基于热管技术的动力电池热管理系统研究现状及展望
关键词:锂离子电池,热管理,热管,强化传热,低温加热
01 热管传热特性分析与设计研究
基于动力电池的热管设计与优化
热管设计是影响传热性能的重要因素,其换热效果与通道尺寸、吸液芯结构、充液率等因素密切相关[63~66],合理的热管设计对提高电池热管理效率十分重要。
由于动力电池产热的特殊性,许多学者在针对电池的热管设计方面展开研究。Jang等人[67]研究了不同工质对回路型重力热管换热性能的影响,当电池发热量为50 W时,以丙酮为工质可控制电池平均温度低于45°C,优于以水为工质的散热效果。Putra等人[68]发现工质散热效果与电池产热率密切相关,针对不同的热源发热量,采用不同工质才能发挥热管的最大功效,当电池产热率大于1.61 W/cm2时,采用乙醇做工质的换热效率最高。Chi等人[69]研究了充液率对脉动热管换热的影响,发现热管的最佳充液率随着电池产热率的增大而提高。因此,需要针对热源条件选择适当的工质种类及充液率,以达到最佳换热效果。
当前研究大多从工质层面(工质种类、充液率)研究和优化热管用于动力电池的传热特性,也有少数文献从结构角度对热管性能进行改善。Swanepoel[70]设计了基于脉动热管的电池热管理系统,分析了介质和管道宽度对热管传热性能的影响,发现当热管内工质为氨水时,热管宽度需小于2.5 mm,才能保证其在电池热管理中的启动及散热效率。
在现有动力电池热管理研究采用了不同种类的热管,如重力型热管、烧结热管、脉动热管、平板环路热管、平板微热管等[71~73],尚无统一的选型或设计方法。从结构形式上看,平板类型热管在动力电池热管理系统中展现出优越性,有望成为动力电池热管理的首选,然而当前针对平板热管的设计研究较少。
热管布置方案设计
电池热管理系统布置方式是影响热管导热性能的另一关键因素。Tran等人[74]对比了水平与垂直放置时热管导热性能。施加38 W热源模拟电池包产热,水平布置时热管蒸发端温度达到61°C,垂直布置时温度仅51°C。饶中浩[75]采用脉动热管进行实验也得到类似的规律,搭建了如图9所示的电池热管理实验测试平台,实验表明在相同产热功率下,竖直放置时电池表面温升较小,且局部温差比水平放置时更小。
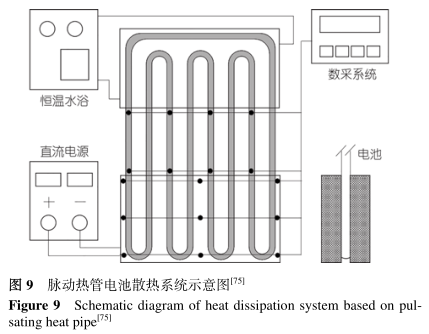
此外,装置倾斜角度也对传热造成影响[74,75]。热管水平安装时,电池表面温差受倾斜角度影响较大; 而热管竖直安装时,重力与毛细力双重作用降低热管传热阻力,路面坡度对局部温差几乎无影响。
上述研究均说明热管竖直布置时的散热及均温效果优于水平布置方式。Wang等人[76]在热管竖直布置方式下研究电池摆放方向对热管传热效果的影响,表明管内工质可迅速将高温端(电极)热量传递至冷凝端,相同产热功率下电极朝上的方式可延缓温度上升时间。
为保证热管传热性能的发挥,电池热管理系统结构设计应充分考虑热管布置方式对其导热性能的影响。
02 热管理系统散热结构设计与传热分析研究
作为电池热管理传热部件,热管吸收电池产热的同时需快速将热量散掉,以保证其在电池组中正常工作。通常情况下,热管冷端可采用风冷和水冷散热两种方式,前者结构简单,易于实现,后者结构相对复杂,但在散热需求较大时表现出更好的性能。
冷端风冷散热
热管冷凝段采用直接风冷是最简单的散热方式。Ye等人[77]对热管冷端进行强制风冷散热,可使电池(LiFePO4,18 A h)在1 C放电条件下维持在35°C以下,若冷端采用自然冷却,放电末期温度高于40°C。为强化热管散热能力,可采用增加冷端翅片数目、改善冷端翅片设计、提高风冷流速、增大冷凝段长度等方式。
热管根数、翅片个数、翅片间距对散热效果也有重要影响[60]。在一节电池表面布置多根热管可强化散热,但由于冷端沿气流方向平均换热系数越来越低,增大了电池表面温度不均匀性。通过在第一根热管前布置扰流圆管(图10(d))可提升电池表面温度均匀性。
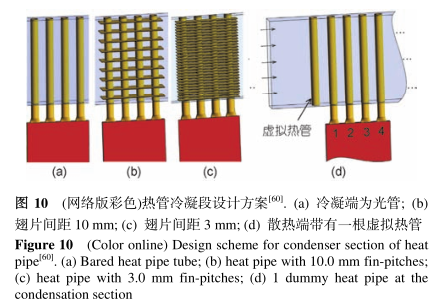
许多研究者采用热管与相变材料耦合散热方式提升电池表面均温性,将PCM附着在电池表面,热管嵌入PCM中带走热量,冷端采用风冷散热[78,79],图11是一种典型的热管-PCM耦合风冷散热系统,该结构可保证电池组2 C放电结束后最大温差低于2°C,且冷却风速会影响电池最高温升[78]。
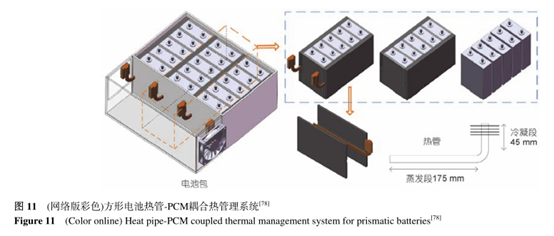
增大冷凝段长度是提升热管散热能力的另一有效途径,然而冷凝段长度增加会导致电池组温差增大,为同时保证电池组温升和温差,并考虑电池组空间布置等实际因素,热管冷凝段长度存在最佳值[80]。
03 冷端液冷散热
由于空气比热容较低,采用热管与液冷耦合散热可弥补空气冷却的不足。根据热管冷端与液体流道接触方式,可分为接触式液冷换热和非接触式液冷换热。接触式液冷系统如图12所示[81],热管冷端浸泡在水槽中,内部通入一定流速液体,2 C持续放电半小时后电池温度不超过42°C,说明热管与液冷耦合散热效果。
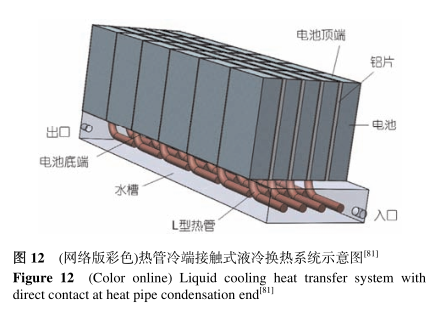
Zhao等人[82]采取冷端喷水提升电池散热效率,每两节电池之间布置一根平板微热管并向其表面以一定频率喷水,电池在2 C持续放电工况下温升仅为4°C,3 C放电工况温差小于2.5°C。
非接触式液冷系统通常将热管排布在电池表面,通过液冷流道与热管冷端接触带走热量,热管冷端并非直接浸泡在冷却液中,安全性较高[83]。奥迪公司[84]设计了如图13所示的电池热管理方案,在每两节电池之间布置一块铜板,并将4根烧结热管嵌入铜板内,最后通过贴在热管冷端表面的液冷板将热量带走。在400 W电池产热功率条件下,该系统可维持电池温度在50°C以下,具有较好的冷却效果。
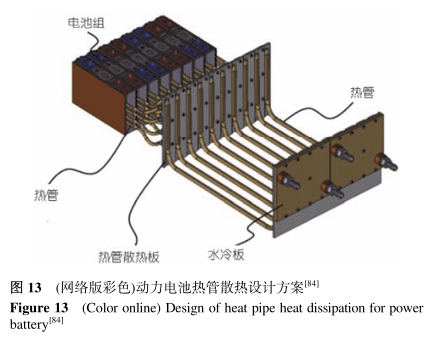
当前大部分研究以电池的温升和温差作为考核指标,然而,强化传热带来更多系统能量消耗及重量增加,较少从系统层面进行设计考量。如何兼顾电池放电特性、散热效果以及系统能耗和轻量化等指标,提出热管理系统高效散热方案,是将来在电池强化散热方面的研究重点。
04 采用热管的电池加热研究
如前文所述,低温环境下锂离子电池充放电效率大幅衰减,目前采用热管作为传热部件的低温加热研究引起广泛关注。
Ye等人[58]采用微平板热管布置在电池表面,另一端采用加热元件加热(图14),电池从-10,-20,-30°C升温至0°C所用的时间分别为350,780,1100 s,温升速率是传统底部加热方式的1.5倍。加热过程中温差可控制在3°C以下,远低于传统加热方式(9°C)。梁佳男等人[85]发现提高加热功率可提升电池升温速率,但同时增大电池表面温差,因此需要综合考虑加热时间和电池温差,以确定最佳加热策略。

Zou等人[86]设计了如图15所示的热管-液体耦合综合热管理系统,既可实现电池低温加热也可以用于高温冷却。管道内的制冷剂经过PTC加热,然后通过热管将热量传递给电池。在加热的初始阶段电池温升较快,随着热管的冷、热端温差逐渐减小,换热能力减弱,最终换热量趋近于定值,约900 s后电池温度上升至20°C。
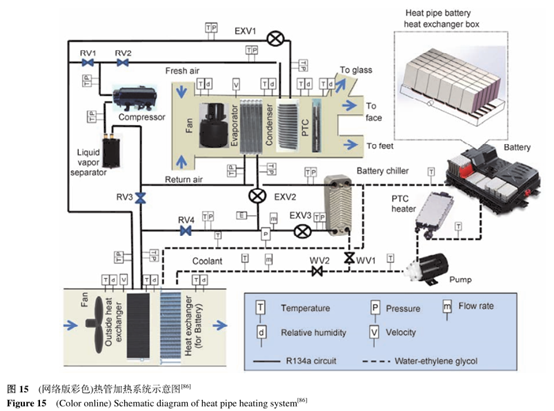
当前基于热管的电池加热系统通常采用传统热管或微通道热管布置在电池表面,另一端采用热水加热或PTC加热,研究大多处于实验验证阶段,现有研究结果充分展示了采用热管加热的高效性和均温性,进一步的研究应围绕低温加热策略展开。
05 总结与展望
温度是影响动力电池性能的关键因素,高效热管理系统对电动汽车具有重要意义。热管具有较强的换热能力和均温能力,是未来电池热管理系统的重要研究方向。
采用热管作为电池散热/加热元件的研究已经取得显著进展,但是随着电动汽车对热管理系统要求的提升,热管的应用目前还存在几方面问题亟待解决:
(1) 动力电池温度与其动态产热工况密切相关,进一步的研究应结合实际车用工况,制定有效的实时控制策略,从而实现高效、低能耗电池热管理。
(2) 热管传热方面,由于影响热管传热性能因素众多,需要综合考虑热管内部结构设计及其在电池组中的布置方式,优化其在使用过程中的传热性能,特别是针对平板类型热管的传热特性分析及优化设计研究,是将来研究的重点之一。
(3) 热管散热方面,当前大部分系统设计侧重于降低电池组温升及温差,较少考虑系统能耗与重量。进一步的热管强化散热研究应聚焦于系统多目标优化,综合系统热、电特性以及系统能耗和轻量化等指标,提出热管理系统散热解决方案。
(4) 采用热管的加热研究方面,当前的研究大多处于测试并验证效果阶段,进一步研究热管在不同使用环境下的换热特性,特别是低温环境下的加热策略研究,是将来研究的重点之一。
随着电动汽车的发展,动力电池技术和热管技术的不断进步,热管在电池热管理中将得到更加广泛的应用。
编辑推荐
最新资讯
-
2025智驾“封神榜”测评|小鹏MONA M03智车
2025-04-29 18:24
-
风噪测试在电动汽车时代的关键作用
2025-04-29 11:34
-
汉航车辆性能测试系列之操纵稳定性测试--汉
2025-04-29 11:09
-
新能源汽车热管理系统验证体系PITMS正式发
2025-04-29 11:09
-
试验载荷谱采集
2025-04-29 11:07