新能源汽车动力电池结构创新实现全面应用
2019年开始动力电池企业积极探索结构创新,以CTP技术对电池包结构内部进 行创新实现高质量降本增效,有效对冲了较大程度的原材料成本上升压力。一方面 通过电池包内材料件与结构件的减少降低材料与工艺成本,另一方面通过标准化与 规模化生产提高生产效率降低生产成本,并且同时实现电池续航能力提升,连续打造爆款车型,2022年产品日益成熟后全面导向市场,尤其在原材料成本压力下将加 快以CTP为代表的结构创新技术应用,不仅短期有效消化了成本压力,在长期指引了技术平价之路。
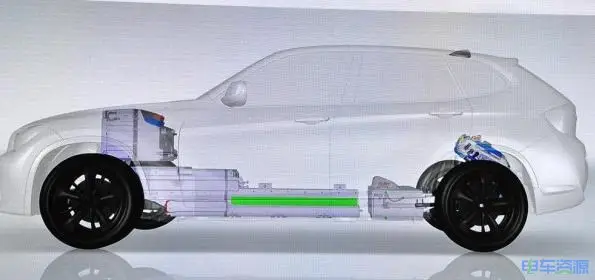
(一)CTP 结合磷酸铁锂技术开启技术平价之路
2020年以来CTP结合磷酸铁锂技术以成本优势推动新能源汽车平价趋势,打造 诸如特斯拉Model 3、比亚迪汉等高性价比爆款车型,并逐步打开海外客户接受度。2021年特斯拉、比亚迪、上汽通用五菱等加大磷酸铁锂应用持续打造爆款车型,2021 年12月宏光MINI EV销量50561辆,维持销量第一,特斯拉Model 3、特斯拉Model Y 分别以40500辆和30102辆随其后,磷酸铁锂车型大幅包揽畅销榜,尤其是2021年3 月小鹏P7开始应用磷酸铁锂与CTP技术,8月特斯拉Model Y上市磷酸铁锂版本,对 销量快速产生积极影响。随着小鹏P5、比亚迪海豚/DM-i系列、长城欧拉等车型集中 交付,CTP结合磷酸铁锂技术更广范围推广,2022年10-20万元新能源乘用车市场需 求有望释放奠定技术平价基石。
2020年10月小鹏P7车型上市,2021年3月,小鹏宣布旗下P7车型将搭载CTP技 术电池包,与此同时当月销量环比上月增长102.63%,后续增长持续放量。
2021年9月23日,蔚来汽车应用新一代CTP技术的75KWh三元铁锂电池上线, 且75KWh电池包车型售价、BaaS价格、换电权益、续航升级权益等与原三元锂 70kWh电池包车型相同。对于ES6而言,新CTP的上线在对车型降本提效的同时保 持价格不变,等同于另一种形式的降价从而获得销量增长。可以看到2021年9月新 CTP电池包上线后,ES6的2021年9-12月销量增速分别为64%/-6%/98%/98%(10月 增速为负系工厂生产线改造为兼容新车型ET7准时上线),显著高于2020年同期增速 与2021年全年增速,2021年9-12月总销量增速亦高于2021年全年。
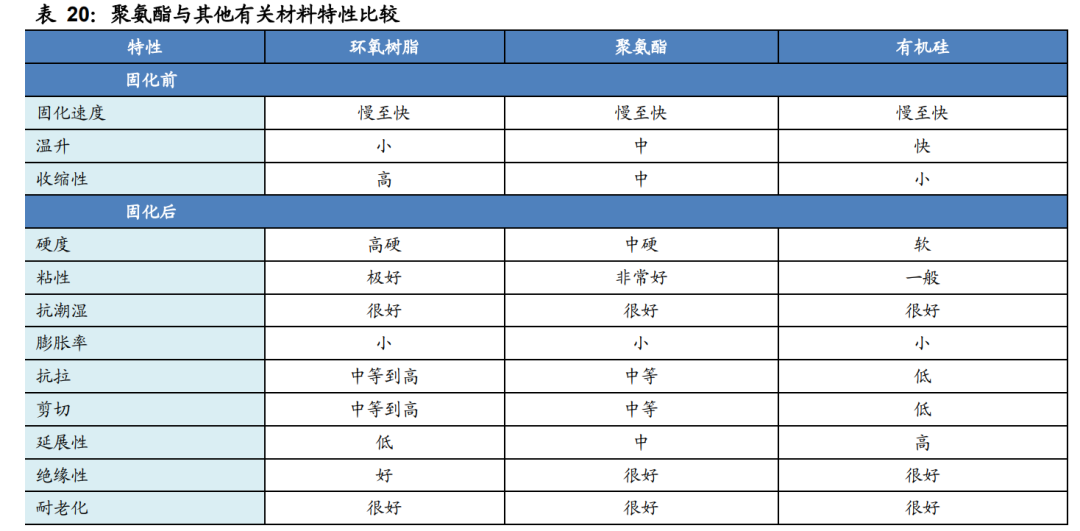
通过复盘CTP电池对小鹏P7以及蔚来ES6销量影响可以推断,造车新势力如蔚 来、小鹏、理想等对于CTP的应用态度会更积极。
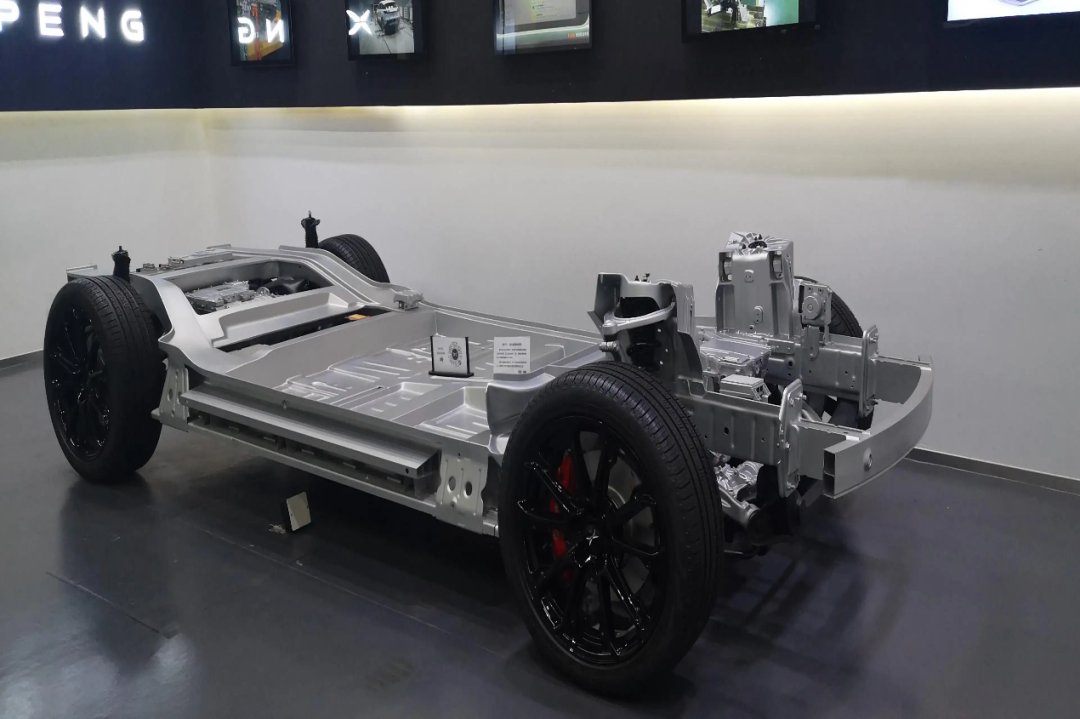
(二)中国电池企业引领全球CTP 技术开发
2019年以来,宁德时代、比亚迪和蜂巢能源陆续发布了CTP(Cell to Pack,无 模组动力电池包)技术,将电芯直接集成至电池包,省去模组环节可以有效提升电池包的空间利用率和能量密度。2021年3月,宁德时代宣布将于2025年前后正式推出高度集成化的CTC(Cell to Chassis,将电芯直接集成到底盘上,省去模组与电池 包)电池技术。按照宁德时代董事长曾毓群介绍,CTC技术不仅会重新布置电池, 还会将三电系统纳入进来,包括电机、电控、整车高压如DC/DC、OBC等。未来, CTC技术还将进一步通过智能化动力域控制器优化动力分配和降低能耗。
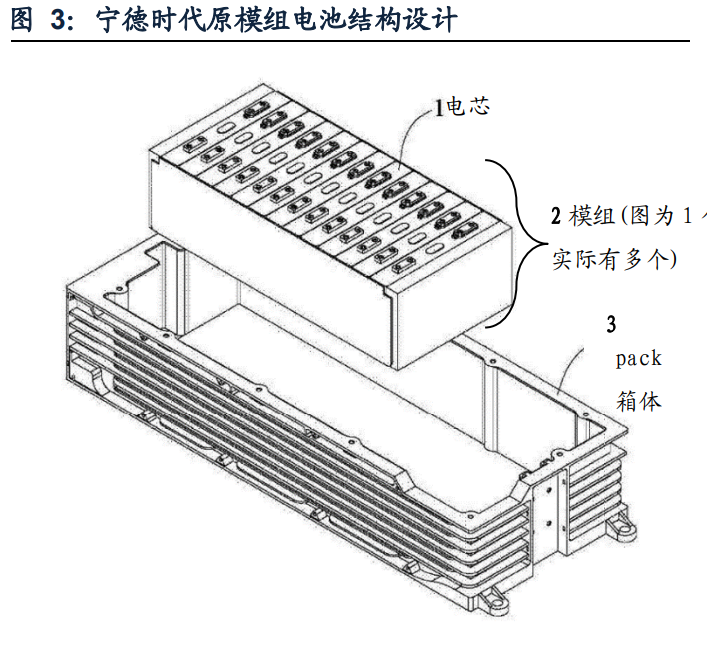
1.宁德时代:CTP的渐进演变模式
常规电池包构成:电芯-模组-电池包。将单个电芯大面相互粘接贴合, 采用焊接两个侧板以及两个端板的方式,将单体电芯固定成电池模组。焊接成组后, 采用吊装夹具的方式,将多个电池模组移入电池箱体中,通过固定板和电池箱体的 固定板上的水平支撑面固定。
CTP电池包构成:电芯-电池包。将多个电芯直接布置在箱体内(用散 热片做隔贴合),无需先将多个单体电芯组装成电池模组,简化了电池包的结构和 组装工艺。
(1)宁德时代原电池包和模组结构:
电芯组装成模组的流程如下:
①首先,电芯与电芯间添加气凝胶(柔性吸能材料)来进行粘连、隔热和防撞优化。
②其次,在堆叠后的电芯组焊接端板、侧板进行成型和稳定加固。侧板和端板见通过焊接相连。其中端板除了起到聚拢单体电芯,提供一定压力的作用以外,有时还会将模组与电池包的固定结构设计在上面。
③再次,在电芯成组上方进行电路布局。在电芯组上方放置隔离板,再将CSC (电池监控单元,上面设置有多个导电片和键合引线)放置在隔离板上,通过导线 将CSC与电芯相连(导线一端串联电芯,一端链接CSC上面的键合引线)。
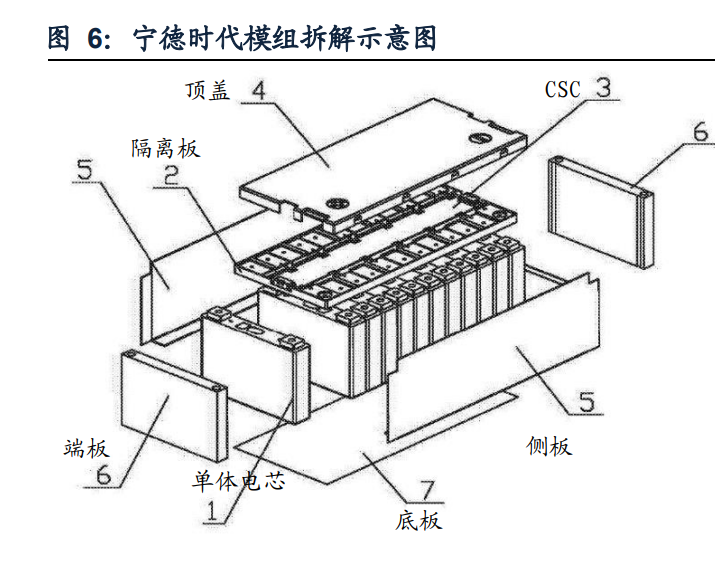
模组装电池包流程:
电池包Pack构成:动力电池模组+电池箱体结构(上盖+托盘+支架结构[电池箱 体的横梁纵梁支撑座螺栓结等)+电气系统(线束+继电器)+热管理系统(液冷板) +电池管理系统BMS。
①结构系统:主要由动力电池Pack上盖、各种金属支架、电池箱外壳、托盘和 螺栓组成,是Pack的“骨骼”,起到支撑、抗机械冲击、机械振动作用。
②电气系统:由高压跨接片或高压线束、低压线束和继电器组成。
③热管理系统:包括液冷板,冷却水管组成。
④动力电池管理系统 (BMS):由传感器、执行器、控制器(电控单元)等组件构 成,采集系统的电压、电流、温度等数据。有效地管理控制动力电池包的充放电,以 及响应整车层面的功能需求。
(2)宁德时代CTP:
宁德时代在专利中提到的CTP可以看到:结构中省去了模组结构(模组顶盖、模 组端板、模组侧板,模组隔离板、模组底板)。上部将电芯正极通过一层绝缘构件+ 结构胶与上箱盖相连。下部将电芯底部通过绝缘构件+结构胶与下箱体相连(液冷板 直接集成在下箱体上)。液冷板与下箱体中间是否有缓冲垫,尚无统一,是选配件。在此种集成过程中节省掉的材料构件及工艺流程有:
①模组的侧板和端板:端侧板构件和端侧板的焊接工艺流程全部省去。
②螺栓及锁附:原来每模组要锁四个螺栓(如有8个模组,总计32个;现在变成 一个模组后仅需四个螺栓。
③输出级的简化:原来每个模组有2个输出级(如果有八个模组,即需要16个输 出级),当前仅需2个输出级[铝牌+铜牌]。同时输出级的焊接工艺也相应减少。
④输出级后接插件简化:原来每个模组都有正负极的接插件。现在仅需两个接 插件。
当前,在车型的实际应用上,宁德时代的CTP结构当前尚未完全去除模组结构,而是将小模组结构转化为大模组结构(如原来8~12个模组,转化为2~4个大模组)。
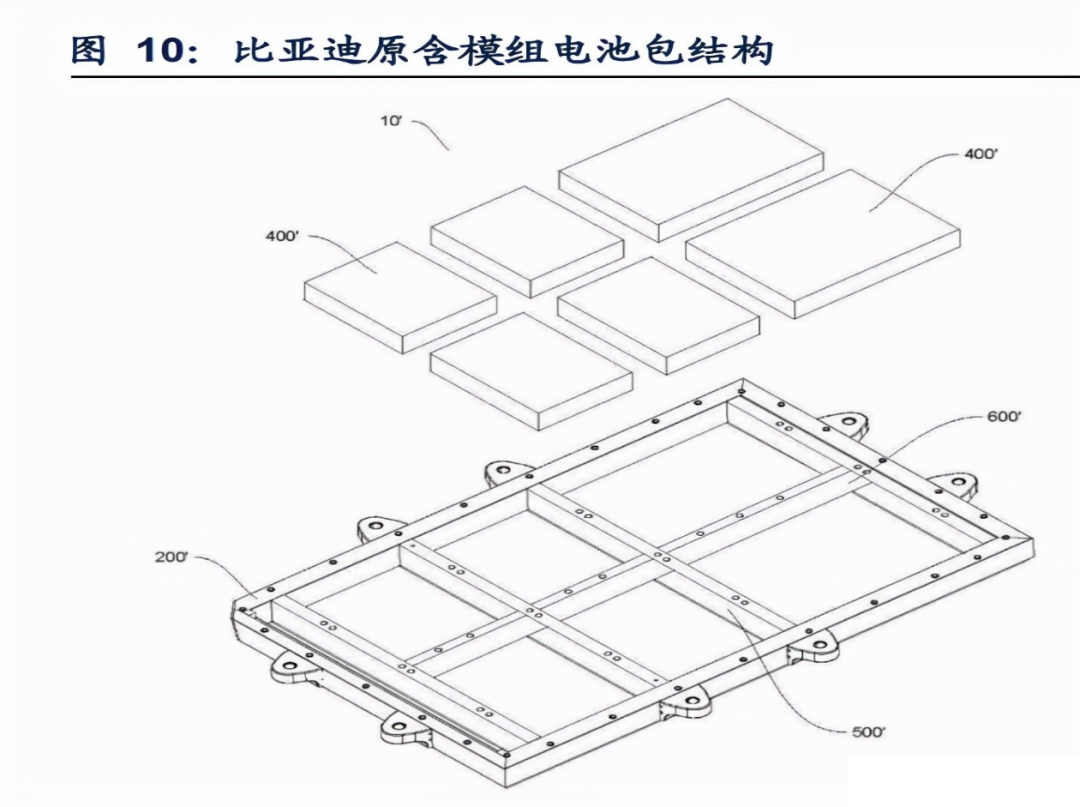
2.比亚迪:刀片电池形态
比亚迪传统电池包的安装
①模组的安装:电池模组包含多个依次排列的单体电芯;在电芯阵列外部设置 有端板和侧板,同时端板和侧板通过螺钉连接,或者通过拉杆等其它链接件连接, 实现对电芯阵列的固定。
②电池包体的安装:包体内设置有两个横梁一个纵梁,两个横梁和一个纵梁将 单体电池分隔成六个电池模组,每个电池模组均具有侧板和端板。电池模组通过螺钉的方式固定在横梁或纵梁上。
这种设计结构下,由于端板和侧板均具有一定的厚度和高度,连接方式中的横 纵梁,均浪费了包体内的空间,降低了包体内的体积利用率。一般情况下,此种结构 中的包内单体电芯体积与包体的体积比值在40%~50%。
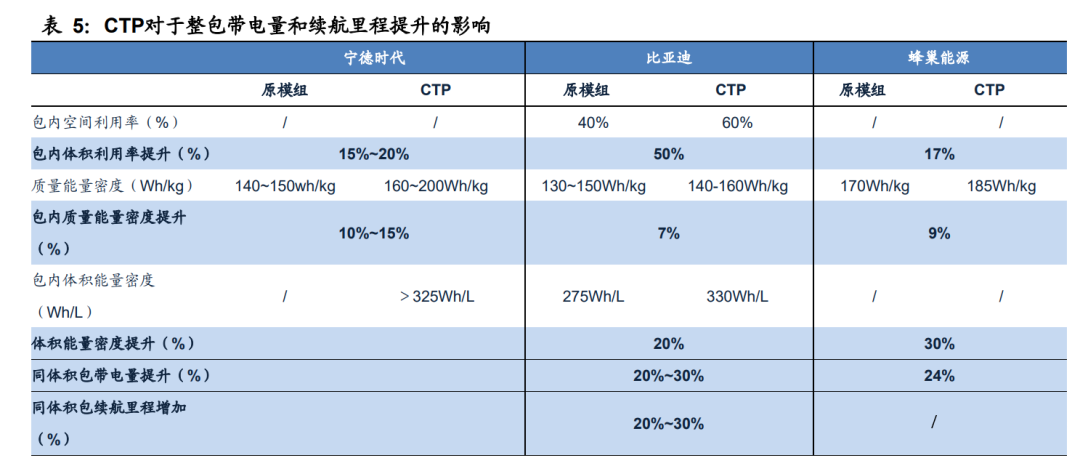
比亚迪刀片电池(无模组电池包的结构):单体电芯的长度直接延申在动力电池的包的整个宽度方向(B)上,即沿动力电 池包的宽度B方向,单体电芯由一侧延申到另一侧,两端配合于宽度方向B上相对的 两侧壁,固定于包体。由于包提内部无需横梁和纵梁,直接通过连接的单体电芯承 担加强筋的作用,极大的简化了包体内部的结构。同时包体的生产制作工艺简化, 单体电芯的组装复杂程度降低,生产成本降低。
另外,还有一种电池包的设计结构。单体电芯的长度方向沿动力电池包 的宽度方向B布置。多个单体电芯沿电池包的长度方向A排列成电池阵列。包提内的 高度方向C至少有两层电芯阵列(两个模组上下叠放)。
3.蜂巢能源:长条型L600“6条”电池LCTP方案
2021年10月,蜂巢能源推出L600长薄型电池。把多个L600“6条”电芯组成的储 电组件直接放置在电池包壳体内,通过电池包壳体与车身的连接,取代现有的电池 包结构,减少了部件数量,使得容纳L600“6条”电芯的空间更大,有效提高了电池 包的能量密度,电池包壳体内部的空间利用率由原来的35%-40%提升至50%-60%。
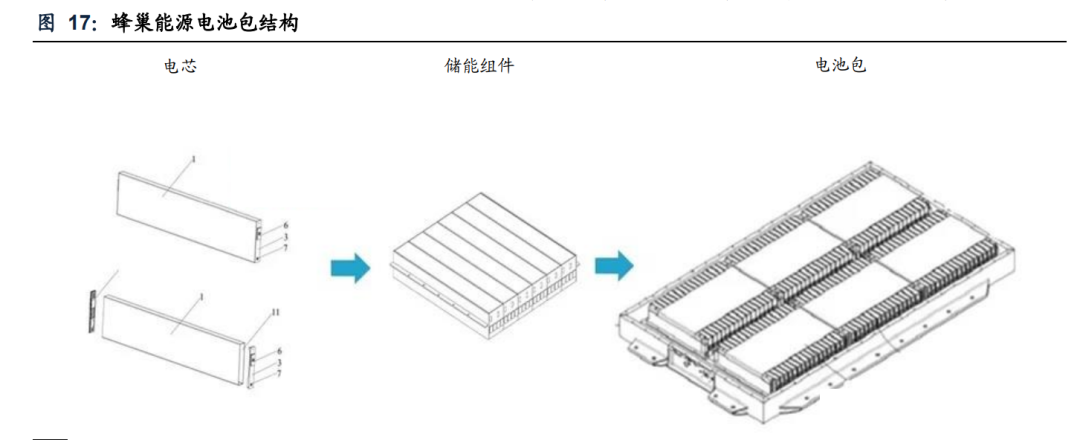
(三)电池结构创新同步降本增效,成本压力下有望加速
1.2021年上游原材料成本上涨200~300元/kwh
2021年以来,上游原材料价格大幅增加,动力电池生产成本不断增加挤压盈利 水平。其中:材料成本占比最高的正极材料:磷酸铁锂从2020年底的3.85万元每吨 上涨至2021年底的10.10万元/吨;三元正极(以5系为例)自2020年底的14~15万元 /吨上涨至2021年底的27~28万元/吨。核心电池级碳酸锂从2020年底的5.00万元/吨 上涨至2021年底的27.51万元/吨。另外电解液价格从2020年底的3.80万元/吨上涨至 2021年底的11.03~12.05万元/吨。电池级铜箔自83元/公斤上涨至107元/公斤。
经由我们测算,2021年以来,由于原材料价格上涨,电芯制造成本的大幅提升;其中三元锂电池电芯成本增加308.15元/Kwh,磷酸铁锂电池电芯成本增加276.20元 /kWh。原材料成本大幅上涨,倒逼电池厂商加速结构创新降本增效。
2.CTP实现降本:结构件材料件减少,有望降本100元/kWh
电池包通过CTP方式组装,一方面模组层面,单体电芯无需布置在两个端板和 两个侧板围设形成的模组框架内,省去了模组相关的结构件(端板侧板以及大量用 于固定安装模组的螺钉等紧固件)。另一方面包体层面,单体电芯本身可承担一部 分机械加强作用,可以省掉或者减少电池托盘的加强筋,包体内的支撑件减少,整 体的材料成本降低。同时整体的制造工艺低得到简化,单体电池的组装复杂程度降 低,节省了大量的人力、物力等生产制造成本。据我们测算,去模组化后整体电池包 减少生产成本约100元/kWh。
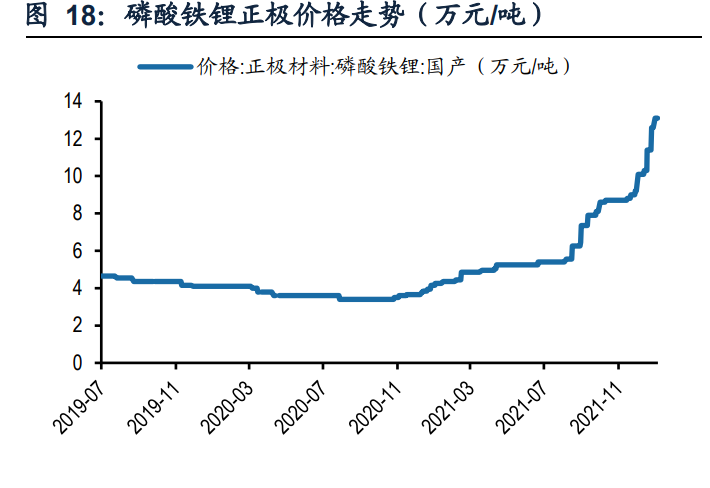
3.CTP实现增效:提升电池包带电量,增强续航里程
CTP电池通过提升电池包内空间利用率,实现体积能量密度提升。同时通过电 池包整体的轻量化程度共同作用,实现续航里程的增加。
(1)宁德时代:包内体积利用率提升15%-20%,整包带电量提升。据宁德时代发布会显示:其CTP电池包较传统电池包而言,体积利用率提高了 15%-20%。在能量密度上,传统的电池包能量密度平均为140-150Wh/kg,CTP电池 包能量密度则可达到200Wh/kg以上。
(2)比亚迪:包内体积利用率提升20%,整包带电量提升20%-30%。从比亚迪申请专利《CN209389112U》能看到,在电池包总体积一致的情况下, 原有的电池PACK结构,包内空间利用率大概在40%左右;而采用了CTP技术的比亚迪电池包,省去各模组的侧板、端板、紧固件、横梁、纵梁等组件,包内空间利用率 大概在60%左右。因此,相较于原有电池包,刀片电池包在同等体积情况下,带电量 约增加20%-30%,续航里程也能提升20%-30%。
(3)蜂巢:包内体积利用率提升17%,整包带电量提升24%。据蜂巢能源发布会资料显示:其L600段刀片磷酸铁锂电池,能量密度175Wh/kg, 采用CTP的全新Pack方案,相较于传统模组电池包,矩阵电池包的空间利用率可提 高17%,体积能量密度提升30%,成组效率提升12%,能量密度增加9%,整包带电 量提升24%,Pack零部件减少20%,成本降低10%。
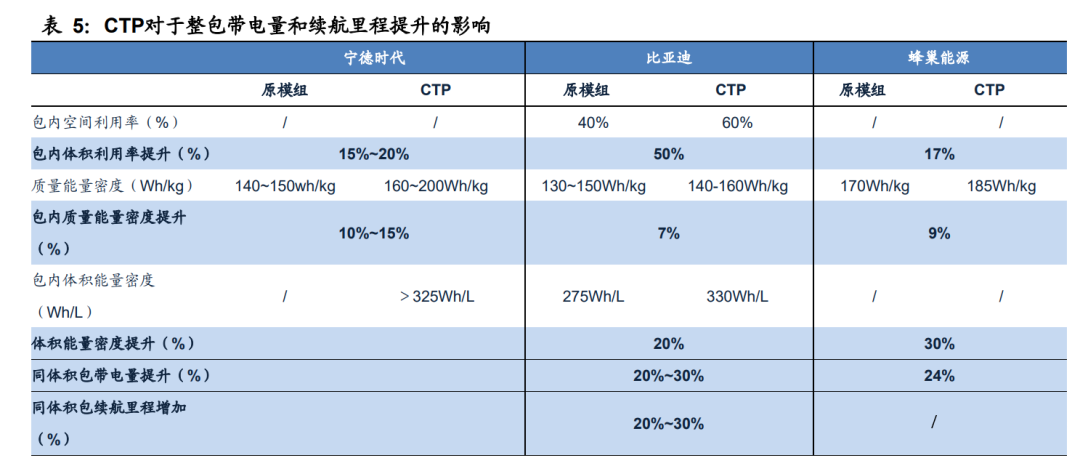
(四)车企连续加快导入,2022 年迎来拐点
自2019年宁德时代在法兰克福车展中提出CTP技术以来,该技术在乘用车市场 和商用车市场都有实现与相关龙头车企展开合作。北汽EU5于2019年9月搭载全球首 款CTP电池包。威马2019年9月宣布将会在2020年北京车展上推出全新威马7系纯电 动轿车,电池包将采用CTP技术。哪吒汽车2020年3月与宁德时代就新能源电池领域 合作正式达成一致,宁德时代将为合众公司CTP高集成度电池Pack技术、5年50万公 里长循环寿命等电池技术,并且表示新电池将很快会应用到未来哪吒汽车等5款车型 上。蔚来于2020年11月6日正式发布容量为100kWhCTP电池包。据悉今后蔚来所有 电池包(标准续航电池包75kWh,长续航电池包100kWh)也将替换为CTP技术电池 包。小鹏旗下G3和P7车型也与分别于2019年和2020年采用CTP技术电池包等。
通过当前已披露的搭载CTP车型的销量数据来看,CTP渗透率在2021年呈现出 明显的增量加速趋势。目前公开的合作车型中也有6款车型还未在2021年实现投产, 这也预示着未来将有更多相关车型陆续实现放量。
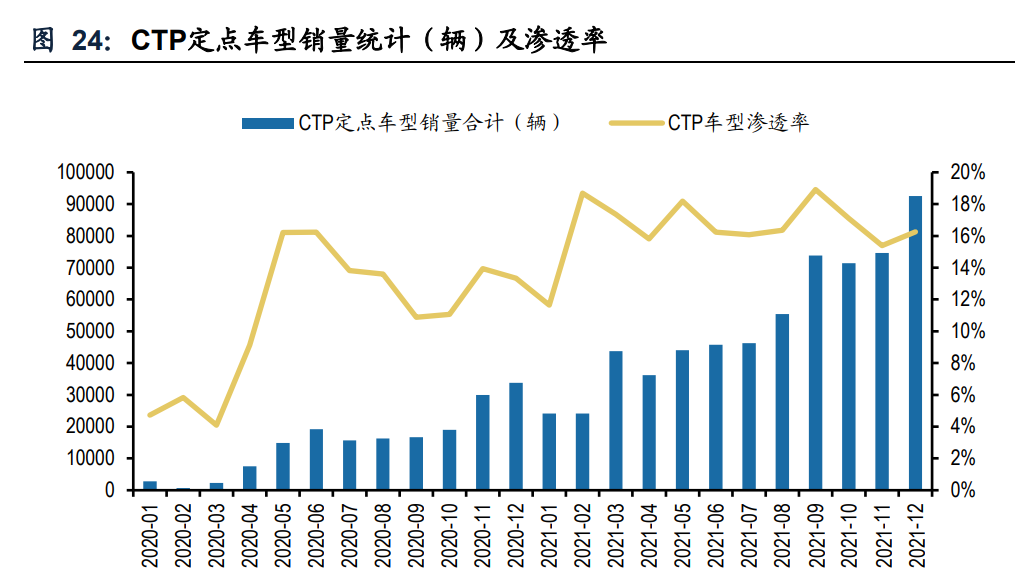

电池企业入场打造全新供应链格局
(一)宁德时代与比亚迪的探索
1.宁德时代:构建从CTP到CTC的全产业链布局
2021年1月27日,宁德时代中国区乘用车解决方案部总裁项延火透露,宁德时代 目前正在规划第二代平台化的CTP电池系统,计划于2022年-2023年投入市场应用。2021年12月21日,宁德时代董事长曾毓群透露其全球首创的CTP技术目前已升级迭 代出第三代。相比上代,电量提升13%,减重10%,能量密度、体积效率继续引领行 业最高。2025年前后,宁德时代计划推出第四代高度集成化的CTC电池系统.2028年 前后有望升级为第五代智能化的CTC电动底盘系统。CTC技术不仅对电池进行重新 排布,还会纳入三电系统,通过智能化动力域控制器优化动力分配和降低能耗,目 标2030年前完成技术开发。目前宁德时代已在积极布局CTC业务相关的除电池系统 之外的核心零部件。
(1)2016年宁德时代实控人之一李平创立上海盘毂动力,布局电机体系。盘毂 动力以盘式电机为核心,集成优化减速箱、控制器等相关零部件,解决了盘式电机一系列的产业化技术难题。据公司介绍,盘毂动力盘式电机体积比同功率径向磁场 电机小56%,重量减轻45%,电机效率MAP超过双90。盘式电机轴向尺寸小、重量 轻的特点为商用车底盘布置提供更优的解决方案,同时能够有效降低整车能耗15% 以上。
(2)2017年设立宁德时代电机。2017年4月,宁德时代设立电机科技有限公 司。公司主营2kW-350kW新能源汽车电机电控及轮边电机桥总成系统、轮毂电机, 低速大扭矩高效节能永磁电机等高科技机电产品。
(3)2020年9月入股芯迈半导体,12月入股杰华特微电子,布局电控核心部件。
(4)2021年9月入股拿森,专注线控底盘解决方案。宁德时代于2021年9月对 拿森进行投资,持股比例约5.47%。专注于智能汽车所需的线控底盘解决方案,主要 产品涵盖电控智能刹车系统 Nbooster、车辆稳定控制系统 ESC、智能转向系统 EPS 等,是国内首个突破线控刹车技术壁垒并量产的公司,是 Booster 产品累计出 货量最大的国产供应商。
(5)2021年10月设立苏州新安,布局电控系统。新安重点布局电动能效优化解 决方案等前沿研发项目开发,包括,电动汽车驱动控制系统、汽车零部件研发及生 产、自动化业务研发、汽车底盘一体化研发及试制等。
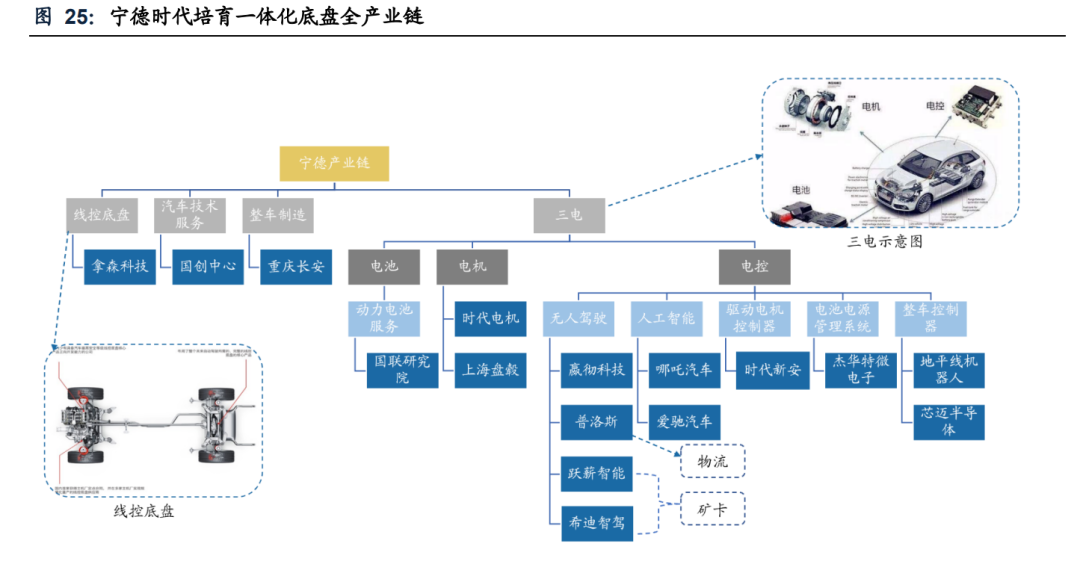
布局下游整车制造与车企,筹备CTC应用落地。2020年3月2日,宁德时代与哪 吒汽车签约战略合作,双方将在新能源电池领域进一步深化合作;2021年5月,宁德 时代通过全资子公司宁波梅山保税港区问鼎投资有限公司入股爱驰汽车;2021年11月,宁德时代入股阿维塔科技(长安汽车子公司),持股比28.99%。
2.比亚迪:“刀片电池+车身”一体,E平台升级3.0进一步集成
刀片电池迅速全车型推进。从2020年1月正式推出刀片电池,短短一年多时间实 现搭载刀片电池的纯电车型和插电混动车型的量产上市,并宣布旗下纯电车型将全 面换装刀片电池。
2021年9月比亚迪正式推出E平台3.0。其将刀片电池作为结构件融入车身一体 化设计,包含全新电子电气架构下的四大域控制器和自主研发的车用操作系统。底 盘关键模块体积更小、重量更轻、性能更强、能耗更低。电驱动系统升级为8合1模 块,综合效率可超89%。搭载e平台3.0的电动车,零百加速可快至2.9s,综合续航里 程最大突破1000km。800V闪充技术,电动车充电5分钟,行驶150km。百公里电耗 比同级别车型降低10%,冬季续航里程至少提升10%。
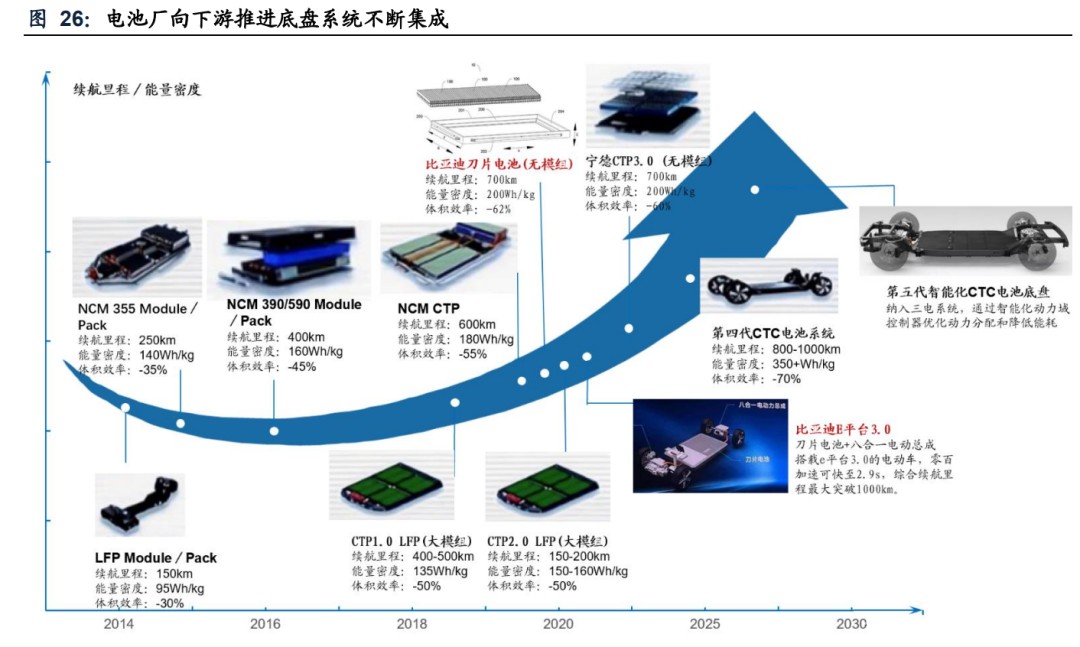
(二)主车厂紧随跟进
1.特斯拉
特斯拉在2020年9月的电池日活动上发布了4680电芯和CTC。公司又于2021年 6月在专利中详细阐述了4680 Structural Battery(CTC)电池系统集成技术,并于10 月在德国柏林工厂举办的参观活动中首次对外展示了4680 Structure Battery(CTC)。特斯拉的CTC方案将制造的电池组作为车身结构,连接前后车身底盘部件,新电池 系统平台仅由一个电池组和两个大型铸件组成。
2. 大众集团
大众集团已开始自建动力电池研发体系,并着手研发CTC。2021年3月15日, 集团举办了首届“Power Day(能量日)”,表示正在研发四种电芯,包括磷酸铁 锂电池、三元锂电池、高锰电池和固态电池。另外相较于现在的MEB平台化技术, 集团在下一代电池集成技术中将考虑CTP和CTC两个方向。预期在后MEB技术路线 上,大众很可能聚焦标准电芯+CTP/CTC。
3.沃尔沃
沃尔沃汽车集团正在加快电动化转型,并积极开发CTP和CTC技术,构建多元 化的电池供应体系。2021年6月30日,沃尔沃在Volvo Cars Tech Moment上透露了 诸多动力电池技术方面的信息,包括第二代PACK技术、下一代CTC方案以及自产 电芯等,并表示公司第三代电池系统集成技术的电池组将采用CTC方案和方形电芯。
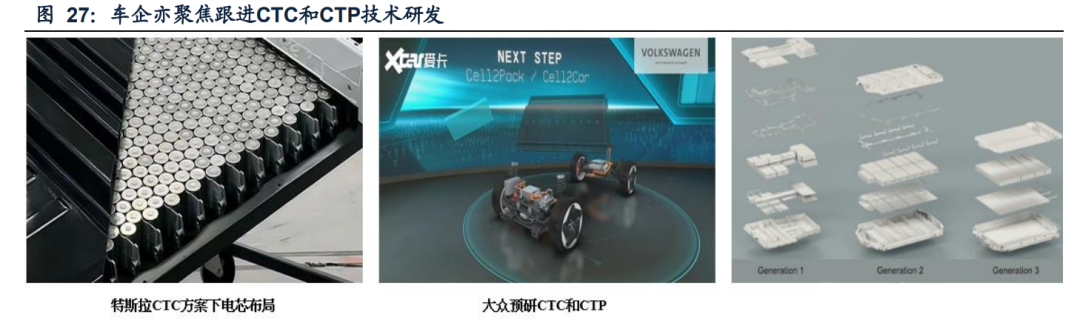
(三)电池企业重构产业壁垒与商业模式
1.集成化与结构革新,高效增强了电池厂在零部件供应链的话语权
电池包CTP化之后,整体的生产制造环节将产生大幅革新,主机厂将从原采购 电芯及模组,自行组装电池包的方式,转向更多的从电池厂整体采购电池包。
首先,当前CTP/CTC技术的革新电池厂整体发力与落地应用相较于主机厂起步 更早,宁德时代与比亚迪的CTP技术落地明显领先。同时基于宁德时代和长安汽车、 华为共同打造全新高端智能汽车品牌的合作关系,以及长安新能源规划突破CTV (Cell to Vehicle)、MTV(Module to Vehicle)关键技术,宁德时代CTC技术有望 加快产业化进度。
其次,以电池为核心,辅以相配应零部件的集成设计,电池厂更具有开发优势。虽然当前车企为把控主动权当前也在积极布局开发CTP→CTC电池包与集成底盘形 式,如特斯拉大众等(另外比亚迪、长城有电池供应体系)均提出要自研CTP/CTC 技术。但电池包的结构设计形态围绕电芯制造为中心,对于电芯性能的发挥和适配 应用,电池厂话语权更加优势。
再次,新势力造车市占率不断提升的市场主导趋势下,电池企业联合新势力 OEM通过技术革新率先应用落地的环境更为友好。2020年开始中国新能 源汽车经过调整升级。新势力凭借优质产品和服务,兼具科技创新与模式创新能力, 突破市场要求电动智能网联汽车在购置成本上与传统燃油车平价的束缚,通过不断 量变积累到质变,市场占有率不断提升。新势力车企在汽车机械制造方面或将对第三方更为友好。
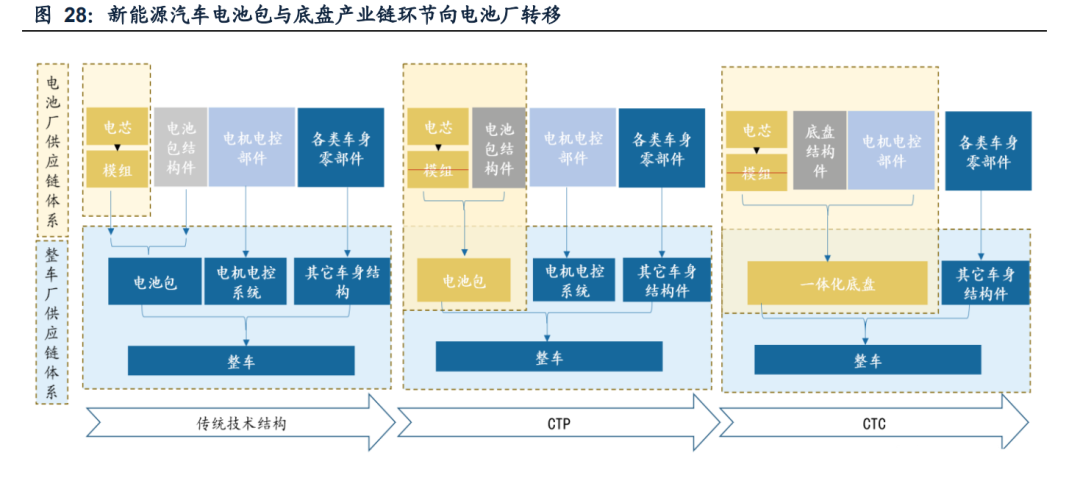
2.集成化与一体化加强了电池包生产环节的规模效应,提高长期盈利中枢
随着电池包的模块化,标准化程度不断加深。整个电池包的生产环节将实现较 大的集中度提升。因此电池厂相对主机厂将有望实现更强的规模效应,随着电池整 包的生产进一步从分散的主机厂开始转向较为集中的电池厂,电池环节长期盈利中枢有望提升。

关注结构创新下产业链变迁
在电池PACK结构简化的过程中,不同结构与材料的增加或减少使用以及传统结 构件在生产供应的格局上均发生较大变迁。CTP电池包一方面新增部分材料件(如导热胶和结构胶,以及绝缘件)的使用, 另一方面传统结构件的产业链结构开始发生迁移,客户结构从原来的以汽车企业为 主慢慢向电池企业渗透,不同环节供应格局也将发生较大变化。
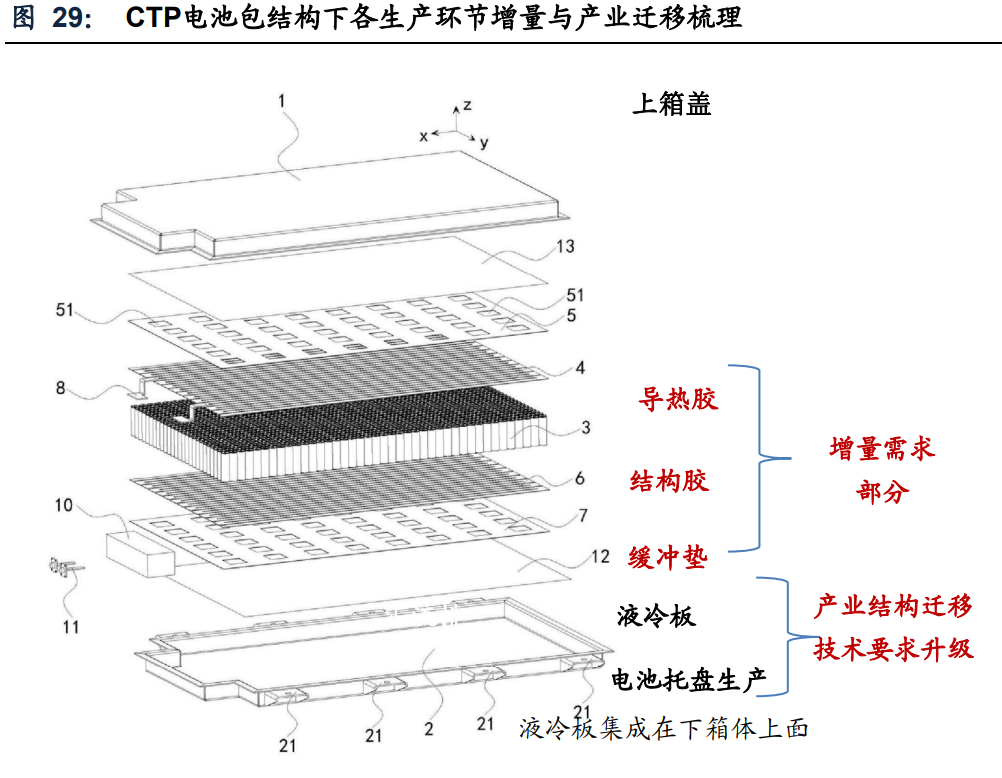
(一)结构件:电池托盘铝型材挤压为当前主流,压铸尝试渗透
1.冲压→挤压/压铸:当期挤压将代替冲压,远期压铸正在局部尝试
铝挤压工艺相比于传统的冲压等生产工艺,具有高刚性、抗震动、抗挤压、抗冲 击等性能,更能适应CTP结构化对电池托盘的新要求,其当前的主流工艺地位将进 一步巩固。冲压工艺由于自身缺点与CTP结构化的要求存在冲突,故预期在此环境 下将面临较大的应用限制。
另外,远期来看,一体化压铸电池托盘也在不断尝试:①铝型材的焊接工序很 长,效率很低,压铸快速成型,效率更高;②型材焊接的焊缝质量问题,一体化压铸 可较好的解决。③从生产成本的角度,无需投资多种铝型材的设备,仅需一台压铸 设备,整体工艺生产流程简化。
虽然此前一体化压铸由于产能与金属材料性能方面的限制,一体化压铸电池包 仍多用于混电车型的小能量电池包。但未来随着多种类合金材料的性能提升,大型 压铸机等的产能放量,纯电车型的大能量电池包也有望实现一体化压铸成型。多家企业已提早布局,如当前宁德时代等与广东鸿图等压铸厂探寻合作电池包相关的一 体化压铸,比亚迪也在逐步开始应用到一体化压铸成型工艺来做一些电池包结构件 等。
2.挤压的连接方式上:FDS替代FWS
FSW(摩擦搅拌焊技术)是以旋转的搅拌针以及轴肩与母材摩擦产生的热为热 源,通过搅拌针的旋转搅拌和轴肩的轴向力实现对母材的塑化流动来得到焊接接头。FSW焊接接头强度高、密封性好,被广泛应用于电池包箱体焊接领域,是当前电池 托盘的主流焊接方法。但FSW也存在因焊接变形导致的精度一般的问题,在CTP结 构化的环境下难以满足新的更高要求。
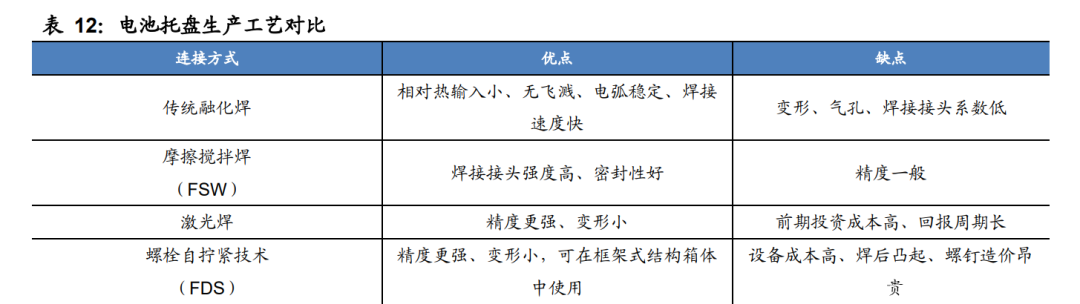
FDS(螺栓自拧紧技术)连接是一种通过设备中心拧紧轴将电动机的高速旋转 传导至待连接板料摩擦生热产生塑性形变后,自攻螺丝并螺栓连接的冷成形工艺, 通常配合机器人使用,自动化程度高。FDS技术精度更强、变形更小、气密性更好, 在保证足够连接强度的同时实现箱体良好的密封性能,预期在CTP结构化环境下未来将成为主流焊接技术。
综上:①生产工艺上,目前已成为主流的铝挤压电池托盘将继续拥有更强的主 导地位;连接方式上,对应的焊接技术将从FSW向FDS进行渗透。②未来远期一体 化压铸可期。
3.当前铝挤压主要市场参与者对比
当前电池托盘的型材挤压以及核心焊接技术仍在不断创新突破。凌云股份与敏 实集团一体化生产能力强,产能全球布局,主机厂客户积累较深。和胜股份切入电 池厂托盘供给、产能快速扩张。
(二)结构件材料:电池托盘探索镁铝合金应用
1.电池包结构件材料应用不断升级
CTP跳过模组环节,技术难度更大,对电池托盘提出了更高的要求——电芯由 于充放电膨胀造成的形变和散热性能变差两个问题需要在整个电池包层面进行解决, 因此CTP技术对电池托盘提出了更高的防震、气密性,以及轻量化等要求。使用材 料也在不断演变:钢制→铝合金→镁铝合金/塑料及碳纤维复合材料。
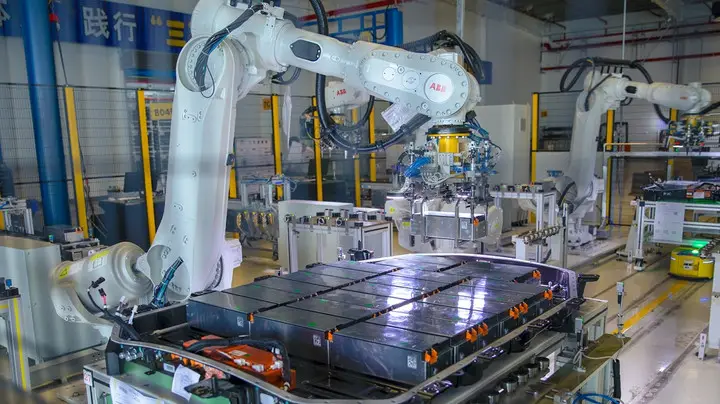
(1)早期:钢质材料
钢材料具有价格经济,有优良的加工及焊接性能,良好的抗石头冲击的能力(实 际路况中由于电池托盘受到不同工况的影响, 如易受到碎石的冲击等)等优点。但 重量较大,装载于车身时是影响新能源汽车的续航里程的重要因素之一。且其其刚 性较差,在发生碰撞过程中易发生挤压变形。早期电动汽车如 Nissan Leaf、Volt等 采用钢制电池箱体;不过当下传统钢制电池下箱体技术路线已经基本被抛弃。
(2)当前:铝合金为主,镁铝合金以及非金属复合等轻质材料也在不断开发
①当前电池包结构件多采用铝合金为主要材料。在诸多轻量化材料中,铝是最 早替代钢材成为车企欢迎的一种新型汽车制造材料。与汽车用钢铁材料相比,铝及 其合金具有强度高、耐蚀性优良、适合多种成型加工方法、较易再生利用、抗冲击性 能好等优点,因而成为应用上比较成熟的轻量化材料。当前主流的多采用:压铸型 与挤压-拼焊铝箱多用在电池包下箱体,冲压-拼焊铝箱用在电池包上箱盖。
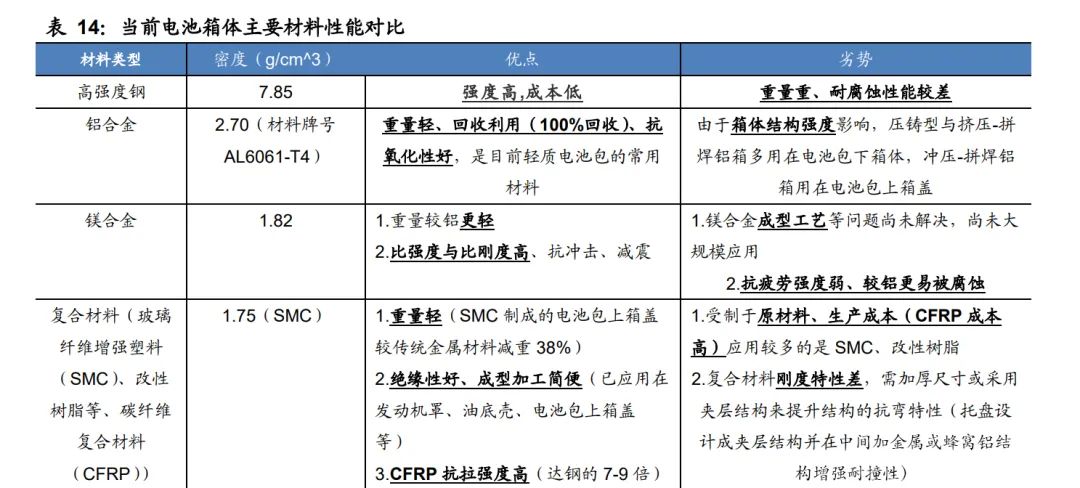
②性能更优的镁铝合金材料已在逐渐渗透至电池托盘的生产制造
镁铝合金重量轻契合电池包轻量化趋势:其密度为铝的三分之二,钢的四分之 一,原来电池壳体使用铝合金,重量达125公斤,采用镁合金制成同尺寸电池壳体仅 需60-70,减重效果达50%。
除轻量化以外,强度高、模铸生产率高也适用于电池包制造:镁有极好的吸震 性能、可吸收震动与噪音,对于用作设备机壳减少噪音传递、提高防冲击与防凹陷 十分有利,与铝相比,单位体积热含量更低,能在模具内更快凝固(生产率比铝压铸 高出40%-50%,最高可达2倍)
③其它非金属复合材料在托盘制造种的使用亦在不断探索,尚有待应用验证
塑料复合材料作为重要的轻量化材料,其比重轻、耐腐蚀,具有很强的设计性 和良好的工艺性能。碳纤维复合材料作为汽车部件,相比于传统铝合金、高强钢和 玻纤复合材料等材料,具有高强轻质、耐冲击性好、零部件一体化、可设计性好、耐 腐蚀性能好等优点,其减重效果和强度优势更加明显。不过当前,制约各种非金属 复合材料大范围应用的主要因素包括性价比、供应商的结构和能力、汽车发展和产 品环境等影响。同时生产和加工技术尚不够成熟,在新能源车的量产使用上仍有待 持续的发展验证。
现如今单一的材料已很难满足汽车刚度和强度方面的需求,除了克服单一材料 现有加工工艺上的技术难点,如何将多种轻量化材料的加工工艺形成技术融合,也是当前轻量化研究领域的热点和发展趋势。
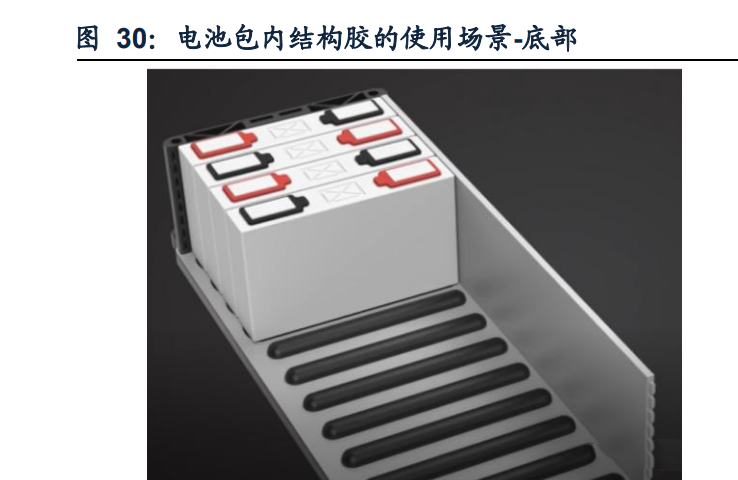
2.新材料企业切入电池包结构件的压铸生产制造
2020年11月,三祥新材与宁德时代、江苏万顺机电集团有限公司、广东文达镁 业科技股份有限公司,在宁德寿宁县共同设立宁德文达镁铝科技有限公司,开展“镁 铝合金压铸项目”。该项目引进一批压铸2500吨、5000吨压铸机进行电池托盘的一 体化生产压铸探索。
2022年2月,据三祥新材公告,该项目整套压铸单元成功试车生产,首个压铸件 电池端板下线。
(三)材料件:结构胶与导热胶应用增加
1.CTP结构下对用胶产生了新的需求:以结构胶和导热胶为主
CTP结构电池包设计省却或大幅省去中间模组部件,使用大量胶来连接固定电 芯。其中胶类的应用主要有两大需求点:第一类为结构胶,即以结构粘接为主,兼顾 一定的导热作用;第二类为导热胶,即以导热粘接为主,胶粘剂应用的目的是将电 芯工作时产生的热量导出到外部的散热部件,实现热管理的部分功能作用,兼顾结 构粘接要求。
结构胶是指应用于受力结构件胶接场合,能承受较大动负荷、静负荷并能长期 使用的胶粘剂。代替螺栓、铆钉或焊接等形式用来接合金属、塑料、玻璃、木材等的 结构部件,属于长时间经受大载荷、而性能仍可信赖的胶粘剂。
导热胶主要用于完成电芯与电芯之间,以及电芯与液冷管之间的热传导,胶的具体 使用形式包括垫片、灌封、填充等。
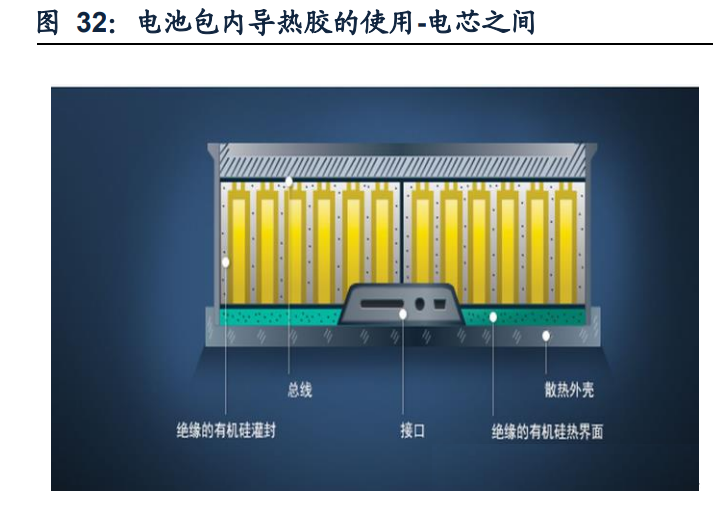
2.结构胶
结构胶需起到将电芯与pack壳体可靠连接、固定的作用,代替原来模组结构的 机械连接,对于强度、柔韧性、耐老化、阻燃绝缘和导热性都提出了较高的性能要 求。
动力电池包结构胶主要有聚氨酯结构胶、丙烯酸结构胶、硅胶、环氧结构胶、UV胶 和耐高温热熔胶,根据其不同的特点分别应用于不同的场景。
对于不同类型的结构胶,评价其粘接性能的具体指标有3点:接头的强度、破坏 形式(内聚破坏是最理想形式,达到接头处材料最大强度)和胶的断裂伸长率(反映胶体弹性)。目前我国主要的动力电池包结构胶 生产厂商中丙烯酸技术路线的有晶华新材和赛伍技术,采用聚氨酯路线的回天新材 则是在聚氨酯粘胶剂上有多年的技术储备。
3.导热胶
导热胶主要由树脂基体(环氧树脂、有机硅和聚氨酯等)和导热填料(提高导热 性,有氮化铝(AlN)、氮化硼(BN)以及氮化硅(Si3N4)、氧化铝(Al2O3)、氧化镁 (MgO)、氧化锌(ZnO)等)组成。电池包在CTP发展趋势下,电池厂商对导热胶 需求量大且有不断降本需求,同时减少结构件的设计也对用胶产生较高强度(大于 10Mpa)的粘接固定需求,因此在粘接强度、经济成本上占优的聚氨酯导热结构胶 成为主流导热用胶选择。
由于电池电芯的最佳工作温度带较窄(20-40℃),CTP结构下导热胶在电芯之间、电芯与液冷板之间实现均衡散热,从而使得电芯温度和电芯间的温差下降1-2℃ 将极大有利于电池热管理系统。
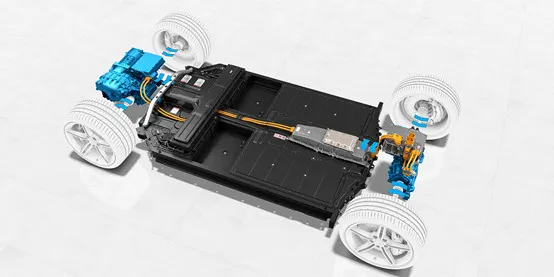
4.市场情况
随着CTP与刀片电池技术的应用,对胶粘剂要求和用量的提高,单个PACK包胶 黏剂用量会从目前的1-2公斤呈现较高倍数的增长,单pack价值量也会从200-300元 增长至400-900元。
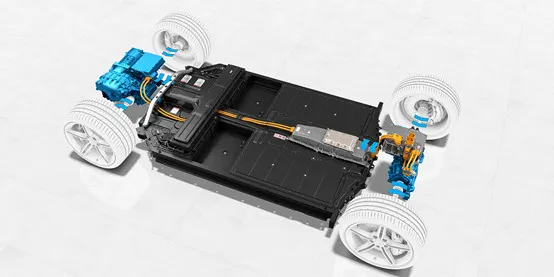
(四)材料件:新增缓冲垫其它绝缘件使用
1.CTP后对减震与保温的要求更高:新增缓冲垫片与保温贴片需求
单体电池模组可以提高散热的效率,减小热失控的风险。CTP去除了模组设计 的环节,因此一方面对保温和热扩散防护要求变得更高,另一方面需要用粘胶、缓 冲垫等材料实现电芯与电芯、电芯与托盘之间的固定与减震。所以相比于传统模组, CTP电池包对减震与保温的要求更高,主要表现形式为缓冲垫和保温贴片需求增加。
缓冲垫原本有蜂窝铝、PVC发泡、有机硅发泡、橡胶等多种材料。但橡胶需要 硫化不易控制温度;PVC低温环境下发硬且粘接不稳定;有机硅机械强度低,发泡 后粘接性比聚氨酯差。与之相比,聚氨酯树脂发泡材料能够在提供持续的反弹力同 时,起到防尘防水密封作用,避免因碰撞振动造成损坏,具有优异的防尘密封、减 震、抗压缩回弹、压缩永久变形、低温缓冲性等性能。以聚酯材料替代部分硅发泡 来用于缓冲,在CTP下具有更强的适用性。
保温贴片是贴在电池外部的零部件。聚氨酯泡沫塑料质量轻、导热系数低、耐 热性好,具有良好的保温性能,可用作保温贴片,包覆于电池包壳体实现保温。
2. 缓冲垫与保温贴片材料:聚氨酯在CTP结构下优势显现
聚氨酯(一般缩写为PU)是指主链中含有氨基甲酸酯特征单元的一类高分 子,可用于制作导热、粘接、减震、保温等材料件。聚氨酯制品主要包括泡沫塑 料、弹性体、纤维塑料、革鞋树脂、胶粘剂和密封胶等,其中泡沫塑料所占比重最 大。因其优异性能,聚氨酯制品广泛地应用于新能源汽车(CTP无模组、刀片电池 等)、密封件浇注件、电子元件、插头插座灌封,也可作为胶粘剂使用。
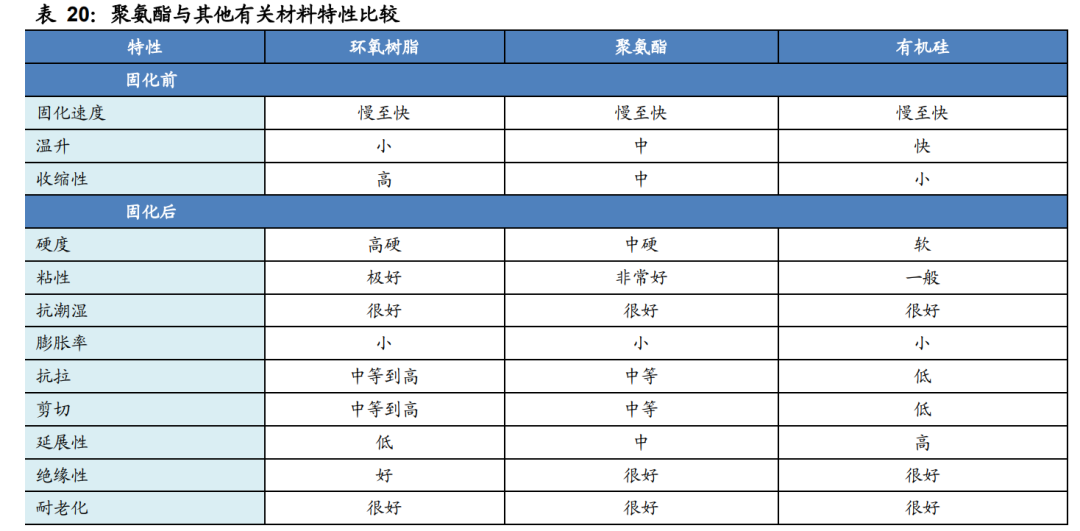
3.主要市场参与者:
(1)汇得科技:公司是聚氨酯材料细分龙头,主要产品为合成革用聚氨酯(PU 合成革)、聚 氨酯弹性体及原液、聚酯多元醇。动力电池包聚氨酯产品方面,目前量产的有电池 包液冷板缓冲垫、电池包保温贴片、更换电池用支撑缓冲块,正在研发泡沫包封胶 等新产品。公司现有产能合计为25万吨/年,年产18万吨聚氨酯树脂及其改性体项 目(二期)目前仍在建设。公司2020年9月起与宁德时代建立业务关系,目前正与 宁德时代商议缓冲垫和保温贴片供应方案,部分产品已完成测试,开始小批量生产 并试销;与中航锂电、蜂巢、比亚迪等电池厂商也在进行产品的送样或对接。
(2)祥源新材:公司主要产品为聚烯烃、聚氨酯等新型发泡材料,主要应用于建筑装饰材料、 消费电子产品、汽车内饰材料、家用电器产品、医疗器械产品等五大领域。公司目 前正积极配套开发新能源动力电池-电芯缓冲隔热、隔热垫、边框密封等系列产 品。在动力电池方面,公司产品在汽车动力电池和电动二轮与三轮的动力电池中均 有应用,占销售比例较小。
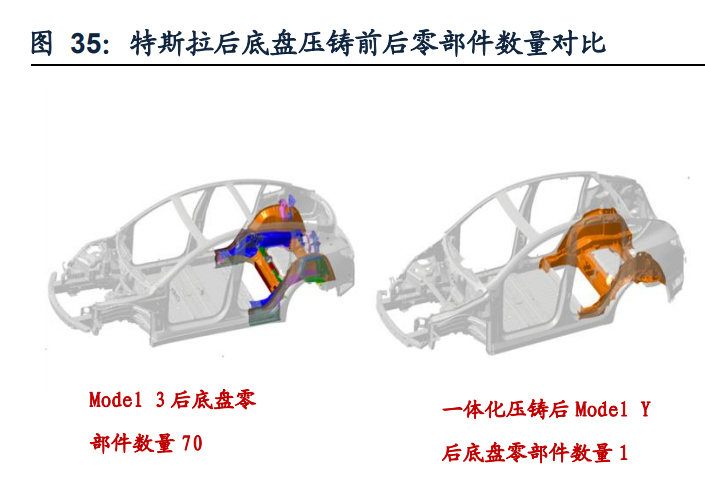
(五)CTC 后底盘开启一体化压铸新纪元
1.特斯拉引领汽车制造工艺创新极简,开启一体化压铸新纪元
2020年9月,特斯拉于电池日上宣布Model Y将采用一体化压铸后地板总成,可 减少下车体总成重量30%,降低40%制造成本,且车身生产工艺流程大幅简化,制 造时间由传统冲压-焊装-涂装-总装制造工艺的1-2小时缩短至一体化压铸的2-3分钟。
2021年5月,特斯拉前舱一体化总成铸件试验也已披露下线,主要构成包括左右 车轮罩、溃缩吸能区、横梁、以及与车身连接的端面和与前碰撞梁或车前端连接的 结构端面,整体重量约为130kg。
当前,特斯拉正在探索一体化压铸的进一步集成,将整个车辆的结构构成大大 简化为四个部分:①前舱一体式压铸总成+②乘员舱结构压铸总成+③一体化电池结 构压铸总成+④后底板一体化压铸总成。其中,据特斯拉发布会介绍,其利用3个大型压铸件(前底板+CTC电池包+后底 板)替换由370个零件组成的整个下车体总成,实现整体减重10%,续航增加14%。
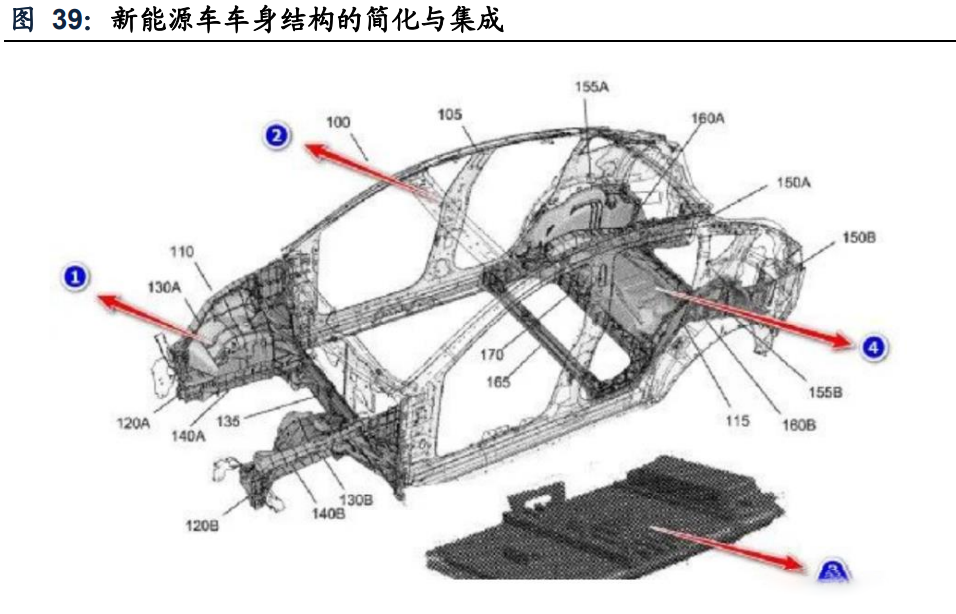
2. 一体化压铸是汽车制造提升集成效率,以及轻量化与降成本必经之路
(1)一体化压铸相对传统工艺,极大的提升了汽车车身的生产效率
传统车身的制造工艺包括冲压-焊装-涂装-总装等多个流程。主车厂采购由全国 各供应商通过冲压、压铸制造的多个结构件,将之组装连接(包括焊接、铆接、涂胶 等)在一起,形成汽车的白车身总成(BIW)。一辆车由大约几百个不同形状、不同 材料的零件焊接而成。任一零件的误差波动都将对最终的车身精度造成影响。
一体化总成零部件一次压铸成型,极大提升了汽车生产效率与集成质量。据特 斯拉数据显示采用了一体式压铸后地板总成的Model Y,由于所有零件一次压铸成型, 零件数量比Model3减少79个,由于应用了新的免热处理合金材料,因此省去了热处 理环节,制造时间由传统工艺的1-2小时缩减至 120-180s。且只有一个零件,无需 开发过多的工装设备,也大幅降低大量零件连接带来的误差累计,提升制造精度。
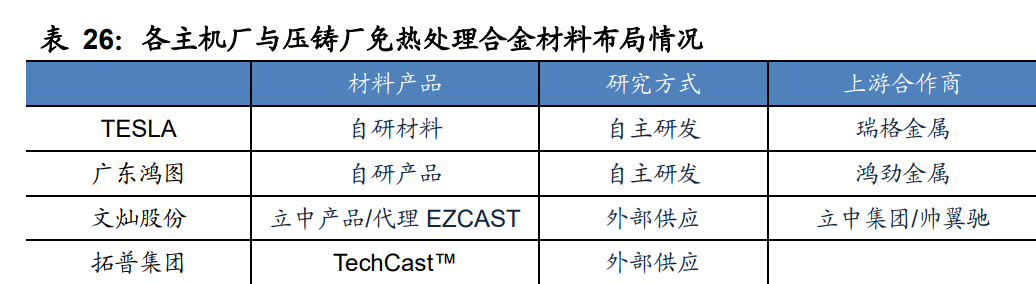
(2)一体化压铸有效实现了汽车轻量化需求
据中国汽车工程学会给出的国内汽车轻量化分阶段目标来看,国内汽车制造轻 量化趋势也在不断加速推进。采用铝合金一体化压铸的全铝白车身重量约在200- 250kg,而同级别钢制车身的重量在350-450kg。重量降低约 150-200kg,采用全铝 一体化压铸工艺极大的提升了汽车的轻量化程度。
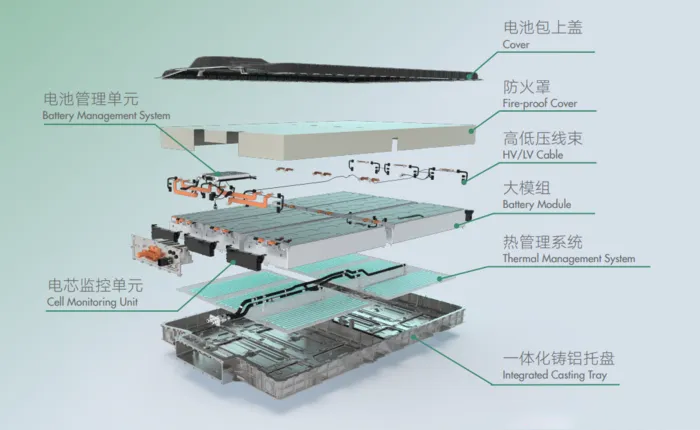
(3)一体化压铸大幅简化生产成本
一方面,大幅降低了生产线成本。在原有的有生产技术成本(冲压、焊装、涂 装、总装)框架下,传统生产70个零部件,每个零部件均需布置机器和模具,以及 生产线周边的机器臂、传输线、夹具等;而一体化压铸成型仅需一台大型压铸机和 一套模具,工艺流程简化过后其它耗材和设备的减少、机加工简化、物料运输、压铸 成本都更小;且省去了热处理设备和过程、省去了塑型设备[修复热处理后的变形]和 过程、省去了钝化设备和过程、省去了结构胶等,综合经济性能更好。另外,一台大 型压铸机占地面积仅100平方米,根据埃隆-马斯克的表示,采用大型压铸机后,工 厂占地面积减少了30%。
另一方面,大幅降低人力成本。国内主流汽车工厂一个焊装工厂大概配套200- 300名生产线工人,采用一体压铸技术后,所需的技术工人也将大幅减少。据特斯拉 在2020年电池日发布会上表示,modelY后底板一体化压铸工艺较原方案降低了40% 制造成本。
3.主车厂与电池厂均跟进,加速布局新能源车底盘一体化压铸项目,行业景气高增
(1)各新能源车厂加速跟进推进一体化压铸:
①沃尔沃布局一体化压铸
2022年2月28日,沃尔沃汽车将投资100亿瑞典克朗给位于瑞典的¬¬Torslanda 制造工厂,以准备生产的下一代全电动汽车。公司将采用大型铸造铝车身部件,新 建电池组装厂和总装车间。其中关键一项是使用 8000T 锁模力的巨型压铸机生产 汽车后底板,这意味着沃尔沃开始在大型汽车零部件中引入压铸工艺。同时,沃尔沃汽车公司和领先的电池公司诺斯沃特也宣布,将投资300亿瑞典克朗,用于开发和制造用于沃尔沃下一代纯电动车型的高品质定制电池。新建 的电池组装厂将导入方壳 CTC 的工艺,为下一代更长续航里程、更快充电速度 和更低成本的纯电车型作准备。传统车企开始布局一体化压铸工艺,也意味着一体化压铸应用推广的进一步加快。
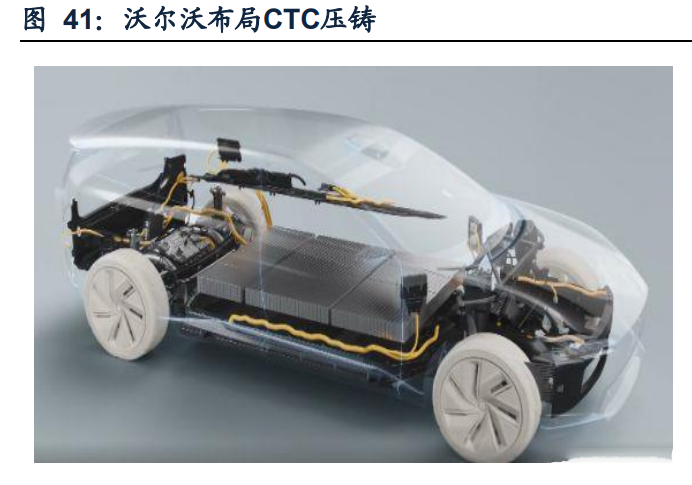
②新势力造车企业携手第三方,开始布局一体化车身压铸
除特斯拉外,新势力造车企业如蔚来、小鹏等也开始布局汽车的一体化压铸后 底板。2021年12月蔚来发布新车 ET5,该车后座板使用一体压铸工艺。小鹏武汉工 厂除了规划了常规的冲压、焊接、涂装车间,还加入了一体化压铸工艺车间,将引进 一套以上超大型压铸岛及自动化生产线。
(2)电池厂商宁德时代深度布局电池包结构压铸
2021年8月,宁德时代与上海临港签订合作协议,拟投资28亿元建设一体化电动 底盘项目。2022年2月19日基地正式开工。项目涉及布局包括先进材料、系统结构、 极限制造和商业模式创新在内的“四大创新体系”。与三祥新材股份有限公司(“三祥新材”)、江苏万顺机电集团有限公司、广东 文达镁业科技股份有限公司,在宁德寿宁县共同投资了“镁铝合金压铸项目”。
该项 目引进一批2500T、5000T吨的压铸设备,用于电池包内部结构件的压铸。随着CTC电池包的高度集成化,底盘结构件、电机电控部件等进行一体化压铸 也将成为可能。传统汽车铝合金压铸厂商以及电池包、电驱动壳体的压铸厂商都将 有机会和动力往价值量更大的一体化压铸CTC电池包以及全车身方向延申。
4.压铸厂商亦高度受益行业景气高增,单车价值量大幅提升,市场空间广阔
除车厂采购压铸机自研一体化压铸后底盘外,车身结构件的压铸厂商以及电池 包和电驱动壳体的压铸厂商同样进行着一体化压铸业务的布局。在当前新能源车销 量高增以及大型压铸件使用不断扩张背景下,零部件厂商高度受益压铸件需求放量。
当前新能源车单件一体化压铸后底板重量约为50-60kg,以50~60元/kg的产品 定价模式预计,一体化压铸后底板单车价值量约为3000元。若将一体化铸件拓展至 CTC电池包(80-90kg)、前舱总成(130kg),合计重量270kg,单车价值量将有望 达到1.2~1.5万元。
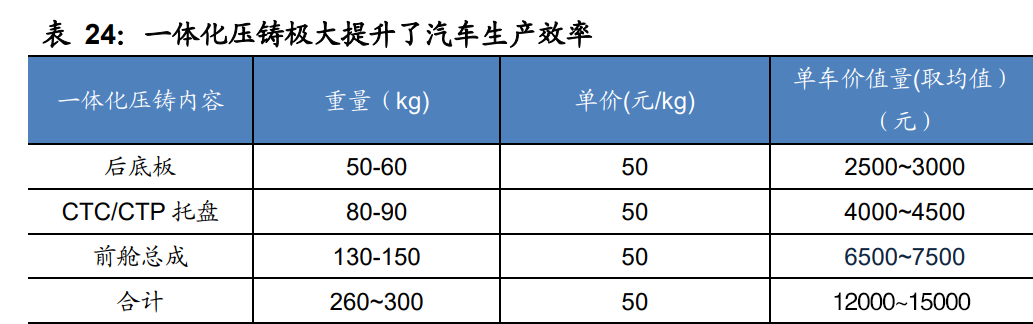
5.一体化压铸对设备-模具-工艺配套流程要求更高,技术壁垒明显,竞争格局更优
(1)一体化压铸“设备-模具-材料-工艺”集成综合壁垒高
在设备端,大型一体化成型件需要采用高吨位压铸机,当前国内外各压铸机设 备厂商开始实现大型压铸机研制突破。为了满足大尺寸部件的制造要求,且同时保 证其强度和量产效率,一体化压铸对压铸机的锁模力、模板尺寸、压射量、压射压力 以及速度控制等均需要更高的要求,具有较高的技术难度。2019年力劲集团成功突 破6,000吨合模力的大型压铸单元,并与意大利子公司意德拉共同为特斯拉的全球工 厂供货。根据意德拉官网产品介绍,6,200吨大型压铸机设备长19.5米,自重430吨, 相比于其他大型压铸机产品,在合模力、压射力、模板尺寸、射料量上均有明显突 破。近两年国内压铸设备厂商海天集团、伊之密等也相继研发出高吨位大型压铸机。各主车厂及第三方压铸厂纷纷采购超大吨位压铸机来实现业务拓展布局。
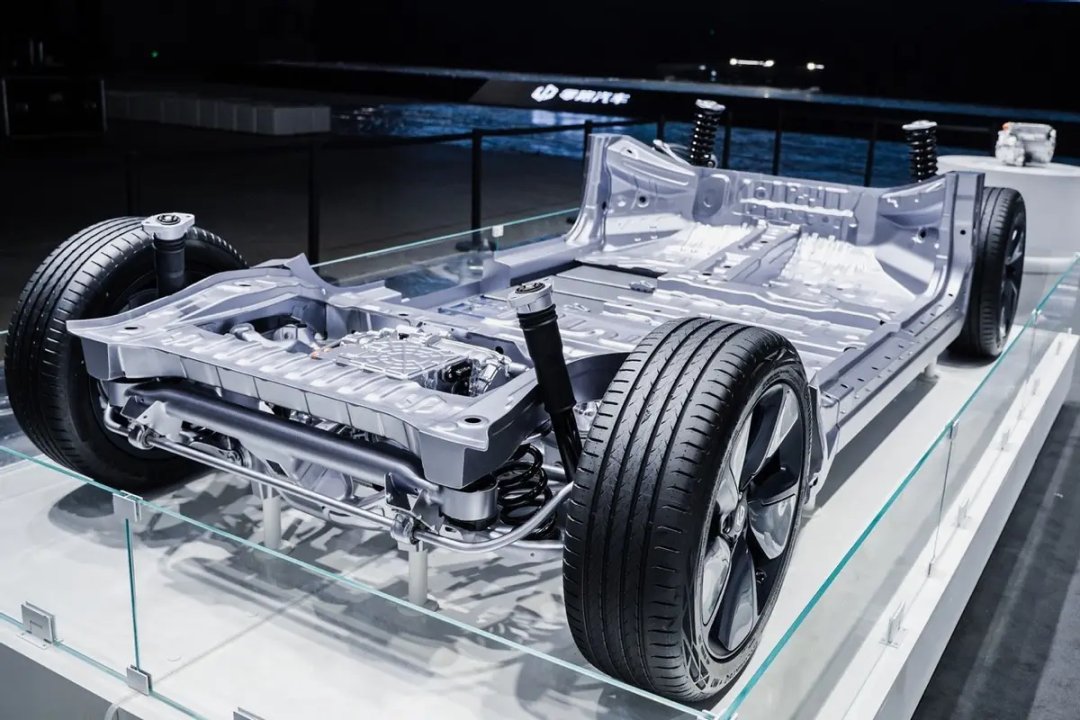
在模具端,大型压铸产品结构复杂,对模具的要求亦进一步增加。在材料端,免热处理合金材料的研制突破助力大型一体化压铸的适用推广。传 统压铸工艺中,需要使用到热处理等工序来提高零部件的机械性能、耐腐蚀性能等。但加热冷却过程中产生的热胀冷缩效应,带来零部件的形变误差,特别是对于一体 化的大体积部件,进一步放大了变形风险。当前,特斯拉,美国镁铝,帅翼驰集团, 华人运通,广东鸿图,立中集团等均在开发以及使用免热处理铝合金材料,使得大 型一体化压铸更加可靠。
在压铸工艺端,将设备-模具-材料大要素有机地加以综合运用在当前仍具备较高 的技术壁垒,其关键点在于能稳定的、有节奏的和高效的生产出外观、内在质量好、 尺寸符合要求的合格铸件。目前国内已试件一体化压铸成功的压铸企业有:广东鸿 图、文灿股份、拓普集团。
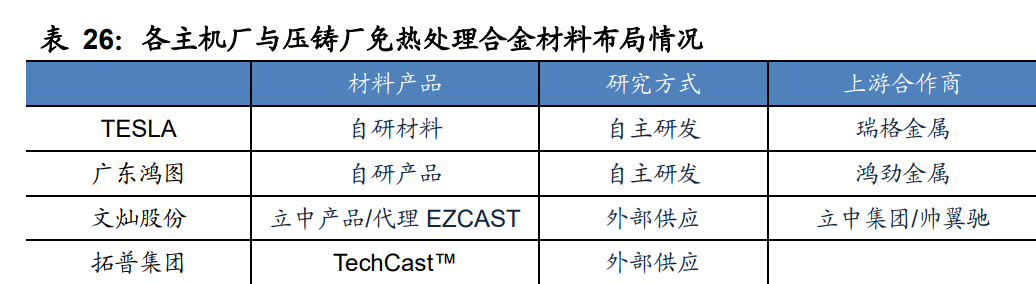
(2)第三方压铸厂凭借压铸工艺优势以及生产规模效应等实现跑马圈地
当前各家零部件压铸厂商均开始进行一体化汽车底盘研制工作,其在压铸方面 的工艺优势以及工厂线规模效应及成本控制方面优势将有望助力其在一体化压铸市场中占据一席之地。
编辑推荐
最新资讯
-
飞书项目落地ASPICE解决方案,助力汽车软件
2025-04-24 09:59
-
驾驶员监控系统DMS合规认证的“中西结合”
2025-04-24 08:23
-
自动驾驶汽车测试关键行人场景生成
2025-04-23 17:12
-
R171.01对DCAS的要求⑧
2025-04-23 17:08
-
迄今为止最先进的版本:imc发布全新imc STU
2025-04-23 17:06