电池热管理系统散/加热特性研究及保温安全设计
目的
研究电动汽车高/低温工况下锂离子(Li–ion)电池散/加热所需时间,完善电池热管理系统(BTMS)的保温与安全设计。方法 通过瞬态仿真分析微通道耦合微热管(MC 耦合 UMHP)式BTMS 作用 Li–ion 电池组散热过程的动态特性,并在该 BTMS 结构上增加电加热辅助设计,考虑到Li–ion 电池组在超低/高温工况运行时的各种不利条件,对 MC 耦合 UMHP 式 BTMS 增加保温与安全设计。结果 在流速为 3 m/s 时,MC 耦合 UMHP 式 BTMS 作用 Li–ion 电池组从初始温度 314 K 降温至目标温度 303 K 所需的时间仅为 135 s,在 Li–ion 电池组初始温度为 258 K 时,加热时间近 258 s,在各种工况下进行散/加热仿真实验中 Li–ion 电池组的最大温差始终小于 5 K。结论 MC 耦合 UMHP 式 BTMS对 Li–ion 电池散/加热所需时间少,换热效果好,温度均衡性好。
关键词:锂离子电池;BTMS;微通道;微热管;安全
作者:王振,李保国 上海理工大学,上海
作为电车动力源,锂离子(Li–ion)电池能够实现平衡其最佳性能与使用寿命的工作温区为 288~308 K[1]。Li–ion 电池性能易受温度影响,在温度为303~313 K 时,Li–ion 电池温度每升高 1 K,其使用寿命将缩短 2 个月[2]。在低温时 Li–ion 电池活性迅速降低并失去部分电量,在高温时 Li–ion 电池生热加剧,易引发安全隐患[3]。电池热管理系统(BTMS)是一种为动力 Li–ion 电池提供及时热量交换与保护而设计的系统,通常采用包裹/贴覆于动力电池表面的结构对其进行换热[4]。可靠的 BTMS 是保证 Li–ion电池在多工况环境下正常工作与安全运行的关键[5]。
受限于电车的小空间尺寸,更加简洁与微型的 BTMS备受市场青睐与需求,要求动力电池的有效散热间隙降低至 2~3 mm[1,3],而基于常规的空气、液冷、相变材料(PCM)以及热管式的 BTMS 已不再适用[6]。要解决 BTMS 中的高换热量与高占用空间等问题,须采用换热性能更好、水力直径更小的微通道与微热管等相关换热技术[3]。
Zhao 等[7]通过改变微通道体积、质量流量、流动方向和进气道尺寸等,对冷却圆柱锂离子电池的散热性能进行了数值模拟研究,结果表明,当微通道数量大于 4,入口质量流量为 10−3 kg/s 时,锂离子电池的最高温度低于 313 K。Liu 等[8]采用数值模拟研究了在微通道中添加纳米颗粒对 5 层方形锂离子电池的控温效果,结果显示,纳米颗粒的换热效果优于同等条件下的水和乙二醇的混合溶液。Bai 等[9]提出了一种基于相变浆液(PCS)和微型通道冷却板结合的BTMS。模拟结果表明,当质量流量小于 3×10−4 kg/s时,体积分数为 20%正十八烷微胶囊和体积分数为80%水组成的 PCS 的冷却性能优于纯水、乙二醇溶液和矿物油。An 等[10]采用仿真研究发现,在放电速率为 2 C 的情况下,对电池单侧的一半表面进行冷却足以使电池组的最大温差小于 3 K。微通道液冷式BTMS 可以有效地保障 Li–ion 电池组在较为合适的温区内工作,并随着微通道和平板数量的增加以及进口流量的增加,微通道换热器的换热性能越好,但随着管道长度与流速的增加,Li–ion 电池组温差随之增大[11-13]。Ye 等[14]采用微热用热管冷却板对锂离子电池组在快速充电状态下的热性能进行研究,得到在 8 C充电倍率和不同的冷却控制策略下其设计的 BTMS均具有良好的散热性能。Liu 等[3]提出了采用扁平超薄微热管(Ultra-Thin Micro Heat Pipe,UMHP,厚度为 1 mm)用于 BTMS,对其在极端情况下的散/加热性能做了实验研究,得到在单体电池生热率小于10 W 时,其表面温度小于 313 K,在产热率为 20~40 W 时,其表面温度小于 328 K,最大温差不超过5 K,但其采用翅片式设计用于微热管散热仍然存在体积较大、效率较低的问题,作为整体的 BTMS 换热结构其体积已超出了小空间占比的设计要求[3,14]。
此外,微通道热管和微通道的区别在于:前者是封闭恒温系统,内部流通的相变制冷剂可自成循环,需要辅助额外的散热设施将热量转移至车载换热设备中;而后者是开放变温系统,内部流通的载冷剂可在泵的驱动下与车载换热设备直接换热,并完成整个换热循环[6]。因此,文中在对微通道(MC)与扁平微热管结构与特性研究的基础上,通过在 UMHP 冷凝端耦合 MC 组对其进行换热,构建 MC 耦合 UMHP 式BTMS。该耦合结构集合了 MC 与 UMHP 的传热优势于一体,从根本上解决 UMHP 式 BTMS 所需换热设备大,以及长尺寸 MC 式 BTMS 中 Li–ion 电池组温差大等问题。文中将通过瞬态仿真分析的方法研究MC 耦合 UMHP 式 BTMS 对 Li–ion 电池散/加热过程的动态特性的影响,并在此基础上完善其对 Li–ion电池的保温与安全设计。
01、模型描述
Li–ion 电池组模型
考虑到方形 Li–ion 电池单体/组是当前国内厂商生产与使用最多的 Li–ion 电池类型,因此,在对Li–ion 电池单体/组的选型时,选择 BTMS 设计还不完善、在国内使用最多的方形 Li–ion 电池单体/组,并以 5组方形 Li–ion电池单体构成的电池组为研究对象,可以完整地用于代替各种不同工况下的电池包的性能测试[15]。5 个型号 GSP09102165F 方形聚合物Li–ion 电池构成的热源系统模型见图 1,该模型主要包含 4 类结构:5 组 Li–ion 电池体模型、5 组阴极极耳、5 组阳极极耳和 5 组电池壳体模型,其详细规格与物性参数见表 1[3]。
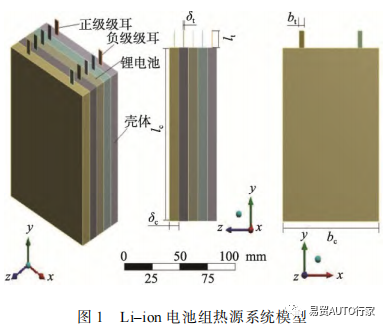
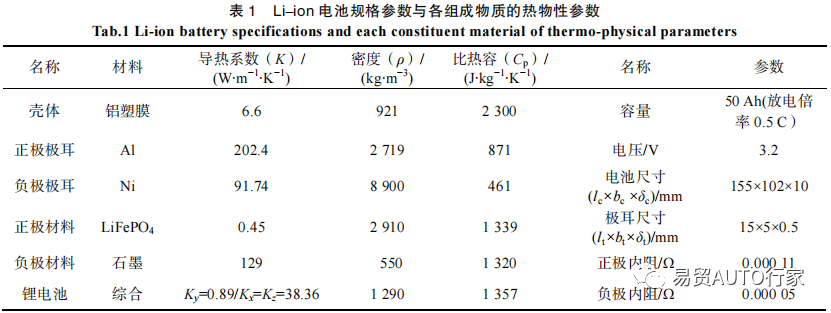
MC 耦合 UMHP 式 BTMS 模型构建
MC 耦合 UMHP 式 BTMS,见图 2,其中 MC 耦合 UMHP(MC–UMHP)换热结构竖直地贴敷于垂直放置的 Li–ion 电池组的侧立面,构成夹层结构。图2b 为放大后的 MC–UMHP 换热结构图,其中 5 组MC 与 5 组 UMHP 通过热融合的方式形成一体结构,并竖直地贴敷于 Li–ion 电池组两侧。该模型的几何参数:MC 的结构特征尺寸为 50.2 mm×6.2 mm×1.4 mm;UMHP 的结构特征尺寸为 161.7 mm×10 mm×1 mm;UMHP 组中相邻 UMHP 单体的间距为 0.5 mm;相邻电池单体的间距为 0.5 mm;相邻 MC–UMHP 结构的间距为 102 mm。
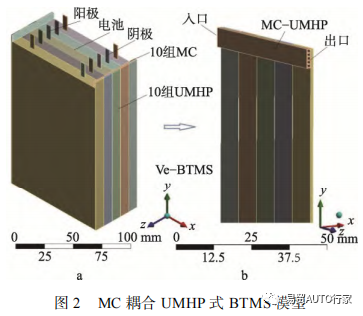
02、数值求解方法及过程
数值求解方法
使用基于有限体积法 19.2 版本的 Fluent 对具有一定初始温度的 Li–ion 电池组热源模型进行瞬态仿真研究,黏性模型选择 k–e,以上选择主要用于计算高雷诺数(Re)条件下微通道中的流体流动。动量与能量方程选择 Quick 方式进行离散,采用 CoupledAlgorithm 算法求解热传导与对流的共压速度耦合,其主要目的是加速微通道中的仿真计算[16-18]。计算域的网格划分采用六面体与四面体单元,研究中的液体是水,固体分别是铝、阳极、阴极和 Li–ion 电池。由于 Re 已超过 2 000,故该流体被认为是三维不可压缩湍流。
边界条件设置
考虑到此次仿真计算的模型结构与传热方式,选择高速流动的液体水作为载冷剂物质用于传热,因此入口边界条件设置为均匀流速入口,出口边界条件设置为充分发展出口,背压为 0;考虑到 MC 与 UMHP耦合面处的传热、流体与壁面间的耦合传热以及UMHP 与 Li–ion 电池组间的耦合传热,耦合面设置为无渗透滑移面边界条件。然而在进行不同工况的仿真计算时边界条件仍有变化,如:入口边界条件 Uin为 0.5、2、3、4 m/s;Tin 为 289、291、293、295 K;Li–ion 电池组的初始温度高温为 298、300、312、314、316 K,低温为 258、263、268、273、278 K;Li–ion电池组的降温目标温度为 303 K,升温目标温度为293 K;电辅热的加热功率为 180 W[3]。
网格独立性验证
Workbench Mesh 软件用于网格划分。为了确保Li–ion 电池与 UMHP 间、UMHP 与 MC 间、MC 壁面与流体间的耦合换热,通过 Mesh 软件在 MC 的内壁面、UMHP 的外壁面以及流体的外表面构建耦合面。为了减少仿真中的计算量并保证计算精度,对Li–ion 电池、UMHP、阴极、阳极体模型采用大尺寸的六面体网格进行划分,但是,由于流体的水力直径远小于 MC 的长度,对 MC 以及 MC 内的流体域只能采用小尺寸的六面体网格进行划分,以确保对流体近壁面区域仿真计算时的精度。此时,BTMS 的网格模型共计分为 6 个区域,即:流体域、MC 域、UMHP域、Li–ion 电池域、阴极域和阳极域,其中各区域中对应的最大网格尺寸设置依次为 0.08、0.1、1.0、1.5、0.5、0.5 mm。参照型 BTMS(Ref 型 BTMS)的网格示意图见图 3,该模型的关键结构网格和传热耦合方式均与 MC 耦合 UMHP 式 BTMS 相同。
不同网格参数配置条件下划分得到的 Ref 型BTMS 的网格数范围为 2 382 684~6 961 415,以及其对应仿真计算得到的努塞尔数(Nu)见表 2。对表2 中数据分析可知,在流体域的网格划分尺寸范围为0.06~0.1 mm,对应 Nu 的最小相对偏差仅为 0.03%,对应 Nu 的平均相对偏为 0.05%,因此,选用网格数和尺寸分别为 3 443 986 和 0.08 mm,可作为后续BTMS 模型网格划分参数的基准,该网格划分参数设置将有助于在保证仿真计算精度的同时降低仿真计算时间。使用该网格划分参数配置时,连续性方程与动量方程的收敛准则设置为 10–3,能量方程的收敛标准设置为 10–6。
时间步长独立性验证
使用网格数为 3 443 986 的 BTMS 仿真计算模型对 4 个不同的时间步长(0.025~2 s)进行时间步长独立性验证研究,见表 3。当时间步长从 0.25 s 更改为 0.5 s 时,以及从 0.5 s 更改为 1 s 时,Li–ion 电池组温度变化率仅为 0.002%和 0.003%。当它从 1 s 更改为 2 s 时,变化率为 0.007%,远大于前面 2 种时间步长对应的 Li–ion 电池组温度变化率,因此,选择 1 s的时间步长作为后续瞬态仿真研究的基准。
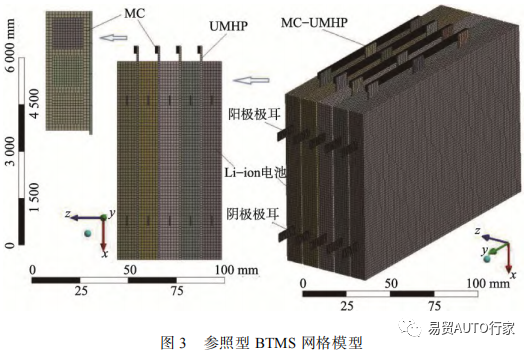
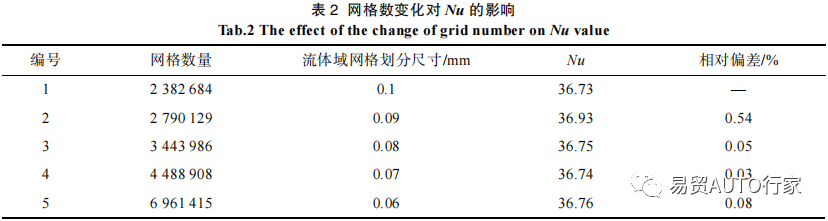
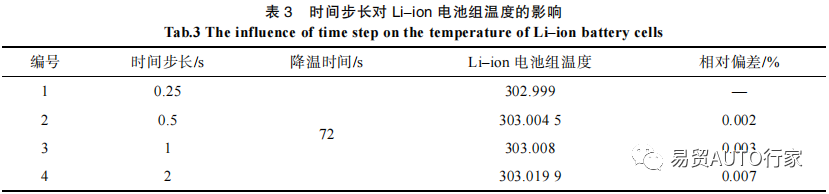
03、结果与讨论
仿真模型验证
参考文献[19-20]中实验数据与验证方法,文中得到的结果见图 4。从图 4 中变化曲线可以看出,3 组数据中的阻力系数(f)均随 Re 增加而缓慢变小,且变化趋势相同。在 Re 相同时,3 种 f 间的相对偏差均小于 5%,平均偏差为 2.4%,可认为当前模型仿真计算结果的精度符合要求。此外,参考文献中相同结构的 BTMS 在 3 C放电实验结束时其对应的电池包最大温差为 7.2 K,对应的电池组最大温差为 4.6 K[3],而该研究中参照型 BTMS 在 3 C放电仿真计算结束时其对应的电池包最大温差为 7.3 K,对应的电池组最大温差为 4.7 K,二者相对偏差小于 2%,即参照型 BTMS仿真计算过程可靠,仿真计算结果准确。由此可推断出 MC 耦合 UMHP 式 BTMS 的仿真结果准确。
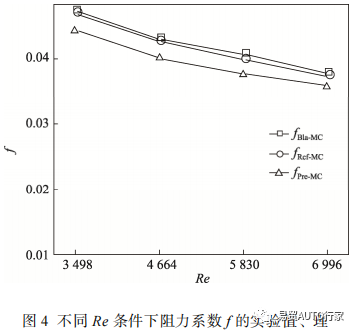
流体入口温度对 Li–ion 电池散热所需
时间的影响
不同入口温度(Tin)条件下,Li–ion 电池组温度从 308 K 降温至 303 K 时所需的时间变化见图 5。在Tin为 289 K 时,其降温时间仅需 53 s,在 Tin 为 293 K时,其降温时间为 72 s,是前者的 1.36 倍,而在Tin大于 293 K 之后,其所需的降温时间更长,因此降低入口流体温度可有效缩短 Li–ion 电池组的降温时间。此外,由图 5 中的折线图的变化趋势可知,在流体入口温度小于 291 K 之前,曲线的变化趋缓,由此可以推断 BTMS 的降温效果会随着入口温度的降低而降低。
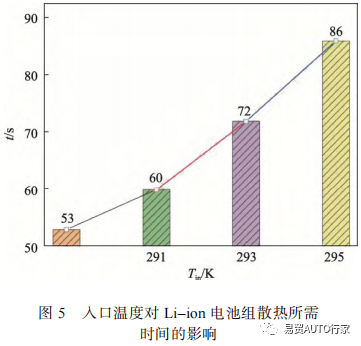
流体入口流速对 Li–ion 电池散热所需
时间的影响
入口流速对 Li–ion 电池组温度从 308 K 和 314 K降温至 303 K 时所需的时间曲线影响见图 6。由图 6对比分析可知,在 Li–ion 电池组初始温度为 308 K 与314 K 时,随着入口流速 Uin 的增加,降至目标温度所需时间缩短,即 Uin 值越大,BTMS 对 Li–ion 电池组的换热越强。通过分析不同 Uin 条件下 2 种初始温度工况对应的 Li–ion 电池组的降温时间差(∆t)可知,Uin 值越大 2 种初始温度工况对应降温时间差越小,在 Uin 值为 3 m/s,Li–ion 电池组初始温度为 314 K 时,Li–ion 电池组在 MC 耦合 UMHP 式 BTMS 的作用下降温至 303 K 所需的时间仅需 135 s,该降温时间可完全满足夏季高温工况时的使用要求。
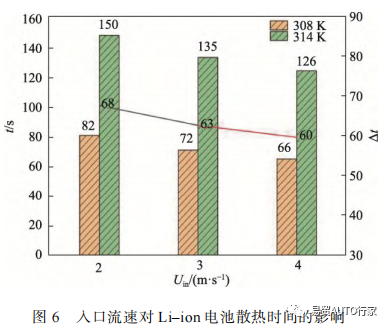
Li–ion 电池初始温度对其散热所需时
间和温度分布的影响
上述研究表明,流体入口 Uin 值为 3 m/s 时,MC耦合 UMHP 式 BTMS 作用 Li–ion 电池组的降温时间较为理想,因此,控制 Uin 值为 3 m/s,通过改变 Li–ion电池组初始温度研究其散热所需时间。不同 Li–ion电池组初始温度对应的降温时间变化曲线见图 7,从图 7 可看出,随着 Li–ion 电池初始温度的增加,降温所需的时间也在增加。Li–ion 电池组降温所需时间与初始温度的变化量呈现线性关系,即 Li–ion 电池组初始温度越高,其降温所需的时间越长,其函数关系式为:y=10x−3 006。
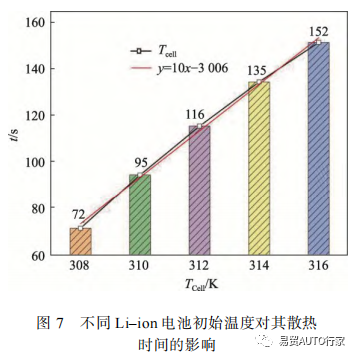
Uin 值为 3 m/s 时,Li–ion 电池组从初始温度分别为 308 K 和 310 K 降温至 303 K 时的温度云图见图 8,通过对比发现,2 幅云图的温度分布相同。低温区域主要集中在 MC 与 UMHP 的耦合交接处,以及 Li–ion电池组的上部两端,而高温区域主要集中在的 Li–ion电池组的中间区域,尤其是底部区域温度值最高,但Li–ion 电池组的最大温差小于 5 K,即通过 MC 耦合UMHP 式 BTMS 对该工况下的 Li–ion 电池组进行散热,可以满足温度均衡性的设计要求。
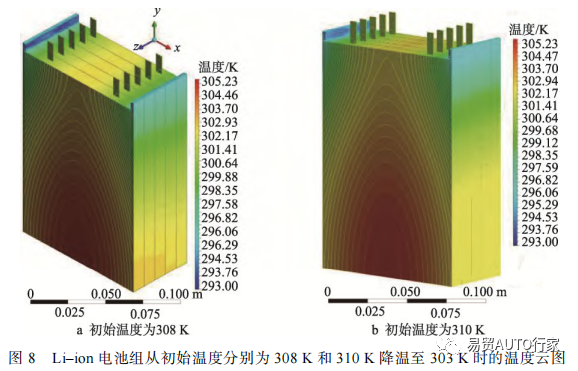
Li–ion 电池初始温度对其加热所需时
间及温度分布的影响
在环境温度小于 283 K 以下时,此时 BTMS 作用Li–ion 电池组加热升温的过程需要辅助电加热系统。对于 MC 耦合 UMHP 式 BTMS,该研究采用 UMHP与电池体侧立面接触的部位作为加热装置的加热面,并通过导线对其施加恒定的加热功率(180 W)。当环境温度小于 268 K以下时,此时的 BTMS将停止工作,对 Li–ion 电池组的加热工作只能采用电加热系统来完成,因此文中对此展开如下研究:控制 Li–ion 电池组初始温度分别为 258、263、268 K,研究电加热作用使其升温至 293 K 时所需时间;控制 Li–ion 电池组初始温度分别为 273 K 和 278 K,研究 BTMS 与电加热联合作用使其升温至 293 K 时所需时间。
不同初始温度的 Li–ion电池组加热至 293 K时所需时间变化图,见图 9。在 Li–ion 电池组初始温度为258 K 时,此时需要的加热时间为 258 s,可完全满足BTMS 加热系统设计要求[21]。在 Li–ion 电池组初始温度为 258~268 K,随着在 Li–ion 电池组初始温度的升高,升温所需的时间减少,二者为线性负相关关系,此时电池的加热过程主要由电加热完成;图 8 中的升温时间曲线在 268 K 和 273 K 处的曲线斜率显著增大,说明 Li–ion 电池组的升温速度加快,其原因是当 Li–ion 电池组初始温度为 273 K 时,此时 BTMS与电加热系统同时对其进行加热,对应的升温所需时间远小于 268 K 时对应的升温时间。
此外通过分析具有一定初始温度(高/低)静态的 Li–ion 电池在 BTMS 的作用下进行散/加热过程中热量的传递方式和传热系数可知,二者的传热方向相反,一个是从低温到高温的加热过程,一个是从高温到低温的散热过程。在一定温区范围内,由于流体的物性参数变化微小,且 UMHP 的蒸发段与冷凝段在仿真建模时被看成一体结构,并使用同一传热系数,因此,静态的 Li–ion 电池通过 BTMS 进行散热或者加热过程中的传热方式,以及该散热或者加热过程中的换热系数都是相同的。单独研究 BTMS 散热动态特性即可代表 Li–ion 电池在 BTMS 作用下的整个散/加热过程的动态特性研究。
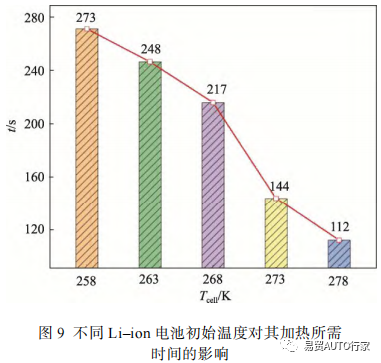
MC 耦合 UMHP 式 BTMS 保温与安全设计
由表 1 与表 2 中的几何参数可知,MC 耦合 UMHP式 BTMS 已在相邻 Li–ion 电池单体间预留了 155 mm×102 mm×0.5 mm 的空间,并在相邻 UMHP 间预留了10 mm×102 mm×0.5 mm 的空间,该预留空间刚好布置气凝胶层,由此设计了图 10a 所示的具有良好保温性能与安全性能的 BTMS,该 BTMS 由前期设计的MC 耦合 UMHP 式 BTMS 和多组气凝胶层构成。无Li–ion 电池组时的气凝胶层与 MC–UMHP 结构见图10b,从图 10b 可以发现气凝胶层与 UMHP 组一起构成了多层矩形箱式结构,每个箱体结构恰好为 Li–ion电池单体提供布置空间。气凝胶作为极轻的固体材料,其密度为 3.55 kg/m3,熔点为 1 473 K,导热系数为 0.013 W/(m·K),可以承受相当于自身质量几千倍的压力,绝缘性能是玻璃纤维的 39 倍。具有气凝胶层与 Ve 型 BTMS 结构的 Li–ion 电池组布置平面图见图 10c。图 10c 的上部分图为等比例绘制的俯视图,从整体上展示了 MC 耦合 UMHP 式 BTMS、Li–ion电池组和气凝胶层的相对位置、相对大小和布置方式。图 10c 的下部图为局部放大示意图,更加直观地介绍气凝胶层与 MC 耦合 UMHP 式 BTMS 结构,以及 Li–ion 电池组的布置方式与相对位置。气凝胶层布置于相邻 Li–ion 电池单体与相邻 UMHP 的间隙中,并在 Li–ion 电池组的最外层两侧布置了气凝胶层,由此气凝胶层与 UMHP 组一起对 Li–ion 电池组中的单体电池构建了独立的包覆结构,即每个 Li–ion 电池单体均具有单独的包覆结构。

通过在 MC 耦合 UMHP 式 BTMS 中增加气凝胶填充层的设计可以实现如下设计功能:隔绝 Li–ion电池组内相邻电池的直接接触,防止部分因质量缺陷而失控的 Li–ion 电池对其他正常 Li–ion 电池的破坏,以及引发的一系列连锁反应;Li–ion 电池单体厚度方向两侧的气凝胶填充层与其侧立面两侧的 UMHP 一起形成独立的保温系统,可有效控制单体 Li–ion 电池的温度,以及防止其与外界/相邻物体传递/吸收热量;气凝胶填充层可将 Li–ion 电池组最大温度差转变成Li–ion 电池单体的最大温度差,因此 MC 耦合 UMHP式 BTMS 的温度均衡性能可得到进一步提升。
04、结论
MC 耦合 UMHP 式 BTMS 对 Li–ion 电池散/加热所需时间少,换热效果好。流体入口温度越低,Li–ion电池组所需的降温时间越少,Li–ion 电池组初始温度越低,加热至目标温度所需时间越长;流体入口流速越大,Li–ion 电池组所需的降温时间越少,在流速为3 m/s 时,Li–ion 电池组从初始温度 314 K 降温至目标温度 303 K 所需的时间仅为 135 s;在 Li–ion 电池组初始温度为 258 K 时,此时需要的加热时间为258 s。在各种工况下进行散/加热仿真实验中 Li–ion电池组的最大温差始终小于 5 K,满足 BTMS 设计的温度均衡性要求。通过在 MC 耦合 UMHP 式 BTMS中增加气凝胶填充层的设计,使得 MC 耦合 UMHP式 BTMS 的保温性能、安全性能和温度均衡性能可以更好。
【参考文献】
[1] PESARAN A A. Battery Thermal Models for HybridVehicle Simulations[J]. Journal of Power Sources, 2002,110(2): 377-382.
[2] TARASCON J M, ARMAND M. Issues and ChallengesFacing Rechargeable Lithium Batteries[J]. Nature, 2001,414(6861): 359-367.
[3] 刘霏霏. 微热管在电动汽车电池热管理系统中应用关键技术研究[D]. 广州: 华南理工大学, 2017: 1-221.LIU Fei-fei. Research on Key Technology of ApplyingMicro Heat Pipes in Battery Thermal Management System for Electric Vehicles[D]. Guangzhou: South ChinaUniversity of Technology, 2017: 1-221.
[4] 王振, 李保国, 罗权权, 等. 电动汽车锂离子电池热管理系统研究进展 [J]. 包装工程 , 2020, 41(15):232-238.WANG Zhen, LI Bao-guo, LUO Quan-quan, et al. Research Progress in Thermal Management Systems forLi–ion Batteries in Electric Vehicles[J]. Packaging Engineering, 2020, 41(15): 232-238.
[5] SMITH J, HINTERBERGER M, HABLE P, et al. Simulative Method for Determining the Optimal Operating Conditions for a Cooling Plate for Lithium-Ion Battery Cell Modules[J]. Journal of Power Sources, 2014,267: 784-792.
[6] KUNDU P K, MonDAL S, CHAKRABORTY S, et al.Experimental and Theoretical evaluation of On-ChipMicro Heat Pipe[J]. Nanoscale and Microscale Thermophysical Engineering, 2015, 19(1): 75-93.
[7] ZHAO J, RAO Z, LI Y. Thermal Performance ofMini-Channel Liquid Cooled Cylinder based BatteryThermal Management for Cylindrical Lithium-Ion Power Battery[J]. Energy Conversion & Management, 2015,103: 157-165.
[8] LIU H, EZE C, ZHAO J. Investigation into the Effectiveness of Nanofluids on the Mini-Channel ThermalManagement for High Power Lithium-Ion Battery[J].Applied Thermal Engineering, 2018, 37(7): 511-523.
[9] BAI Fan-fei, CHEN Ming-biao, SONG Wen-ji, et al.Investigation of Thermal Management for Lithium-IonPouch Battery Module based on Phase Change Slurryand Mini Channel Cooling Plate[J]. Energy, 2019, 167:561-574.
[10] AN Z, SHAH K. A Parametric Study for Optimization ofMini-Channel based Battery Thermal ManagementSystem. Applied Thermal Engineering[J]. 2019, 154:593-601.
[11] ZHEN Q, YI M. Thermal Performance of Lithium-IonBattery Thermal Management System by UsingMini-Channel Cooling[J]. Energy Conversion andManagement, 2016, 126: 622-631.
[12] LAN C, XU J. Thermal Management for High PowerLithium-Ion Battery by Mini-channel AluminumTubes[J]. Applied Thermal Engineering, 2016, 25:284-292.
[13] WANG Cong, ZHANG Guo-qing, MENG Li-ke, et al.Liquid Cooling based on Thermal Silica Plate forBattery Thermal Management System[J]. International Journal of Energy Research, 2017, 41(15):2468-2479.
[14] YE Y, SHI Y, SAW L H, et al. Performance Assessmentand Optimization of a Heat Pipe Thermal ManagementSystem for Fast Charging Lithium ion Battery Packs[J].International Journal of Heat and Mass Transfer, 2016,92: 893-903.
[15] LIU H, WEI Z, HE W, et al. Thermal Issues about Lithium Batteries and Recent Progress in Battery ThermalManagement Systems: A Review[J]. Energy Conversionand Management, 2017, 150: 304-330.
[16] DHARAIYA V V, KANDLIKAR S G. A NumericalStudy on the Effects of 2D Structured Sinusoidal Elements on Flow and Heat Transfer at Micro-Scale[J]. International Journal of Heat and Mass Transfer, 2013, 57:190-201.
[17] LEE P S, GARIMELLA S V. Thermally DevelopingFlow and Heat Transfer in Rectangular Microchannelsof Different Aspect Ratios[J]. International Journal ofHeat and Mass Transfer, 2006, 49(17): 3060-3067.
[18] 史周浩, 谢占山, 施卫东, 等. 基于正交试验的微通道翼形流场特征分析[J]. 流体机械, 2021, 49(12):42-48.SHI Zhou-hao, XIE Zhan-shan, SHI Wei-dong, et al.Analysis of Microchannel Airfoil Flow Field Characteristics based on Orthogonal Experiments[J]. Fluid Machinery, 2021, 49(12): 42-48.
[19] MENTER F. Zonal Two Equation K-W TurbulenceModels for Aerodynamic Flows[C]// 23rd Fluid Dynamics, Plasmadynamics, and Lasers Conference, Orlando, FL Reston, Virginia: AIAA, 1993: 2906.
[20] WANG Zhen, LI Bao-guo, LUO Quan-quan, et al. Effectof Wall Roughness by the Bionic Structure of DragonflyWing on Micro-Fluid Flow and Heat Transfer Characteristics[J]. International Journal of Heat and Mass Transfer, 2021, 173: 121-201.
[21] 黄文华, 韩晓东, 陈全世, 等. 电动汽车 SOC 估计算法与电池管理系统的研究[J]. 汽车工程, 2007, 29(3):198-202.HUANG Wen-hua, HAN Xiao-dong, CHEN Quan-shi,et al. A Study on SOC Estimation Algorithm and BatteryManagement System for Electric Vehicle[J]. AutomotiveEngineering, 2007, 29(3): 198-202.
- 下一篇:内燃机内部流场测量
- 上一篇:增压双VVT汽油机缸内充量工程化建模方法
编辑推荐
最新资讯
-
标准解读丨ISO 21111 《道路车辆车载以太网
2025-03-31 19:15
-
清研精准兆瓦级充放电测试设备——重新定义
2025-03-31 19:13
-
强强联合:imc FAMOS内嵌Python接口,提高
2025-03-31 19:12
-
汽车动力电池与发动机系列标准宣贯会在武汉
2025-03-31 16:08
-
氢内燃机2.0-西南研究院(SwRI)启动第二阶
2025-03-31 16:06