基于赛车序列式变速箱的气动换挡系统设计
前言
赛车运动中,对于赛车所搭载的序列式变速箱而言,拨片换挡相对传统手动机械换挡具有较大的性能优势。而气动换挡作为拨片换挡的一种较为经济的方式,可以在较低成本的前提下获得较大的性能提升,解放车手的双手,有效的提高赛车在各个项目的成绩。
本文从FSAE大学生方程式赛车的设计需求出发,针对赛车所采用的WR450发动机及其自带的序列式5档变速箱,设计了一套气动换挡系统。满足了FSAE赛车快速、便捷换挡的目的,明显地提升了赛车性能,同时也具有较好的经济性。
1 气动换挡系统原理
1.1 换挡技术概述
拨片换挡技术最早起源于 F1 赛车,近些年在乘用车上也逐渐流行起来。拨片换挡即在方向盘后面加装拨片,换挡过程中,驾驶员手不需离开方向盘,不用脚踩离合器,只需拨动拨片,利用方向盘后拨片的开关信号通过自动控制来实现换挡。这种换挡的主要优势在于使驾驶员能够更加快速的完成换挡操作,另外对于换挡的时机和换挡力的控制也更加精确,大大提高了赛车操纵性能。换挡的执行机构通常有气动和电动两种形式:
气动换挡:即利用气缸等执行机构对换挡杆施加推力和拉力,实现换挡。气动换挡系统一般包括气体、压缩机、储气的气瓶、减压阀、电磁阀、气缸以及控制器等部件,通过电信号控制压缩气体经由气缸执行换挡动作。在乘用车上,普通 H 型手动挡的换挡至少需要两个气缸,才能完成 X 和 Y 轴两个方向的动作。而在赛车上所常见的序列式变速箱只需要一个气缸即可实现升档和降档,设计较为方便,控制上也容易实现。
电动换挡:电动换挡的形式有很多,常见的换挡执行器有齿轮马达、电磁推杆等等,利用马达提供的扭矩或电磁推杆的推力完成换挡动作。为了实现高速换挡,需要执行器瞬时提供强大的扭矩或推力,这些用电设备的瞬时电流也会非常大,对电压的管理要求相对较高。同时高扭矩(或高推力)的马达或电磁推杆在国内很难买到, 价格也较昂贵,故从系统落地周期以及成本角度考虑,可行性相对较低。
所以对于FSAE大学生方程式赛车,气动换挡是在综合考虑成本、性能、开发周期、安全性等因素下的最优选择。故本文选择气动换挡系统进行开发设计,应用在FSAE赛车上。
1.2 气动换挡系统原理
对于一般乘用车而言,升档操作包括以下几步:踩离合、松油门、换挡、松离合、补油。要想完成一次平顺的换挡,使车辆运行无顿挫感,需要以上步骤精确的配合。而气动换挡系统的设计要求,就是要做到车手只需要触动拨片开关, 不踩离合,不松油门,就可以由换挡系统自动执行以上几个步骤。
本文所要设计的气动换挡系统,是针对FSAE赛车上所搭载序列式变速箱的换挡辅助系统。由于序列式变速箱换挡只有上下两个动作,相比于普通H挡手动变速箱操作简单,换挡时间短。而且因为只能按顺序依次换挡,所以不容易损坏变速箱。这样简单的换挡动作,可以用一个双作用气缸代替完成。
整个换挡系统除了变速箱,一般还包括拨片信号触发机构、用于储存气体的气瓶、降低气压的减压阀、控制气体的电磁阀、用于做功的气缸及其他执行机构、以及相关的信号采集检测与控制系统。
下图为本文设计的气动换挡系统示意图,其中包括气路部分布置与电路布置。鉴于换挡系统的复杂性,本文中基于自主研发的控制电路模块,将仅针对信号采集以及控制气缸完成换挡动作的过程,而暂不介绍与离合器控制相关的控制与和 ECU 有关的断油补油控制。
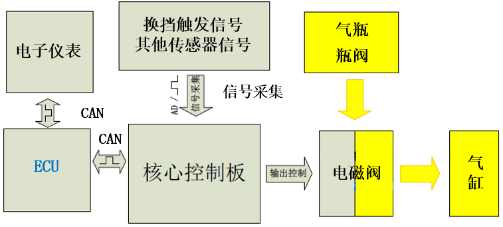
图1 气动换挡系统原理图
2 气动换挡系统设计方案
基于换挡系统的原理图,本文将换挡系统细分为换挡拨片机构、换挡执行机构、充放气气路、换挡电气控制等四个子系统。现对这四个子系统的设计进行分别介绍。
2.1 换挡拨片机构设计
换挡拨片作为换挡的触发机构,是车手控制换挡系统的唯一纽带。该机构的设计不仅应该注重稳定性,还要保证一定的拨片手感。
2.1.1 拨片开关
拨片开关用于换挡信号的触发,是换挡控制系统的重要部件,故其选型主要考虑到使用稳定性。本设计选用的开关为防水防爆开关。耐压值为250V,最大电流2A,接触电阻50毫欧。绝缘电阻100M欧。使用温度为-20度到85度。寿命为20万次。以上参数完全可以满足其在赛车上作为换挡开关的使用要求。
2.1.2 拨片机构设计
拨片机构如图2,包括抬高垫圈、延伸垫片、拨片支架与拨片。
拨片固定在拨片支架上。车手通过拨动拨片按下开关,触发换挡操作。同时拨片设计尺寸较大,为了能够让车手在驾驶的同时,更加方便的找到拨片,实现“盲操作”。
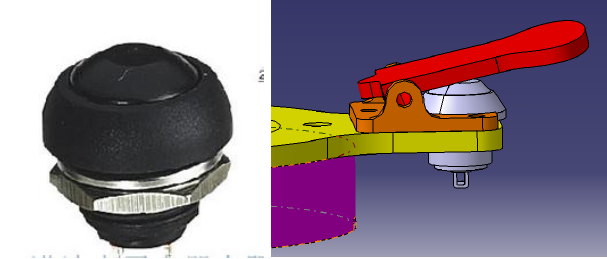
图2 按钮选型与拨片设计细节
2.2 换挡执行机构设计
换挡动作的执行机构主要由气缸、换挡臂与气缸支架组成。气缸作为换挡机构的动力执行机构,选型尤为重要,气缸的主要基本参数有缸径与行程。要想成功换挡,需要有两个必要条件,即足够的换挡力以及足够的换挡作用角度。在气压一定的情况下,换挡力主要由气缸的缸径决定,换挡作用角度由气缸行程和换挡摇臂共同决定。
通过查询技术参数,赛车搭载的序列式变速箱需要的换挡力大致为约为11.25Nm,所需换挡角度约为32度。在满足换挡力与角度要求的同时,为了保证换挡的成功率与换挡速度,应该尽量减少充气时间和作用过程,这样才能够缩短换挡时间,提升赛车性能。
首先对气缸尺寸进行设计。原则上,为了使气缸快速充气,减少换挡时间,所以应该尽量用最大的气压来工作。市场上气缸的耐压值一般为0.7MPa~1MPa不等。而缸径有12mm、16mm、20mm、25mm等各类气缸。这样,可以方便的得出各个气缸可以提供的最大输出力分别约为:90N、161N、251N、393N。
变速箱自带的换挡摇臂原长大约为90mm。根据换挡所需扭矩,从而可以推算出需要气缸施加的换挡力大约为125N。这样就初步选定了缸径16mm的气缸作为执行元件。因为气缸的耐压值为8bar,故此气缸能提供的最大输出力为:
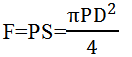
得出F=160.85N。而根据换挡所需扭矩11.25Nm来计算,可以得出所选气缸所对应的换挡长度约为70mm,下图即为设计的换挡原理图。左图初始状态下,气缸活塞位于中部,且气缸与换挡摇臂垂直。右图为换挡过程中,换挡摇臂的上下极限位置角度,即可得到气缸上下的行程,从而确定气缸的有效行程。
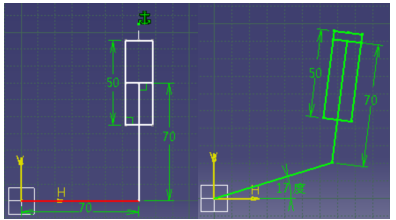
图3 气缸行程原理图
从图中可以看出,要提供32度的转角,50mm的气缸行程即可满足需求,且正好有一定的余量。
根据上述计算得到的相关参数与选型,并结合实际的整车布置情况,本文对整个换挡执行机构进行了设计。下图是换挡机构的实际三维模型设计,包括了换挡摇臂、气缸支架、气缸、电磁阀与电磁阀支架。
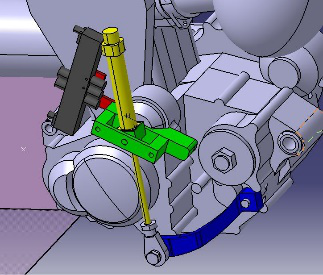
图4 换挡执行机构设计建模
由于发动机输出链轮与用于支撑链轮力的支架都为整车主要承力部件,其形状都经过了拓扑优化的分析与严密设计,所以不方便改动,换挡机构只能避免与这些机构造成干涉。气缸输出轴的直径为8mm,攻有0.8mm螺距的螺纹,连接一个杆端轴承。轴承与换挡摇臂末端连接,连接处安装带有橡胶垫的螺栓,防止换挡瞬间冲击过大而造成的结构损伤,提高机构寿命。
气缸支架固定在发动机支架上。参见图4。气缸动作时,会有轻微的扭转,所以气缸支架设计成可以带着气缸绕着固定轴旋转,同时在行程的极限位置又保证不会与电磁阀相干涉。
2.3 充放气气路设计
要实现气动换挡,气源不可缺少。从上节的计算可以得出,成功换挡需要为气缸提供至少8个大气压的气体,作为动力源。由于FSAE赛车是一辆单座小型赛车,整车质量约为200kg左右,质量最轻的赛车仅需150kg左右。所以在车上加装空气压缩泵等机构会对赛车重量带来较大影响,而且对只有33kW的发动机也会构成不小的负担。所以,本文将压缩好的气体存放在气瓶里,当作气动系统的气源。
本文采用二氧化碳作为推动气缸做功的气体,主要考虑到它易液化的性质。这样,在一定的气瓶体积下,气体以液态的形式存在于气瓶中,能够保证比赛过程中更多次的使用。气瓶的选型包括气瓶材质与体积。另外由于气瓶的应用领域较广,所以气瓶的接口各异,选型也应考虑的瓶头阀的选型。
2.3.1 气瓶设计选型
气瓶的容积根据气体的需求量来确定。根据经验,整场比赛总共需要换挡300多次,加上安全系数,取500次作为气瓶能够提供给气缸做功的次数。假设每次换挡都用尽气缸半缸的气体,且整个过程气体温度不变,忽略二氧化碳气化吸热带来的影响。依据理想气体状态方程:

可知当气体温度不变时,气体在各状态下的气压与对应的体积的乘积应该等于一个定值。即常用到的一个推论:
PV=PV1+PV2+PV3··· (3)
式中P,V为气瓶内的初始体积与压强。Pn,Vn为每次放气的体积和对应的压强,当每次放气的压强和体积相等时:
PV=nP0V0 (4)
式中,P0V0是每次放出的体积与压强,n为放气次数。当放气次数要求为500次,选用内径16mm,换挡行程为25mm(单次换挡行程为气缸总行程的一半)的气缸时:
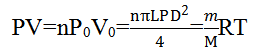
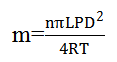
将数据带入上式。可以得到最终需要的气体质量m约为36g。而二氧化碳液态时密度与水相当,所以只需要不到0.1L的气瓶就可以满足要求。为了保守起见,本文选用0.4-0.5L的气瓶,同时也可以提高换挡机构的持续使用性。
同时,考虑到碳纤维气瓶耐压值一般可达30MPa,质量也非常轻,正符合了赛车对于轻量化的要求,能够最大限度的符合对性能的追求。故选用碳纤维材质的气瓶来储存液态的二氧化碳。
2.3.2 气管与减压阀的设计选型
二氧化碳在气缸做功时,气压约为0.8MPa,即8bar。所以可以选用PU管作为传送气体的介质。PU管标称耐压值为10bar,实际耐压可高达16bar。
由于在气瓶中气压约为5.8MPa。所以,在气瓶出口,必须要接一个减压阀,将管内气压降至1MPa左右,才能保证气管不被压爆。同时还要有一个瓶口阀,可以控制出气的开关,允许直接通过瓶口阀向内充气。两个阀还需要与气瓶相匹配,才能发挥出最佳工作效果。
最终本文选择了容积0.5L,工作压力为50MPa的碳纤维气瓶,并找到了与之匹配的减压阀与瓶口阀,使得整套充放气装置重量仅有1.1Kg,体积也十分紧凑。
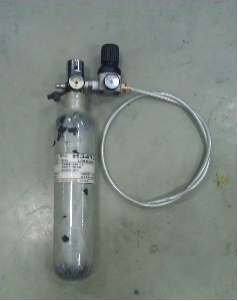
图5 充放气装置
2.3.3 电磁阀的设计选型
气动换挡过程中,需要将一路具有一定压力的气体,按照实际需求分配给双作用气缸的两个进气口,所以在本设计中要用到方向控制阀。
图6是方向控制阀的典型结构。这是一个二位五通直动式弹簧复位阀。其主要结构有:
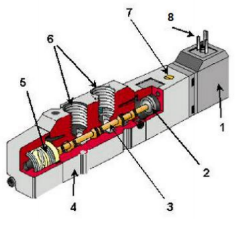
图6 电磁阀内部结构图
(1) 电磁铁
(2) 控制活塞
(3) 滑柱式铜芯
(4) 阀体
(5) 复位弹簧
(6) 出气口
(7) 手动按钮
(8) 电磁铁接线座
根据气动换挡的实际应用场景,使用频率要求不高,但需要较大的流量和压强,所以本文选用先导式电磁阀来进行气路控制。
2.4 换挡电气控制系统设计
从前几节可以看出,要完成换挡控制,需要进行换挡触发信号采集、档位信号采集、电磁阀控制等。这些功能的实现都离不开集成电路与单片机的控制。本节将简要介绍气动换挡的电气硬件部分。
2.4.1 信号采集与控制底板设计
信号采集与控制底板是单片机核心板与无线发射模块等的接口,上面还集成了许多功能模块。其设计主要为了对赛车进行数据采集、记录、无线发送、接收以及换挡控制、发动机冷却系统控制等。由于其功能针对性强,本文自行设计了此款底板,具有集成度高、体积小、功能丰富等特点。其主要功能包括:
1) 4路外部触发中断
2) 2路温度检测
3) 13路AD检测
4) 5路脉冲计数
5) 7路低端输出(1A)
6) 1路H桥(10A)
7) 1路CAN
8) 三轴加速度/陀螺仪(12位精度)
9) 时钟模块
10) SD卡记录
11) 无线数据接收/发送模块
12) 电子钥匙无线遥控器接收模块
13) 5V输出(2A)
其中换挡部分需要用到的几个功能有:
2路外部触发中断,接两个拨片触点信号开关。1路AD检测,用于检测档位。4路脉冲计数,用于测量四个轮子的轮速。CAN总线,负责与发动机ECU、仪表的信息交互。2路低端输出,用于电磁阀的控制。
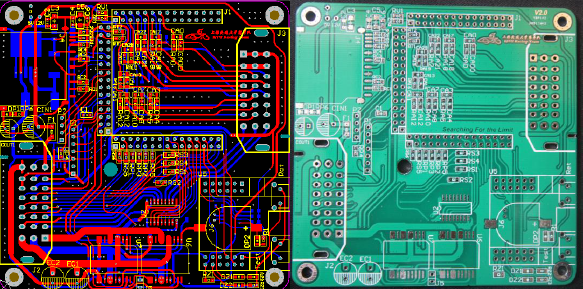
图7 数据采集电路板2.0版PCB设计与打样裸板
2.4.2 单片机简介
该单片机用在信号采集与控制底板上。在赛车上,要求单片机工作稳定,而底板的要求又较高,所以单片机采用飞思卡尔的S12系列16位单片机,型号为MC9S12XEP100MAL。
本次选用的MC9S12XEP100MAL是一款高性能双核16位单片机,它内部集成了16路,12bit的AD转换器、8路可级联的PWM、多路外部触发中断、多路CAN,SCI,SPI等总线接口,非常适合嵌入式开发。这些多功能引脚可以减少控制系统的外部元器件,简化电路,而且具有更高的稳定性和抗干扰能力。
3 换挡系统测试
对于赛车所搭载的气动换挡系统,最需要关心的是能否稳定换挡,以及单次充气后换挡次数能否达到要求。如果换挡的成功率低,则将会严重影响赛车及车手的发挥。而换挡次数不能达到要求,在赛场上将导致换挡系统的瘫痪。
在整套换挡系统中,最需要进行可靠性验证的就是换挡执行机构,因为机械结构实际的工作情况和理论计算的背景会有较大的差别,所以需要不断地进行测试和改进。
根据本文对整套换挡系统的设计,将换挡系统各个子部分进行加工制造或选型,并装配到发动机与变速箱上(如下图中所示),同时在FSAE赛车上进行了实际的测试。

图8 换挡执行机构在发动机变速箱上的装配
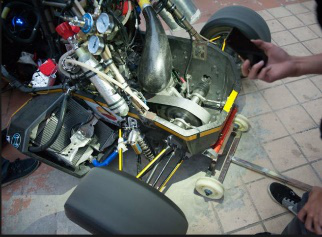
图9 换挡系统在赛车上的测试
在经过静态与动态的多次实验与测试后,结果显示,整体换挡成功率维持在90%左右,换挡延迟约为150ms-200ms,单次充气后的换挡次数也完全可以满足单场比赛的需求。系统设计基本满足了目标要求,但日后还需要进一步进行改进与优化。
4 总结与展望
本文基于FSAE大学生方程式赛车所搭载的序列式变速箱,设计并制造了一套气动换挡系统。并且通过实验,验证了整套换挡系统能够在赛车静止以及动态测试的时候顺利实现加减档操作。不仅实现了整套气动换挡装置的基本功能,满足了赛车对于高性能、快速换挡的需求,同时也一定程度上兼顾了经济性,符合FSAE比赛的原则与初衷。
另外,整套系统依然存在一些需要改进的地方。比如会出现气压不稳定、换挡卡顿、偶尔甚至会出现换不上档等问题。这就需要接下来进行进一步的优化,比如在气体利用率的提高、机械结构的拓扑优化、线束的优化、控制电路的集成化等方面进行更加深入的工作。
编辑推荐
最新资讯
-
Rivian与MAE合作定制电动车测试设备安装项
2025-04-10 14:41
-
重型商用车辆和客车的动力学——操纵性
2025-04-10 14:40
-
新能源汽车VCU、BMS、MCU控制器图解
2025-04-10 14:39
-
陶琳回应电动车辐射高:特斯拉辐射值远低于
2025-04-10 13:14
-
nCode2025版本发布说明
2025-04-10 13:12