一种电池包底部抗碰撞性能的测试方法研究
文章来源:吉利汽车研究院(宁波)有限公司
0引言
由于道路路况复杂,电动汽车的电池包通常布置于车辆底部。在实际的行驶过程中,电池包底部容易受到各种异物的冲击,造成不同程度和多种形式的损伤。电池包结构受损,正负电极容易短路并引起内部温度急剧升高,最终致使电池自燃。车辆电池包底部损伤主要有水平撞击、翻转撞击和负坎工况3种形式。水平撞击主要发生在平坦路面上,车辆行驶过程中电池包底部被在竖直方向存在高差的固定物体撞击;翻转撞击主要发生在平坦路面,车辆行驶过程中电池包底部被在竖直方向存在高差的非固定物体撞击,撞击过程中该物体出现运动;负坎工况主要发生车辆行驶过程中路面存在明显高差,车辆底部前端的副车架等车体结构容易避开障碍物,使电池包底部直接与障碍物撞击,造成电池包底部严重损伤。根据调查分析,售后调查的电池包的损伤场景发生在负坎工况。
1负坎试验测试系统设计
负坎试验测试系统主要有跑道系统、牵引系统、数采系统、灯光摄像系统和触发系统。其中牵引系统、数采系统和灯光摄像系统在市场上已有成熟的测试设备,但跑道系统和触发系统需要单独进行设计。
1.1跑道台架设计1.1.1试验跑道如图1所示,跑道主要由斜坡、高台阶跑道、低台阶跑道和冲击壁障4个部分组成。斜坡主要目的是保证车辆顺利运行至高台阶跑道上面。为了保证力墙传感器和冲击壁障的安装,将跑道进行了抬高设计,高台阶跑道离地高度330mm,长度需保证车辆前后轮从斜坡上来后均在其上方运行。车辆行驶上高台阶跑道后须保证一个车位运行距离,结合车型轴距,高台阶跑道长度设计为6m。
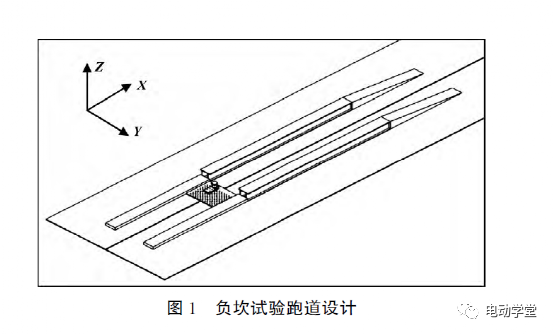
为减小斜坡对加速度分量的影响,计算跑道斜坡角度控制在6°以下,最后推算斜坡长度约3m。低台阶跑道的高度可调,以实现车辆负坎高度的调节,同时也避免车辆从高台阶跑道下落时直接撞击试验地面,造成试验场地损坏。此次试验的低台阶跑道高度为110mm。因此该试验方案的负坎高度为220mm。整个试验过程中,利用实车碰撞试验的牵引系统驱动试验车辆运行,从斜坡运行至高台阶跑道上并继续向前运行。当车辆从高台阶跑道开始跌落时,牵引系统与试验车辆分离。车辆从高台阶跑道跌落过程中,电池包底部与撞击壁障发生接触冲击。
1.1.2撞击壁障设计行驶过程中的车辆具有很大的动能,当汽车底部的电池包与地面异物碰撞时,其动能将导致接触区材料快速进入塑性状态,极大影响电池包的安全性。汽车电池包与道路异物撞击时具有很多非线性表现,这些非线性表现由车辆的运动状态、道路异物的几何形状等不确定因素所决定,因此汽车电池包和道路异物的碰撞问题比较复杂。
为了简化模型,提高试验结果的可对比性以及试验过程的安全性,在车辆负坎试验中,设计如表1所示的壁障尺寸,模拟负坎时的面面接触形式,撞击壁障如图2所示。
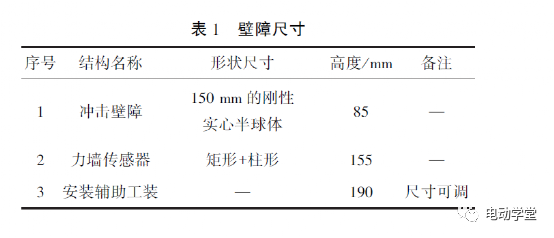
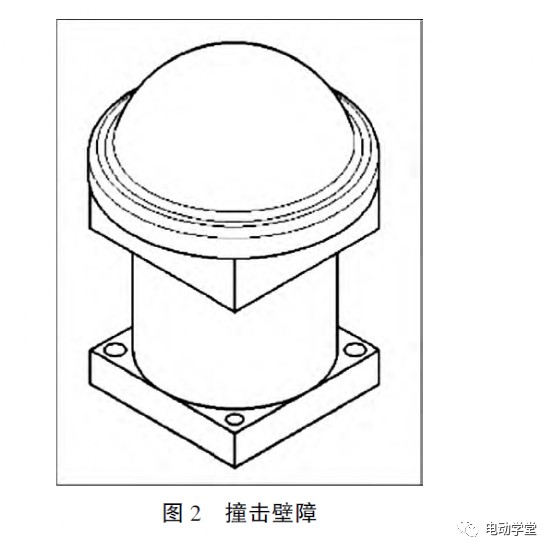
1.1.3撞击壁障安装位置的确定如图3所示,撞击壁障中心线X方向距离高台阶跑道30mm,壁障高度距离地面430mm,即高出高台阶跑道100mm。
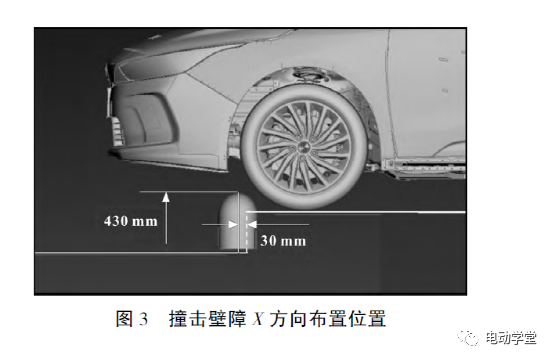
如图4所示,撞击壁障中心线Y向距离车辆纵向中心线40mm。
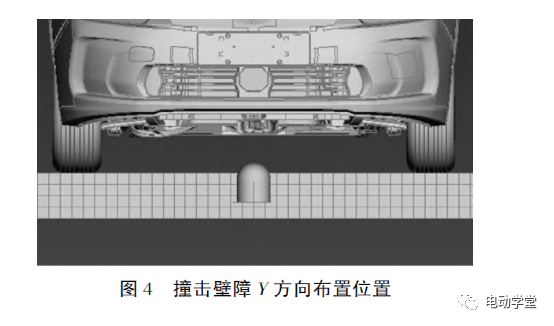
1.2触发系统的设计传统触发是通过带状开关撞击实现数采系统的触发。但在负坎试验中通过带状开关触发会影响撞击壁障和车辆的重叠量,同时对电池包底部撞击点的损伤程度也有一定影响。因此根据数采系统触发原理,设计了非接触式的红外触发系统,如图5所示。红外触发系统的信号处理模块根据红外线激光的变化进行信号处理,然后通过继电器模块产生高低电平信号,实现高压电测量系统触发。同时,可以根据触发时刻确认数采系统零时刻。
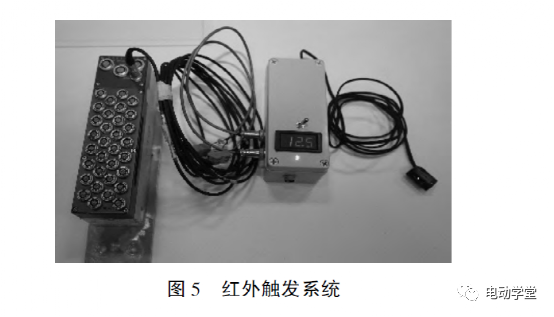
1.3负坎试验速度确定负坎工况的电池包底部剐蹭主要出现在车辆低速行驶过程中,同时如果速度过快车辆将可能由于惯性从壁障上方飞过从而不能与壁障发生接触。结合负坎高度和壁障高度,经过分析调试确认此次负坎试验速度设定为20km/h。车辆通过牵引系统加速,在高台阶跑道上速度达到20km/h后跌落,复现负坎工况。
2负坎试验及电池包底部损伤分析
试验后底部损伤照片,如图6所示。
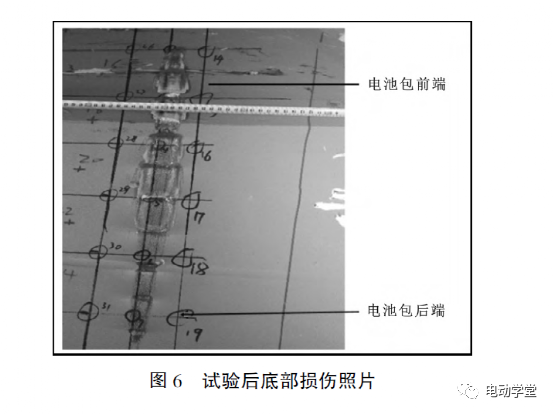
在负坎试验工况下,呈现面面接触形式。电池包与壁障接触面积较大,集中载荷较小,底部没有被壁障击穿,接触区域出现隆起和较大面积变形。电池包底部在与撞击壁障主要呈现塑性变形。试验过程中,电池包未出现开裂或者击穿。壁障Z方向力最大值为25300N,X方向力最大值为4093N。撞击壁障Z方向力如图7所示。
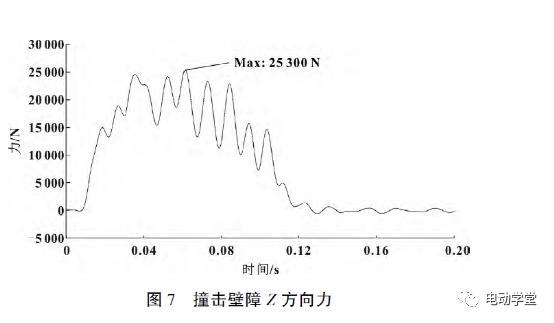
3结论
本文介绍了一种用于检测电池包底部防护性能的负坎试验方法,设计的壁障以及撞击壁障可以在X、Y、Z3个方向可调,以满足轿车和SUV车辆的不同重叠量测试需求,用于复现实际场景中电池包的损伤情况,也可以用于验证汽车电池包在负坎工况中的抗冲击性能。同时也设计了一种非接触式触发系统,代替了传统的接触式触发方式实现了数据采集系统的触发和高压电的零时刻确定。
电池包底部损伤过程复杂,主要有塑性变形、开裂和击穿等失效模式。试验主要复现了电池包的塑性变形,未能复现电池包的开裂和击穿等失效模式,后期可以调整壁障形式实现在负坎工况中,对电池包损伤进行更深的损伤研究。
编辑推荐
最新资讯
-
全球首次!IVISTA 2023版修订版引入带灯光
2025-04-28 09:59
-
我国首批5G毫米波行业标准送审稿审查通过
2025-04-28 08:56
-
5/16 厦门- 新能源汽车电驱测试技术的创新
2025-04-28 08:53
-
国内首个汽车电磁防护技术验证体系EMTA正式
2025-04-28 08:49
-
一文带你了解滤波器
2025-04-28 08:35