基于振动的疲劳失效分析
在上篇文章《管道振动的诊断和解决方案 - Part I》中,我们提到管道的机械振动会造成疲劳失效问题。那接下来一个很重要的问题就是,如何评估管道由于振动引起的疲劳失效问题。在这篇文章中我们将探讨这个问题。
01、疲劳强度评估的基本原理
首先,我们需要简要地介绍一下疲劳强度的基本原理。在1830年,人们已经认识到一个相对于一般机械强度,较低往复式的应力同样可以造成金属的断裂。随后,标称应力法(S-N curve)应运而生。这种方法主要是为了理解动态应力与出现金属断裂的时间的关系。一个典型对于金属的S-N曲线如下图所示:
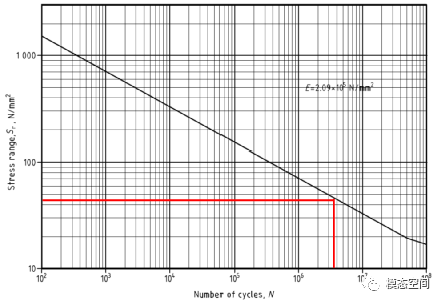
对于S-N曲线,它的横坐标是金属元件加载周期性往复力的次数,纵坐标是相应的极限疲劳波峰-波峰应力范围(peak-to-peak range)。对于特定的往复力次数,当此元件的最大疲劳应力范围大于S-N上所示的极限应力的数值时,这个元件就有极高的风险出现疲劳失效。
对于任何机械元件,一般都有设计的使用寿命。我们假设这个使用寿命是 年;与此同时,假设这台机器每天24个小时不停地运转,那么这个元件设计的最大往复力加载的次数为:
其中 是这个周期往复力的频率。值得注意的是,这个S-N曲线法仅仅适用于高周疲劳(high cycle fatigue)的情况。也就是说,金属元件始终是处于弹性形变的状态。对于低周疲劳(low cycle fatigue)的情况,由于塑性变形(plastic deformation)对于整体的疲劳失效有很大的贡献,所以说,应该使用基于应变的疲劳失效理论。
对于管道的振动问题,它往往和管道的固有频率有关。可以看到,管道的固有频率往往都是在100Hz以上。也就是说,机械振动所造成的位移都是相对较小的。因此,振动所造成的动态应变往往还是在材料的弹性区间以内。所以,高周疲劳还是通常比较普适的。因此,在接下来的文章中,我们主要讨论如何使用S-N曲线来判断管道的疲劳失效。
除了上述所述的动态应力对于材料疲劳特性的影响外,另一个重要的因素是管道内的压力所造成的静态应力(mean stress)。在1899年时,Goodman做了一系列的实验,最终拟合出了一条直线。这条直线也被称为Goodman曲线(如下图所示)。
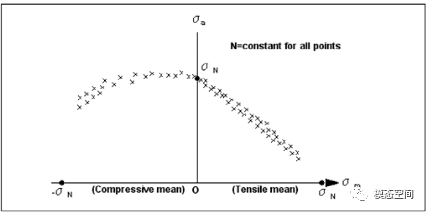
从这条Goodman曲线中,我们可以看到,随着静态应力的增加,疲劳应力极限会相应降低。根据这条Goodman曲线,我们可以使用下面这个式子判断金属元件是否会疲劳失效:
σσσσω
其中 σ 是静态应力, σ 是材料的极限拉应力, σ 是材料所受到的最大往复应力范围, σω 是材料的疲劳应力极限, 是安全系数。当上面这个表达式成立时,金属元件在很大概率上不会有疲劳失效问题。值得注意的是,对于金属元件不同的设计寿命,我们将会使用不同的最大疲劳应力极限( σω )。
02、常见金属的疲劳S-N曲线
通常情况下,疲劳强度极限值都是通过材料测试来确定的。传统上而言,我们一般认为,对于低碳钢和铸铁材料,当试件循环加载107次后,疲劳测试强度将不会继续下降(如下图所示)。而对于铝合金材料,疲劳强度会随着加载次数的增加而继续下降。最新的实验数据表明,即使对于很多的低碳钢和铸铁试样,甚至在加载108后,疲劳强度还是依然会随着加载次数的增加而下降。这可能是由于在切削加工或者是焊接时,对材料内部产生了微裂纹(micro-cracks)。感兴趣的读者可以阅读Bathias等所著的论文【1】。
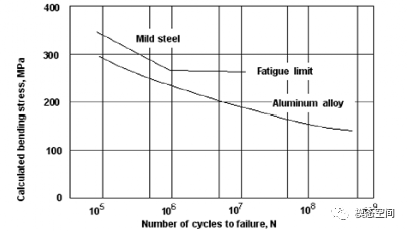
不过对于工程应用而言,我们依旧使用经典假设,即当一个材料在经历107加载后不会产生疲劳失效,就认为它不会产生疲劳失效问题。对照不同材料的疲劳强度极限,在不同的标准中,都会有相应的计算方法。感兴趣的读者可以去阅读英国标准BS7608(PD5500)或者是美国标准 ASME code Section III。
03、管道的疲劳分析
对于一个典型的管道疲劳分析,最简单的方式就是使用应变片来直接测量静态与动态应力。但在实际工程上,这种方法还是存在一定的缺陷,下面让我们看一个实际的管道案例。下图显示了一台工程机械内的管道系统。从下图中,我们可以看到这根管道是由不同的次级管道焊接而成的。
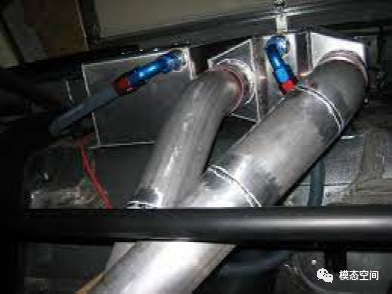
对于疲劳失效,它往往更容易出现在焊接点附近,主要原因是:在焊接过程中,焊接点周边的金属将承受更高的温度,这些高温会在金属内部造成许多微裂纹(micro-cracks),从而造成更低的疲劳强度。遗憾的是,这些微裂纹的分布在同一焊接平面内并不是均匀的。也就是说,较低的疲劳强度可能出现在管道焊接截面上的任意位置。
回到我们所说的应变片应力测试的问题,可以看到,在焊接管道的截面上,焊接的质量也不一定完全一致。由于这个原因,在不同位置所能测到的应力集中系数(stress concentration factor)也会有所不同。在这种情况下,就很难判断在哪个位置需要贴应变片来测试应力。
其次,我们可以看到,由于应力集中的原因,在接近焊趾的金属位置,它所受到的应力将远远高于远离焊趾的位置,并且,应力测试距离与最大应力的关系是一条类似于双曲线的关系。
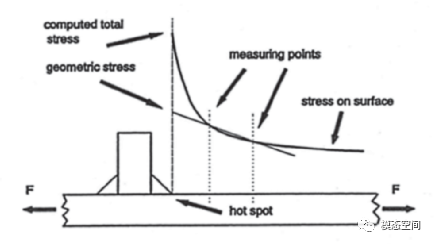
对于一般的应变片而言,它有一定的尺寸。我们所测到的应力值是在应变片所粘贴的面积上的平均应力。也就是说,在焊趾附近贴上的一个应变片所测试到的平均应力很有可能比实际上的最大应力值(hot-spot stress)更低,从而导致我们低估了这个金属元件的最大动态应力。
还有一个更重要的原因是难以决定应变片粘贴的位置。由于工程上使用的管道普遍是三维的,我们很难预测最大的振动出现在哪个方向上,所以最大应力在管道截面上出现的位置也往往难以确定。如果我们只进行应变测试,需要粘贴许多应变片。而应变片测试往往相对比较复杂,特别是应变片的电气绝缘较难实现。所以,通常对于应变片会获得更高的背景噪声。更麻烦的是,对于高频振动,结构所受的应变往往相对较小,一般应变片的信噪比并不足以获得可靠的应力数值,所以,应变测试一般不是一个很容易且方便快速的选择。
相对而言,使用加速度计进行的振动测试往往十分便捷可靠迅速。除此之外,我们可以看到,在很多状况下,振动的数值直接与机械应力呈正比。所以往往可以使用管道最大的振动值来进行疲劳失效的筛查方法。在下一小节,我们将介绍一种基于振动速度的简化方法来判断管道疲劳失效的可能性。
04、基于振动管道疲劳失效筛选方法
为了建立管道的最大速度与最大动应力(dynamic stress)的关系,我们需要判断管道的振型(mode shape)。基于振型,可以推导出管道弯曲的曲率(curvature),通过这个曲率我们可以推导在边界条件处(boundary condition)的最大应力。不过这个过程需要相对复杂的数学建模,一般不利于工程应用。在下一篇文章中,我们将会详细介绍。在这一小节,我们仅仅介绍一种工程上常用的方法,这个方法是基于德国国家标准VDI3842 [2]。
下图是在VDI3842第7.2.3节提供的一种基于最大RMS振动速度的判断准则。
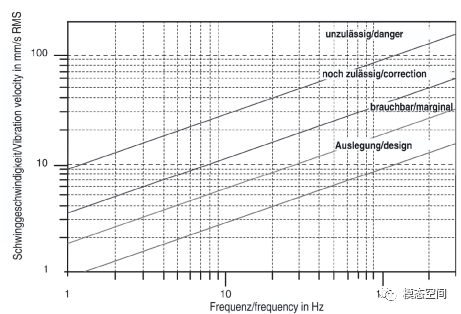
值得注意的是,这个标准中的曲线只能适用于初步的分析。原因有二:(1)这个图仅仅适用于300Hz以下的振动,对于很多应用而言,振动频率远远高于300Hz,它将不再适用;(2)这个振动的标准是基于石化行业经验而来的,也就是说,它只适用于管径和管道支撑间隔,类似于石化行业的管道,对于很多应用它并不适用。所以,我们需要使用其他的方法来将管道振动转化为最大的应力。由于这个原因,VDI标准也提供了另外一种方法来完成这个转换。在这个方法中,确定最大应力的近似公式是:
σθμ
其中各个参数的定义如下所示:
-
是对于管道中存在离散的质量(Discrete mass)的修正系数
-
是对于管道的形状的修正系数
-
θ 是对于管道振型的修正系数
-
是测量到的最大的振动速度
-
是材料的弹性模量
-
µ 是单位长度的管道质量
-
是转动惯量
首先,我们可以来看一下质量修正系数 。在通常的管道系统中,由于我们会使用法兰来对两段不同的管道进行连接。法兰盘的质量往往会高于管道的质量,所以这就会造成在管道系统中出现一些集中质量。这些集中质量对于最大应力的影响可以使用fM来修正。在这个标准中,它提供了典型结构的集中质量修正系数:
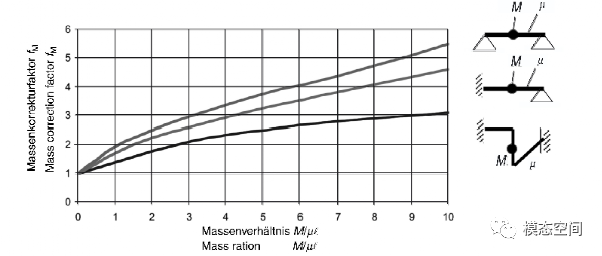
其次,我们来讨论下对于管道结构的修正系数 ;例如,如果管道上存在一些常见的部件时,它对于管道弯曲的曲率影响补偿系数。
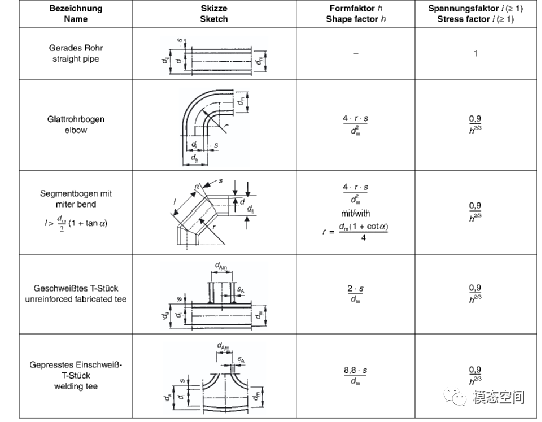
再次,我们来讨论管道振型 θ 的补偿系数。通过基本的振动理论,可以很容易得知,振动所造成的位移比系统的静态位移往往可以放大很多倍。从本节最开始所提出的公式来看,我们所计算的最大应力还是基于简支梁或者悬臂梁的第一阶振型所做的分析。所以,对于其他边界条件,振动模态振型就必须进行相应的修正。下面的表格中就列出一些常见的结构的模态修正系数。值得注意的是,所有这些结构的模态修正系数都是基于这些结构的第一阶弯曲振动。对于高阶振动,这些修正系数将会造成一定程度的误差。
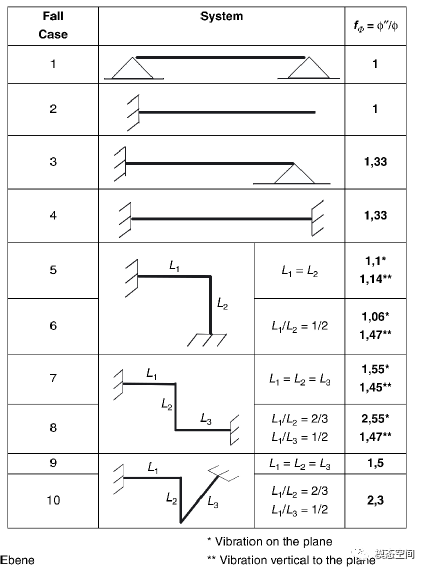
可以看到,以上这些修正都是基于一系列很有限的结构。比如说,对于集中质量的修正,它只提供了三种不同边界条件,并且,集中质量的位置对于模态也会有影响,这些影响并没有考虑到这个修正系数中。同样地,对于模态振型的修正,也存在同样的问题。对于实际的管道系统,它远远比我们看到的例子复杂,如果仅仅使用上表中的结构,只能寻找最为类似的结构。在这种情况下,会引入更多的误差,最终造成对于管道结构的过度设计。由于这些问题,我们需要引入更复杂的方法(Rayleigh-Ritz法或者有限元的方法)来进行设计。在下一篇文章中,我们首先会用一些简单的结构来验证这个VDI的方法,之后会简要介绍Rayleigh-Ritz法来求解结构的振型,随后,这些振型将用来求解最大应力。最后,我们将用一个实际的例子来解释如何使用这种方法来评估管道结构的疲劳。
参考:
[1] Bathias C, Drouillac L, Le Francois P. How and why the fatigue S–N curve does not approach a horizontal asymptote[J]. International journal of fatigue, 2001, 23: 143-151.
[2] VDI (2004). VDI 3842:2004-6 Vibrations in piping systems, Verein Deutscher Ingenieure, Düsseldorf, 87
作者简介
Dr Ning Tang,谢菲尔德大学博士,博士后。现在混迹在欧洲某工程机械公司,主要从事振动和噪声的被动控制。学术研究方向为非线性调谐质量块阻尼器的设计,非线性材料的阻尼研究,橡胶材料动态特性的研究以及转动叶片的振动监测。私人微信为mep10nt,同时运营的公众号为:Rayleigh的追随者。
最新资讯
-
中汽中心工程院能量流测试设备上线全新专家
2025-04-03 08:46
-
上新|AutoHawk Extreme 横空出世-新一代实
2025-04-03 08:42
-
「智能座椅」东风日产N7为何敢称“百万级大
2025-04-03 08:31
-
基于加速度计补偿的俯仰角和路面坡度角估计
2025-04-03 08:30
-
《北京市自动驾驶汽车条例》正式实施 L3级
2025-04-02 20:23