一种机电一体离合器执行器设计
本文研究的主要方向是设计一种低成本、高效率的离合器执行器。
1 传统的离合器执行机构原理及组成
传统MT使用液压式操纵机构,通过踏板连接的连杆,推动离合器主缸内的液压油,从而推动离合器副缸的推杆或CSC(Concentric Slave Cylinder)活塞,实现离合器的结合与分离[1],如图1所示。

图1 手动变速器液压式操纵机构
传统AT、AMT、DCT通过油泵泵油,由电磁阀分配液压油经过油路,推动活塞压紧或分离压盘与从动盘;推动分离叉,带动分离轴承通过膜片弹簧压紧或分离离合器压盘与离合器从动盘,实现离合器结合或分离动作[2],如图2所示。
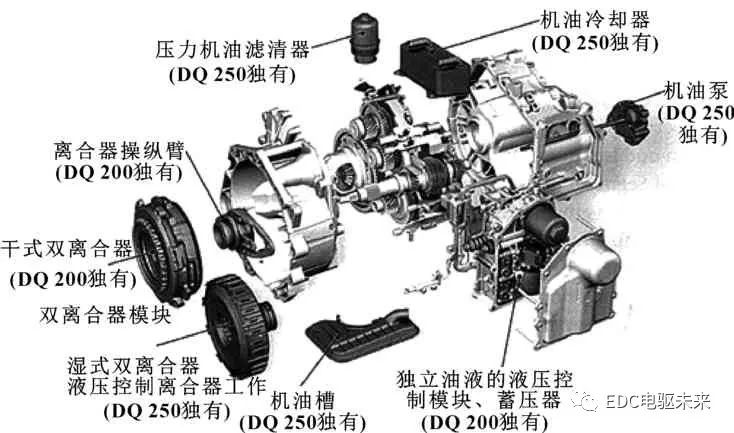
图2 双离合变速器液压式操纵机构
2 传统离合器执行机构的不足
传统MT的离合器执行器需要与加速踏板、制动踏板、换挡杆操作进行配合,长时间驾驶容易疲劳;离合器摩擦片发生磨损时,踏板行程会发生偏移,人工操纵难以实现精确控制,将导致离合器磨损加剧。当离合器摩擦片即将达到寿命极限时,会发生离合器结合不稳定的情况,造成整车抖动或动力性下降,影响驾驶体验。
传统AT、AMT、DCT使用的液压系统,为了实现精确控制,电磁阀的制造精度较高、配合间隙小,因此对零件清洁度的要求高,零件制造难度大。布置阀板油路时需要综合考虑离合器控制油路与换挡油路,设计难度大,结构相对复杂,占用体积较大,因此会造成执行机构成本较高。
3 机电一体式离合器执行器设计方案
针对传统离合器执行器的问题,开发一种机电一体式离合器执行器,这种离合器执行机构主要由控制系统、驱动机构、执行机构及其他元件组成。两套机电一体式离合器执行器组合使用,可用于驱动DCT的双离合器,其系统组成如图3所示。
驱动机构包括:电动机、传动齿轮副、丝杆螺母副和主液压缸。电动机的旋转运动通过齿轮副减速增扭及丝杠螺母副运动转换,变为主液压缸活塞的直线运动。

图3 机电一体式离合器执行器系统组成
执行机构包括:主液压缸活塞、内外CSC(用于AMT时可使用单缸CSC)、内外离合器(用于AMT时可使用单离合器),主液压缸活塞的运动通过油液传递至内外CSC,分别执行内外离合器打开、闭合及滑磨的动作。
控制系统主要包括以下部件:TCU、压力传感器、位移传感器及目标磁铁。TCU根据判定条件向电机发出转动信号,位移传感器反馈运动终止位置,压力传感器反馈执行压力。通过自学习找到离合器的结合点,通过算法计算进行离合器的准确控制。
其他元件包括:支撑轴承,排气用的排气阀、补油装置、丝杠防转销等,实现排除油液中空气、补偿油液损失、防止丝杠周向转动等功能。
这种新型的机电一体式离合器执行器的系统组成元件少、结构简单,简化了液压系统油路,也减少了电磁阀的使用。将此模块在变速器总成上减少的占用体积,应用于AMT、DCT上时,可降低对零件清洁度的要求,也降低了系统集成难度,有利于控制成本。
这种新型离合器执行器的控制系统可以读取压力传感器及位移传感器的信号,从而诊断实际工作状态是否符合设定值,图4为其控制逻辑图。
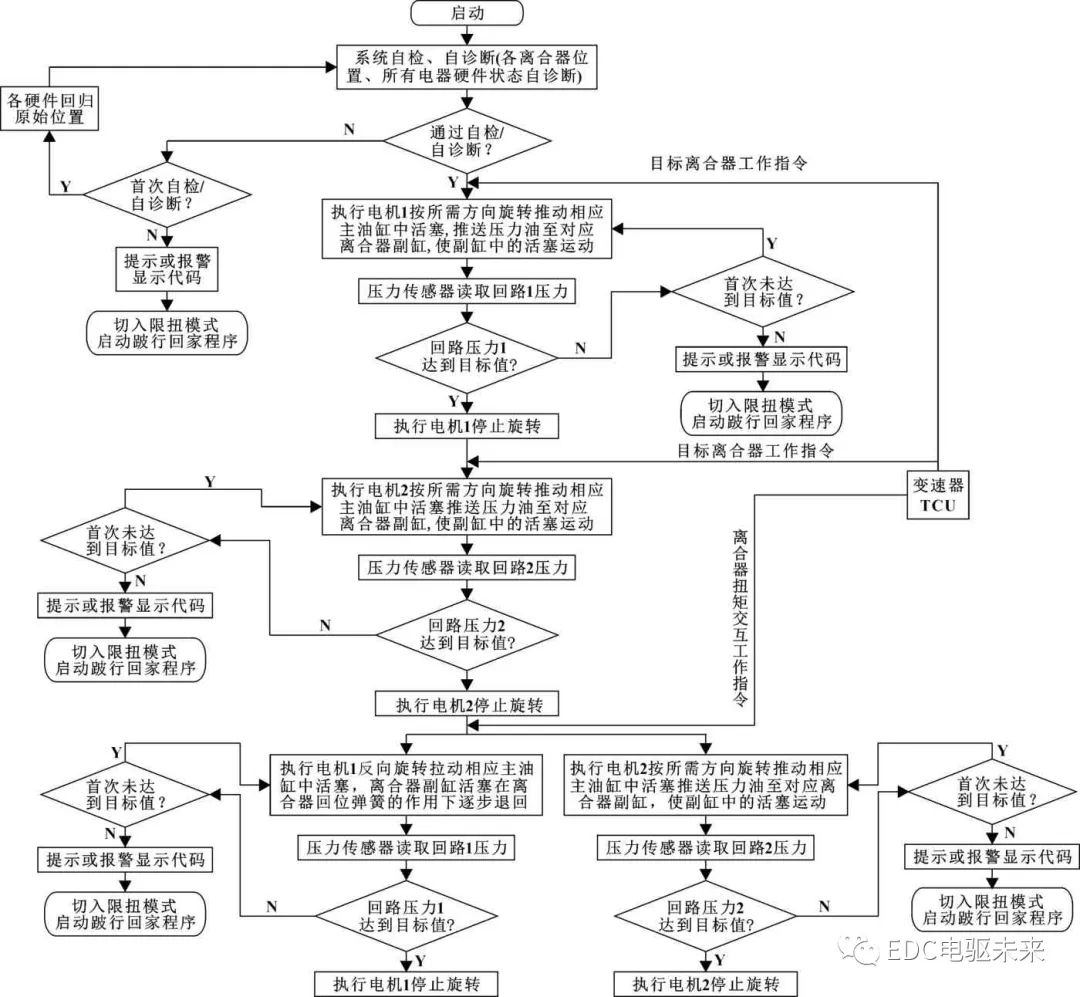
图4 系统控制逻辑
4 设计参数匹配优化
为满足系统功能需求,离合器执行系统的设计参数需要依据被执行件(CSC及离合器)的参数进行匹配设计。
4.1 匹配的CSC需求参数
匹配的CSC需求参数,如表1所示。
表1 匹配CSC参数
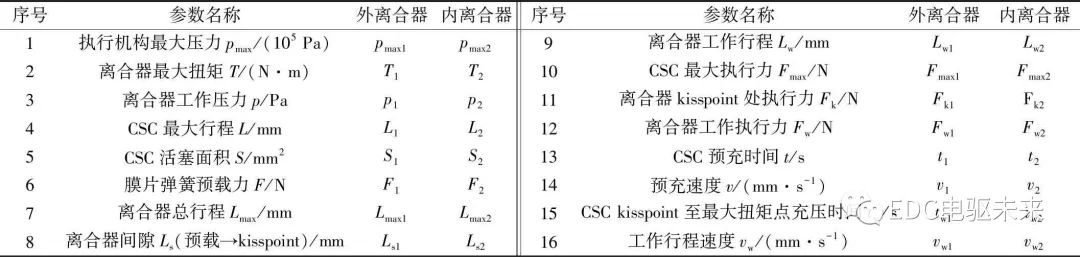
4.2 丝杠螺母参数计算
回转运动转化为直线运动时效率:
η1=(0.95~0.99)tanλ/tan(λ±ρ′)[3]
其中:λ=arctan Sd/(πd2)≤ρ′;
ρ′=arctanf/(cosα/2)
式中:λ为螺纹升角;ρ′为当量摩擦角;Sd为导程;f为摩擦因数;d2为螺纹中径;支撑效率为0.95~0.99。
满足容许载荷的前提下,选直径小、效率高的丝杠螺母。
4.3 电机选型
(1) 驱动功率计算
空行程输出功率:P1=Fk1v1;P2=Fk2v2
工作行程输出功率:Pw1=Fw1v1;Pw2=Fw2v2
取输出功率大的离合器进行计算(以外离合器为例),工作行程驱动功率:

其中:η2为机械效率;η3为电机效率。
根据功率需求,选择合适的执行电机功率。
(2)主液压缸活塞直径与CSC直径比的选择
执行器考虑兼顾双离合器的工作,且减小主缸活塞受载。初选活塞缸直径D,主缸活塞面积Sz=1/4πD2,活塞面积比分别为Y1=S1/Sz、Y2=S2/Sz,丝杠最大轴向力分别为

根据最大轴向受力,选择合适的主活塞直径。
(3) 需求扭矩计算
空行程需求推力:
FN1 =2πη1TN1/Sd,FN1≥Fk1/Y1
则需求扭矩TN1≥Fk1Sd/(2πη1Y1)
工作行程需求推力:
FNw1 =2πη1TNw1/Sd,FNw1≥Fw1/Y1
则TNw1≥Fw1Sd/(2πη1Y1)
根据扭矩需求及电机输出扭矩特性,选择合适的减速比。
4.4 齿轮副设计
(1)按活塞空行程移动速度预选减速比
活塞缸工作行程移动速度
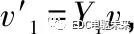
此时螺母需求转速
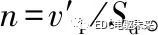
假设电机转速为n′时满足扭矩要求,电机输出扭矩约为

初选减速比i=n′/n。
(2) 确定实际减速比
电机输出齿Z1,从动齿Z2,则实际速比i′=Z2/Z1(略大于i)。此时,螺母实际转速n实=n′/ i′,活塞移动速度

至最大扭矩点实际充压时间:

需t w1实≤t w1。
(3) 验算空行程预充时间
根据电机特性,假设电机转速n″时需要满足扭矩要求,此时电机输出扭矩约为

此时,输出到螺母的转速
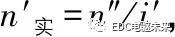
活塞移动速度

实际预充时间t实
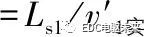
需验算:

4.5 传感器选择及其他细节设计
(1) 依据执行机构工作压力计选择合适的压力传感器pN1=FNw1/Sz,pN1≤pmax1。
(2) 依据CSC最大行程L选择合适的位移传感器。
(3)依据需求设计补油壶、油管等附件。
4.6 功能演示模型搭建
所有功能模块设计完成后,即可进行功能演示模型的搭建,如图5所示;完成模型搭建,检查分析并制造试验样件,如图6所示,即可进行功能测试。
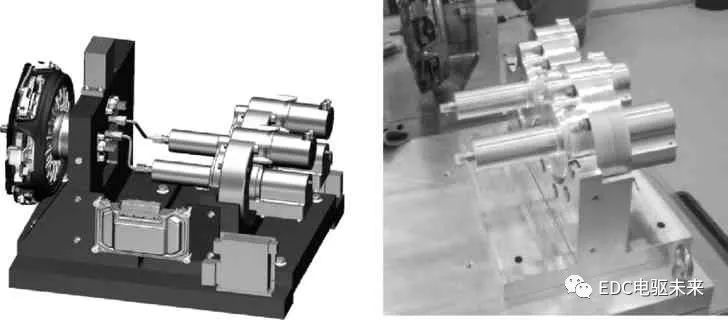
图5 功能演示模型 图6 试验样件
5 功能测试验证
对试验样件进行功能测试,确认是否满足功能需求。
(1) 执行机构最大驱动力验证
试验样件的传感器输出电压-压力特性曲线如图7所示。
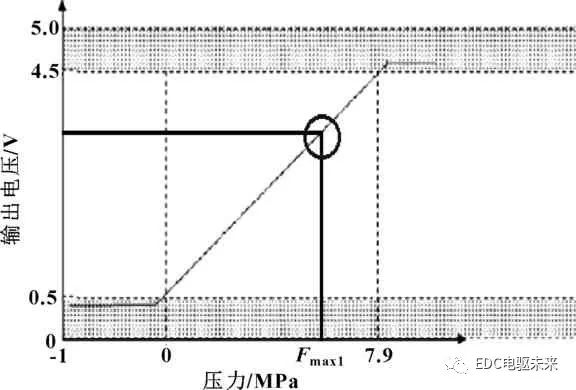
图7 压力传感器输出曲线
使驱动电机运动至行程末端,传感器输出电压约为3.8V,进行油压换算,试验测试油压不小于Fmax1。因此试验样件满足CSC最大执行力需求。
(2)执行机构位移验证
为试验样件选取的位移传感器占空比-位移特性曲线如图8所示。
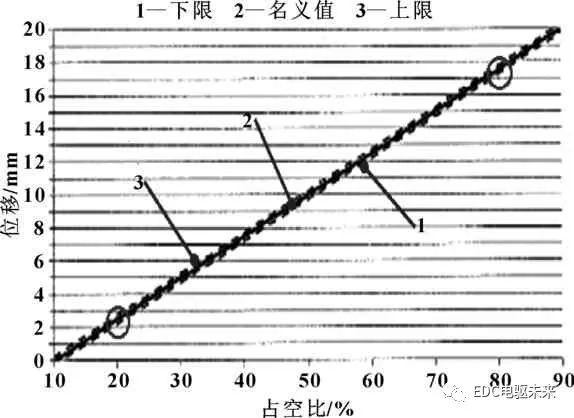
图8 位移传感器输出曲线
执行机构运行至初始行程,并进行占空比标定(约20%),记录行程LA≈3 mm。执行机构运行至最大行程,并进行占空比标定(约80%),记录行程LB≈18 mm。所以:
LB-LA=15 mm≥Lmax1
则试验样件满足离合器最大行程需求。
(3)执行机构执行时间验证
通过控制器读取CSC端建压的实际时间,如图9所示。
读取电机迟滞时间tA约为0.15 s,电机运行至kisspoint的时间tB约为0.15 s,执行机构运动时间tC约为0.5 s。tA+tB≈0.3 s≤t1,且tC≈0.5 s≤tw1,试验样件满足离合器最大行程需求。
根据试验样件测试结果,文中设计的试验样件基本能满足离合器的驱动力、位移及驱动速度要求。
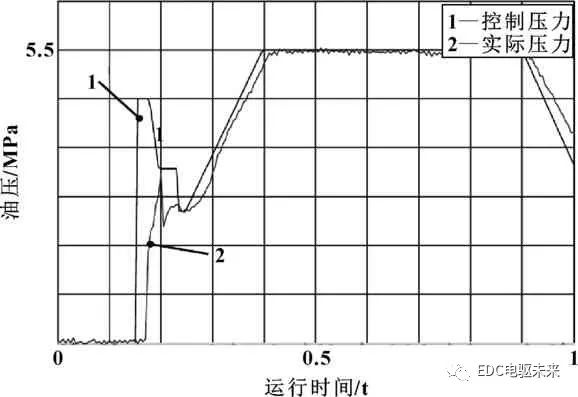
图9 CSC充压曲线
6 总结
本文作者设计的离合器执行机构,是一种新型的机电一体式执行机构。相较于现有的离合器执行机构,此种离合器执行机构通过继续改进优化,可实现更低成本、更轻量化及更高的执行效率。此模块高度集成,可以推广应用到更多种类的变速器总成(如AMT、CVT等)。
编辑推荐
最新资讯
-
全球首次!IVISTA 2023版修订版引入带灯光
2025-04-28 09:59
-
我国首批5G毫米波行业标准送审稿审查通过
2025-04-28 08:56
-
5/16 厦门- 新能源汽车电驱测试技术的创新
2025-04-28 08:53
-
国内首个汽车电磁防护技术验证体系EMTA正式
2025-04-28 08:49
-
一文带你了解滤波器
2025-04-28 08:35