新能源重卡电驱动构型分析
新能源汽车是汽车产业发展趋势,新能源(纯电)重卡迎来了发展机遇,其常见结构如下图所示。
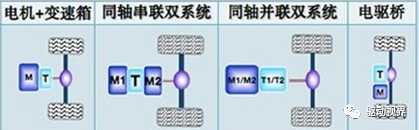
图1 纯电重卡常见结构类型
本文针对新能源重卡几种常见构型进行分析。
1.“电机+变速箱+传统桥”构型
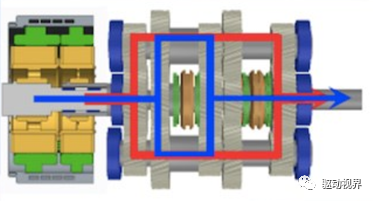
图2 纯电重卡的电机、变速器、传动桥型结构图
1.1 构型优缺点分析
纯电重卡领域采用电机、变速器和传动桥的组合是取代传统燃油车的重大实践。如图2所示,纯电重卡的核心部件电机、变速器、驱动桥的结构图。纯电重卡动力系统的发展阶段、设计理念、市场需求、设计理念的不同,类型较多。从电机数量上分为:单一电机变速器组合和双电机变速器组合;从组合方式上分为同轴串联双系统、同轴并联双系统、多轴并联双系统。不同类型的结构各有优缺点。具体如下:
(1)单一电机变速器组合动力系统
采用单一电机和变速器结构形式的电动卡车,主要有一个电动机和一套变速系统配套的控制系统组成。
主要优点:
①结构简单、重量轻、成本低;电机普遍采用传统异步电机或者永磁同步电动机,构造简单,对原燃油车架构改动少,容易快速形成产品的产业化应用;
②运行可靠,经久耐用。驱动桥技术比较成熟,功率覆盖范围宽。
③控制技术成熟。异步电机控制器普遍采用矢量控制或者直接转矩控制,技术相对成熟。
缺点:换挡时动力容易中断,重卡的工作条件需要输出较大的功率和扭矩,特别是上坡时,由于异步电机存在转速差,容易出现换挡时动力中断,有溜坡的风险,采用一个驱动电机产生动力中断的问题满足不了重卡的动力需求
(2)同轴串联双系统
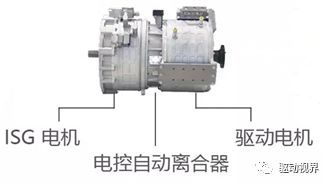
图3 同轴串联双系统(宇通)
如图3所示,同轴串联双系统的结构图,在驱动电机的输出轴串联一个ISG/M2电机或者M2电机,电控自动离合器对两个电机进行控制,相当于在原来电机+变速箱的再串一个直驱电机,换挡时ISG/M电机仍然可以提供动力,进行扭矩补偿,实现动力不中断。这种方案的优点是,结构相对比较简单,在现有的基础上加一套电机在后面;控制也比较简单,换挡也可以实现动力无中断。缺点:M2电机相对而言动力较小,作用有限。比如说,用在矿卡上,前面“M1+T”这一套最大输出扭矩可以达到15000Nm左右,ISG/M2在换挡的时候最多能提供3000Nm扭矩,也就是20%左右的补偿,这样在爬较大的坡时动力中断也会比较明显。
(3)同轴并联双系统
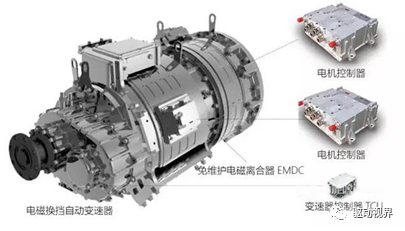
图4 同轴并联双系统总体结构图
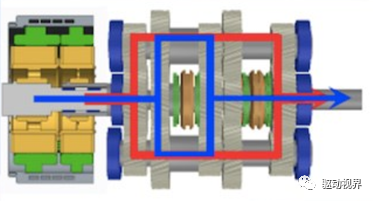
图5 同轴并联联双系统结构
如图4所示,同轴并联双系统总体结构图。该系统采用双绕组电机匹配双输入变速箱,双输入变速箱实际是两个独立工作的变速箱,通过共同的输出轴将动力耦合输出。两套系统独立工作,如图5所示,红色和蓝色箭头所示,是同轴并联双系统输出示意图,可以实现50%以上的扭矩补偿,在爬坡时效果非常明显。这种动力方案的优势是换挡不存在动力中断,单系统动力仍然很强,因此一套系统换挡时仍然有较大的动力输出,平顺性跟直驱几乎没有区别。而且因为是两套系统,电机扭矩和对应挡位可以优化分配,负荷小的时候一个电机工作,负荷大的时候两个电机工作,可以让电机工作在比较高效的区域,且电耗低。缺点是系统成本比较高,而且结构和控制也比较复杂。
因此这种方案的定位是高端车型或高性能的动力系统。在路况复杂的自卸车、矿卡等领域,这种方案动力性和平稳性优势非常明显。
(4)异轴并联双系统
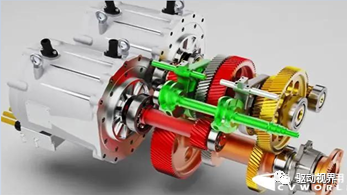
图6 异轴并联联双系统结构
如图6所示,异轴并联双系统动力系统性能和同轴并联系统虽然结构上存在一定的差异,但工作原理相似。通过两个高速、高效电机及多模变速箱的组合,确保了换挡过程无动力中断,使得纯电动卡车驱动系统能够更好地应用于复杂路况。缺点是两个电机要并排布置,对布置空间要求较高,且传动速比大,传动级数多变速箱效率较低,没有直接挡,高速运行效率更差。所以,电耗和布置空间可能会成为这种方案的短板,综合成本也比较高,因为要用到两个比较大的电机。因此,这种方案更适用于坡度较小的矿车。
1.3 目前主要供应商(电机/变速箱/控制器)情况、主机厂匹配及应用情况、销量
表1 纯电重卡电驱动配套产业链情况统计表
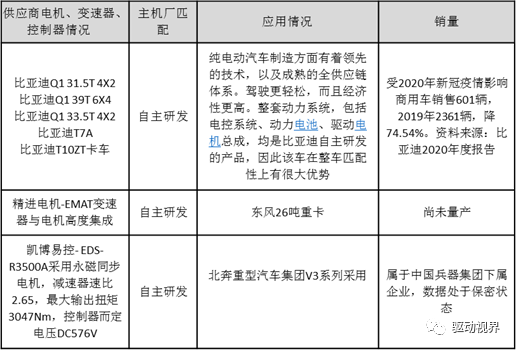
2.“电驱桥”构型
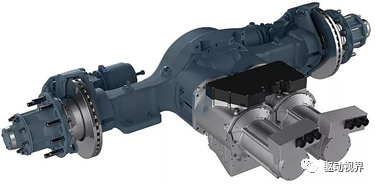
图7 电驱桥整体结构
车桥属于传统制造业的范畴,电驱桥是电动机和车桥的组合,也是电动重卡电气化的产物。如图7所示,双电机电驱桥的总体结构。电驱桥的将电机和车桥合成一体,俗称二合一,电机通过减速机构、差速器、半轴将动力传递给驱动轮。按电机的驱动类型分为单电机中央驱动、双电机中央驱动、单电机直驱。按电机分布位置不同,电驱桥分为轮边电机桥和轮毂电机驱动桥两种。
2.1构型优缺点分析
电驱桥主要是电机和传统车桥的组合,车桥设计和制造属于纯机械,成本低,传统重卡采用内燃机作为动力源,电动卡车使用的电驱桥。缺点也有,第一驱动桥结构复杂,簧下质量大。采用整体传统车桥和电机的结合,由于电机的转速较高,一级减速器满足不了要求,通常需要二级减速,这样一来,减速器的结构就比较复杂,簧下质量大幅提高。其次是电机的转速范围宽,要求功率和输出扭矩大,对控制器提出的要求高,控制器的软硬件开发难度大,特别是芯片开发成本高。
2.2目前主要供应商情况、主机厂匹配及应用情况、销量
表2 纯电重卡电驱桥构型配套产业链统计表
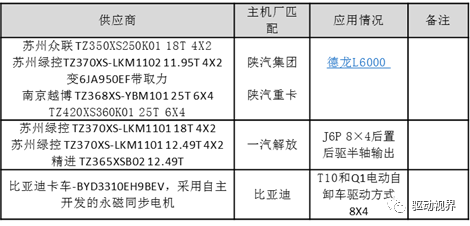
2.3成本分析
新能源重卡电机+变速器+传统桥产业由于属于新事物,在生产规模上已与竞争对手存在较大的差异。陕汽、一汽解放新能源重卡、比亚迪是国内主流重卡生产企业,陕气和一汽都有一定的市场基础和良好的传统商用车市场占有率,但在新能源重卡领域存在一定的短板,电机和控制器研发和生产能力稍微欠缺,需要对外进行采购,一定程度上增加了成本。
在新能源重卡研发、生产制造电机及控制器方面仍然没有掌握核心技术,在目前仅依靠传统的投资建设、自主研发的方式进行发展,短时间内仍难以赶超竞争对手。比亚迪在重卡领域虽然起步较晚,但在新能源乘用车方面积累了大量的经验,并且具有电池、电机、电控全产业链的生产、研发、能力,每年研发投入较多,还具有自己的营销渠道,在这方面就比较有优势。不足之处,知名度不高,口碑积淀和市场占有率不高。
综上所述,新能源汽车整体成本差距不是很大,各个重卡生产企业各有优劣,相比之下,比亚迪在成本控制方面优势暂时领先。
3.“轮边电机”构型
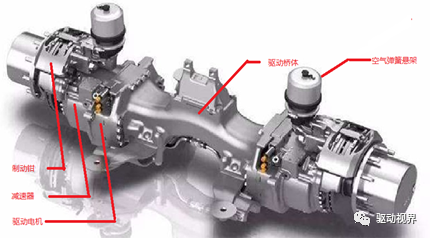
图8 轮边电机及驱动器结构
3.1构型优缺点分析
轮边电机的主要结构特征是将驱动电机直接安装在驱动轮内或驱动轮附近 (轮边),具有驱动传动链短、传动高效、结构紧凑等优点,为汽车结构的变革创造了条件。如图8所示,轮边电机及驱动器结构。轮边电机的驱动方式主要有减速驱动和直接驱动两种。在减速驱动方式下,一般采用普通的内转子高速电机。安置在电动轮附近,通过减速机构与电动轮相连,通常称为轮边电机。为了获得较高的功率密度,电机的转速通常高达 10000r/min。该类型结构紧凑,可大幅度提高轮边电驱动总成的转矩密度和效率,已成为电动轮总成技术发展的重要方向。但是,高速行星齿轮装置设计和制造难度大、噪声难以控制、相关核心技术有待解决。
轮边电机分布驱动技术具备很大的优势,具体表现在以下方面:
①结构简单、布置灵活,不需要复杂的机械传动系统,车辆的空间利用率高,传动系统效 率高。
②电机小型化分布驱动,独立控制,故障容错能力强。
③采用现代控制技术整体控制各个轮边电机的转速、转向和功率输出等参数,实现在传统汽车上难以实现的一些高性能控制功能,大大改善了汽车的行驶性能。
④在减速或下坡时,动能或势能可转化为电能,通过功率变换器回馈给电池,实现能量回馈,增加了电动汽车的行驶里程。
缺点:设计和制造过于紧凑,对制造技术要求很高,重卡控制器要对两个电机进行协调控制,算法设计难度大,开发成本较高。
3.2 目前主要供应商情况、主机厂匹配及应用情况
表3 纯电重卡轮边分布式驱动配套产业链统计表
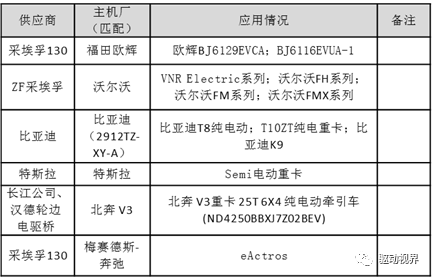
3.3 成本分析
轮边电机重卡在前期研发阶段需要巨大投入,需要软件和硬件大量的实验,虽然仿真技术日渐成熟,但研发成本依然居高不下。在生产过程中,由于结构非常紧凑,需要高精度设备、零配件,以及熟练的总装技术人员,成本是中央电机桥的2-3倍。
综上所述,轮边电机驱动重卡成本与上面几类电驱重卡技术相比,成本较高。
3.“轮毂电机”构型
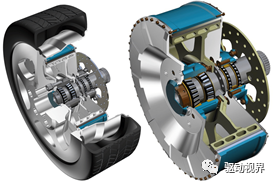
图9 某轮毂电机结构
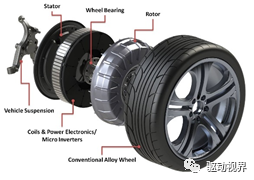
图10某轮毂电机结构
轮毂电机技术又称车轮内装电机技术(In-wheel-motor),特点是驱动电机安装在车轮内部。如图9、10所示,轮毂电机的结构,将电机、制动、轮毂等系统集合在一起。
3.1 构型优缺点分析
1.轮毂电机的优点:
(1)轮毂电机可以实现高度集成化
轮毂电机将驱动电机、制动系统、传动装置集中在车轮轮毂中,舍弃了传统的变速器、传动轴、差速器、分动器,同时,轮毂电机还能进行能量回收,大幅度简化车辆底盘系统,实现高度集成化。
(2)驱动控制方式多样化
通过电机控制器可以实现每个轮毂电机车轮的独立驱动控制,前驱、后驱、四驱以及多轮驱动、转向、制动的实现就容易,只要车轮的自由度设计合理,几乎可以实现原地转向。如图11所示,德国ETE卡车在特殊情况下还能实现原地转向。
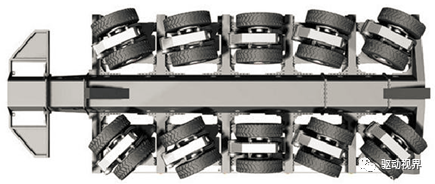
图11 德国ETE欧洲卡车全轮驱动转向系统
(3)轮毂电机能源驱动方式多元化
不仅传统燃油汽车、混合动力汽车可以采用轮毂电机,纯电动汽车、增程式汽车也可以采用轮毂电机,能源驱动方式多元化。
3.2 轮毂电机的缺点:
1) 簧下质量高,设计制造难度大:虽然轮毂电机重卡降低了整车质量,但簧下质量大幅增加,整车操控性、舒适性以及悬挂可靠性设计制造的难度却很大。
2) 可靠性差,成本高:重卡轮毂精密电机工作环境恶劣,容易损坏,可靠性差。轮毂控制器需要大量的芯片,软件设计、整车配套开发,成本高。
3) 轮毂电机散热难,制动热衰退明显:轮毂电机结构过于紧凑,散热困难,特别是重卡功率大、装载质量大,制动时热衰退明显,制动效能差。
总体看来,轮毂电机的分布式驱动与集中驱动相比拥有明显的技术优势,主要体现在节能降耗、增加车内空间利用率、减少整车设计与制造成本、适应电动汽车智能化开发等方面。
3.3 目前主要供应商情况、主机厂匹配及应用情况
表4 轮毂电机配套产业链统计表
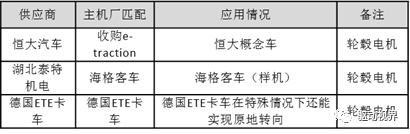
轮毂电机主要的成本构成轮毂轴承、电机、制动系统、控制系统,国内比较成熟且能,轮毂电机配套的电机电控产品,电控研究纯电动汽车动力系统匹配理论,动力系统参数匹配运用MATLAB编写程序进行驱动电机、动力电池总需求参数的计算,研发周期长,成本非常高。目前,国内还没有实现量产的车企。
3.4 成本分析
综上所述,轮毂电机重卡虽然在研发阶段,在市场上还没有出现,但由于它具有良好的机动性和操纵性,具有很好的使用价值,发展潜力巨大。
编辑推荐
最新资讯
-
推荐性国家标准《乘/商用车电子机械制动卡
2025-04-30 11:13
-
载荷分解
2025-04-30 10:46
-
布雷博在上海开设亚洲首个灵感实验室
2025-04-30 10:25
-
组分性能对锂离子电池卷芯挤压力学响应的影
2025-04-30 09:00
-
美国发布自动驾驶新框架,放宽报告要求+扩
2025-04-30 08:59