数字控制替代模拟控制,电池分容化成测试精度效率再提升
为什么电池制造需要分容?
电池的分容是通过化成分容柜来完成的,它可以同时为大量的电池充放电。电池分容时通过电脑管理得到每一个检测点的数据,从而分析出这些电池容量的大小和内阻等数据,确定电池的质量等级,这个过程就是分容。
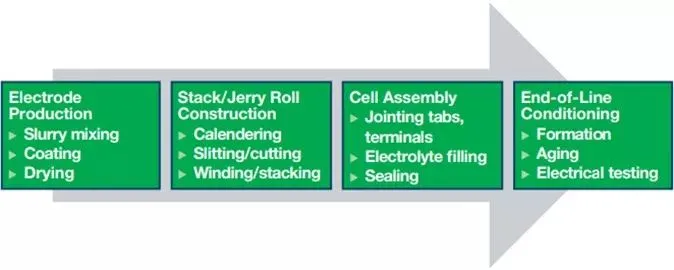
锂离子电池制造的漫长过程
分容的另外一个目的是对电池进行分档组编,就是筛选出单体的内阻和容量相同的单体进行组合。组合时,只有性能很接近的才能组成电池组。比如,动力电池组为满足电动汽车的能量需求,往往需要数十支到数千支电池组成,受到系统复杂性的影响,电池组的行为有其独特性,并不是单体电池的做一个简单的加减法就能够获得电池组的性能。
另一方面,单体电池的一致性差也可能会导致电池组安全性降低。研究显示即便是单体电池循环寿命可达1000次以上,在组成电池组时,如果没有均衡设备的保护,电池组的循环寿命可能不足200次。
因此,为了提高电池的循环寿命、稳定性、自放电性、安全性等电化学性能,必须严格控制锂电池的一致性或精确评定电池等级,所以对分容设备的电流和电压的测量精度有很高的要求。
高精度、高效率电池分容化成系统设计
限于传感器采集精度,目前市场上化成分容设备电流和电压的测量精度一般在千分之一左右。对于电池分容过程而言,电流和电压的控制精度越高,锂电池产品的质量就会越好,电流电压传感器在万分之一以上的精度是比较理想的选择。
为了降低电池成本,制造商需要统筹兼顾,首先利用供应商的系统级专业知识来减少整体电池测试电路面积大小,同时增加通道的数量。需要注意的是,两者必须同时保持电池化成和测试测量的准确性、精确性、可靠性和速度,确保满足安全、性能和可靠性要求。而要进行这些重要的电池测量,需要质量很高的仪表放大器和相关的并联电阻来测量电池充电/放电电流,即使在恶劣的工厂条件下,也要实现±0.05%以上的精度。
因此,电动汽车电池制造商与例如ADI等拥有化成和测试系统专业知识的供应商合作,能在这一关键制造阶段减少所涉时间和成本,同时仍保持先进电池化学制品所需的精确性。
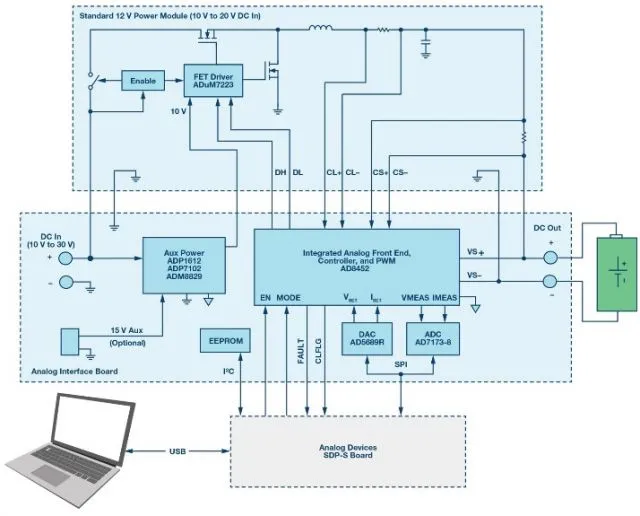
AD8452电池分容化成解决方案
将电池分容所涉及的测试组件合并为一个完整的解决方案有多种方式,但要最大限度地提高性能和减少系统占用空间,这是一个重大的挑战。这也是ADI将模拟前端、功率控制和监控电路集成在单个IC AD8452中的原因。AD8452为电池分容化成系统提供了高精度(依据具体设计方法,最多可达0.01%精度),高可靠性,高效率的单芯片方案,同时减少了所需器件数量和电路板布板面积。每片AD8452既可以单独控制最多30A的充放电流,也可以多片并联,来控制更大的输出电流。
降本增效,ADI新一代分容测试技术解读
AD8452基于模拟控制回路的架构,在当时设计理念也是非常先进的,得到了客户大量的使用和广泛的认可。时至今日,电池分容化成测试设备开始逐步由模拟控制向数字控制演进。因为针对不同的电池测试参数,传统的模拟环路只能去通过修改或调整线路板上的电容或者是电阻网络去改进这个值,这不仅对电容提出了很高的要求,在测试进行的过程中的调试也会非常不方便。如果是数字控制环路的测试方案,可能只需修改几行代码即可完成,大大提高了测试效率。
正是基于这种理念,ADBT1000/1/2系列芯片便是ADI新推出的高精度测试芯片,基于数字环路控制设计,集成了外围的ADC、检测电路,可以大大减少客户开发电池分容系统的时间。
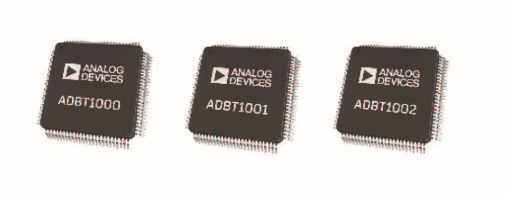
与此同时,相较AD8452的单通道方案,ADBT1000系列芯片拥有最多4个数据采集通道,客户可以多路自由组合。例如同时可以两两定向,既能通过两个通道的并联,去输出更大的电流,也可以把4个通道同时并联,单芯片实现了高达240A的大电流充放电,符合于现阶段电池容量持续提升的大趋势。
本文小结
随着电动汽车市场的爆炸式增长,对车辆供电的高性能电池需求也随之增加。ADI持续研发了许多新产品、参考设计和集成解决方案,新一代ADBT1000系列测试芯片便在提供高精度的同时,以数字化环路控制替代模拟控制,提高了工厂对于电池分容化成的测试能力,扩大了测试规模,使制造商能够更高效地生产安全强劲的动力电池组。
- 下一篇:250.3亿!中国车谷重大项目签约
- 上一篇:苹果发布自动驾驶汽车V2V通信系统专利
编辑推荐
最新资讯
-
全球首次!IVISTA 2023版修订版引入带灯光
2025-04-28 09:59
-
我国首批5G毫米波行业标准送审稿审查通过
2025-04-28 08:56
-
5/16 厦门- 新能源汽车电驱测试技术的创新
2025-04-28 08:53
-
国内首个汽车电磁防护技术验证体系EMTA正式
2025-04-28 08:49
-
一文带你了解滤波器
2025-04-28 08:35