磷酸铁锂正极锂离子电池安全性能影响因素
摘要:选择起火事故大巴车上残存的20只32650型磷酸铁锂动力锂离子电池,用内阻测试仪测试内阻、电压,用充放电设备分析容量,用绝热加速量热(ARC)进行绝热热失控分析,用差示扫描量热(DSC)分析电极和电解液的热稳定性,用SEM研究负极表面和正极截面的形貌与组成,用x射线光电子能谱(XPS)研究负极表面组成和固体电解质相界面(SEI)膜厚度,用气相色谱一质谱(GC—MS)研究电解液有机溶剂组成的变化。20只电池的内阻分布于12.12~18.26越,一致性很差。内阻最高(18.26 m11)的电池防爆阀启动温度比内阻最低(12.12 ml't)的约低7℃。材料分析发现,一致性差的原因是:极卷最外层负极压实密度过大造成负极中残留大量死锂;电解液存在N一甲基吡咯烷酮杂质,易造成活性物质脱落;正极活性材料中存在Fe.P化合物杂质,使得电池容量不一致;电解液纯度低,出现大量副反应产气。
关键词:起火事故;磷酸铁锂(LiFePO。);锂离子电池;热安全性能
作者:
贺兴:中国标准化研究院
林波:中国标准化研究院
缪文泉:上海智能新能源汽车科创功能平台有限公司
韩广帅:同济大学汽车学院
电动汽车可分为油电混合动力汽车及纯电动汽车两类,大多以锂离子电池为电力存储装置。电动汽车在使用过程中存在安全问题,解决动力锂离子电池的安全隐患势在必行。动力锂离子电池从使用正极材料的角度,主要分为磷酸铁锂(LiFePO4)、锰酸锂和三元材料等3类。LiFePO4具有高热稳定性、体积变化小等优势,是3种材料中安全性能和电化学循环性能较好的。研究LiFePO4动力电池安全性能的影响因素,有利于改善电动汽车的安全问题。
本文作者以事故电动大巴车残存的32650型LiFePO4动力电池为研究对象,对基本的电化学性能、热安全性能进行测试分析,进而拆解电池观察内部结构,对关键材料进行解析,判断电池生产工艺及关键材料性能对电池安全|生的影响。1 实验1.1 样品及测试环境实验以起火事故TEG6110电动大巴车(湖南产)上残存的32650型LiFePO4动力锂离子电池(深圳产,额定容量为5 Ah)为研究对象。测试环境温度为(25±1)℃;环境相对湿度不高于30%。1.2 电池电化学性能测试用BT3563内阻测试仪(日本产)对20只电池样品进行电压、内阻测试。用5V/10A电池充放电测试仪(深圳产)进行容量标定。电池以1.5A恒流充电至3.65 V,转恒压充电至0.15 A;以1.5 A恒流放电至2.00 V。循环3次,以第3次放电的容量作为标定容量。1.3 电池热安全性能测试用BTC-130型绝热加速量热(ARC)仪(英国产)测试电池充放电过程中的自放热温升情况,以分析电池工作过程中的热安全性。1.4 电解液收集和电池拆解将事故电池调整到放电态(2.00 V),离心收集电解液,再在充满氩气的手套箱中于放电态下拆解。将拆解得到的正极、负极和隔膜分别用碳酸二甲酯(DMC,苏州产,电池级)浸泡12h后,在40℃下真空(-105Pa)干燥2h,备用。1.5 关键材料测试1.5.1 电极表截面形貌及组成用IB一19520CCP型冷冻横截面抛光仪(日本产)进行极片截面的制备。用JSM-7610FPlus型场发射扫描电子显微镜(日本产)观察负极的表截面形貌及组成;用K-ALPHA型X射线光电子能谱(XPS)仪(美国产)分析负极表面组成,并通过刻蚀半定量的方法分析固体电解质相界面(SEI)膜的厚度。1.5.2 电解液测试用5977B型气相色谱-质谱(GC-MS)仪进行电解液溶剂测试,测试条件:全程操作规避空气接触;初始升温温度为35℃;以10℃/min升温至230℃。用5110型电感耦合等离子光谱(ICP-OES)仪(美国产)对电解质盐进行分析。1.5.3 热稳定性测试用DSC3+型差示扫描量热(DSC)仪(瑞土产)测试纯电解液、正极和负极的热稳定性。在手套箱中将极片裁剪成2mmx2mm,放入镀金高压坩埚中,装入2.5µl从电池中收集的电解液并润湿极片,在手套箱中密封后进行测试。测试的温度为25-350℃,升温速率为10℃/min。2 结果与讨论2.1 电化学性能20只电池的电压、内阻测试结果如图1所示。
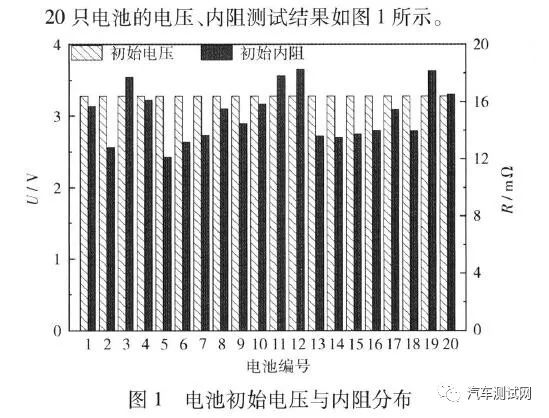
依据电池出厂信息可知,该电池的满电态电压为3.65 V,出厂内阻值≤10 mΩ。从图1可知,各电池初始电压一致,均接近半电态;5号电池内阻最低,为12.12 mΩ,12号电池内阻最高,为18.26 mΩ。取样电池的内阻差值在6.14 mΩ内,且所有内阻均高于出厂信息中的最高值10mΩ,说明该事故残存电池的内阻与出厂时相比有不同程度的增加。
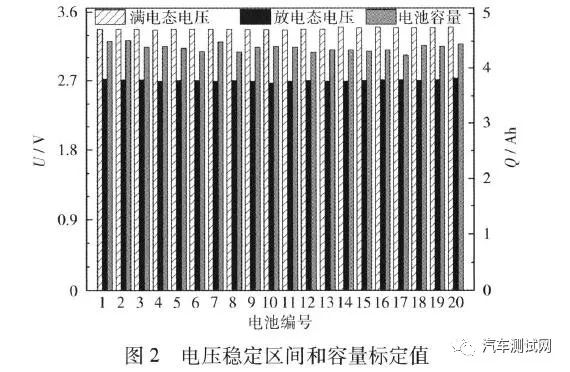
从图2可知,电池在测试后的稳定电压区间位于2.67~3.41 V,说明该事故残存电池的极化增大,与内阻的变化趋势一致。20只电池的容量标定值分布于4.238~4.517Ah,均低于5Ah的标称容量,说明事故残存电池的容量已出现下降,且一致性变差。综上所述,电池的内阻增大、极化变大且一致性变差,可能会增加发热量,降低热失控温度,加速性能衰减,影响使用安全。为研究内阻不一致电池之间的热安全差异,选择5号(内阻为12.12 mΩ)和12号(内阻为18.26 mΩ)样品,进行热安全性能分析。为研究电池内部是否存在可能引发异常的因素,选择内阻基本一致的8号(内阻为15.51 mΩ)、17号(内阻为15.44 mΩ)样品,在放电态进行拆解分析。2.2 电池热安全性能电池热失控温度-时问曲线见图3。
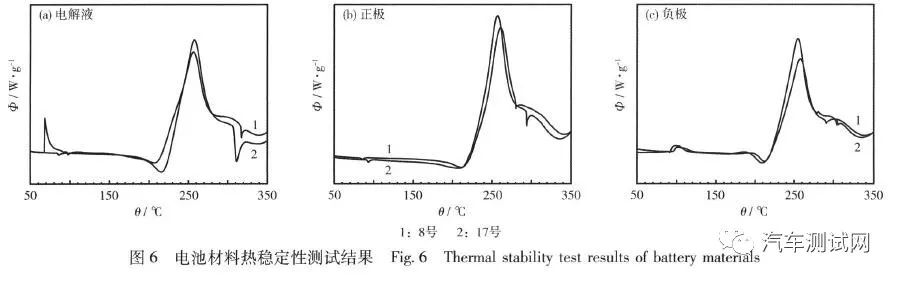
从图3可知,5号及12号电池开始自放热的温度分别为79.8℃和70.8c℃;防爆阀启动的温度分别为121.2℃和114.2℃。电池开始自放热和防爆阀启动的温度均比较低,在实际使用时,如果散热不好,很容易在环境温度和充放电产热的双重影响下开始自放热,引发热失控、起火和爆炸。2.3 生产工艺对电池安全性能的影响拆解电池观察电池内部各部分结构,可判断生产工艺对电池安全性能的影响。在拆解过程中打开电池防爆阀处顶盖时,可感受到明显的气体排出,从气体的存在可以推测,电解液很可能发生了变质。图4为电池拆解及电流切断装置(CID)示意图。图5为从电池卷芯中取出的正极、负极、隔膜的展开示意图。从图4可知,电池正极侧有CID,用于在失效导致内部产气过多时,阻断电池内部极卷与正极极柱的接触,防止电池出现安全问题。实验观察到17号电池的CID启动,说明内部已发生剧烈的副反应,导致大量产气。从图5可知,8号及17号电池中的正、负极均未见掉料问题,正极、隔膜表面无明显异常,但在极卷最外面一圈的负极内侧面,出现了异常颜色花纹,同时,后续负极中心区域也能见到隐约的铜色。异常颜色,说明负极中残留较多死锂,从侧面证实电池容量发生了衰减。极卷最外侧那层负极的异常颜色更突出,将导致嵌入负极的锂难脱出,与负极最外层压实密度过大有关。此处死锂的存在,成为电池内部安全性较差的影响因素之一。若电池因外界滥用造成温度升高,该区域较其他部位更容易出现安全问题。
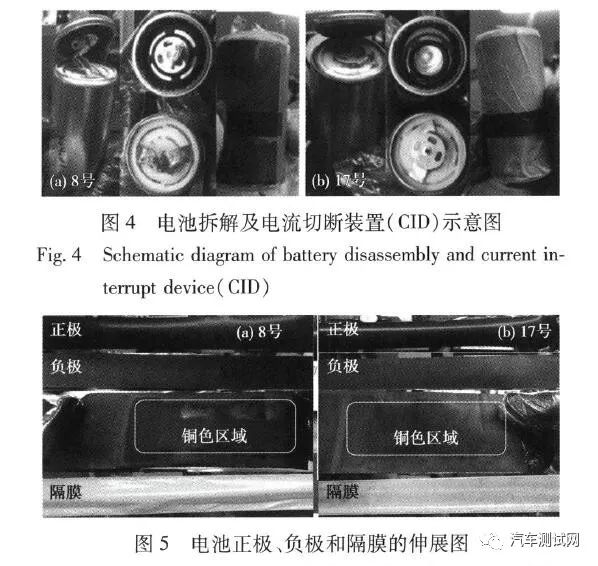
2.4 电池关键材料的安全性能2.4.1 电池材料的热稳定性电池材料热稳定性测试结果见图6。从图6可知,各材料的主要放热峰均出现在256℃左右,与电解液的放热峰相近,说明该电池中正负极材料的热稳定性与电解液密切相关。对比来看,17号电池的电解液存在异常情况,在68℃出现了一个小的放热峰,推测电解液中出现了异常组分,且该组分在70℃左右的较低温度下就会出现放热现象,不利于电池的热稳定性。
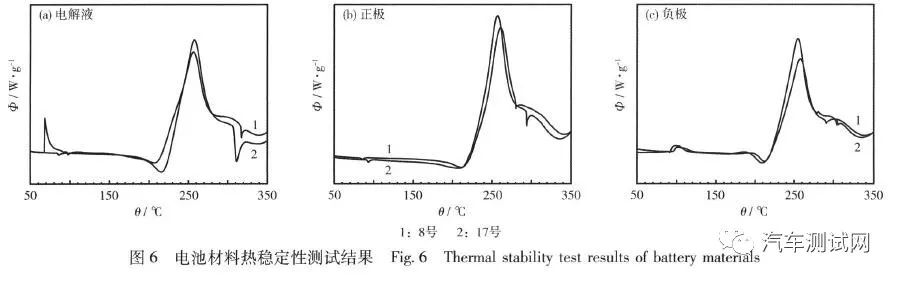
图6 电池材料热稳定性测试结果2.4.2 电解液的组成两只电池中收集到的电解液均呈现黄色,而正常状态下电解液为无色透明液体,说明电解液的部分成分可能发生变化。电池电解液溶剂组分的分析结果见图7。
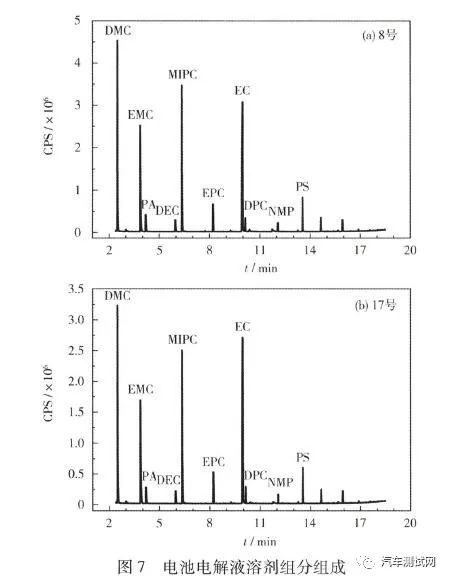
从图7可知,电解液主体有机溶剂以DMC、碳酸甲乙酯(EMC)、碳酸甲异丙酯(MIPC)和碳酸乙烯酯(EC)为主,添加剂为1,3-丙烷磺酸酯(PS),其他组分有少量的碳酸二乙酯(DEC)、丙酸甲酯(PA)、碳酸丙乙酯(EPC)和碳酸二丙酯(DPC)等,可能是由于有机溶剂不纯,或在电化学环境下有机溶剂的分解所致[如式(1)]。存在的长链化合物,可能是由于有机溶剂的聚合而成[如式(2)]。两个样品的电解液中均检测到N-甲基吡咯烷酮(NMP),可能是正极极片烘烤不充分残留的。NMP长时间残留,会影响极片的黏结性,增加电池内阻,进而影响电池的循环和安全性能。
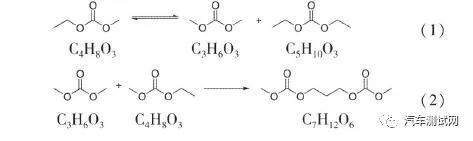
2.4.3 负极表面形貌8号与17号电池负极表面的形貌见图8。
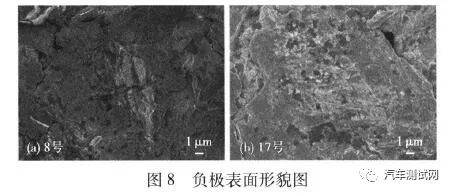
从图8可知,8号与17号电池负极表面的石墨形貌轮廓均比较模糊,表明负极表面覆盖有一层膜状物质,说明负极表面形成了较厚的SEI膜。SEI膜在电池循环过程中的持续生长,也是电池容量衰减、内阻增大主要的原因。2.4.4 负极表面SEI膜组成及厚度XPS分析得到的负极表面的元素含量列于表1。表1 负极表面元素物质的含量
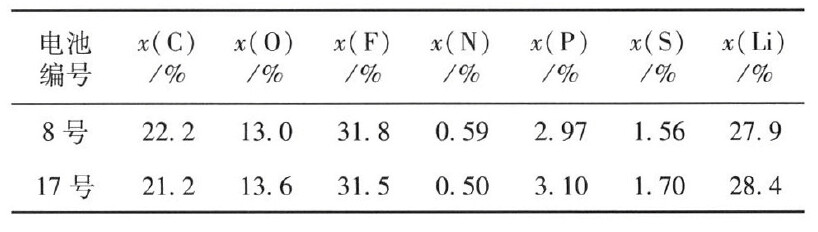
从表1可知,8号和17号样品负极表面含有C、O、F、Li、P、S和N元素,表明有电解液残留。表面元素分析结果表明:负极表面有一层SEI膜,主要成分为Li2CO3、LiF及烷基锂等,均为SEI膜的常见组分,未见异常。负极表面以F元素和Li元素为主,其次是C元素,推测负极表面SEI膜中的主要成分是氟化锂。石墨负极的表面元素通过氩气离子团簇随刻蚀时间变化的曲线见图9。
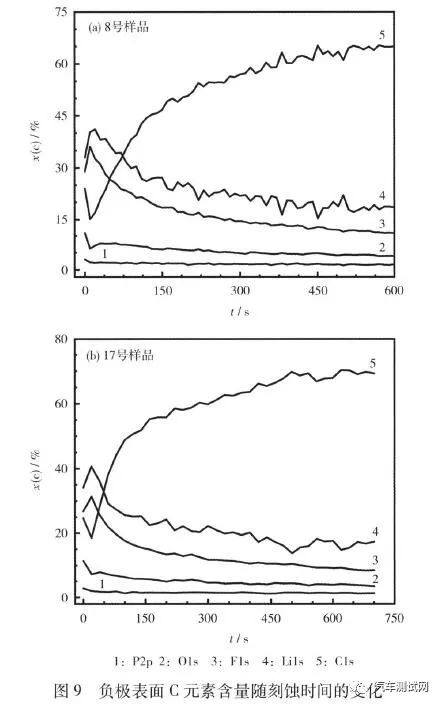
从图9可知,以二氧化硅刻蚀速率作为参比,计算得出8号电池表面SEI膜厚度在刻蚀150s时约为69nm;17号电池表面SEI膜厚度在刻蚀125s时约为58 nm。这表明,两只电池负极表面的SEI膜均较厚,说明电池内部发生的副反应较多,导致SEI膜增厚。这会导致容量衰减、内阻增大,进而影响电池的循环和安全性能。2.4.5 正极截面形貌及组成正极截面SEM图及选区元素见图10,正极截面选区元素分析结果见表2。
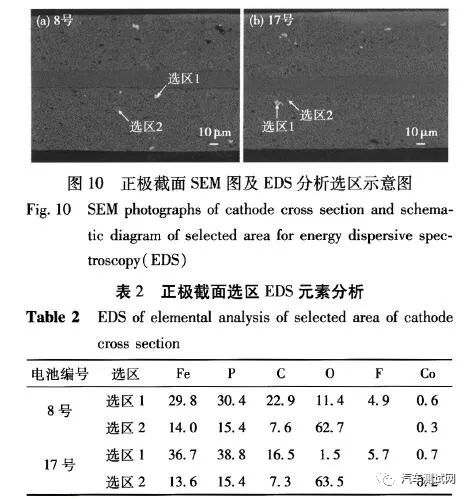
结合图10和表2可知,正极截面上观察到少量块状杂质。分别对大片同色区域和局部少量亮色杂质区域进行选区元素分析,发现不论该杂质区域还是正常活性材料区域,均普遍存在微量的Co元素,可能是原料或者生产过程引入的杂质。对白色区域杂质分析可知,该区域氧含量明显低于正常LiFePO4。材料,推测可能存在不含氧的Fe-P化合物。该化合物可能是生产LiFePO4。过程中产生的副产物,它的引入,可能是电池设计容量不足、容量不一致、极化增大的原因之一。
3 结论
本文作者对电池整体进行分析研究,发现该LiFePO4。动力锂离子电池的批次一致性较差,标定容量值均小于额定容量值5Ah,同时,内阻均比出厂信息标注的最大值10mΩ大。出现上述问题的原因可总结如下。
生产工艺方面存在两个问题:①极卷最外层负极压实密度过大,造成了电池卷芯最外层负极中残存大量死锂无法脱出,导致容量降低;②电解液中检测出NMP,说明极片烘干不彻底,导致电极内的黏结性下降,活性物质脱落,电池容量降低,内阻增加,进而影响电池的安全性能。
关键材料方面存在两个问题:①正极活性材料LiFePO4。中存在Fe-P化合物杂质,导致电池容量不一致、极化增大;②电解液纯度低,导致循环过程中发生大量副反应,引起电池产气。
参考文献:
[1] 王绥军,傅凯,徐斌.磷酸铁锂动力电池寿命中期低温安全性能[J].电源技术,2017,41(3):364—366.
[2] YUAN L X,WANG Z H.Development and challenges of LiFeP04 cathode material for lithium—ion batteries[J].J Energy Environ Sci,2011,2(4):269—284.
[3] 张长煦,倪子潇.车用三元锂电池与磷酸铁锂电池对比分析[J].汽车实用技术,2019,(23):28—29.
[4] 王国增.锂离子电池正极材料磷酸铁锂的研究[D].天津:天津大学,2008.
[5]COMAN P T,MAT]&FI-TEMPFLI S,VEJE C T,et a1.Modeling vapofization,gas generation and venting in Li—ion battery cens with a dimethyl carbonate electrolyte[J].J Electrochem Soc,2017,164 (9):AI 858一A1 865.
[6]黄可龙,王兆翔,刘素琴.锂离子电池原理与关键材料技术[M].北京:化学工业出版社,2007.
[7] OSWALD S,HOFFMANN M,ZIER M.Peak position differencesobserved during XPS sputter depth profiling of the SEI on lithiated and delithiated carbon—based anode material for Li—ion batteries [J].Appl Surface Sci,2017,401:408—413.
- 下一篇:车辆安全过弯中的速度规划问题与探索
- 上一篇:扁线电机产品的技术现状及未来发展趋势
编辑推荐
最新资讯
-
《汽车轮胎耐撞击性能试验方法-车辆法》等
2025-04-25 11:45
-
“真实”而精确的能量流测试:电动汽车能效
2025-04-25 11:44
-
GRAS助力中国高校科研升级
2025-04-25 10:25
-
梅赛德斯-AMG使用VI-CarRealTime开发其控制
2025-04-25 10:21
-
天检新能力VOL.95 | 乘员晕车仿生测试能力
2025-04-25 10:14