林晓斌博士:车辆一体化耐久性可靠性工程
林晓斌博士《车辆一体化耐久性可靠性工程》主题报告。报告内容包括如何建立整车和零部件耐久性可靠性目标、如何进行耐久性可靠性实验、如何在设计阶段使用有效的虚拟仿真技术、加快产品开发等,以及针对新能源车辆以及新能源车辆的耐久性及可靠性问题提出一些思路和案例。
报告分为以下6个部分:
· 车辆耐久性可靠性工作流程
· 用户载荷环境及使用表征
· 耐久性可靠性目标建立
· 疲劳耐久性预测和可靠性分析
· 数值预测和实际结果关联
· 耐久性可靠性试验验证
1、车辆耐久性可靠性工作流程
汽车行业的竞争近年来达到了一个新的高度,制造商如何在短时间内以有限的资源开发出符合用户要求的耐久性可靠性的产品,是必须面对的一个重大挑战。
疲劳耐久性/可靠性主要解决动态载荷所引起的结构零部件或电子元器件的疲劳失效问题。
典型的车辆(疲劳)耐久性工作流程主要有两方面,一是基于试验的车辆疲劳耐久分析,二是基于虚拟模型的车辆疲劳耐久分析,两者之间既有联系又有区分。
产品整体开发过程的可靠性步骤分为:概念、设计、开发、测试、生产及支持。
概念阶段:明确可靠性的要求,根据量化的载荷环境和用户使用习惯为可靠性目标制定符合要求的测试方法和标准。
设计阶段:估计每个零部件和整车系统的失效模式和风险,鉴别零部件的设计缺陷,提高部件的可靠度。
开发阶段:通过可靠性预测及系统建模模拟零部件失效机理,提出可靠性改进计划。
测试阶段:根据可靠性测试结果建立系统模型,失效分析,设计评审、改进及可靠性预测。
生产阶段:生产领域的可靠性控制包括PFMEA与控制计划、初始生产单元验证测试及Burn-in试验等。
支持阶段:用户使用支持通过故障报告和根本原因分析等进行产品可靠性监控。
2、用户载荷环境及使用表征
车辆的耐久性/可靠性和载荷环境(路面、载重、气候等)紧密相关,很多零部件的寿命也和车辆的驾驶(使用)方式相关,主要载荷包括:力/力矩,压力,加速度,温度,湿度,电压等。
耐久性/可靠性设计目标必须包含车辆在役载荷环境,没有指定载荷环境的车辆使用寿命是不确定的。整车、系统、组件、零部件等都有各自的关键载荷,通常也需要设定不同的设计目标。
(1)车辆载荷获取方式
车辆载荷必须要通过大量的用户使用数据和用户载荷分析,然后进行统计得出。主要包括以下载荷信息:
· 直接测试车辆系统的载荷和环境信息
· 监控测量典型用户车辆的载荷信息
· 实测和虚拟模拟相结合得到各系统或零部件的载荷
· 完全虚拟模拟路面及车辆典型行驶
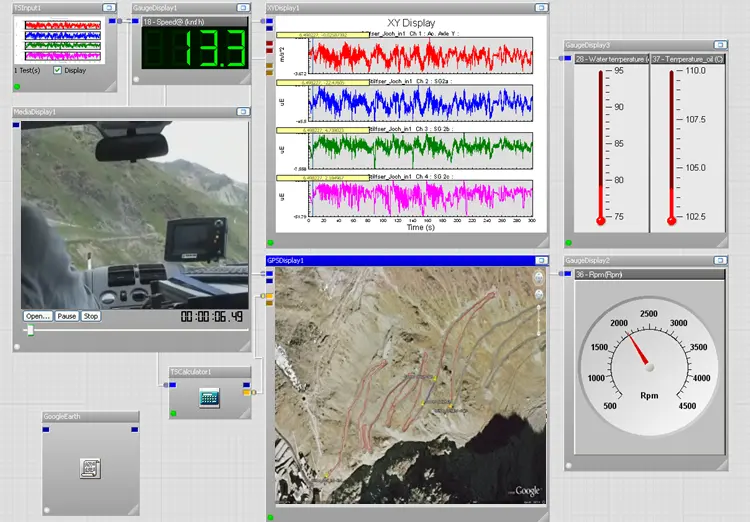
(2)车辆使用信息获取方式
· 用户调查
· 监控测量典型用户车辆的使用信息
(3)影响车辆寿命的主要因素
· 行驶里程
· 车辆载重
· 行驶路线(路面等级、不平度、坡度、弯道)
· 行驶车速
· 典型工况(制动、转向)
GPS大数据综合分析案例:对GPS数据进行综合分析,输出显示全部轨迹、时间、里程、车速、侧向加速度、纵向加速度、方向角等统计量,以及相关量的统计分布。
3、耐久性可靠性目标建立
耐久性可靠性目标建立方法如下:
定义可靠性目标:在规定条件和规定时间内产品可能完成规定功能(可靠的/存活),可能完不成规定功能(不可靠的/失效)。
选取可靠性度量:产品在规定条件,规定时间内,完成规定功能的概率。
建立用户分布模型:根据用户载荷数据进行综合分布,建立用户的分布模型。
获取指定严酷度下的设计目标:根据给定条件,获取耐久性可靠性的设计目标值。
可靠性目标建立流程:根据各个用户的损伤数据(结构件)或扭矩谱数据(传动系统),应用nCode软件进行仿真分析,求取相应部件可靠性的设计目标值。
4、疲劳耐久性预测和可靠性分析
(1)疲劳失效及预测
疲劳寿命预测可以很大程度上改进优化车辆结构和零部件的耐久性和可靠性,并帮助进行耐久性试验验证的简化和加速,是现代车辆设计必不可少的一个关键技术,可以指导提高产品的可靠性。
疲劳是车辆耐久性/可靠性中最主要的失效模式,据统计,疲劳失效占结构失效的50-90%。疲劳是由于载荷变化所引起,一般包含裂纹萌生和随后的裂纹扩展两个过程,循环塑性变形是金属产生疲劳的主要原因。
典型的疲劳分析技术如下:
金属结构和零部件的疲劳寿命可以基于小试样中获得的疲劳性能曲线,结合材料中的应力或应变变化进行预测。例如焊缝疲劳分析和白车身焊点疲劳分析是从关键位置的测试数据(如应变)预测寿命。
(2)可靠性分析
可靠性分析主要是针对一些实验失效的数据来建立模型,模型可以进行可靠性分配,识别计算测试对象的最弱点,可以加速测试对象的可靠性分析。
5、数值预测和实际结果关联
比较虚拟分析和真实试验结果的符合程度,可以验证虚拟分析的可信度,为改进虚拟分析提供直接的数据,同时也为制定设计阶段的虚拟验证规范提供基础,充分发挥虚拟分析在产品开发中的作用。
可靠性数值预测和试验结果常用的关联包括:载荷关联、振动关联、应变关联、疲劳失效位置关联、疲劳失效寿命关联等。
6、耐久性可靠性试验验证
耐久性/可靠性试验是车辆研发中非常重要的一环,直接关系到最终产品的耐久性和可靠性。试验设计和验证方法至关重要,既要符合系统的加载条件及设定的耐久性可靠性目标,又需要对试验进行合理的简化和加速。
典型的试验有设计验证和产品验证,适用于不同的研发阶段。对于疲劳耐久性试验,通常可以使用疲劳损伤慨念,对试验进行简化和加速;而对于非疲劳可靠性试验,可通过可靠性理论中的ALT(加速寿命)试验技术,实现试验加速。
典型试验类型包括:等幅疲劳试验、多级谱(块谱)疲劳试验、单轴或多轴变幅时域模拟试验、频域振动台疲劳试验、传动系试验、高低温试验、盐雾试验、多“应力”复合试验等。
nCode软件在耐久性可靠性试验验证中的应用案例包括:副车架试验载荷简化、电池包试验标准开发及传动系统台架试验标准开发等。
总而言之,汽车可靠性和耐久性设计、开发和验证,不仅关系到汽车企业的生存和发展,也关系到消费者的利益和安全。在未来的汽车制造和设计中,需要更加注重汽车质量、可靠性和耐久性的提高,以适应不断发展的市场需求和消费者要求。
2024年10月19-20日,林博士专题培训课,详情点击下方图片链接
延伸阅读
- 下一篇:主动横向稳定杆,听听“孔辉”说悬架...
- 上一篇:中汽中心与华为签署战略合作协议
最新资讯
-
欧洲欲禁碳纤维
2025-04-16 15:47
-
模糊测试究竟在干什么
2025-04-16 15:23
-
越野车辆动力学 —— 越野车辆的平顺性
2025-04-16 14:50
-
Euro 7排放:欧盟委员会匆忙发布轻型车的实
2025-04-16 13:29
-
Applus+ IDIADA宣布采用全频谱碳纤维座舱用
2025-04-16 13:27