简单介绍动力电池箱体的CAE仿真技术
CAE软件的主体是有限元分析(Finite Element Analysis)软件,有限元方法的基本思路是把结构离散化,用有限个容易分析的单元表示复杂对象,单元之间通过有限个节点相互连接,根据变形协调条件综合求解。由于单元数目是有限的,节点数量也是有限的,所以 称为有限元法。该方法灵活性较大,改变单元的数量可以使解得精确度改变,得到与真实情况无限接近的解。有人估算过CAE各阶段花费的时间:模型的建立和数据输入在~45%左右,结果分析和评定大约50%左右,而真正的计算时间大约占据5%左右。
采用CAD工具建立CAE的几何模型和物理模型,完成分析数据的输入,称之为CAE前处理。前处理模块主要用于给实体建模以及参数化建模,构建的布尔运算、单元自动剖分、节点编号与节点参数生成、载荷与材料参数直接输入有公式参数化导入、节点载荷自动生成、模型信息自动生成等。
之后就是有限元分析,对有限元模型进行单元特性分析、有限元单元组装、有限元系统求解和有限元结果生成。有限元分析模块包含有限元库,材料库和相关算法,约束处理算法,有限元系统组装模块,静力、动力、振动、线性和非线性解法库。通过分解成子问题,用不同的有限元分析子系统完成分析。子系统包括线性静力分析子系统、动力分析子系统、震动模态分析子系统、热分析子系统等等。
同样,CAE结果也需要 CAD技术生成图形输出,例如位移图、应力、温度、压力分布的等值线图形,表示应力、温度、压力分布的彩色明暗图,以及随着机械载荷和温度载荷变化生成位移、应力、温度、压力分布的动态显示图。后处理模块包括数据平滑,个物理层的加工和现实,针对工程或产品设计要求的数据检验和规范校核,设计优化与模型修改等,这些都可以看作是CAE后处理。
下图是一般的CAE分析流程
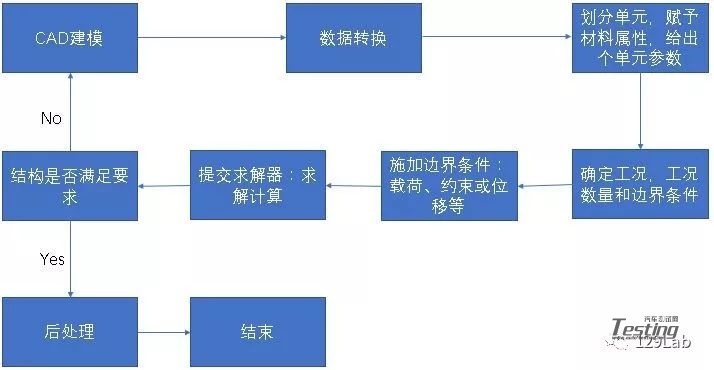
电池包结构的CAE分析一般有模态分析、静态分析、动态分析、疲劳分析等。其中电池箱的CAE分析一般包括:
1、 建立仿真模型
a) 定义材料属性。根据电池箱材料确定相关材料参数:密度、弹性模量、泊松比、强度极限等。进行静力学强度、刚度及模态分析,采用线性弹性材料仿真时,一般要输入材料的弹性模量、密度和泊松比,进行轴向振动冲击仿真时,一般是材料的非线性,采用应力-应变曲线定义材料模型
b) 划分网格。例如采用Hypermesh对电池箱进行数模处理和网格划分。一般需要按照质量要求划分网格,使其单元长宽比尽量接近1。同时处理好网格扭曲,例如,四边形尽量接近正方形,如果扭曲避免,可采用细化网格减轻扭曲程度。翘曲问题可以采用翘曲条件和映射网格消除,不可避免时,也采用细化网格减轻翘曲。电池箱各部件的网格需要进行交叉穿透检查, 重负调整直到合格
c) 定义相互作用、边界条件、施加载荷。定义各部件之间的焊接、螺栓连接和多轴向振动冲击仿真时模块与电池箱的接触。边界条件主要模拟电池箱和车体的连接,将螺栓连接孔的自由度全部约束
2、 仿真分析
a) 静强度分析。电池箱不直接承受工作载荷,汽车在不平整路面行驶时,电池模块晃动产生的惯性冲击力作用于电池箱内壁,进行有限元仿真时,把模块的冲击载荷通过动载荷系数等效为静载荷,均匀施加在电池箱内壁。载荷工况分为:颠簸行驶并转弯:根据汽车转弯常见的加速度和路面不平产生的加速度来确定作用在侧壁的载荷。颠簸行驶和刹车的载荷加载类似,但是此时载荷作用在另一侧侧壁。
b) 刚度分析。主要考虑的工况为扭转和弯曲。当电池箱结构跨度较大时,容易产生形变。通过应力云图得出在扭转或玩去载荷作用下,可以得到电池箱结构容易产生破坏的地方。
c) 模态分析。通过在底部添加质量点来模拟电池模块的质量分布。模态分析目的是为了得到电池箱结构的固有频率,如果结构固有频率与定频振动测试的频率接近,则需要对结构改进,改变其固有频率,避免共振。
d) 多轴向振动冲击仿真。定频振动时:包括上下、左右、前后,需要分别施加三个方向的载荷模拟试验台对电池箱施加的激励。把随着时间变化的加速度转化为相应的位移来施加振动载荷,振动载荷加在拖脚处,即给拖脚部分施加一个随着时间变化的强迫位移;扫频振动时:按照试验条件事假载荷。
e) 疲劳分析。这需要整车CAE分析结果和实验数据、电池箱材料的S-N(应力-寿命曲线)、材料的疲劳极限图、有效应力集中因数、尺寸因数和表面质量因数等参数。如果没有足够的实验参数支持,可以对电池箱结构进行虚拟工况下的疲劳分析,即假设电池箱在真实约束状况下受正弦交变载荷作用,分析此时的电池箱疲劳寿命。
f) 碰撞性能。电池箱碰撞性能也需要整车碰撞数据支持,或者根据经验值分析。
今天先介绍到这里,后面针对每一个方面还需要具体展开。
最新资讯
-
组分性能对锂离子电池卷芯挤压力学响应的影
2025-04-30 09:00
-
美国发布自动驾驶新框架,放宽报告要求+扩
2025-04-30 08:59
-
中国汽研联合清华大学牵头编制的《乘用车避
2025-04-30 08:53
-
2025年汽车标准化工作要点
2025-04-30 08:51
-
关于Audio Precision音频分析仪产品价格稳
2025-04-30 08:51