新能源电池系统设计——BDU设计
首先我们理解概念:什么是BDU,BDU即Battery Distribution Unit;也就是电池包断路单元。
①电池系统为何需要BDU ,BDU作用?
②BDU设计主要考虑哪些因素,构成?
③目前行业的BDU电气原理设计是那样,BDU产品主要包些电器件?
④随着兆瓦及充电,BDU的设计方向?
①:首先我们来看电池系统为何需要BDU,我们都知道在新能源电动汽车中,电池系统是整车能源系统,那么电池系统也就充当着整车能量吐纳的机构。需要进行能量的吞吐那就需要电力分配单元(PDU),在这里我们就单论安装在电池系统里面的电力分配单元(BDU)用以控制电池系统的充放电系统平稳的进行。如图是一个简单的整车高压拓扑,图中除了电池、电控电机,其他部分就是BUD里面电器件。早期的的FUSE,是内置于MSD中,也就是为什么需要串联在电池组中间的原因(断开的时候将电池系统电压减半,安全考虑,目前由于成本等一些因素逐渐去掉MSD,FUSE直接集成于BDU内部) 可以看出BDU主要集成了电流传感器、主继电器、预充继电器、预充电阻等一些电器件。当然不同需求集成的电器件也不同,功能也会随之增加。
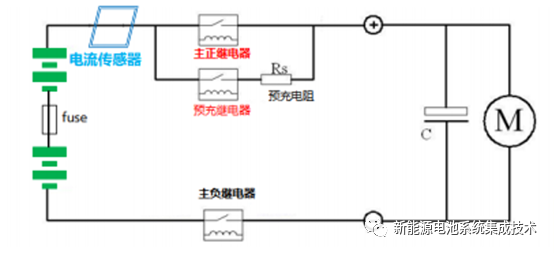
②:BDU设计需要考虑哪些因素:大体分为(机械、电气、热、磁)。首先我们要知道BDU就是一个电力分配单元,也就是他的作用是能够在系统需要断开/闭合的时刻能够断开/闭合。所以我们需要考虑整个系统/整车工况的参数:系统的额定/峰值电压,持续充放电电流,快充电流(系统快充MAP图表);峰值放电电流(整车放电需求工况电流曲线)以及我们还需要知道整车X电容(电机控制器电容值)用来计算预充电阻的选型。当然在这里,我们需求的一些参数可能会是以功率数值的情况输入给我们的。这里我们就需要考虑整车的功率分配需求,整车存在前、后电机功率输出需求;空调功率(制热/制冷功率)需求;电池系统加热功率需求;以及其他娱乐影音系统的功率需求等。如果这些都存在,我们在考虑电池系统放电工况的时候我们需要考虑这些工况,哪些是同时存在的,那么功率需求就需要累积。当然在电池充电的时候,我们也需要对电池系统充电能力的工况评估,得到充电MAP。这些只是我们针对BDU电器件的选型需求,当然我们设计BDU这一产品的同时是基于电池系统/整车平台考虑的,我们还需要考虑系统电压给我们电气设计带来的电气间隙、爬电距离;系统充放电流情况下给BDU电器件、电连接带来的散热;以及电流磁效应带来的干扰等。当然我们这些都是基于电气,热,磁方面考虑,所以还需要考虑整个BDU产品系统集成的机械性能(震动、碰撞等),结构如何设计。
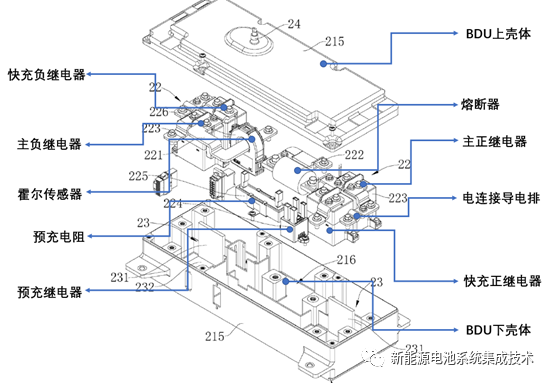
③:目前行业的BDU电气设计原理,思路。总体上常规方案就是基本分为两种模式,这里我们只聊放置在电池系统内部的。一种是快充接触器和主接触器并联的,一种是快充接触器和主接触器串联的形式。当然还有就是快充接触器和主接触器共用一个的情况(OEM省成本)。这里我们只聊前两种。
串联形式的电气原理,这种方案,目前来说是应用的比较多的,图中我们可以看出串联形式在需要快充的时候主接触器和快充接触器是都需要闭合才可以的。另一方面在整车没有PDU的时候,在整车快充的时候,电池系统的放电母线是直接通到电控上的。也就是电控是带电的。但是并不处于驱动模式。并联形式下,充电、放电系统是相互独立的。也就是说充电和放电在某种意义上是互不干涉的。这两种形式的对比,可能会想到串联形式情况下充电需要闭合前后四个接触器,而并联形式只需要闭合两个。前者的安全性是不是更佳,其实从整个系统级别考虑这两种形式的安全性都是满足要求的。这两种方案仅仅是整车架构原理需求不同决定的,当然这个高压架构的不同最终是取决于OEM在开发整车平台时的一个功能逻辑策略,不同的策略,对应的架构截然不同。举个例子:串联形式的快充策略是建立在上电策略之上的,然而并联形式的快充策略是独立的,在策略开发的过程中,需要单独建立一个模块,所考虑的工况情景也就更多。
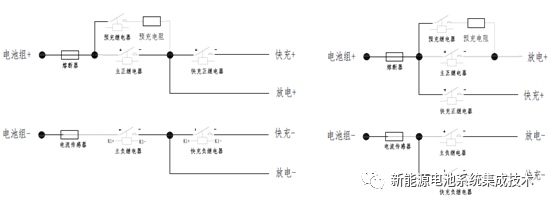
④:伴随着兆瓦级别的充电,电池系统BDU的设计方向在哪?针对这个问题,这里只聊聊大电流给系统系统级别带来的痛点在哪?随着目前整车需求的快充需求,电池系统的充电速率越来越高,随之而来的是充电电流的加大,现在普遍的250A,300A快充,也存在一些400A,600A的快充需求,达到这个级别的电流对整个系统的电连接都是一个较大的考验。一方面的系统的电压升到800V平台,一方面电流需求也在不断升高。回归到电气设计上就是电气间隙、爬电距离、各种电气件的耐压、大电流带来的电器件温升过高,整个电气产品随着温升升高的耐久是否值得我们考虑?当然还有电压平台升高、额定电流的增大对电气件的选型也需要选到更高级别,这也就带来更高成本的投入;电器件的体积的也会随之更大,整个系统的断路工况下接触器和传统熔断器的配合也会随之变难,甚至基本无法完美配合;被迫的只能选择智能熔断器。这对于整个电池系统来说是很难受的。(一方面成本急剧升高,一方面电池系统的空间寸土寸金,除了电芯其他东西都是在Pack的夹缝求生存)。所以基于这么一些原因,我们就考虑如何才能避免成本,空间给我们带来压力,那就是设计一种可以既可以过大电流的BDU,它的发热还比较小,选用的电器件还可以小于电流工况下的电器。这就需要设计冷却系统对BDU的发热件进行冷却。那么液冷BDU需要如何设计?如何考虑整个系统的方案?基于什么系统用什么样的冷却方案?
下一期我们聊一聊BDU冷却的方案。
本文由新能源电池系统集成技术原创,作者:南山拾壹
编辑推荐
最新资讯
-
推荐性国家标准《乘/商用车电子机械制动卡
2025-04-30 11:13
-
载荷分解
2025-04-30 10:46
-
布雷博在上海开设亚洲首个灵感实验室
2025-04-30 10:25
-
组分性能对锂离子电池卷芯挤压力学响应的影
2025-04-30 09:00
-
美国发布自动驾驶新框架,放宽报告要求+扩
2025-04-30 08:59