车用电池热管理系统试验台架研制与试验研究
为了满足电动汽车电池包和电池热管理系统开发和试验需求,设计和搭建了基于 CAN 总线通讯交互的电池热管理系统试验台架。通过高温 US06 工况和低温 NEDC 工况电池热管理试验研究表明,该试验台架功能运行正常,电池包设计符合热管理要求。并初步验证了电池热管理基本控制策略的正确性,为后续整车级电池热管理标定试验和策略优化提供依据。
关键词:电动汽车;电池热管理;试验台架;试验研究
随着电动汽车的快速普及和更新迭代,导致目前电动汽车的研发周期相对于传统燃油汽车较短,尤其是电池包开发时间。如果能在样车装车之前完成大部分相对准确的系统级别试验测试,尽早发现问题和解决问题,可以为项目开发节约大量费用和时间[1-2]。为此建立一个通用性较好的电池热管理系统试验台架显得尤为重要,可以显著地缩短电池包开发时间和电池热管理策略标定试验周期,对于研究和评价电池热管理系统性能同样具有重要意义。
1 电池热管理系统试验台架总体设计
电池热管理系统试验台架设计
为了满足电动汽车用电池包前期开发需求,完成装车之前的电池热管理系统性能验证,以及电池热管理控制策略系统级别验证及优化,需要设计一个可靠性较好、通用性较强的电池热管理系统试验台架,用以模拟电动汽车复杂行驶工况、环境温度等条件,从而更有效地为后期的电池包优化设计和整车电池热管理标定试验做铺垫,同时也能为仿真分析提供可靠数据来源,更真实地校准仿真模型。
本文研制的车用电池热管理系统试验台架主要包括被测对象、模拟整车充放电工况的装置、数据采集模块、供电模块、外部电池管理系统模块和模拟整车环境条件模块,整个系统试验台架构造原理如图 1 所示。其中,被测对象可以为电池包、或 Chiller、或电池热管理控制器等部件或系统;模拟整车充放电工况的装置为具有输出直流电压 30V~800V 和输出电流±300A 能力的充放电柜及其充放电柜控制平台;数据采集模块包括电芯温度采集单元、测量电池包入口水流量的流量计、通过 CAN 总线传输温度压力等信息的报文读取设备和电脑。供电模块主要指供电给低压零部件或设备的可调电源模块;外部电池管理系统模块主要为电池包提供冷源或热源的系统及热管理控制器,主要结构原理如图 2 所示[3];模拟整车环境条件模块为小型环境舱,其功率为 100kW,可以模拟环境温度范围为-40℃~+85℃,温度控制精度为±2℃, 环境相对湿度为 20%~98%,相对湿度控制精度为±5%。本文设计的电池热管理系统试验台架主要采用的设备规格型号见表 1 所示。
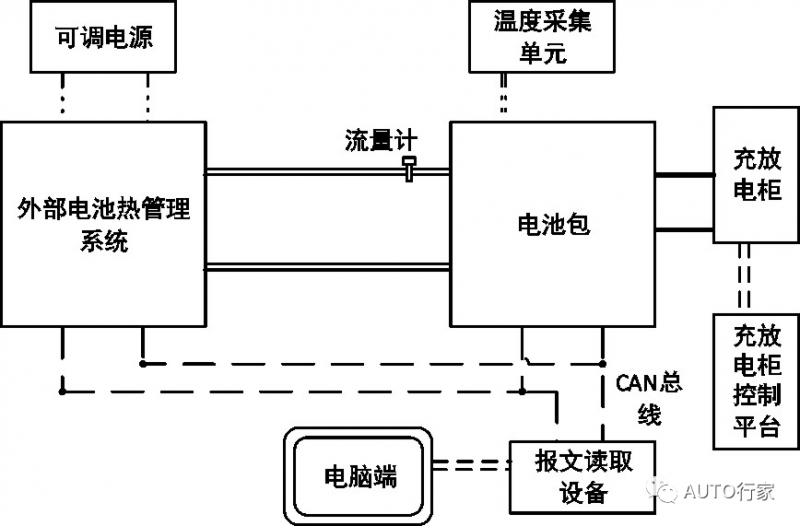
图1 电池热管理系统试验台架示意图
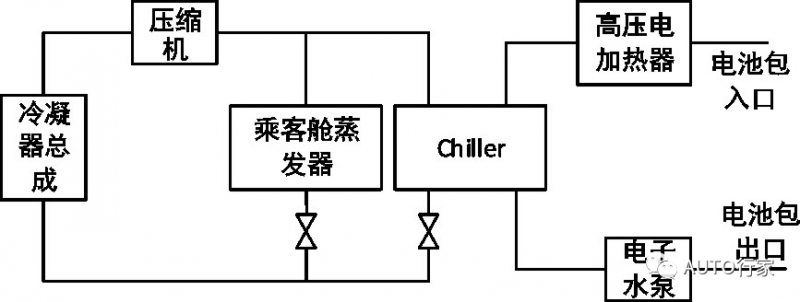
图2 外部电池热管理系统水路循环示意图
表1 试验台架主要设备的规格型号
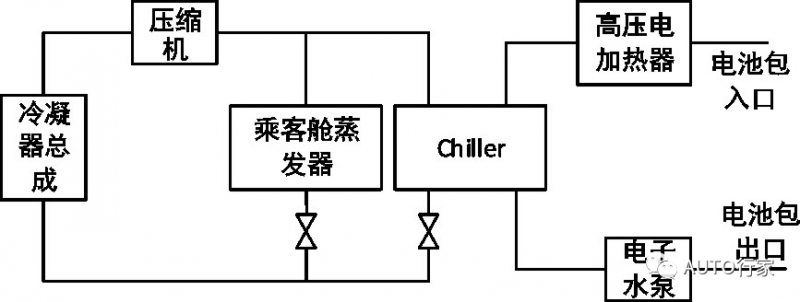
根据试验台架构造原理图搭建的电池热管理系统试验台架实物如图 3 所示。试验开始之前,需要将试验台架的电池包与外部电池热管理系统模块放置于小型环境舱内进行预处理再进行试验,同时,供电模块、充放电柜、采集设备等模块放置于小型环境舱之外,这样既可以保护设备,防止受高温或低温环境影响其使用寿命,又利于测试人员在外监测数据。其中,外部电池热管理系统的热管理控制器可以通过硬线采集压缩机排气压力,通过PWM 控制电子水泵,通过CAN 总线与压缩机和高压电加热器进行控制交互;而电池包内的电池管理模块可以实时采集电芯温度和电压等参数,并通过CAN 总线与热管理控制器进行通讯交互,可以实时发送和接收所需要的报文信息,并通过 CAN 报文读取设备上传至电脑端,便于测试人员观测实时动态数据,同时电脑端也可以通过软件动态修改标定参数进行控制对应节点工作[4]。
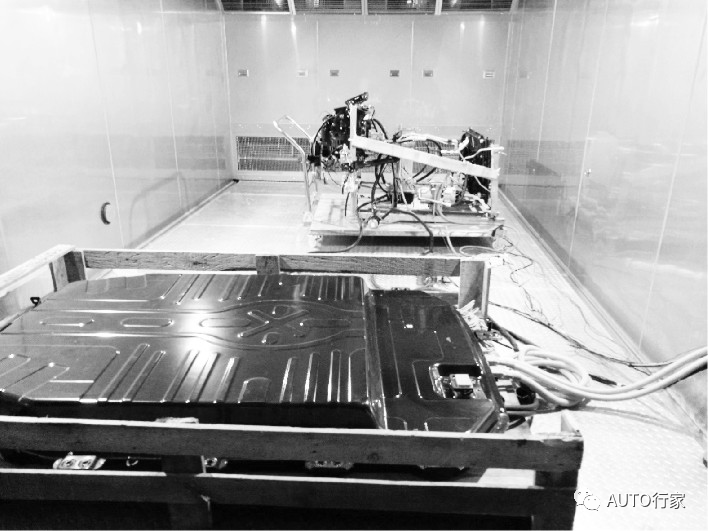
图 3 电池热管理系统试验台架实物图
电池热管理系统试验台架功能
基于设计和搭建的车用电池热管理系统试验台架可以实现如下功能:
1. 可以进行高温、低温和常温电池包放电容量测试, 为电池包优化设计、公告试验和整车放电 MAP 优化提供数据基础;
2. 可以完成高温、低温和常温电池包充电容量测试, 为电池包优化设计、公告试验和整车充电控制策略优化提供数据基础;
3. 可以实现高温、低温、和常温电池包充电速率测试,为电池包优化设计和整车充电控制策略优化提供数据基础;
4. 能完成电池热管理系统 Chiller 等零部件性能匹配测试,为零部件选型匹配提供数据支持和性能验证;
5. 能模拟整车各个环境温度条件和充放电工况进行电池热管理系统性能评价试验,为整车级系统优化设计提供数据支持和性能验证;
6. 能实现高温电池制冷、低温电池加热测试功能,对电池热管理控制策略进行优化与验证,同时也可以进行系统级的电池热管理标定优化试验,为整车级电池热管理标定试验做数据支撑,缩短整车开发周期。
2 电池热管理系统台架试验分析
为了验证电池热管理系统试验台架搭建的准确性和电池热管理控制功能的可靠性,以及优化电池热管理控制策略做基础,本文进行了 US06 循环工况的高温电池热管理台架试验和 NEDC 循环工况的低温电池热管理台架试验。
US06 循环工况的高温电池热管理台架试验
本次试验前提条件为电池热管理系统试验台架浸置于40℃恒温环境舱内不少于 4 小时,使得电池包温度和电池热管理系统其余零部件的温度基本达到与 40℃环境温度一致, 且电池平均温度与设定环境温度的差值不能超过 2℃,才确定为达到试验预处理的环境适应性目标[5]。
试验结果如图 4 所示,基于 US06 循环工况的高温电池热管理台架试验总共试验时间约为 177min,从试验数据中可以得出,试验起始的电池最小温度为 39℃,电池最大温度为41℃,电池平均温度为 40℃,电芯温差为 2℃,经过约 17 个模拟整车激烈高速驾驶的 US06 工况电池包放电试验之后,电池热管理制冷功能正常开启,高温环境下的电池包各温度可以得到有效控制,并逐渐降低。试验结束时,电池最小温度为 32℃,电池最大温度为 36℃,电池平均温度为 33℃,电芯温差为 4℃。整个试验过程中,电池实际入口水温随着压缩机的开启工作逐渐降低,并且电池实际入口水温可以达到目标水温 25℃,并随着试验的进行最终稳定于 23℃~24℃区间。
同时,根据试验结果可以得到电芯温差随时间的变化关系,如图 5 所示,从图中可以看出,电芯温差也随着高温工况试验的进行逐渐增大而后缓慢趋于稳定,并最终稳定于 4℃,其中约在试验进行到 70min 时刻,电芯温差达到最大值5℃。
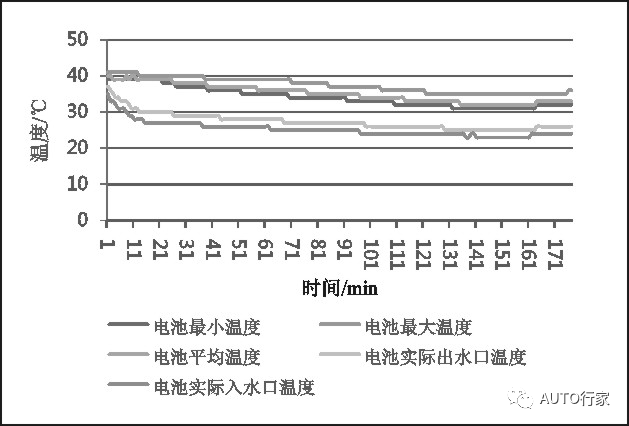
图4 US06循环工况的高温电池热管理试验数据
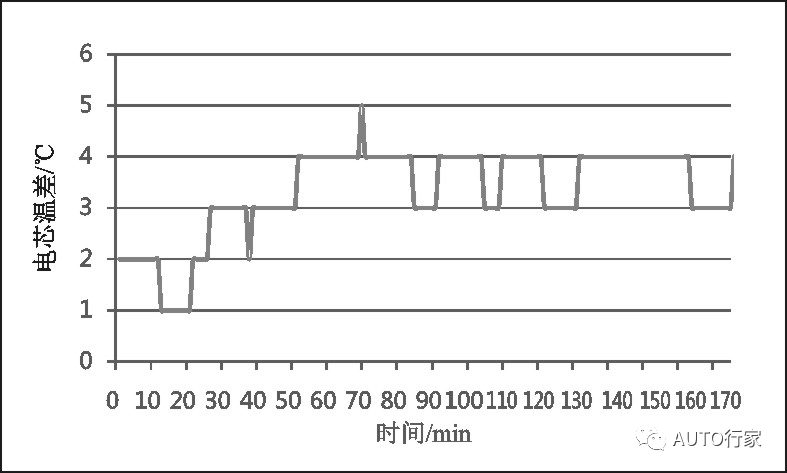
图5 US06循环工况的高温试验电芯温差数据
NEDC 循环工况的低温电池热管理台架试验
本次试验前提条件为电池热管理系统试验台架浸置于 0℃恒温环境舱内不小于 6 小时,使得电池包温度和电池热管理系统其余零部件的温度基本达到与 0℃环境温度一致,且电池平均温度与设定环境温度的差值不能超过 2℃,才确定为达到试验预处理的环境适应性目标[5]。
试验结果如图 6 所示,基于 NEDC 循环工况的低温电池热管理台架试验总共试验运行循环为 26 个 NEDC 工况,时间总计约为 511min。从图中可以得到,试验起始时刻的电池最小温度为-1℃,电池最大温度为 1℃,电池平均温度为-1℃,起始电芯温差为 2℃。试验结束之后电池最小温度为 10℃,电池最大温度为 12℃,电池平均温度为 11℃,电芯温差为 2℃。低温试验过程中,电池热管理加热功能正常,当电池平均温度低于电池热管理控制策略加热设计阈值 5℃的条件,电池用高压电加热器开启进行加热水路系统的冷却液, 使电池入口实际水温达到电池入口目标水温 30℃,当电池加热进行到 18min 的时刻,电池平均温度达到电池热管理策略设计阈值 5℃,则停止加热,此时电池入口实际水温也开始逐渐降低。由于电池包一直以 NEDC 循环工况进行放电,在后续的试验过程中,电池平均温度并未再低于 5℃阈值,这主要是由于电池包依靠自身的发热量可以维持电池平均温度。
再根据该试验结果可得电芯温差随时间的变化关系,如图 7 所示,从图中可以看出,试验前 30min,电芯温差有逐渐增大的趋势,并于试验进行至 24min 时刻,电芯温差达到最大值 4℃,后续试验过程中,电芯温差比较稳定,最终电芯温差稳定于 2℃~3℃区间。
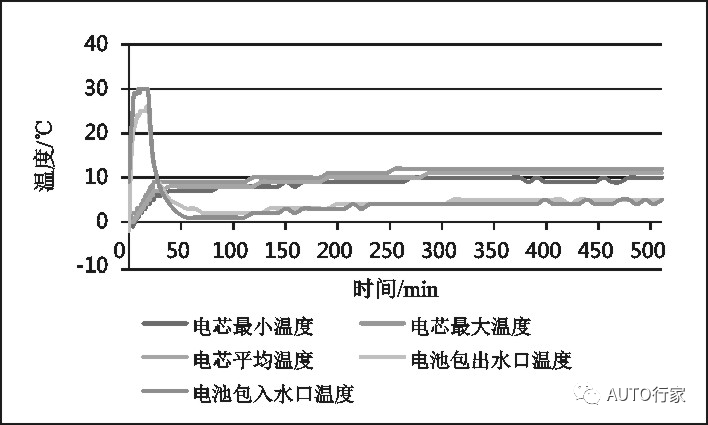
图6 NEDC循环工况的低温电池热管理试验数据
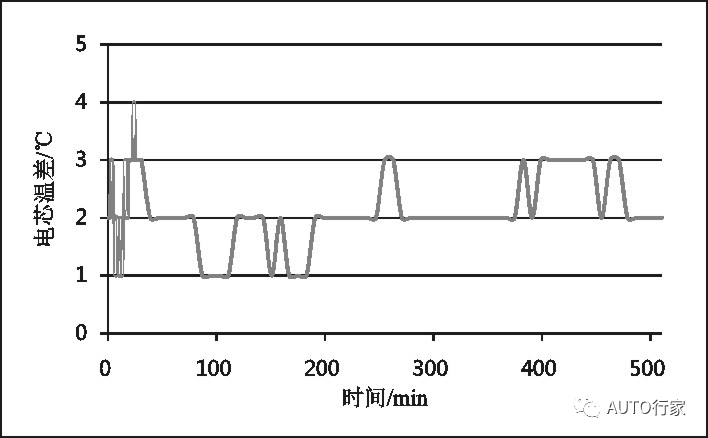
图7 NEDC循环工况的低温试验电芯温差数据
3 结论
(1)本文研制了电动汽车用电池热管理系统试验台架, 可以模拟车辆各工况下电池包等热管理相关对象的工作特性,不仅可以完成简单的各环境温度下电池包充放电容量测试试验,还可以完成电动汽车电池热管理系统的性能评价试验、零部件选型匹配验证试验、电池热管理控制策略优化试验等系统级别的试验研究,为整车级别的电池热管理高低温标定试验和控制策略优化工作奠定基础。
(2)基于 US06 循环工况的高温电池热管理台架试验测试数据可以表明,本文搭建的电池热管理系统试验台架功能稳定可靠,电池热管理制冷功能可以正常运行,40℃高温环境下电池最高温度逐渐降低,电池各温度均可以得到有效控制,电芯温差维持于 1℃~5℃区间,电池温降和电芯温差均匀性符合设计要求。
(3)根据 NEDC 循环工况的低温电池热管理台架测试数据可以得出,电池热管理加热功能可以正常运行,电池平均温度被加热至 5℃之后,0℃环境温度下电池包依靠自身热量可以维持电池平均温度,电芯温差稳定区间为 2℃~3℃, 电池温升和电芯温差均匀性符合设计要求。
参考文献
[1] 张博,姚烈,蔡庆住等.新型零部件台架试验方法及策略[J].汽车零部件,2017(3):44-47.
[2] 顾柏良.汽车工程手册-试验篇[M].北京:人民交通出版社,2001.
[3] 肖军,张明,梁辉,等.一种电池包热管理系统及其控制方法[P].中国, CN109305060A,2018.
[4] 常智.基于 CAN 总线在车辆通讯协议中的研究和应用[D].太原:中北大学,2019.
[5] 中华人民共和国国家质量监督检验检疫总局,等.GB/T 31467.2- 2015.电动汽车用锂离子动力蓄电池包和系统第 2 部分:高能量应用测试规程[S].北京:中国标准出版社,2015
最新资讯
-
全球首次!IVISTA 2023版修订版引入带灯光
2025-04-28 09:59
-
我国首批5G毫米波行业标准送审稿审查通过
2025-04-28 08:56
-
5/16 厦门- 新能源汽车电驱测试技术的创新
2025-04-28 08:53
-
国内首个汽车电磁防护技术验证体系EMTA正式
2025-04-28 08:49
-
一文带你了解滤波器
2025-04-28 08:35