清华丨新型分布式驱动液氢燃料电池重型商用车设计、分析与验证
根据重型商用车动力系统高性能、长续航里程、低成本的开发需求,本文提出了分布式驱动液氢燃料电池重型商用车技术方案,探索性地应用了大功率燃料电池系统、大容量车载液氢储供系统和分布式电动轮驱动系统等多项创新技术。基于燃料电池系统设计与匹配技术,开发了国内首套上公告的百千瓦级燃料电池系统(109 kW);. 基于车载液氢储罐设计、液氢汽化器设计和车载液氢BOG 处理与全系统安全监控等关键技术突破,研制了国内首套车载大容量液氢储供系统(60 kg/110 kg);基于轮毂电机磁热设计、构型设计和集成设计创新,研制了适用于重型车辆双胎并装车轮的电动轮,所开发的电动轮单轮峰值转矩16 000 N·m,短时峰值转矩超过18 000 N·m,电动轮峰值转矩密度可达60 N·m/kg。基于上述关键部件技术,完成了全球首辆分布式驱动液氢燃料电池重型商用车开发,设计续驶里程超过1 000 km,所研制的35 t级与49 t级重型商用车分别进行了道路试验,验证了液氢储氢、动力系统与分布式电驱动系统的技术可行性,为重型商用车的电动化探索了可行的方向。
关键词:重型商用车;液氢燃料电池;分布式驱动;新能源商用车
前言
交通行业消耗了我国50%的石油消费总量,并产生10%的二氧化碳总碳排放量[1],以节能减排为核心的交通电动化升级,是支撑国家“双碳”战略目标与能源安全转型重大战略需求的关键技术。
我国新能源汽车市场增长十分迅速。乘联会统计的数据显示,我国2021 年新能源汽车销量达到352.1 万辆,同比增长157.5%,汽车电动化升级已经进入加速阶段。
工信部于2020 年制定的《推动公共领域车辆电动化行动计划》中提出:“目前我国的重型商用车保有量已超850万辆,工程机械保有量也超过了800万辆,如果将这1 650万辆重型商用车和工程机械全部电动化,在全部应用清洁能源的前提下,每年可直接减少二氧化碳排放9 亿t,占全国二氧化碳排放的近9%,节能减排效果显著”。但是,商用车电动化升级对成本和性能也更为敏感,是国内外新能源技术竞争的焦点与难点。
氢燃料电池功率大、能量密度高、零排放,被认为是大负载、长距离重型商用车的理想技术方案[2-3]。目前,国内外的汽车厂商和专家学者对燃料电池重型商用车已经开展了一些探索,陆续完成了一些概念车型开发,如图1 所示。自“十五”以来,我国持续探索以商用车为代表的燃料电池汽车发展路线。目前,轻中型的燃料电池物流车技术发展十分迅速,已有多款车型完成公告,并累计生产超过3 000辆,占总保有量的50%左右[4]。随交通电动化的需求越来越迫切,中重型氢燃料电池商用车近两年持续升温,成为国内外技术竞争的焦点。
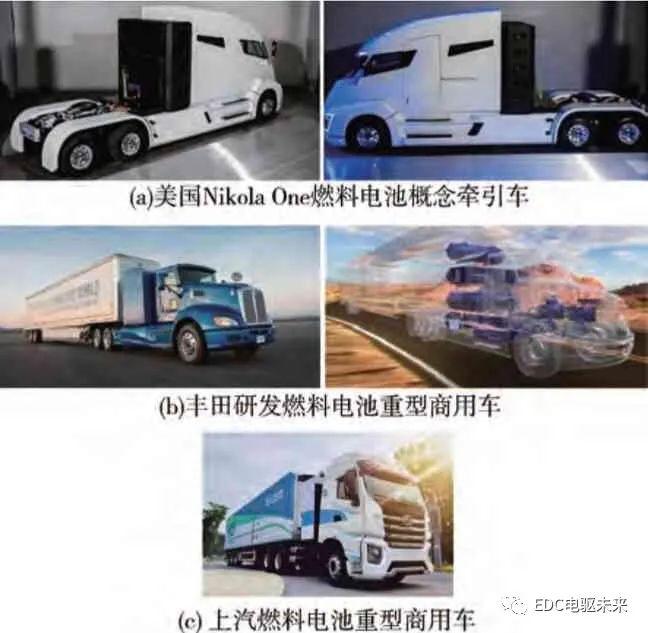
图1 国内外燃料电池重型商用车研发车型
表1列出当前国内外燃料电池重型商用车的主要性能。由表可见,其续驶里程普遍在400 km水平,一般不超过600 km,已成为重型长途燃料电池商用车的主要短板。
表1 国内外氢燃料电池重型商用车性能
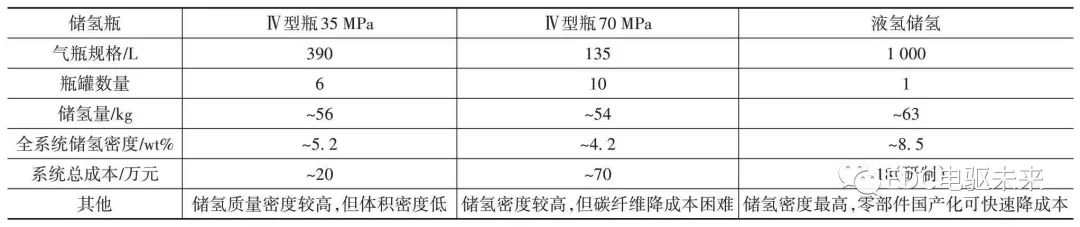
提高续驶里程的关键在于增加整车携氢量与提高系统的能量转化效率。从能量流与动力系统的角度出发,则须突破高效大功率燃料电池、高密度储氢[5-6]和高效率电传动技术[7-8]等关键技术。
目前,针对干线物流重型商用车的电动化技术仍在探索中,产业与学界对此提出了一系列的创新思路[9-12],但与之对应的应用开发研究十分不足,各项关键技术也尚未形成明确的技术路线。本文中针对城市重型、长途货运重型商用车的电动化需求,提出了分布式驱动液氢燃料电池重型商用车技术方案,探索了大功率燃料电池系统、大容量液氢系统和大功率轮毂电机等前沿技术的设计与开发,完成了2 辆35 t级液氢燃料电池载货车和2辆49 t级液氢燃料电池牵引车的设计、集成、制造和测试。
1 重型商用车动力系统构型分析与设计
1.1 动力系统构型设计
商用车是重要生产工具,其电动化转型既须保证性能与燃油车相当,更须控制成本的增加。从全生命周期成本分析,商用车的总燃油成本是其购置成本的5~10 倍水平[13],如何提高动力系统效率、降低燃料成本,是推动商用车电动化升级的关键。
燃料电池商用车动力系统结构相对简单,其效率主要取决于燃料电池系统效率和驱动系统效率。
目前,电动汽车主要使用了集中电驱动与分布式电驱动两种构型[14-15]。图2 对比了两种典型动力系统的传动效率,集中驱动与传统动力系统构型相似,通过变速器、主减速器和轮边减速器等传动机构,将一台大功率电机的驱动转矩传递至各个轮胎,其技术方案可参考传统动力系统,相对较为成熟,但由于传动链较长,没有充分发挥电传动的高效优势,部分低载荷区的效率甚至会降低到60%左右[16]。
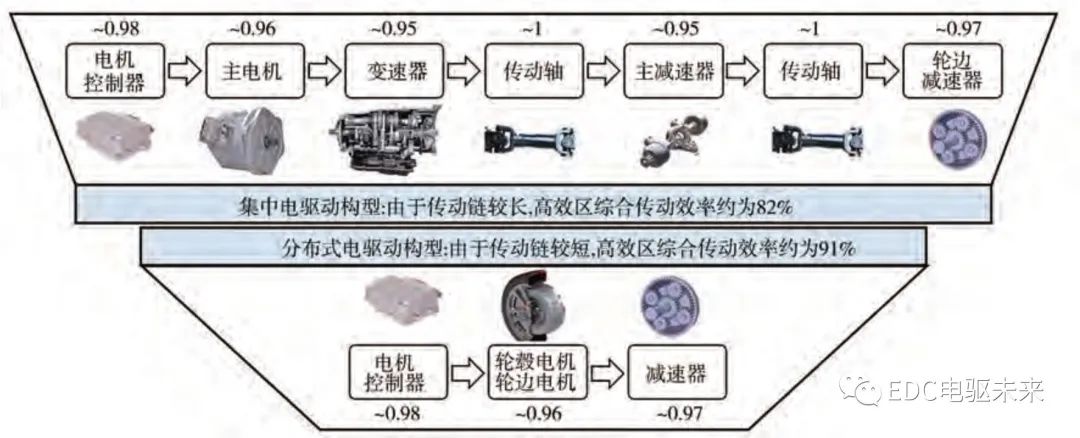
图2 分布式电驱动与集中式驱动效率对比
对比图2所示两种传动系统构型和各传动部件效率,分布式电驱动系统构型可以有效缩短传动链,相比集中式电驱动构型有望将整车驱动效率提升近10%[17],并大幅简化驱动系统的布置。根据汽车生命周期成本评估方法[18],汽车全生命周期总成本为

式中:TC 表示汽车在全生命周期所发生的总成本;IC 表示购置成本;OCn 表示运营成本,包括汽车n 年使用过程中所花费的能源费用、维护费用、税与保险和其他成本的总和;SV表示汽车处置时的残值。
运营成本包括能源成本、维护成本和税费、保险费等。其中,能源成本为
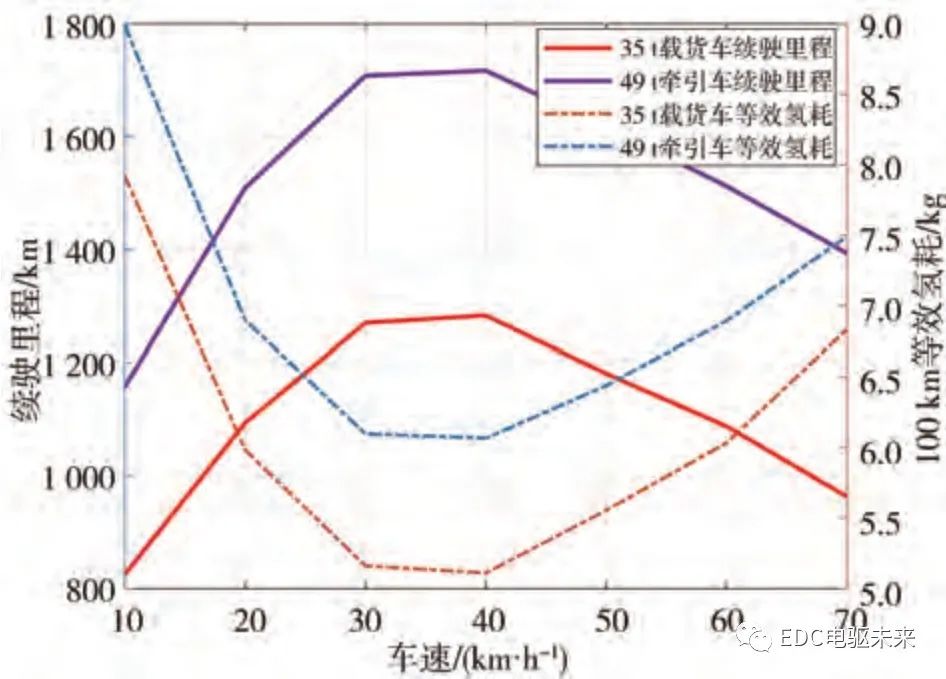
式中:N为氢燃料电池汽车每100 km氢耗,kg/100 km;P表示氢气价格,元/kg;D表示汽车总行驶里程,km。
考虑商用车运营成本可达到购置成本的10 倍,如果驱动系统效率提升5%~10%,所节省的费用相当于现有整车购置费用的50%~100%,使用成本下降∆EC 完全可以覆盖电驱动系统的成本增加∆IC,从而显著降低商用车全生命周期使用成本。这也是本文选择分布式驱动方案的主要原因。
据此,本文针对重型商用车应用需求,提出了面向35 t 级燃料电池重型商用车的8×4 分布式驱动方案,和49 t级燃料电池重型商用车的6×4分布式驱动方案,以探索重载电动轮的技术可行性。
氢燃料电池系统是重型商用车开发的难点。重型商用车功率需求大、续驶里程长,需要突破100~200 kW 水平的高效燃料电池系统与100 kg 级的储氢系统两项关键技术。
高压储氢技术存在体积质量大、加氢慢、成本高等问题,难以适用于大容量储氢系统的需求。液氢技术储氢密度高,加注方便,国外已应用于氢气大规模输运与站上储氢,被认为是大容量车载储氢的重要技术方向。国内液氢主要应用于航天领域,在本文工作前尚未在车载领域得到应用探索。
十三五以来,我国车载液化天然气(liquefied natural gas,LNG)技术发展已十分成熟,全产业链逐一实现了国产化,使单罐售价已降至3 万元以下[19]。液氢储氢在核心零部件上与LNG 具有技术相似性,基于LNG 技术的开发经验,本文中拟探索大容量车载液氢储氢技术方案。
储氢技术方案成本对比如表2 所示,从最核心的成本角度分析,液氢系统具备降低成本的巨大潜力。即使在研制阶段,其性能与成本也比35 与70 MPa 的IV 型瓶有显著优势,未来全系统国产化后,更是有望将储氢成本降至1 000元/kg以下。
表2 储氢技术方案对比
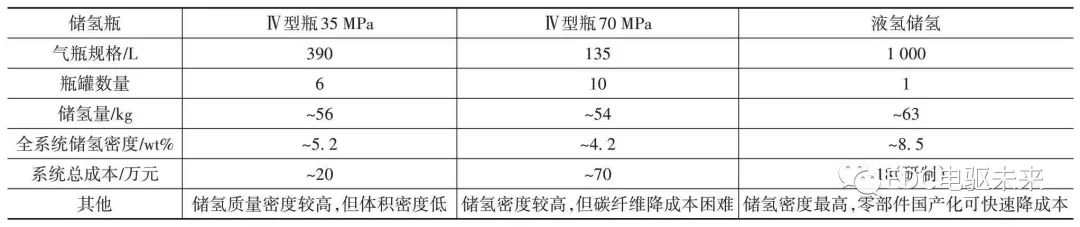
基于上述分析,本文以液氢储供与分布式驱动作为主要创新点,提出了分布式驱动液氢燃料电池重型商用车构型,如图3 所示,并以此开发了35 t 级载货车和49 t 级牵引车两款重型商用车车型。
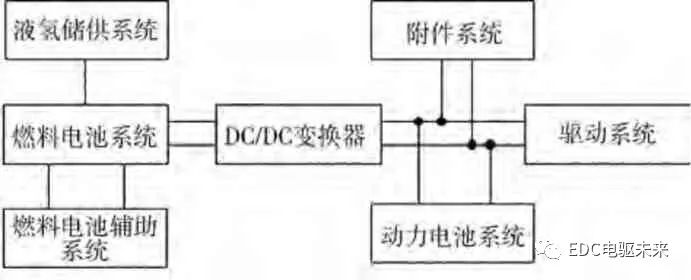
图3 动力系统总成拓扑结构
该动力系统构型主要包括由燃料电池系统、液氢储供系统与动力电池系统组成的混合动力系统、电动轮与驱动桥控制器组成的电驱动系统和其他附件系统构成。
其中,燃料电池系统包含燃料电池、燃料电池辅助装置和DC/DC 变换器,通过DC/DC 变换器、燃料电池系统与动力电池组成串联混合动力系统;液氢储供系统向燃料电池供氢,主要包含液氢瓶、复合汽化器、缓冲罐、挥发氢气回收系统和氢系统控制器等部件;电驱动系统包含4 个相同的轮毂电机独立驱动电动轮和两个驱动桥控制器,每个驱动桥控制器上集成了同桥左右两侧电机的电机控制器,两套电机控制器共用低压逻辑单元和冷却水路。
所开发的动力系统总成具有以下特点和优势:
(1)驱动高效率:分布电驱动系统可以最大限度地提升驱动效率;
(2)燃料电池高效率:串联混合动力系统使燃料电池输出功率与整车功率需求解耦,燃料电池系统可以稳定工作在高效区;
(3)高动力性:动力电池系统可以提供系统所需的瞬时高功率,快速响应整车动力需求[20]。为节省底盘布置空间,动力电池电量相对较小(<100 kW·h)而峰值功率较大(>500 kW),因此采用大倍率功率型电池;
(4)热管理高效率:液氢系统不仅可以提升储氢密度,通过综合热管理,利用液氢挥发吸热能力还能消纳燃料电池系统的部分散热压力。
1.2 整车设计参数与动力系统参数匹配
针对典型重型商用车性能需求[21],所设计的35 t和49 t级燃料电池重型商用车的基本参数如表3所示。
表3 燃料电池重型商用车设计参数与性能指标
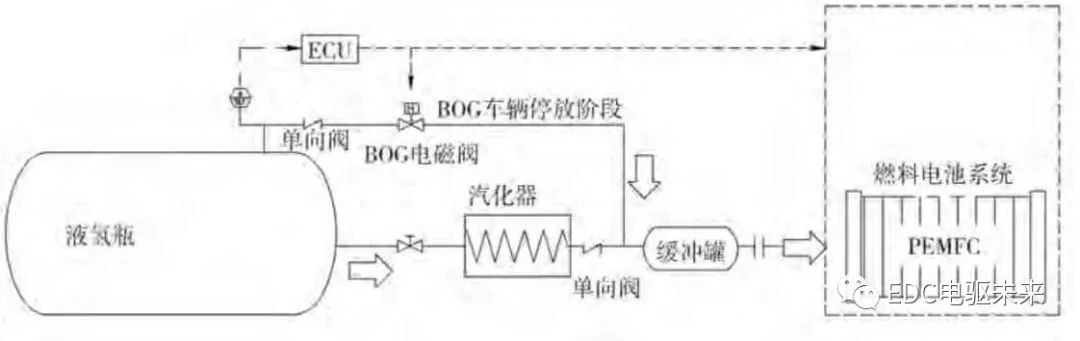
1.2.1 燃料电池系统参数设计
由于目标车型的高速、重载和车辆加速制动频繁的特点,为保护燃料电池的耐久性,适应燃料电池系统相对较低的响应速度,采用燃料电池系统提供车辆行驶的稳态输出功率,瞬态大功率需求由动力电池系统补足的策略。这一策略可以保证燃料电池系统工况平稳、提高系统效率和整车的动力性与动力学响应速度。
根据汽车纵向动力学功率平衡方程,电驱动系统对混合动力系统的总功率需求为

式中:η为电驱动系统效率;m 为整车质量,kg;f为轮胎的滚动阻力系数;α 为地面坡度角,(°);CD 为空气阻力系数;A 为汽车迎风面积,m2;ρ 为空气密度,kg/m3;u为行驶车速,m/s;δ为旋转质量换算系数。
35 t 级载货车,以持续最高车速80 km/h 在水平路上行驶时,所需混合动力系统功率为
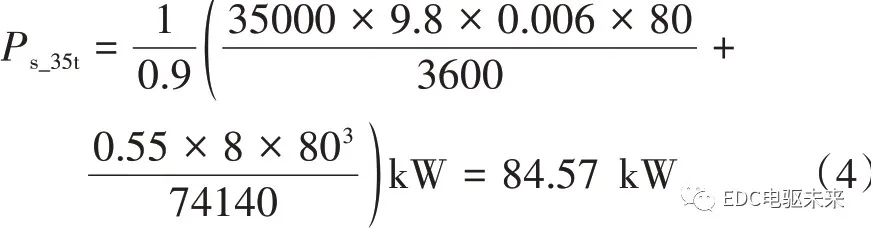
49 t 级牵引车,以持续最高车速90 km/h 行驶时,所需混合动力系统功率为
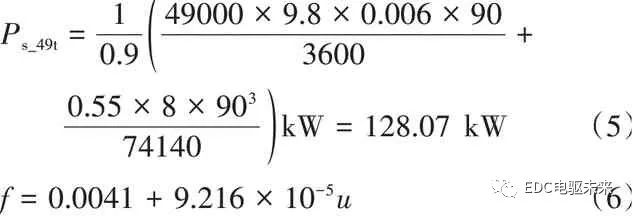
其中,轮胎的滚动阻力系数根据货车轮胎滚阻经验公式[22]确定,如式(6)所示;电驱动系统效率包括电机控制器效率和电动轮平均减速器效率,根据仿真和试验结果,取η = 90.0%。考虑到整车存在附件系统与燃料电池附件系统用电功率与DC/DC 变换器的效率,综合考虑车辆稳态行驶下的最高功率需求,最终选定动力系统中的燃料电池系统方案为:35 t级载货车的燃料电池系统由单台额定功率100 kW燃料电池组成,49 t 级牵引车的燃料电池系统由两台并联的额定功率100 kW燃料电池组成。
1.2.2 动力电池参数设计
燃料电池系统作为车用电源有效率高、污染小、续驶里程长、运行平稳和振动噪声低等优点,但同时也存在一些问题。动力电池系统相比燃料电池系统具备响应速度快和峰值功率高的特点,可以满足整车频繁的加速、制动等工况的功率响应需求与大功率输出及能量回馈要求。因此,本文中采用的燃料电池混合动力系统构型将燃料电池系统通过DC/DC变换器与动力电池系统并联,共同为驱动系统提供能源,采用该构型动力电池可回收再生制动的能量和吸收燃料电池富余的能量;动力电池作为燃料电池的输出功率平衡器,可以调节燃料电池的效率和动态特性,改善整车燃料经济性,提高动态响应速度。
整车在加速或爬坡过程中,功率需求高,燃料电池无法快速响应,由动力电池瞬时大功率放电;在整车制动工况过程中,不再消耗动力系统能量,此外由于燃料电池响应慢,依然保持功率输出,此时要求动力电池具备吸收瞬间大功率的能力,否则会拉高母线电压,造成负载过压保护。因此,动力电池最大放电功率须满足:

式中Pfc 为燃料电池净输出功率。为满足续驶里程指标,匀速行驶工况下,动力电池容量须满足:

式中:Ubat 为动力电池总线电压;Lm 为续驶里程;k(SOC)为与动力电池常用使用区间相关的系数,取值0~1。
通过对本文设计的单台额定功率100 kW 燃料电池的性能特性分析,燃料电池最大净输出功率109 kW,动力电池在工作过程中须具备不小于109 kW的回馈能量能力。由于动力电池在高SOC区间峰值充电能力弱,在低SOC 区间峰值放电能力弱,无法同时满足大倍率的充放电要求,故混合动力系统中动力电池的SOC 使用区间一般为30%~80%,根据不同的系统需求会有一定变化。
根据燃料电池工作电压范围和两型燃料电池重型商用车的动力系统构型,为35 t级燃料电池载货车匹配了最大持续放电功率196 kW、峰值放电功率480 kW的动力电池系统;为49 t级燃料电池牵引车匹配了最大持续放电功率147 kW、峰值放电功率700 kW的动力电池系统。具体性能指标如表4所示。
表4 动力电池系统性能参数

1.2.3 电动轮系统参数设计和整车动力性能校核
重载电动轮需要满足大载荷、大功率、大转矩和高效率的需求[23]。通过构型比较,采用中速电机+一级减速的电动轮构型方案。该构型可兼顾高转矩与高功率,适合多数载荷较大的场景。通过电机设计优化,达到了较高的最高效率和较宽的高效区分布;通过电机与减速器的匹配优化,电动轮可以更多地工作在高效区,实现较高的经济性。
基于表3选定的构型方案与动力系统峰值功率和转矩需求,初步明确电动轮的设计性能参数如表5所示。
表5 电动轮系统性能参数
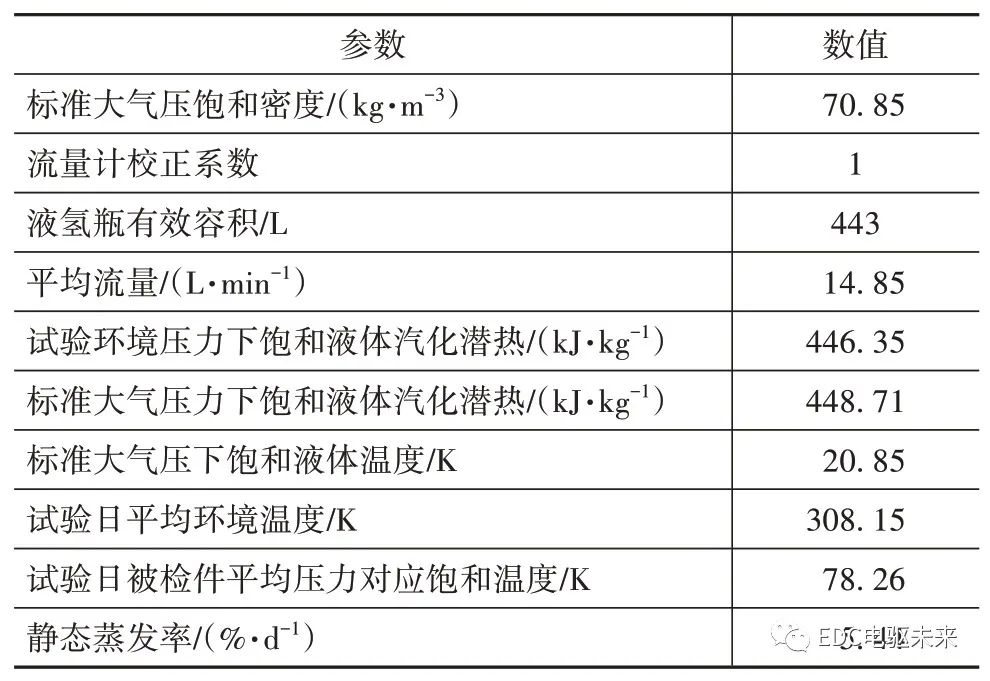
基于上述电动轮参数设计,按照取ηm = 96.0%的电动轮平均减速器效率,电动轮的峰值转矩达到了16 700 N·m,短时峰值转矩可达18 350 N·m。
基于整车基本参数和设计的电动轮系统参数,可以进行35 t 级载货车和49 t 级牵引车两型燃料电池重型商用车的动力性能指标校核计算。
根据运动学关系,两型燃料电池重型商用车的最大车速可达100 km/h 以上,符合一般重型商用车的高速巡航需求,即
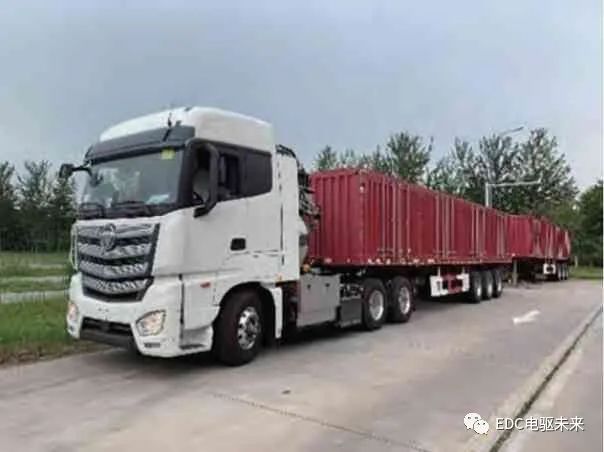
式中:nmax为驱动电机最大转速;i为电动轮减速器速比;R为电动轮轮胎有效半径。
式(3)所示的汽车纵向动力学功率平衡方程中,将电驱动系统效率η 替换为电动轮平均减速器效率ηm,计算平直路面下,满载车辆以峰值最高车速100 km/h行驶时,电动轮驱动电机总输出功率需求:
35 t级载货车,驱动电机总输出功率为
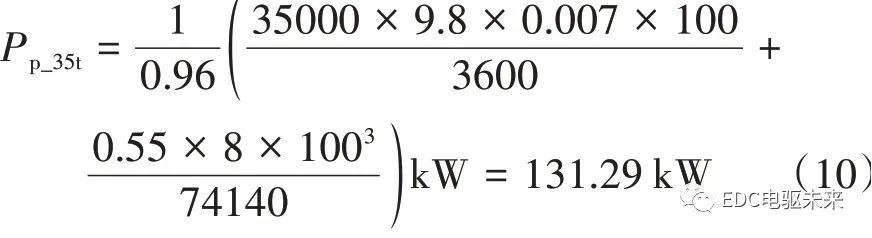
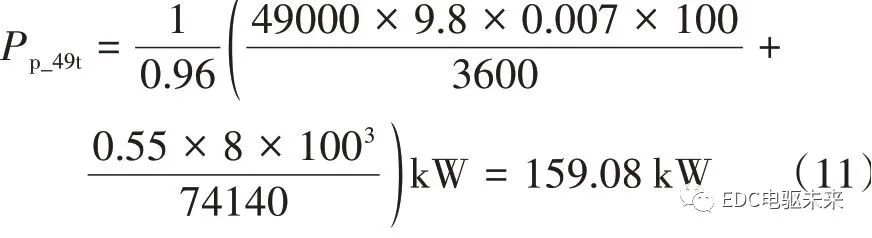
49 t级牵引车,驱动电机总输出功率为根据设计驱动电机的额定功率60 kW,4台驱动电机总额定功率可达240 kW,符合一般重型商用车高速巡航需求车速100 km/h的持续驱动功率需求。35 t 级载货车以20 km/h 车速通过坡度25%,即坡角为14.04°的坡道时,驱动电机总输出功率需求为
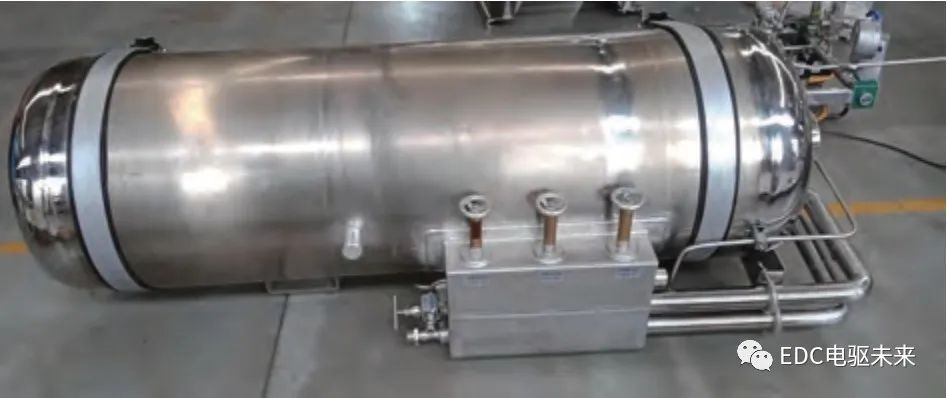
49 t 级牵引车以20 km/h 车速通过坡度20%,即坡角为11.31°的坡道时,驱动电机总输出功率需求为
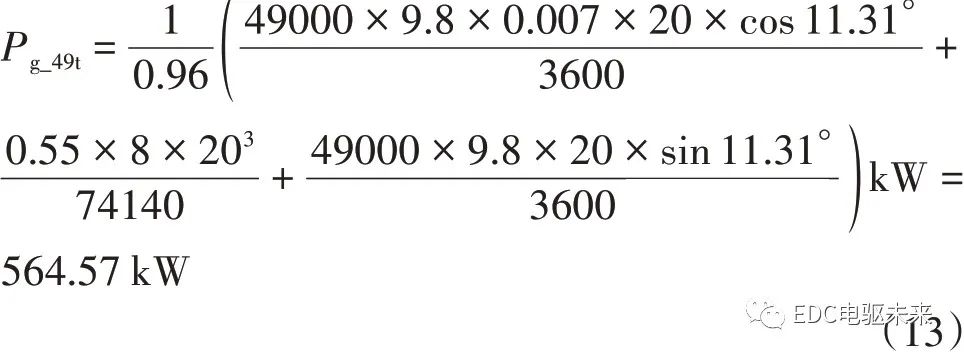
根据设计驱动电机的短时峰值功率180 kW,4 台驱动电机总峰值功率720 kW,符合本论文设计的两型燃料电池重型商用车的最大爬坡度性能指标。
基于燃料电池、动力电池与电动轮的初步参数设计,对整车加速动力性分析如图4 和图5 所示[24]。对于35 t级载货车,若动力系统提供峰值功率(动力电池、燃料电池满功率输出),0-100 km/h 加速时间需23.17 s,0-60 km/h 的加速时间为8.3 s;若燃料电池不输出功率、仅由动力电池提供额定功率,0-60 km/h 的加速时间也可保证在20.07 s 以内,具有较好的动力性。对于49 t 级牵引车,若动力系统提供峰值功率,0-100 km/h 加速时间需36.00 s,0-60 km/h 的加速时间为12.67s;若动力系统仅由动力电池提供额定功率、燃料电池不工作,0-60 km/h 的加速时间为46.73 s。
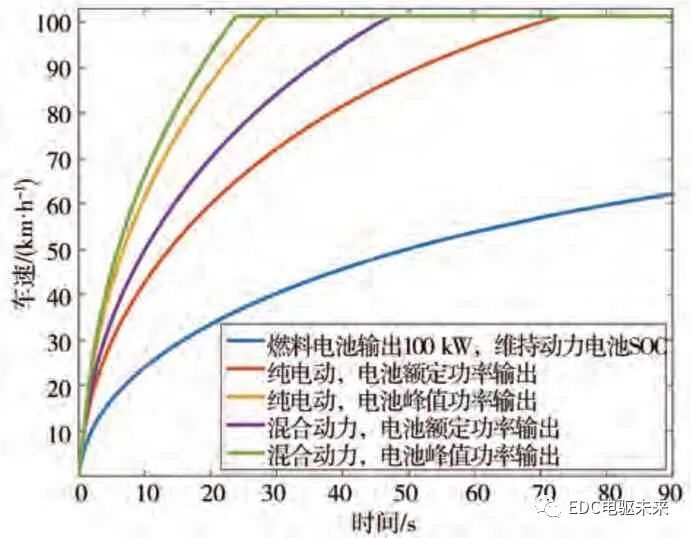
图4 35 t级重型商用车加速性能分析
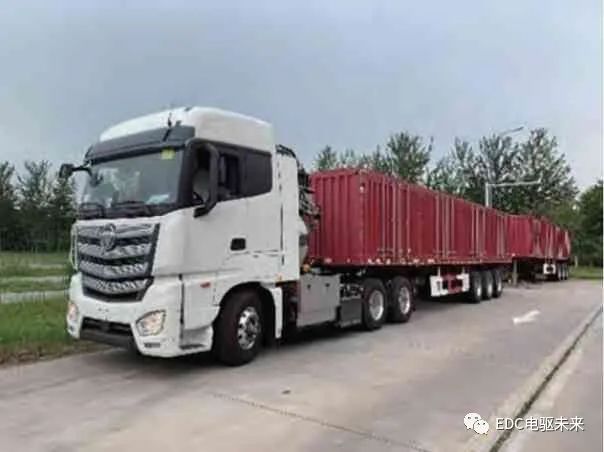
图5 49 t级重型商用车加速性能分析
基于所设计的分布式驱动系统,重型商用车的爬坡性能也得到显著提升。基于爬坡状态下的整车行驶阻力平衡图与动力系统功率平衡图分析[24],在动力系统峰值功率工况下,35 t 级载货车动力系统可满足40%爬坡需求并维持16.80 km/h 车速,49 t级牵引车动力系统可满足25%爬坡需求并维持14.10Km/h车速。
综上所述,结合动力系统功率能力,本文设计的电动轮性能可以满足两型重型商用车爬坡、最高车速、巡航车速能力的预设性能指标。
进一步分析两型重型商用车的续驶里程,基于动态规划算法计算C-WTVC 驾驶循环下的最长续驶里程[25-26],结果如表6所示。此时两型重型商用车的等效100 km氢耗分别为10.80和14.91 kg/100 km,最大续驶里程分别可达615.3和768.7 km。
表6 C-WTVC循环工况分析结果
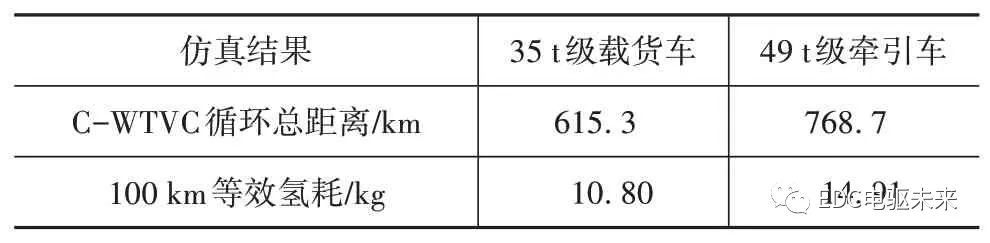
考虑重型商用车主要工况为高速巡航,图6 展示了不同巡航速度下,重型商用车的100 km 氢耗的计算结果。由图可见,在60 km/h 工况下,两种车型的续驶里程可分别达到1 088 和1 512 km。这也验证了液氢系统对于续驶里程的积极效益。
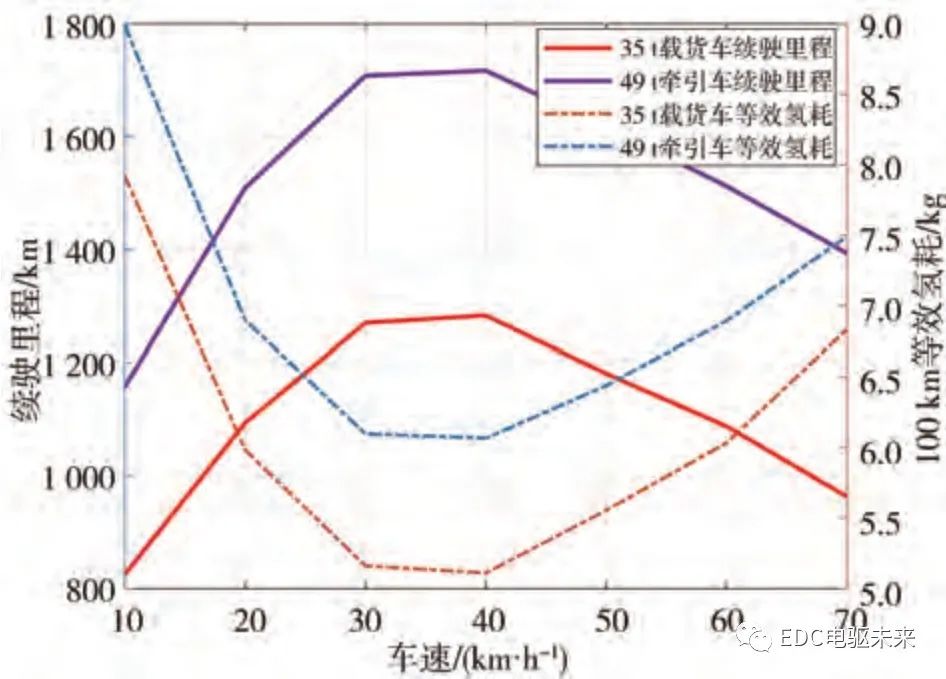
图6 匀速续驶里程和100 km氢耗曲线
2 分布式驱动系统设计
2.1 高转矩密度轮毂电机设计
簧下质量是制约电动轮使用的关键因素,如何提高电机转矩密度,降低轮毂电机质量是本文关注的重点。
为提高电机的峰值功率,电机采用端部直接油冷散热方案,冷却油直接与电机端部绕组接触。端部喷淋油冷方式大大缩短了热量传递路径,提高了散热效率,提升了电机额定与峰值转矩[27-29]。
针对油冷需求,轮毂电机引入了定子油路系统,以外部油泵驱动冷却油循环,内部在电机机壳端部开设淋油口,冷却油在重力作用下淋至电机的端部绕组。由于绕组的轴向导热系数远高于径向导热系数,故该方案在冷却定子端部绕组后,中心绕组的热量可以快速通过轴向传输到端部完成热交换,有效缩短热量传递路径,避免了水冷方案冷却水无法直接与电机端部接触散热而导致的端部热孤岛现象[30]。通过仿真得到的电机额定工况下不同散热方式时的温度分布如图7所示。由图7可以看到,相同电机工况下,油冷方式下的电机最高温度比水冷降低了30.3 ℃。
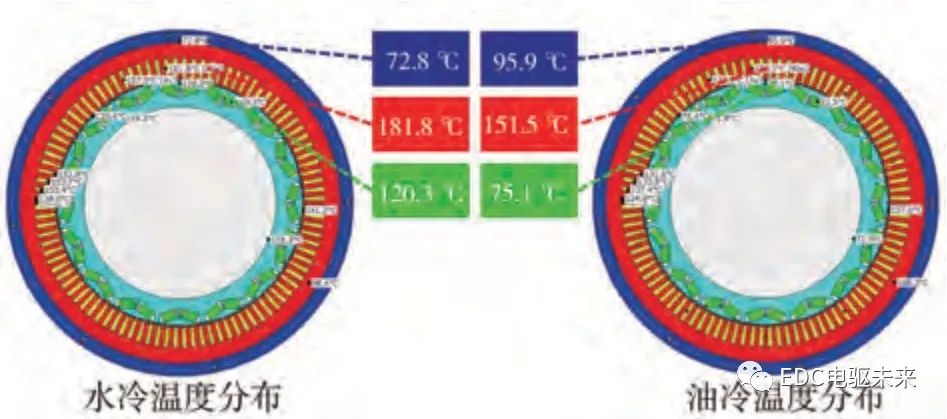
图7 电机水冷与油冷温度分布示意图
进一步地,在实际电机设计时,往往会根据材料特性设置一个散热的边界条件,如C 级绕组稳态工作最高温度≤155 ℃。在此条件下对电机在相同散热要求下进行仿真,结果见图8。
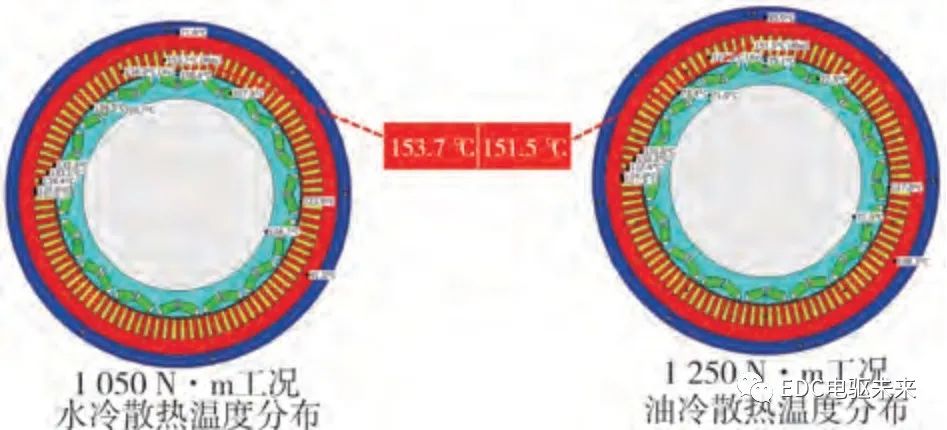
图8 限值温度下的电机水冷与油冷温度分布示意图
由图可见:(1)在水冷方式下,电机转矩在1 050 N·m时绕组最高温度为153.7 ℃;(2)在油冷方式下,电机转矩在1 250 N·m时绕组最高温度为151.5 ℃。
由此可得,在相近的温度要求下,油冷散热方式电机的转矩密度提升了20%左右,油冷电机方案有效提高了电机的功率密度。
针对减质量需求,本文还探索了一种弯扭解耦构型,如图9 所示。传统电动轮的薄壁承力结构,轮毂电机壳体既承重力又传递转矩,易受力变形,影响定转子气隙。本构型通过将轮毂电机的承弯与承扭结构功能解耦,套筒-车轴主要承力(图中红线),电机壳体不传递弯矩仅传递转矩(图中蓝线),使电机结构可大幅减薄,所集成的高效率大转矩电动轮的转矩密度可达60 N·m/kg,有效减轻了簧下质量[31]。
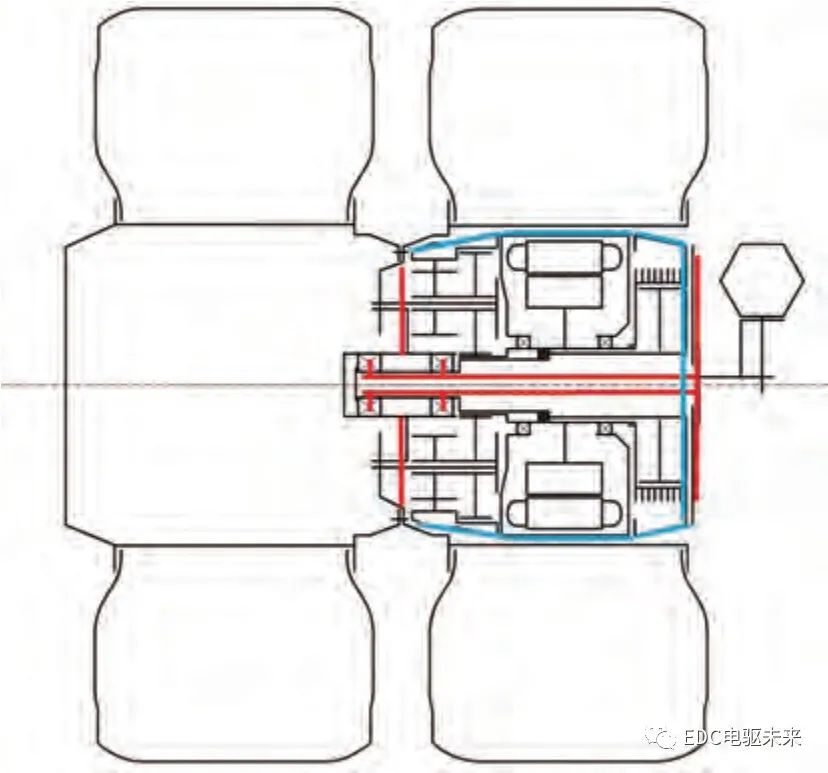
图9 弯扭解耦的电动轮构型示意图
基于所开发的轮毂电机,进行联合效率测试。按照100~3 200 r/min电机转速区间每个采样点间隔100 r/min,0~2 000 N·m 电机转矩区间每个采样点间隔100 N·m 进行标定,最终所得的电机与电机控制器的联合系统实测效率如图10所示。
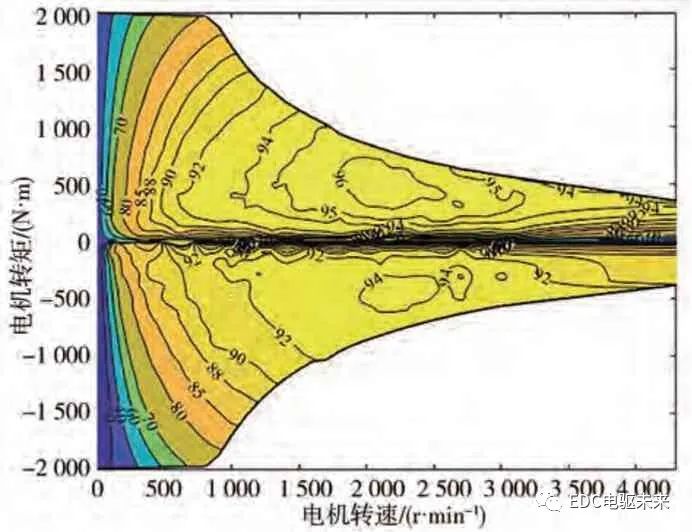
图10 电机及控制器效率MAP
进一步,将电机效率图与仿真得到的减速器效率图相结合,可得整个电动轮的效率MAP 图,如图11 所示。图中横坐标为车轮转速,纵坐标为车轮驱/制动转矩。考虑整车主要运行车速范围为30~70 km/h,对应转速约为150~350 r/min,此时电驱动系统的总体效率均在90%以上,可以很好地满足商用车节能减排要求。从全生命周期的成本来看,电动轮带来的运行成本下降基本与整车购置成本相当,经济效益明显,这也能有效支撑电动轮的商业应用。

图11 电动轮的效率MAP 图
2.2 电驱动桥设计
基于该电动轮,考虑载荷、性能和装配等因素,开发了双轮并装的轮边驱动电动轮的驱动桥方案[32],并引入转矩矢量分配控制,保证低速转向轻便与高速稳定性控制,提高整车经济性与安全性。驱动桥控制器采用TC275 三核MCU,一个单片机可以同时控制驱动桥的左右两台电动轮轮毂电机。驱动桥如图12所示。
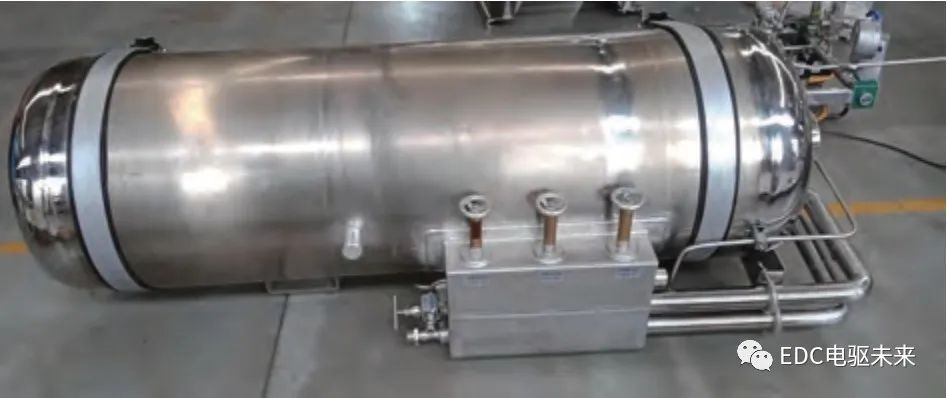
图12 双轮并装驱动桥方案
图13为所开发的电动轮与当前已发布的产品级电动轮的对比,可见采用新构型+匹配优化+油冷的设计方案取得了更高的驱动转矩与更轻的单桥质量,当前整桥质量已和传统集中驱动相当,有效解决了簧下质量问题。考虑到上述基于电动轮的分布式电驱动系统的直驱优势,系统的驱动效率比集中驱动还能进一步提升近10%,使其在性能和成本上均具有优势。
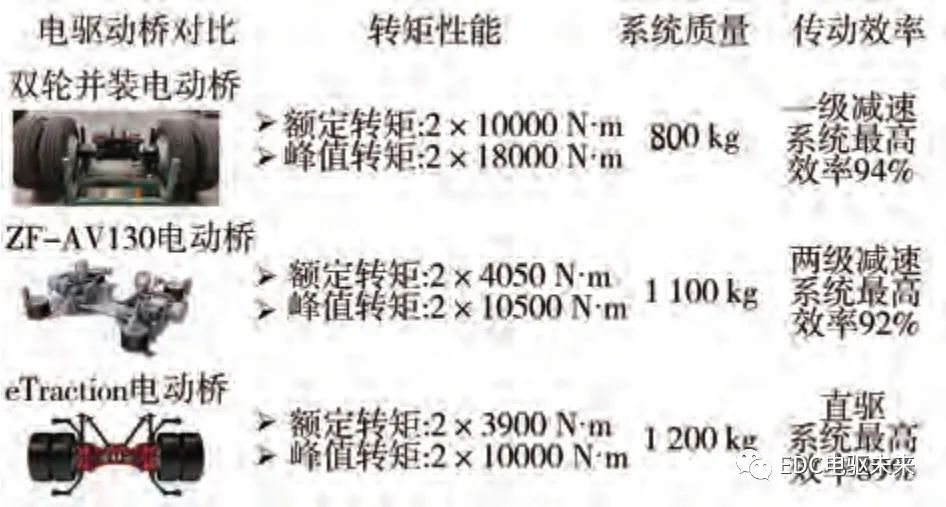
图13 电驱动桥方案对比
3 储氢与燃料电池系统设计
3.1 燃料电池系统
重载商用车功率需求大,根据上述系统参数设计,35 t 级载货车80 km/h 的巡航平均功率可达84.57 kW 以上,49 t级牵引车90 km/h的巡航平均功率可达128.07 kW 以上。但在本文开展动力系统设计阶段,国内尚无100 kW 燃料电池系统,给技术开发带来了极大的挑战。
围绕100 kW 燃料电池研发目标,本文团队通过和国内产业链企业联合技术攻关,逐一解决了空压机、循环泵和冷却水泵等大功率燃料电池零部件空白难题,开发了国内首个上公告的大功率燃料电池系统,如图14和图15所示;在此基础上,近两年进一步完成了全球首台单系统240 kW 燃料电池系统开发,如图16 所示。两代燃料电池系统基本性能参数如表7所示。
表7 燃料电池系统性能参数
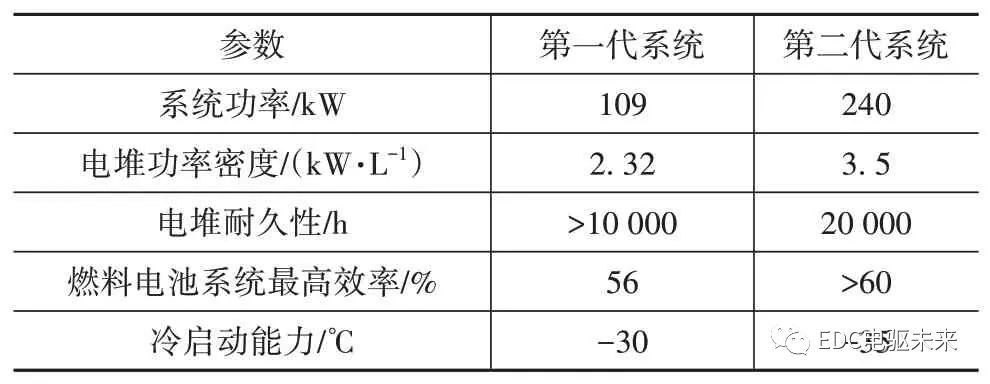
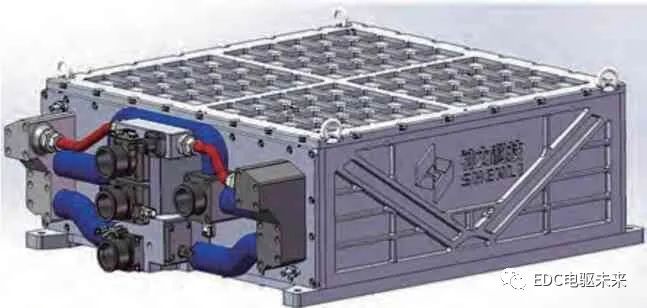
图14 燃料电池系统电堆外形图
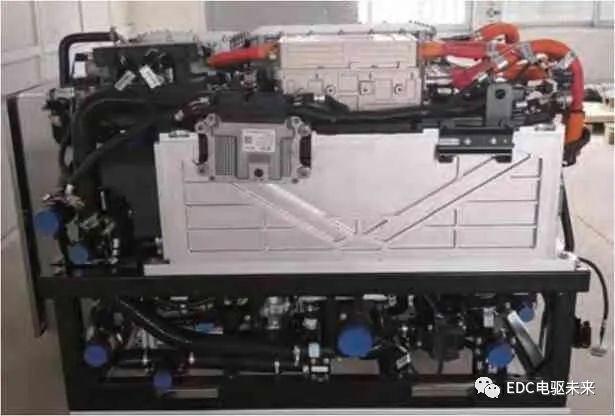
图15 109 kW燃料电池系统
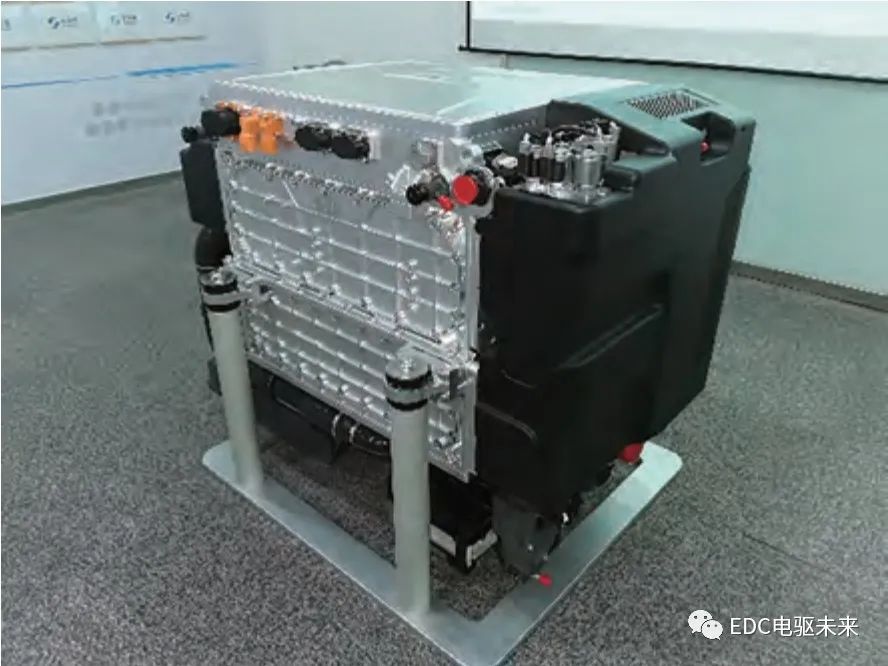
图16 240 kW燃料电池系统
本文所开发系统使用了第一代大功率燃料电池系统,通过优化电堆设计和控制策略,系统在工作温度75 ℃、氢气压力170 kPa(绝压)、空气压力150 kPa(绝压)、空气计量比1.8 和氢气计量比1.4的条件下,系统输出功率可达109 kW,电堆电压标准差为6 mV,可以满足整车大功率输出需求。
为验证大功率燃料电池系统的耐久性,将该燃料电池系统装在具有道路测试资格的城市客车上,完成了1 500 h 道路实车测试。以20%性能衰退为终点分析主要工作点的衰退速度,该款燃料电池系统的预测寿命超过了10 000 h。
从全生命周期使用成本的角度考虑,商用车燃料电池系统的核心还是耐久性与效率。根据汽车生命周期成本评估,燃料电池系统的额定点效率从45%提升到50%,可使汽车全生命周期的能源成本下降近10%,所带来的收益对于系统设计影响显著。因此,商用车燃料电池系统匹配设计须特别关注效率优化,在最大空间尺寸的边界下,尽量兼顾高效与长寿命需求,这对于降低全生命周期成本具有重要意义。
3.2 液氢储供系统
高密度、高安全和低成本的车载储氢系统是氢燃料电池汽车走向实用化、规模化的关键。针对车载储氢需求,目前已发展出高压气态储氢、低温液态储氢、高压深冷储氢、金属储氢和有机物储氢等多种技术路线[33-35]。其中,低温液态储氢技术在成本与储氢质量密度上具有更佳的潜力,并在国外氢能领域和国内航天技术领域已有一定应用[36]。目前,我国尚未有液氢车载应用的先例,本文希望以此探索该项技术的可行性。
相比高压气态储氢罐,车载液氢储供系统须突破车载液氢储罐设计与制备、多工况液氢流量压力精确控制和车载液氢系统氢气回收处理等关键技术。
针对液氢储罐绝热设计、真空设计、支撑结构设计和轻量化设计等核心技术难题,采用了低漏热支撑与出管结构、小间距高真空多层绝热结构和夹层管气封液结构设计等关键技术,通过低温卧式容器传热性能优化,最终的液氢储罐结构如图17所示。
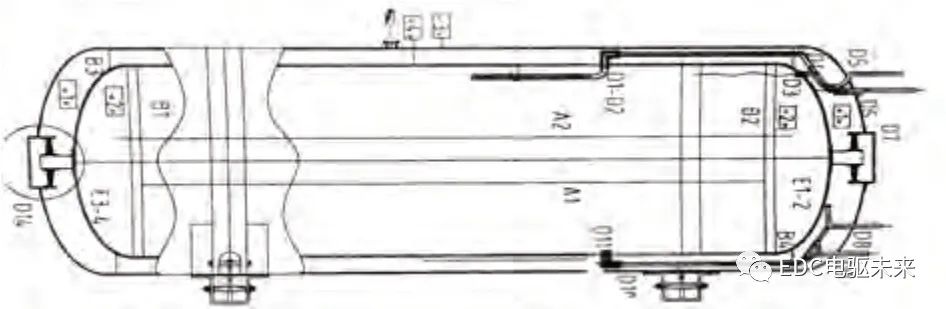
图17 液氢储罐结构图
为保证液氢储罐使用安全,系统在构型、工艺、材料和使用等方面提出了一系列安全方案。
(1)液态氢转变为气态氢会导致体积膨胀约845 倍,超压设计对安全尤为重要。液氢储罐的安全泄放装置包括两个安全阀,或一个安全阀和爆破片串联。爆破片可以在超压泄放前避免氢气泄漏,安全阀可以在超压泄放后回到关闭状态。
(2)自增压汽化器上设置低温截止阀和电磁阀,通过工艺流程保证不同时关闭。
(3)所有涉氢管道、阀门等设备和管道组成件的材料均与氢相容,主体材料为奥氏体不锈钢304、316L,管材供货状态为固溶、酸洗钝化。
(4)液氢外容器的安全泄放装置采用保险器,可反复使用。即使夹层真空度丧失,保险器弹出后也可复位。
(5)氢气排放方向、场所的要求:氢气排放位置高于供电部件200 mm以上。
在液氢储氢系统工作时,液氢须换热蒸发为常温氢气后再供应至燃料电池。为保证氢气的持续供应,本系统采用挤压供应方案维持液氢储罐持续排液,图18为其示意图。
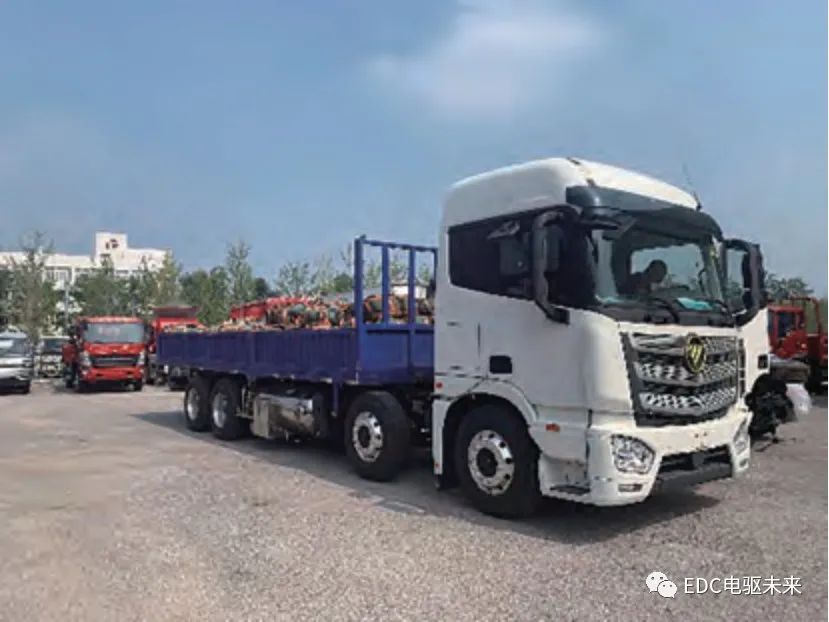
图18 液氢储罐自增压挤压供液
液氢复合汽化器是液氢储供系统冷能和热能综合利用的核心,通过将燃料电池散热系统与氢汽化系统耦合,可实现散热与加热的能量综合利用。为维持氢系统压力稳定,氢回路中还增加了一套缓冲罐,通过压力闭环控制,以实现氢系统与燃料电池系统的连续稳定运行。
由于低温液体难以与环境绝对绝热,液氢在静置状态下会不断蒸发导致系统压力上升,如果压力超过警戒值则须打开泄压阀排氢,对系统经济性、安全性与使用便利性带来不利影响。
为维持储罐内压力稳定,本文设计了液氢储供系统的挥发氢气(boil-off gas,BOG)回收系统,由液氢储罐压力传感器、电磁阀、液氢储罐、液氢汽化器、单向阀、缓冲罐和连接管路组成。其中,电磁阀分别与压力传感器和液氢储罐连接。压力传感器指示的液氢储罐内压力作为电控单元的输入信号,电磁阀作为执行器。
BOG 系统如图19 所示,根据燃料电池开机和停机分为两种模式。
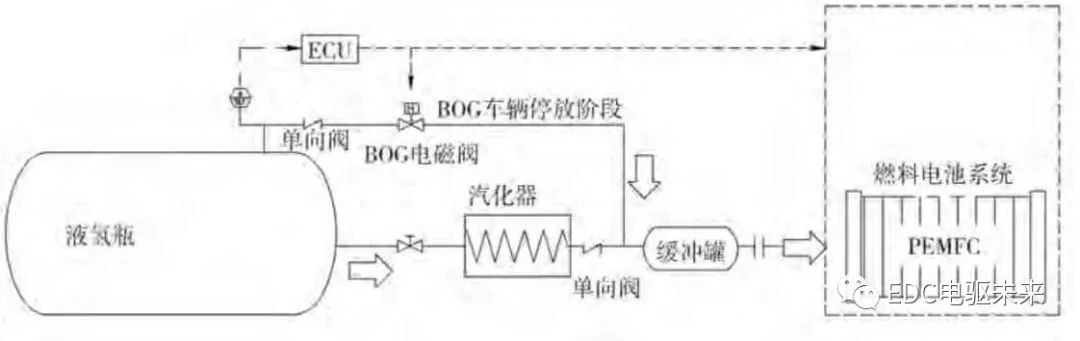
图19 液氢储供系统BOG回收系统图
(1)燃料电池工作时,挥发氢气回收系统管路中的电磁阀关闭,液氢供氢管路阀门开启,液氢汽化后正常进入到燃料电池系统参与反应。
(2)燃料电池停机时,挥发氢气回收系统管路中的BOG 电磁阀关闭,液氢供氢管路阀门关闭。此外,若压力传感器测量的氢气压力超过设置值时,系统控制电磁阀开启,氢气经过缓冲罐后进入到燃料电池;当压力再次低于设置值时,控制单元控制电磁阀关闭。
BOG 系统保证了液氢储罐内压力的稳定,且尽可能地减少了氢气的蒸发浪费。
基于上述液氢储供系统关键技术的研究和整车性能指标的需求,本文完成了35 t级载货车与49 t级牵引车的液氢储供系统布局。35 t级载货车的60 kg级储供系统包含2 套30 kg 液氢罐(图20),49 t 级牵引车的100 kg 级储供系统采用80 kg 液氢储罐(图21)后置+30 kg 液氢储罐侧置的组合方案。30 和80 kg 两种规格液氢储罐的质量储氢密度(不含附件)分别为9.33%和10.24%;两种规格液氢储罐的体积储氢密度(不含附件)分别为45.3 和40.8 g/L,液氢储供系统具体技术规格如表8所示。
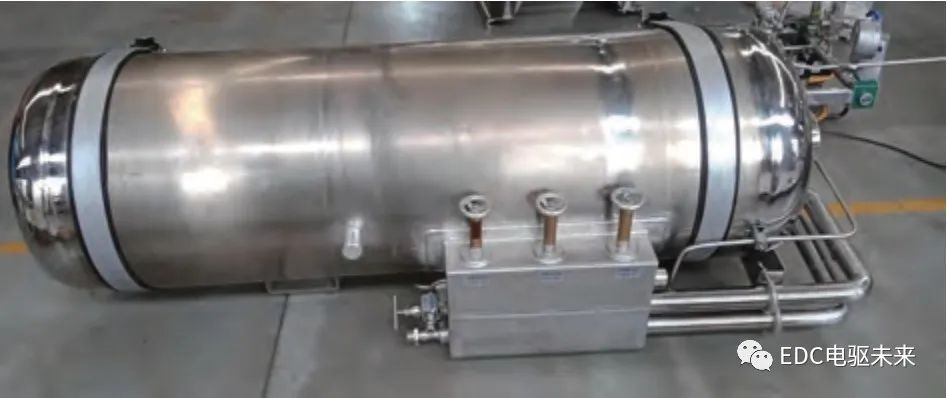
图20 30 kg级液氢储供系统
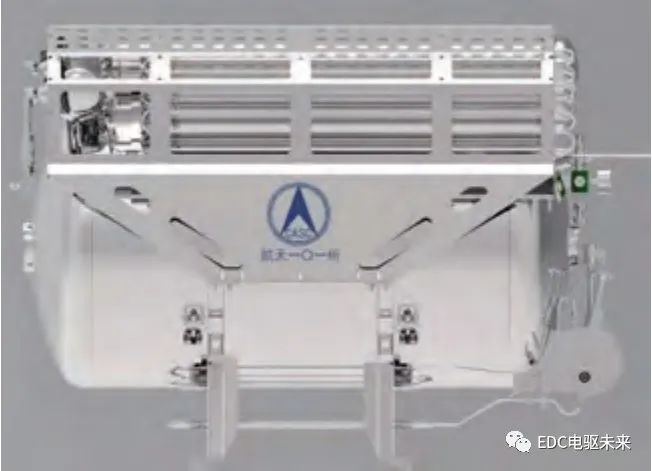
图21 80 kg级液氢储供系统
表8 液氢储供系统技术规格
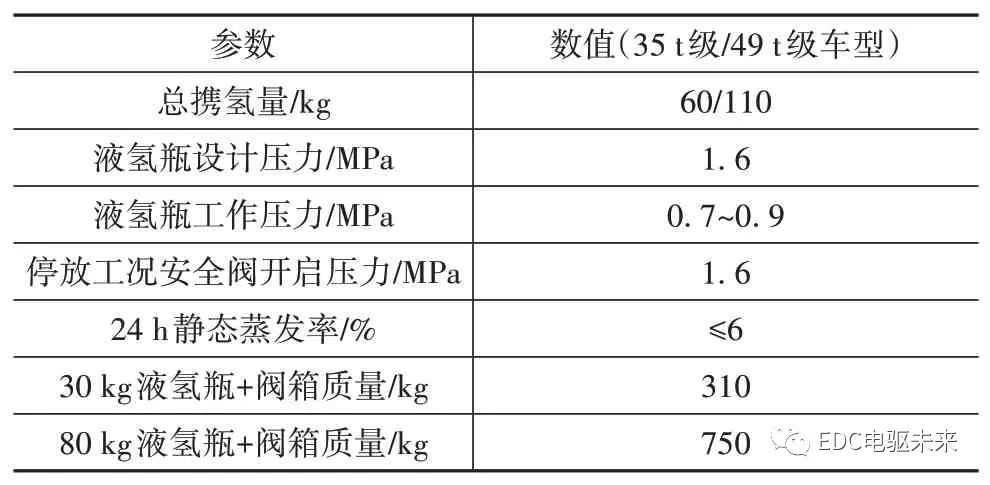
3.3 液氢系统日静态蒸发率测试
为更好地评价所开发的氢系统的绝热能力,本文测试了液氢系统的日静态蒸发率。依据GB/T18443.5—2010《真空绝热深冷设备性能试验方法第5 部分:静态蒸发率测量》,采用气体质量流量计测量单位时间内被检件中液氢蒸发后通过流量计的气体流量。蒸发率测试方法示意图如图22 所示,测试现场照片见图23。蒸发率计算公式为
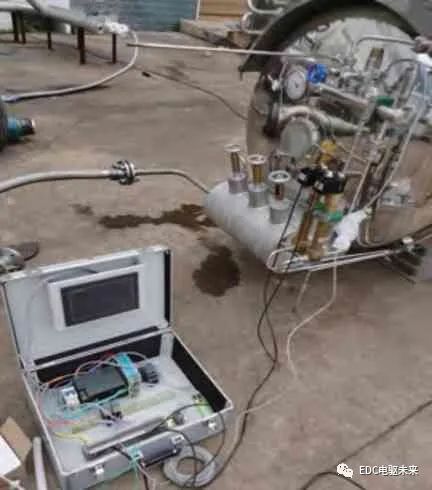
图22 静态蒸发率测试方法
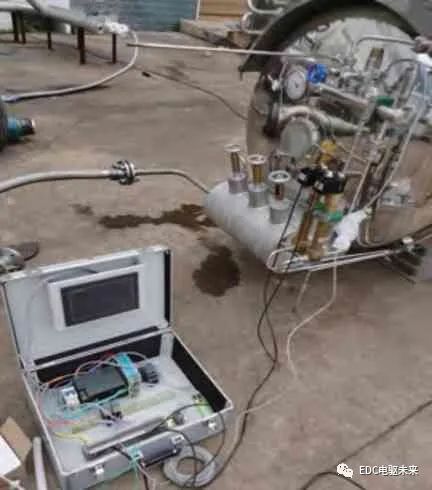
图23 静态蒸发率测试现场照片
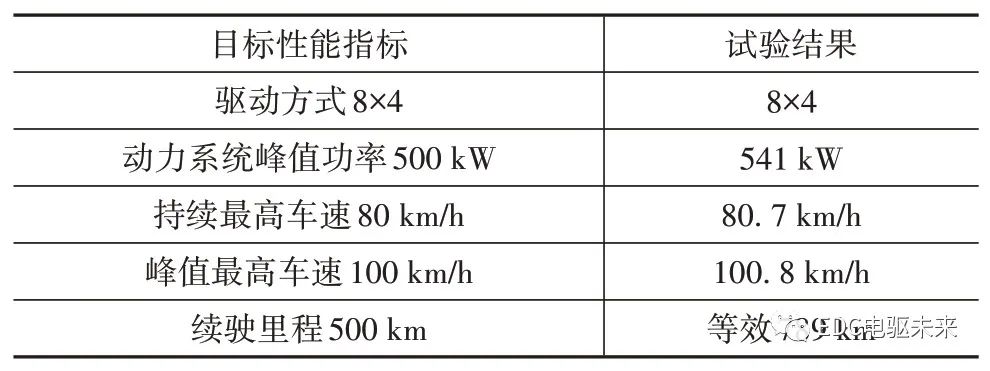
式中:αH2和α20分别为测试蒸发率和静态蒸发率,%/d;qm 为排放气体质量流量,kg/d;ψ 为流量计的校准系数;ρ1 为标准大气压下饱和液体密度,kg/m3;V 为液氢瓶有效容积,m3;h 和hfg 分别为试验环境压力下和标准大气压力下饱和液氢汽化潜热,kJ/kg;Ts、T1和T2 分别为标准大气压下饱和液氢温度、试验日平均环境温度和试验日被检件平均压力对应饱和温度,K。
用于液氢蒸发率测试的计算参数如表9所示。
表9 液氢蒸发率测试表
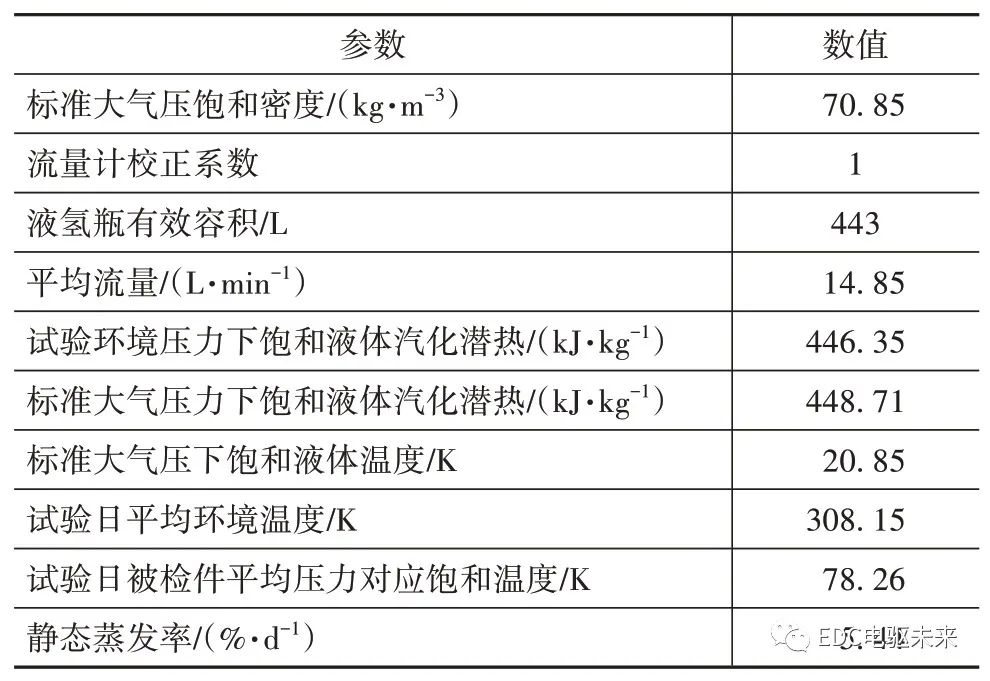
基于上述测试方案,30 kg 液氢储罐基于液氢介质完成了液氢储氢系统的日蒸发率测试,测试结果如图24所示。
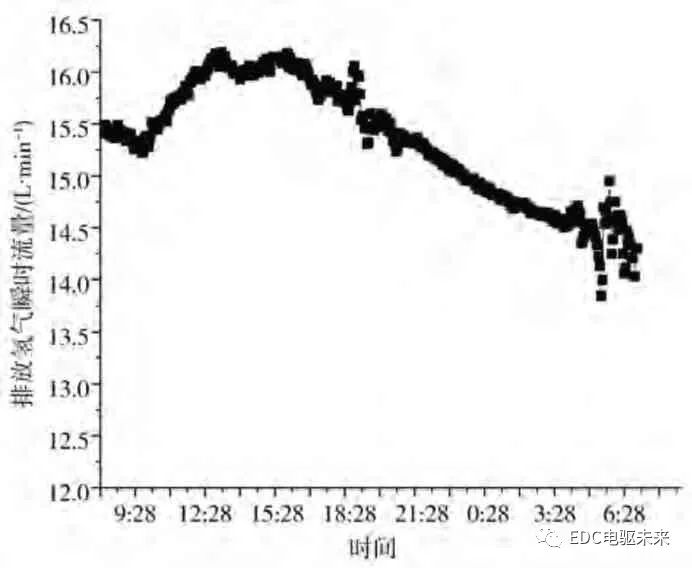
图24 蒸发量变化曲线
基于测试结果可知,液氢储氢系统使用液氮介质的日静态蒸发率为5.44%,满足低于6%的液氢储供系统性能指标要求。
在液氢储供系统开发过程中,其安全阀开启压力成为关键指标。开启压力过高可能对系统安全性带来较大风险,而开启压力过低既不利于实际使用,也不利于燃料电池系统氢气系统供给利用。
液氢储供系统的泄压阀开启压力应与液氢的物理性质相符合。图25 为液氢的三相图,其中液氢的临界压力为12.84 bar,高于临界压力,氢将从液态转化为临界态,使系统压力快速上升。从系统安全角度考虑,储氢系统必须严格避免进入临界状态,一旦液氢全部转为临界状态,系统无法通过泄压维持系统压力安全。由此,液氢的安全压力建议设计在12.84 bar 以下,以满足对于氢系统的安全监控需求。需要注意的是,如果以此为压力范围,未来也须进一步优化燃料电池氢系统的设计,使其兼容低压氢气供给工作状态。
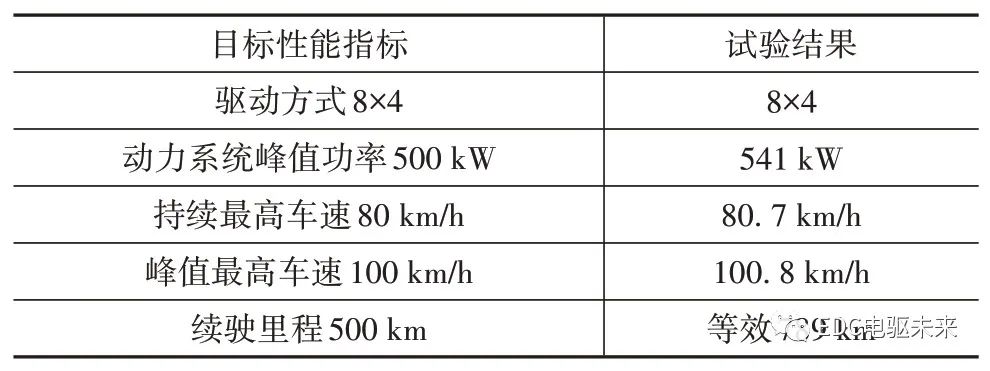
图25 氢气相图[37]
4 整车开发与实车测试验证
4.1 整车布置
基于图3 串联混合动力系统拓扑结构,与上面整车动力系统部件设计参数匹配,两型燃料电池重型商用车的具体底盘动力系统布置如图26所示。
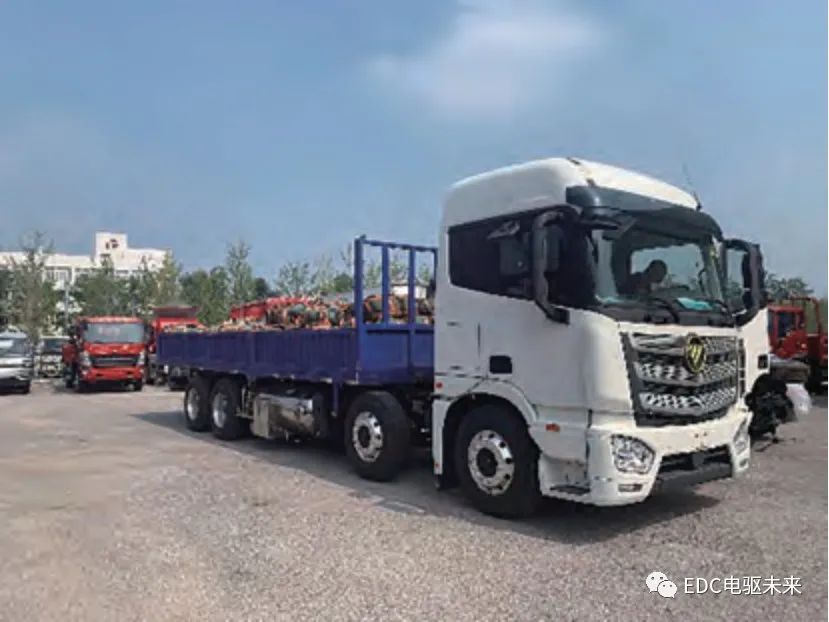
图26 重型商用车动力系统技术方案
基于上述布置,本文完成了两型液氢燃料电池重型商用车样车的试制和集成,如图27 和图28所示。
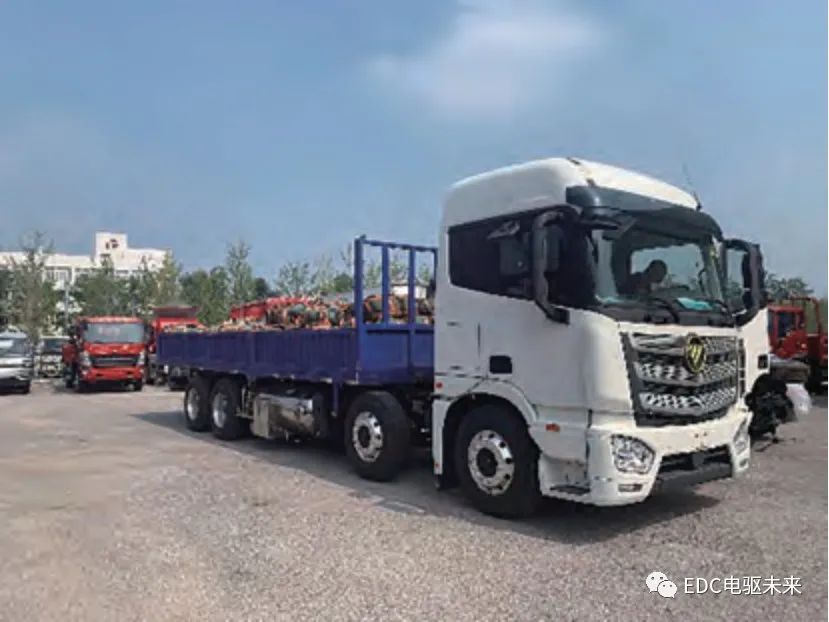
图27 35 t级载货车实物图
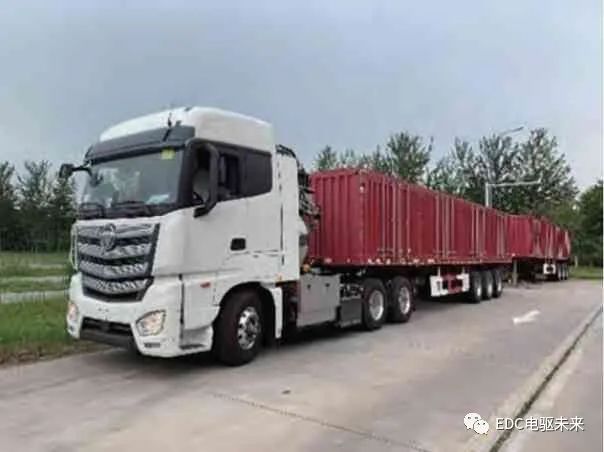
图28 49 t级牵引车实物图
4.2 实车道路试验
在第三方汽车检测技术公司的参与下,两型液氢燃料电池重型商用车样车在交通部公路交通试验场完成了动力性和经济性试验。
试验主要内容如下:
(1)30 min巡航车速试验;
(2)最高车速试验;
(3)动力系统峰值功率试验;
(4)巡航经济性试验。
受限于测试时间与用氢规范,经济性试验中整车采用40 km/h匀速行驶,并推算至满容量储氢续驶里程,采集记录实测行驶里程、时间、电量与液氢液位。在计算氢耗时,动力电池电量变化会根据燃料电池系统平均效率折算为氢耗。基于采集实测里程与等效总氢耗,即可通过液氢储供系统的总储氢量线性估计最大续驶里程。
基于上述方法,两型液氢燃料电池重型商用车完成了约200 km 的经济性高环测试和动力性试验与经济性试验,两款车型试验结果分别如表10 和表11所示。
表10 35 t级载货车实车道路试验结果
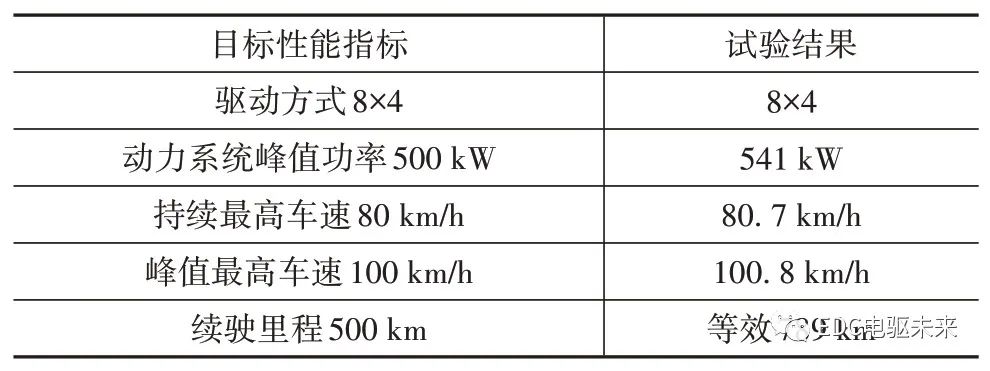
表11 49 t级牵引车实车道路试验结果
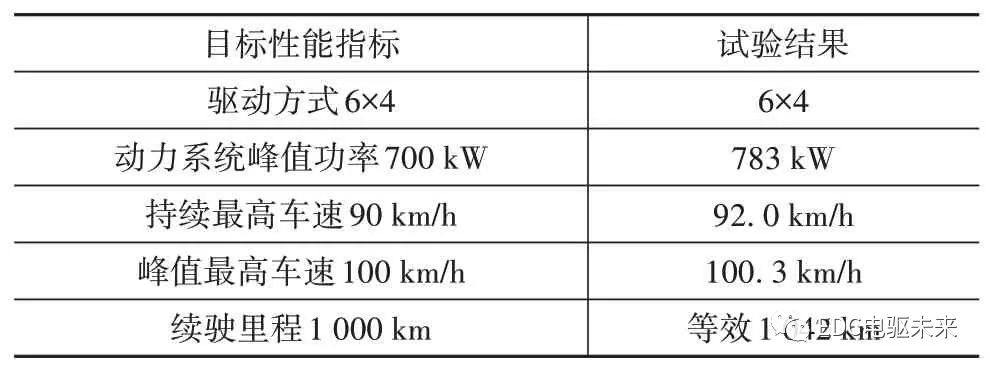
试验结果表明,本文所开发的两型液氢燃料电池重型商用车动力系统部件设计和参数选定满足预期设计指标,也验证了液氢储氢、电动轮与大功率燃料电池系统的技术可行性。
4.3 分析讨论
分布式驱动液氢燃料电池重型商用车完成了多项创新技术的验证,但仍需一段时间完成从技术向产品的优化与迭代。结合行业与产品的应用推广规律,本文也对各项创新技术产品化应用的潜在瓶颈与挑战进行了综合讨论。
(1)液氢终端消费价格
当前液氢仅供特种领域应用,制备成本仍极高,要实现商业化应用,价格在持续降低至30元/kg以下。
降低液氢成本的契机源于两个方面:一是可再生能源的电价成本降低;二是大规模氢液化工厂的关键技术突破。基于当前光伏0.2 元/(kW·h)电价和30 t/天液化工厂8 kW·h/kg的液化电耗,液氢的出厂价格可控制在15元/kg以下。进一步,考虑液氢的运输与加注成本相比高压气氢显著降低,这使液氢的终端消费者价格非常有希望降至30元/kg以下。
(2)大功率燃料电池的成本与寿命
商用车燃料电池须满足3万h的使用需求,总价格须控制在5万元水平,面临极大的挑战。
参考路线图的发展预期,燃料电池系统的中期价格有望降至1 000元/kW,重型商用车100-200 kW燃料电池系统所需的购置成本为10~20万元,使用户购置体验不佳,须予以一定补贴支持或优惠政策。对照内燃机5万元的价格水平,补贴后或远期价格降至300元/kW以下时,购置压力可以得到全面缓解。
需要注意的是,燃油成本是决定重型商用车经济性的核心,燃料电池节能的关键是效率。当市场接受燃料电池之后,适当提高燃料电池价格以配置更高的工作效率与更长寿命,来达到更低的全生命周期成本,也是可行的技术路线。
(3)液氢储罐成本的降低与批量应用
液氢长期以来一直应用于特种领域,相关技术在车载应用基本处于空白状态,全面应用还需要大量验证与体系建设。
对比来看,液氢技术与LNG 具有很大的相似性。自我国开始应用车载LNG 技术,全产业链在十三五期间逐步实现了国产化替代,瓶、罐、阀、泵、加注枪等成本飞速下降,单罐售价降低到3 万元以下,并已开发出双罐1 000 km 的长途重载方案。参考LNG 的国产化替代过程,目前产业链上下游对于液氢技术体系的突破充满信心。由于液氢产业链较长,技术空白多,须从系统架构的角度逐步完善体系建设。
(4)分布式驱动电动轮技术
当前,商用车智能化、电动化已是大趋势,系统对于驱制动性能的要求也会不断提升。由于电机在高速与低速的效率难以同时兼顾,现有集中驱动构型为满足全工况高效率使用需求,不可避免地要引入变速器等传动结构,这使系统复杂度较高,且效率难以全面提升至90%以上。轮毂电机驱动技术在经济性和制动性能方面的潜力还未全面挖掘,具有极大的空间。
从近期国内外发布的最新产品来看,分布式驱动与电动轮技术逐步升温。电动轮的技术优势已很明晰,核心的难点还是工程可靠性的提高和成本的降低。
5 结论
针对商用车电动化升级需求,面向燃料电池重型商用车平台,围绕高性能、长续航、低成本使用目标,提出了分布式驱动液氢燃料电池重型商用车技术方案,探索了大功率燃料电池系统、大容量车载液氢储供系统与大转矩轮毂电机的创新技术。
基于关键零部件技术方案突破,开发了国内首个直接应用于整车的大容量车载液氢储供系统,和首款上公告的百千瓦级燃料电池系统,同时完成了全球首辆35 t 级和49 t 级液氢燃料电池分布式驱动重型商用车的研制与道路试验。
开发过程中取得的经验有:
(1)发展分布式驱动技术可缩短动力传递环节,将驱动系统的传动效率提升8%~10%,降低全生命周期成本;
(2)车载液氢储氢系统比高压储氢具有更高的储氢密度和更好的成本下降预期,其储氢密度可达到8%以上,续驶里程可以突破1 000 km,使燃料电池在长途重载场景具备实际应用价值;
(3)重型商用车用大功率燃料电池须更加注重效率与寿命,提高效率可有效减少全生命周期氢耗,降低运营成本。
本文所涉及的创新技术方案基本完成了验证,但在后续产业化过程中还须突破系列量产化关键工艺与技术。
- 下一篇:一文了解视线追踪系统技术及应用
- 上一篇:燃料电池汽车整车及关键零部件布置研究
编辑推荐
最新资讯
-
推荐性国家标准《乘/商用车电子机械制动卡
2025-04-30 11:13
-
载荷分解
2025-04-30 10:46
-
布雷博在上海开设亚洲首个灵感实验室
2025-04-30 10:25
-
组分性能对锂离子电池卷芯挤压力学响应的影
2025-04-30 09:00
-
美国发布自动驾驶新框架,放宽报告要求+扩
2025-04-30 08:59