水源热泵技术在燃料电池热管理系统中的应用分析
燃料电池冷却水水温较传统燃油车低,制热量同比降低约28%。使用PTC 加热冷却水会迫使燃料电池余热直接排放到空气中,能效较低,影响车辆冬季开热空调时的续航里程。文章通过研究分析发现,热泵制热技术应用在燃料电池车中可以有效避开此技术低温制热面临的难点,提高了制热系统能效。同时,整理现有汽车空调制冷系统改造成热泵系统所需优化的方向,为后续开发提供了参考。
关键词:燃料电池 热泵 余热应用
电动车辆的开发及应用越来越多,但受电池技术制约,续航里程及充电速度一直是电动车辆发展的瓶颈。在诸多发电增程的解决方案中,氢燃料电池具有因不受卡诺循环限制( 热效率高) 、没有机械部件( 运行噪声小) 、无尾气排放的污染处理需求( 环境友好) 等优点,被认为是最有发展前途的电池技术。
但是氢燃料电池应用对于环境的要求与传统发动机有较大差异。传统发动机能够给予空调85 ℃以上的热水供制热/除霜。以-20 ℃环境温度作为基准,气液温差达到105 ℃,空调暖风芯体的换热效率相对较高。而氢燃料电池水温一般低于65 ℃,对于相同的环境温度,气液温差明显降低,空调制热/除霜的出风温度都有较大幅度降低。
表1 为某车型空调暖风芯体制热数据。由表可知,在450 kg/h 风量下,进水温度从85 ℃降到65 ℃( 汽液温差从105 ℃降到85 ℃) ,制热量降低28.8%,出风温度降低34.3%。
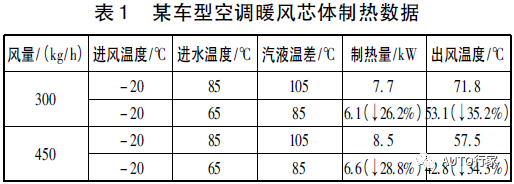
为了提高出风温度,可以通过增加冷却水流量来进行弥补,但是气液温差降低后,换热效率也相应降低,出风温度改善很有限,而且因系统液侧流阻的存在,流量增加量也有限。或者使用风侧PTC 直接提高出风温度,但鉴于 PTC 的特性,系统能效比较低。
已经有开发实例使用水侧 PTC 辅助加热,受限于空调水温需求高于燃料电池水温,水路无法共用。燃料电池的余热需完全向空气散热。而PTC 的制热能效比较低( 最高为1) ,在满足空调制热、除霜、除雾需求的前提下,需要消耗大量的电能,这无疑又大幅降低了车辆的续航里程。
因此,在燃料电池车上有必要探寻一种新制热模式,将燃料电池的余热利用起来,减少电能消耗,增加续航里程。
1 热泵制热技术的引入
遵循逆卡诺定理的热泵技术可以将热量从低温热源运送到高温热源。通常制热的能效比可以达到 3 ~ 4,即 1 倍电能消耗可获得 3 ~ 4 倍制热量,符合新能源车低温热源的实际情况以及对于能效比的需求。
为了从较低的环境温度中吸取热量,系统内的蒸发压力会变得很低,这样压缩机吸气点的密度会降低,体现在吸气比容较大,直接限制了制冷剂循环质量流量和最终的系统制热量。以目前车用空调 R134a 制冷剂为例,其饱和蒸发压力( 吸气压力) 及过热 5 ℃ 下的物性状态对比如表 2 所示。
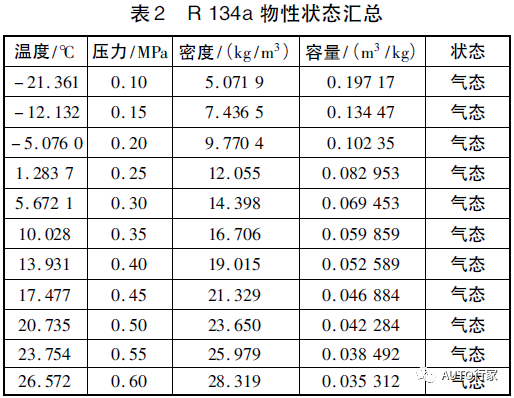
以10℃和-5℃吸气压力为例,密度从16.706降到9. 7704,降低了42% ; 比容从0.059859升到 0.10235,增加了 95% 。在压缩机排量和转速一定的情况下,制冷剂循环质量流量及制热量同步降低了 42% 。
此外,使用R134a 在 1 个大气压下对应的饱和蒸发温度约为-21 ℃ 。根据经验,空气侧温度通常比饱和蒸发温度高约5 ℃ ,即此时对应的空气侧温度约为-16 ℃ ,此为R134a 制冷系统的制热极限。当需要从-16 ℃ 或更低的环境温度中吸取热量时,系统低压会低于大气压,由于此时系统内低压较低,不再使制冷剂向大气泄漏,而空气会渗漏至制冷系统中,最终严重影响制冷系统的正常运行。
为了获得较高的出风温度,必须要有足够高的高压作为饱和冷凝温度,在吸气压力较低时,吸排气压缩比会大幅增加,引起排气温度升高。较高的排气温度会使冷冻机油粘度降低,油膜承载力下降,这对于压缩机的工作寿命影响较大,甚至会引起压缩机自带的保护机构启动,致使整个系统无法正常运行。以R134a 制冷剂为例,当熵压缩到 3.0 MPa( 对应 86 ℃ 饱和冷凝温度) 时可以发现,在吸气温度从26.572℃ 降低到 -21.361℃的过程中,排气温度反而从97.429℃ 升高到104.5 ℃ ,对应的吸排气温差则从 70.9℃ 升高到125.9℃ 。如果吸气过热超过5℃,在低温制热时排气温度将会更高,如表 3 所示。
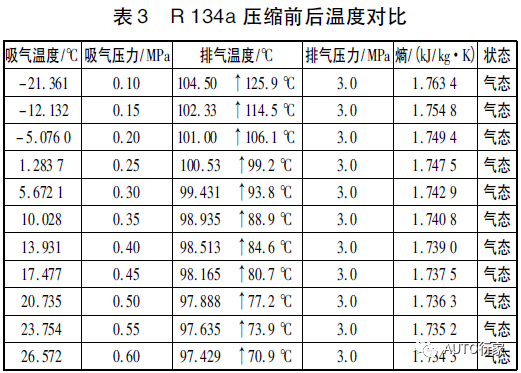
为了改善热泵低温制热技术,业界从上世纪70 年代开始,陆续开始了补气增焓的研究应用。有的引入中压液态制冷剂直接对压缩腔进行喷射增焓,也有用中压蒸汽直接提高吸气点密度。在应用变频技术后,通过提高压缩机转速来增加系统的循环质量流量,进而增加系统制热量。在新型制冷剂研究中,也有考虑使用R744,但此新制冷剂的应用将颠覆现有国内汽车空调R134a 制冷剂的零部件供应体系,系统改造代价较高。
另外,在低温制热时,难免会发生室外换热器因结霜、结冰影响换热器正常工作的情况。为了除冰化霜,空调在制热工作一段时间以后,即会转入除霜运行,此时车内的制热功能将停止。这种情况如果发生在汽车除雾时,会影响车辆的行车安全,故除霜运行也限制了单一的热泵系统在汽车上的应用。
2 水源热泵制热在燃料电池热管理中的应用
某车型计划选用额定功率为30kW 的燃料电池,以47%名义系统电效率进行估算,将会有33.8kW的余热通过温度较低的冷却水循环排放到空气中。这远远大于空调在制热过程中的热量需求。
如果将热泵制热技术与燃料电池水循环相结合,在制热工况时,燃料电池的循环冷却水可以提供一个稳定的65 ℃进水温度。如果热泵空调能从冷却水中吸取热量,则上文中提到的热泵低温制热的技术难题就可完美地解决。
下面提供一种系统解决方案,对热泵系统运行工况进行进一步的分析估算( 有关方案的优劣及细化不在本文探讨范畴) ,如图 1 所示。
由图可知,当截止阀1接通、截止阀2断开, 制冷剂流向如黑色箭头所示,实现热泵制冷功能; 当截止阀1断开、截止阀2接通,制冷剂流向如深灰色箭头所示,实现热泵制热功能。
燃料电池的冷却水回路为浅灰色箭头所示, 本文仅提供一种经典接法用以热泵运行工况估算。在制冷模式时,冷水机是否需要旁通、电机以及燃料电池是需要并联还是串联,需要在后期细化设计中予以考虑。
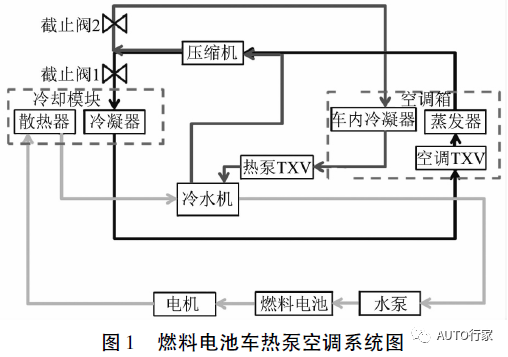
3 水源热泵在燃料电池热管理中的运行工况估算
某车型制热需求为5500W,使用排量为34mL的电动涡旋压缩机时,对其热泵系统的运行工况进行估算。为了保持和传统燃油车相同的制热性能,拟设定车内冷凝器的饱和冷凝温度为 85 ℃ ,过冷及过热度设定为 5 ℃ ,结果如表 4 所示。
从热泵工况估算结果可见,系统运行会面临以下几个问题:
( 1 ) 85 ℃ 冷凝温度对应的高压为2.9258MPa[A],此压力高于常规制冷系统运行情况,系统压力开关等设备及控制逻辑需要对热泵系统重新标定。同时需要确认该工况是否在压缩机和车内冷凝器的运行范围内。
( 2) 热泵制热工况下吸气密度较高,系统质量流量有所增加,此时系统循环制冷剂需求量会与制冷工况不同,因此制冷剂充注量需要针对热泵重新标定,并设置足够大的储液器,以在制冷过程中容纳多余的制冷剂。
( 3) 吸气压力和循环流量较制冷情况更高,需要对TXV重新选型并进行匹配。
( 4) 表 4 中的计算制冷量即为热泵系统通过冷水机从燃料电池冷却水中吸取的热量,可以用于冷水机的选型。如果选择较大的冷水机,可以通过调整TXV进一步扩大制热量。但是受空调箱散热能力限制,高压会进一步升高,引起系统停机风险,在后期细化设计时需要考虑。
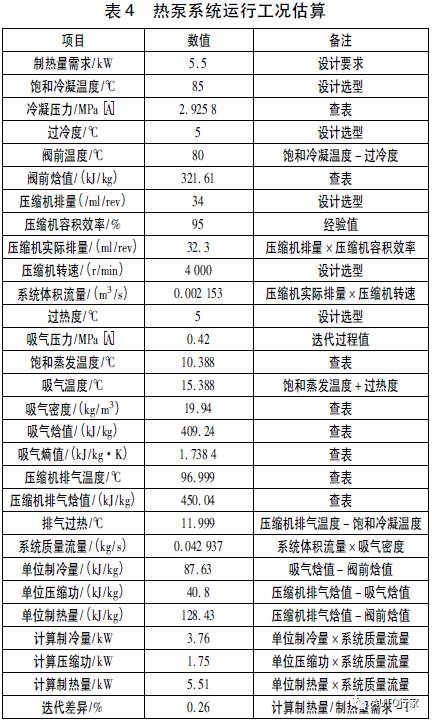
( 5) 表 4 中计算压缩功为 1.75kW,考虑绝热压缩的等熵效率、压缩机泵体摩擦副的机械效率以及电机效率,最终的系统 COP约为2.5,即5500 W制热量只需要2200 W 的电能需求,比使用 PTC 单独提供5500 W制热量节省了约 60% 的电能,节能效果明显。以某新能源车冬季开 PTC 制热衰减 50% 里程为例,采用热泵系统后,里程衰减减小为 20%,即冬季开空调制热时续航里程增加了 30% 。
4 结论
燃料电池冷却水温较传统燃油车低,直接使用该冷却水,制热/ 除霜效果会相对燃油车情况变差。如果使用 PTC,会造成大量的能量浪费,影响续航里程。
水源热泵技术可以充分利用燃料电池余热, 将较低温度的冷却水提升至与燃油车相同的温度。在获得相同制热量的前提下,对比PTC方案, 具有显著的节能效果,可以直接增加车辆冬季开空调制热时的续航里程。
鉴于水源热泵的工作特性,该技术在新能源车热管理中有广阔的应用前景,可以横向拓展到新能源车的三电余热回收利用,提高整车的系统能效。但是,在应用水源热泵时,需要对原先单冷空调系统进行设计优化,这会涉及到整个系统物料成本及开发费用投入,需要在后续的细化设计中予以分析考虑。
参考文献
[1] 康启平,我国燃料电池汽车商业化发展影响因素分析[J]. 上海汽车,2018( 3) : 33-37.
[2] 王如竹. 制冷原理与技术[M]. 北京: 科学出版社,2003.
- 下一篇:某皮卡驾驶室声学包设计和结构优化
- 上一篇:某串联混合动力汽车驱动控制策略解析
编辑推荐
最新资讯
-
中汽中心工程院能量流测试设备上线全新专家
2025-04-03 08:46
-
上新|AutoHawk Extreme 横空出世-新一代实
2025-04-03 08:42
-
「智能座椅」东风日产N7为何敢称“百万级大
2025-04-03 08:31
-
基于加速度计补偿的俯仰角和路面坡度角估计
2025-04-03 08:30
-
《北京市自动驾驶汽车条例》正式实施 L3级
2025-04-02 20:23