燃料电池电动汽车匹配设计流程和方法
1、燃料电池电动汽车的工作原理
燃料电池电动汽车是指由电动机驱动,由燃料电池提供部分或全部电能的新能源汽车,主要由电机系统、燃料电池系统、储氢系统、整车控制器(VCU)、燃料电池控制器(FC-ECU)、蓄电池、电池管理系统(BMS)等组成,如图1所示。与常规电动汽车类似,燃料电池电动汽车的动力源为电机,整车控制器根据驾驶员需求,控制电机转矩的大小,从而驱动整车运动;与常规电动汽车的不同之处在于,常规电动汽车的能量源为蓄电池,而燃料电池电动汽车为燃料电池或燃料电池和蓄电池的组合。燃料电池以氢气和空气为燃料,在燃料电池堆中通过电化学反应产生电流,通过DC/DC逆变器实现与蓄电池的耦合,共同为电机供电,从而实现整车驱动。燃料电池控制器根据VCU的控制指令,控制输入燃料电池的氢气和空气的流量,从而实现对燃料电池输出电流的控制。
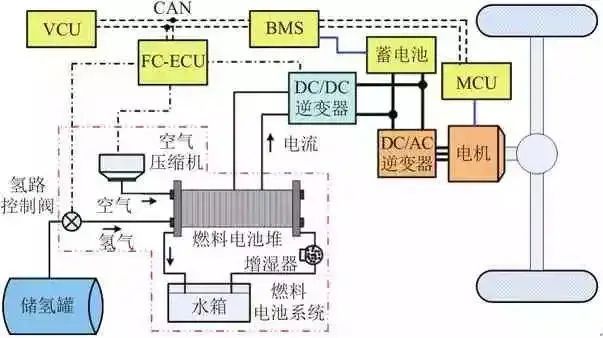
图1 燃料电池电动汽车工作原理
2、燃料电池电动汽车构型设计流程
目前,国内燃料电池电动汽车尚处于研发阶段,相应的关键技术也处于探索阶段,因此,本文基于成熟的传统汽车设计开发流程,提出了如图2所示的燃料电池电动汽车匹配设计流程。
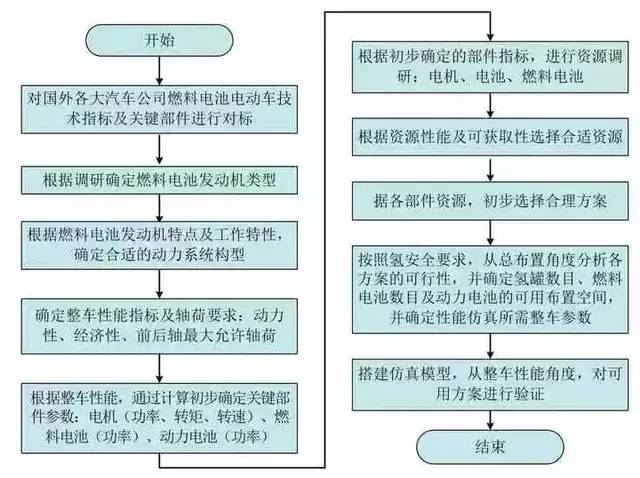
图2 燃料电池电动汽车匹配设计流程
由于目前国内在研发燃料电池电动汽车方面可借鉴的经验较少,所以设计前期的工作步骤如下:(1)针对国外成熟的燃料电池电动汽车开展对标分析,为燃料电池电动汽车的开发提供参考,并确定合适的燃料电池电动汽车动力构型。(2)根据关键总成的技术现状,确定包括动力性、经济性、前后轴最大允许轴荷在内的燃料电池电动汽车的关键指标;基于整车性能指标,通过计算初步确定关键部件参数,并根据相应参数及可用资源选择可用部件;基于选定的电机、电池、燃料电池等部件,进行总布置设计,以确定总布置的合理性,此时需要重点关注储氢系统的布置方案。(3)根据总布置确定的整车参数,通过搭建仿真模型,对整车性能进行验证。
3、燃料电池电动汽车构型方案选择
3.1、燃料电池电动汽车对标分析
根据本研究提出的燃料电池电动汽车设计流程,首先对奔驰、丰田、本田、通用、现代等具备量产能力的燃料电池电动汽车的性能及关键部件进行对标分析,并得出以下对后续开发具有指导意义的结论:(1)燃料电池类型均采用质子交换膜燃料电池(PEMFC)。(2)储氢系统采用高压气态储氢。(3)整车构型均采用电电混合方案。(4)最高车速、续驶里程、冷启动温度等整车性能与传统汽车接近。
3.2、燃料电池选型及特性
根据电解质的不同,燃料电池可分为质子交换膜燃料电池、碱性燃料电池、磷酸燃料电池、熔融碳酸盐燃料电池、固体氧化物燃料电池,其中PEMFC具有启动时间短、比功率高、单位面积功率高、工作效率高、工作温度适合车用等优点,因此,结合对标结果,本研究选用PEMFC。
燃料电池特性是合理使用燃料电池发动机、设计燃料电池电动汽车动力系统构型、开发整车控制系统的基础。与其它能量源相比,PEMFC具有很高的能量密度,而其功率密度却较小,如图3所示。因此,为了获得较长的续驶里程和整车动力性,一般采用与蓄电池耦合的供电方式。

图3 PEMFC特性1
由图4可知,燃料电池的最佳运行区在中负荷区;当负荷较小(轻载区)时,由于空气压缩机等附件的寄生功率较大,所以系统总体效率较低;当负荷较大(重载区)时,虽然净功率密度较大,但所需燃料及空气量较大,其系统效率下降较快,又由于存在浓度损失,所以电压下降较快。同时,燃料电池在重载区工作对其使用寿命影响较大。因此,为了延长燃料电池的使用寿命,需要将燃料电池尽量控制在中负荷区工作。
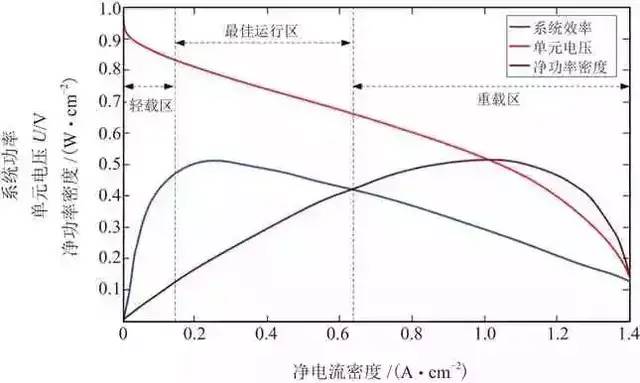
图4 PEMFC特性2
3.3、燃料电池电动汽车动力系统构型方案选择
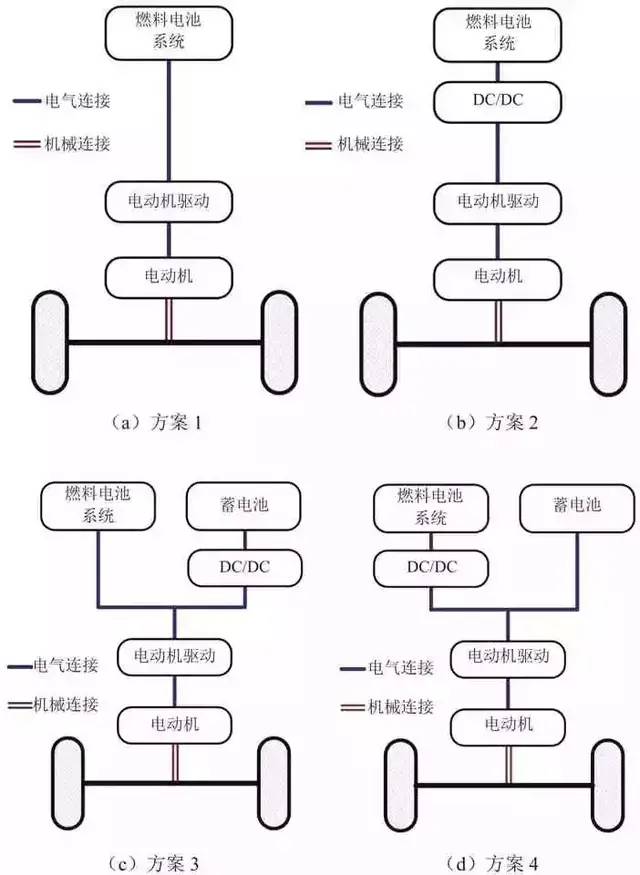
图5 燃料电池电动汽车动力构型可行方案
根据整车供能系统的不同组合,燃料电池电动汽车动力系统目前有4种可行构型,如图5所示。本研究基于图3和图4所示的燃料电池特性,从整车动力性、整车续驶里程、制动能量回收功能、燃料电池寿命、整车启动速度等方面对4种构型进行了对比分析,结果见表1,表中“×”表示缺点,“√”表示优点。
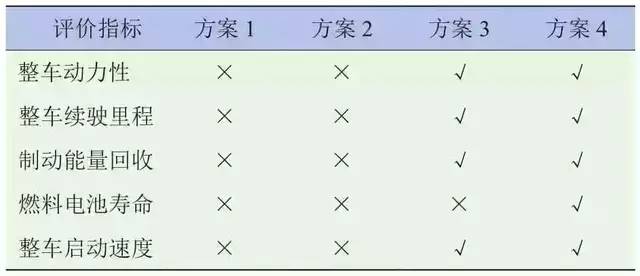
表1 燃料电池电动汽车构型方案对比表
方案1和方案2以燃料电池作为唯一能量源,这需要由燃料电池独自满足整车功率需求,而燃料电池本身功率密度较低,会导致整车动力性弱、燃料电池寿命短、整车启动速度慢等问题,且无法实现制动能量回收功能,整车续驶里程相对较短。方案3以燃料电池和蓄电池作为能量源,通过DC/DC调节蓄电池电压以跟踪燃料电池电压变化,由燃料电池的工作特性可知,其电压随负载变化大,且不稳定,这会导致燃料电池寿命较短。方案4也以燃料电池和蓄电池作为能量源,通过DC/DC调节燃料电池发动机输出电压,以跟踪蓄电池电压,通过燃料电池与蓄电池的组合共同满足整车功率需求,因此,整车启动速度快、动力性强,可实现制动能量回收功能,续驶里程长,燃料电池可稳定工作在中负荷区域,燃料电池寿命长,同时该方案可减少燃料电池需求功率,从而降低整车成本,更易实现商业化。因此,本研究选用方案4。
4、燃料电池电动汽车参数匹配
根据图2所示的燃料电池电动汽车匹配设计流程,明确燃料电池电动汽车构型后,需要根据表2所示的整车性能指标完成关键总成参数匹配,并根据总成资源确定关键总成。
4.1、燃料电池电动汽车动力系统参数匹配
燃料电池电动汽车只有一个动力源,因此,其动力系统参数的匹配主要是确定动力电机的参数,以便选择合适的电机。相关参数包括峰值功率、额定功率、峰值转矩、额定转矩、最高转速等,确定方法如下。
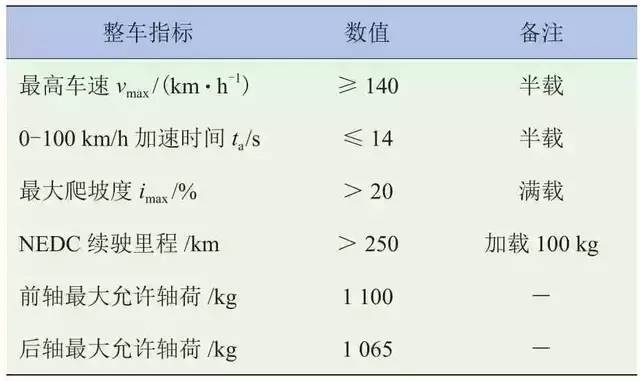
表2 燃料电池电动汽车整车性能指标
4.1.1、电机峰值功率
电机峰值功率由最高车速、最大爬坡度、百公里加速时间确定。
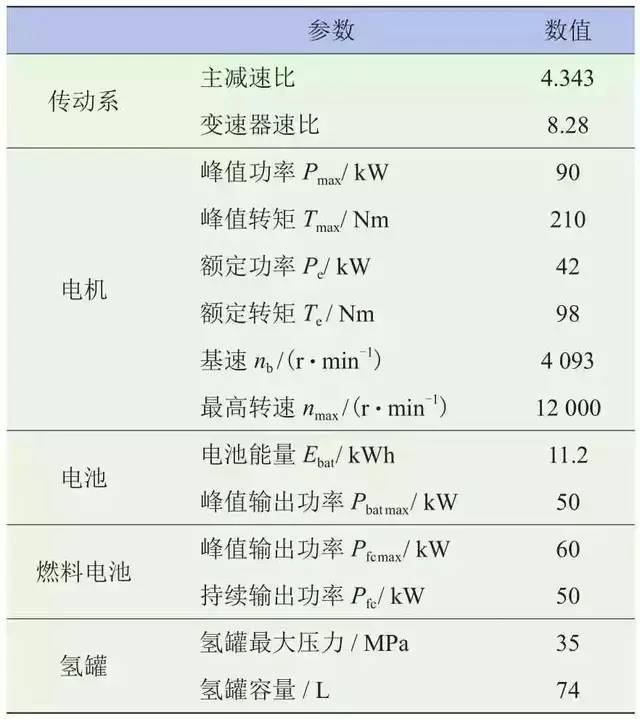
式中:Pmax1为根据最高车速确定的电机峰值功率,kW;Pmax2为根据最大爬坡度确定的电机峰值功率,kW;Pmax3为根据百公里加速时间确定的电机峰值功率,kW;uamax为最高车速,m/s;η为整车传动系传动效率;M为整车质量,kg;g为重力加速度,9.8 m/s2;f为路面滚动阻力系数;CD为空气阻力系数;A为整车迎风面积,m2;ρ为空气密度,1.225 8 N·s2/m4;ur为汽车与空气的相对速度,m/s;α为坡度,(°);ua为爬坡车速,m/s;δ为旋转质量换算系数;ta为百公里加速时间,s;Vb为电机基速对应的车速,m/s;Vf为加速终止的车速,m/s。
4.1.2、电机额定功率
电机额定功率由最高车速确定:

式中:Pe为电机额定功率,kW。
4.1.3、电机最高转速

式中:nmax为电机最高转速,r/min;ig变速器速比;i0为主减速器减速比;r为轮胎滚动半径,m。
4.1.4、电机峰值转矩

式中:Tmax为电机峰值转矩,Nm。
4.1.5、电机的额定转速和转矩
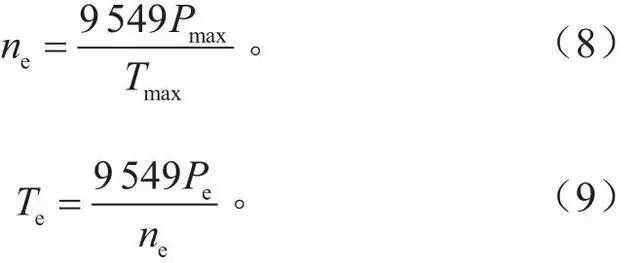
式中:ne为电机的额定转速,r/min;Te为电机的额定转矩,Nm;Pe为额定功率,kW。
4.2、能量系统参数
能量系统匹配是燃料电池电动汽车匹配的关键,包括燃料电池功率、动力电池功率和容量的确定。
4.2.1、燃料电池功率
燃料电池功率需要在考虑总成资源的前提下,根据最高车速确定。

式中:Pfc为燃料电池的输出功率,kW。
4.2.2、动力电池功率和容量
动力电池功率根据电机峰值功率和燃料电池功率的差值确定。

式中:i为余量系数。
动力电池最小容量由坡路起步工况和百公里加速所需能量确定,考虑到增大电池容量可减小燃料电池在重载区工作的比率,因此在总布置空间允许的前提下,要尽可能地增大动力电池容量。
4.3、储氢系统参数
就燃料电池电动汽车而言,如何将燃料供给车载燃料电池是其主要难题。至今,有3种车载储氢方法:在环境温度下,高压储存压缩氢;低温液氢储存;金属氢化物储存法。本文选择适于车用的高压储氢方法,储氢罐体积可由下式求得[12]:

式中:V为储氢容器容积,m3;P为储氢压力,Pa;EH为所需能量,kJ;R为气体常数;T为绝对温度,K;WH为氢的分子量;HV为氢的热值,MJ/kg。
4.4 关键总成参数匹配结果
基于上述关键总成的匹配方法及国内关键总成的资源情况,选择相应总成的参数见表3。
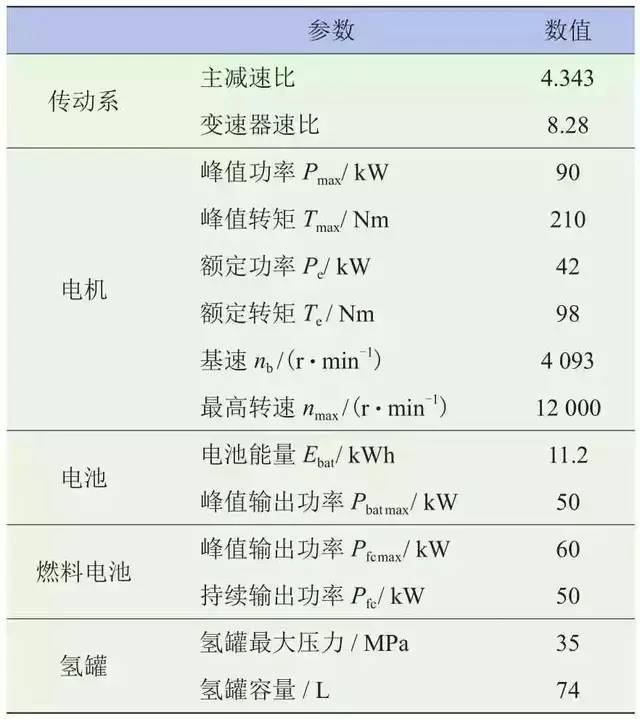
表3 燃料电池电动汽车关键总成参数表
5、燃料电池电动汽车匹配开发可行性验证
燃料电池电动汽车匹配开发可行性主要从总布置和整车性能两个方面进行验证。
5.1、燃料电池电动汽车总布置验证
在完成关键部件选型后,需要进一步从整车总布置方面对整车布置可行性进行验证。本研究选择将燃料电池堆、锂电池等高压电源零部件布置于底盘下面,这样可以与氢气区分开,同时降低非专业人员的触电危险。此外,燃料电池电动汽车与传统汽车及常规电动汽车不同,需要从安全角度考虑储氢装置和供氢管路的布置。主要遵循以下几个原则:(1)氢管路要避开蓄电池及热源(至少保持200 mm的距离)。(2)储氢罐和管路不应装在行李舱、乘客舱或其它通风不良的地方,否则必须设计通风管路或采取其它措施。(3)储氢容器及附件的安装位置距车辆边缘至少100 mm。(4)燃料电池应尽量远离运动部件(至少保持200 mm的距离)。本研究基于上述设计原则及传统汽车布置原则,对燃料电池电动汽车在总布置方面进行了验证。
燃料电池电动汽车底盘总布置图,如图6所示。整车前部布置电机、逆变器、传动系等总成,整车中部地板下方布置燃料电池和动力电池,整车后部布置氢罐,各部件布置满足氢安全原则,符合布置要求。燃料电池电动汽车的氢罐布置图和发动机舱布置图,如图7和图8所示。
根据整车总布置得到燃料电池电动汽车的整车参数(表4),相关参数是整车性能仿真验证的基础。
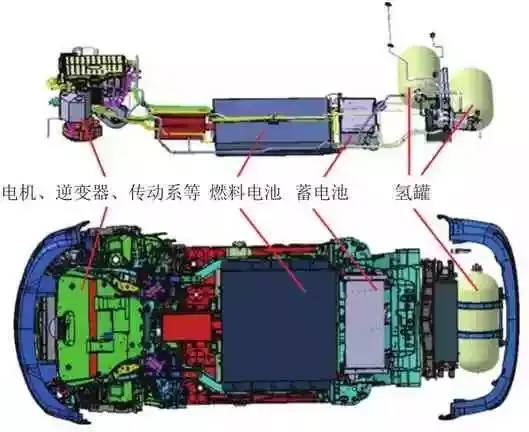
图6 燃料电池电动汽车底盘总布置图

图7 燃料电池电动汽车氢罐布置图
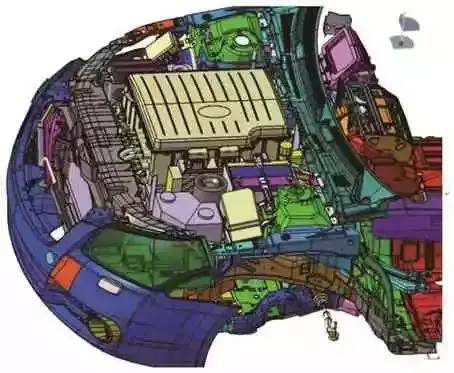
图8 燃料电池电动汽车发动机舱布置图
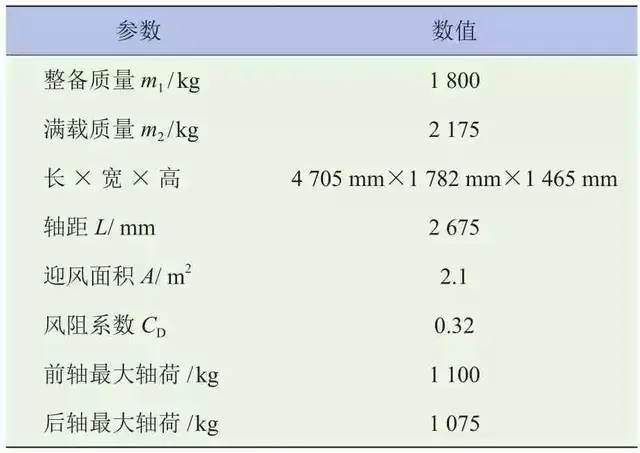
表4 燃料电池电动汽车整车参数
5.2、燃料电池电动汽车整车性能验证
在燃料电池电动汽车总布置完成后,整车装配完成之前,为保证开发的可行性,需要通过性能仿真对整车性能进行验证。因此,本研究搭建了如图9所示的包括循环工况、驾驶员模型、VCU模型、电机模型、传动系模型、车辆模型、DC-DC模型、燃料电池模型、电池模型等在内的燃料电池电动汽车仿真模型。图中,Vgk为工况车速,V为实际车速,ΔV为工况车速与实际车速的差值,αb为制动踏板开度,αd为油门踏板开度,Tbtar为目标液压制动力矩,Tb为实际液压制动力矩,Pm为电机功率,Lmot为电机负荷率,Tm为电机转矩,Td为传动系输出转矩,Pfcdem为燃料电池需求功率,Pfc为燃料电池输出功率,Pacc为电动附件消耗功率,Pbat为电池功率,SOC为电池荷电状态,U为蓄电池电压。
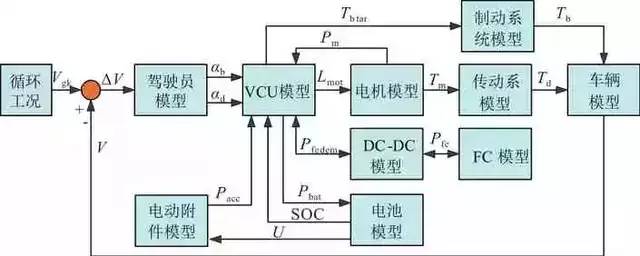
图9 燃料电池电动汽车性能仿真模型原理图
燃料电池电动汽车的能量管理策略是整车控制策略的核心,本研究基于燃料电池特性和选用构型制定了如图10所示的整车能量管理策略。图中,αb为制动踏板开度,αd为油门踏板开度,αbmin为判断驾驶员是否踩下制动踏板的踏板开度下限值,V为车速,Vbmin为允许制动能量回收的车速门限(标定值),SOCmax为允许制动能量回收的SOC门限(标定值),k1、k2、k3、k4为标定系数,Pfc为燃料电池输出功率,Pbat为电池输出功率,Pd为整车需求驱动功率,kb为制动能量回收强度标定系数,αdmin为判断驾驶员踩下油门踏板的踏板开度门限(标定值),Pfc_rate为燃料电池输出的额定功率,SOCmin为允许蓄电池输出电能的SOC下限值(标定值),Pbat_max1为在相应SOC状态下电池能够输出的最大功率,V1为滑行状态下进入充电模式时的车速门限值,Pbat_charge为蓄电池充电功率。
基于上述模型和能量管理策略对整车性能进行了仿真验证,结果见表5。由表5可知,整车性能能够达到相应的目标要求。
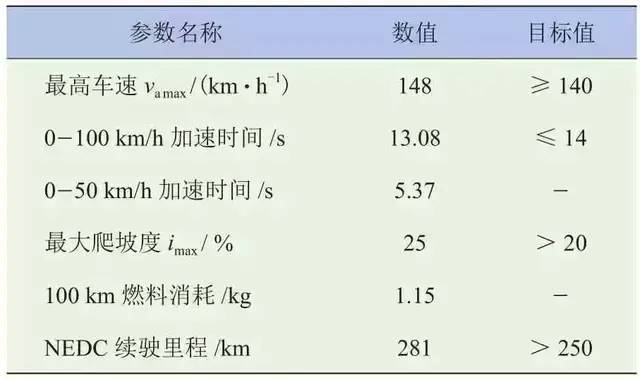
表5 燃料电池电动汽车整车性能
6、结论
本文针对国内外燃料电池电动汽车的研究现状,提出了燃料电池电动汽车匹配设计开发流程,并从匹配、设计、验证的角度开展了系统研究。
(1)基于国内燃料电池电动汽车研发现状和成熟的传统汽车开发流程,提出了考虑总成资源、总布置方案和性能仿真的燃料电池电动汽车匹配设计流程。
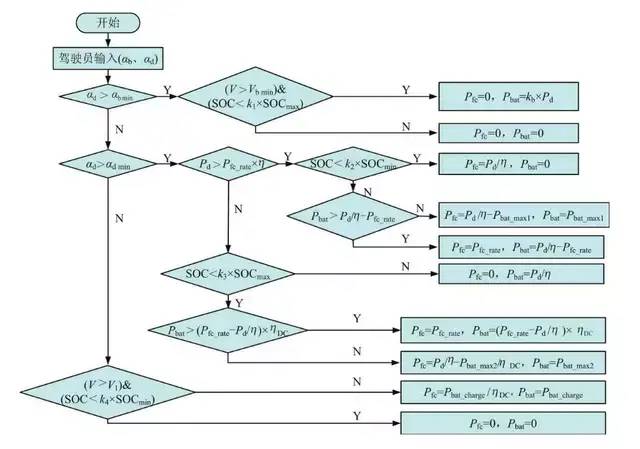
图10 燃料电池电动汽车能量管理策略
(2)基于燃料电池特性,对4种构型方案进行了对比分析,以某B级燃料电池电动汽车为研究对象,提出了匹配方法,并结合国内资源情况确定了关键总成。
(3)从整车总布置和整车性能角度出发,对燃料电池电动汽车可行性进行了验证。
编辑推荐
最新资讯
-
自动驾驶卡车创企Kodiak 将通过SPAC方式上
2025-04-19 20:36
-
编队行驶卡车仍在奔跑
2025-04-19 20:29
-
全国汽车标准化技术委员会汽车节能分技术委
2025-04-18 17:34
-
我国联合牵头由DC/DC变换器供电的低压电气
2025-04-18 17:33
-
中国汽研牵头的首个ITU-T国际标准正式立项
2025-04-18 17:32