汽车制动引起转向盘抖动问题分析
摘 要:采用模态分析方法得到汽车制动引起转向盘抖动的原因是前悬架系统模态;通过改变控制臂后衬套刚度可改变悬架系统模态。试验结果表明:增加下摆臂后衬套刚度可改变悬架系统模态,有效缩短振动频域,降低转向盘抖动幅度。
引 言
制动引起的踏板、车体振动及转向盘抖动发生的根源是机加工中制动盘厚度变化不均匀[1],这类振动或抖动称为冷抖动(Cold Judder)。制动盘圆周方向厚度不均匀会引起制动摩擦力矩周期性变化,导致转向盘抖动,是机械结构中由激励源、振动传递器和振动放大输出等环节组成的机械振动系统。由于制造精度不足引起制动盘圆周方向厚度尺寸不一致,这在汽车界是一大难题;另外,用户长期使用中频繁制动产生的制动摩擦力矩及不同的制动强度等因素,也会引起制动盘局部磨损,从而加剧制动盘沿着圆周方向的厚度尺寸变化不均匀。以上原因导致制动过程中制动盘与摩擦片之间的制动摩擦力产生周期性变化[2],周期性变化的制动力矩作为一种外部激励传递给悬架系统、转向系统及车身结构系统,当制动力矩的变化频率与悬架系统、转向系统、轮端等结构模态频率相同时,会发生共振。由于采用的悬架结构、轮端结构及转向系统结构不同,驾驶员对制动引起的转向盘振动主观感受也会不同[3]。针对转向盘抖动问题,国内学者通过抖动现象描述、试验研究和定性分析进行研究。
在某SUV开发过程的路试阶段,在75~95 km/h车速下制动时,车辆发生抖动,转向盘抖动严重,制动踏板和车身地板轻微抖动。
1 制动抖动发生机理
制动抖动发生的主要原因是制动力矩波动导致地面制动纵向力波动[4],引起前轮摆振,该振动通过转向系统及悬架摆臂衬套分别传递给转向盘及前副车架,再由副车架放大后传递给转向盘、车身,引起转向盘抖动、车身地板抖动。
根据以上分析及故障车型的具体结构,得出制动抖动的传递路径,如图1所示。

图1 制动抖动传递路径原理图
根据图1并结合整车路试测试,分析该振动问题的传递途径,分辨共振部件,计算共振频率,结合整车结构布置,进行改进验证。
2 共振源模态分析
2.1 激励源频率分析
若制动盘的圆周内厚度不均匀现象出现1~2次,则汽车行驶时,随着车轮旋转1圈,会产生1~2次激励[5]。轮胎每秒钟转动的圈数为
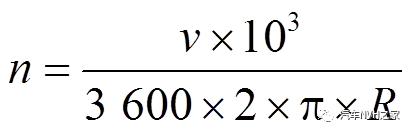
(1)
式中:v为故障车车速,km/h;R为轮胎滚动半径,mm。当v为75~95 km/h,轮胎滚动半径R为330 mm时,轮胎转动圈数为10.0 ~12.7圈/s,计算得出制动盘与摩擦片产生的激励频率分别为10.0~12.7 Hz和20~26 Hz。若该故障车悬架、转向及轮边等部件固有频率正好处于该范围内,则会引起共振。
2.2 麦弗逊前悬架模态分析
该车前悬架采用麦弗逊悬架,模态分析结果见表1。
表1 前麦弗逊悬架系统模态分析 Hz

由表1可知,前悬架系统的纵向模态频率为24.9 Hz,处于该车在75~95 km/h(对应车速为93 km/h)下的激励频率范围20~26 Hz,会引起共振,导致车体、制动踏板及转向盘抖动。
2.3 轮边制动部件模态分析
带转向节的前轮制动部件包括前转向节、制动卡钳、制动盘及摩擦片。模态分析结果见表2。
表2 轮边制动部件模态分析 Hz

表2中自由模态是结构自身的固有模态,工作模态是用于工程时施加边界约束后的实际结构模态。带转向节的前轮制动部件的模态频率,不在75~95 km/h制动时的激励频率范围内,避免了系统共振发生。
2.4 转向系统模态分析
通过HyperWorks软件对该车转向系统的模态分析得到,前后方向振动频率是51.9 Hz,左右方向振动频率是68 Hz。转向系统模态频率均不在75~95 km/h制动时的激励频率范围内,避免了系统共振发生。
3 整车道路试验研究
为了测试制动力矩从轮边到转向盘的具体传递过程,在良好的沥青路面上进行制动抖动再现试验,实车不同部位安装15个同步信号加速度传感器(3个方向)。加速点测点布置见表3。
表3 传感器测试布置
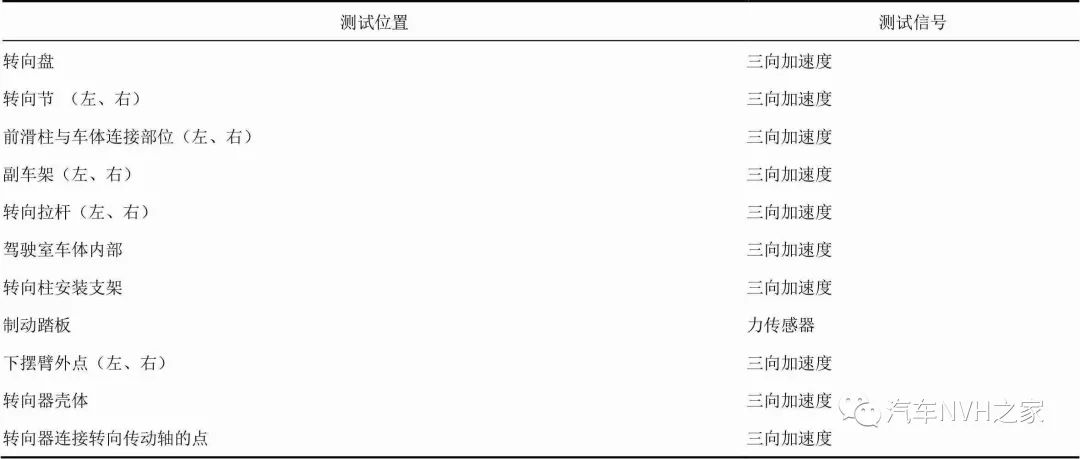
通过以上测点可以实时测试各个环节振动加速度幅值。
3.1 试验改进方案
对前悬架系统模态进行研究,随着控制臂后衬套刚度增加,前悬架模态随之改变。橡胶衬套刚度与悬架固有模态之间的关系见表4。
表4 橡胶衬套刚度与悬架系统模态关系

增加控制臂后衬套刚度,可提升悬架系统模态频率,可将模态频率移出制动抖动车速下的激励频率范围。结合式(1)计算的故障车激励频率,将控制臂后衬套径向刚度相比原刚度增加200%作为最终的改进方案,见表5。
表5 控制臂后衬套刚度改进 N/mm

3.2 改进方案的主观评价结果
对故障车分别进行原车状态及改进方案试验,制动引起转向盘抖动的主观评价见表6。
表6 主观评价结果
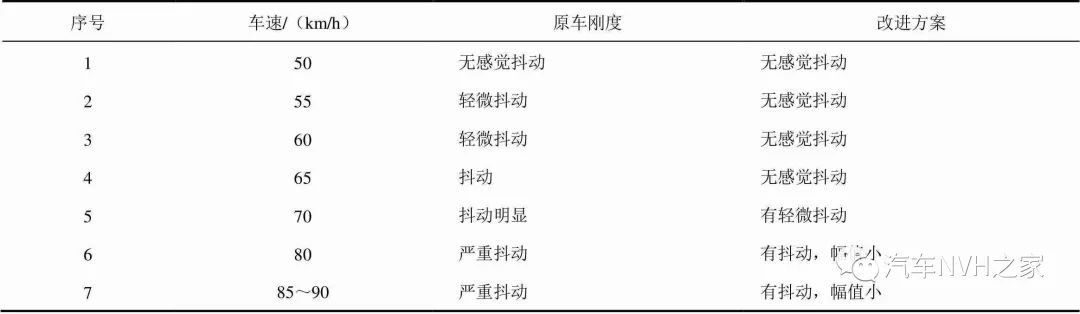
从表6评价结果可知,采用改进方案后,在50~70 km/h速度段,转向盘抖动幅度比原车降低,改善明显;在70~90 km/h速度段,制动抖动幅值变小,改善明显。
3.3 改进方案的客观评价结果
对原车及改进方案分别进行80 km/h速度下制动,并进行转向盘抖动测试。测试部位如图2所示,测试结果如图3所示。
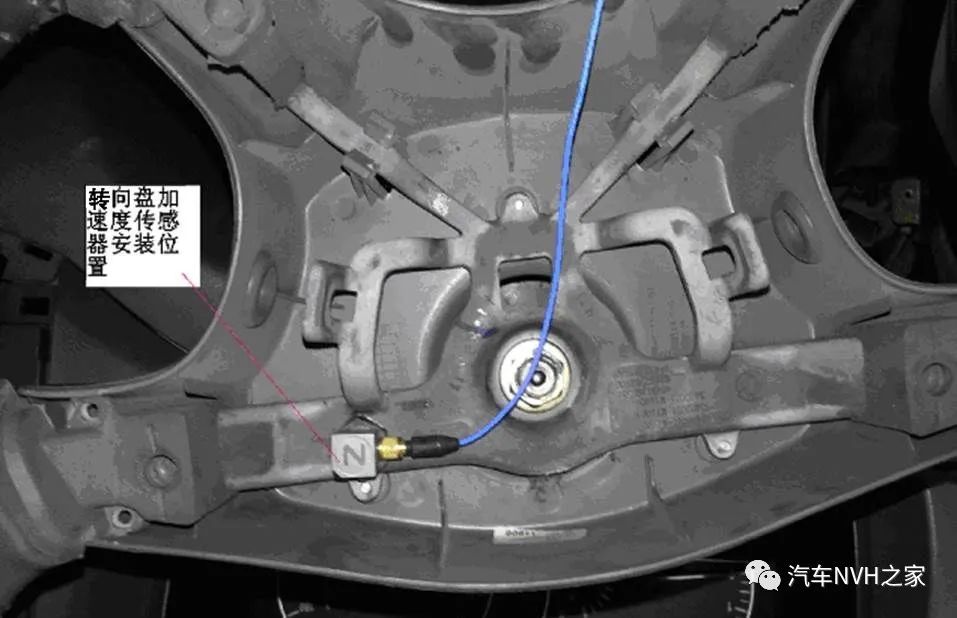
图2 转向盘抖动测试传感器安装
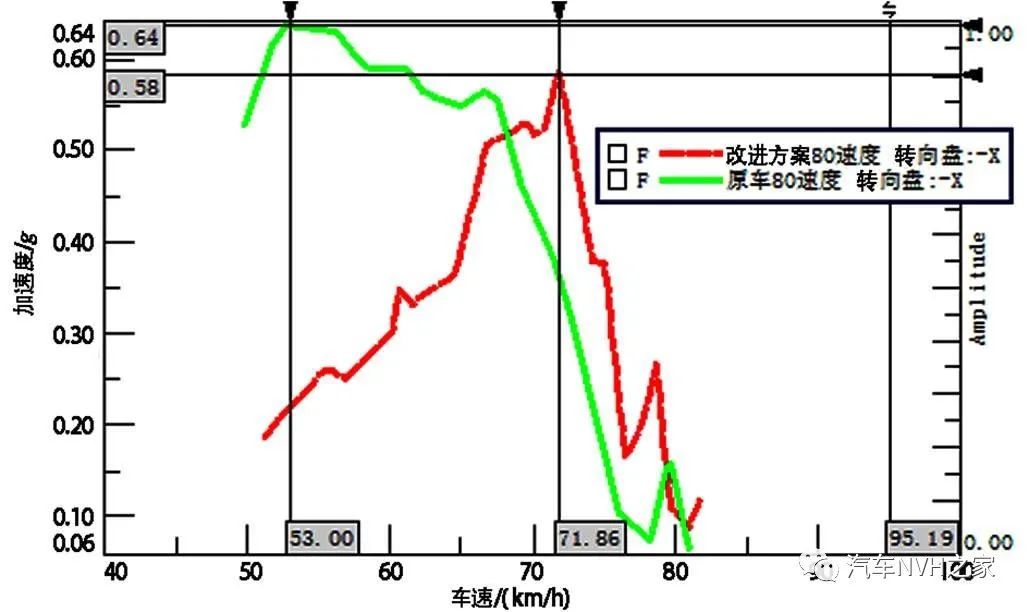
图3 50~80 km/h制动时转向盘抖动
由图3得到以下结论:(1)以80 km/h初速度制动时,原车转向盘抖动幅值最大为0.64g,改进方案转向盘抖动幅值最大为0.58g,降低近10%;(2)改进方案在50~72 km/h阶段转向盘抖动迅速下降,原车在50~70 km/h阶段转向盘抖动幅值呈现上升趋势;因此,在50~70 km/h车速范围内,改进方案转向盘抖动较原车有明显改善,同主观评价结果一致。
4 结 论
(1)制动引起转向盘抖动的共振源是前悬架系统,通过改变控制臂后衬套刚度可改变悬架系统模态;
(2)试验结果表明:增加下摆臂后衬套刚度可改变悬架系统模态,有效缩短振动频率,降低转向盘抖动幅值。
编辑推荐
最新资讯
-
推荐性国家标准《乘/商用车电子机械制动卡
2025-04-30 11:13
-
载荷分解
2025-04-30 10:46
-
布雷博在上海开设亚洲首个灵感实验室
2025-04-30 10:25
-
组分性能对锂离子电池卷芯挤压力学响应的影
2025-04-30 09:00
-
美国发布自动驾驶新框架,放宽报告要求+扩
2025-04-30 08:59