同轴电桥传动技术解析
1同轴电桥概述
同轴电桥,因其结构紧凑、轻量化、高功率密度、高扭矩密度等诸多优点而被主机厂青睐。同轴电桥的传动结构一般需要行星排加持,原因可能是由于行星排的各要素是同轴传动的,并且根据目前单级减速器的速比匹配,一般要达到9~13,要在有限的空间内既要同轴又要实现如此高的减速比,行星齿轮机构就成为较好的选择方案。
我国变速箱行业起步较晚,尤其是AT变速箱,更是比国外落后了不止一代。由此AT中核心传动部件——行星排的设计、加工、质量把控等全流程,国内的产业都不是多成熟——没有获得充分的成长空间。同轴电桥的开发也呈现这种状况,目前见诸于市并被各公众号自媒体报道的大多都是国外的产品。
2同轴电桥传动技术分析
2.1雪佛兰BOLT EV
说起同轴电桥,通用雪佛兰的Spark EV和Bolt EV当首先被提及,通用早在2012年就推出了Spark EV,并于2016年推出了Bolt EV
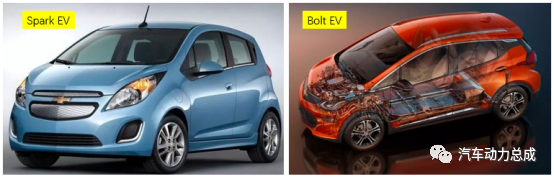
图1 A00级Spark EV以及A0级Bolt EV
两车的技术参数见下表
表1 Spark EV和Bolt EV性能参数
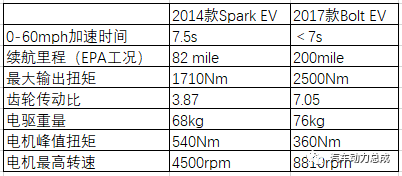
表1中的参数现在看来并不亮眼,但是要知道那可是2012年,10年前通用雪佛兰就已经成功推出类似于今天五菱Mini纯电动的车型,多么的超前!
Bolt EV的电桥采用同轴设计,动力经两级减速后传递至差壳,并经半轴输出驱动车轮。
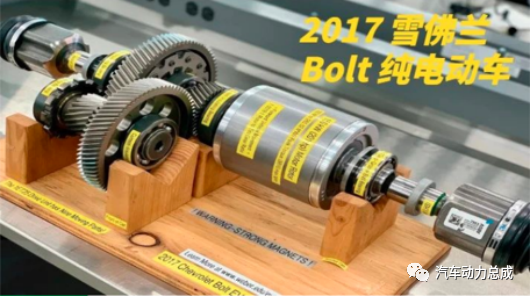
图2 雪佛兰Bolt驱动系统
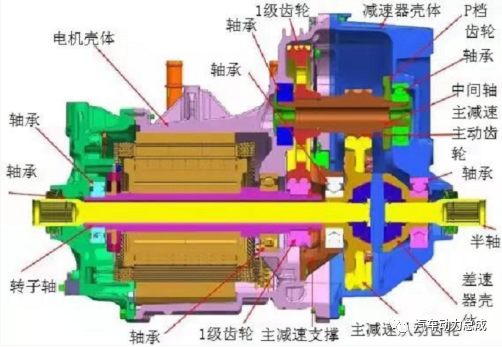
图3 Bolt EV电桥剖面图
图3中两级减速的齿轮轴上使用的都是深沟球轴承,未使用锥轴承,可能出于提高效率的考虑,但是由此带来的问题是当高速运转时轴承要承受较大的轴向力;此外由于半轴要从电机轴中穿过,第一级输入齿轮不得不做的很大,这样就不容易匹配出总速比为12(单级减速器常规速比要求)左右的减速齿轮,表1中Blot EV减速比做到7.05,勉强可以,而Spark EV减速比却只有3.87,尽管电机的峰值扭矩不小,但是输出扭矩却大打折扣。Bolt EV为了提高减速比将两个被动齿轮做的特别大,导致的结果是占用的空间并不比非同轴的减速器小多少。
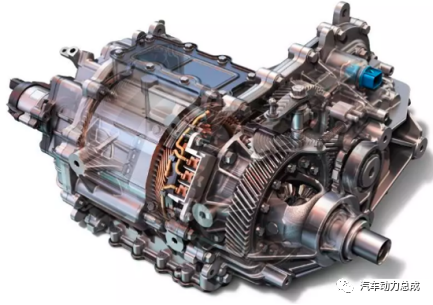
图4 Bolt EV电桥
在今天看来,Bolt EV的性能参数早已掉出第一梯队,但是作为当今一众电驱动桥的“前辈”,它理当被我们所记忆。
2.2加特克
日本加特克在2019年上海车展上提出了他们应对汽车电气化的解决方案,并推出了一款同轴电桥。电机的最大扭矩为155Nm,峰值功率100kW,最高转速达到20000rpm,应该说在2019年的时候,20000rpm已经很高。
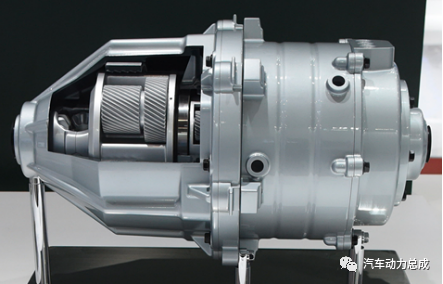
图5 加特克同轴电桥
减速器基于行星齿轮机构打造,由上图可见,行星排为NW型。该款电桥的减速比达到了16.5,图片中未显示全部轮系,但是根据其高达16.5的速比,合理推断该款加特克的同轴电桥为两级行星排减速+差速器,且第二级行星排和差速器共用行星架,可能的结构简图如图7所示
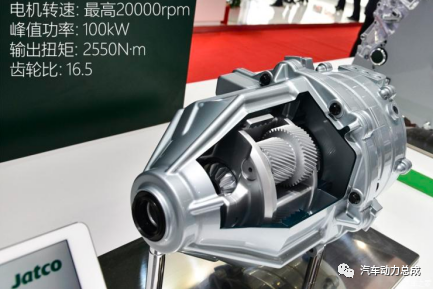
图6 加特克同轴电桥性能参数
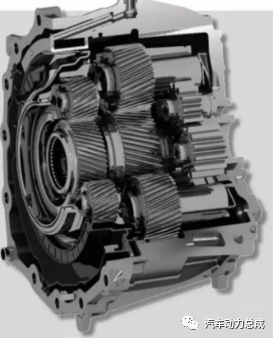
图7 结构简图
杠杆图如下
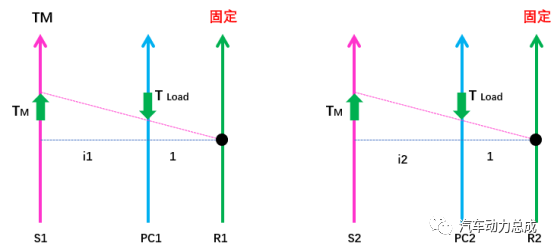
图8 两级减速行星排模拟杠杆图
根据杠杆图,加特克的同轴电桥速比为:
i=(1+i1)*(1+i2)
上式表明,16.5的速比由i1和i2共同分配,如果由单一行星排来获得16.5的减速比还是很困难的,两级的话就比较合理。
2.3
GKN同轴电桥
GKN同轴电桥的发展很好地诠释了产品的迭代过程,从中也能窥见一个零部件企业对产品不断追求不断打磨的精益求精的精神。GKN同轴电桥经过了三代的发展,第一代于2016年公布,搭载于沃尔沃 XC90 T8 插电混动车型的后轴上,助力沃尔沃实现了P4混动。
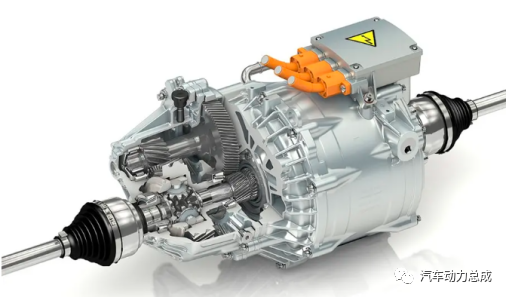
图9 GKN同轴电桥——Volvo XC90
该箱减速器的设计理念同Bolt EV类似,单级减速器,速比达到10,没有复杂的换档装置。电机动力经过一个偏置布置的二级减速器后回到和电机同轴布置的差速器上。通过这种减速齿轮偏置的结构,实现左右输出半轴和电机输入轴同轴,从而降低了电桥对安装空间的需求。
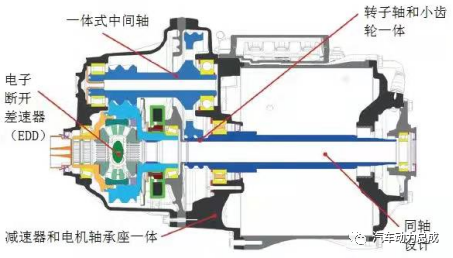
图10 第一代电桥剖面图
图9、图10所示为GKN第一代电桥,配备的电机最高转速只有13000rpm,这个转速在2016年份基本上已经是极限了,尽管和现在动辄20000rpm的转速没法比。较低的电机转速带来的弊端是车速不高,电机允许的最高车速只有170kph,而沃尔沃 XC90 T8 最高车速是230kph,所以当车速超过一定限制时电桥必须断开,这就是为什么图10中吉凯恩配备EDD(Electronic Disconnect Differential)的原因。
GKN第二代电桥在第一代基础上,去掉了差速器和EDD,取而代之的是两个多片湿式离合器。
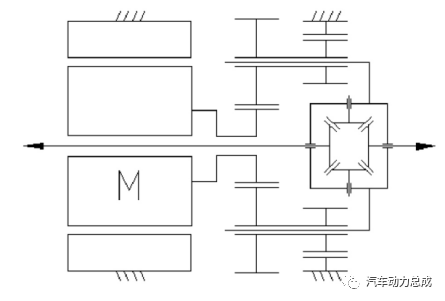
图11 第二代电桥——eTwinster
其三:
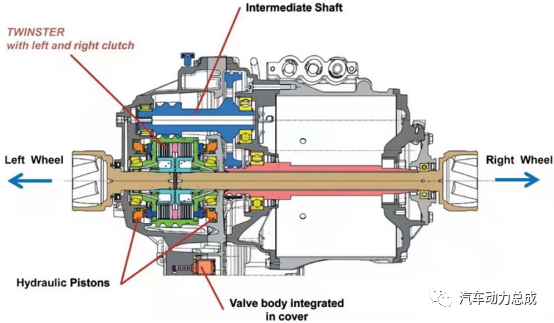
图12 eTwinster剖视图
两个多片湿式离合器,实现了扭矩矢量分配,它们属于轮间差速器的范畴,根据活塞对摩擦片对偶片的压紧程度来控制不同扭矩的分配,同时当车速达到电机转速上限时打开离合器,电机与车轮分开,实现第一代产品EDD的功能。
第二代产品应该说已经很完美——同轴驱动、四驱、扭矩矢量分配等等标签,但是单挡减速器始终对电机的性能要求比较高,为了解决该问题,第三代产品应运而生。
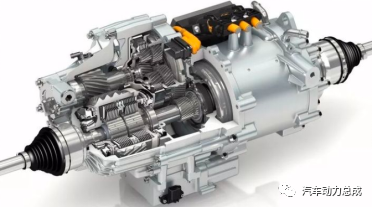
图13 GKN第三代电桥——eTwinsterX
根据GKN的解释,“X”代表二挡箱。其剖视图如下
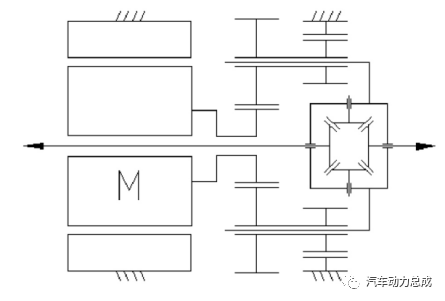
图14 eTwinsterX剖视图
eTwinsterX的行星排采用的是WW构型,虽然吉凯恩的两档实现方式结构新颖、紧凑,但是该结构的缺点也是明显的,其中主要的问题是复杂,加工装配困难。具体分析见《基于行星齿轮机构的两挡电桥传动方案分析》。
2.4
单级行星排减速+差速器方案
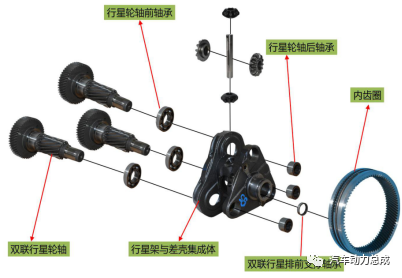
图15 舍弗勒单级行星排减速+轻量化差速器方案
一级减速和差速器组合的方案,就同轴电桥而言,总结目前市场上已有的产品至少有四家在做。该类产品的关键是如何通过一级减速即达到10以上的速比,只有减速比达到这样的量级,才能更好地发挥电机的性能。仅通过一级减速达到目标速比,这样才能达到减少零部件,增大扭矩密度、功率密度的目的。
图15所示为舍弗勒AKA320同轴电桥,这是一个非常巧妙而且大胆的设计,采用NW行星排实现9左右的减速比,勉强能够满足要求,采用无齿圈的拉维纳行星排实现差速器的功能,两行星排共用行星架,具体参见《舍弗勒同轴电桥传动原理分析》。
一级减速和传统开式差速器组合的方案有美桥、麦格纳、一汽红旗等。美桥的产品搭载于捷豹路虎I-pace ,麦格纳的产品是否搭车暂时未知,一汽红旗样件已经试制成功,见图16、17、18
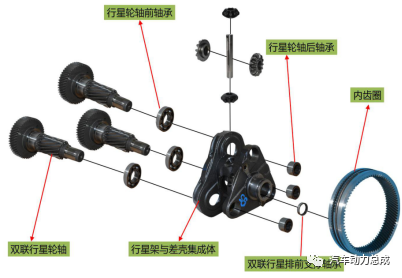
图16 美桥减速器行星排
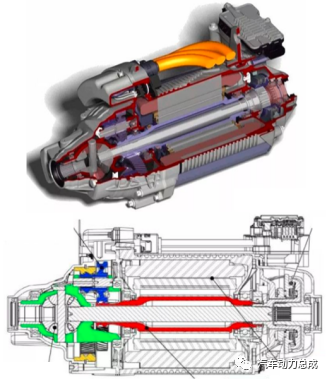
图17 麦格纳同轴电桥
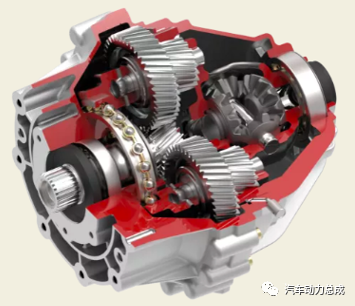
图18 一汽红旗减速器剖面图
上述三家产品方案一样,结构简图如下
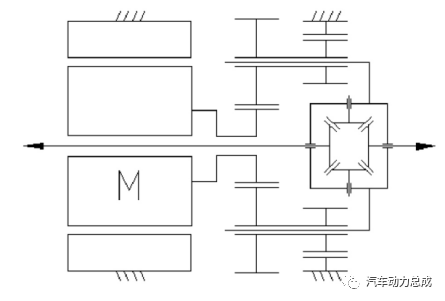
图19 单级减速行星排和开式差速器组合结构简图
舍弗勒、美桥、麦格纳、红旗等电桥减速器,无一例外地使用了NW行星排作为减速机构,原因是要达到10以上的减速比,而且是单级减速,只有NW行星排可以达到且具有工程使用的意义。其他行星排,如NGW,虽然简单可靠,但是一级速比达不到10以上,NN行星排虽然速比能达到,但是不适合乘用车减速器使用,因而各企业不约而同地使用了NW行星排构型,关于NW行星排的详细分析参考《舍弗勒同轴电桥传动原理分析》。
2.5保时捷Taycan前桥减速器
Taycan前桥减速器重量约16kg,由两个简单行星排组合在一起作为减速机构,速比为8.05。差速器同样为行星排结构,和奥迪e-tron一样是一个无齿圈的拉维纳行星排,第二级和第三级行星排共用行星架,见图20
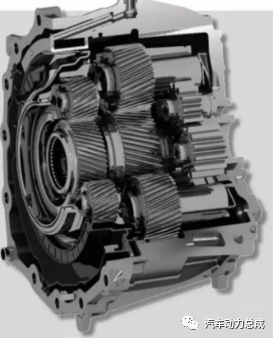
图20 Taycan前桥减速器
结构简图见图21
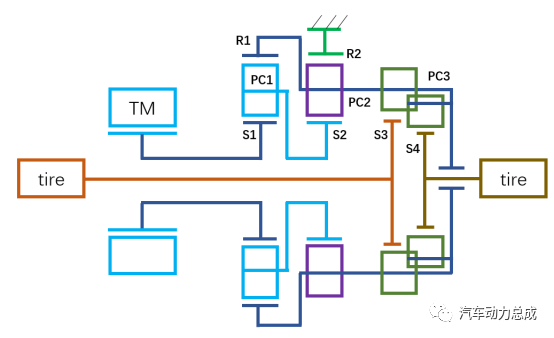
图21 前桥减速器结构简图
为便于计算速比,除第三级差速器行星排外,其余两级合并后的模拟杠杆图如图22所示,差速器的模拟杠杆图如图23
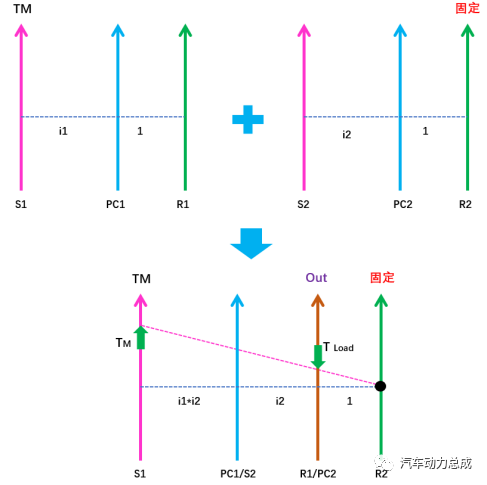
图22 前桥减速器行星排模拟杠杆图
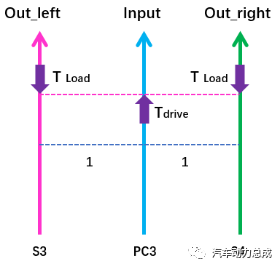
图23 差速器模拟杠杆图
根据图22,其减速比为

前桥减速比是8.05,根据上述计算公式以及NGW行星排的特点,其实保时捷开发团队完全可以将该速比设计的更大一些,两级NGW也还有速比增大的空间。对于单级减速的同轴电桥来说,8.05的速比显然是不能够充分发挥电机的性能的。为什么没有将速比调成更大呢?原因在于保时捷Taycan还有后桥电驱,而后桥电驱的一挡速比高达16,足以支撑Taycan的弹射起步。关于Taycan后桥减速器的详细分析参考《Taycan&e-tron电驱传动技术分析》。
2.6FEV
FEV在2019年公布了一款结构紧凑的同轴电桥,电机、电控、减速器高度集成,典型的三合一产品。采用同轴的构型,FEV官宣的说法是为了较低的总高度以及更好的NVH。
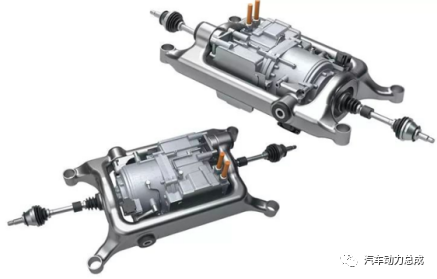
图24 FEV同轴电桥
该箱最大轴端扭矩为3500 Nm,0至100km/h 加速时间<6 s,最高车速200kph,电机峰值功率 230kW,持续功率100kW,在坡度3%时巡航速度可达180公里/小时,具备驻车锁和空档功能。
FEV同轴电桥核心部件为一套WW行星排,行星架PC连接TM电机作为输入轴,S1被一个多模离合器B1连接到壳体上,实现锁止或释放,锁止时S1为整个行星排提供支点,释放时为空挡,S2连接到差速器壳体,为动力输出,行星排外形见下图。
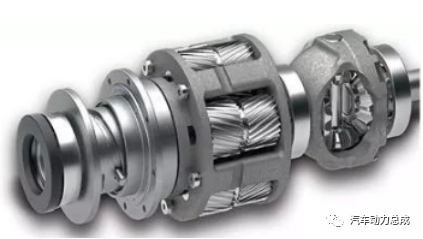
图25 WW行星排
图26为其剖面图,显示了内部结构
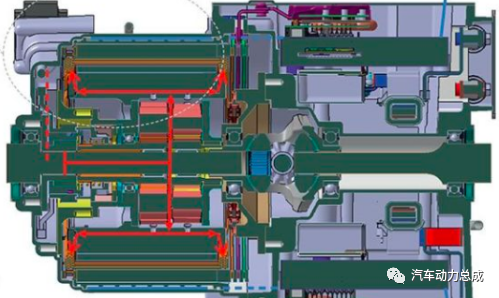
图26 FEV同轴电桥剖视图
根据图26绘制杠杆图如下
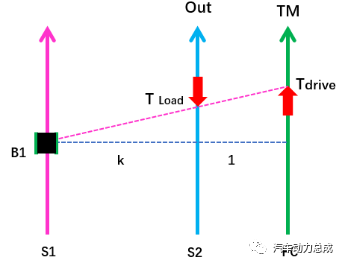
图27 模拟杠杆图
其中k为行星排特性参数,k=(ZP1/ZS1)*(ZS2/ZP2)-1,由图27显见,驱动系统减速比为(k+1)/k,这个减速比还是比较小的,不利于电机性能的发挥。基于较小的速比,笔者猜测其作为P4电桥使用,和其他动力源(电机或发动机)共同驱动车辆。
3发展趋势展望
目前随着我国碳中和、碳达峰的时间表和路线图的确定,国家顶层设计层面明确了燃油车禁售政策,出台了双积分管理办法。相对传统燃油车,新能源车型在排放上具有绝对的优势,从而使得其呈现井喷式的发展,也带动了包括同轴电桥在内的电驱动桥的需求增长。
总体上同轴电桥的发展趋势为高效率、高转速、高功率密度、高扭矩密度、高NVH性能,轻量化、低成本,集成化。具体到传动系统,也就是电桥减速器,其发展趋势个人认为应该包括如下几个方面:
1)高效率、高功率密度
a、电机高速化后,需对油封和轴承进行专门的开发,一方面新开发的油封和轴承要适应高转速的电机轴,另一方面要采用低摩擦的设计,从而减小因摩擦引起的功率损失;
b、对齿轮和轴承的润滑进行定点强制喷淋,目的是降低油液面,从而减少齿轮的搅油损失;
c、减速器采用两挡或多挡(一般电驱桥两挡减速器已经足够),拓宽电机的高效率运行区间,或者采用多电机(一般也是两个电机),其作用和两挡减速器一样也是为了优化电机的效率。高速和低速时分别用不同的电机驱动,从而使得电机始终工作在高效区间。
2)轻量化、小体积、低成本、高扭矩密度
对箱体、齿轴采用新材料、新工艺,通过CAE模拟仿真优化设计,减小体积、减少使用材料,从而降低壳体齿轴的重量,降低成本,提高扭矩密度;采用新的设计方案,比如舍弗勒的轻量化差速器、奥迪e-tron后驱的电子差速器、吉凯恩eTwinsterX扭矩矢量控制差速器;
3)高NVH性能
a、电机转速提高,齿轮啮合频率自燃也随之提高,在保证速比前提下,需要对齿数、齿轴结构进行优化,以便提高传动系统刚度,避开与电驱总成的固有频率耦合,避免产生共振;
b、优化齿轮宏观参数,采用多齿、小模数、细高齿设计,增大重合度,增强传动的平稳性,此外微观修形上要尽可能做到全工况覆盖,减小TE,降低啮合激励引起的齿轮啸叫;
c、提高齿轮配合精度,除预留必要的润滑和中和热变形的空间外,尽量减小传动系统的配合间隙,以消除rattle;
编辑推荐
最新资讯
-
奇石乐推出用于DAQ数据采集系统的KiStudio
2025-04-28 17:51
-
全球首次!IVISTA 2023版修订版引入带灯光
2025-04-28 09:59
-
我国首批5G毫米波行业标准送审稿审查通过
2025-04-28 08:56
-
5/16 厦门- 新能源汽车电驱测试技术的创新
2025-04-28 08:53
-
国内首个汽车电磁防护技术验证体系EMTA正式
2025-04-28 08:49