和特嗨一起拆解|一体化封装电堆
燃料电池堆的封装工艺对于其性能和安全性至关重要。封装工艺需要确保电池堆内部压力分布的一致性,这对于电堆的稳定性、寿命和功率密度等性能参数有着直接影响。燃料电池堆根据其不同的封装结构形式可划分为螺杆、拉杆、绑带、壳体一体化四种形式。
当前燃料电池堆封装方式多以螺杆、拉带和绑带封装形式为主,有结构复杂、装配效率低和塌腰失效等劣势,复杂的工艺会导致如封装力或密封压力分布不均匀等问题,这会引起气体泄漏,降低发电效率,甚至引起氢气爆炸事故。
一体化封装方式集拉紧、固定于一体,由壳体直接承担堆芯的压装力。堆芯压装后,套装壳体固定堆芯,省略了螺杆、拉杆、绑带等配件及紧固操作步骤。这种形式结构简易、成本低、可靠性高,提高了生产效率。
一体化封装具备功率密度提升、集成化成都高、工艺简化等优势,正成为目前车用金属板电堆集成的重要发展方向。本文通过拆解一体化封装工艺电堆总结其的技术特点。
01 功率密度的优势
由于采用外固定的一体化封装工艺,简化了电堆壳体内部结构,提升了壳体内部空间利用率,同时M车型膜电极采用了多孔质碳载体,在保证性能的同时减少了单电池片数,进而减小了电堆的体积。粗略估算M车型电堆(含壳体)体积,仅为同功率级别的拉杆式封装工艺电堆体积的70%,对应的体积功率密度高出52%。
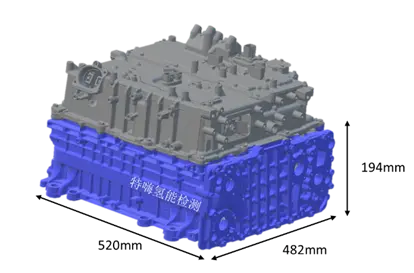
M车型一体化封装电堆尺寸
02 集成化设计思路
集成化
承载组装力的气口端板和承压端板直接与封装壳体连接,封装壳体是承载堆芯组装力的直接媒介。气口端板为注塑一体化端板,通过螺栓与封装壳体连接。承压端板活装于壳体内部,通过安装于壳体外部的顶紧螺栓调节电堆压缩位移。
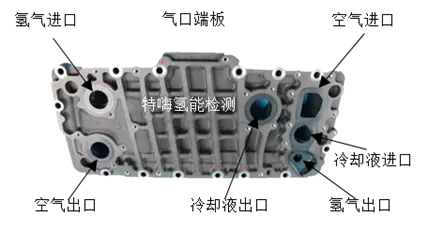
气口端板接口示意图
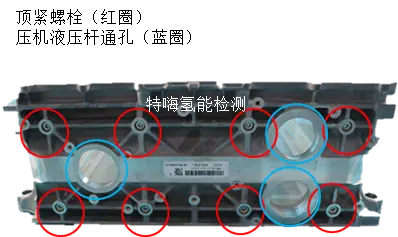
电堆盲端孔位示意
轻量化
电堆及FCDC总成高度集成,壳体均为铝合金材质。FCDC居上无下盖板,电堆居下无上盖板,二者互借壳体结构合二为一,省掉两个盖板的重量。
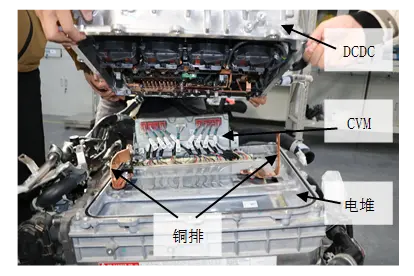
电堆与DCDC总成分离过程
小型化
CVM封装于电堆及DCDC总成内,安装在电堆上方,DCDC壳体留有其布置空间,不占用电堆的横向空间,且总成外部无CVM维修口,设计紧凑。
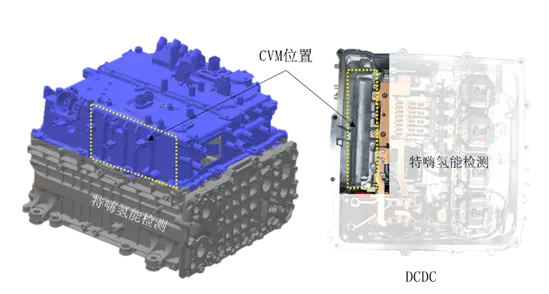
CVM布置位置
工艺简化
上壳体、下壳体采用压铸方法制成,上壳体的横梁具有导向及拉带的作用。电堆上壳体与下壳体通过搅拌摩擦焊方法形成,直接省掉了螺栓安装过程和密封工艺。
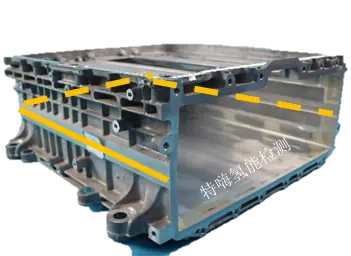
电堆上下壳体搅拌摩擦焊
03 一体化封装工序
通过M车型电堆拆解过程中观测到壳体孔位,单电池及承压端板定位结构等,推测电堆封装工序如下,具有工序少,自动化程度高的特点:
①压装前,将堆芯纵置于压机之上,气口端版位于堆芯底部,承压端板位于堆芯顶部,堆芯两侧通过定位工装保证堆叠不错位,壳体通过工装固定在压机上部,壳体预留有液压杆穿过孔位;
②液压杆将承压端板从上往下向堆芯施压,当压紧时,移除定位工装,保持压紧状态;
③壳体通过工装沿液压杆方向从上往下安装,下部与气口端板接触,上部与承压端板接触;
④下部气口端版通过螺栓与壳体连接,上部顶紧螺栓连接于壳体将承压端板顶紧。
04 总结
通过拆解M车型电堆,了解到一体化封装在功率密度提升,集成化、轻量化、小型化,生产效率提升等方面有诸多优势,但对密封性、安全性、稳定性提出了较高的要求。可以肯定的是一体化封装正成为电堆集成的重要发展方向。后续我司将继续分享一体化封装工艺相关内容,如密封、绝缘、防塌腰设计等。
最新资讯
-
全国汽车标准化技术委员会汽车节能分技术委
2025-04-18 17:34
-
我国联合牵头由DC/DC变换器供电的低压电气
2025-04-18 17:33
-
中国汽研牵头的首个ITU-T国际标准正式立项
2025-04-18 17:32
-
为什么要进行汽车以太网接收测试?汽车以太
2025-04-18 17:26
-
产品手册下载 | NI 全新USB数据采集-NI mio
2025-04-18 16:39