汽车电驱动后桥。
2.3 五连杆悬架
五连杆悬架是由双横臂悬架演变而来的一种高端舒适的后悬架形式,将双横臂悬架的上下叉臂均改为了连杆。五连杆悬架通过各连杆的配合来限制转向节的运动,需要至少两根连杆的内侧硬点在X方向延伸较多,以保证转向节前后方向与翻转方向的限制刚度;其余三根连杆则垂直于车轮平面按直线布置,主要以承受悬架的侧向载荷,且增强了悬架的侧向刚度。五连杆悬架结构及其在整车上的布置特点如图4所示。
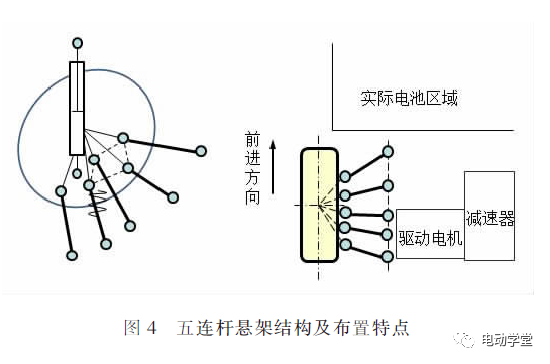
五连杆悬架的横向尺寸相对较小,有利于大功率电驱动总成的布置;但其X方向延伸较多的两根连杆的空间布置特点,使得副车架纵向边界对动力电池长度产生一定程度上的限制。
2.4 H臂多连杆悬架
H臂多连杆悬架是由拖曳臂多连杆悬架演变而来的一种后悬架形式,主要由H型控制臂、上控制臂、前束拉杆、桥接杆、螺旋弹簧和减振器构成。其中,横向布置的H型控制臂其内侧两个安装点与外侧的一个安装点构成了一个类似三角形的控制臂,可有效分解车轮的横向载荷与纵向载荷,因此H臂多连杆悬架不需要纵向拖曳臂;H型控制臂的外侧还通过一根Z向布置的桥接杆与转向节连接,可有效控制车辆在驱动和制动时转向节绕车轮轴线的翻滚。H臂多连杆悬架结构及其在整车上的布置特点如图5所示。
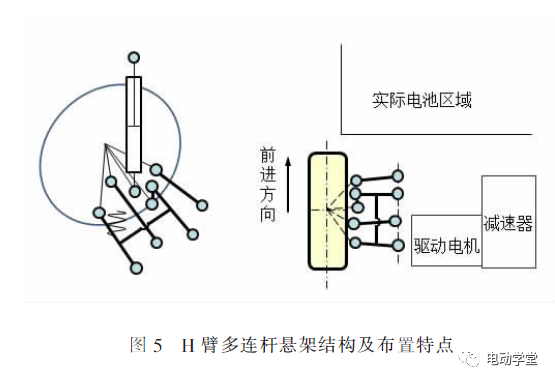
H臂多连杆悬架导向机构,在整车纵向及横向占用空间较小,有利于动力电池和电驱动总成的布置;悬架各连杆的功能解耦性较好,降低了悬架系统的开发与调校难度;H型控制臂通常采用中空式铸铝结构,其刚度较高,可获得更干脆的路感。因此,结构紧凑、性能优越的H臂多连杆悬架,被广泛应用于电驱动后桥。
2.5 悬架选型结论
基于悬架性能、布置空间及平台拓展能力分析,H臂多连杆悬架和五连杆悬架更适合于纯电动汽车后驱动桥,综合悬架系统性能调校难度,最终选择了H臂多连杆悬架结构形式。
3 电驱动后桥布置原则
本章基于电驱动后桥底盘架构及关键零部件特点,分析与研究电驱动后桥底盘架构布置过程中关键尺寸因子的影响关系及子系统布置原则。
3.1 电驱动总成位置定义
电驱动总成位置定义主要包括电驱动总成初始设计姿态及在整车上的位置定义。根据电机旋转轴和减速器输出轴的相对位置不同,平行轴电驱动总成初始设计姿态可分为电机前置和电机后置两种形式。为提供更多的X向空间以布置整车动力电池,纯电动汽车后桥电驱动总成较多采用电机后置的姿态形式。
电驱动总成整车布置位置定义,主要考虑驱动轴布置角度和周边布置间隙要求。减速器输出轴位置定义需满足驱动轴布置角度小于5度,且电机扭矩越大,对驱动轴布置角度要求越严苛;电驱动总成Y向布置空间,主要受轮距及车身纵梁宽度限制,轮距越大,电驱动总成的Y向布置空间越自由;电驱动总成Z向布置空间,主要受车身地板高度及离地间隙限制,车身地板作为承载件,更多的还要考虑室内座椅及人体的布置。
3.2 电驱动总成悬置布置
传统燃油发动机悬置系统通常采用扭矩轴(TRA)布置和模态解耦设计理念,其目的是通过提高悬置系统的隔振能力,以控制内燃机的燃烧及曲轴旋转产生的扭矩波动及不平衡力矩所引起的振动向车身传递。
驱动电机的扭矩波动激励较小,其激励主要来源于电磁力和齿轮啮合产生的高频振动,频率远高于电驱动总成的刚体模态频率,通常不会与电驱动总成刚体模态产生响应或共振;但相比于前舱车身结构,后部车身的局部刚度偏小,后桥电驱动总成悬置的布置需考虑电驱动总成刚体模态与周边子系统模态频率避开;且通常驱动电机的扭矩大,扭矩响应快,对车体的瞬态冲击大,特别在tipin/tipout工况下很容易造成车体前后抖动。因此,电驱动总成悬置设计匹配的着眼点则应该是电驱动总成刚体模态分布及扭矩,在兼顾电驱动总成刚体模态与周边子系统模态完全分离的同时,更多的偏向于控制电驱动总成的瞬态冲击,即确保在扭矩快速变换情况下,悬置系统能够对电驱动总成的位移、转角等姿态变化产生明显的限制作用,从而降低车辆行驶过程中产生的顿挫感,提高驾乘感受。
图6~图9为后桥电驱动总成悬置系统的四种布置形式。基于相同的电驱动总成转动惯量与扭矩、相同的悬置刚度曲线,对电驱动总成姿态的变化(主要考虑扭矩轴坐标系下绕Y轴的旋转角度Ry)和悬置受力进行分析,得到如下结果。
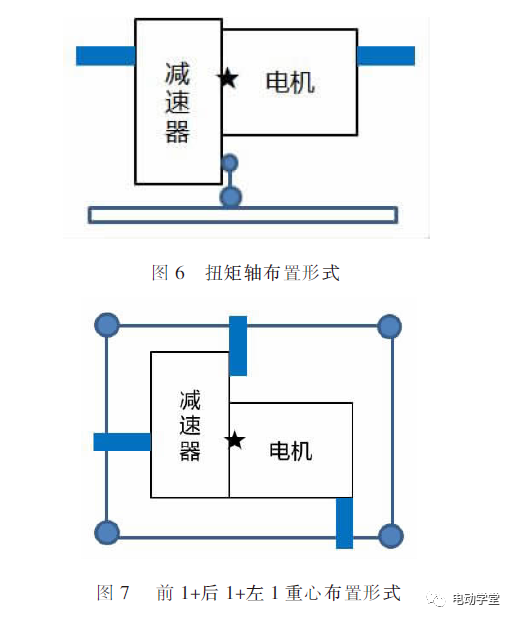
1)图6扭矩轴布置形式下,电驱动总成绕左右悬置连线的转动趋势最为明显,其姿态变化和防扭拉杆后悬置受力均是其它布置形式下的2倍以上,需通过大幅增加防扭拉杆后悬置X向刚度来提升其抗扭性能,这将会在一定程度上降低悬置的隔振率。
2)图7、图8均为三点重心布置形式,通过三个悬置点构成一个几何面,以抑制电驱动总成的翻转、滚动趋势;根据其布置特点,前后悬置同时起抗扭作用,左或右悬置主要起约束刚体模态的作用。经过分析,两种布置形式对电驱动总成姿态的控制能力基本相当,且明显优于传统的扭矩轴布置形式。
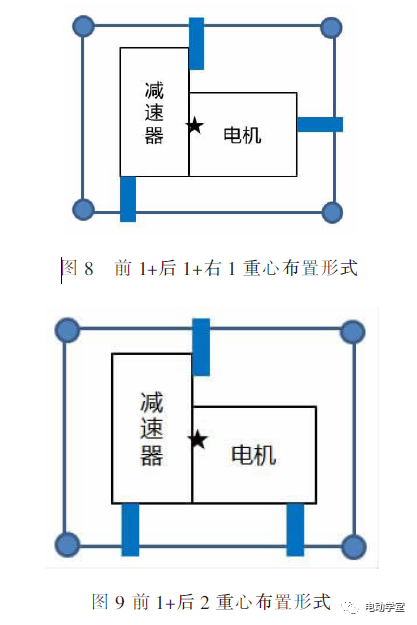
3)图9同样为三点重心布置形式,相比于图7、图8所示布置形式,其特点为电驱动总成质心位于三个悬置点所构成的三角形的中心位置,且抗扭悬置数量由2个增加至3个;通过悬置点位置的优化调整,可使得3个抗扭悬置所承载的扭矩载荷基本相近。因此,基于对电驱动总成运动趋势控制、抗扭能力及悬置受力均匀性考虑,图9所示布置形式较优。
综上分析,电驱动总成悬置通常采用三点或四点重心布置形式,即在俯视图上电驱动总成的重心落在各悬置弹性中心点所形成的三角形或四边形区域内,并通过悬置点布置位置的优化,使各悬置受力趋向均匀,以采用刚度相对较小的悬置软垫设计,在控制电驱动总成姿态变化的同时获得更好的整车驾乘感受。
3.3 悬架杆系布置
悬架杆系布置其实就是悬架硬点的设计与优化过程。根据整车架构尺寸、布置边界、悬架行程等初步设定悬架零部件的基本尺寸和关键硬点,并采用参数化建模的方式建立多体动力学仿真模型。基于动力学模型,通过DOE方法进行悬架运动学灵敏度分析,确定对悬架运动学特性影响较大的悬架硬点并进行位置优化,以满足整车动力学性能目标。悬架硬点的优化调整需满足周边布置间隙要求,需基于悬架系统DMU分析,对轮胎、驱动轴、稳定杆等关键零部件的运动包络进行校核,检查零部件布置的合理性。图10所示为优化后的H臂多连杆悬架结构。
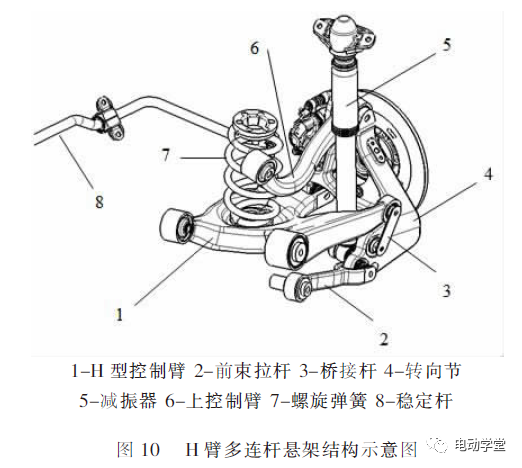
基于模块化电驱动后桥架构的H臂悬架主要布置特点与要求如下。
1)H型控制臂内侧前后两个安装点通过橡胶衬套与副车架连接,外侧的后安装点通过球销与转向节连接,外侧的前安装点通过桥接杆与转向节连接,根据布置空间,桥接杆可以布置在H臂的上方或者下方。
2)H臂的Y向长度和布置方向决定悬架的侧倾中心高度和纵倾中心高度,通常根据悬架运动学特性来优化调整确定。在满足布置边界的条件下,H臂的Y向越长,车轮跳动时弹簧受力越小,有利于减小弹簧刚度。实际布置过程中,H臂Y向长度还受轮距及电驱总成尺寸制约,如果搭载更大的电驱动总成,其轮距也需相应增大。
3)上控制臂的长度和布置方向同样根据悬架运动学特性来优化调整,并结合车身后地板纵梁边界、减振器位置和驱动轴运动包络来综合确定。
4)前束拉杆通常布置在H臂悬架的最前端,H臂的上方或者下方,其长度和和布置方向根据悬架的不足转向特性优化结果,并结合车身后地板纵梁高度、悬架离地间隙来综合确定。
5)减振器和弹簧采用分开布置,根据H臂悬架杆系的纵向分布特点,减振器和弹簧分别布置在上控制臂的前方和后方,同时考虑上控制臂的运动包络。
4 电驱动后桥模块化与平台化设计
4.1 模块化设计
根据底盘电动化和平台化发展的趋势,电驱动后桥采用模块化设计。后副车架作为电驱动后桥模块化设计的载体,采用框式结构设计,其两侧主要连接悬架导向连杆,且需避让驱动轴运动包络;除了连接悬架导向连杆之外,后副车架还需连接与支撑整个电驱动总成。
通过模块化设计,可提高悬架系统整体刚度,获得精准的悬架运动特性,提升车辆操纵稳定性;电驱动后桥模块通过副车架上的四个橡胶衬套与车身连接,相当于在悬架和车身之间、电驱动总成和车身之间增加了一级缓冲与隔振,减轻了车身的负荷,且通过副车架衬套的二级隔振,可有效降低路面及电驱动总成的高频振动,提升车辆舒适性。
如图11所示为模块化电驱动后桥结构。
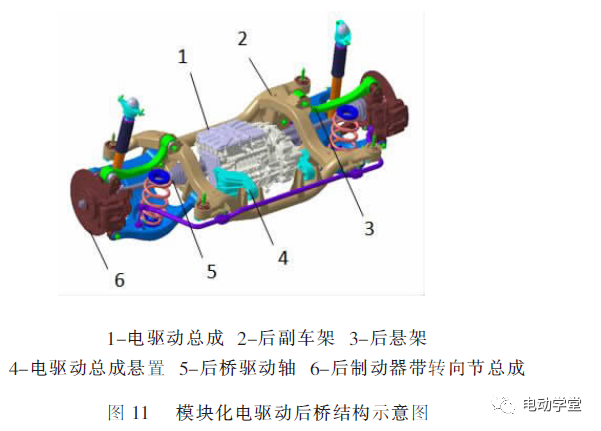
4.2 平台化设计
在模块化设计的基础上,电驱动后桥总成具有一定的平台拓展性与兼容性。拓展性是指通过模块化设计以匹配不同的轮距和轴距,进而适配平台内不同尺寸和级别的车辆;兼容性是指通过较小的设计更改以匹配不同结构尺寸的电驱动总成。

图12、图13所示为平台化电驱动后桥副车架常见的两种工艺结构。基于平台化设计要求,副车架前后横梁的前后跨距根据平台规划的电驱动总成布置需求设计;且副车架前后横梁的中间部位采用钢管结构或铝型材焊接结构,以实现一定范围内的轮距拓展及不同结构尺寸的电驱动总成拓展;在平台拓展时,可保持悬架连接硬点的相对位置不变。
5 结束语
本文基于某SUV整车平台电驱动后桥概念布置阶段的架构分析、结构选型和集成设计,分析与研究了乘用车电驱动后桥关键结构选型与设计原则,并通过后桥模块化与平台化设计,实现了不同整车轮距与不同结构尺寸的电驱动总成的拓展,且在平台拓展时可保持悬架连接硬点的相对位置不变,缩减了悬架系统的开发调校周期与成本。
编辑推荐
最新资讯
-
大卓智能端到端直播实测,16公里复杂路段挑
2025-04-25 17:16
-
《汽车轮胎耐撞击性能试验方法-车辆法》等
2025-04-25 11:45
-
“真实”而精确的能量流测试:电动汽车能效
2025-04-25 11:44
-
GRAS助力中国高校科研升级
2025-04-25 10:25
-
梅赛德斯-AMG使用VI-CarRealTime开发其控制
2025-04-25 10:21