低速转向行驶的差速器异响测试分析及优化
摘 要
差速器是汽车传动系统的重要传动部件之一,其故障模式的分析与控制一直是汽车行业内关注的热点。以某搭载紧凑型轿车的低速行驶转弯异响为背景,系统阐述了问题分析与排查过程,通过差速器性能台架实现了异响问题的复现,结合故障零部件的解析,提出了差速器异响问题的潜在机理和解决思路。通过行星轴定位装配方式和加工工艺的优化,准确有效地消除了该车型差速器的异响,这对于整车瞬态工况下传动系统NVH(Noise、Vibration、Harshness)与异响问题的解决排查,具有一定的工程指导价值。
关键词:差速器,异响,行星齿轮,半轴齿轮,行星齿轮轴
作者:张军,鲍勇仲,储胜祥,张翰芳
单位:吉利汽车研究院(宁波)有限公司, 浙江宁波
0 引言
差速器是汽车传动系统的重要传动部件之一,其作用是保证汽车转弯过程中内/外轮速度差与动力转矩的传递,直接影响着车辆行驶的功能可靠性和舒适性。随着汽车NVH(Noise、Vibration、Harshness)性能整体水平的提高,市场用户对车辆异响问题的要求也越来越关注。由于异响问题往往是差速器功能失效和异常磨损的前期征兆[1-3],因此,汽车差速器的故障模式分析方法和开发设计能力,一直是汽车行业内研究的热点领域之一[4-5]。
陈煜等[6]通过差速器齿轮垫片黏滑摩擦性能的研究和垫片表面处理工艺的改进,解决了某纯电动车行驶转向过程的异响问题。Wan X等[7]提出了一种小波包分析方法,可快速准确识别出汽车转向的轮毂轴承异响问题。封旗旗等[8]采用行星齿轮齿廓修形和偏心螺旋线修形的方法,降低了差速器齿轮噪声。刘宏等[9]对差速器的双金属垫片和钢垫片进行了台架磨损对比试验。Yuan W等[10]研究了差速器径向沟槽垫片的摩擦特性。易勇等[11]提出,试验规范和装配技术要求是差速器异响性能开发控制体系的重要因素。虽然行业内对差速器异响与噪声性能的排查分析和试验流程等方面取得一定的进展,但研究领域主要集中在整车准稳态工况和耐久可靠性领域,对于差速器瞬态不确定性异响问题的分析与工程化应用研究较少。
本文中以某紧凑型轿车的低速行驶转弯异响为案例,系统阐述了差速器异响的排查分析过程,分析了整车与差速器试验台架的客观测试数据关联性,通过行星轴定位装配方式和加工工艺的优化改进,快速有效地解决了该车型的差速器异响问题。
1 问题描述
某搭载1. 5 L 四缸自吸发动机和CVT(Continu⁃ously variable transmission)无级变速器的横置前驱紧凑型轿车,在光滑路面的低速转弯加速行驶过程中,在底盘ESP(Electronic stability program)功能未激活时,前机舱内存在较明显的“嗒嗒”异响(前机舱的动力传动系统如图1所示),但整车没有抖动或耸动现象。并且,左、右两侧的转向工况都存在该异常噪声,而在车辆直行时则异响消失;同时,松油门转弯过程也没有异响。由于低速转弯行驶时的车内背景噪声较低,这种金属撞击特征异响声就更容易被车内的驾乘人员感知和抱怨。此外,在车辆持续地“绕8字”磨合行驶短暂里程之后,该异响发生几率有一定程度的降低。
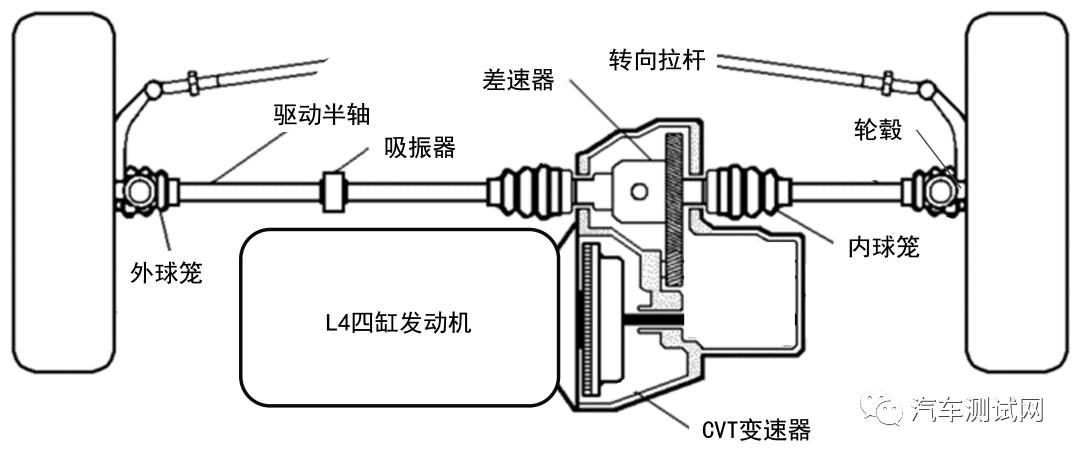
图1 前悬架动力传动系统示意图
为了排查转弯异响问题的原因,将车辆放置在柱式举升机上,整车的方向盘偏转一定角度,在D挡下小油门加速,异响没有复现;另外,自动变速器挂入N挡,人工手动转动任何一侧的前轮胎,也没有复现出该异响。因此,初步推测该异响问题可能与变速器润滑相关,或者与动力传动部件的磨合水平相关;且无法主观识别判断出异响源位置,需要进一步进行振动噪声的客观测试分析。
1.1►
整车测试方案
为了排查该车型转弯异响问题特征和异响源位置,分析异响与前机舱内底盘传动系统的关联性,分别在轮毂轴承、差速器输出接口、前悬架控制臂和转向横拉杆等位置布置了振动加速度传感器,在发动机舱内底部布置了麦克风传感器,如图2所示。同时,通过CAN总线同步采集了ESC(Electronic sta⁃bility control)系统的左、右驱动半轴速度、车速和发动机输出转矩等信号。
如图3所示,在综合性能试验场的光滑宽阔路面上,车辆在D 挡模式下以15% 的小油门持续加速,定圆转弯稳定行驶,车速保持在15 km/h以内,进行了多次循环的重复试验,同步测试与采集前机舱内动力传动系统部件的振动信号。
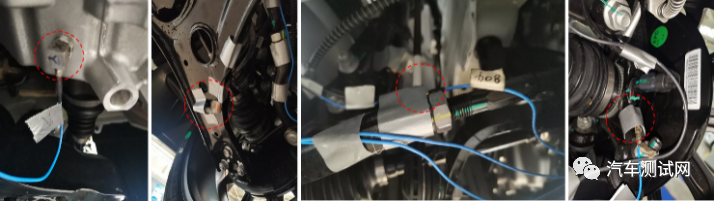
图2 整车测试的传感器布置
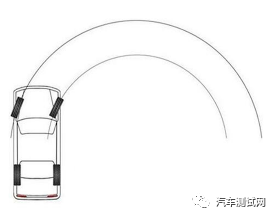
图3 整车测试行驶示意图
1.2►
整车测试结果的分析
在ESC系统测试过程中,由于前机舱底部发动机与路面的背景噪声都较大,所采集的麦克风声音信号的异响特征不显著。然而,通过对各底盘传动位置测点振动信号的时域特征分析和音频的反复回放,结合主客观评价的对比辨识,可以明显发现,前悬架和传动系统的各个测点都存在振动冲击特征,且发生在同一时刻,如图4所示。结合左、右车轮速度和车速等信息,由图4中可以清晰地识别出各振动冲击信号的瞬态时域特征以及冲击次数与幅值水平等。
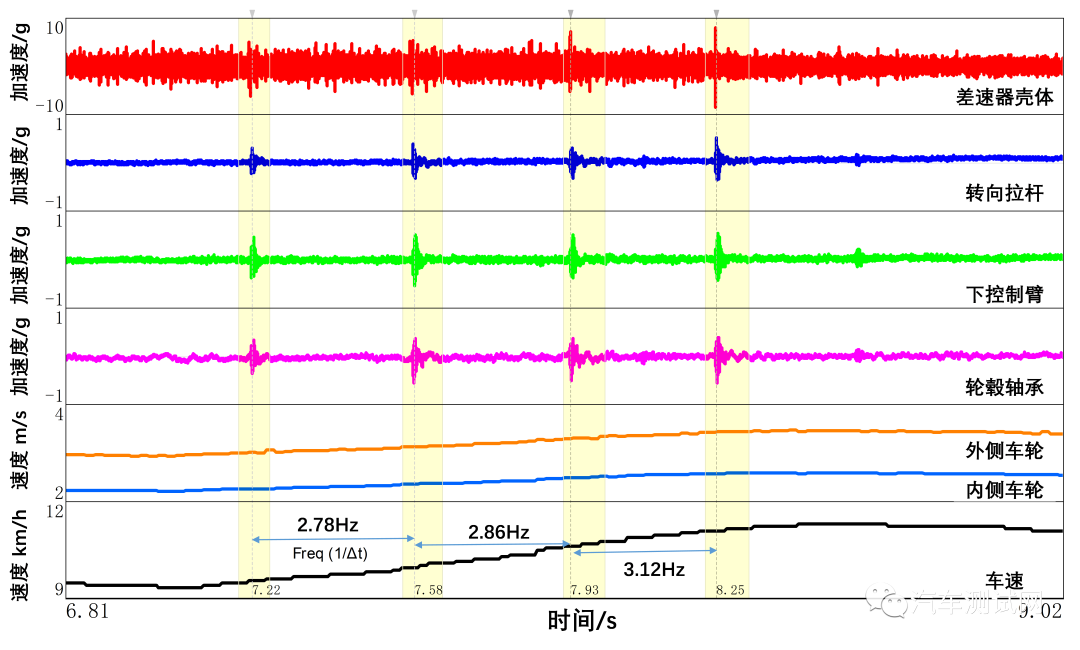
图4 转弯异响的振动测试时域特征分析
根据图4中信道的测试结果对比可知,①该车辆在车速为9~11 km/h的定圆转弯行驶过程中,前机舱底盘传动部件的振动加速度出现了4~5次的瞬时冲击特征;②差速器输出口壳体处的瞬时振动冲击幅值最大,其振动加速度峰值接近8 m/s2,超过底盘其他位置10多倍以上。而差速器壳体处的振动是典型的旋转机械非线性和非高斯信号,存在较强的动力总成激励载荷干扰,信噪比不高,其故障特征模式识别与降噪处理方法已有较多的研究文献[12-13],本文不再赘述;③转向拉杆、下控制臂和轮胎轮毂位置的异常振动冲击特征更加显著,这主要是由于减小了动力驱动系统的振动干扰,其峰值幅值约在0. 5 m/s2以下;④在准稳态转向过程中,通过各振动冲击特征时刻的时域间隔,换算出异响频率F(1/Δt)约为2. 78~3. 12 Hz。
1.3►
差速器内部结构设计简述
该车型CVT变速器搭载了已被广泛应用的对称式圆锥齿轮开式差速器,其内部结构如图5所示。其主要零部件有两个圆锥行星齿轮(齿数zp 为10)、一字式行星齿轮轴、两个圆锥半轴齿轮(齿数zs为25)、两个平面垫片、两个球形垫片、差速器壳体和两个推力轴承等。两个行星齿轮分别空套在行星轴轴颈上,半轴齿轮与行星齿轮相互啮合,行星齿轮轴通过圆柱销定位在差速器壳体之间。其中,为保证行星齿轮与行星轴轴颈之间的正常润滑,采用通槽式的行星轴结构设计,在两侧表面分别对称地铣出平面,坯材为20CrMnTiH,并进行了表面镀镍耐磨处理。
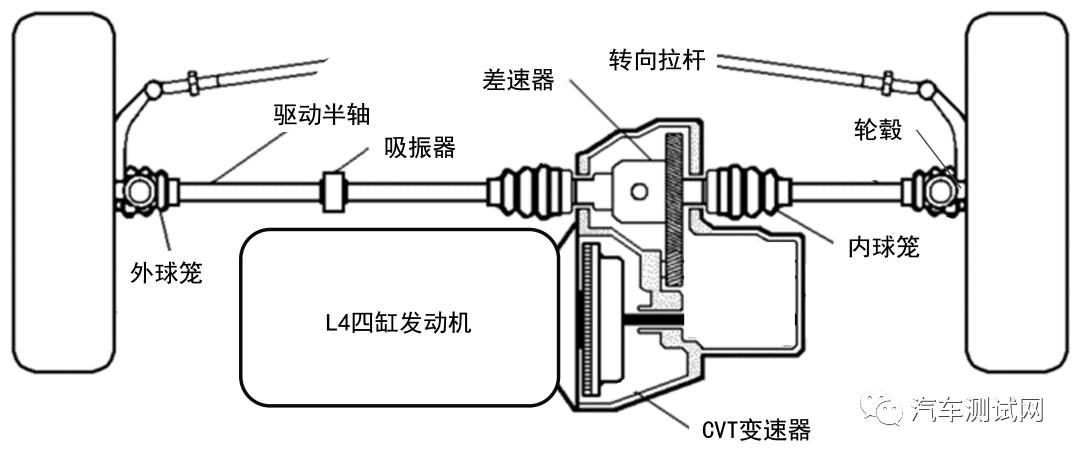
图5 差速器内部结构示意图
1.4►
行星齿轮自转与异响冲击频率的关联分析
车辆直行时,行星齿轮无自转运动,只存在公转,并驱动两个半轴齿轮同速同向转动。汽车转弯时,由于两侧车轮转弯半径的差异,差速器的内摩擦力矩引起两个行星齿轮方向相反的自转运动,以抵消车轮之间的转弯附加阻力矩,如图6所示。行星齿轮驱动半轴之间的转速差Δω 为[14-15]
Δω = ω1 - ω2 = 2ω3 (zp /zs ) (1)
式中,ω1 为外侧半轴转速;ω2 为内侧半轴转速;ω3
为行星齿轮自转转速;zp 为行星齿轮齿数;zs 为半轴
齿轮齿数。
根据图4中ESC系统测试采集的内/外侧车轮速度差Δv 约为0. 83 m/s,由前轮型号205/55R17换算出的轮胎周长C 为2. 06 m。通过公式Δω = Δv/C,可以推算出整车转弯测试过程的半轴齿轮转速差Δω 约为24. 17 r/min,再基于式(1),可得到行星齿轮自转转速为30. 21 r/min。假设行星齿轮为主动齿轮,并与半轴齿轮在转矩传递过程中产生啮合敲击,那么,撞击频率就约为5. 04 Hz, 而这与图4 中给出的2. 78~3. 12 Hz异响频率F(1/Δt)相差较大。因此,整车转弯异响的原因与差速器的齿轮啮合过程没有直接的关联性。
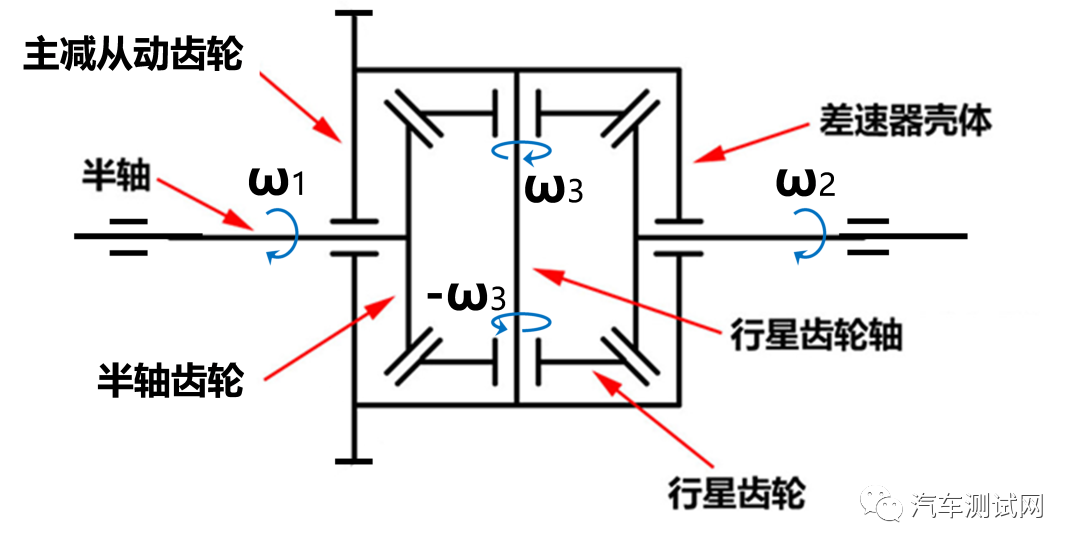
图6 转弯工况差速器零部件运动的示意图
综上所述,该车辆的转弯异响可以初步排除驱动轴外球笼、转向拉杆球头、车轮轮毂、半轴谐振器和齿轮啮合敲击等常见因素;再根据异响时域特征以瞬时振动冲击为主,也大致可以排除轴承类和垫片类的连续性界面摩擦异响因素。因此,推测该异响源可能发生在差速器内运动部件之间的干涉撞击。通常,这种瞬态冲击异响的影响因素较多,可能涉及到差速器内多个运动零部件的间隙冲击,其问题排除与工程解决的难度较大。
2 基于变速器差速性能台架的异响排查分析
经整车转弯行驶工况的测试分析,初步判定异常噪声与无级变速器内的差速器存在较强关联性。但由于差速器壳体表面上振动传感器测试信号的信噪比不高,因此,有必要在前驱变速器差速性能试验台架上开展进一步的异响源排查工作。如图7所示,按照实车的安装状态,变速器总成刚性固定在驱动电机的输出端,左、右驱动半轴夹角保持与整车一致,通过轮毂轴承分别连接到测功机,并提取整车测试工况的发动机转矩和半轴输出转速,作为试验台架施加的模拟载荷。同时,在差速器壳体、左、右轮毂位置分别布置加速度传感器,同步采集驱动电机转速、左、右半轴转速和转矩等信号,在变速器总成差速运行工况下,进行异响问题的排查分析测试工作。
将实车转弯工况存在异响的变速器整体拆装下来,再安装在变速器试验台架上,进行了对比验证。在变速器差速运行的试验现场,人耳可以清晰地辨识出复现的异常冲击噪声,而当两侧驱动轴的转速相同时,异响则消失。根据图8所示的台架测试结果,该差速器壳体的振动瞬时冲击特征与整车测试的时域形态相吻合。并且,由于没有发动机激励载荷的干扰,与整车测试情况相比,变速器试验台架的差速器壳体振动通道信噪比明显提高。经测试数据对比分析可知:①变速器差速性能台架试验可以复现整车转弯工况的异响问题,以此可快速进行零部件级的原因排查工作;②差速器壳体处的瞬时冲击特征最为显著;③与左、右驱动半轴相连的轮毂位置几乎没有相似的振动冲击特征,其振动音频回放的撞击声也极小。因此,进一步验证了整车转弯异响源来自于差速器内部传动的过程。
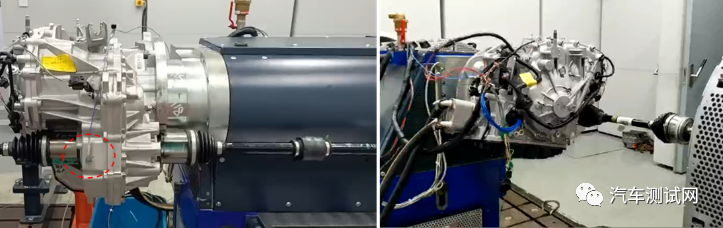
图7 变速器差速性能试验台架和传感器布置
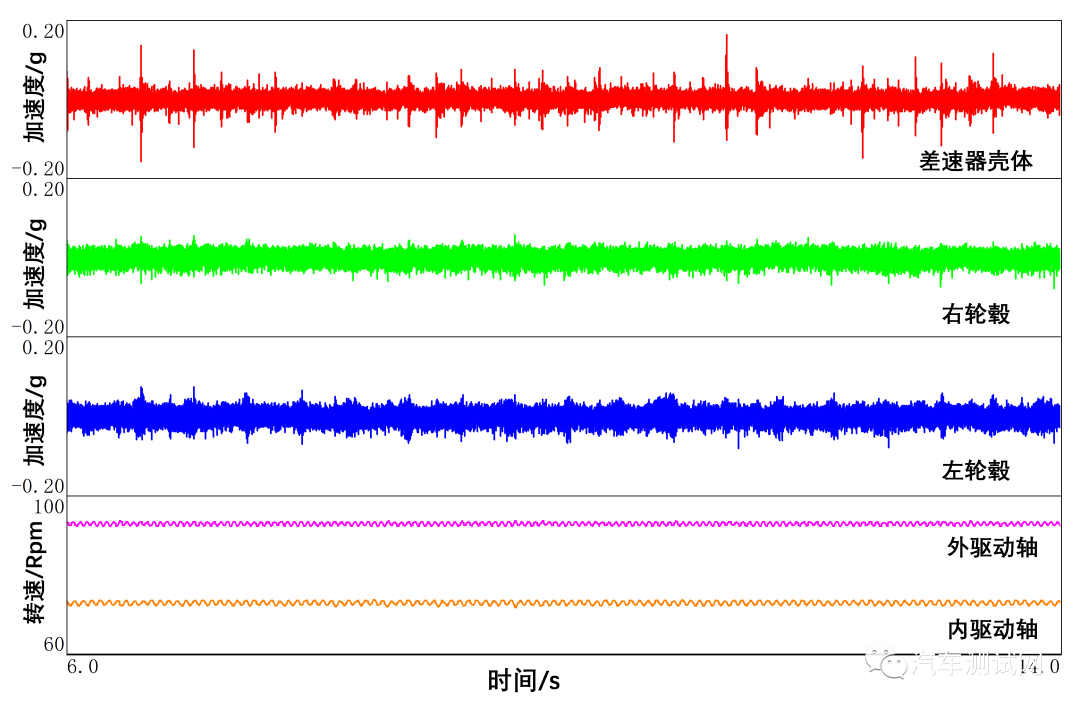
图8 变速器差速性能台架试验的时域特征分析
3 差速器异响潜在原因分析与工程控制思路
3.1►
异响故障差速器的零部件解析
经对存在异响的故障差速器进行拆解,各零部件的外观上无明显的磕碰或缺陷,无错漏装的情况;半轴/行星锥齿轮的啮合表面没有发现撞击痕迹;在行星齿轮平垫片和行星齿轮球面垫片上存在有正常的磨痕。但是,在与行星轴间隙配合安装的圆柱定位销表面,发现了异常的线面撞击痕迹;行星轴平面槽的棱边处也发现了异常干涉的刮痕,如图9所示。这与之前整车测试结果的异响原因分析推测比较吻合。
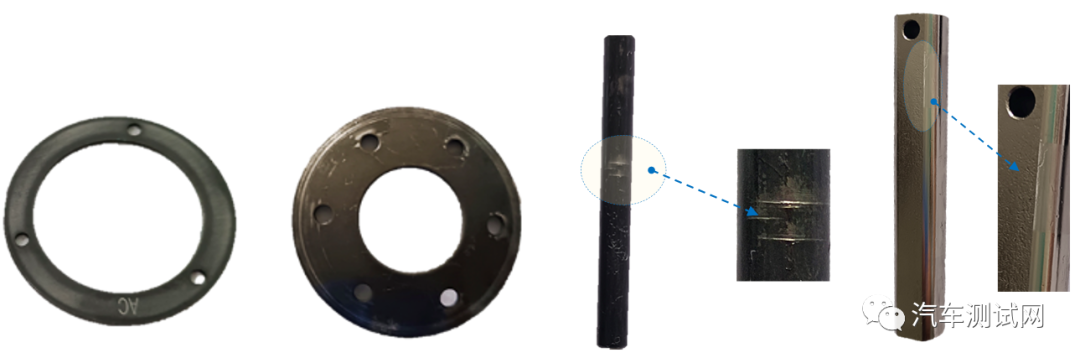
(a) 平垫/球面垫片的正常磨痕 (b)定位销/行星轴的异常痕迹
图9 故障差速器的零部件解析
3.2►
差速器异响的潜在原因分析
基于整车和变速器台架的试验测试排查分析以及故障零部件的解析,可以推断:该车型转弯异响的主要原因是行星齿轮轴与圆柱定位销之间的配合间隙过大,在差速器壳体驱动一字式行星轴和行星齿轮的过程中,存在转矩传递不连续的问题,引起行星齿轮轴的轴向滑移和非正常的自转运动,导致行星轴与差速器壳体之间发生间歇性冲击现象,并在行星轴定位销表面产生了明显的线条状撞击印痕;另外,如果行星轴与行星齿轮之间润滑油膜动态压力的稳定性发生破坏,可能导致干摩擦接触现象,这应该是产生该异响的次要原因。
3.3►
差速器异响的工程解决思路
在实际的动力传动系统复杂异响问题解决过程中,由于对问题机理缺乏深入的分析与推断,通常会采用“试错法”开展大量的排查工作,这反而会降低异响排查的效率。本文中根据以上整车与台架的测试数据分析结果以及对差速器异响的潜在机理推测,建议可以从以下4个方面改善或解决整车转弯异响的问题:
(1) 首要的改进措施是减小或消除行星齿轮轴定位销的安装配合间隙。比如,通过采用过渡或过盈配合的行星轴销孔安装方式;将原来的圆柱定位销部件更改为中空开口的弹性销组合,或者螺纹连接结构的固定销,如图10所示。
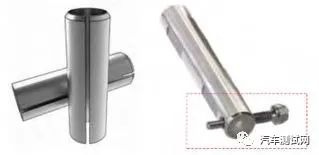
图10 弹性销和螺纹连接销
(2) 提高行星齿轮与行星轴之间的弹性润滑油膜的稳定性,避免产生“碰摩”现象。比如,为了减小行星轴截面的不规则性,减少平行槽的铣削厚度,或者增加平行槽棱边的圆角过渡,避免在楔形油膜间隙的动态压力突变;在行星齿轮的齿间,加工出径向油孔通道;采用多孔的球面垫片、在行星轴的表面加工螺旋导油槽结构等。
(3) 适度降低差速器锥齿轮之间的啮合侧隙,减小行星轴与差速器壳体之间的冲击能量。比如,减小齿轮轴向安装尺寸链封闭环的配合间隙;增加半轴齿轮或行星齿轮的垫片厚度等。此外,差速器运转的工作温度也会影响啮合齿轮与运动部件之间的动态侧隙[16]。
(4) 通过底盘ESC标定的优化,降低左、右半轴的转速差限值,也可间接地减少转弯过程中差速器异响发生的频次[17]。
4 工程改进方案与试验验证
在保持差速器的主体结构设计不变以及不影响其可靠耐久的综合性能前提下,不调整齿轮的啮合侧隙状态,再结合该车型项目开发成本和后期设变周期等因素,本文中主要从行星轴定位安装的尺寸要求与加工工艺方面,为快速有效地解决车辆转弯的差速器异响问题,提出了3项具体的优化措施方案:①将原来的行星轴安装孔与圆柱定位销之间配合间隙0. 28~0. 38 mm,更改为0. 1~0. 18 mm;②减小行星轴与差速器壳体的配合间隙, 从0. 016~0. 052 mm变更为0. 010~0. 036 mm;③增加对通槽式行星轴棱边的圆角打磨工序,提高与行星齿轮运转的油膜稳定性。
优化措施实施后,基于变速器差速性能台架进行了改进优化方案的试验对比验证,主观上已经感知不到“嗒嗒”的撞击异响声;由图11所示优化前/后客观测试数据的对比可知,差速器壳体的振动冲击特征基本消失,内/外侧半轴输出转矩的波动幅值显著降低,说明差速器转矩传递过程更加平稳。整车换装改进后的变速器总成之后,低速行驶转弯工况的异响消失了,提升了该车型的驾驶品质。
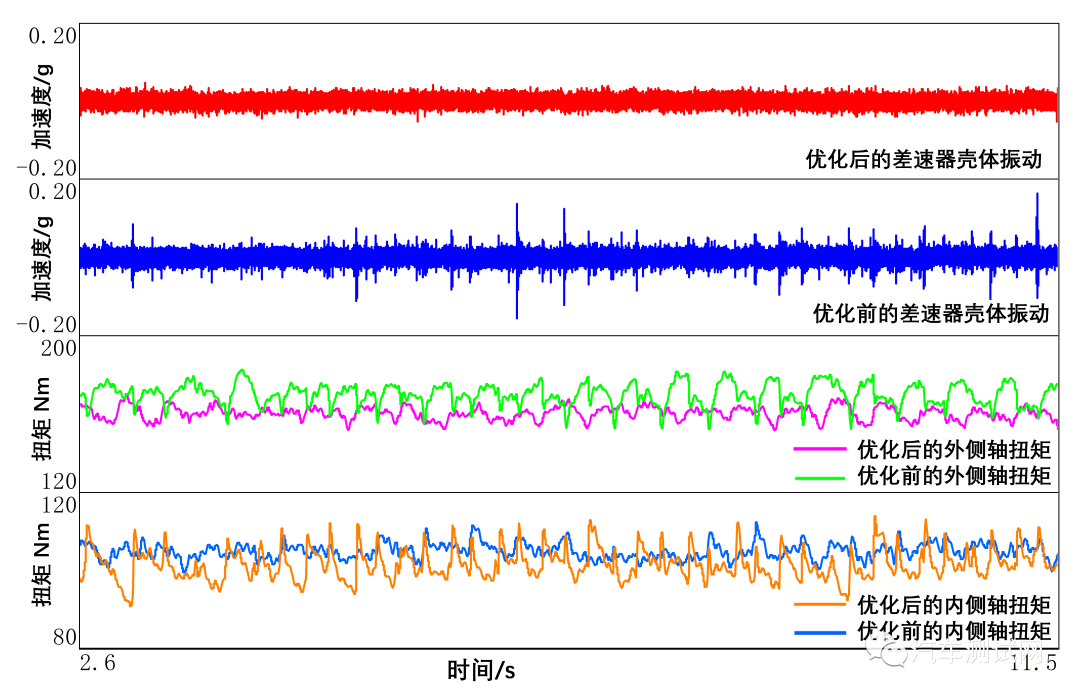
图11 优化前/后的差速器台架试验对比
5 结论
由于车辆转弯异响问题的影响因素较多,其异响机理也不尽相同,涉及到的排查过程也较繁琐,通常很难快速有效地进行解决。差速器是保障汽车转向能力的重要部分,而行星齿轮组和行星轴又是汽车差速功能的关键核心组件。本文中以某搭载无级变速器紧凑型轿车的低速行驶转弯异响为例,系统阐述了该异响问题的分析排查过程,通过差速器性能台架实现了异响问题的复现,结合故障零部件的解析,提出了差速器异响问题的潜在机理和改进措施,并通过行星轴定位装配方式和加工工艺的优化,快速准确地消除了该异响问题。
随着市场用户对汽车NVH 性能的要求越来越高,动力驱动系统的噪声水平与异响控制越来越重要。在差速器部件开发集成初期,可基于差速器性能台架进行模拟整车全工况的振动噪声试验测试和验证,以提升核心传动零部件开发与整车性能集成的技术水平。
参考文献
[1] 柴少彪,汤会芳,孟庆祥.减速箱差速器行星轮圆柱销失效分析[J].汽车科技,2020(5):80-83.
[2] 姚书涛,关崴,赵彦辉,等.自动变速器差速器烧蚀故障分析[J].汽车实用技术,2016(11):149-151.
[3] 宋开勋.轴间差速器十字轴的疲劳断裂分析与改进[J].中国重型装备,2013(2):16-18.
[4] SHI Zhenghong,CHEN Jui,KOLIVAND Mohsen,et al.Design optimization of differential bevel gear for NVH improvement[C].SAE Technical Paper,2019-01-1552,DOI:https://doi. org/10.4271/2019-01-1552.
[5] Miho Nakatsuka,Tetsuya Miwa,Junji Yoshida.Development of an analytical method for rear differential gear whine noise utilizing principal component contribution by OTPA and CAE[C]. SAE Technical Paper,2019-01-1555,DOI:https://doi. org/10.4271/ 2019-01-1555.
[6] 陈煜,张军,滕晓雷,等.电驱总成转向引起的差速器异响诊断与分析[C].中国汽车工程学会年会暨展览会,2020:1179-1182.
[7] WAN X,ZHANG J,XU Z M,et al.A fault identification method of rear axle bearing under lateral dynamic load of vehicle[C].China SAE Congress,2018:749-763.
[8] 封旗旗,王陶,王良模,等. 基于多目标优化的差速器齿轮修形[J].机械传动,2020,44(9):153-158.
[9] 刘宏,范春利,李浩亮.双金属垫片在驱动桥差速器中的应用及参数设计研究[J].汽车实用技术,2018(20):156-158.
[10] YUAN W,DONG G N,GUO Q J,et al.Tribological performance of differential gear end-face sliding on washer with a radial groove[J].
Engineering Failure Analysis,2017,85:126-136.
[11] 易勇,刘志浩,姜文义,等.差速器耐久性规范与异响失效分析[J].汽车技术,2014(10):32-35.
[12] 郭远晶,魏燕定,周晓军,等.基于S变换谱阈值去噪的冲击特征提取方法[J].振动与冲击,2014,33(21):44-50.
[13] LEE J Y,NANDI A K.Extraction of impacting signals using blind deconvolution[J].Journal of Sound and Vibration,2000,232(5):945-962.
[14] 张利鹏,祁炳楠.对称式行星齿轮差速器的转矩转速分配特性研究[J].机械设计与制造,2012(9):138-140.
[15] 周新建,于孟,查小净,等.差速器齿轮机构的运动学及动力学分析[J].机械传动,2010,34(3):18-21.
[16] 魏聪,王优强,周亚博,等.汽车差速器锥齿轮差速工况下的热弹流润滑分析[J].机械传动,2019,43(5):110-115.
[17] 刘丽新,汤一飞,屠有余,等.某汽车差速器故障原因分析及对策[J].汽车文摘,2020(8):54-57.
作者简介
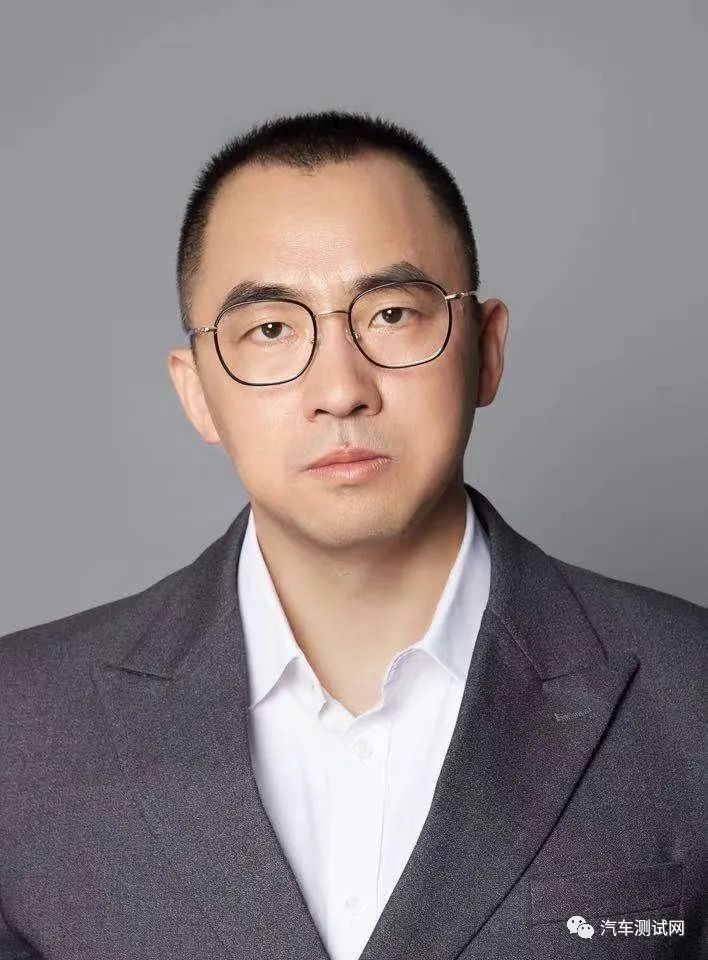
张军
博士,正高级工程师
吉利汽车研究院
上海交通大学博士,正高级工程师,现任吉利汽车研究院NVH技术专家,专注于振动噪声领域研究与工程实践20多年。
E-mail:zj_zmkm@126.com
原载于《机械传动》2022年第9期,
DOI:10. 16578/j. issn. 1004. 2539. 2022. 09. 017
受作者授权发布在本平台,未经允许不得转载。
投稿:marketing@auto-testing.net
最新资讯
-
沃尔沃汽车:创新驱动的豪华品牌
2025-04-24 18:16
-
飞书项目落地ASPICE解决方案,助力汽车软件
2025-04-24 09:59
-
驾驶员监控系统DMS合规认证的“中西结合”
2025-04-24 08:23
-
自动驾驶汽车测试关键行人场景生成
2025-04-23 17:12
-
R171.01对DCAS的要求⑧
2025-04-23 17:08