电驱减速器啸叫噪声问题分析与优化
来源: 白学斌 金子嵛 于博瑞、中国一汽车集团
以某单电机电驱系统减速器为研究对象,针对整车NVH试验评价中减速器啸叫问题进行专项分析和优化,通过建立精确的减速器总成动力学性能分析虚拟样机模型,对齿轮啮合振动激励机理、传动路径和振动响应等进行详细分析,根据台架试验和整车试验结果标定虚拟样机模型,通过齿轮宏观参数及微观修形优化对齿轮加工误差、传递误差、啮合刚度和动态啮合力进行专项优化和控制;同时通过对零部件及系统的模态及振动响应分析,分析传递路径及系统响应结果,预测振动噪声风险,通过传递路径刚度及激励频率优化,降低系统振动响应和噪声风险;最后通过整车NVH性能试验验证改进效果。通过以上手段,显著降低了减速器的啸叫噪声,最终达成整车NVH性能要求。
1 前言
随着纯电动汽车的日益发展和消费者对整车乘坐舒适性要求的提高,减速器作为电动汽车主要的噪声源,通过对其进行严苛的噪声控制成为整车声品质提升的关键因素之一。减速器噪声主要包括啸叫噪声和敲击噪声,对于单挡减速器,啸叫噪声是其主要的噪声表现形式,啸叫噪声是由内部齿轮在啮合传动中所产生的振动激励引起的一种中高频噪声,这是一种很容易被人耳识别的中高频纯音,用户抱怨度比较高,必须降低或者消除。相比于传统燃油车,电动汽车中发动机总成“掩蔽效应”消失,背景噪声更小[1],这就对减速器的噪声控制提出了更高的要求和挑战。
本文以某电动汽车的单挡减速器为研究对象,针对减速器的啸叫噪声,分析啸叫噪声的产生机理和相关因素,并提出一种基于齿轮参数、振动激励、传递路径和系统响应的综合优化设计方法,以改善啸叫问题,为在减速器产品开发中,啸叫问题的正向开发控制提供一种方法。
2 问题描述
本文研究的减速器为二级三轴式结构,在整车NVH主观评价试验时,发现在30 km/h~50 km/h(输入转速2 300 r/min~3 200 r/min、30%×电机输入最大扭矩)和90 km/h~110 km/h(输入转速6 350 r/min~7 500 r/min、70%x×输入最大扭矩)两个加速段,车内能明显感受到啸叫噪声,通过客观测试识别到22阶次噪声明显,超出客观评价最大值5 dB,22阶次为减速器一级齿轮阶次,减速器一级阶次噪声不达标。
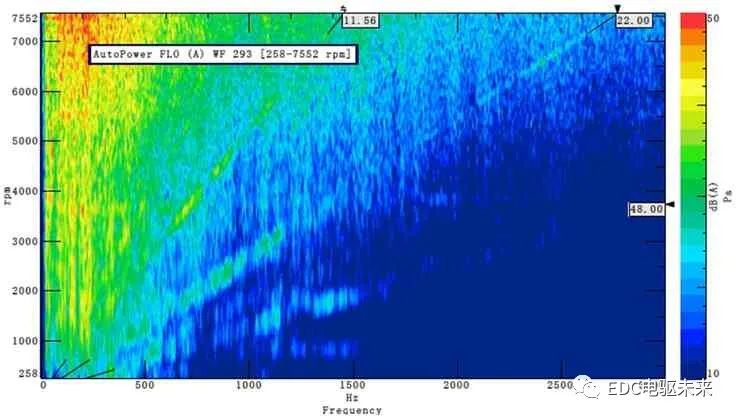
图1 加速噪声客观测试结果
Fig.1 Objective test results of accelerated noise
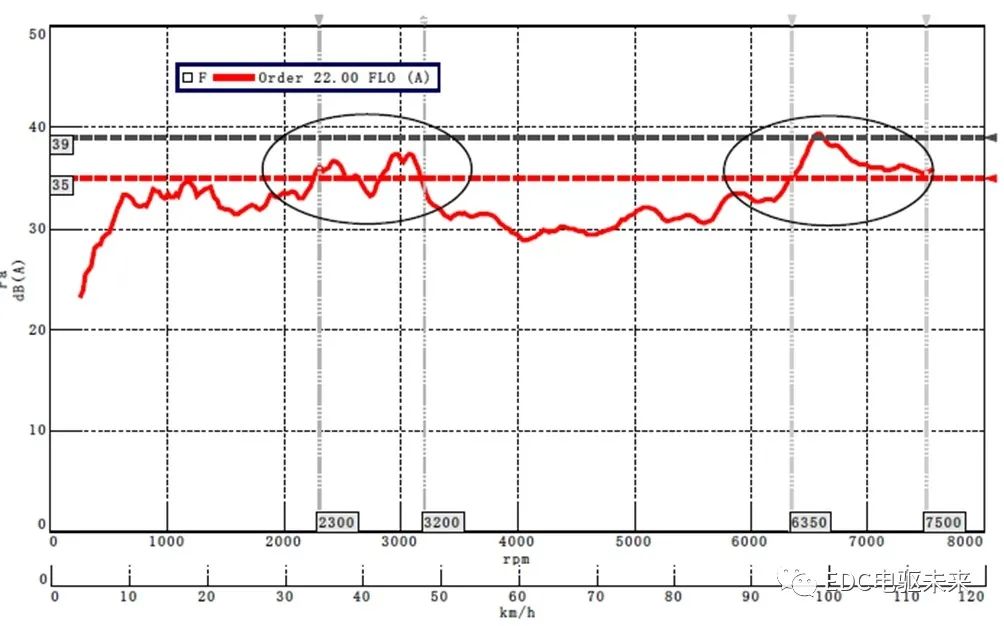
图2 22阶次噪声曲线
Fig.2 22 order noise curve
3 问题分析
3.1 啸叫机理分析
减速器啸叫噪声是齿轮箱弹性系统在动态激励载荷作用下产生的刚柔耦合响应。齿轮啸叫噪声是一种动态啮合力激励产生的稳态噪声,由于齿轮啮合过程中啮合刚度的不断变化引起传递误差的波动,它作为一种动态激励源直接导致齿轮受载接触应力的波动,这种接触应力的波动激起内部结构振动,振动再通过轴、轴承、减速器壳体、悬置和车身等零部件传递到车内。减速器啸叫噪声具有明显的阶次特征,与齿轮的齿数相关,在中高频率较高转速范围内都可能出现。当减速器的壳体模态频率和齿轮的激励频率相同时会发生共振,啸叫噪声表现更明显[7]。
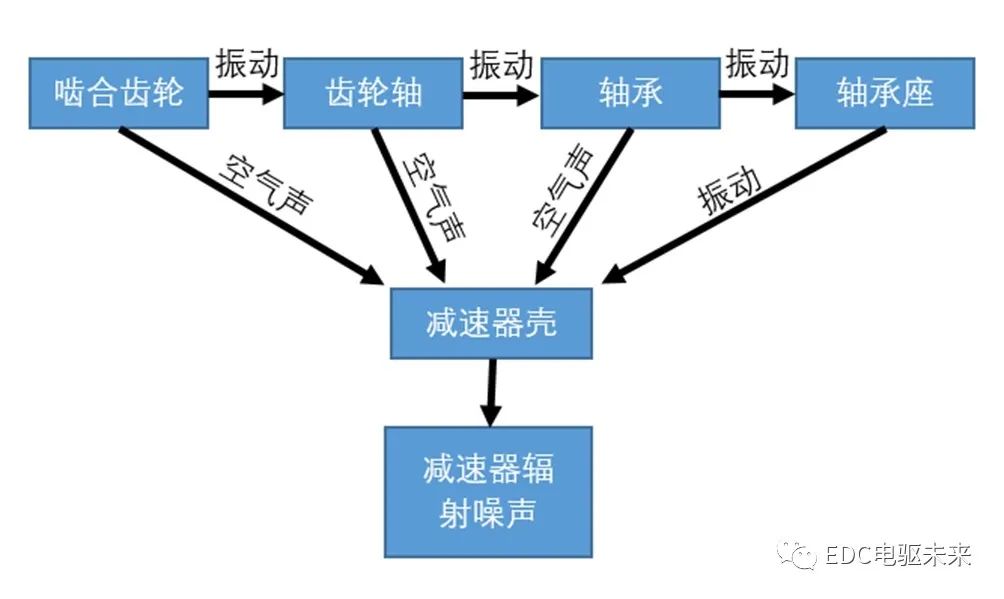
图3 噪声传递路径
Fig.3 Noise transfer path
影响减速器啸叫噪声的因素主要包括振动激励源、传动路径和系统响应三个面。
振动激励源方面:主要包含影响齿轮动态啮合性能的关键因素,包括齿轮宏观参数、微观修形参数、接触应力分布、传递误差、啮合刚度、啮合刚度和制造安装误差等。
传递路径方面:包括齿轮轮辐、轴、和轴承等零件的支撑刚度和模态特性,以及相关零部件之间的配合刚度等因素。
系统响应方面:包括壳体刚度和模态特性,以及系统的耦合模态频率等因素。
3.2 制造安装误差分析
制造安装误差也是导致齿轮啮合啸叫噪声的因素之一,拆解减速器总成,对零部件制造安装误差进行复检,通过检测报告除一级齿轮外,其余零部件的关键尺寸公差均无超差项,一级齿轮存在齿顶修缘量超差和单个齿距跳齿问题,可能对啸叫噪声有所贡献。
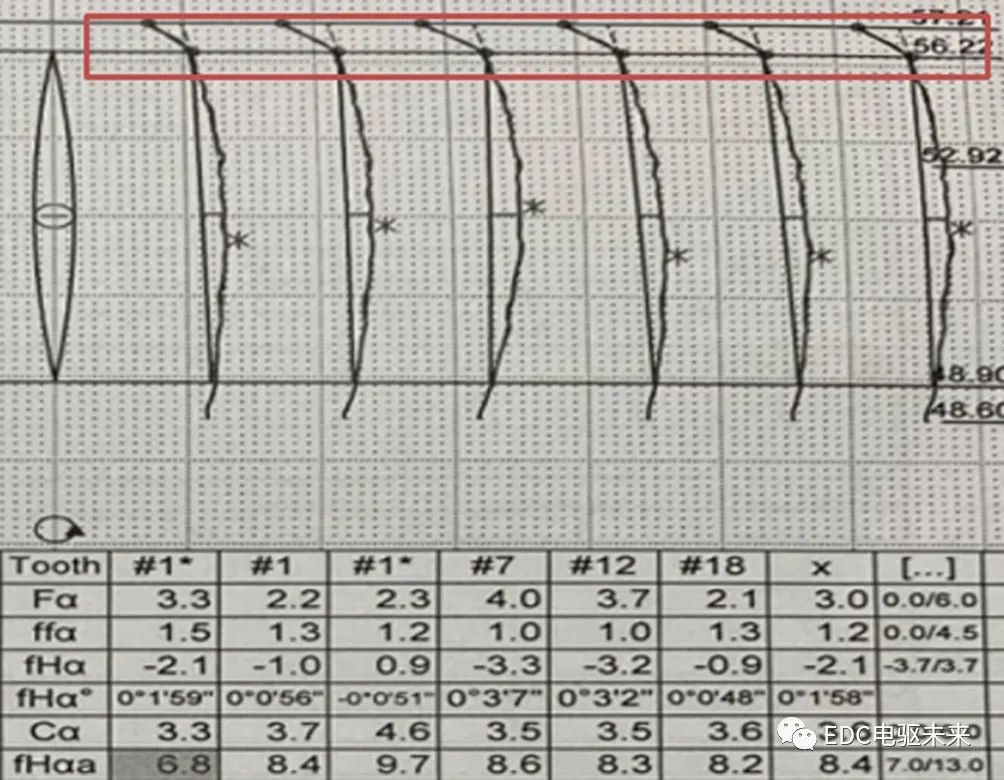
图4 齿轮检测结果一
Fig.4 Gear test result 1
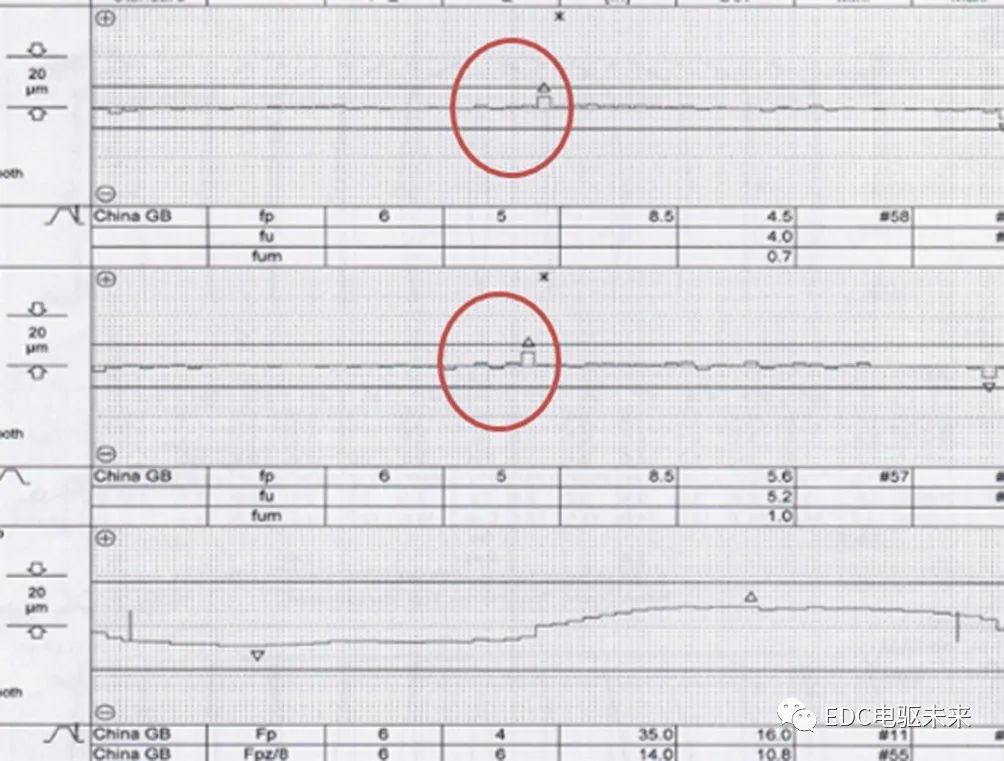
图5 齿轮检测结果二
Fig.5 Gear test result 2
针对以上超差问题,通过工艺改善,消除了超差问题,挑选合格齿轮进行换装测试,啸叫噪声并未明显改善,这说明啸叫噪声并不是此项制造超差带来的。
3.3 减速器动力学仿真模型搭建与标定
基于MASTA软件建立减速器总成虚拟样机仿真分析模型,对于轴、齿轮轮辐、差速器壳体、减速器壳体等零部件通过有限元法获得准确刚度、质量和模态等信息并导入仿真分析模型,以获得准确的动力学性能仿真分析模型。
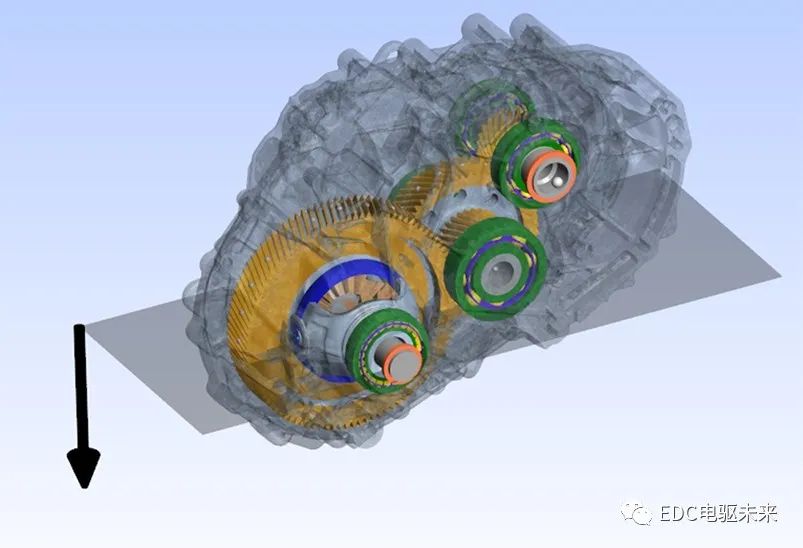
图6 减速器总成仿真分析模型
Fig.6 Simulation analysis model of reducer assembly
通过减速器总成齿轮接触区试验结果、振动噪声试验结果和零部件制造及装配误差标定仿真分析模型,标定后仿真分析模型的计算结果与试验结果一致。
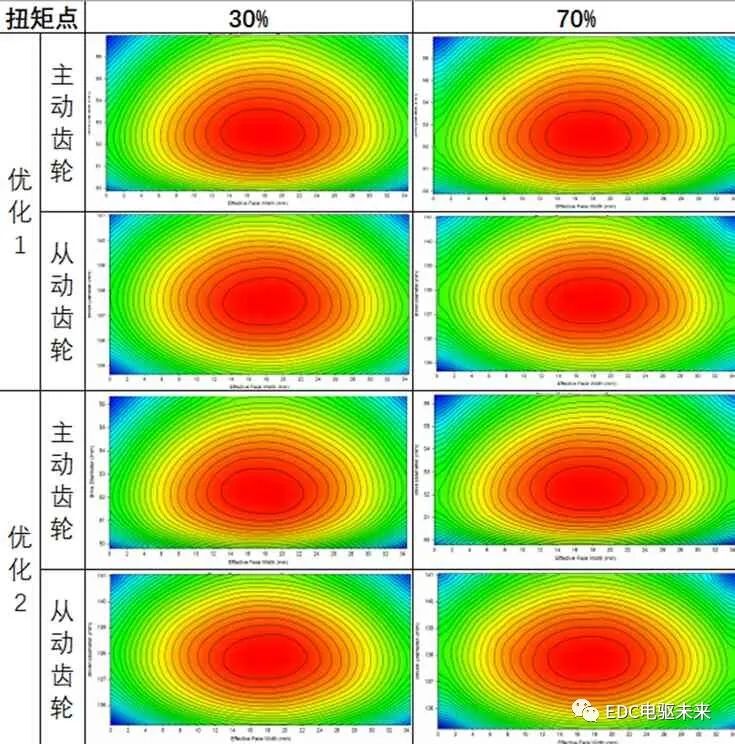
图7 齿轮接触区试验与计算结果对比
Fig.7 Comparison of test and calculation results of gear
contact zone
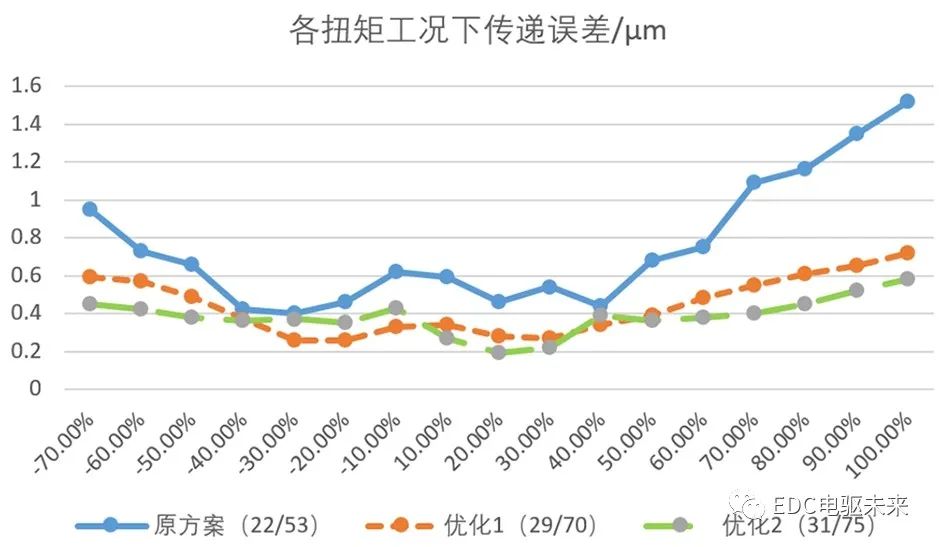
图8 振动噪声试验与计算结果对比
Fig.8 Comparison of vibration and noise test and
calculation results
3.4 振动激励源分析
振动激励源主要是齿轮啮合产生的,主要表现形式为齿轮啮合的传递误差、啮合刚度和动态啮合力,针对减速器一级齿轮进行振动激励源分析,分析结果显示,在啸叫问题工况下,传递误差峰峰值为0.54 μm和1.09 μm,传递误差值较大;啮合刚度最大波动量为2.06 N/(μm·mm)和1.84 N/(μm·mm),啮合刚度波动较大;齿轮动态啮合力在啸叫问题工况区间存在峰值,峰值分别为0.62 kN/μm、1.53 kN/μm和0.96 kN/μm、1.99 kN/μm。以上振动激励幅值需优化降低。
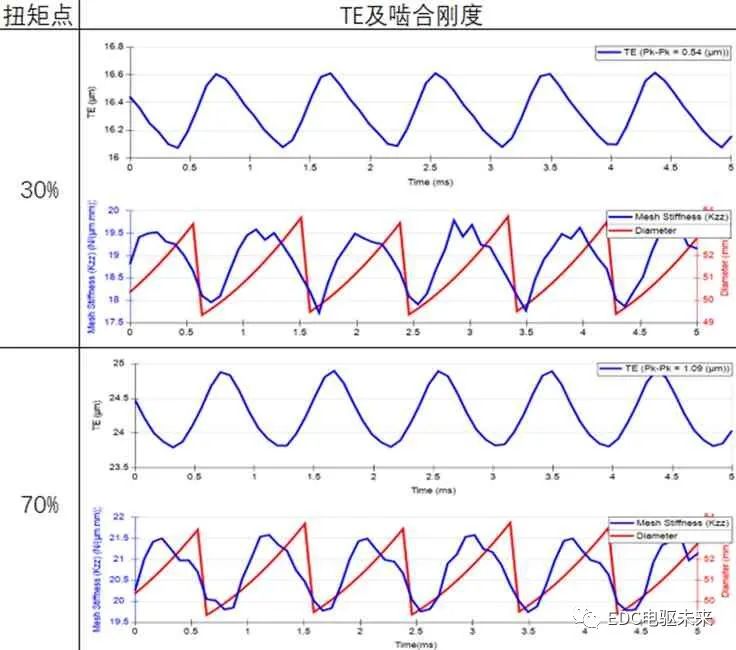
图9 传递误差及啮合刚度计算结果
Fig.9 Transmission error and mesh stiffness
calculation results
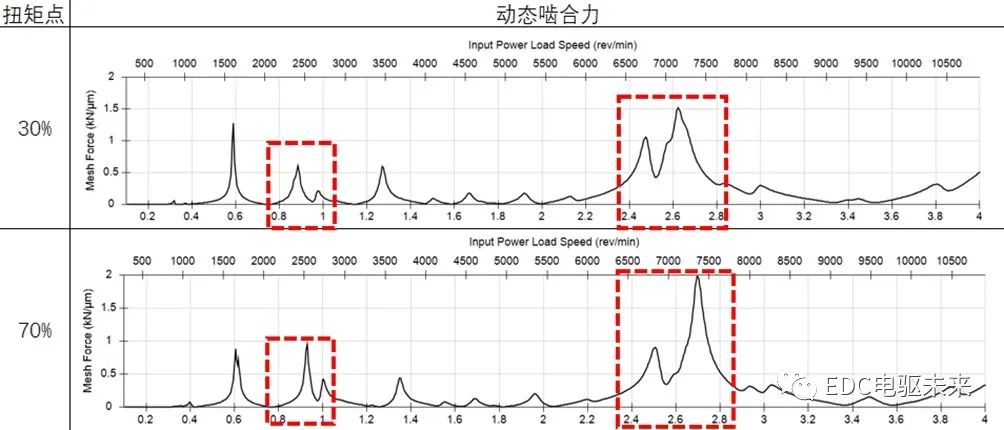
图10 动态啮合力计算结果
Fig.10 Dynamic meshing force calculation results
3.5 传递路径分析
齿轮啮合产生的振动激励通过轮辐、轴和轴承传递至壳体,进而产生壳体辐射噪声,这些零件的支撑刚度不足会使齿轮啮合错位量增大,进而传递误差和动态啮合力等激励也会增大,系统变形分析结果显示,一级从动齿轮轮辐轴向变形较大,支撑刚度不足,需做结构优化设计,强化支撑刚度。
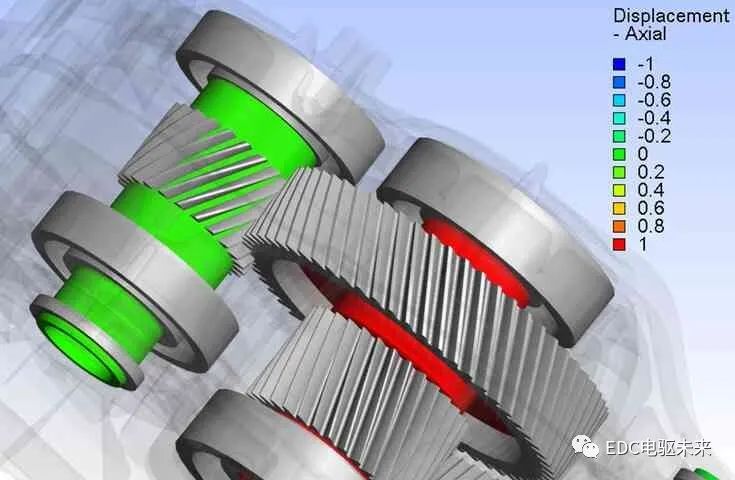
图11 系统变形计算结果
Fig.11 System deformation calculation result
3.6 系统振动响应分析
通过耦合模态分析及系统振动响应分析,能计算系统耦合模态及频率,分析获得系统振动响应结果,识别系统及零部件振动特性及频率激振情况,计算结果显示,在啸叫问题工况区,存在频率临近的多个模态频率,产生了模态频率共振问题,对应峰值转速2 513 r/min和6 853 r/min,模态共振问题需优化。
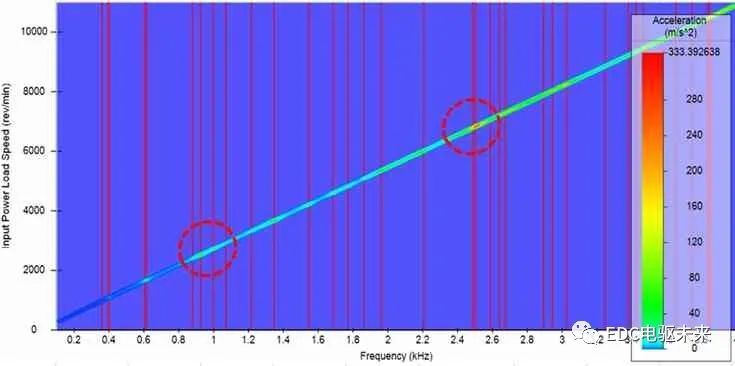
图12 振动响应频谱图计算结果(22阶)
Fig.12 Vibration response spectrogram calculation
results (22th order)
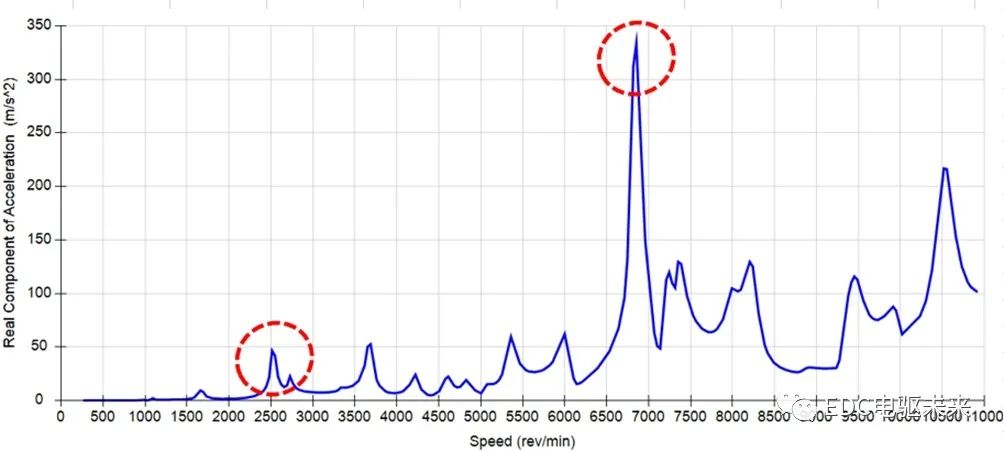
图13 22阶次切片图
Fig.13 22th order slice diagram
4 方案优化设计及分析
根据前文的啸叫噪声原因分析结果以及综合考虑方案优化更改的可行性及有效性,制定便捷有效的改进设计方案。
关于一级从动齿轮轮辐支撑刚度不足问题,通过优化轮辐结构,加宽轮辐辐板厚度,辐板厚度由原10 mm增至15 mm,在辐板上增加减重孔以控制零件重量的增加,同时将轮缘厚度增加,以提高轮齿支撑刚度。
关于模态共振问题,可通过更改激振频率或者共振零部件的模态频率来改善,但由于更改零部件的响应模态频率需要壳体和轴齿件结构做较大的更改,更改方案可行性差,因此本文通过更改激振频率即一级齿轮的齿数来优化激振频率,避开优化目标转速区间内的共振模态频率,在保证速比不变的前提下,优化齿数,如表1所示。
表1 齿数优化方案对比表
Tab.1 Comparison of tooth number optimization schemes
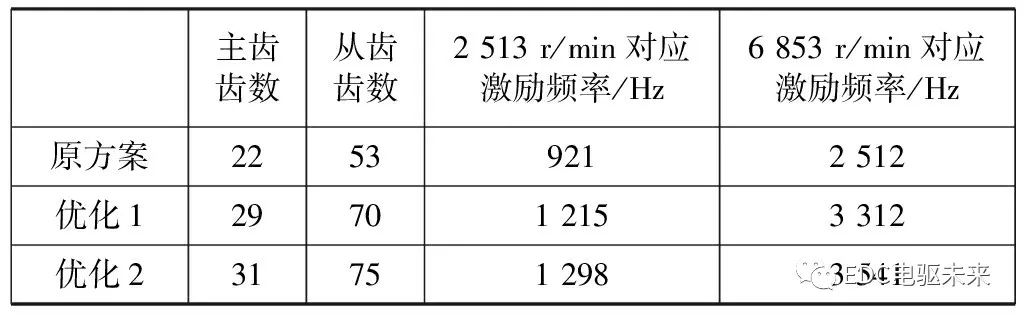
除了以上措施,降低齿轮啮合振动激励源是改善齿轮啸叫噪声最直接和最有效的措施,基于以上两种齿数优化方案,以降低传递误差、啮合刚度和动态啮合力为优化目标,对齿轮的宏观参数和微观修形参数进行优化设计。
齿轮宏观参数设计时,恰当的重合度设计能够在保证可靠性的前提下,增强轮齿啮合刚度,降低齿轮啮合错位量和传递误差,重合度优化结果如表2所示。
表2 重合度优化方案对比表
Tab.2 Comparison table of optimization schemes for coincidence degree

齿轮微观修形参数设计时,要保证齿面接触应力在齿宽和齿高方向上保持正中间,且接触面积要大于全齿面积的70%;同时,要保证重点关注扭矩工况下的传递误差峰峰值尽可能的小,并降低齿轮啮合刚度波动量和齿轮动态啮合力峰值。
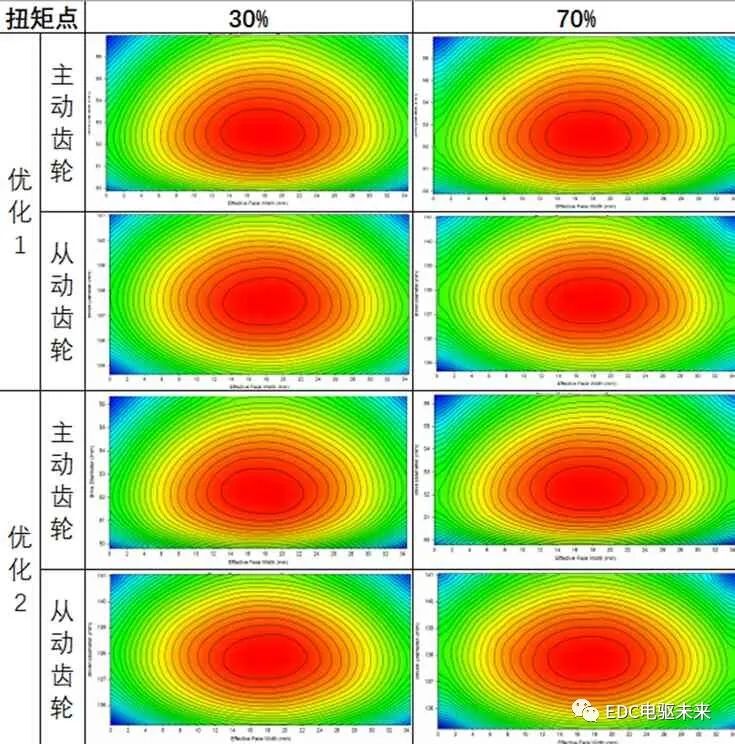
图14 齿面接触应力计算结果
Fig.14 Tooth contact stress calculation result
目标扭矩工况下,齿面接触应力分布居中,未出现明显偏载,齿轮啮合接触状态良好。
表3 传递误差及啮合刚度优化结果对比表
Tab.3 Comparison table of transmission error and mesh stiffness optimization results
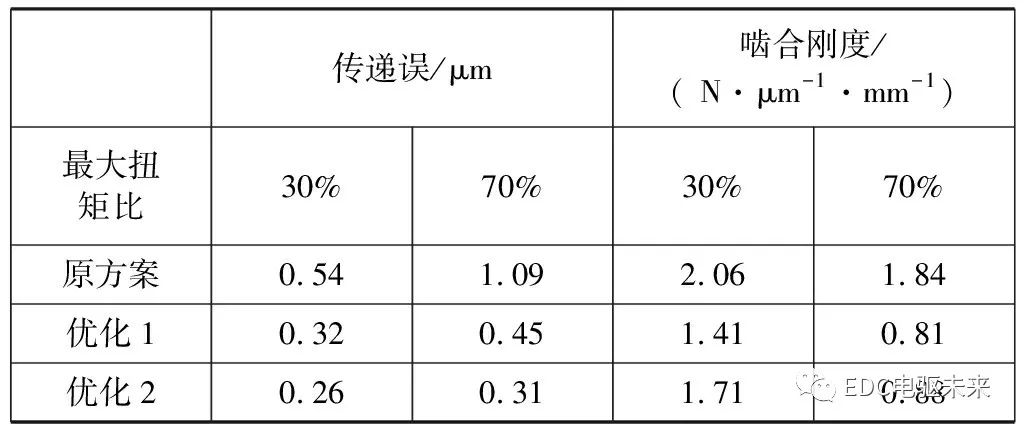
优化方案与原方案相比,啸叫问题工况下的传递误差和啮合刚度均大幅降低,达成优化预期目标。
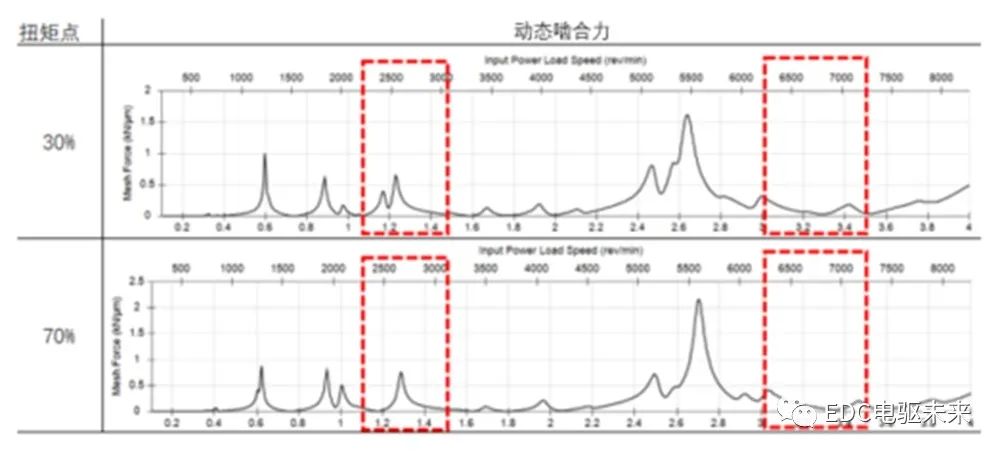
图15 动态啮合力计算结果-优化1
Fig.15 Dynamic meshing force calculation
results-optimization 1
优化后的动态啮合力计算结果显示,2 300 r/min~3 200 r/min峰值依然存在,但幅值有所减小;6 350 r/min~7 500 r/min加速区间波峰消失,但2 600 Hz~2 700 Hz频率区间的波峰依然存在,波峰移动到加速区5 000 r/min~5 500 r/min,这说明共振模态频率依然存在,为避免将目标转速区域的啸叫噪声改善后,其他转速区间的啸叫噪声恶化,需对全扭矩段的传递误差峰峰值进行优化控制,将全扭矩段工况下对应的传递误差峰峰值降低。
如图16所示,优化1和优化2方案各扭矩工况下传递误差峰峰值均低于原方案,全扭矩段工况下的啸叫噪声风险可控。
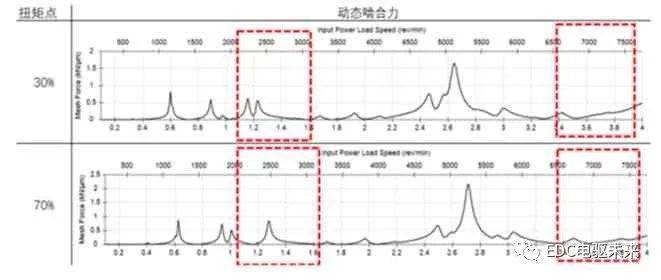
图16 动态啮合力计算结果-优化2
Fig.16 Dynamic meshing force calculation
results-optimization 2
最后对优化方案进行阶次噪声声功率分析,预测优化方案的啸叫噪声情况,如图17和图18所示,计算结果显示,优化1和优化2的阶次噪声均低于35 dB目标值,符合设计优化目标要求。
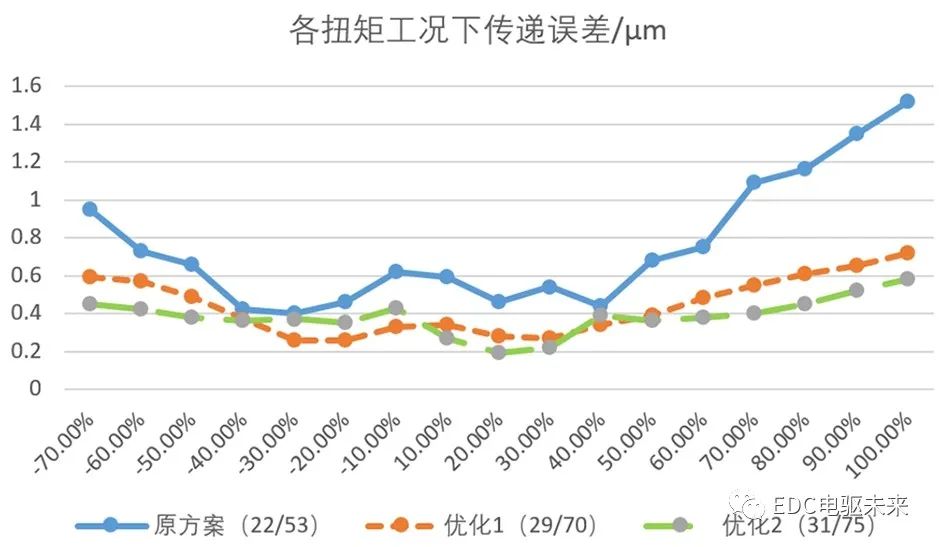
图17 各扭矩工况下传递误差计算结果
Fig.17 Transmission error calculation results under
various torque conditions
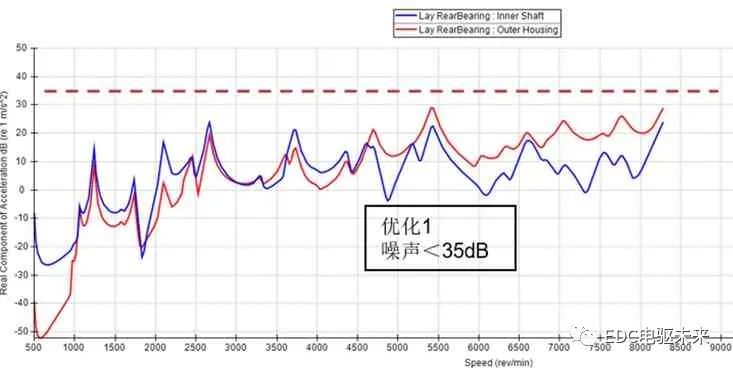
图18 29阶次噪声计算结果-优化1
Fig.18 29th order noise calculation results-optimization 1
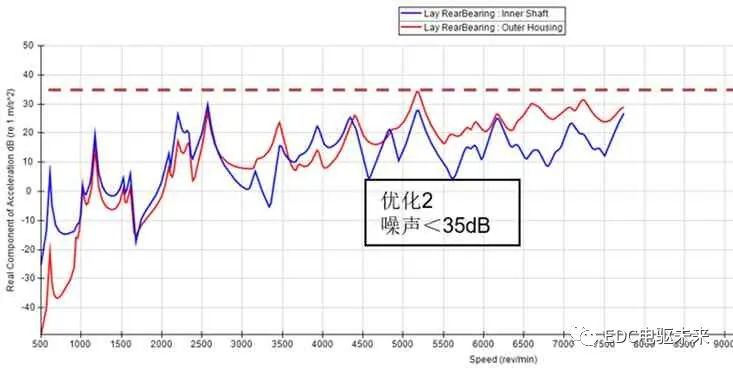
图19 31阶次噪声计算结果-优化2
Fig.19 31th order noise calculation results-optimization 2
5 试验验证
针对优化1和优化2两个方案进行试制,并进行整车NVH客观试验测试,测试结果显示,两个优化方案的一级齿轮阶次噪声均低于35 dB(A),其中优化1阶次噪声较原方案降低11 dB(A),优化2阶次噪声较原方案降低14 dB(A),两个方案阶次噪声值均达成目标值,并大幅低于阶次噪声控制目标值。
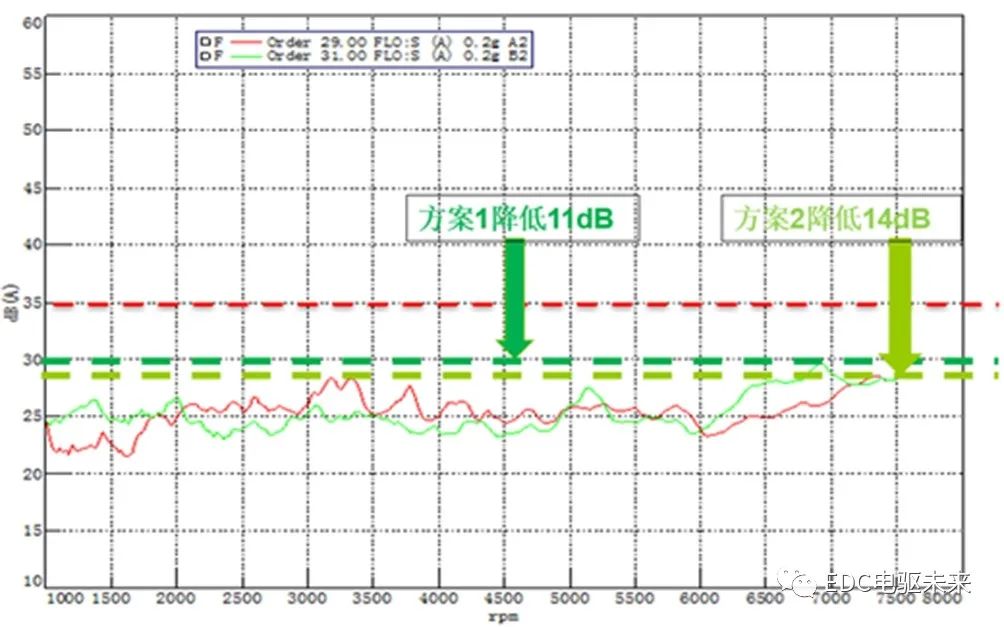
图20 优化方案振动噪声试验结果
Fig.20 Optimized plan vibration and noise test results
6 结论
本文以某纯电动汽车减速器为例,针对该减速器在整车NVH试验中出现的啸叫噪声问题,应用减速器动力学性能虚拟样,通过仿真分析手段,对减速器齿轮啸叫噪声产生的机理进行了深入的分析,从振动激励源、传递路径和系统振动响应等方向全面分析了一级齿轮啸叫振动噪声的产生、传递以及响应过程,并通过优化振动激励、支撑刚度和模态共振频率等手段,改善了齿轮啸叫噪声,达成了减速器产品噪声开发目标,为减速器的NVH性能正向开发提供了一个比较全面的思路,并得出以下结论:
(1)准确和全面的试验测试是解决问题的前提,对于减速器啸叫问题解决,必须通过试验准确获取相关试验测试数据,包括整车行驶工况对应的扭矩、转速、齿轮接触区以及振动噪声客观试验数据等,以及零部件的模态试验数据等。
(2)虚拟样机模型的准确性对于解决噪声问题至关重要,需通过试验结果,结合有限元等多种手段对虚拟样机模型进行精确的标定优化。
(3)优化齿轮啮合传动产生的振动激励源,是解决啸叫噪声问题最直接有效的手段,通过齿轮宏观参数和微观修形参数的综合迭代优化设计,可以显著降低振动激励。
(4)传递路径及壳体的支撑刚度和模态,在结构总布置设计时就应该充分考虑NVH性能开发的需求,在总成及零部件设计方案锁定前,需对结构支撑刚度和模态进行综合优化。
(5)系统及零部件耦合模态频率是客观存在无法消除的,在进行方案设计时,对于噪声敏感的工况需避开共振模态频率,并尽量降低振动激励。
参考文献
[1] 闫硕, 王宏伟. 纯电动汽车减速器噪声优化研究[J]. 中国汽车, 2019, 000(007):49-53.
[2] 温国庆, 李艳斌, 殷麒麟,等. 采用传递路径分析的纯电动车减速器啸叫噪声优化[J]. 重庆理工大学学报(自然科学), 2017, 09(212):59-63.
[3] 潘晓东, 刘祥环, 黎超. 纯电动汽车高速齿轮传动NVH性能优化研究[J]. 重庆理工大学学报, 2017,11(31):25-31.
[4] ASME M , J DEERE, PARKER R G . Mesh stiffness variation instabilities in two-stage gear systems [J]. Journal of vibration and acoustics,2002,124(1):68-76.
[5] 李彦昊, 吴光强, 栾文博. 基于齿轮修形的变速器啸叫特性优化[J]. 机械传动, 2014(1):18-22.
[6] KANDA Y , SAKA T , FUJIKAWA M , ET AL. Experimental Transfer Path Analysis of Gear Whine[J]. SAE 2005:01-2288.
[7] 徐忠四, 承忠平, 高立新,等. 电动汽车减速器啸叫噪声的双目标优化[J]. 汽车工程, 2018,1(40):76-81.
最新资讯
-
大卓智能端到端直播实测,16公里复杂路段挑
2025-04-25 17:16
-
《汽车轮胎耐撞击性能试验方法-车辆法》等
2025-04-25 11:45
-
“真实”而精确的能量流测试:电动汽车能效
2025-04-25 11:44
-
GRAS助力中国高校科研升级
2025-04-25 10:25
-
梅赛德斯-AMG使用VI-CarRealTime开发其控制
2025-04-25 10:21