燃料电池电动汽车车载氢系统安全——氢系统结构安全仿真分析
由于燃料电池车载储氢系统安装在车辆上,车辆运行过程中会受到振动和冲击。为确保车载储氢系统的安全运行,模拟车辆的实际运行状况,可对其结构及安全性能进行仿真分析与设计。仿真分析主要包括静强度分析、模态分析、随机振动分析、疲劳分析和振动冲击分析。
氢系统结构及安全性能仿真分析分析过程可分为以下几步:首先建立结构的有限元模型;接着进行结构的模态分析,确定其固有频率、振型以及敏感频率;再计算结构的频率响应;然后根据功能性随机振动试验的加速度功率谱密度曲线开展垂向、横向和纵向的功能性随机振动试验仿真;之后根据长使用寿命试验的加速度功率谱密度曲线开展垂向、横向和纵向的长使用寿命试验疲劳仿真;最后开展垂向、横向和纵向的显式动力学冲击试验仿真。
一、CAE 分析前处理
在进行CAE 分析前,为得到满足需求的几何模型,需要对车载氢系统的三维模型进行前处理,达到满足需求的几何模型,然后建立有限元模型。建立有限元模型主要包括:模型简化、网格划分、材料属性定义和约束条件施加等。
1、模型简化
一般,完整的三维模型须经过适当的简化修改。可忽略安装辅助构件的小孔、小凸台、小倒角等小特征;忽略支架等的螺纹孔等对结构力学性能影响较小的特征;去掉一些对分析结果影响不大但结构复杂的小零件等。对于长度远远大于零件厚度的零件,有限元中壳单元能很好地模拟其力学特性,并且拥有高效的计算效率,因此储氢模块的有限元模型主要是由壳单元模拟。在实体结构中,大多数零件的连接方式为螺栓连接,分析可采用1d-bar 单元来模拟其预紧、拉压等力学特性。气瓶固定卡带与气瓶之间的橡胶垫使用实体单元来模拟。另外,若需减少计算量,对对称模型可以仅留对称部分的几何模型,在边界条件设定为对称即可,这样网格数量变少,计算时间缩短图3-4 为某燃料电池电动汽车中的储氢系统结构和有限元模型。
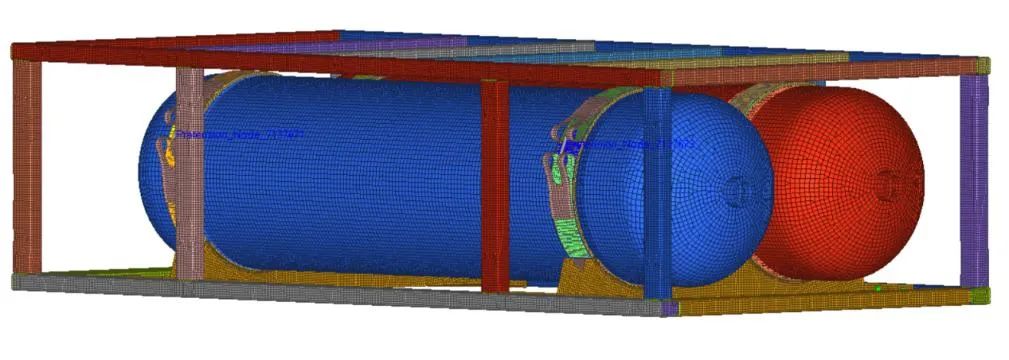
图3-4 某储氢系统结构和有限元模型
2、网格划分
对于车载储氢系统,一般划分为壳单元。无法划分为壳单元网格的三维几何结构一般选用四面体和六面体结构,最好的情况是划分成六面体网格,因为其数量少,求解快。但有时模型复杂,无法离散成六面体网格,可采用四面体网格。
3、设置材料属性
在对结构材料设置材料属性,进行模态和后续分析时需要对其中密度、弹性模量、泊松比、应力应变曲线进行设置,一些常见材料的参数见表3-2。材料设置过程中应考虑各物理量单位设置的一致性。
例如,在结构分析中,采用毫米(mm)、秒(s)、吨(t)作为三个基本单位,其余单位由此导出,加速度单位采用mm/s2,加速度功率谱密度单位采用mm2/s3。
表3-2 材料属性

4、施加约束条件
约束方面,根据台架的实际安装情况,在系统结构的随机振动分析中,对工装孔上的所有节点施加全约束或者加载给定的加速度载荷。
二、CAE 分析
1、静强度分析
结构静力分析是结构设计与强度校核的基础,主要是计算在固定不变的载荷作用下(包含由定常加速度引起的平衡惯性载荷)结构的响应(位移、应力、应变和力),不考虑阻尼的影响;静强度分析主要是确保结构不会产生永久变形或断裂,即对应结构应力不超过材料屈服应力或超过抗拉应力,应变不超过材料的断裂延伸率。仿真分析时参考特定标准中结构要求的载荷工况评估储氢模块结构强度。
对于车载氢系统支架、支座、储氢瓶绑带,应该评估支架结构的最大应力值,最大应力小于材料的屈服极限,不会产生永久变形,满足强度标准要求。
表3.3 加载工况
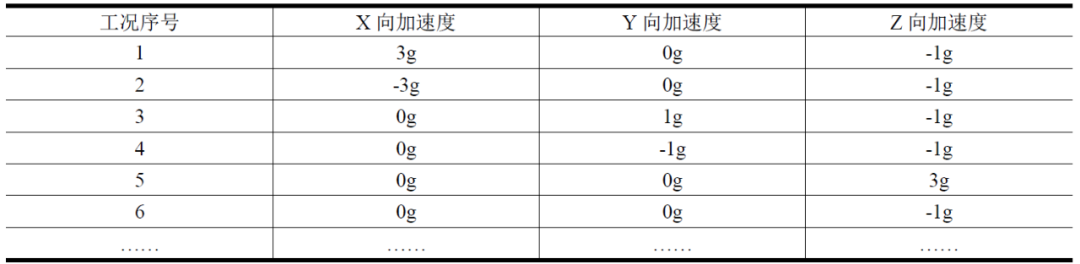
氢系统静强度主要分析不同工况(如表3-3 所示为一工况案例,特定仿真则参考要求的标准拟定工况)下氢系统框架结构和绑带等应力情况。通常储氢罐绑带螺栓处应力集中严重,开裂风险较大,在仿真中需要重点关注。依据强度分析结果,发现结构存在的薄弱环节,再针对薄弱环节进行改进、优化设计。改进、优化设计可从以下方法实现:①更换Q235B 绑带至Q345B 材料的绑带;②增加绑带厚度;③绑带形状设计等方法。
2、模态分析
车辆行驶过程中会受到地面激励,若车载储氢系统的固有频率与这些激励的频率接近,便会发生共振,从而降低车载储氢系统的使用寿命。因此,需对其进行模态分析,使得车载储氢系统设计过程中固有频率避开激励频率,避免共振现象的发生。结构的模态分析是结构振动分析的基础。模态也就是结构产生自由振动时的振动形态,每一个自由振动的固有频率都对应一个振型。
模态分析是用来确定结构振动特性的一种技术,通过模态分析可以得到结构的固有频率、模态振型和模态参与因子等信息,同时模态分析也是采用模态叠加方法对振动系统在激励作用下的动态响应进行计算的基础。因此,对于动态分析,需要全面了解模态参数,并对特定结构的固有频率和模态振型进行计算。同时通过对系统模态的求解并获取固有频率,在设计中应避开共振频率和选择合适的安装位置等方面有重要的作用。因此,模态分析用以确定模型的固有频率及振型,然后在模态分析的基础上进行随机振动分析,以确定模型在随机振动载荷下的响应情况。
3、随机振动及疲劳分析
汽车行驶在凹凸不平道路上,极易遭受来自路面不平度引发的冲击载荷,使车载储氢系统受到竖直方向的振动。由于路面不平度是一种随机变量,每一条道路都有其特有的不平度,所以汽车振动为随机振动。这样,作用在车载储氢系统上的载荷是随机振动载荷,致使车载储氢系统结构损坏的因素可能是路面随机激励的长时间作用而引发的疲劳失效,或是在凹凸不平的路面上运行时车载储氢系统的动强度不足。因此,对车载储氢系统进行随机振动分析,在工程实际中有非常重要的现实意义。
随机振动分析可利用仿真软件的随机振动模块,完成对系统的功能性随机振动分析。先根据模型进行模态分析,得到模态频率和振型,然后根据所承受的随机振动条件,设置模型功率谱密度曲线,并设置相应的阻尼参数,振动分别沿X、Y、Z 三个方向,分析不同随机载荷下系统的均方根位移、均方根应力和均方根加速度响应。
车载氢系统主要由铝合金型材、铝合金板材和绑带支架等部件通过焊接或螺栓预紧等方式组合而成。由于汽车行驶工况复杂,为了进一步确定其使用寿命是否满足要求,对其进行疲劳模拟。根据特定参考标准的要求,分别计算系统在X、Y、Z 三个激励工况下的支架结构应力,结合材料的S-N 曲线计算结构疲劳损伤,评判结构的疲劳寿命水平。通过换算把单位时间结构的损伤,转化为结构的试验寿命。
4、冲击强度分析
由于燃料电池车载储氢系统安装在车辆行驶过程中会受到大加速度载荷瞬态冲击。为验证系统抵抗冲击的性能,对车载储氢系统,按拟仿真的参考标准施加一系列持续时间为D、峰值为A 的单个半正弦脉冲。
在求解过程中,主要关注气瓶支架和绑带在载荷下的响应,监测应力应变分布的情况,同时获得结构的应力和相应的阻尼参数。分析结构的最大应力值是否小于材料屈服应力,最大应变是否小于材料断裂延伸率,进而判断氢系统是否存在冲击破坏的风险。
5、优化设计
设计优化是在给定约束条件下,按某种目标(如重量最轻、成本最低、刚度最大等)求出最好的设计方案。优化的三大要素包括:设计变量(自变量,每个设计变量都有上下限,定义了设计变量的变化范围);约束条件(因变量,设计变量的函数,可以有上下限,也可以只有上限或者下限);目标函数(结构优化的约束条件一般有几何约束条件和性态约束条件两种)。例如,对燃料电池车载储氢系统中的支架进行设计优化,在软件中把支架质量定义为目标函数;把支架的厚度定义为设计变量;把支架的最大应力定义为约束条件。软件将求解出满足各种定义工况下应力标准的支架最小质量对应的支架厚度。
最新资讯
-
R171.01对DCAS的要求⑤
2025-04-20 10:58
-
自动驾驶卡车创企Kodiak 将通过SPAC方式上
2025-04-19 20:36
-
编队行驶卡车仍在奔跑
2025-04-19 20:29
-
全国汽车标准化技术委员会汽车节能分技术委
2025-04-18 17:34
-
我国联合牵头由DC/DC变换器供电的低压电气
2025-04-18 17:33