万字解析线控底盘技术
引言
在当今这个由科技驱动的时代,汽车电动化、智能化已成为汽车行业的热门话题。特斯拉的自动驾驶功能、蔚来的换电模式、以及比亚迪的刀片电池技术,这些创新不仅引领着市场趋势,也推动着消费者对智能、环保出行方式的期待。
在这样的背景下,线控技术(x-by-wire)作为智能汽车的核心技术之一,正迅速成为市场关注的焦点。这项技术最初在航空领域大放异彩,如今在汽车行业同样展现出其革命性的潜力,为智能驾驶和电动汽车提供了前所未有的控制精度和响应速度。
线控技术的核心在于通过电子信号代替传统的机械或液压系统来实现对车辆的精确控制。这种技术不仅极大提升了车辆的操控性能,更为实现全面智能化和自动化驾驶铺平了道路。
线控底盘,作为汽车线控技术的承载,涵盖了驱动、制动、转向和悬架等多个系统,它们共同构成了自动驾驶的”基石“。
本文将深入探讨线控底盘的纵向和横向控制,从线控驱动系统的速度控制,到线控制动系统的制动力精确施加,再到线控转向系统的敏捷响应,我们将一一解析这些系统是如何提升汽车性能,增强驾驶体验,并为未来的自动驾驶奠定基础。同时,我们也将审视线控技术面临的挑战和未来的发展方向,以期为读者提供一个全面的视角。
01 什么是线控底盘?
线控技术(x-by-wire),这一源自航空领域的革命性创新,最初应用于飞机的飞行控制系统(fly-by-wire)。
它的工作原理十分直观:通过传感器捕捉飞行员的操作动作,这些动作随即被转换为电信号,经过电子控制单元(ECU)的精确处理,最终传递至执行机构,实现对飞机的精准控制。
这种技术,也被称为电控技术,它利用精确的电子传感器和执行元件,取代了传统的机械或液压系统。
应用了这项技术的汽车底盘系统,我们称之为线控底盘。
在智能驾驶的场景中,车辆的感知模块负责收集周围环境的信息,决策规划模块根据这些信息做出任务决策,并规划出车辆的最佳行驶轨迹。随后,控制模块便负责确保车辆严格遵循这一规划轨迹行驶。
车辆执行控制模块发出的指令,主要涉及哪些方面呢?

图1 线控底盘基本控制原理图
答案包括加速、刹车、转向等关键操作,这些操作在车辆上体现为对驱动、制动、转向等系统的精确控制。为了进一步提升车辆在行驶中的平顺性和操控稳定性,悬架系统的控制同样不可或缺。
概括来说,线控底盘的核心任务是对汽车的驱动、制动、转向和悬架系统进行精确控制。对于以内燃机为动力的汽车,线控底盘还包括对档位的控制。
线控底盘系统将传统的机械操作转化为电子信号,不仅提升了车辆的响应速度和操控精度,也为智能驾驶和自动驾驶的实现奠定了坚实的基础。
接下来,我们将从汽车行驶纵向和横向控制来对线控底盘系统的子系统进行介绍。
02 线控驱动系统
无论是发动机动力汽车还是电动汽车,线控驱动系统的核心任务都是精确控制车辆的速度。而对于动力系统而言,则是要控制输出的功率。
如果我们驾驶的是发动机动力的汽车,我们希望控制车辆加速,是通过油门踏板将加速的意图传递给发动机ECU。如果驾驶的是电动汽车,则是通过加速踏板将信息传递给VCU。这里的“油门”踏板和“加速”踏板,其本质都是传感器,采集的是驾驶员的驾驶意图,而踏板的开度和开度的变化率就分别对应到“想要获得什么样的速度”和“期望多长时间能够达到这个速度”。
我们先看内燃机动力的汽车,线控驱动系统是如何工作的。
1.传统油门
在传统的内燃机汽车中,油门踏板通过一根钢索或连杆与节气门相连。当驾驶员踩下油门,节气门开度随之变化,而安装在节气门上的空气流量计检测到进气量并传递给ECU。ECU根据进气量和车速等信息,计算出所需的喷油量,从而控制发动机的动力输出。
图2 传统油门结构示意图(图源网络)
这种方式的优点是结构简单、可靠性高,能够快速响应驾驶员的意图。然而,它的缺点在于节气门的开度完全由驾驶员主观控制,没有考虑到车辆的实际工况、道路条件或天气因素,这可能导致油耗增加和排放污染。
2.电子节气门
为了解决这个问题,电子节气门控制系统应运而生。
图3 电子节气门结构原理示意图(图源网络)
电子节气门取消了油门踏板和节气门之间的机械连接,转而采用位置传感器来传递踏板位移信息给ECU。ECU再结合其他传感器的信息,计算出最佳的节气门开度,并驱动节气门控制电机实现精确控制。这个过程形成了一个闭环控制,确保发动机以最高效的方式运行,同时减少了油耗和排放。
图4 电子节气门控制原理示意图
电子节气门技术已经非常成熟,几乎完全取代了传统油门系统,市场占有率达到了99%以上。
3.加速踏板
在电动汽车上,加速控制本质上就是“线控”。当驾驶员踩下加速踏板,整车控制器根据各传感器输入信号判断车辆当前工况并决策驱动电机的目标转矩,然后通过CAN总线将目标值发送给电机控制器(MCU),电机控制器根据接收到指令对电机进行控制。
图5 加速踏板工作原理示意图
线控驱动技术被认为是线控底盘技术中最成熟的技术之一,已经实现了大规模的商业化应用。随着电气化水平的提升,线控驱动技术预计将由集中式驱动向分布式驱动发展,以满足未来智能汽车的需求。
03 线控制动系统
线控制动的核心也是对车辆的速度控制,通过控制施加在车轮上的制动力来控制车轮转速,从而达到控制车速的目的。
那么施加在车轮上的制动力又是从何而来呢?
1.机械液压制动到电子液压助力的演进
最原始的制动系统中,制动力几乎完全来自于“人力”——驾驶员操纵一组简单的机械装置向制动器直接施加作用力。但随着汽车越来越重,单纯依赖“人力”的机械制动已经无法满足基础制动需求,人们希望能在制动的时候施加一些“助力”。
早期的助力是采用真空助力的方式,整个系统包括真空助力器+液压制动系统,即机械液压制动。驾驶员踩下制动踏板,通过杠杆作用,踏板力经过第一级放大传递到真空助力器;真空助力器经第二级放大,将制动力传递到主缸;主缸的制动液被推入轮缸,并在压强的作用下产生更大的制动力。制动力推动轮端卡钳加紧制动盘阻碍刹车盘的转动,从而实现对车轮的制动。
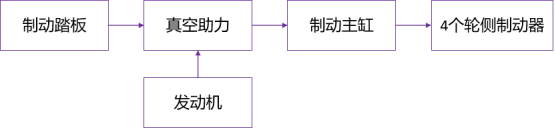
图6 传统燃油车制动系统能量传输示意图
在这一时期,随着对制动性能、安全性要求的提高,基于液压制动系统结合电子控制技术,出现了一系列电子辅助制动系统,包括有解决制动时车轮抱死问题的ABS、解决驱动工况下稳定性问题的TCS、解决车辆侧向稳定性问题的VDC。
ESP是由博世推出的集成了ABS、TCS和VDC功能的产品,在1995年实现批量生产及首次应用。随后其他厂家也陆续推出类似的产品,统称为电子稳定性控制系统ESC。当前市场上的ESC系统除了基础的稳定性控制功能外,还提供一系列辅助驾驶功能,下表为ESC包含的部分功能。
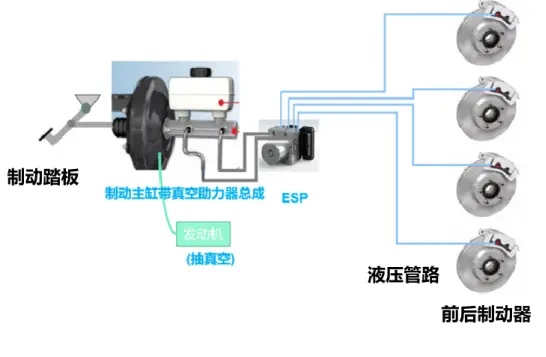
图7 传统燃油车制动系统结构示意图(图源网络)
总而言之,汽车制动系统到此演进为“真空助力+ESP”的方案。
2.电机助力eBooster的突破
传统的机械液压制动系统真空助力器的真空源来自于发动机。
而在电动汽车或者是增程式混动汽车上,一方面,由于没有发动机或者发动机不持续工作,依赖发动机产生真空源的真空助力器的使用受到了限制。另一方面,由于动力电池的存在以及节能的需求,新能源汽车需要通过电机进行制动能量回收。
传统的依赖发动机真空源的助力器已很难满足工作要求。
因此出现了两种解决方案:
电子真空助力
第一种方案是采用电子真空泵来保证真空助力器的真空环境。这种方案的优点是维持真空+液压为主体的结构,技术成熟且成本较低;能够采用12V的车载电源,现有的车辆电路系统满足要求。缺点是性能相对较差,噪音大,并且故障率高。同时这种方案依然是机械传动,而非线控系统,不能满足汽车智能驾驶辅助功能如ADAS等的需求。
电机助力
第二种方案是采用电机助力的方式,完全放弃了真空助力,而采用电机+减速器替代了真空泵和真空助力器。
最早的电机助力的产品是由博世推出的,命名为iBooster。
在博世以后,国内外市场上又涌现了出了电动助力器产品,各个厂家对其命名各异,但统称eBooster。
iBooster利用传感器感知驾驶者踩下制动踏板的力度和速度,并将信号处理之后传给电控单元,电控单元计算出所需的制动力,并将信号传递至伺服电机,伺服电机输出对应的扭矩,并在机电放大机构的驱动下,推动制动主缸内的制动液,从而形成制动力达到制动效果。
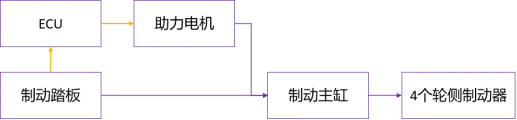
图8 电机助力制动系统能量传递示意图
在这个方案中,通过对电机的线控,实现了制动力的精准输出。
图9 博世第二代iBooster
3.电子液压制动系统之Two-box与One-box
由于制动执行机构依然是采用的液压传动的方式,这类电机助力制动系统被称为电子液压制动系统EHB(electro hydraulic brake system)。
根据助力系统与ESP的集成部不同,EHB又有Two-box和One-box两种方案。
Two-box方案
图10 Two-box系统结构示意图
Two-box方案中,iBooster与ESP是两个独立的模块,两种协同工作,其原理如下:
iBooster与ESP共用一套液压系统,包括制动主缸、制动管路、制动油壶等。
iBooster的助力电机产生驱动力推动制动主缸活塞运动,使油壶中的制动液流入主缸管路并进入ESP进液阀,经ESP流入四个轮缸,从而建立制动力。
当iBooster不工作时,ESP也可以独立控制制动液从主缸流入轮缸,从而建立制动力。
iBooster建压的动态响应速度比ESP主动建压快,且NVH表现更好,因此在这个制动系统方案中,iBooster使主执行机构。
从上述Two box的工作原理可以看出,Two box方案除了实现制动助力和稳定性控制外,iBooster与ESP互为冗余,一旦iBooster失效,ESP系统将接管并提供制动助力;即便是在在两者都失效的情况下,驾驶员仍然可以通过纯液压制动系统制动。
另外,iBooster与ESP还能在实现制动能量回收的同时协调配合,保证在电制动和液制动的切换中实现驾驶员的踏板感一致。
图11 两级失效保护
但,由于iBooster的助力器与制动踏板没有完全解耦,机械上还是直接连接的,当智能驾驶系统请求制动控制时,在驾驶员无干预的情况下,制动踏板会根据减速度大小而动态升降,这样有可能会出现夹脚的问题。
另外,踏板感的调教需要在项目开发前期考虑制动器的需液量、主缸大小、踏板的杠杆比、助力器的助力比、起始力等,相关机械件一旦确定后,踏板感就无法更改。并且,不同车辆需要进行重新设计,费钱费力。
同时,L2及以下的智能辅助驾驶系统对制动系统没有冗余需求,对线控制动系统的需要主要是高动态响应特性以及制动能量回收功能,在这种情况下,two box方案的成本与体积都不具优势。
One-box方案
在此背景下,博世将iBooster与ESC集成为一体,推出智能集成制动系统IPB(integrated power brake),这就是业内常说的EHB的另一个方案——One box方案。
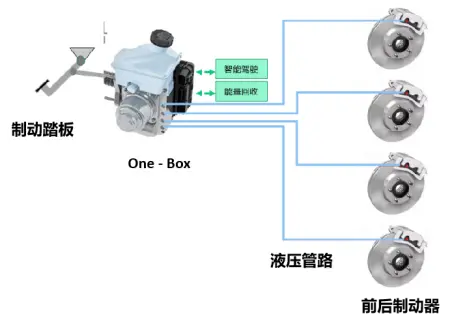
图12 One-box系统结构示意图
One box方案与Two box方案相比,制动助力都是由电机提供,主要的差异在于one box中制动踏板与助力器完全解耦。
以博世的IPB为例,IPB制动系统主要由以下部分组成:制动踏板、制动主缸、踏板模拟器,建压部分以及压力调节部分。
IPB的工作原理分两种情况,一种是正常工作状态,另一种是助力失效状态。
正常工作状态
正常工作时,当驾驶员踩下制动踏板后,推杆推动IPB内部的主缸主腔活塞,制动液进入踏板模拟器模块,此时主缸主腔和副腔通向轮端的电磁阀关闭,从而实现解耦。与此同时,IPB的ECU通过检测到推杆处的踏板位移信号,按照预先标定好的踏板位移-制动系统压力曲线控制内部电机建压,从而产生车辆减速度。
图13 IPB工作原理示意图(图源:Integrated Power Brake – modular set extension for highly automated driving)
助力失效状态
当断电等情况造成助力失效时,IPB进入机械backup模式,通往踏板模拟器的电磁阀1关闭,电机通往轮端的电磁阀4、5也关闭,主缸主腔和副腔通往轮端的电磁阀2、3打开。驾驶员踩踏板建立的压力直接进入轮缸从而实现制动减速,根据法规要求,当驾驶员输入500Nm的踏板力时,IPB系统应产生≥2.44m/s²的制动减速度。
根据GB/T 40429-2021《汽车驾驶自动化分级》文件可知,在L3及之前,制动系统发生故障后进入back-up模式,要求驾驶员接管车辆。而在里L4和L5,制动系统失效后的车辆状态由车辆控制系统负责,这就意味着,原本由驾驶员接管并完成的动作,需要全部由系统来完成。这就需要L4、L5智能驾驶汽车的制动系统需要有冗余备份控制单元。
针对这个问题,博世提出了一个冗余制动单元RBU(redundant brake unit)作为IPB的补充,即IPB作为主要的制动系统来执行正常情况下的制动请求,RBU作为IPB失效情况下的冗余制动,代替驾驶员操作。
图14 RBU工作原理示意图(图源:Integrated Power Brake – modular set extension for highly automated driving)
无论是Two box方案还是One box 方案,都是对制动系统的动力输入端进行的线控改进,而制动执行单元仍然保留液压系统,所以这两类方案被统称为电子液压制动系统EHB(electro-hydraulic brake)。
另外根据法规要求,乘用车在电子助力失效的情况下,机械部件仍然要保证驾驶员在用500Nm踩制动踏板时能产生2.44m/s²的减速度,因此当前的EHB系统都保留了机械备份。这使得EHB系统被认为并非“完全“的线控系统。
4.电子机械制动系统EMB(elecro-mechanical brake)
EMB与EHB最大的区别在于取消了制动液压系统,制动力矩完全是由四个轮端电机驱动的制动卡钳产生,并且制动踏板与制动系统之间也实现机械解耦,所有信号都通过电信号来传递,实现了真正意义上的“线控“制动。
图15 EMB结构示意图
相比EHB,EMB完全取消液压制动装置,降低主机厂的装配成本,且支持软硬件解耦。
简单的结构,使得EMB的体积更小,也能为整车节省安装布置空间及减少10%的重量。
EMB通过电信号可直接控制轮端电驱制动器,将汽车制动响应速度从150毫秒左右,缩减至80毫秒,大幅提升汽车行驶安全性。
虽然EMB有很多优势,但高度线控化也对EMB的可靠性提出了更高的要求,例如:
制动执行机构采用电机驱动,轮端集成了电机及驱动模块、减速模块、传感器等,车辆运行时车轮的震动、制动时产生的高温、以及雨水灰尘的腐蚀都对相关元器件的性能提出更高要求。
轮端制动需要更大的制动力,需要制动电机产生足够的功率,而轮侧空间有限,这就需要电机以较小的体积产生较大的功率,同时需要48V或更高电压来进行驱动。
EMB没有机械冗余,当系统线路短路或电源故障,如何满足失效备份的法规要求。
目前EMB系统尚未成熟,其量产应用面临着技术和工程上的诸多难题。根据高工智能汽车调研,预计最快在2026年实现在高端车型上的小批量量产。
04 线控转向系统
汽车转向系统是用来控制车辆横向运动的关键机构,直接影响车辆的操作稳定性与安全性,在驾驶过程中至关重要。
与汽车的驱动系统、制动系统一样,转向系统也经历了由纯机械转向到机械液压助力转向、电子液压助力转向、电动助力转向、线控转向的历程。电动助力转向是当前汽车转向系统的主流产品,线控转向是未来技术发展方向。
机械转向系统的结构原理很好理解,由包括方向盘、转向管柱的转向操纵机构、转向器、转向执行机构(转向节、转向摇臂、转向节臂、横拉杆等)三大部分。
图16 机械转向系统结构示意图(图源网络)
驾驶员转动方向盘,通过转向管柱传递到转向器,转向器将转向力放大后,再通过转向执行机构的传递,推动车轮偏转,从而改变汽车行驶方向。
显然这个系统相当费人力,稳定性、准确性和安全性都无法保证。
于是,人们想到给转向系统添加”助力“。
1.机械液压助力转向(HPS)
最早出现的助力方式是机械液压助力(HPS),在原来的系统上增加了转向助力泵、三通转向控制阀、可左右移动的液压缸、储油罐等。
图17 机械液压助力转向HPS系统结构图
转向助力泵由发动机带动,当发动机启动时,转向助力泵维持运转。当转动方向盘时,方向盘带动三通转向控制阀的开闭,控制液压油的流动,从而驱动轮胎转动。
由于助力泵是由发动机通过皮带带动,那么只要发动机在运转,助力泵将一直工作,持续消耗能量。并且方向盘到前轮的转向传动比固定不变,无法兼顾车辆在低速和高速时的转向特性。
2.电子液压助力转向(EHPS)
EHPS系统是在HPS系统的基础上发展而来,将转向助力泵的动力来源由发动机改为电动机,同时增加车速传感器、方向盘扭矩传感器、转向助力 ECU等。
图18 电子液压助力转向EHPS系统结构示意图
EHPS的助力原理与HPS基本相同,通过引入车速传感器等信号判断车辆行驶速度,借助电磁阀控制转向助力大小,使之可以根据车速变化,这在一定程度上满足了转向系统在低速时的操作灵活性要求,又提高了高速时的稳定性。
3.电动助力转向(EPS)
电动助力转向系统取消了液压系统,而是采用电机直接驱动。主要部件有电控单元、车速传感器、扭矩传感器、电机、减速机构、离合器、转向操纵机构、机械式转向器、转向执行机构等。
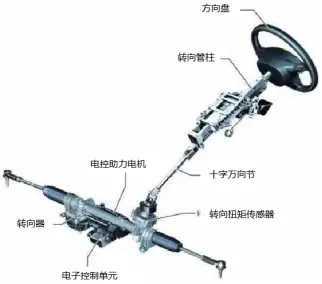
图19 电动助力转向系统结构示意图
EPS的工作原理比较好理解,通过车速、转向盘转矩、转向盘转角增量、电机位置等传感器信号,电子控制单元(ECU)可以做出更加优化的决策,控制电机的转向以及工作电流,进而控制转向助力的大小和方向。这进一步保证了车辆在低速时转向轻便,高速时,转向稳定、路感明确。
根据助力电机和减速机构的布置位置,EPS又分转向管柱助力式(C-EPS)、齿轮助力式(PE-EPS)、双齿轮助力式(DP-EPS)、齿条助力式(R-EPS)等。
值得一提的是,EPS通过电机已经足够实现智能驾驶系统对转向的精准控制,所以虽然有机械连接,但业内也认为EPS已经是一定程度上的线控产品。并且,由于驾驶员输入端与执行端的机械连接,当电动助力失效时,仍然可以通过人力来控制方向,提供安全备份。
那为什么还会有发展SBW的需求呢?
汽车智能化的发展要求转向系统能够不依赖人力,根据算法独立运转,同时要求响应时间更短,转向更加精准。
虽然EPS已经实现了部分的线控,但是其本质上依然是助力系统,转向信号是来自于人力。另外受限于机械结构而导致安装空间、力传递特性、角传递特性等因素,EPS是难以实现自动驾驶所要求的特性。
4.线控转向系统(steering by wire)
与EPS相比,SBW最显著的特征是去掉了从方向盘到转向执行器之间的机械连接,完全由信号实现转向的信息传递和控制。
图20 SBW原理示意图(图源网络)
SBW通常由路感反馈总成、转向执行总成、控制器以及相关传感器组成。
图21 线控转向组成结构示意图
路感反馈总成:由方向盘、扭矩转角传感器、路感电机、减速器等组成。路感反馈总成通过检测方向盘的转角和转矩,将驾驶员的转向意图转换成电信号,并传递给线控转向控制器;同时,路感反馈总成接收线控转向控制器反馈的力矩信号,产生方向盘的回正力矩,为驾驶员提供合适的路感。
线控转向控制器:是线控转向的核心,主要作用是分析和处理各路信号,判断转向意图和汽车的运动状态,并输出相应的控制指令。这里的控制指令包括路感反馈控制指令与转向执行控制指令。
转向执行总成:转向执行总成的作用是实现和执行驾驶员的转向意图,由转向器、转向执行电机、转向ECU、转矩转角传感器、车轮转向组件等组成。转向ECU接收到SBW控制器的指令,通过转向电机控制转向轮的转动,实现转向。
由于方向盘与转向执行器之间完全机械解耦,转向执行器接收到的转向信号是来源于SBW控制器的控制算法,而SBW控制器输出的转向信号是依据输入的驾驶意图信号,这个信号可以是通过方向盘扭矩转角信号获得的驾驶员输入的转向需求,也可以是脱离方向盘的智能驾驶系统的转向要求。
相比于当前主流的电动助力转向系统,线控转向具有响应灵敏度更好、智驾功能拓展性更高等优势;线控转向实现了驾驶员操作与车辆运动的解耦,可提高紧急转向操作的正确性和安全性;另外,方向盘与执行器的机械解耦意味着可以释放更多的前排腿部空间,传统机械式方向盘可以灵活的物理伸缩,以满足从手动到自动驾驶的空间转换。
与线控制动技术类似,线控转向技术的大批量推广还有一些问题需要解决。
首先是可靠性与安全性问题,所有的控制都通过电信号实现,那么如何确保电子部件发生故障后,系统仍然具备基本转向功能。
其次,线控转向系统需要实时地模拟路感,以便驾驶员感知实际行驶状况和路面状况,这对算法性能提出了较高的要求。
此外,线控转向对转向电机的功率、对传感器的精度要求高,如何平衡成本也是需要解决的问题之一。
根据高工智能其次研究院监测数据,2022年1-8月中国市场乘用车EPS前装搭载率为98.71%。而线控转向产品仍处于研发或小批量应用阶段。最早的量产线控转向系统是2015年英菲尼迪Q50搭载的DAS线控转向,DAS线控转向属于机械冗余线控路线。
2022年丰田推出的纯电动车bZ4X搭载了One Motion Grip线控转向系统,无机械备份,方向盘通过电线和电子系统连接到前轮。丰田的线控转向系统包括方向盘位置的转向扭矩执行器和转向轴位置的转向控制执行器组成。一方面方向盘扭矩和方向盘角度信号作为转向控制的核心输入量,与可变转向齿比功能结合计算出目标前轮角度控制变量,送入转向控制执行器当中的角度反馈控制器,基于前轮角度和电机电流进行精准控制。另一方面,前轮角度和电机电流又作为路面信息送回方向盘执行器产生转向反馈力。
同时为了确保安全性,这套线控转向系统又一个完整的备用控制器和线路。在一套系统故障失去功能的情况下,另一套系统可有效接管并执行必要的转向操作。
图22 丰田One Motion Grip线控转向系统
05 总结
线控技术在底盘上各子系统的应用成熟度和渗透率存在很大差异。
线控驱动/油门技术已相对成熟并广泛应用。
线控制动技术中的EHB的One-box方案也趋于成熟,预计到2025年one-box在EHB搭载量中的占比将达到90%。而适用于高级别自动驾驶的EMB产品还未见大批量量产产品,因此也称为国内外企业竞相布局的热门领域。
线控转向领域的EPS已达到98.71%的前装搭载率,随着底盘智能化需求的驱动和政策端的刺激,SBW的普及速度正在加快。在线控转向技术领域国内部分厂商已经有一定的积累。
编辑推荐
最新资讯
-
全球首次!IVISTA 2023版修订版引入带灯光
2025-04-28 09:59
-
我国首批5G毫米波行业标准送审稿审查通过
2025-04-28 08:56
-
5/16 厦门- 新能源汽车电驱测试技术的创新
2025-04-28 08:53
-
国内首个汽车电磁防护技术验证体系EMTA正式
2025-04-28 08:49
-
一文带你了解滤波器
2025-04-28 08:35