摘要:产品的RAMS设计与分析是提高产品竞争力的必由之路,是企业的管理决策系统的组成部分。现阶段RAMS主要采用专家组评审并基于表格的方式进行实施,工业数字化阶段RAMS遭遇系统复杂性增加、分布式设计与国际化、减少成本与认证周期、有效产品维护等方面的挑战;现有RAMS工具具有主观因素影响、数据可用性有限等缺陷。基于模型的系统工程工具MADe建立了RAMS的风险数字双胞胎,功能包括基于功能分析方法的模型建立、安全与风险分析、可靠性、可用性与可维护性分析、产品的故障进行预测与健康的管理;具有在产品生命周期的每个阶段确保RAMS的实施、整合功能规范和供应链、集成PLM与数字孪生、更完整的FMEA分析等优势;复杂装备与军工领域具有多个用户。
1前言
1.1初识RAMS
每个有燃油汽车的人几乎都有“汽车每5千公里需要小保养,每2万公里就要大保养”的常识,但为什么汽车要5千公里、2万公里就进行保养,新品类电动汽车保养是否也采用同样的保养方式,类似的交通工具如飞机、船舶、火车是应该怎么保养与安全使用方式,工业中核电站装备、航空发动机、柴油机、机床、大型医疗器械等是应该怎么保养与安全使用方式等问题绝大多数人就应该不知道了。
以上问题实际上是在产品的设计阶段就需要严格考虑的技术问题,对应的技术名词叫做RAMS设计与分析。RAMS即可靠性(Reliability)、可用性(Availability)、维修性(Maintainability,含测试性Testability)、安全性(Safety)的缩写,横跨工业产品设计阶段、产品验证阶段、产品批量化制造与工作维护阶段的技术问题;关心RAMS设计与分析的工业领域机构也都是大家耳熟能详工程领域的行业巨头机构,例如国际系统安全学会、可靠性工程学会、工业与系统工程师学会、电气与电子工程师协会等等。
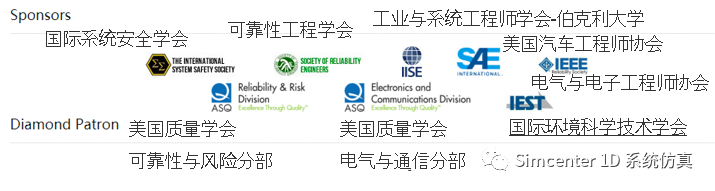
图 RAMS领域国际领导工程机构
RAMS是提高产品竞争力的必由之路,流程上RAMS贯穿产品生命周期全过程,具体工作包括设计、分析、试验和管理四个方面,缺一不可;RAMS应当与产品研发各阶段同步进行,并落实到产品的设计、工艺、制造和使用维护中去。
RAMS是企业的管理决策系统的组成部分,涉及到的人员除了各级领导外,还需要全体工程技术人员来贯彻实施,包括设计工程师、可靠性工程师、维护工程师、测试诊断工程师等,必要的时候RAMS工作还需要延伸到各级供应商。
国内军工体系与重大装备产品的设计与RAMS相对应的有GJB9001B国军标六性设计,具体包括可靠性、安全性、维修性、可测性、保障性、环境适应性。GJB9001B国军标六性设计也是基于国际协会拟定的方向,基于自己的装备与系统提出并逐步形成;二者虽然名称与内容上有一定差别,但是关注的具体方向基本上是一致的。
现阶段国内绝大多数企业的RAMS设计与分析仍然是以满足法规而做的分析,部分认识到RAMS技术对企业发展重要性的企业,通常情况下具体的实施方式如下:1) 在产品的设计阶段形成专家组,基于专家组的经验与前期同类产品研发、制造与用户使用过程整个生命全周期出现的故障与解决方案等进行综合设计与分析的评审;(国际上各大成熟工业产品均具有自己整个生命全周期中故障与解决方案不断更新的数据库,例如 Ford 汽车基于其产品的长期开发迭代形成的 RAMS 数据库就是汽车领域领域最大的数据库之一)2)基于评审中的信息与解决方案确定RAMS各主要问题设计、制造与产品维护过程中的应对方法,可以形成DFEAM、PFEAM、FMEAC等跟踪文档,基于跟踪文档的技术实施,保证产品的RAMS性能;此次评审中未提及或未预见的技术问题如果在产品研发、制造、使用生命全周期出现,则可能需要通过下一轮的产品迭代进行解决,如果所出现的技术问题严重危害安全性、可靠性则需要立即成立专家组进行补救解决;
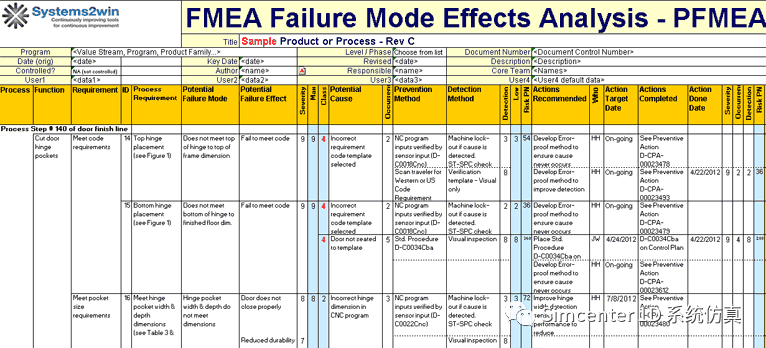
图 研发与生产阶段的失效分析评审文件
3)如果在产品研发、制造、使用生命全周期中出现了安全性、功能性等严重问题时,则产品的研发、制造都可能需要紧急停止,正在使用的产品也需要被召回进行改进;(大量的汽车、飞机召回事件,就是由于用户使用过程中发现了很严重RAMS问题后的紧急补救措施,这些措施会带来了严重的经济与企业信用损失。由此可见,全面严格的RAMS实施实际上是关系到企业生存重要保障;军工领域的RAMS问题则可能会造成战争中装备的失灵,并进一步关系到军事的成败)
为了满足产品RAMS的要求,安全性、可靠性要求较高的特殊工业产品,例如飞机则需要做大量的试验以确定产品的RAMS性能。例如对于商用飞机就有大量的FAA适航认证要求;下图即为FAA认证标准与飞机机身的适航认证过程;火箭、卫星等,也具有大量的RAMS试验确保其在空间中可靠运行。
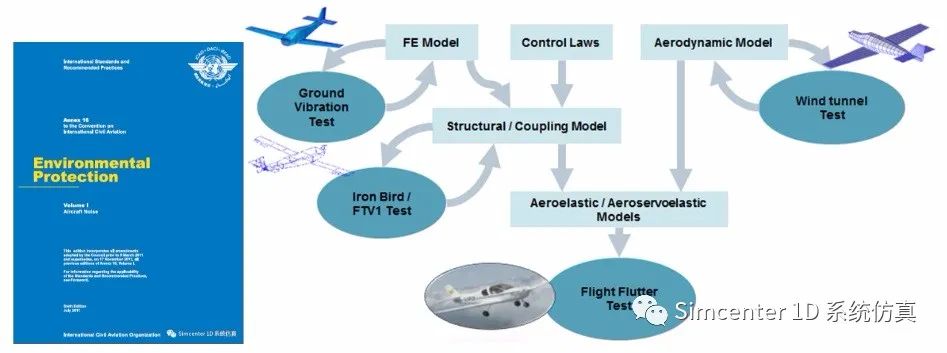
a) FAA适航认证要求 b)机身适航认证过程
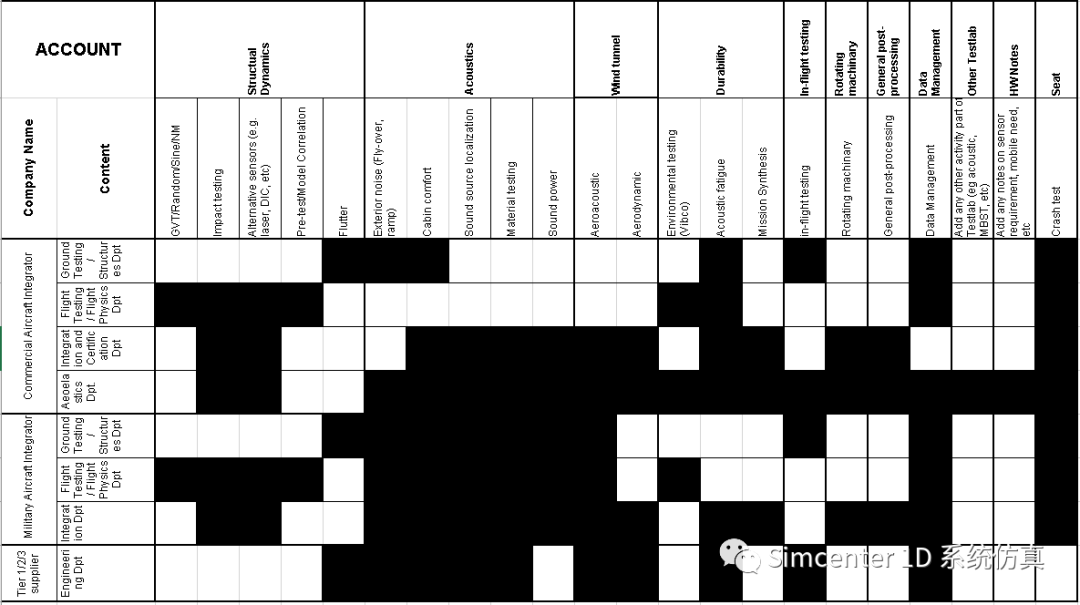
c)西门子飞机适航认证试验矩阵
图 飞机的RAMS试验
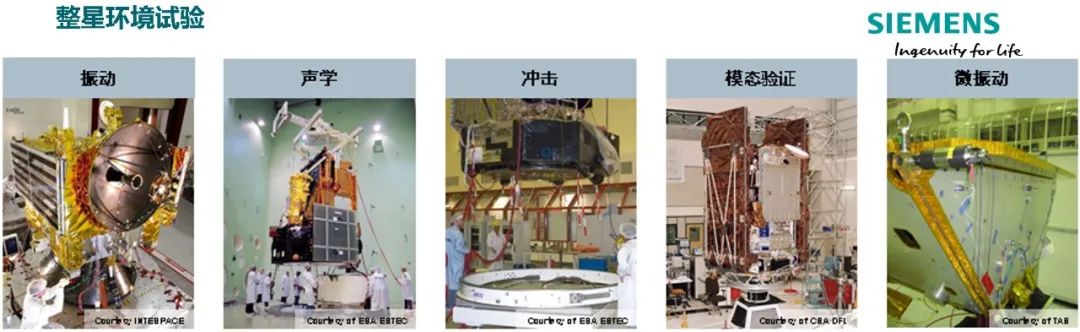
a)航天领域RAMS性能相关试验
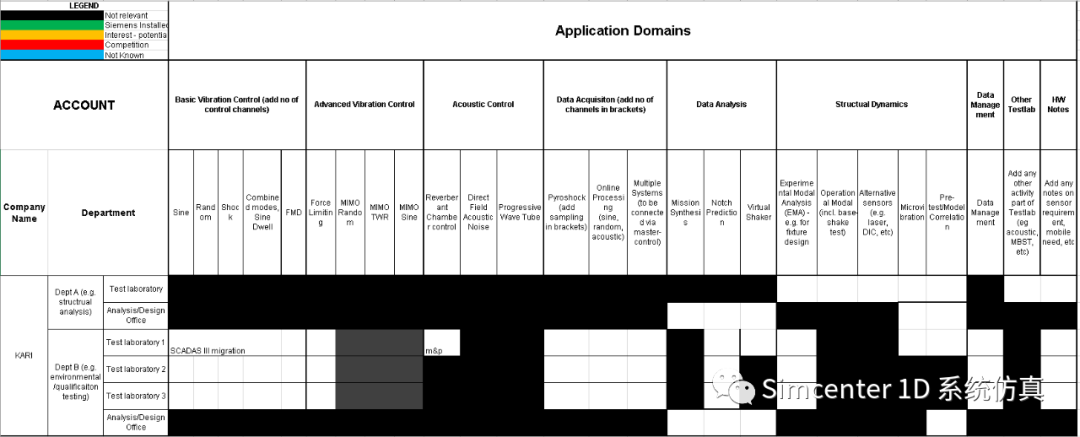
b)西门子航天领域试验矩阵图
图 航天RAMS试验
RAMS实施的关键步骤包括:数字化系统集成、安全与风险评估、法规与标准的验证、可靠性与可用性的分析、操作与维护设计、智能监控与评估、维修与维持费用评估、知识的获取与重用等;具体如下图所示:
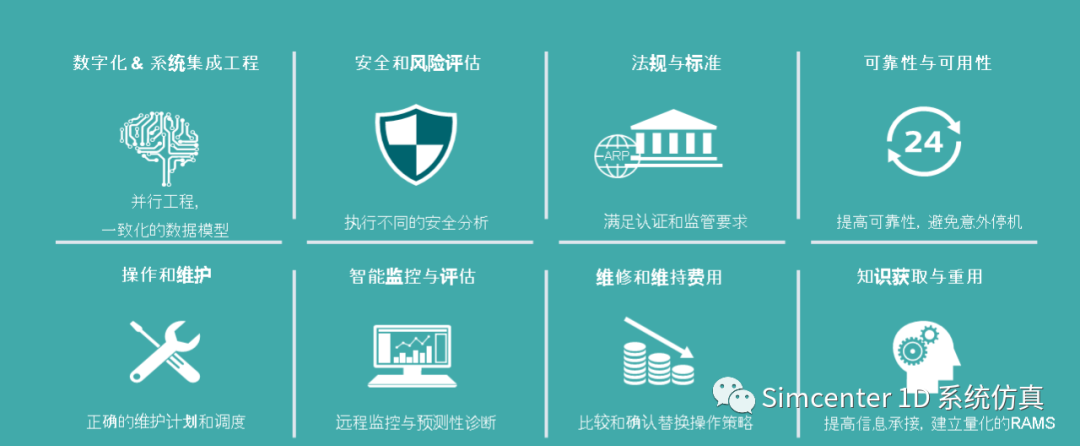
图 RAMS实施关键步骤
1.3 工业数字化阶段RAMS的挑战
工业的数字化无疑会为工业带来突飞猛进的变化,工业产品种类会更多,产品也会更加复杂,对RAMS的实施也就带来了更多的挑战。
1)系统复杂性带来的挑战:
RAMS专家组的经验通常情况是前期设计中遇到的特殊情况解决方法,对于越来越复杂的工业产品,是无法囊括所有的RAMS技术问题的;例如对于具有400万个零件、供应链涉及30个国家的波音380,就不可能仅凭借前期专家组开发机型的经验来解决波音380的RAMS问题;
此外,整机专家组的经验主要集中于整机级及其一级或二级子系统,对于更深层次的技术问题则无法透彻地进行分析,这在子系统单独运行时是一个状态,子系统集成到上一级系统后子系统特性发生变化的场景下尤为突出。
2)分布式设计与国际化带来的挑战:
现阶段复杂产品的设计跨跃多个部门与单位,甚至跨跃多个国家,复杂产品的供应商来源于多个国家,例如商飞现阶段航空发动机来源于英国的罗罗,航电系统来与美国的霍尼韦尔,各个部件的集成与团队协作离不开远程分布式实施;
RAMS的实施离不开各个部门之间进行交互与整合,分布式与国际化的状态对RAMS实施的统一性、效率提出了更大的挑战。
3)减少成本与认证周期、有效产品维护的挑战:
从上面RAMS的实施过程中我们可以看出,现有RAMS的实施系统存在无法完全覆盖的技术盲点,主要原因是概念设计或产品定义阶段由于专家组经验的适用范围无法覆盖新产品的技术问题,对于一个全新的工业产品基于前期经验的RAMS设计与分析无疑会带来更多核心技术问题的遗漏;如下图所述绿色线即为设计过程中设计缺陷各阶段发生的统计结果;
图 产品成本、失效原因、失效发现关系
而在产品样机生产已经完成,验证试验结束并进行产品的发布阶段,由于前期设计引起的绝大多数缺陷才会被发现,而此时产品研发与试制的成本已经产生,并且此阶段一旦出现问题则无法避免校正所带来的高昂成本与产品投产延迟。
对于飞机产业而言,统计表明按照传统的RAMS进行认证所产生的费用已经比开发飞机的花费更多,周期也更长;例如波音787客机需要20个月的认证过程,230多万件零部件来自45家一级供应商(30%来自国际供应商)。
4)新型商业模式的挑战
“基于性能的保障”(PBL)签订合同的商业模式在航空发动机领域已经获得了很好的应用,例如罗罗与GE航空发动机公司,均通过签订航空发动机按照正常运行的时间周期与其客户签订合同的方式对航空发动机进行售卖。此外美国海军自2004年起就采用“基于性能的保障”(PBL)的方式为美海军“海鹰”直升机(MH-60)提供持续保障服务,与西科斯基和洛马公司合资成立的“海事直升机保障公司”合作,对共530架直升机和约1700个零部件提供保障服务。多于单件价值高,运行可靠性高的工业产品,采取“基于性能的保障” (PBL)签订合同的模式已经成为企业源源不断发展的有效商业模式。 “ 基于性能的保障 ” ( PBL )签订合同的模式中,采用有效地、成本更低的产品性能维护与方式则成为该商业模式成功实施的关键;这对 RAMS 实施的应用与推广即是机遇,也是挑战。
2 基于模型的产品风险数字双胞胎
2.1产品风险数字双胞胎平台MADe
自从西门子2017提出了数字化双胞胎的概念后,随着人们对数字化的理解,数字双胞胎的分类与划分也越来越详细,现阶段产品数字双胞、生产数字双胞(西门子收购软件整合后的综合平台是Opcenter)与性能数字双胞胎(西门子收购软件整合后的综合平台是Simcenter)的分类方式已经基本成为数字双胞胎的共识。
图 数字双胞胎架构
西门子的产品风险数字双胞胎是基于MADe软件平台建立模型进行RAMS分析,MADe全称为Maintenance Aware Design environment。MADe的分析过程遵循基于模型的系统工程方法(MBSE),基于MADe软件平台可以实现:1) 对产品进行系统建模,基于系统模型对产品失效模式进行仿真分析;3) 基于系统模型对产品的可靠性、可用性与可维护性分析与设计;4) 基于系统模型对产品的故障进行预测与健康的管理;
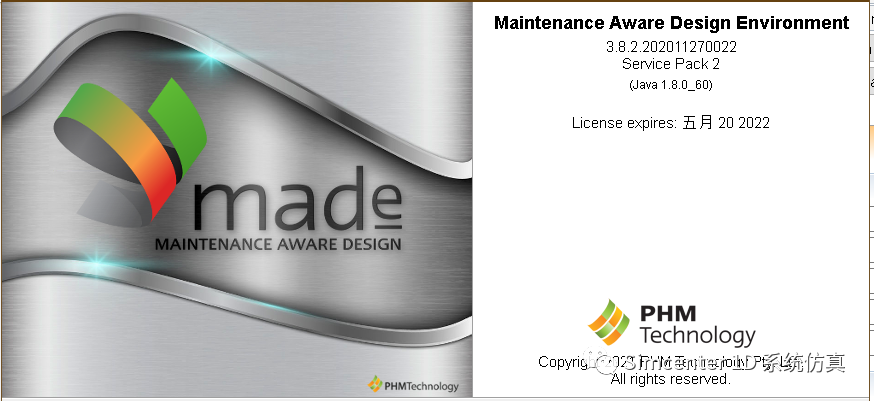
图 MADe软件平台
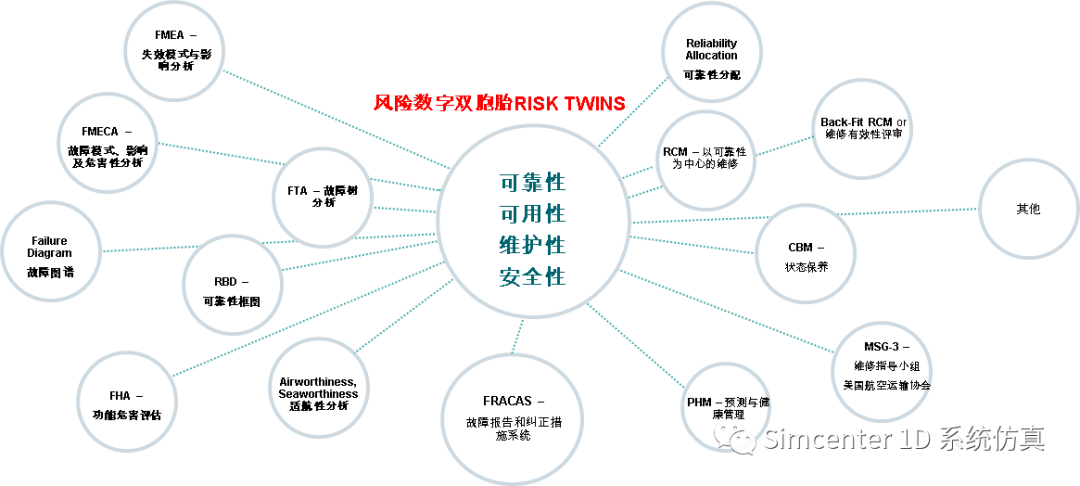
图 MADe风险数字双胞功能图谱
MADe中RAMS设计与分析主要功能图谱如上图所示。基于MADe对RAMS进行的设计与分析更多地与性能数字双胞的内容相关,但与产品数字双胞与生产数字双胞台又具有密切的联系:
-
与产品数字双胞之间的关系:MADe中系统建模所使用的功能分析方法与产品数字双胞胎是一一对应的,在产品组成已经知道的情况下,RAMS模型中的系统组成架构来源于产品数字双胞胎;
-
与生产数字双胞胎之间的关系:MADe平台RAMS分析产生的FEMA等报表是可以与生产数字双胞相对接的,是西门子OpcenterQuality模块在产品研发阶段的实施方式;
-
与性能数字双胞胎内部各个模块之间的关系:MADe的RAMS分析结果在产品的研发阶段,是产品设计试验仿真一体化研发过程中试验验证需求的提供方与规划方,试验验证结果的反馈则是RAMS体系中产品迭代知识获取的重要来源。
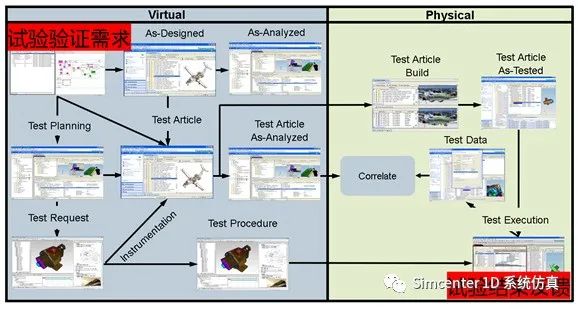
图 西门子设计试验仿真一体化架构
此外,MADe还可以与西门子其他模块形成综合解决方案;例如与Teamcenter、Mendix、Simcenter等模块综合形成FRACAS(故障报告、分析及纠正措施系统),可以实现产品的质量回溯闭环回路。具有非常明显的优势:
图 MADe形成的FRACAS
FRACAS是华为等优秀企业正在使用的体系。如下图所示为华为的FRACAS进行质量回溯的流程。
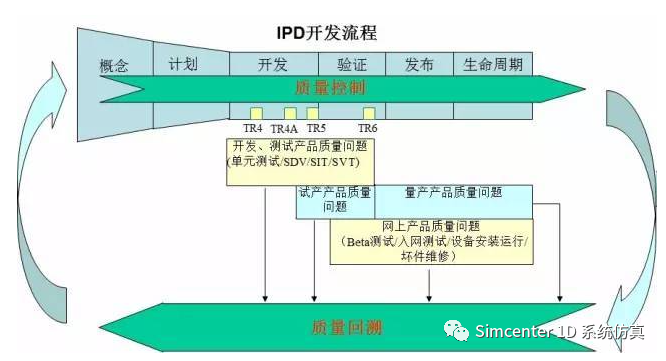
图 华为的FRACAS质量回溯系统
MADe的具体实施从系统建模开始,过程与内容如下所示。
-
含有维护理念的设计模型(MADeModeling):通过该模块可以基于功能分析方法建立系统架构模型(SystemModel)、功能模型(FunctionDiagram),定义产品的研发与运行全生命周期过程(MissionProfile),定义产品运行过程中的维护方式(MaintenanceActions)等;
-
安全与风险评估(SRA):基于所建立模型,通过失效注入(Failure Injection)的方式可以生成产品失效框图(Failure Diagram),可以对保证整个产品正常运转的关键因素进行分析与确认(Critical Analysis),可以分析各组成失效所带来的危害程度(Function Hazard Analysis),并可以获得模型中引起故障的可能原因,具有故障树建立工具(Fault TreeBuilder)建立产品故障树(FaultTree),可以形成失效模式库(CommonModel Analysis)作为产品优化迭代与新一轮产品设计参考;
-
可靠性、可用性与可维护性的分析与设计(RAM):基于所建立的模型,基于模糊认知图(Fuzzy Cognitive Map)的方法与键合图(Bond Graph)的方法可对故障率进行预测(Failure Rate Prediction)、可进行马尔可夫分析(Markov Analysis)、生成可靠性框图(RBD)并进行可靠性的分配(Reliabilityallocation),基于研发与运行全生命周期过程(MissionProfile)对维护的费用进行估算(MaintenanceCost Estimates),从而选择最优的维护方式;可对可靠性性维护方式(RCM)方式进行设计评估;
-
故障预测与健康管理(PHM):对产品的状态进行维护(RCM)离不开对产品的状态进行确认;故障预测与健康管理(PHM)就是通过在产品相应的部件上布置对应的传感器进行状态的监测与报警;可在PHM中的诊断分析模块(Diagnostic Analyses)实现传感器种类的选择与设计(Automated Sensor Generation)与优化;可以设计传感器族(Sensor set)与布置的位置(Sensorallocation);可设定诊断的准则(DiagnosticSets),并对比不同传感器布置方式的数量(Numberof Sensors)、成本(Costof Detection)、探测概率(ProbabilityDetection)进行统计分析,形成最优的监测方式;
-
报告的输出(ReportWizard):以上分析可以自动生成标准化的报告,例如FMEA(AIAG,FMEA 4th Ed.)、FMECA(MIL-STD-1629A)、FMECA Maintainability Information(MIL-STD-1629A)、Functional Hazard Assessment(SAE ARP4761)等35种行业标准要求格式的报告;输出格式可以Pdf或Excel或CSV格式;便于用户根据标准报告调整成为自己独特的报告格式。
后期将详细介绍MADe中各个模块的具体功能与应用情况。
图 MADe产品风险数字双胞实施过程
2.2 基于模型RAMS的优势
MADe是基于模型的RAMS分析,相对于传统的RAMS分析方法具有明显的优势。
图 传统RAMS项目组成员信息架构图
-
在产品生命周期的每个阶段确保RAMS的实施;
-
可以整合功能规范和供应链;
-
可以集成PLM与数字孪生;
-
可以自动模拟系统的功能关系和相互关联;
-
复合分析:实现功能与性能的同步分析;
-
完整的失效工况分析:基于多层级模型获得完整的失效模式而不遗漏;
-
基于模型可设计分析各个因素的影响并优化设计;
-
可以根据模型实施配置管理;
-
可基于模型进行持续改进;
-
有效的知识获取:基于模型可追溯有效的知识信息并重用;
-
单一真相:设计工程师、可靠性工程师、维护工程师、测试诊断工程师之间的信息是统一的;
图 基于模型的RAMS项目组成员信息架构图
3 应用案例
MADe已具有重大装备与军工领域的多个用户,如下图为各主要领域的用户。
4参考文献
[1] Nancy J. Lindsey, MahdiAlimardani. Luis D. Gallo. Reliability Analysis of Complex NASA Systems withModel-based Engineering. Reliability & Maintainability Symposium(RAMS).2020.
[2] Hong Suk Chang1, Jong Chan Park.A Study on PHM Method Suitable for Motor-Driven Commercial Vehicle. ANNUALConFERENCE OF THE PROGNOSTICS AND HEALTH MANAGEMENT SOCIETY 2016.
[3] William Glover1, Joshua Cross1,Andrew Lucas1, Chris Stecki2, and Jacek Stecki. The Use of Prognostic HealthManagement for Autonomous Unmanned Air Systems. Annual Conference of thePrognostics and Health Management Society, 2010.
5作者简介:
蒋爱华:上海交通大学机械系统与振动国家重点实验室,机械设计及理论方向博士毕业;研究方向包括流激振动、转子动力学、振动信号处理与故障诊断等,参与过多项国防科工委基础预研项目;发表论文24篇,专利15个。曾负责Simcenter Test试验验证,现阶段关注Simcenter 1D基于模型的系统工程(MBSE)。