车用燃料电池热管理性能仿真与试验研究
前言
燃料电池汽车作为一种清洁能源交通工具,具有高效节能、排放无污染等优势,已经成为未来新能源汽车行业发展的一个重要技术方向。与传统的燃油发动机相比,燃料电池的效率要高10%~20%,但是燃料电池对于工作环境温度的要求比较严苛。例如质子交换膜氢燃料电池(proton exchange membrane fuel cell,PEMFC)的适宜工作温度一般在60~80 ℃,少数可达到90 ℃。温度过低,会导致燃料电池内部催化剂活性降低、欧姆极化严重并使电池阻抗增加,从而降低电池性能。温度过高,会加剧电池内部液态水的蒸发而引发质子交换膜脱水干涸,阻碍氢离子的传导并降低电池的效率,长期高温还会损害电池寿命。热管理性能作为影响燃料电池工作效率、寿命和安全的重要因素,是目前燃料电池汽车研究的技术热点。
Adzakpa、Amphlet 和Pukrushpan 等建立了电堆的动态仿真模型,分析电堆启动、负载阶跃变化和电堆停止时电堆电压及温度的动态变化。上述文献只对电堆本体的特性进行研究,并未考虑电堆外部的热管理部件,并且所建立的模型复杂度较高、计算效率相对较低,用于整车系统级的分析难度较大。对此,郭爱建立了车用燃料电池热管理系统模型,研究了电堆电流、冷却液流速、旁路阀开度等因素对电堆及散热器入口与出口温度差的影响。常国峰等建立燃料电池汽车热管理系统散热器模型,使仿真误差控制在10%以内。丁琰基于AMESim软件建立整车热管理系统一维仿真模型,并对极端工况下的热管理性能进行评估。
本文中采用理论与试验相结合的方法,根据电堆工作时的功率电压之间的关系,基于AMESim 软件平台建立电堆的稳态热模型,并以此为基础建立燃料电池热管理系统模型。经验证,该模型可较准确地评估电堆在不同工况下的出水温度,为燃料电池热管理性能分析和优化提供了参考,具有实际工程意义。
1 燃料电池热模型
1.1 燃料电池产热模型
燃料电池工作时,氢燃料和氧气发生化学反应,一部分能量转换成电能对外输出,一部分能量以热的形式耗散掉。氢燃料电池发生如下的化学反应:
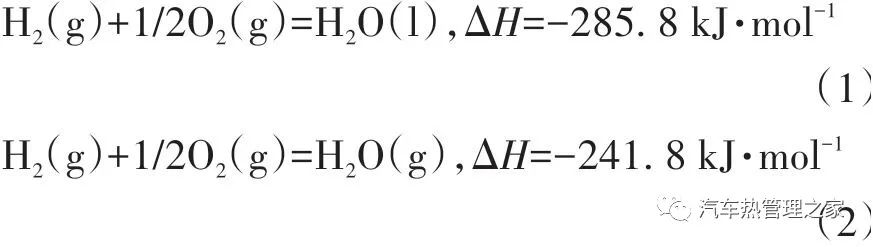
式(1)表示化学反应全部生成液态水,对应的焓差为-285.8 kJ·mol-1,称为高热值,负号代表放出热量;式(2)表示化学反应全部生成水蒸气,对应的焓差为-241.8 kJ·mol-1,称为低热值。根据上述热反应方程式,可以计算出室温和标准大气压力下燃料电池单体的理论电压值。

式中:k 为反应过程中消耗1 mol 反应物所转移的电子数,对于氢燃料电池,k=2;e 为元电荷数,e=1.60×10-19 C;NA 为阿伏加德罗常数,NA=6.02×1023 mol-1。假设燃料电池反应的生成物全部都是液态水,则通过高热值△H=-285.8 kJ·mol-1计算得到燃料电池单体的理论电压值为U0=1.48 V,低热值计算理论电压值为U0=1.26 V。某款氢燃料电池汽车电堆的正常工作区间内,单体电压值U 处于0.59~0.81 V 之间。根据式(4)可计算得到该电堆的效率范围处于46.8%~64.3%之间。

假设燃料电池工作时,燃料完全反应所产生的能量除了转化为电能之外,其余能量全部以热量的形式耗散掉。如果已知电堆工作时的功率P 及其单体电压值U,则根据电堆效率式(4)可计算电堆工作时的产热量Q1,如式(5)所示。

1.2 燃料电池散热模型
车载燃料电池的散热途径主要有3 种。第1 种是电堆本体与环境之间的辐射散热,散热量一般不超过电堆总发热的1%。第2 种由排气系统带走部分的废热。燃料电池系统的排气温度范围处于70 ℃~90 ℃之间,相对传统燃油车而言,废气带走的热量非常有限,仅占电堆总发热量的3%左右。第3 种是通过热管理系统与冷却液之间进行换热,冷却液带走的热量占电堆总发热量的95%以上。因此要保证电堆始终处于适宜的工作温度范围内,热管理系统的散热性能是关键。热管理系统运行时,由冷却液带走的热量Q2为

其中:c为冷却液的比热容;m 为冷却液的质量流量;T1为电堆进口水温;T2为电堆出口水温。忽略辐射散热和排气系统带走热量的条件下,当燃料电池系统处于热平衡状态时,电堆产生的热量与冷却系统带走的热量是相等的。可建立电堆发热与散热之间的热平衡方程式,如式(7)所示。

根据上述电堆热平衡方程式可知,当电堆功率与效率一定时,决定系统散热能力主要参数是冷却液流量m 和冷却液水温T1和T2。T2由电堆内部流道结构、电堆本体的材料热属性和电堆的功率状态决定。T1则与前端散热器的性能和进风温度相关,是热管理系统设计要重点关注的参数。工程上通过电堆台架测试,可获得电堆功率、单体电压、冷却液流量和温度等参数,通过电堆热平衡方程式可评估电堆在不同工况下的发热情况。台架实测电堆散热量与电堆产生模型计算的产热量对比如图1所示。
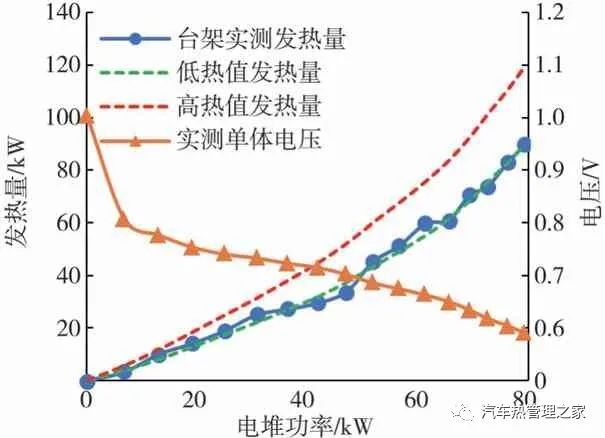
图1 电堆发热量实测与理论计算结果
图1 中,红色虚线和绿色虚线分别是采用高热值和低热值经过产热模型理论计算得到的电堆发热量,蓝色曲线是根据台架实测电堆进、出水温度和流量数据,通过式(6)计算得到的电堆实际散热量。台架测试结果表明,电堆产热模型中以高热值计算的电堆发热量比试验值偏大,而以低热值计算的电堆发热量跟台架实测试验值基本一致,误差均在5%以内。试验结果证明了所建立的电堆产热模型的有效性,后续建立热管理系统一维仿真模型时将以低热值计算电堆发热量。
2 热管理系统建模与仿真计算
2.1 建立热管理系统模型
电堆热管理系统包括电堆、高压水泵、水壶、散热器、中冷器、离子交换器、和冷却管路等部件,其热管理系统架构如图2 所示。利用AMESim 软件建立电堆热管理系统一维热管理模型,如图3所示。
建模的关键是电堆的发热量输入和散热器标定。电堆发热量计算模型在上一节已经通过台架试验得到验证。散热器的建模主要采用对数平均温差法来计算散热负荷。利用软件半经验公式标定方法,得到努谢尔特数Nu 和雷诺数Re 求解。然后计算散热器空气侧和液侧的对流换热系数A 和散热器的传热系数k,计算对数平均温差。最后查取修正系数,得到散热器的散热量[13]。表1 所示为散热器模型计算的散热量与散热器风洞测试的散热量对比,证明了散热器模型的准确性。
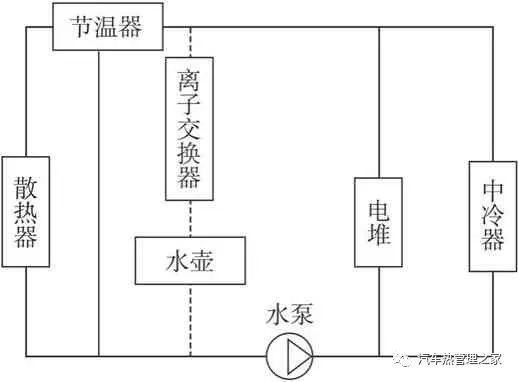
图2 整车温控系统架构图
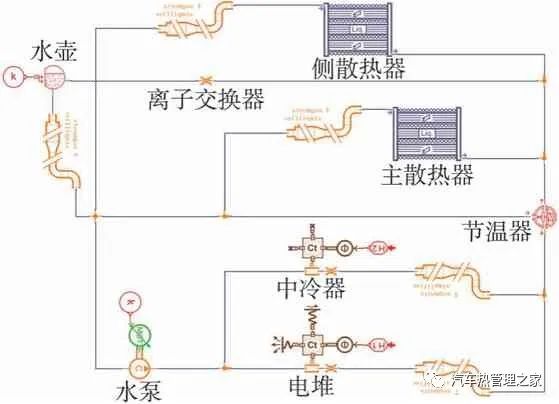
图3 整车温控系统架构图
表1 散热器散热量仿真与实测结果对比
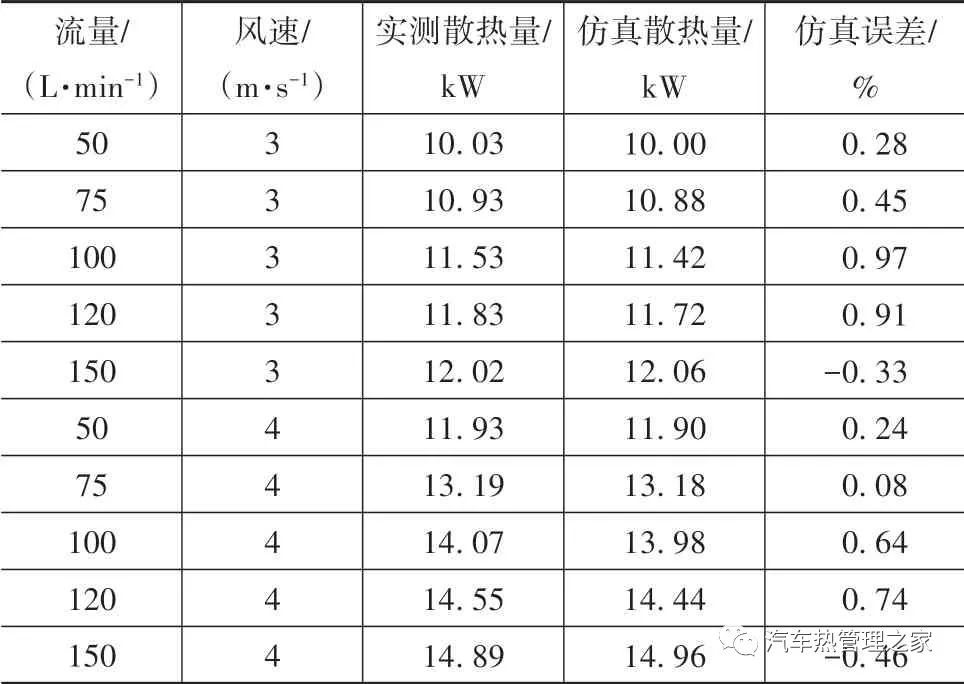
2.2 仿真计算
利用已经建立的电堆热管理系统一维仿真模型,可以预测在不同整车工况下电堆的冷却性能。整车设计时主要通过3 个典型工况对电堆冷却性能进行考核,分别是中低速爬坡工况(40 km/h,7.2%坡度)、高速平坦路工况(120 km/h)和高速超速工况(140 km/h)。仿真得到3 种典型工况下电堆的冷却性能如表2所示。
表2 电堆冷却液温度仿真结果
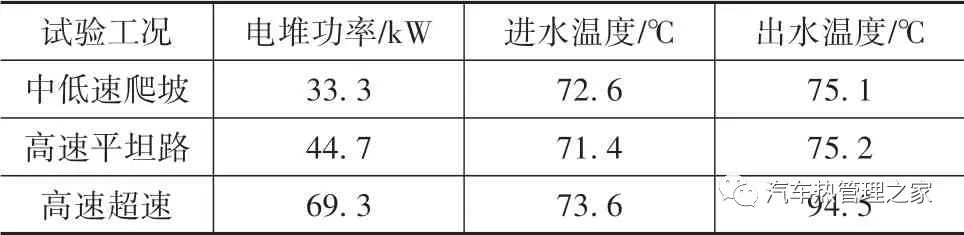
从仿真结果来看,中低速爬坡和高速平坦路工况,电堆出水温度均未超过限值78 ℃。在高速超速工况下,仅由电堆提供驱动功率时电堆的发热功率高达63.3 kW,此时电堆的出水温度高达94.5 ℃,发生严重的过温并且会导致降功率行驶。为避免电堆发生过温降功率行驶,需要增大散热系统的换热能力。在热管理架构及零部件选型已经确定的条件下,决定冷却系统散热能力的主要影响因素是前端模块的进风量和进风温度。图4 为不同风速对应的电堆出水温度仿真结果。分析图4 可知,在高速工况下,假设电堆输出功率恒定,提高风速可降低电堆的出水温度。但是当风速大于4 m/s之后,风速的提高对于降低电堆出水温度的影响逐渐降低。因此,整车热管理策略上,针对高车速工况,在保证电堆出水温度不超过78.0 ℃限值的前提下可以适当降低冷却风扇的转速,从而达到节能的目的。
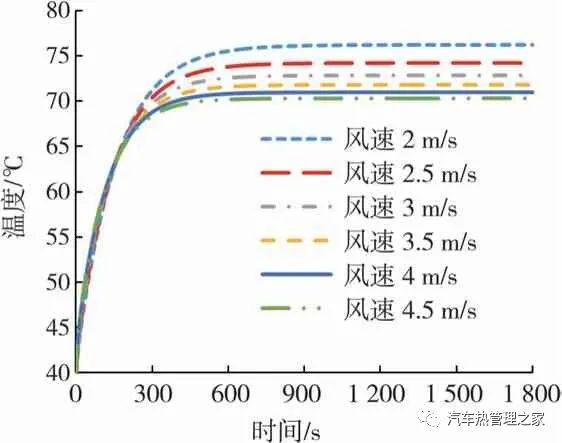
图4 不同进风速度对于电堆出水温度的影响
图5 为不同进风温度对应的电堆出水温度仿真结果。由图可知,进风温度对于水温的影响比较明显,通过降低进风温度的方式可以明显降低电堆的出水温度。影响前端模块进风温度的主要因素是冷凝器负荷,冷凝器负荷主要跟空调压缩机功率有关。为保证高速超速工况水温不超过目标值,可通过切换内循环的方式降低冷凝器负荷。或者从策略上主动对电堆进行降功率,从而降低系统发热量,电堆下降部分的功率可通过动力电池进行补偿。
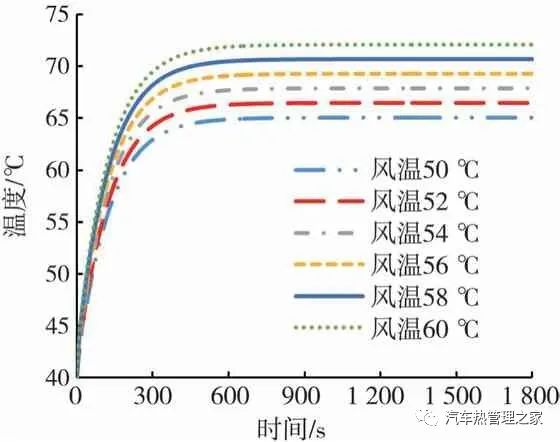
图5 不同进风温度对于电堆出水温度的影响
3 试验验证与结果分析
为了对整车热管理系统的性能进行验证,同时验证所建立的燃料电池热管理系统一维仿真模型的准确性,对整车进行高温环模试验验证,如图6 所示。试验工况为高温工况,重点考核燃料电池系统在高温大负荷工况下的冷却性能是否满足设计要求。试验工况选择车辆常用的典型工况,分别是中低速定速爬坡、高速平坦路匀速和高速超速工况。不同工况的试验边界条件如表3所示。
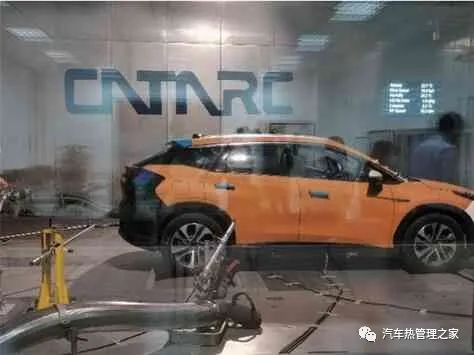
图6 整车高温环境舱试验
表3 整车试验工况及环境条件
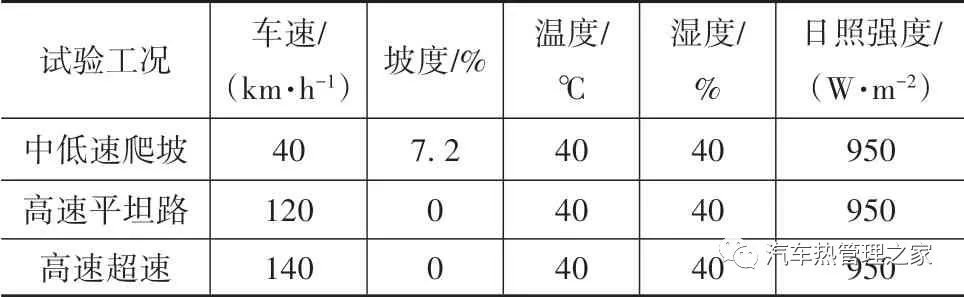
3.1 中低速爬坡工况
中低速爬坡工况主要考核车辆在低速大负荷工况下的热管理性能。该工况下车速较低,前端进气量较小,对于电堆的热管理提出较为严峻的挑战。图7 为中低速爬坡工况下试验结果与仿真结果对比。
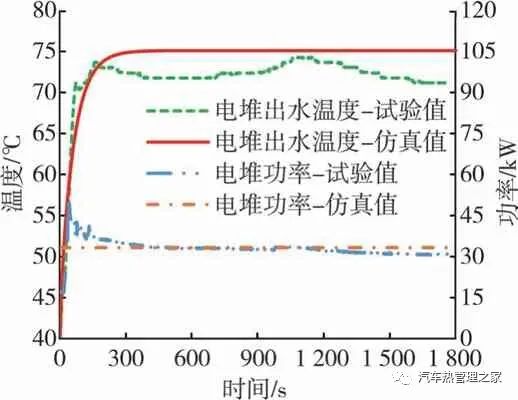
图7 中低速爬坡工况电堆功率及水温
试验刚开始时,水温迅速上升,300 s 后达到热平衡。热平衡时仿真计算的电堆出水温度为75.1 ℃,试验实测的电堆出水最高温度为74.3 ℃。由于试验过程中空调负荷会存在波动,对于前端进风温度的影响较大。试验时散热器前端进风温度比仿真值略小,并且一直处于波动状态,因此仿真值比试验值偏高,但是最大误差不超过3 ℃。
3.2 高速平坦路工况
高速平坦路工况主要模拟汽车日常高速行驶工况,是汽车使用频率较高的工况。图8 为该工况下试验结果与仿真结果对比。由于高速工况下电堆负荷较大,输出功率约45 kW,远大于中低速爬坡工况,因此在试验开始后约180 s后水温即上升到最大值75.2 ℃,试验实测的电堆出水最高温度为73.7 ℃。高速工况由于车速快,前端进风量比中低速工况要大,因此整车的冷却效果相对较好。
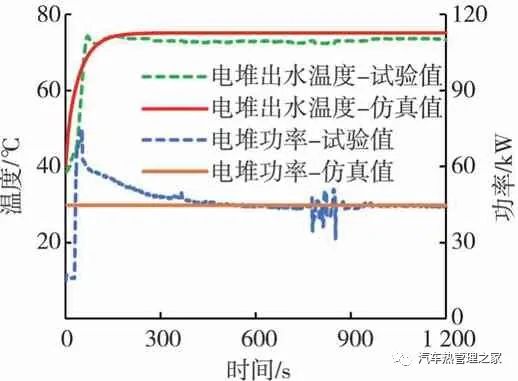
图8 高速平坦路工况电堆功率及水温
3.3 高速超速工况
高速超速工况主要考核在高速行驶时需要超车时的热管理性能。图9 为该工况下试验结果与仿真结果对比。仿真工况1 是仅由电堆输出功率得到的结果,此时未考虑动力电池的输出功率,因此电堆功率达到了69.3 kW,从而导致电堆出水温度超过90 ℃。仿真工况2是考虑电池补偿功率和电堆降功率策略后的仿真结果,此时得到的电堆的出水温度与试验的电堆出水温度基本接近。在高速超速工况下,整车是由电堆和电池同时提供动力,在试验的前120 s 内整车处于纯电模式,电堆输出功率为零,电堆出水温度与环境温度相同。随后电堆功率迅速上升,电堆水温也迅速上升,在700 s 附近时电堆出水温度超过了78 ℃限值。根据安全保护策略,水温超过限值之后电堆需要降功率。电堆降功率后,降低的部分功率由电池提供,才能维持车速不变。当电堆功率下降后,电堆水温也随之下降,在20 s内水温降低到78 ℃以下,此时电堆功率又恢复上升,如此反复循环波动。结果表明,高速超速工况下,如果电池的功率不足,有可能会导致电堆发生降功率从而引发整车动力不足。
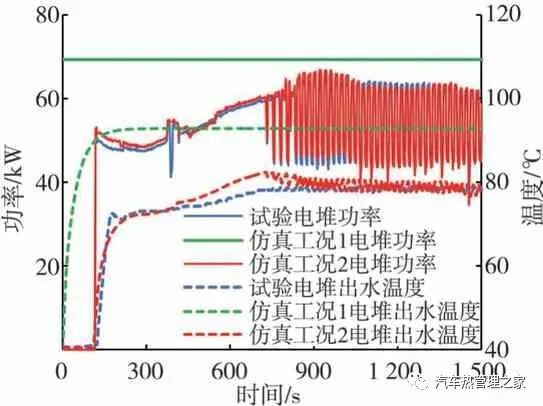
图9 高速超速工况电堆功率及水温
4 结论
采用理论与试验相结合的方法,根据电堆工作时的功率电压之间的关系,建立起电堆的产热模型,通过建立电堆的产热与散热平衡方程式可准确评估电堆在不同工况下的出水温度,为燃料电池热管理性能分析和优化提供了参考。
(1)建立电堆的产热和散热模型并通过台架试验验证了模型的有效性,比电化学热模型更加简单,更具有实际工程应用价值。
(2)建立整车的燃料电池热管理系统一维仿真模型,研究风速、风温等因素对电堆出水温度的影响,较准确地预估了在3 种整车工况下电堆的出水温度,为热管理系统的性能评价和设计优化提供了有益的参考。
(3)整车试验结果表明,所建立的热管理系统模型可有效计算不同工况下电堆的出水温度。识别出高速超速工况电堆发生降功率的风险,为整车热管理优化设计指明了方向。
作者:郑文杰,杨 径,朱林培,熊 飞
广州汽车集团股份有限公司汽车工程研究院
编辑推荐
最新资讯
-
全国汽车标准化技术委员会汽车节能分技术委
2025-04-18 17:34
-
我国联合牵头由DC/DC变换器供电的低压电气
2025-04-18 17:33
-
中国汽研牵头的首个ITU-T国际标准正式立项
2025-04-18 17:32
-
为什么要进行汽车以太网接收测试?汽车以太
2025-04-18 17:26
-
产品手册下载 | NI 全新USB数据采集-NI mio
2025-04-18 16:39