汽车ECU虚拟标定浅谈及展望
背 景 介 绍 ✦
Background
近几年来,随着产业升级及技术革新,汽车行业的产品升级换代变得越来越频繁。留给车型开发的周期已经越来越短,无论是设计仿真还是试验、测试以及标定工作,每一个主机厂都在尽力压缩开发的每一个环节从而确保新车型尽早地投入到市场。
作为汽车行业客户长久以来的合作伙伴,SISW的工程服务即ES团队也一直在探索新的技术方案,如何给客户带来新技术新方法从而提高产品开发的效率、缩短研发周期和降低开发成本。
通过和客户的项目合作以及对行业的理解,目前汽车行业OEM客户的一大需求就是如何通过“虚拟标定”来提升车型开发流程的效率、质量,最终提升市场竞争力。毕竟无论是元部件或整车的标定工作,在哪个客户的研发流程中都是要调用大量人力物力去完成,并且通常标定工作都是车型开发的收尾阶段,马上要面临车型上市的时间节点要求,压缩的标定周期也会对标定工作的交付有一定影响。
随着“数字化双胞胎”的理念越来越被广泛的接受,各行各业的客户都在探索数字化的工业实践,希望通过数字化或者虚拟技术来更好地服务于产品研发流程。依靠积累大量的CAD及CAE技术的应用和经验,那么孕育出虚拟标定的需求就是最自然不过的事情了。尤其是在CAE领域的长期积累,让工程师们敢于畅想通过虚拟的模型去做更多的开发支持工作;同时对于标定工程师来说如果有更多更有效的手段来协助或支撑他们繁重的标定工作,那自然可以缓解车型上市前的标定工作压力了:比如可以将一部分标定工作前移,而不必非要等到最后的道路标定;亦或是采用脚本的自动化标定或优化方法来缩短标定周期提高标定质量。
目前来讲,“虚拟标定”的工程方法还处在探索和尝试阶段,还并没有大规模地应用到日常的开发工作中。因此本文的内容也是基于有限的项目经验和虚拟标定可能的落地方案来展开论述,欢迎大家提供反馈意见多多交流。
软件定义汽车
众所周知,近些年随着汽车的电动化,智能化的高速发展,车辆的软硬件系统已经越来越复杂。“三电系统”的引入,直接给整车研发的难度提升了可能不止一个等级,从整车布置到电气系统选型、设计和验证,以及最终的标定,每个环节都有不少的仿真计算、验证和试验工作要完成。而让新加入的硬件统一协调运转,完成车辆对驾驶员操作的及时准确地动作响应,再同时兼顾能耗、续航里程等硬指标,难度可想而知。底层硬件的设计决定了车辆能有多大的潜力,但车辆性能能发挥多出色就主要取决于在软件层面上下的功夫了。
我们知道过去传统车的配置在二三十年前含有的电控系统很少,发动机还配置的是化油器,变速箱也是手动档,甚至当时有的车还没有防抱死;真碰到需要紧急制动的情况,只能寄希望于老司机的“脚动防抱死”操作。现如今发动机变速箱底盘等总成已经配备了很成熟的电控系统,几乎榨尽了硬件的性能;而且无论是车辆的基本性能还是更高阶的安全性、舒适性、便捷性还是娱乐性都比之前有了质的飞跃。
此外,新能源车的普及也对软件开发提出了新的挑战:电机MCU和电池BMS这两大控制系统的策略开发就有一套完整的流程,然后还需要在集成到整车后进行调整,最后再统一由VCU进行调度和控制。尤其是对于混动车型,相当于两套动力总成需要按驾驶需求来切换不同模式,对于开发工作着实是一种新的挑战。
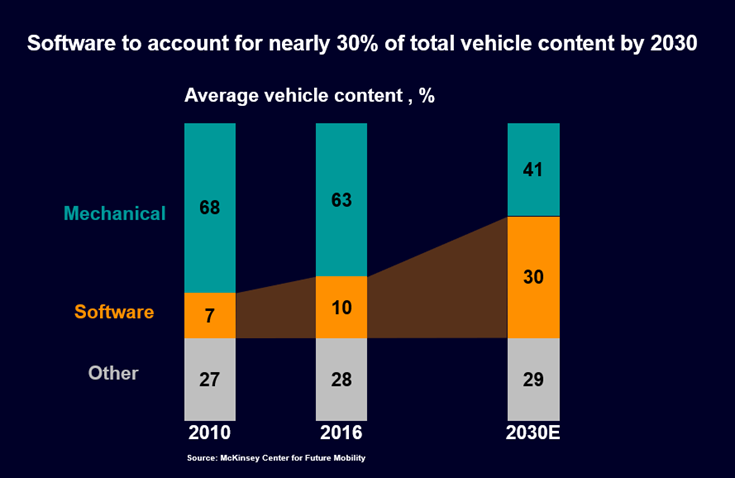
图表1 – 软件在占整车系统的比重(McKinsey)
另外,随着市场和消费者对于自动驾驶的渴望,ADAS系统的功能优劣甚至影响到品牌竞争力。而ADAS系统的开发由于要考虑和测试的工况可以说是不计其数,光是一个控制模块比如AEB或者LKA就需要大量的测试和验证。
因此,行业里现在流行的“软件定义汽车”的说法也从某种程度上反应了大家对软件的重视程度已经远超以前。从图表 1的柱状图中可以看出McKinsey对于未来整车中软件所占比重的预测,在2030年可以达到三成;而机械部分或者说传统的硬件部分从2010年的占绝对优势,到2030年的时候可能下降到只占四成了。
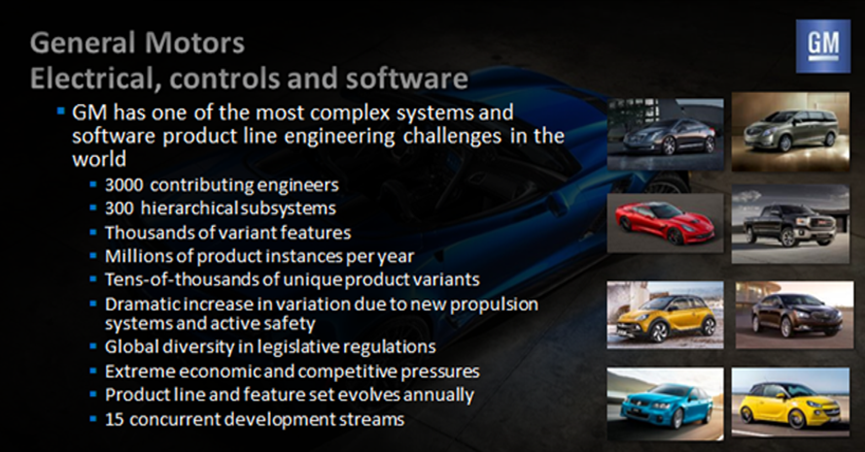
图表 2 – 电控及软件系统复杂程度– 通用汽车
作为OEM,从原来主要专注于机械相关的整车设计及制造,到现在必须要大力投入到整车电动化及软件开发的领域。许多主机厂也早已经开始了自己的布局,比如像图表 2中展示的美国通用汽车公司中和“整车电气/控制/软件”业务领域相关的数字。无论是涉及到的工程师人数,产品线数量(比如新能源车型和主动安全引入后带来大量新的衍生车型)可能远超我们的想像;而且全球不同区域不同法规下产品多样化的要求,以及市场化的竞争压力下,每年并行开发的车型数量,原型产品数量目前似乎已经到了上限,那么企业要么就继续扩大人员、设备、工具等资源的投入来应对这种挑战,要么就要从开发流程的质量和效率入手,寻找新的技术或新的工程解决方案。
虚拟标定技术路线探讨
当然,能够提升开发流程效率或者缩短周期的方法有很多,尤其对于整车相关的软件和策略的开发每个主机厂都有自己独特的流程,在本文中我们只针对软件的标定工作如何拓展为“虚拟标定”来展开。而且这里只从通用的方法或技术路线方案上做一些探讨,不涉及具体的技术实施内容。
一般来说进行传统的标定工作需要等到ECU软硬件到位后,在零部件台架或者整车路试的阶段才能进行。但因为软件版本硬件设计等已经基本定型,所以但凡需要更改任何参数或设计,那么涉及到的时间周期、成本投入,包括重新进行计算仿真,调试调教甚至试验验证等工作在车型开发的收尾阶段都是不小的投入,而且还要同时面对车型上市的时间压力。
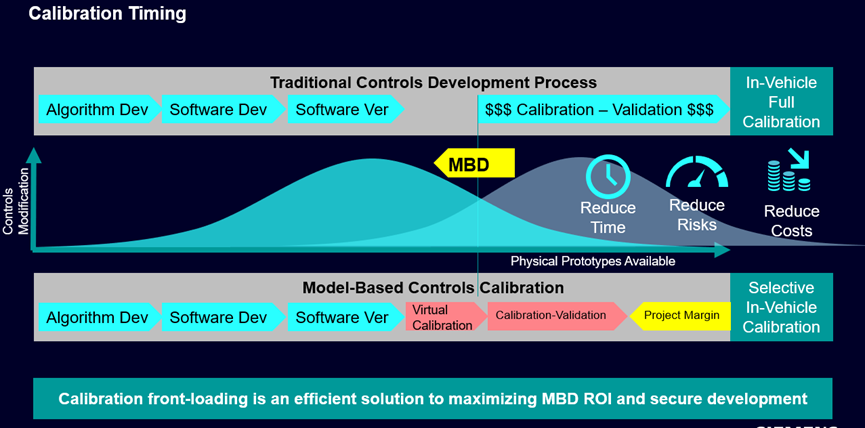
图表 3 – 基于模型的虚拟标定
但是随着虚拟仿真及数字模型的开发工作在主机厂里越来越广泛地得到应用;而且不只是广度,在任何一个专业科室或领域,应用的深度也是不断得到突破。这种切实的“数字孪生”落地,不仅本身丰富了系统和产品的开发手段,提高了开发流程的效率并保证了输出物的质量,而且更重要的一点是让工程师们更加敢于畅想如何将这种虚拟的和数字化的方法用到其它环节的开发工作上。其实结合虚拟仿真已经有成熟的应用了,现在无非是更近一步地探究。或者前面这段说人话就是:系统仿真模型已经成熟地用在了MiL/HiL等环境来验证控制策略;那么我们能不能更进一步地让系统仿真模型来支持虚拟标定工作,从而获得“缩短标定周期,提前开展标定工作,减少后期设计或参数更改”的收益。
也就是说在传统的标定工作流程中,我们提前在软件策略开发好后,就利用系统仿真模型来和策略模型/代码进行闭环,争取开展一部分标定工作,或是为了后续的台架及整车标定提供参考,或是暴露一些技术问题,或是替代一部分基本的标定工作,从而将工作量前移,为后续标定省出宝贵的时间。如图表 3所示,在软件开发/版本确定后,引入基于模型(MBD)的虚拟标定环节,既可以提前着手开始标定,又可以节约后续开发工作的成本,给车型项目留出更多的裕度。
如果我们将标定工作的完整流程和想要实施的虚拟标定融合或衔接,其可能的流程会如图表 4所示。其实这种流程也无非是在“XX在环”的基础上一个直接的拓展,如果主机厂已经有了HiL平台,或者MiL和HiL兼备;亦或是MiL/SiL/HiL的环境都具备,那在现有平台上拓展新功能新用法即可以节省投入,又可以提升效率扩展用途。

图表 4 – 虚拟标定的流程之一
既然是从现有的MiL/SiL/HiL的方案上衍生出来的新用法,那“虚拟标定”的内容也要按照模型在环到硬件在环的步骤来规划。如果从被控对象模型开发的角度来看,在进行任何“XX在环”的测试之前,都要先确定开环模型的结果(图表 4中最左侧的第一步工作)。说白了就是对物理系统进行建模和验证,确保模型仿真结果的准确性或可信度。这一步虽然也被称作了“Analytical calibration”(暂且翻译为分析性/解析性标定),但毕竟这个环节还没有引入控制的影响,是纯物理系统的性能验证,比如图示中列举的发动机扭矩特性,换档曲线等特性参数。
接下来当控制开发团队已经完成了策略模型,或者模型和代码都已经具备,那么就可以利用已经成熟的MiL或SiL环境来开展部分虚拟标定工作。因为被控对象模型中包含了一定量的物理细节,所以理论上和这些物理细节相关的系统动态响应过程中涉及到的控制参数都可以进行初步的调教。比如一些执行机构的阈值大小,变量的饱和上下限设定,触发标志位的条件设定等,只要模型中包含了的内容,都可以里用MiL或SiL的虚拟环境来进行初步标定。当然,整车标定参数的种类及数量成百上千,在这个环节可以做哪些参数的虚拟标定或者预标定,能做到什么程度,后续环节是否还需要重复验证等问题,目前看就只能根据在开发车型的特点、主机厂开发流程的成熟度和工具链等具体情况来分析并提前规划了。
当控制器ECU的软硬件都已具备,那么能够通过虚拟标定来提前检验比如控制器的I/O接口相关的参数,诊断相关的阈值参数设定等。因为在这个环节已经引入了控制器硬件,所以测试和标定的重点也需要围绕和控制器硬件相关的参数。理论上来说,这个环节应该不再去标定和车辆稳态或动态性能相关的物理系统参数了,毕竟HiL平台有实时条件的限制,模型的计算精确度有可能满足不了特定标定参数的要求。
最后,原型车已有并可以进行试验了,此时是传统标定工作的起点。但借助于虚拟标定我们在这之前已经积累的不少标定结果,所以我们可以利用整车的一些测试和试验结果来做进一步的虚拟标定,或者说对于一些关键参数,之前在MiL或HiL环节已经进行过初步标定的,可以在这个阶段进行复核。
除此之外,由于某些参数可能无法通过建模手段来(准确)模拟,那么这类参数就需要在规划虚拟标定的工作时,划归到最终有整车可进行测试和试验后去进行标定:比如像之前提到的发动机扭矩特性或换档曲线这种参数也和驾驶员主观踏板感觉相关;或者一些极端工况比如极低温下模型无法准确模拟的工况,都留到最后的整车道路标定环节上去实施,就没必要在之前的环节浪费时间做任何初步的标定工作。
虚拟模拟的开发助力虚拟标定
既然我们讨论的是“虚拟”标定,那么其核心其实应该是虚拟模型,而并不是标定。将系统仿真模型引入到标定工作中,并不会改变标定工作的本质,而是提供了额外的技术手段来使标定工作更加高效且稳妥。
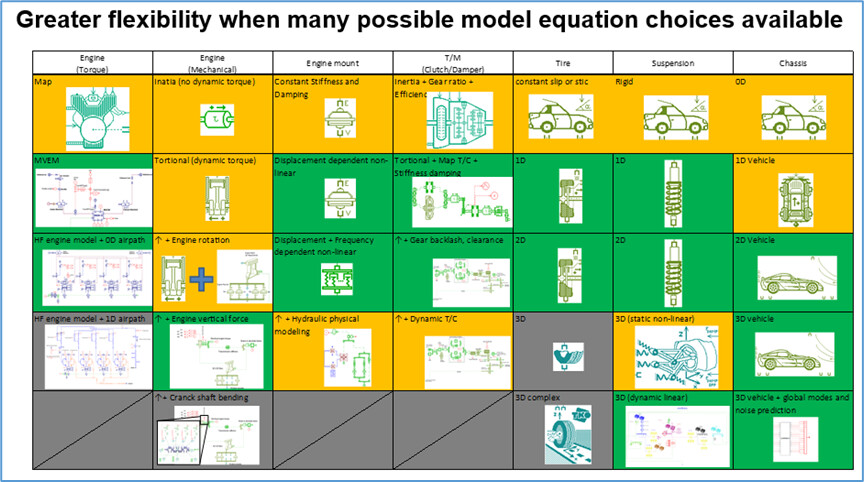
图表 5 – 模型的层级划分示意图
面对纷繁复杂的众多标定参数,是不可能用一个庞大且详细的模型就能满足虚拟标定的要求的;现在实现不了,未来短期内也不可能。所以势必要从模型的详细程度出发,根据想要标定的参数内容来将模型进行分类分级的开发,这样才能在准确的、恰当的模型支持下去进行参数标定。如图表 5所示,一个简单的整车动力模型,如果按照发动机、变速箱、悬置、整车负载和车轮轮胎等几个子系统按横向展开后,再按照详细程度纵向拓展,那么就可以形成一种矩阵式的模型库结构。
对于不同的标定参数项,我们需要事先规划每个子系统需要的模型详细程度。比如,如果标定怠速相关的参数时,发动机模型我们可能需要细化到考虑缸内燃烧,计算出高频的缸压曲线及扭矩波动曲线;并且加入悬置模型,来适应需要标定的参数;而变速箱及整车负载我们可能只需要考虑成简单的速比和一维动力学模型即可。但当我们需要标定的参数比如说是变速箱的选换档执行机构中的电磁阀特性时,那么像发动机的部分我们很可能就是简单的转速输入信号施加到变速箱输入轴即可,而变速箱部分我们就需要扩展到详细的液压加机械的模型才可以。
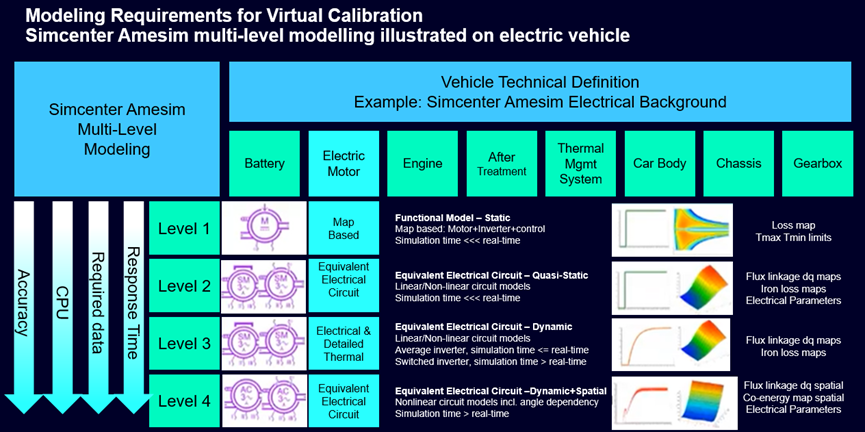
图表 6 – 不同层级的电机模型
对于新能源车型我们也需要对最关键的电机和动力电池的模型进行提前规划,如图表 6和图表 7所示,电机的模型最简单的层级只需要“最大最小扭矩特性”和“损失/效率特性”曲线就可以描述扭矩转速及功率的变化,但对于电机MCU相关的虚拟标定要求,能提供的细节就太少了。对于电机的等效电路模型来说,其电气特性相关的参数以及产热传热相关的参数引入后,那么此时模型能够表征的物理现象就可以关联到MCU中的标定参数。比如不同的励磁电流下,转子的响应快慢以及扭矩输出的曲线可以通过相应的标定项来进行调整;同时,由于热模型计算出的生热及传热过程,可以获得电机本体或壳体的温度,再结合外部冷却系统模型,可以对电机冷却回路中的水泵转速或者控制阀的相关参数进行初步标定。
动力电池的模型层级简单来说也和电机的模型类似,包含电气特性和热学特性;而对于更细致的需求,比如考虑电化学反应或者老化的仿真,也有对应的子模型可供选择。通常来讲主机厂客户一般不会关注电池内部的电化学反应或者特性,这是电池供应商需要做的设计仿真工作,所以电池的物理模型一般做到整包或者详细到模组的层级就可以满足虚拟标定的基本要求了。如果希望尽量多的将BMS的虚拟标定工作前移,那么电池包的物理模型则需要考虑到电芯级别的模型;因为BMS中的一些策略模块(比如cell balancing)是专门针对电芯来进行调整的。
综上所述,对于不同的控制器和不同的标定参数项,其被控对象的模型复杂度需要根据标定目的去提前规划好,而且如果同时要对多个控制器进行虚拟标定,那么势必需要不同详细程度的子模型以及集成的系统模型来准确复现实际物理过程,而且每一个模型并不是越详细越好,毕竟受限于硬件资源和CPU的速度,怎么合理组合子系统模型也是需要实际工程项目去探索和总结的。

图表 7 – 不同层级的动力电池模型
除此之外,还有更重要的一点是虚拟模型的精度水平以及模型的可预测性。这直接决定了虚拟标定的最终受益效果,也直接决定了虚拟标定和实车标定的工作划分。我们在统筹虚拟标定的工作内容时,需要综合考虑控制器的数量,信号接口数量,每个控制器是否需要不仅标定应用层策略相关的参数,也需要对诊断和通讯进行标定;被控对象系统的物理模型可以做到哪种详细程度,是否有经验数据或试验数据可以作为模型验证的依据;在模型验证好后,怎么评估模型的预测性以及变参数后的结果可信度,这也是虚拟标定如何划分工作步骤和内容的依据。
引入优化手段助力虚拟标定
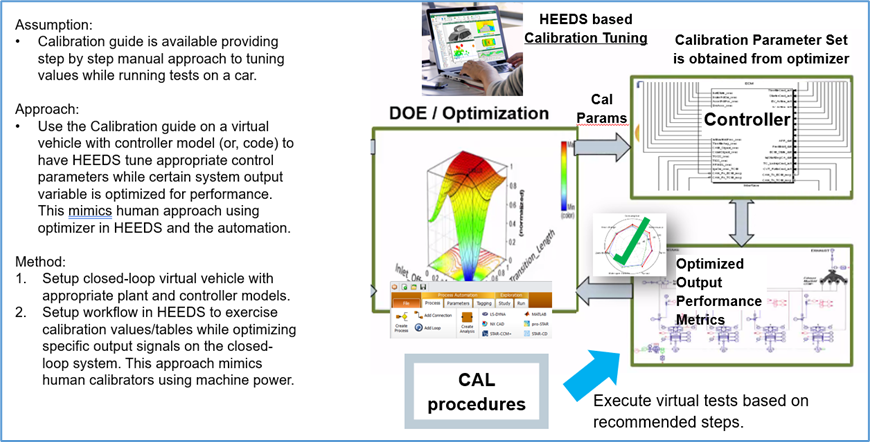
图表 8 – 依托优化工具辅助虚拟标定
借助优化工具在虚拟模型的平台上去寻找最佳的参数设定,从而让系统的特定目标最优;所以在虚拟标定中引入优化手段就顺理成章了。毕竟在实际标定工作中,标定工程师们清楚地知道自己可以调教哪些参数,更加知道自己想要最终达到的目标是什么。如图表 8所示,将优化工具加入到虚拟标定过程中,其实就是依据工程师的实际标定工作步骤和流程,在虚拟模型的平台上进行实现(比如通过编写脚本等方式)。优化工具在这里起到的作用就是代替人力,去自动寻优;每次寻优后的参数值自动带入到模型后,去检验仿真输出的目标是否达到设定值,如果未达到则继续寻优迭代,直至找到最优值。
比如在MiL环境下,我们可以将优化工具Heeds集成到Simulink控制模型和AMESim的被控对象构成的闭环系统中,如图表 9所示:在设定好成本函数和标定参数初值后,由Heeds通过优化算法去寻优,生成的参数值传递给Simulink以及AMESim的模型来设定运行工况,给参数赋值。当然,需要提前在控制模型中开放相应的参数值或参数表给外部环境,这样才能让Heeds访问并修改这些量。

图表 9 – Heeds优化工具用于虚拟标定闭环控制系统
可以看到在这个过程中,只要提前定义好标定参数的数量及标定值的范围,在Heeds中定义成本函数以及优化目标(可以是多个),那么通过优化过程就可以大大提高寻优效率,生成的标定值即便只是MiL环境的仿真结果,但对于后面的开发工作可以提供相应参考。

总结
在“数字孪生”的大潮下,“虚拟”技术的应用已经越来越广泛且迅速,甚至说到了野蛮生长的地步也不为过。但越是在这种情形下,越要保持清醒并明确引入新技术手段的目的是什么。对于虚拟标定来说,不能妄图一步到位,应该规划出阶段性的工作,控制项目风险,确保步进式的项目收益。
最后,总结如下几点作为本文的概括:
1First
虚拟标定的核心是“虚拟”而非标定,整车传统标定工作的目的和流程是梳理虚拟标定工作内容的依据。只有在充分了解标定工程师的标定流程和目标,系统设计和系统仿真工程师的技术能力,以及项目相关的所有输入数据(设计参数,试验数据等)后,才能规划好建立“虚拟”环境的步骤和内容,搭建好虚拟标定工作的平台。
2Second
虚拟的模型要根据标定内容进行层级划分:不同的控制器标定项对应了不同的物理过程,模型的开发势必要提前统筹。需要用几种模型,几种不同复杂程度,如何组合和集成,模型间接口定义等工作,都是要考虑的方面。而且从MiL到HiL还要涉及到模型的实时化处理,模型在不同阶段也需要有效的衔接来支持虚拟标定工作。
3Third
优化工具的使用可以进一步助力虚拟标定,将本来是人工的参数调教工作,转化为优化工具里设定的步骤,最终通过工具来自动寻找最佳的标定参数,从而达到标定目的。但优化结果可信度的大小是取决于物理模型本身的精度和可预测性的。
最后的最后,感谢各位的阅读,也欢迎大家讨论交流,虚拟标定以后会是一个很有趣的业务方向。
- 下一篇:声功率与声强(4)—— 基于声强测量的声功率测试
- 上一篇:导远设立临港研发中心
最新资讯
-
奇石乐推出用于DAQ数据采集系统的KiStudio
2025-04-28 17:51
-
全球首次!IVISTA 2023版修订版引入带灯光
2025-04-28 09:59
-
我国首批5G毫米波行业标准送审稿审查通过
2025-04-28 08:56
-
5/16 厦门- 新能源汽车电驱测试技术的创新
2025-04-28 08:53
-
国内首个汽车电磁防护技术验证体系EMTA正式
2025-04-28 08:49