汽车底盘的开发流程
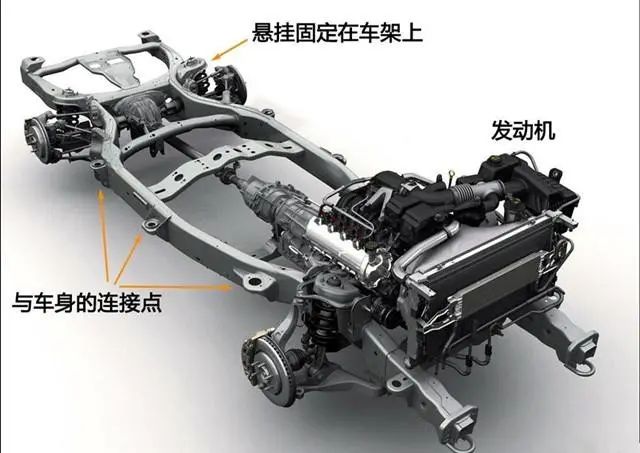
底盘设计开发需要测试的项目有哪些?如何建立性能指标?如何测试并用测试结果来改进设计?底盘工程是如何在有限的时间内一步步把产品开发出来完的?这些将在本文中进行详细介绍。
对底盘开发的认识
汽车要有好的品质就要把设计和生产工艺都做到位,成功的汽车企业需要具备高水准的技术、优质的组织管理以及良好的经营。虽然汽车底盘开发是技术能力问题,但需要强调成功的底盘开发更取决于组织管理和有效的团队合作。底盘技术的开发和汽车其他系统的开发都是本着反复测试再反复改进的原则。底盘开发的挑战在于有无正确、完整的开发计划、技术成熟的工作团队和严格的系统化作业。
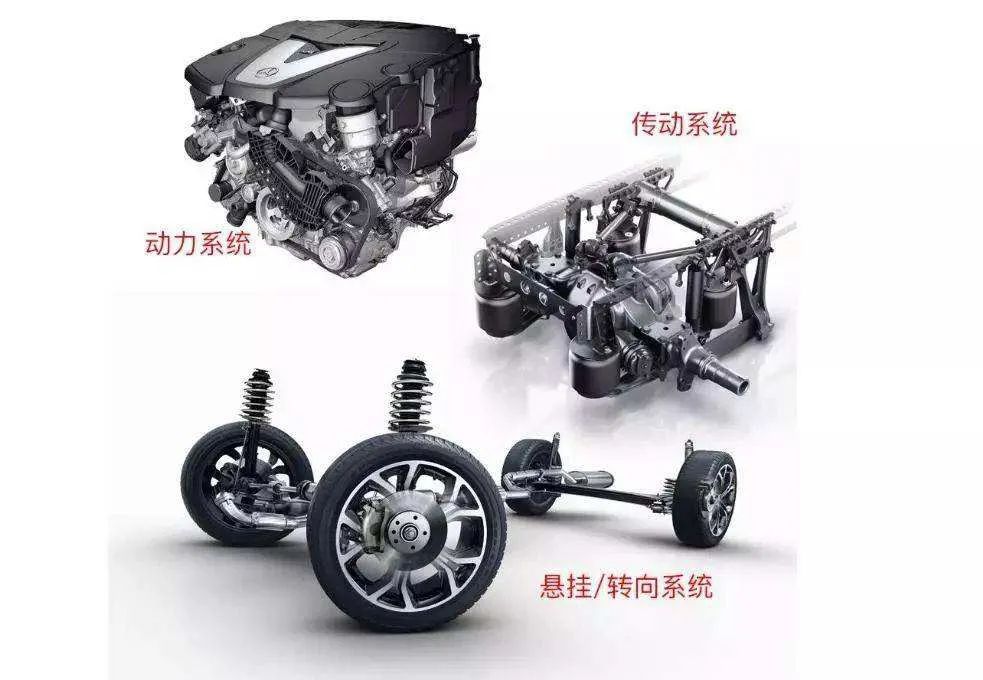
看看目前企业所用的底盘开发流程,无论商用车还是乘用车,都是在确定了平台、车型以及成立了项目组后,展开项目工作的早期就要依照清单测试参考的竞争车所有和底盘有关的性能,测试内容包括整车的主观评价、客观评价和拆解分析。在资源许可的情况下还要做K&C台架测试,它是客观评价的一种,针对车辆前后悬架的Kinematics(运动学)及Compliance(受力变形性能)作各项测量。主观评价和客观评价都要做,才能确保所开发的车型具有优良的性能。主观评价不需要测试仪器和实验场,可以作多次的评价来帮助改进,在设备和资源缺乏时这是很好的途径。根据这些测试数据,掌握目标车的性能指标。目前底盘开发技术非常依赖CAE(计算机辅助工程)来定方向。底盘设计所用的CAE包括车辆动力学和机械运动学模拟、工程设计3维数模和有限元结构分析模拟。我们用来开发目标车底盘的工具是这套目标车的数模,所有和竞争车有关的工作可以看作是“搭桥工作”。建立成功的目标车的整车模拟和K&C模拟,就掌握了待开发车的底盘设计,也就不难完成样车制造。无可否认,经过对样车作主观、客观评价及K&C台架测试,我们对目标车的设计成功就更具信心。然而,样车的底盘部件并不是为量产设计的,二者的差别主要是部件耐久性和生产工艺的质量没有在样车上体现验证,所以在这个阶段的重要工作是设计开发量产的部件,它所涉及的工作有有限元结构分析、量产部件台架实验和对整车在试车场作耐久性测试等。耐久性测试需要很长时间,为了争取时间我们总希望提早开始量产部件的开发,这是个很大的挑战。试制的量产车组装完成时有一项关键的工作,就是底盘调校,调校的结果会对底盘某些零部件的设计有小幅度的更改。
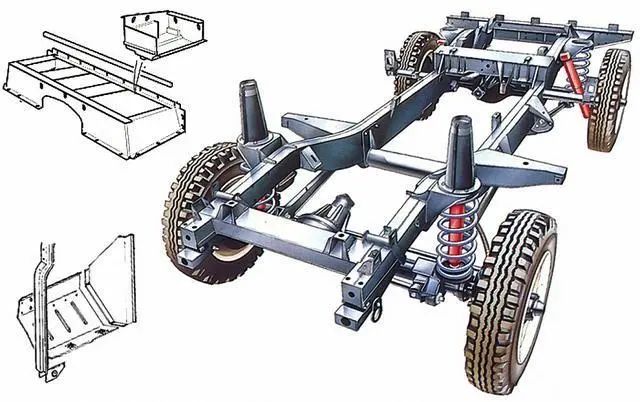
汽车性能的鉴定方法
前面提过与底盘设计最有关的是操稳性和平顺性,简单来说就是“要容易控制,平稳但反应够快,不会颠簸或发生噪声振动,开起来轻松舒服”。为了保证顾客满意,底盘工程师要不断试车和改进。主观评价和客观评价试车的项目很多,以乘用车为例,仅针对操稳性平顺性(不包括NVH)的主观和客观测试就超过30种。主观评价要请多位有经验的人驾驶车辆作性能对比打分。客观评价要用仪器测量各种关键的性能参数并确认是否在指标要求范围内。一般来说,竞争车的测试在项目的初期完成,而目标车的测试要在样车制造后才能进行,这之间有1年半以上的时差。在这段时间内,目标车底盘设计完全在CAE上运作。
操稳性能测试。一个重要的客观测试称为“等半径稳态稳度测试”,车辆作等半径等速圆周运动,在不同车速下量取转向盘的转角和车的侧向加速度,由汇集的测试资料提取一个称为“不足转向梯度”的参数值,通常希望这个参数值为2°~6°/g。在这个实验中,还可以同时量取到另外几个重要的整车性能参数:一个是侧倾增益,它由车的侧倾角与侧向加速度的关系提取,通常该值为4°~8°/g ;另一个重要参数是转向敏感度,这是针对侧向加速度和对应的转向盘所打角度来作评价,通常希望这个值在车速为100 km/h的状况下是0.8~1.4g/100°-SWA。另一个重要的整车性能测试称为阶跃输入瞬时响应,实验时在计划车速下把转向盘以预定的角转速转到目标转角,整个过程车的侧向加速度、横摆角速度等重要性能参数随时间变化的曲线是分析的要点。客观评价的性能参数比较抽象,但它的优点是可以计算或测量具体的数值以帮助工程设计。
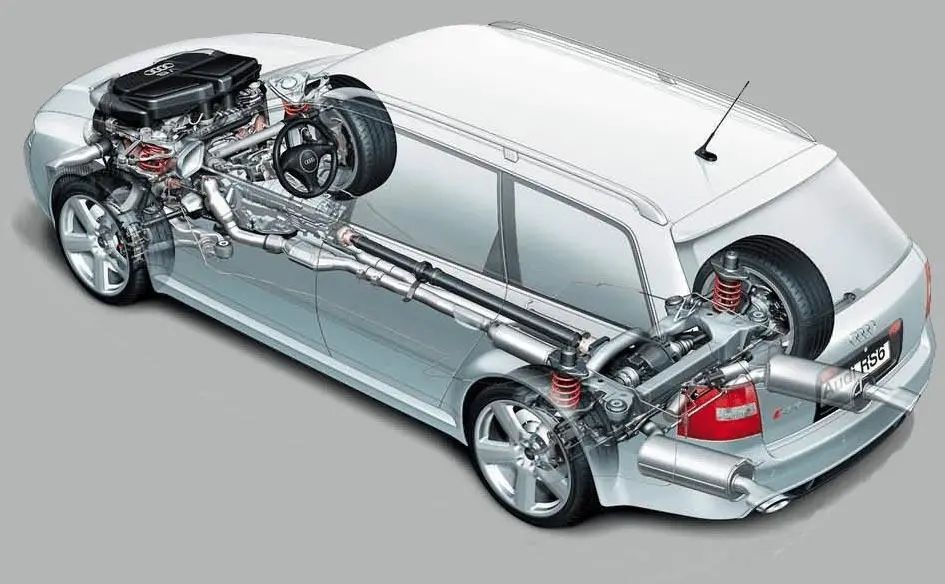
乘坐舒适性能测试。在客观评价中要测量前后悬架的偏频,对于乘用车这个值在前悬应该在l Hz左右,在后悬应当比前悬高20%左右,高出这个指标就表示弹簧太硬,会影响乘坐舒适性。对于越野车和卡车,为了适应起伏路面,弹簧的刚度会高些。典型的舒适性客观评价车要以低、中、高3种车速通过特别选定的试车路线,在驾驶员座椅、乘客座椅、转向盘、地板等处测量前后、侧向及垂直3个方向的线性加速度在时域内的变化,试车要在光滑路面和粗糙路面2种路线各作1次。有了这些数据就可把目标车和竞争车每种状况的加速度均方根值取来作对比,来了解目标车在乘坐舒适性方面的表现。与这个性能调校相关的部件有弹簧刚度、减振器阻尼、前后稳定杆扭转刚度和各处的衬套刚度。
制动性能测试。由于制动器属于行车安全相关的部件,因此,对它的性能测试需依照法规要求,如欧洲的ECE、美国的FMVSS和中国的GB。车辆制动性能的保障首先要求制动器本身功能要达标,比如根据车的质量分布以及用0.5~0.6g加速度可以来鉴定车的前后制动器能力总和是否配置得当。此外,需要对制动器的摩擦片性能进行冷测试、衰减测试和磨损测试。整车测试则包括直线行驶测试、制动距离测试和跑偏测试等。对于ABS的性能鉴定,则需要在一个左右两侧地面摩擦因数不同路面进行测试。此外,商用车的制动测试还包括下长坡制动性能测试。
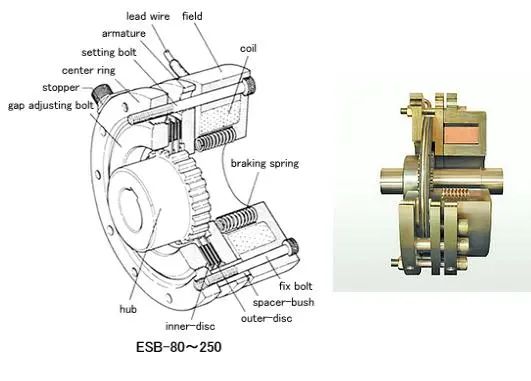
悬架K&C性能测试。K&C性能测试是底盘设计开发过程中的重要一环。需要量取前悬及后悬各30~50个实验及参数曲线,将竞争车与目标车的这些参数曲线一一对比就可以非常精确地明白目标车需要努力改进之处。K&C测试不但可以在试验室进行,也可在计算机上模拟,一方面替竞争车作K&C测试,一方面替还没制造好的目标车作K&C测试然后作对比。Kinematics测试是把左右车轮相对于车身逐渐举起(弹簧压缩)再放下(弹簧伸长),量取此过程中左右轮前束角、外倾角、主销后倾角、主销内倾角、轮距、侧倾中心高度等各参数的变化曲线。Compliance测试是把一定的某特定的位置及方向的力渐渐加在左右车轮上,量取该过程中左右轮前束角、外倾角和主销后倾角等各参数的变化曲线。乍看这些K&C试验与整车性能好像没什么关联,然而如果前后悬K&C的各种性能都和竞争车的性能相符合时,那么目标车的各项与底盘相关的整车性能也都和竞争车的整车性能相接近。
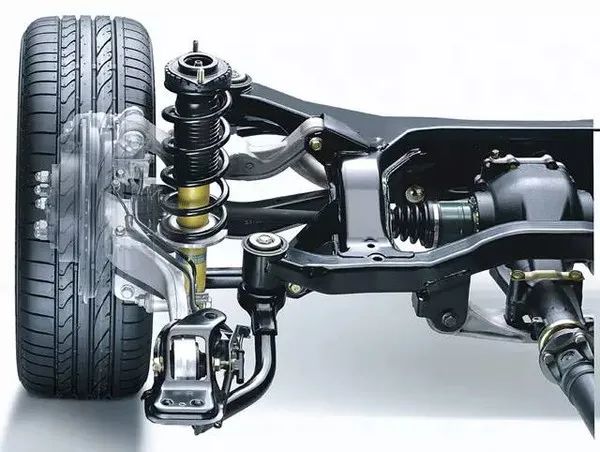
CAE模拟在底盘开发中的重要性
作测试评价的目的是帮助改进设计,但是如果用实车整车性能测试来达到优化设计还有一定困难。首先,在目标车样车没有制造出来前,没有办法作目标车的实车测试评价;第二,经过实车整车测试鉴定问题再进行设计改进的循环作业既慢成本又高,而且不够精确。
如今,国内外的底盘开发工程都开始用计算机模拟(CAE),作大部分的客观评价测试。CAE和实车测试有相辅相成的功效,在汽车产品开发中对于它们在不同时间节点的工作配合有严格的要求。
CAE模是如何建立的?建立CAD的外形模和分析数模需要的参考数据都由实验组提供。这些包括前后悬的活动部件接头点的空间3维坐标、车的质量及其分布、轮距、轴距、弹簧刚度、减振器的力与速度的关系、稳定杆的扭转刚度、轮胎性能和衬套性能。当一切都具备时,即可在电脑上作K&C和整车性能仿真分析。这些电脑性能测试的结果要与先前针对竞争车在试验台上量取的K&C以及实车客观评价的数据对比,以了解CAE工作是否已经完善。另一方面,CAE工程师要配合底盘设计工程部开始针对目标车进行设计及用CAD/CAE建立K&C和整车性能模拟来开发目标车。
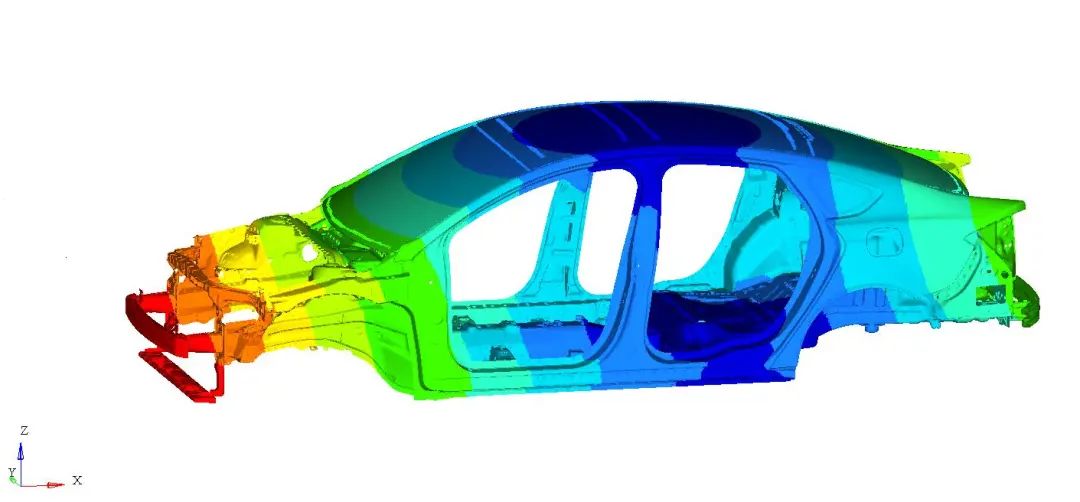
汽车底盘开发流程
建立底盘设计指标相关的工作。指标的参数包括K&C的及整车性能,通常有40~50个之多,这是提取竞争车数据后再斟酌调整决定的。除此之外,往往还需要扫描、拆解竞争车,并作车身刚度及模态测量以增加了解。
建立底盘设计CAD/CAE相关的工作。替竞争车作CAE模拟,完成后容易转换作目标车的CAE模拟。把目标车K&C及整车性能模拟结果与一定的指标相对比,可以了解目标车改进的方向.
样车制造和测试。虽然是样车,但部件尺寸和性能要求要严格,针对底盘性能的样车至少有2辆。一旦有了样车就可针对样车作目标车的实车K&C和整车性能测试,如果前期工作到位,则这个样车测试的作用只在于验证。
底盘部件的强度和耐久性。样车测试不包括耐久性,量产的部件强度和疲劳寿命的设计开发需经过零部件有限元结构分析、零部件台架测试、悬架台架测试和试车场耐久性强化测试。
底盘调校。调校工作是因为底盘的组件多,生产品组装与设计部件累积公差造成误差,所以必须进行调校。需要调校的部件包括前后稳定杆的直径大小、前后螺簧刚度、减振器阻尼及各处衬套的刚度等。调校工作由专家负责,根据主观评价试车并更换上述零件,以对比选择最优的部件。目前很多企业的底盘调校并不是系统作业,笔者认为这方面有待加强。
编辑推荐
最新资讯
-
漫说信息智能 · 电动车防晕车大作战
2025-04-27 16:28
-
R171.01对DCAS的要求⑨
2025-04-27 15:29
-
智驾标准法规体系大全
2025-04-27 15:28
-
国内最大汽车创作者大会开幕,懂车帝投入5
2025-04-27 13:18
-
大卓智能端到端直播实测,16公里复杂路段挑
2025-04-25 17:16