燃料电池商用车安全和热管理
1.1 公交客车安全设计
燃料电池客车氢系统结构安全设计主要涉及储氢瓶固定结构和氢系统结构两方面。储氢瓶固定结构强度应满足GB/T 26990-2011相关规定,即储氢瓶紧固后,应能承受上、下、前、后、左、右六个方向上8g的冲击力,保证储氢瓶与固定座不损坏,相对位移不超过13mm。如果管路与相邻部件接触或穿越孔板,应采用橡胶套管进行保护,保证管路与相邻部件不产生碰撞和摩擦。氢系统结构方面,应保证储氢瓶及其管路距车辆边缘至少有100mm的安全间距,否则应增加保护措施。
根据储氢瓶在客车上的布置位置,氢系统可分为顶置式和底置式。一般来说,公交客车采用顶置式布置方式,公路客车采用底置式布置方式。顶置式氢系统储氢瓶在车顶一般呈横向或纵向放置,并用气瓶支架固定。顶置式氢系统应设置储氢瓶覆盖物或遮阳棚,防止储氢瓶直接暴露在阳光下,导致储氢瓶老化。顶置式气瓶支架结构如图7-10所示。
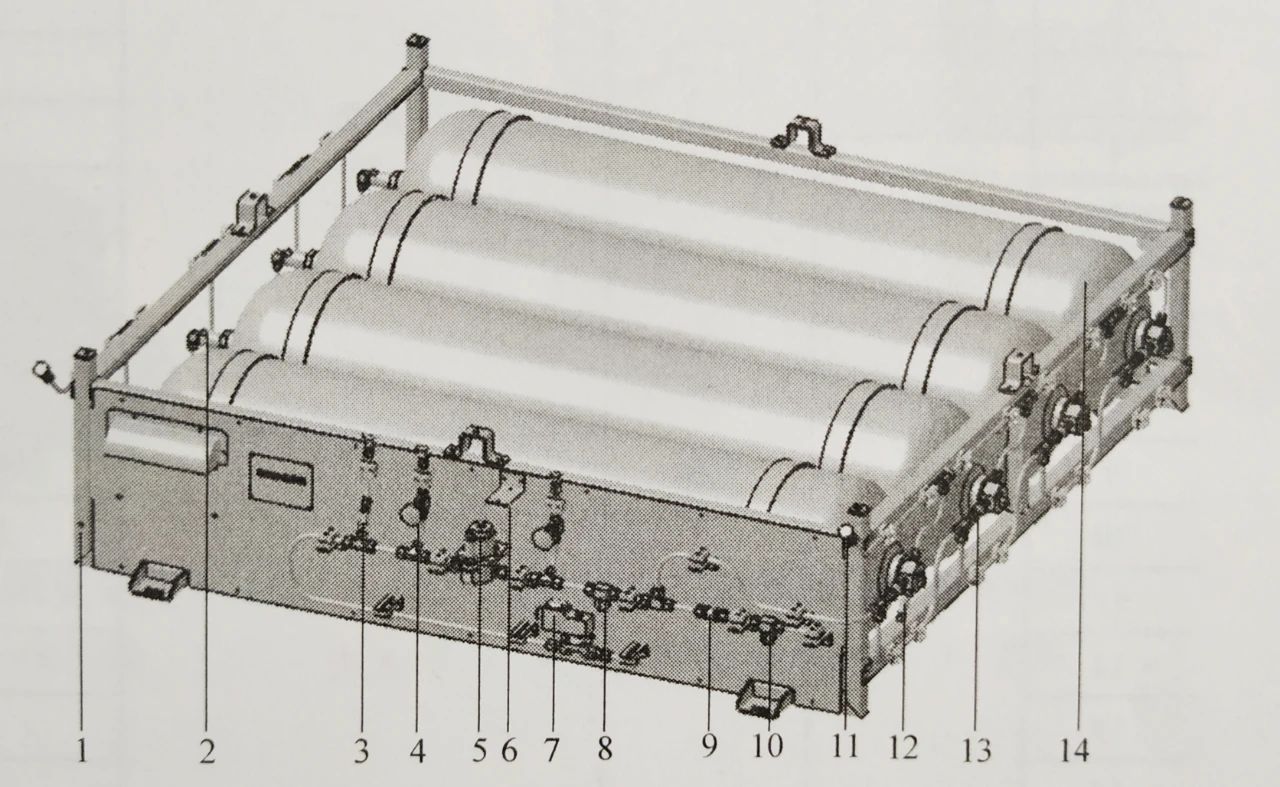
图7-10 顶置式气瓶支架结构
1-气瓶支架2-瓶尾TPRD3-安全阀4-减压阀5-放空阀6-氢泄漏探头7-电磁阀8、10-过滤器9单向阀11-放空口12-瓶阀13-过流量阀14-储氢瓶
燃料电池客车氢安全设计需要考虑以下两个方面。
1)氢安全防护。氢系统管路安装位置及走向要避开热源以及电器、蓄电池等可能产生电弧的地方,至少应有200mm的距离,尤其是管路接头不能位于密闭的空间内;加氢口距暴露的电气端子、电气开关和点火源至少应有200mm的距离。高压管路及部件可能产生静电的地方要可靠接地,或采取其他控制氢泄漏量及浓度的措施,确保在产生静电的地方,也不会产生安全问题。储氢瓶和管路般不应布置在乘员舱、行李舱或其他通风不良的地方;如果不可避免要安装在行李舱或其他通风不良的地方时,应设计通风管路或其他措施,将可能泄漏的氢气及时排除。
2)氢泄漏检测。整车存在氢气泄漏的区域应设置氢气泄漏探测器,能实时检测氢气的泄漏量,并将信号传递给氢气泄漏报警装置。整车能够根据氢气泄漏量发出警告或切断氢气供应。
氢系统高压安全设计包括以下三方面:氢系统及储氢瓶型式试验;储氢瓶、阀门、管路和管件密封性能及耐压强度安全;氢系统过压保护。
氢系统装车前应进行各项型式试验,型式试验合格后方可装车,氢系统高压安全型式试验项目见表7-14。
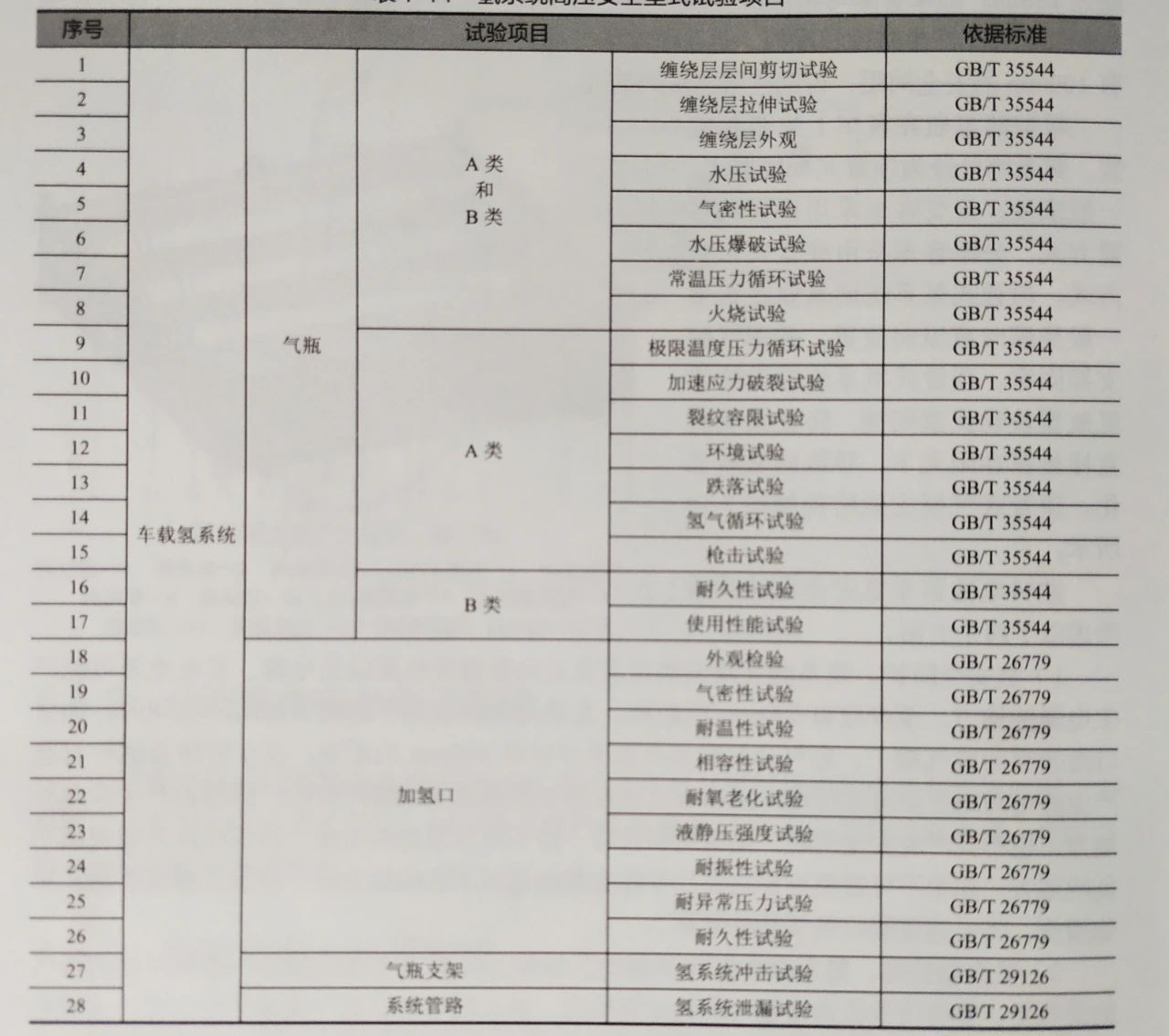
表7-14 氢系统高压安全型式试验项目
按GB/T 26990-2011中4.3.1条要求,氢系统氢气渗透和泄漏量在稳态条件下应不超过0.15NL/min。储氢瓶、阀门、管路和管道设计压力应高于工作压力,与氢气接触材料应具有良好的抗氢脆性能,管路接口密封结构可靠性应能满足氢系统使用工况要求,常用氢气管路接头密封结构分为卡套密封(图7-11)、O形圈密封(图7-12)和金属管道采用硬密封(图7-13)。
氢系统过压保护主要通过设置安全附件及氢系统安全控制实现。氢系统安全附件包括瓶口TPRD(温度驱动安全泄压装置)、瓶尾TPRD、管路安全阀、压力传感器和温度传感器等;氢系统安全控制主要可在供氢管路超压时紧急切断供氢等。
应根据储氢瓶的容积和工作压力来确定是否需要在瓶口或瓶尾安装TPRD。瓶口TPRD为易熔合金,通过瓶口组合阀直接连通到储氢瓶内部。当储氢瓶温度达到设定温度后,TPRD开启,释放储氢瓶内氢气。
瓶尾TPRD为易熔合金,部分厂家增加爆破片装置,当储氢瓶温度达到设定温度或储氢瓶压力达到设定压力后,TPRD开启,释放储氢瓶内氢气。安全阀位于氢系统低压管路上,对氢系统低压管路起超压保护作用。当减压阀下游低压管路达到安全阀开启压力时,安全阀开启,释放低压管路氧气,从而防止低压管路压力进一步升高。
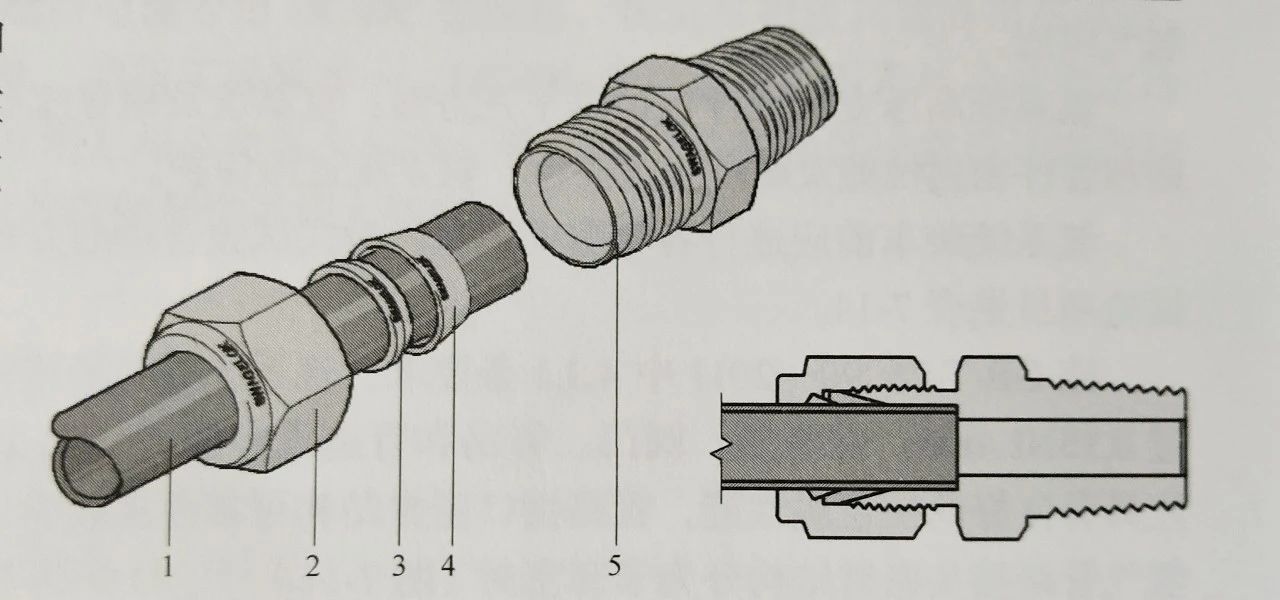
图7-11 卡套接头密封结构(图片来源:世伟洛克公司)
1-卡套管2-螺母3-后卡套4-前卡套5-接头本体
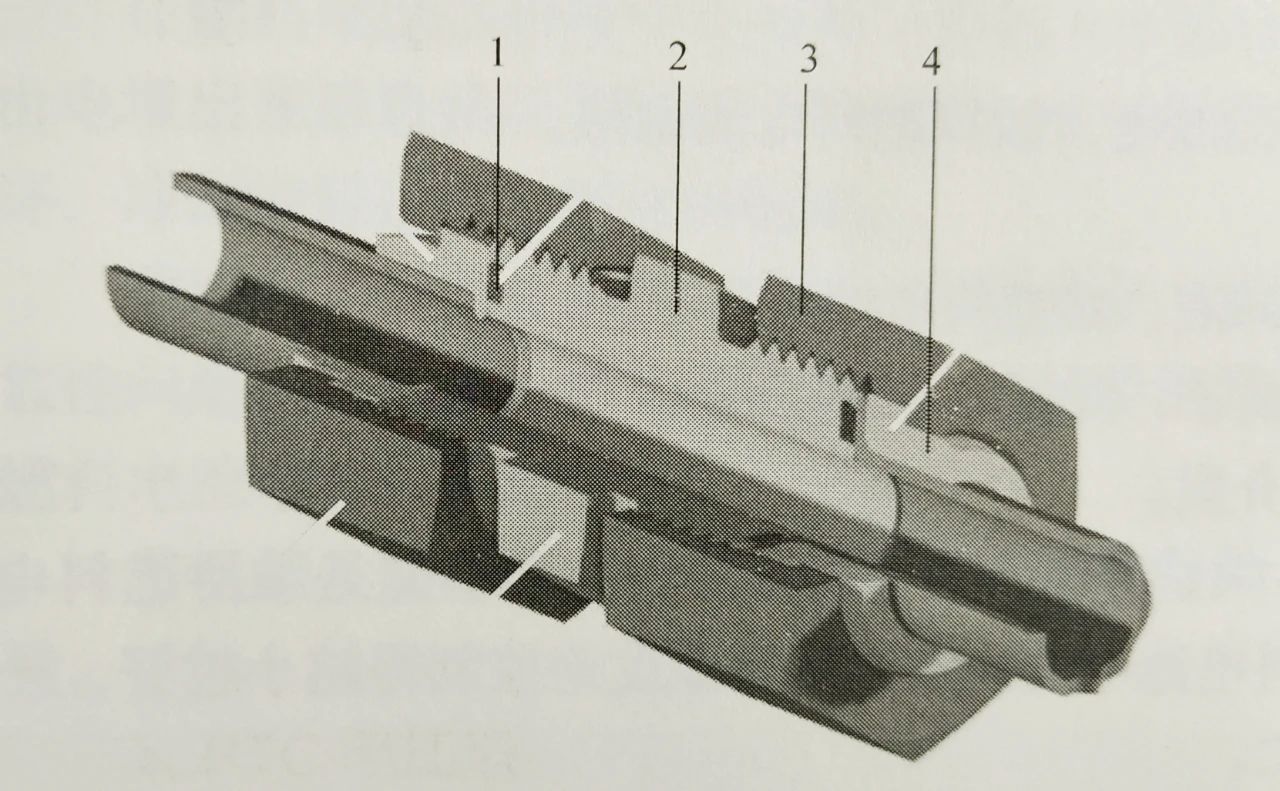
图7-12 O形密封圈结构(图片来源:派克公司)
1-0形密圈2-接头3-螺母4-法兰套
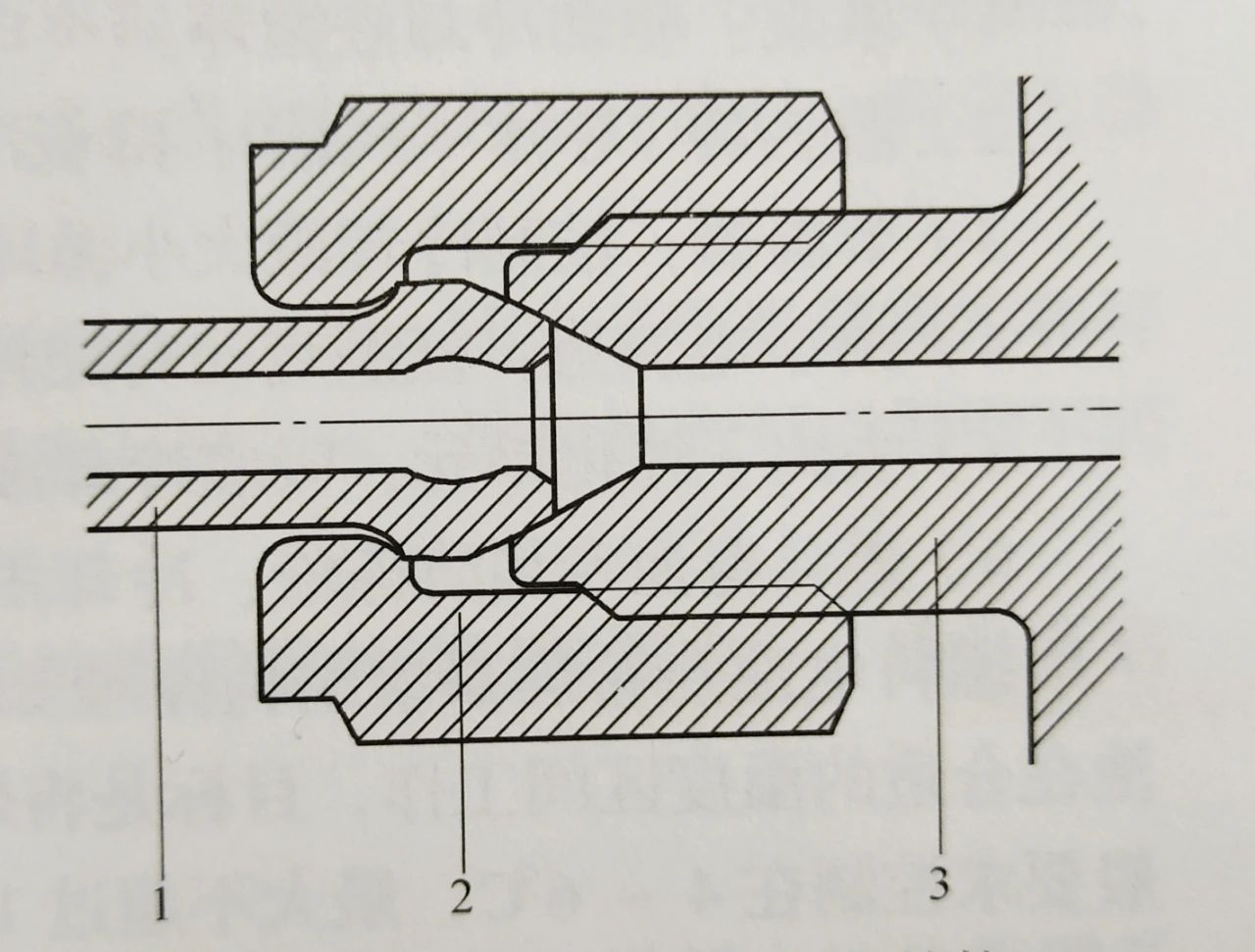
图7-13 金属管道硬密封结构
1-金属管2-螺母3-接头
1.2 公路客车安全设计
公路客车车载氢系统一般采用底置式布置方式。底置式氢系统布置于车辆底部,储氢瓶呈一层或多层布置,通过气瓶支架集成后固定于车架或直接悬挂于车架上。底置式氢系统舱室两侧应设置防撞梁,对储氢瓶及管路附件进行防撞保护。底置式储氢瓶悬挂结构如图7-14所示。底置式储氢瓶客车储氢瓶舱室应与乘员舱有效隔离,并通过烟雾试验进行检测。氢安全防护和氢泄漏检测方面参照燃料电池公交客车安全设计。
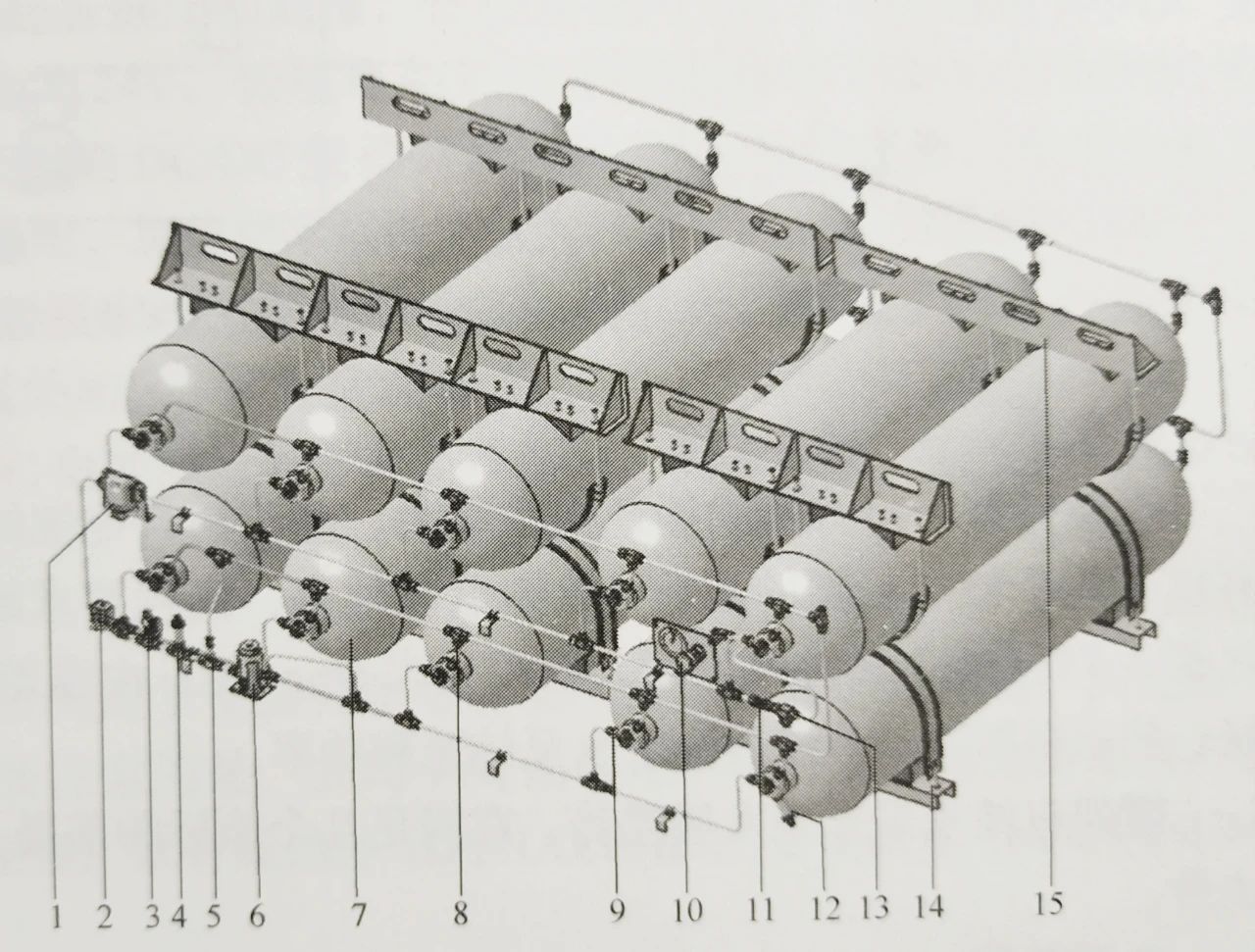
图7-14底置式储氢瓶悬挂结构
1-控制器2-电磁阀3-放空阀4-低压传感器5-安全阀
6减压阀7-储氢瓶8-瓶阀9-过流量阀10-加氢口11-单向阀
12-高压传感器13-过滤器14-底层气瓶支架15-顶层气瓶支架
2、燃料电池商用车热管理
2.1 公交客车综合热管理
燃料电池公交客车综合热管理主要包括:燃料电池自身热管理、动力电池自身热管理、整车冬季采暖和夏季制冷以及基于燃料电池余热利用的整车综合热管理设计。
燃料电池热管理系统核心零部件主要包括:
1)水泵:驱动冷却液循环。
2)散热器(芯体+风扇):降低冷却液温度,散掉燃料电池余热。
3)节温器:控制冷却液大小循环。
4)PTC电加热:低温启动时加热冷却液,对燃料电池进行预热。
5)去离子纯化单元:吸收冷却液中离子,降低电导率。
6)燃料电池专用防冻液:冷却用的介质。
燃料电池热管理系统结构原理如图7-15所示。热管理系统的主要功能是维持燃料电池在合适的温度区间工作,目标是将燃料电池电堆的进出水口温度差控制得越小越好,一般要求控制在4~6°C,最大不超过10°C。
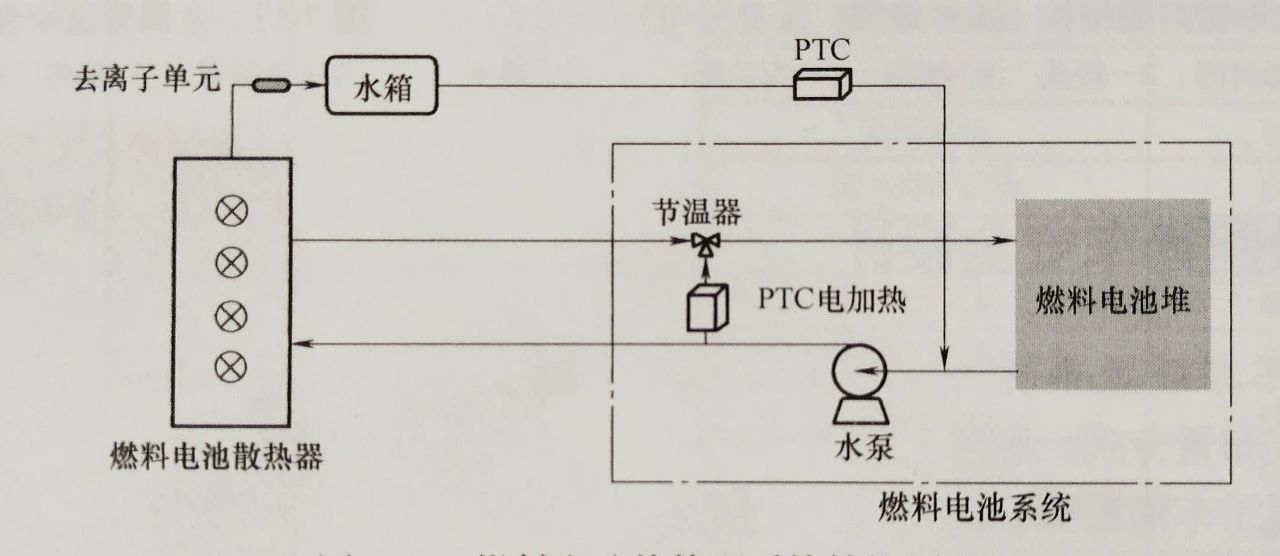
图7-15 燃料电池热管理系统结构原理
2.1.1 水泵
水泵为整个冷却液的循环提供动力。基于燃料电池的特性,需要热管理系统的水泵有以下几个特点:高的扬程(单体电池越多,扬程要求越高)、高冷却液流量(30kW散热量≥75L/min)和功率可调。根据公式Q=mc△t,由温差△t和散热量Q计算出冷却液流量,然后根据冷却液流量标定水泵转速和功率。
燃料电池水泵未来发展趋势:在满足几个指标的前提下,能耗持续降低,可靠性持续上升。
2.1.2 散热器
散热器包括散热器芯体和散热风扇。散热器芯体核心指标为单位散热面积。目前燃料电池散热器并无开发专用产品,与传统汽车散热器相同,为铝制管带式或翅片式散热器。
散热器发展趋势:开发出燃料电池专用散热器,在材料方面有所提升,要求能够提升内部清洁度和降低离子析出程度。
散热风扇核心指标有风机功率和最大风量。目前散热风扇主要为低压风扇,SPAL产品为主流,504型号风扇最大风量为4300m2/h,额定功率约800W;506型号风扇最大风量为3700m3/h,额定功率约500W。因504风扇噪声较大,目前燃料电池车辆以采用506风扇为主。
散热风扇发展趋势:散热风扇后续可以在电压平台上变化,直接适应燃料电池或动力电池的电压,不需通过DC/DC变换器,提升效率。
2.1.3 节温器
在燃料电池热管理中主要用于控制大小循环,当水温较低时,冷却液不经过散热器,由电堆出来后直接经节温器返回电堆,使电堆快速升温;当水温达到设计值时,开启大循环,冷却液经过散热器返回电堆。
节温器本质为个三通接头,分为电子节温器和机械节温器,因电子节温器成本和可靠性问题,目前以机械节温器为主。机械节温器内部为石蜡芯体,熔化温度可以根据不同燃料电池电堆需求定制。
节温器发展趋势:电子节温器是未来的趋势,能够根据需求随时控制大、小循环开启量。
2.1.4 PTC电加热
PTC电加热主要用于冬季燃料电池低温启动过程。PTC电加热在燃料电池热管理系统中一般有两个位置,如图7-15所示,在小循环中和补水管路中,以小循环最常见。
冬季低温时,从动力电池取电,加热小循环和补水管路中的冷却液,热的冷却液再加热电堆,直到电堆温度达到目标值、可以启动燃料电池,停止电加热。
PTC电加热根据电压平台分为低压和高压,低压主要为24V,需要通过DC/DC变换器把动力电池的高电压转化为24V。低压电加热功率主要受限于24V的DC/DC变换器,目前车辆高压转24V低压的DC/DC变换器最大只有6kW的规格。高压主要为450~700V,与动力电池电压匹配,加热功率可以比较大,主要取决于加热器的体积。
目前国内的燃料电池系统低温启动主要通过外加热的方式,即通过PTC加热暖机;国外的丰田等公司,则不需通过外加热,可直接启动。
燃料电池热管理系统用PTC电加热发展方向是小型化、高可靠性、安全的高压PTC电加热。
2.1.5 去离子纯化单元
去离子纯化单元的核心部分为离子交换树脂等能够吸收阴阳离子的物质。关注的主要指标为价格、更换周期。需要注意的是,去离子纯化单元不能与燃料电池防冻液产生溶解等物理化学反应。市场上主要厂家有戴纳林、曼胡默尔等。
目前冷却液电导率要求≤5μS/cm(不同燃料电池厂家要求会有不同),而去离子单元正常情况下设计的更换周期为:燃料电池运行每500h或整车行驶每10000km(先到为准)。
冷却液循环过程中需接触双极板(金属)、冷却管路、散热器芯体等诸多金属材质,长期接触不可避免地会导致冷却液中离子浓度和电导率越来越高;而燃料电池、DC/DC变换器和动力电池通过高压线实现电连接,为高压电,冷却液电导率过高会导致整车绝缘值下降,存在安全风险。因此冷却液中需要去离子纯化单元来不断吸收冷却液中的离子,如果吸收达到饱和需要定期更换。
去离子纯化单元未来发展趋势:使用寿命更长,价格更低廉。
2.1.6 燃料电池专用防冻液
目前国内主流燃料电池家只同意使用去离子水(电导率≤5μS/cm)或巴斯夫燃料电池专用防冻液。
燃料电池专用防冻液无色,能够在-36°C情况下使用,经过长期使用验证,发现对燃料电池无明显影响。目前燃料电池专用防冻液价格较高,未来期望随着参与的公司越来越多,价格能够下降。
随着制冷剂的发展,未来使用制冷剂直接给燃料电池散热也是一个重要的技术方向。
燃料电池在工作过程中,会有大量的热产生,这些热量大部分通过冷却液循环散去,一小部分随尾气排出,造成了能量的浪费。因此利用燃料电池余热主要两方面考虑:冷却液余热和尾气余热。
(1)冷却液余热利用主要方式
1)冷却液直接加热乘员舱。冷却液可以流经乘客舱中水暖散热器,实现冬季给乘客舱供暖。该方法设计简单,但对水暖散热器的洁净度要求高。
2)冷却液通过板式换热器加热乘客舱。通过板式换热器将冷却液中热量传递给乘客舱中的水暖散热器,实现冬季供暖。该方法对水暖散热器的洁净度要求不高,但冷却管路设计相对复杂。
3)冷却液通过空调加热乘客舱。将散热器集成于车载空调内部,空调空气循环系统的风吹过散热器表面时将冷却液中的余热传递给乘客舱。
上述几种方式利用燃料电池冷却液余热都有定的局限性,氢氧燃料电池反应温度低,多处于50~70°C,热品质较低,因此单纯依靠燃料电池余热并不能满足整车取暖需求,还需要配备常规的取暖装置,配合燃料电池余热共同为整车供暖。
(2)尾气余热利用主要方式
1)通过换热器利用尾气余热。燃料电池尾气热量通过尾气换热器,将置换的热量传递给水暖循环水路,再由水暖循环通过车厢内部的水暖散热器传递到乘客舱。该方法会影响燃料电池空气系统的出堆压力,对燃料电池性能的影响需要进一步评估。
2)直接将尾气净化后通入乘客舱。燃料电池尾气中含有大量的水汽和少量氢气,通过气水分离装置除水、氢气吸收装置除氢后可直接将该部分尾气通入乘客舱。
2.2 公路客车综合热管理
电池热管理主要功能包括:电池温度精确测量和监控;电池温度过高时有效散热和冷却;电池温度过低时有效保温与加热;电池包内温度场均匀分布。
电池热管理系统主要有三种形式:风冷,即电池与空气换热;液冷,即电池与冷却液换热;直冷,即电池与制冷剂换热。
2.2.1 风冷
该形式主要通过翅片散热器来实现电池热量由内向外传递,从而实现有效散热和冷却。至于加热,则主要通过电池包外加热膜的方式实现。电池风冷原理如图7-16所示。
2.2.2 液冷
该形式主要通过导热热管和水冷板实现,热管将电池热量由模组内导出传递给水冷板,水冷板再通过冷却器将电池热量交换给空调系统的蒸发器。至于加热,同样通过电池包外加热膜的方式实现。电池液冷原理如图7-17所示。
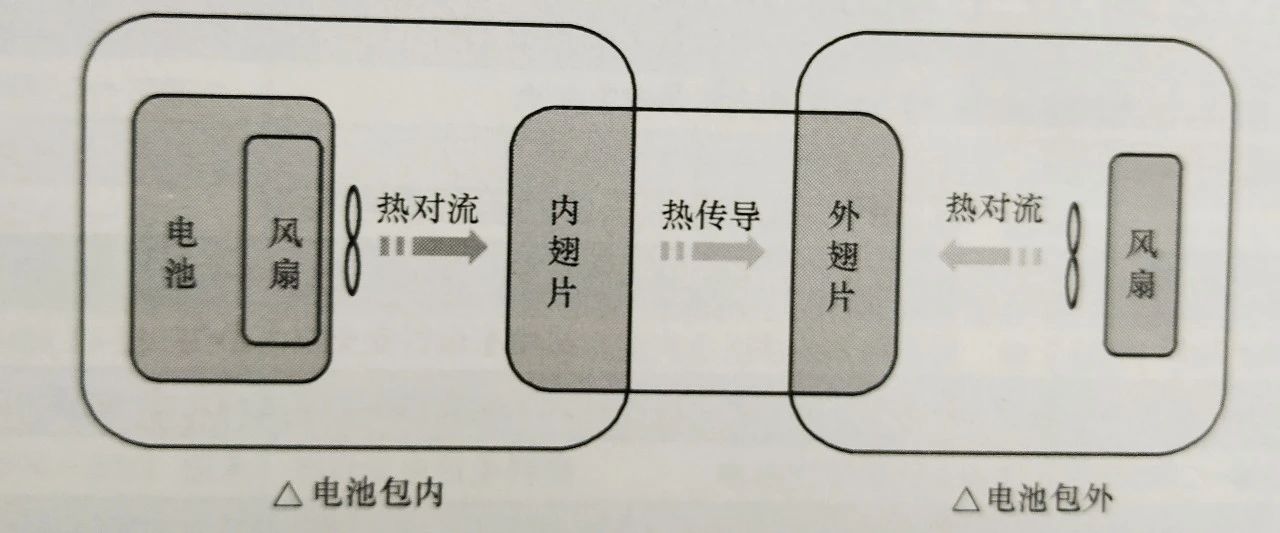
图7-16 电池风冷原理
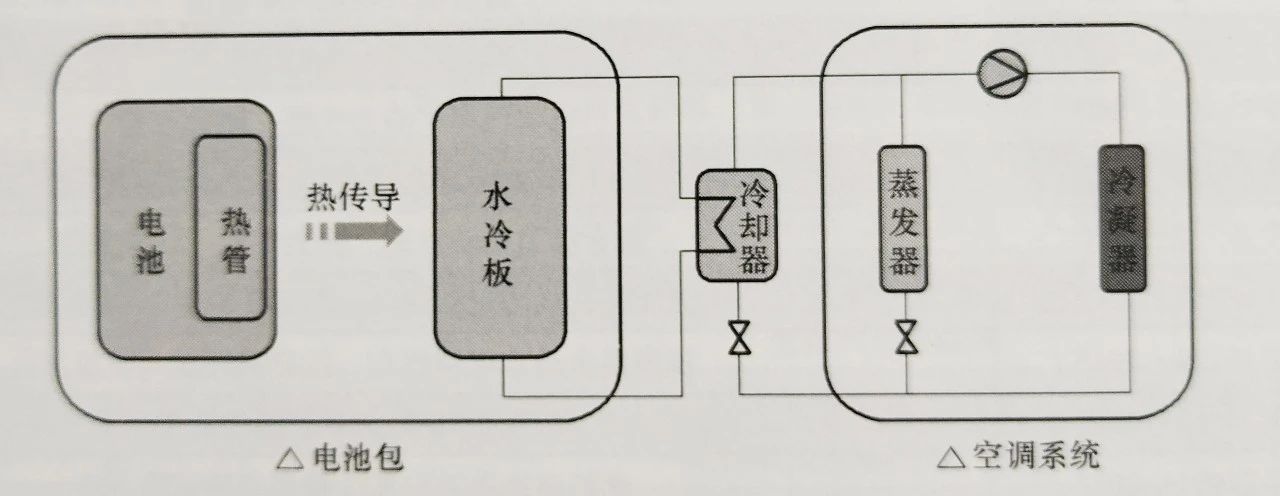
图7-17 电池液冷原理
2.2.3 直冷
电池内设置水冷板,水冷板作为蒸发器,内部流通制冷剂,制冷剂蒸发吸热带走电池内部的热量,从而实现热管理。直冷是未来的发展趋势,电池直冷原理如图7-18所示。
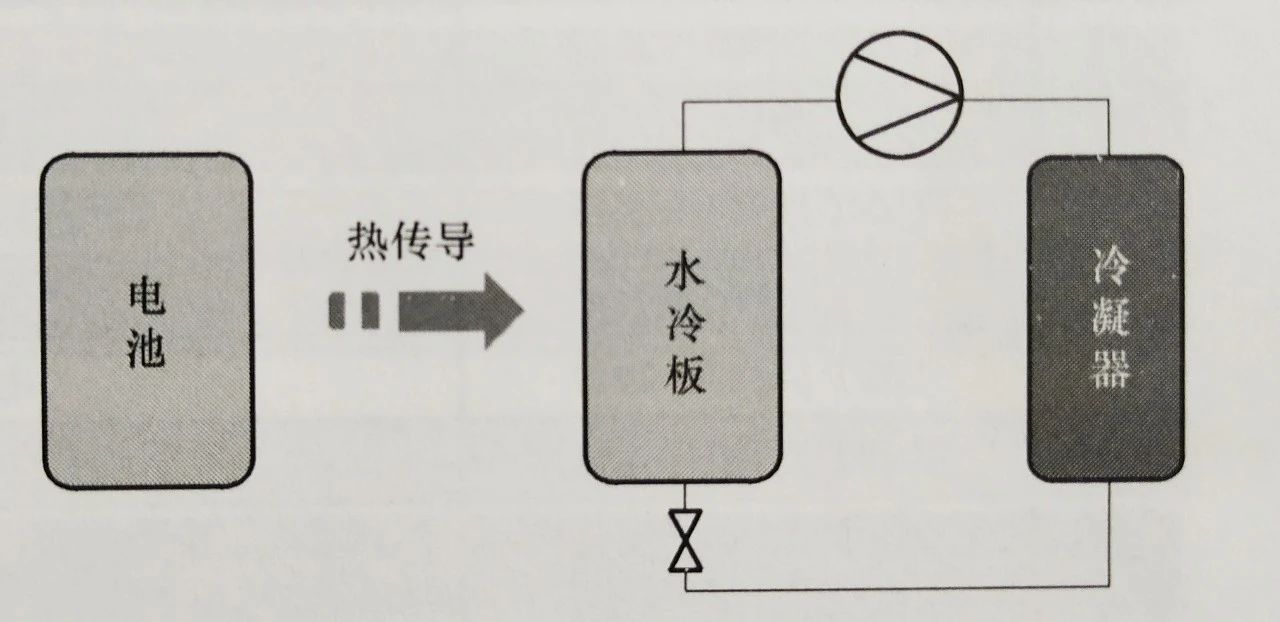
图7-18 电池直冷原理
目前燃料电池商用车采暖有多种方式:热泵空调,利用热泵原理制热,当温度过低、热泵效应受限时,通过电加热PTC制热;水暖散热器,热水流过散热器,通过风扇将热水的热量吹入乘员舱,热水主要通过PTC电加热获得;电加热散热器,电加热丝加热空气,风扇将热空气吹入乘客舱,该方式吹出热风温度高、湿度低。
未来的空调会包含更多功能,满足节能、可靠、舒适、智能的要求,空气净化技术将是未来的标准配置。
2.3 物流车综合热管理
物流车燃料电池自身热管理,主要设计准则与公交客车致;动力电池热管理形式与公路客车一致。
物流车驾驶室取暖可使用燃料电池冷却液余热,参照燃油物流车,将燃料电池冷却液通入空调系统风道内散热器,将热量通过空调系统传递到驾驶室。物流车制冷可参考纯电动物流车,使用电空调制冷。
- 下一篇:自动驾驶汽车道路安全探究(上篇)
- 上一篇:基于架构开发的汽车悬架控制臂优化设计
编辑推荐
最新资讯
-
R171.01对DCAS的要求⑤
2025-04-20 10:58
-
自动驾驶卡车创企Kodiak 将通过SPAC方式上
2025-04-19 20:36
-
编队行驶卡车仍在奔跑
2025-04-19 20:29
-
全国汽车标准化技术委员会汽车节能分技术委
2025-04-18 17:34
-
我国联合牵头由DC/DC变换器供电的低压电气
2025-04-18 17:33