质子交换膜燃料电池堆安全——质子交换膜燃料电池堆测评技术
一、燃料电池堆性能测评
燃料电池堆在确保运行安全的前提下可进行性能测试,主要进行燃料电池堆正常运行试验、持续和短时电功率试验。按照GB/T 20042.2-2008《质子交换膜燃料电池电池堆通用技术条件》中5.3 节的要求,进行燃料电池堆正常运行试验。
燃料电池堆在完成泄漏测试、电绝缘测试和耐高压测试后,确保没有泄漏、绝缘和耐高压问题才可以进行燃料电池堆性能测试。应采用相应的工装将燃料电池堆放置在燃料电池性能评价测试台上,避免燃料电池堆碰撞及掉落对工作人员或燃料电池堆模块造成损伤。测试台应配有防护舱,在燃料电池堆气密性及性能测试过程中,应保持舱门关闭,避免因零部件弹出及误触高压电导致人员伤害。
连接供气管路、冷却液管路前,应清洗管路,以免将污染物带入燃料电池堆内部堵塞流道、损伤MEA。应保证紧固件有效,避免接头处泄漏。保证流体进出管路通畅,以免因堵塞造成压差过高损伤燃料电池堆。连接负载线路、巡检线路,应保证接触良好,避免因接触电阻过大导致局部过热造成伤害。
连接工作完成后,关闭测试台舱门,先进行燃料电池堆与测试台的保压测试,防止因管路或接头泄漏而造成气体泄漏。保压测试通过后,开始给燃料电池堆加热,待燃料电池堆温度达到指定温度后开始给燃料电池堆通气和加载。加载电流根据电池堆的设计有所区别,一般加载至额定工作电流,同时检测燃料电池堆电压情况,单体电压最低不能低于0.3V,避免燃料电池堆中单体电压过低引起反极,将质子交换膜烧穿导致氢空混合,出现安全隐患。当单体电压低于0.3V 时,应及时减小电流输出,提升燃料电池单体最低电压,如果减小电流单体电压仍然低于0.3V,应立即停止测试,寻找原因。若燃料电池堆运行正常,待达到热稳定后,测量下述参数并记录结果,确认测试结果是否符合燃料电池堆相应规定值:
①满载电流条件下燃料电池堆的终端电压。
②燃料电池堆的运行温度、最高表面温度及环境温度。
③氢气压力,其测得值应不超出规定值的95%~105%或相应规定值±1kPa(两者中取较高值)。
④氢气耗用速率,其测得值应不超出规定值的95%~105%。
⑤氧气消耗速率,其测得值应不超出规定值的95%~105%。
⑥空气压力,其测得值应不超出规定值的95%~105%或相应规定值±1kPa(两者中取较高值)。
⑦冷却剂的入口和出口温度、压力、流量。
按照GB/T 29838-2013《燃料电池模块》中5.7 节的规定,进行燃料电池堆持续和短时电功率试验,应在额定电流下稳定后将电流上升到规定的短时电功率输出并维持规定的时间。系统不得有破裂、裂缝、永久变形或其他物理损坏。所有测试结果均应符合制造商的规定。
二、电性能测试中的氢、电安全测评
燃料电池堆在出厂前需要进行相关的氢、电安全测试,在保证性能的同时保证安全,同时需要对燃料电池堆的外观进行检测,保证燃料电池堆外观没有明显缺损。
(1)燃料电池性能测试中的氢气泄漏监测
根据标准GB/T 29838-2013,根据设计的不同,燃料电池堆性能测试时应检测氢气外漏率,以便于燃料电池系统集成商确定通风系统的最小通风能力,吹扫和通风流量要求。若燃料电池模块不含渗漏保护装置,产品说明书应说明,系统集成商必须提供防护设备或操作程序。
(2)泄漏测试
为确保电池堆的气密性,需要对燃料电池堆进行泄漏测试。将电池堆的氢气、空气和冷却水端口与泄漏测试机的三个端口相连接,打开测漏机开始进行泄漏测试,测试电池堆的外部泄漏量(总外漏、空气腔外漏、燃料腔外漏、冷却腔外漏)。电池堆中每片单电池外部泄漏量不得超过相应的规定值,该规定值由测量使用气体的类型、压力以及MEA 的面积来确定。按照GB/T 20042.2-2008《质子交换膜燃料电池电池堆通用技术条件》中5.2 节的规定进行气体泄漏试验,试验结果应不超过给用户提供的技术文件中对于气体泄漏速率的规定。
对于氢泄漏测试,燃料电池堆应先在满载电流下运行,直至最高温度下达到热稳定。达到这些条件后,停止运行,吹扫燃料电池堆并关闭气体出口;燃料电池堆的温度降至规定的最低运行温度甚至更低。然后逐渐充入阳极气体,也可以是充入氦气或氮气,直至压力达到最高工作压力,并稳定1min。在泄漏试验过程中入口压力应稳定不变,用位于燃料电池堆进气口、泄压装置上游、精度不低于2%的流量计测量漏气速率。如果用氦气或氮气做试验气体,漏气速率应该进行校正,校正公式如下:
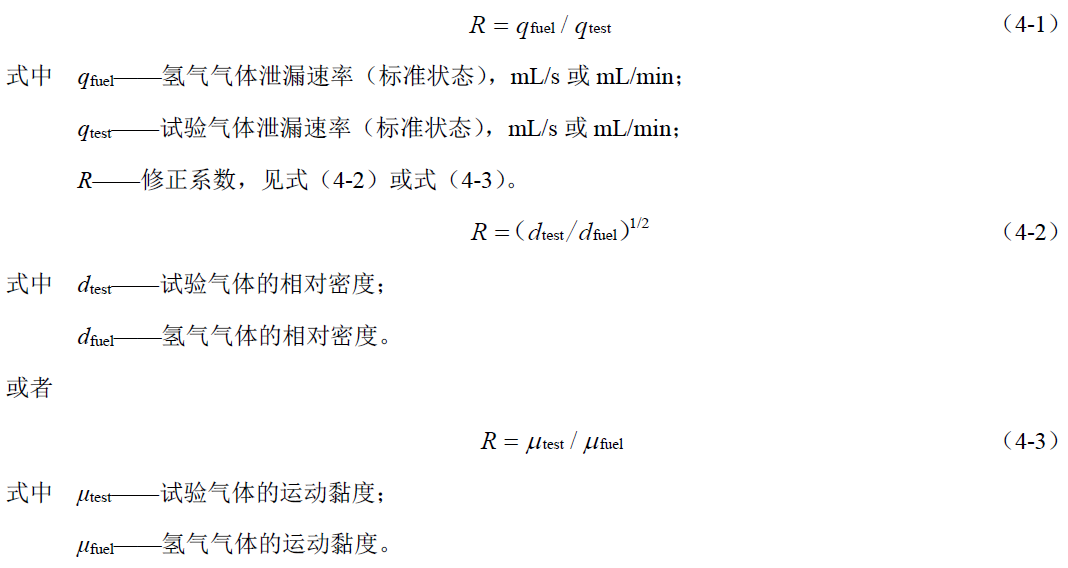
应采用式(4-2)和式(4-3)计算修正系数R,取较高值,并写入试验报告。
记录包括气体通过泄压阀的流速率在内的气体泄漏速率,并写入试验报告。如果因为压力滞后现象或压力设定而在试验中没有采用泄压装置,总泄漏值应该是测得值与泄压装置在最大氢气供应压力下的单独测得的泄漏量之和。
考虑参考条件和气体种类的修正,若用氢气气体或氦气作为试验气体,则将测得的气体泄漏率乘以1.5;若用氮气作为试验气体,则将测得的气体泄漏率乘以2。这一最终计算的结果,应不超过给用户提供的技术文件中的气体泄漏速率的规定,并应向燃料电池系统集成制造商说明,要求将此信息提供给产品最终使用者,以便计算必要通风量。
(3)窜气测试
按照GB/T 20042.2-2008《质子交换膜燃料电池电池堆通用技术条件》中5.6 节的规定进行窜气试验,试验包括燃料腔向氧化剂腔窜气速度的测定,以及燃料腔和氧化剂腔向冷却剂腔的窜气速度的测定。所测得的窜气泄漏速度不大于制造商所提供的最大窜气速率(包括燃料腔对氧化剂腔和燃料腔对冷却剂腔)的规定值可判定为符合要求。
燃料腔向氧化剂腔窜气速度的测定试验中,除燃料腔和氧化剂腔的各一个进气接口外,其余进出接口全部封住。将氧化剂腔的进气接口接上精度不低于2%的流量计(如皂泡流量计),由燃料腔的进气接口通入氮气,调整压力至允许最大工作压力差,稳定1min 后,读出在时间t1 内流量计读数Q1。相应窜气速度X1 按下式求得:
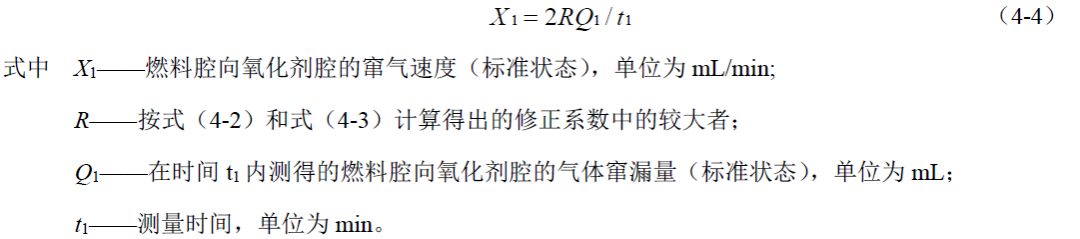
燃料腔和氧化剂腔向冷却剂腔的窜气速度的测定试验中,除燃料腔、氧化剂腔和冷却剂腔的各一个进气接口外,其余进出接口全部封住。将冷却剂腔进口接上精度不低于2%的流量计(如皂泡流量计),由燃料腔和氧化剂腔的进气接口同时通入氮气,调整气压至燃料腔的最大运行压力,并稳定压力1min,读出在t2 内流量计读数Q2,相应窜气速度可按式(2)求得。
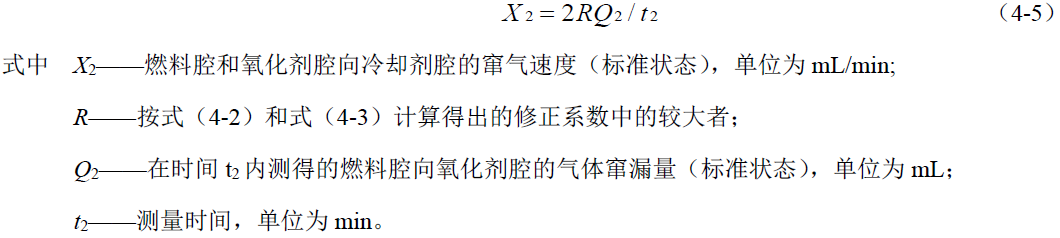
需要注意的是,对于无冷却剂腔或冷却剂腔为开放型的燃料电池堆,燃料腔和氧化剂腔对冷却剂腔的窜气的测定不必进行。
(4)易燃气体浓度试验
本项试验仅适用于带有集中安全通风系统和吹扫程序的封闭系统,其运行温度低于易燃气体的自燃温度。按照GB/T 20042.2-2008《质子交换膜燃料电池电池堆通用技术条件》中5.13 节的规定进行试验,安全通风和吹扫过程与燃料电池堆的具体特征和要求密切相关,此试验应测定正常运行时燃料电池堆外壳内易燃气体的最高浓度。
试验应在安全正常条件下进行,试验区域内应没有可感知的气流。燃料电池堆在正常温度范围内运行,直至达到热稳定。然后在距吹扫口和气体排放出口一定距离的位置测量,以保证测得的易燃气体浓度是外壳内的浓度。此试验应连续进行,两个测量读数间的时间间隔应不少于30min,直到连续两个测得值的增量不超过连续四个测得值平均值的5%。测得的易燃气体浓度应低于可燃极限下限的25%。
(5)气密性测试
按照GB/T 36288-2018《燃料电池电动汽车燃料电池堆安全要求》中6.2 节的规定,对燃料电池堆进行气密性试验。
测试方法为,非风冷燃料电池堆处于冷态,关闭燃料电池堆的氢气排气端口、空气排气端口和冷却液出口,同时向氢气流道、空气流道和冷却液流道加注氦氮混合气体,氦气浓度不低于10%,压力设定在正常工作压力(表压),压力稳定后关闭进气阀门,保压20min。采用压降法测试燃料电池堆的气密性,结果不应低于初始压力的85%。
(6)允许工作压力测试
按照GB/T 20042.2-2008《质子交换膜燃料电池电池堆通用技术条件》中5.4 节的规定,对燃料电池堆进行允许工作压力试验。
燃料电池堆应进行氢气、空气和冷却剂腔许可工作压力试验。燃料电池堆应在最高或最低运行温度下进行试验,以要求更高者为准。在本试验中,如果燃料电池堆模块在正常运行时氢气和空气两侧压力相同,氢气和空气侧可相互连通测试。进行单腔测试时,关闭所有出口腔和非测试腔的进口,向测试腔进口通入氮气或空气,逐步加压到不低于1.3 倍许可工作压力,并维持稳定不低于1min。如果无法实现试验温度条件,则应在环境温度下加压到不低于1.5 倍许可工作压力下进行试验。
试验中,燃料电池堆不应出现开裂、破碎、永久变形或其他物理损伤。
(7)压力差测试
按照GB/T 20042.2-2008《质子交换膜燃料电池电池堆通用技术条件》中5.10 节的规定,对燃料电池堆进行压力差试验。
试验在燃料电池堆最高允许工作温度或最低允许工作温度(取两者中更为严格者)下进行。向阳极和阴极通道通入适当的气体,并逐渐加压,直至达到最大允许工作压差的1.3 倍,保持压力稳定不少于1min,测量泄漏速率。
试验中,燃料电池堆不应出现开裂、破碎、永久变形或其他物理损伤。在试验温度下,不应因为本项试验导致阴极和阳极之间的泄漏率增大。增压后的测得值与最初试验结果的偏差,不应超过仪器的精度要求。
(8)绝缘检测
按照GB/T 36288-2018《燃料电池电动汽车燃料电池堆安全要求》的规定,采用GB/T 18384-2020中的测量方法,测量燃料电池堆的绝缘电阻值。
绝缘电阻的测量应在出现露点的阶段,以适当的频次进行测量,以便得到绝缘电阻的最小值。测量时应闭合全部开关,关闭车辆绝缘电阻检测系统,以免影响测量值。应当将测量设备适当稳定的读数作为测量值。
燃料电池堆在加注冷却液而且冷却液处于冷冻循环状态下,正负极的对地绝缘性要求分别不应低于100Ω/V。
(9)耐高压测试
按照GB/T 18384.3-2015 中7.3 节的试验方法,对燃料电池堆进行耐电压试验,试验中不应发生介质击穿或电弧现象。
(10)接地保护测试
按照GB/T 36288-2018《燃料电池电动汽车燃料电池堆安全要求》的规定,对燃料电池堆进行测试。
测量前,断开与燃料电池堆相连的其他供电电源和负载;测量时,测量仪表端子分别连接至接地端子和燃料电池堆外壳。当燃料电池堆输出电压高于60V 时,燃料电池堆需有接地点,接地点与所有裸露的金属间电阻小于0.1Ω。
(11)电气过载测试
按照GB/T 20042.2-2008《质子交换膜燃料电池电池堆通用技术条件》中5.8 节的规定,对燃料电池堆进行电气过载试验。
燃料电池堆应在额定电流下稳定运行,然后将电流逐渐增加到规定值并在规定时间内保持不变。
过载试验后,燃料电池堆不应出现开裂、破碎、永久变形或其他物理损伤。
(12)介电强度测试
按照GB/T 20042.2-2008《质子交换膜燃料电池电池堆通用技术条件》中5.9 节的规定,对燃料电池堆进行介电强度试验。
如果燃料电池堆不能保持运行温度不变,介电强度试验应该在最高允许温度下进行,并应记录试验时的温度。对进行介电强度试验的燃料电池堆,应切断氢气供应,并用吹扫气体进行吹扫。在带电部分和不带电金属构件之间施加试验电压,采用直流电或50Hz±2Hz 的正弦交流电,试验电压应在不少于10s 的时间内稳定增加到规定值,然后至少维持1min。
如果没有出现绝缘击穿,且泄漏电流不超过1mA 乘以试验电压与开路电压之比,则认为燃料电池堆的介电强度符合要求。
三、机械振动、冲击测试中的安全测评
燃料电池堆在使用中经常受到运行中的短时、瞬态振动所引起的短持续时间脉冲和震荡力的作用,这些力的特性和被测样品的阻尼使样品的振动响应达不到稳态条件。当用正弦或随机振动进行了初始振动响应检查之后,时间历程试验将使样品经受由具有模拟动态应力特性的响应谱确定的振动(加速度、速度或位移)时间历程。为了满足产品在整车应用中的机械振动和冲击的要求,需要对产品的抗振动和抗冲击进行试验验证。基本测试流程包括以下步骤:
1)初始检测:燃料电池堆被测样品应按有关规范的要求进行外观、尺寸和功能检测。
2)一般要求:除非有关规范另有规定,燃料电池堆被测样品应按照标准要求,在优选的每条轴向上进行振动。若有关规定没有另做规定,轴向间的顺序是不重要的。
3)中间检测:当有关规范有规定时,在所规定的时间历程试验或正弦扫频试验期间,样品应工作,并检测其性能。
4)最后检测:应按有关规范的规定对样品进行外观、尺寸和功能检查。有关规范应提供接受或拒收样品的判据。
(1)机械振动测试
振动测试模拟车辆长时间在复杂路况行驶(如搓板路、颠簸路、起伏路等)过程中的性能变化。
燃料电池堆长时间振动颠簸后,其内部不能出现错位,从而发生短路和气体泄漏等安全问题。按照GB/T20042.2-2008《质子交换膜燃料电池电池堆通用技术条件》中5.7 节的要求,对燃料电池堆进行耐振动试验,试验方法按照GB/T 2423.10-2019 中第8 章的规定进行。
试验要对燃料电池堆进行依次X、Y、Z 三个方向的振动测试,轴向的选择应选最可能暴露故障的方向。要求测试结束后,电池堆连接可靠、结构完好,不应出现开裂、破碎或其他物理损伤,且应能承受介电强度试验、压力差试验、气体泄漏试验、正常运行试验和易燃气体的浓度试验并符合相关要求;最小监控单元电压无锐变,电压差的绝对值不大于0.15V,无泄漏、外壳破裂、爆炸或着火等现象;燃料电池堆的绝缘性能和气密性性能无明显下降。
振动测试后,燃料电池堆中的零部件无明显位移、扭转和弯曲;零部件的谐振频率与初始值的偏差应小于10%,各个紧固螺丝的剩余紧固力不低于初始值的60%;各个电气连接点的电阻与初始值的偏差应小于5%。
(2)机械冲击测试
按照GB/T 36288-2018《燃料电池电动汽车燃料电池堆安全要求》中6.1 节的规定,对燃料电池堆进行机械冲击试验。燃料电池安装固定后,在X 向、Y 向、Z 向上分别以5.0g 的冲击加速度进行冲击试验。机械冲击脉冲采取半正弦波形,持续时间15ms,每个方向各进行一次。
燃料电池堆冲击测试之后,机械结构应不发生损坏,气密性满足气密性检测要求,绝缘性应满足绝缘性要求。
四、高、低温存储及低温启动测试中的安全测评
燃料电池堆储存温度要求及高低温储存测试应符合国家标准相关细则规定。其中,模块储存温度范围为-40℃~60℃。
(1)高温存储试验
按照GB/T 33978-2017《道路车辆用质子交换膜燃料电池模块》中6.13.2 节的规定,对燃料电池堆进行高温存储测试。
将燃料电池堆置于高温存储试验环境中,静置12h 以上,至燃料电池堆内温度达到预定的储存温度(如60℃);将燃料电池堆试验环境温度降至室温,静置12h 以上;重复以上过程共三次。
试验后,燃料电池堆不应出现裂缝、扭曲变形等缺陷;按照GB/T 20042.2-2008 中5.6 节的规定进行模块的燃料腔、氧化剂腔、冷却剂腔的窜气实验,并能满足相关要求。
(2)低温存储试验
按照GB/T 31035-2014《质子交换膜燃料电池电堆低温特性试验方法》中8.4.2 节的规定,对燃料电池堆进行低温存储试验。
燃料电池堆正常稳定运行条件下且燃料电池堆内部温度达到正常工作温度,按照关机程序进行燃料电池堆关机,记录关机所用的时间与消耗的能量与物质的量;将燃料电池堆置于低温存储试验箱中,按试验要求设置试验箱温度,静置12h 以上;将燃料电池堆试验环境温度升至室温,静置12h 以上,按照启动程序进行燃料电池堆的启动;重复上述过程,达到连续成功启动两次。
试验后,观察燃料电池堆模块封装壳体和封装安装固定部件是否出现裂缝、扭曲变形等缺陷;燃料电池堆模块按照GB/T 29838-2013 中5.3 节和5.4 节的规定进行气密性和运行试验;按照GB/T20042.2-2008 中5.6 节的规定进行燃料腔、氧化剂腔、冷却剂腔的窜气试验,试验中,燃料电池堆模块应能满足相关要求。
(3)低温启动试验
按照GB/T 31035-2014《质子交换膜燃料电池电堆低温特性试验方法》中8.4.3 节的规定,对燃料电池堆进行低温启动试验。
燃料电池堆正常稳定运行情况下,按照关机程序对低温存储前的燃料电池堆进行关机;将燃料电池堆置于低温存储试验箱中,按照试验要求设置试验箱温度,静置12h 以上;将燃料电池堆在低温试验环境中按照启动程序启动,记录达到额定功率输出的时间、气体消耗及相关的电流、电压;将燃料电池堆在额定功率下输出稳定运行10min(功率加载误差≤2%);重复上述过程,达到连续成功启动两次。
试验后,在室温下对燃料电池堆进行气密性试验、运行试验、允许工作压力试验、冷却系统压力试验、窜气试验、压力差试验、启动试验、关机试验、发电性能试验,燃料电池堆应均能满足相关要求。
五、IP 测试中的安全测评
质子交换膜燃料电池堆应具备防水防尘能力,保护燃料电池堆内部材料与部件不受水、灰尘影响。
若整车对燃料电池堆模块有进一步要求,则按照整车的要求;若无特殊要求,按GB/T 4208-2017 中的规定执行测试,模块防水应满足GB/T 4208-2017 中IPX5 等级要求,防尘应满足GB/T 4208-2017 中IP5X等级要求。
(1)防水试验
按GB/T 4208-2017《外壳防护等级(IP 代码)》中的规定,对燃料电池堆进行防水试验。
防水试验包括滴水箱试验、摆管或淋水喷头试验、喷嘴试验、浸水试验和喷水试验,不同外壳防护等级防水试验和试验方法见表4-2。
表4-2 不同外壳防护等级防水试验和试验方法


依据GB/T 33978-2017《道路车辆用质子交换膜燃料电池模块》,若燃料电池整车对燃料电池模块防水有要求,则按照整车的要求,若无特殊要求,模块防水应满足IPX5 等级要求。
(2)防尘试验
按GB/T 4208-2017《外壳防护等级(IP 代码)》中13.4 节的规定,对燃料电池堆进行防尘测试。
防尘试验应在防尘箱中进行,密封试验箱内的粉末循环泵可以用能使滑石粉悬浮的其他方法替代。
滑石粉应用金属方孔塞滤过,金属丝直径50μm,筛孔尺寸为75μm。滑石粉用量为每立方米试验箱容积2kg,使用次数不得超过20 次。被试验的外壳按正常工作位置放入试验箱内,可不与真空泵连接。
在正常情况下开启的泄水孔,试验期间应保持开启。防尘试验持续8h。
如不能将整台设备置于试验箱内做试验,可选用下列方法之一进行:用外壳的各个封闭部分做试验;用外壳有代表性的部件(包括组件)试验,试验时这些部件应安装就位;用具有相同结构、按比例缩小的设备进行试验。
对于后两种情况,试验时抽出设备的空气体积,应与整台设备时规定相同。试验后,观察滑石粉沉积量及沉积地点,如果同其他粉尘一样,不足以影响燃料电池堆的正常操作或安全,即认为试验合格。除非燃料电池堆设计时明确规定了特例,在可能沿爬电距离导致电痕化处不允许有灰尘沉积。
依据GB/T 33978-2017《道路车辆用质子交换膜燃料电池模块》,若燃料电池整车对燃料电池模块防尘有要求,则按照整车的要求,若无特殊要求,模块防尘应满足IP5X 等级要求。
六、盐雾腐蚀测试中的安全测评
燃料电池堆应对腐蚀环境具有耐受性,满足腐蚀工作环境的安全要求。按照GB/T 28046.4-2011 中5.5.2 节所述的测试方法和GB/T 2423.17-2008《电工电子产品环境试验第2 部分试验方法试验Ka:盐雾》,进行燃料电池堆的盐雾腐蚀测试。
盐雾腐蚀试验应在试验箱中进行,试样应按正常使用状态进行试验,试样之间不应有接触,也不能与其他金属部件接触。试验箱的温度应维持在(35±2)℃。所有的暴露区域都维持盐雾条件,至少用两个面积为80cm2、放置在不受试样遮挡、不同位置处的器皿在暴露区域的任何一点连续收集至少16h 的雾化沉积溶液,平均每小时收集量应在1.0mL~2.0mL 之间。器皿内的溶液用于测试pH 值和浓度,在(35±2)℃测量时,溶液浓度满足(5±1)%(质量比)要求,pH 值在6.5~7.2 内。试验结束后,小试样应在不超过35℃自来水下重洗5min,然后用不超过35℃的蒸馏水或者去离子水重洗,最后晃动或者用气流去掉水滴。试验在标准恢复条件下放置1~2h。一般测试盐溶液采用氯化钠(化学纯、分析纯)和蒸馏水或去离子水配置,其浓度为5%±1%(质量分数),(35±2)℃下测量pH 至在6.5~7.2之间。
试验后,可通过目视检查盐雾腐蚀情况,然后对燃料电池堆进行气密性试验、运行试验、窜气试验、绝缘试验、电气过载试验、介电强度试验,并能满足相关要求。
最新资讯
-
R171.01对DCAS的要求⑤
2025-04-20 10:58
-
自动驾驶卡车创企Kodiak 将通过SPAC方式上
2025-04-19 20:36
-
编队行驶卡车仍在奔跑
2025-04-19 20:29
-
全国汽车标准化技术委员会汽车节能分技术委
2025-04-18 17:34
-
我国联合牵头由DC/DC变换器供电的低压电气
2025-04-18 17:33