新能源汽车动力电池CTP技术
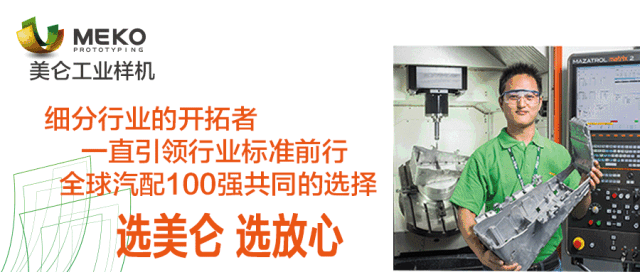
动力电池作为新能源汽车的三大件之一,其重要性必然是不容小觑的, 但多年来,动力电池的成本一直居高不下,占到整车成本的40%,甚至更高,许多电池供应商和主机厂一直在寻求降低电池成本的方案。现有的电池pack结构由三级组成:电芯(Cell)、模组(Module)、包(Pack);当然,它们之间的关系我们可以这样理解,最小的单元是电芯,一组电芯组成一个模组,多个模组组合再加上BMS、配重模块等零部件则组合成我们所说的“电池pack结构”。
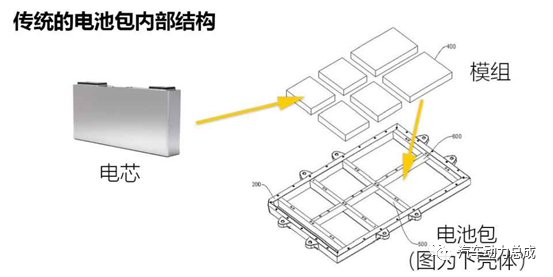
模组有什么用?
在讲CTP技术之前,我们先来了解一个概念,Cell to PACK( 无模组动力电池包 ),我们可以理解为该技术省去了中间模组环节(Module),将电芯直接集成到电池包。 那么去掉的这个模组是什么? 它在传统电池包里充当什么角色?
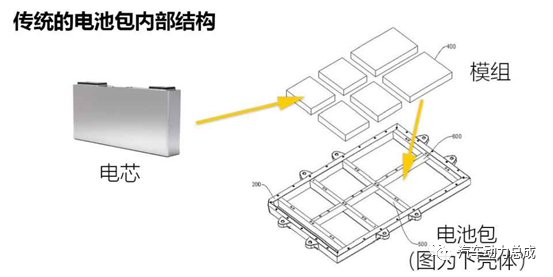
读到这里,我想有人肯定会问:模组在电池包里充当这么多角色,能够有效保护电池的稳定性与安全性,在发生故障需要维修时还能简化维修成本与难度,为什么还要一味的追求“去模组化”呢?
这点开头我们有提到,许多电池供应商和主机厂一直在寻求降低电池成本的方案,模组的硬件费用约占电池总成本的15%,而且电芯对于电池包的空间利用率仅为40%,我想,“去模组化”将会是未来的趋势。但正是因为模组充当了多种角色,所以“去模组化”实现起来并不是那么容易,这就意味了去除模组后的电池包在强度以及可靠性不能降低,这就对了电芯以及电池包的制造工艺和材料选择提出了更高的要求。
什么是CTP、目前国内CTP路线有哪些?
CTP(无模组动力电池包),即Cell to PACK,是电芯直接集成为电池包,从而省去了中间模组环节。国内的CTP技术分为两种路线,一种是以比亚迪为代表的的完全无模组方案,另外一种是以宁德时代为代表的以大模组代替小模组的方案,当然也有其他企业例如特斯拉、长城汽车的蜂巢能源、国轩高科等也都在研发自己的CTP技术。我们今天就以两种具有代表性的技术路线来讲。
比亚迪CTP技术(刀片电池)
比亚迪采用了CTP(Cell To Pack)设计思路,即把电芯以列阵方式直接装到电池包壳体内,省略了把电芯组装成模组这一步。比亚迪通过CTP设计在保证了电池包的强度前提下,省去了横梁、纵梁以及螺栓等附件,将电池包壳体内部的空间利用率由原来的40%-50%提升至60%-80%。
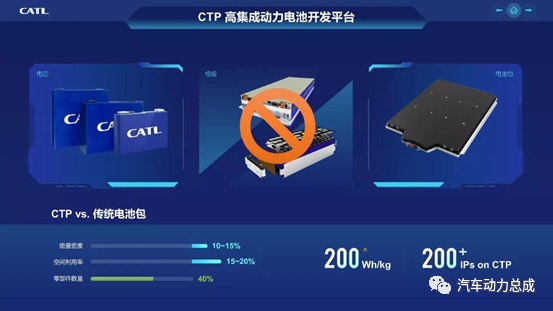
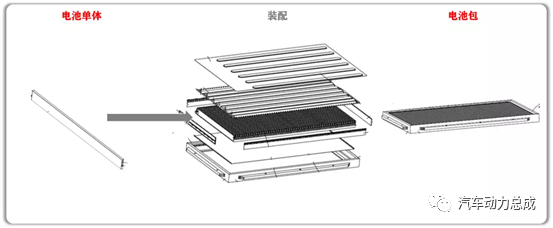
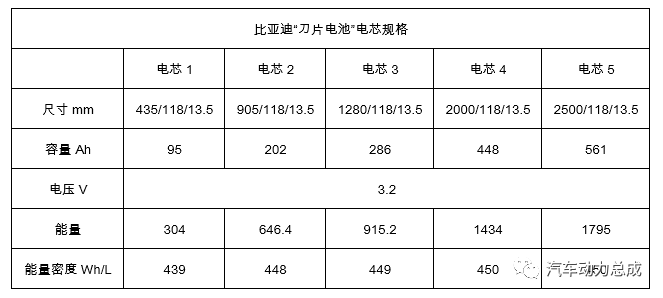
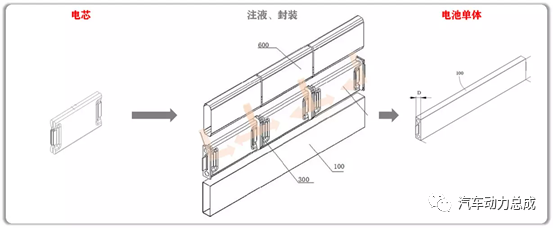
宁德时代CTP技术
宁德时代则在提升能量密度和降低电池成本方面找到了一条新的路径,简单来说就是以大模组代替小模组的方案。从宁德时代发布的专利图来看,电池壳体为塑料材质,在注塑时,将散热板嵌入箱体内,与电池壳体外壁相连通(散热板内部有贯穿的通道),这就方便了外部冷却管路的连接。
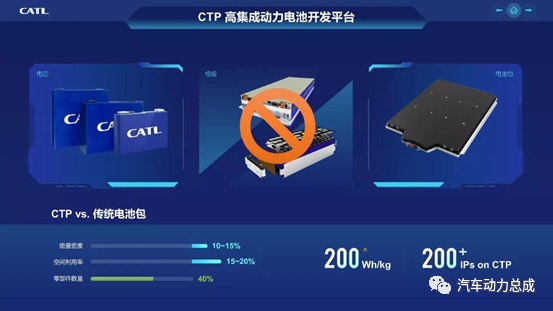
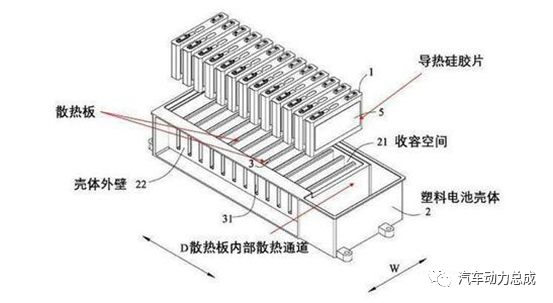
动力电池CTP技术优点、缺点
CTP技术优点:
传统的电池包内部结构,由多个电芯(Cell)构成的电池模组(Module),会通过螺栓固定到带有横梁和纵梁的外壳上,形成电池包(Pack)。这种电芯-电池模组-电池包的集成设计,横梁和纵梁占用了许多空间,螺栓等附件增加了重量,很大程度上限制了电池包容量和能量密度的提升。
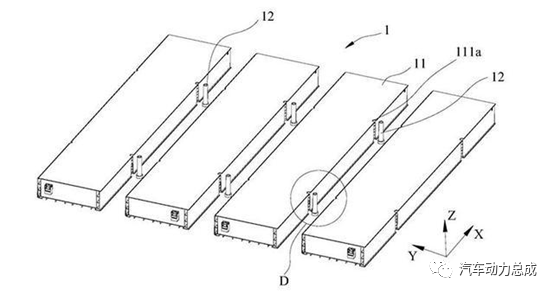
CTP技术缺点:
传统电池包里的模组各自管理自己的单体电芯组,有助于温度的控制,同时有效防止在发生事故时电池热失控的传播,但无模组方案中电芯热失控管理难度加大。以往当某一个电池电芯发生故障需要更换时,只需要找到所属的模组,对其进行更换,就能够解决故障。
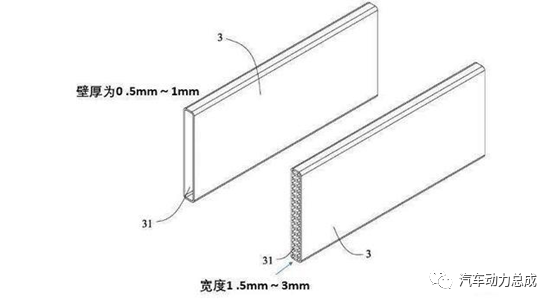
CTP技术未来市场
除了比亚迪、宁德时代在研发CTP技术外,其他车企或厂家也没停下脚步,据长城汽车的蜂巢能源透露,他们的CTP技术既有无模组方案,也有大模组方案。相比蜂巢能源传统的590模组,CTP-G1减少24%零部件数量,每Wh电池成本降低0.1元;CTP-G2提升5%-10%重量成组效率,提升5%空间利用率,减少22%零部件数量,每Wh电池成本降低0.21元/Wh。这就说明了,各大车企对于CTP技术还是有能力、有信心去研发的。
编辑推荐
最新资讯
-
大卓智能端到端直播实测,16公里复杂路段挑
2025-04-25 17:16
-
《汽车轮胎耐撞击性能试验方法-车辆法》等
2025-04-25 11:45
-
“真实”而精确的能量流测试:电动汽车能效
2025-04-25 11:44
-
GRAS助力中国高校科研升级
2025-04-25 10:25
-
梅赛德斯-AMG使用VI-CarRealTime开发其控制
2025-04-25 10:21