简单分析电动汽车振动噪音问题的电机“本体解”(一)
为什么电动汽车电机振动噪音问题会突出?
电机都有振动噪音隐患, 但电驱动电机更加突出。这一方面是因为要求更严格了,因为电机的振动很容易通过传递引起减速器、车架等部件的二次振动和耦合振动;另一方面电动汽车应用的工况特点也对电机产生了较大的约束,这些约束会恶化振动噪音问题 。比如说高磁密问题和集中绕组问题。
电驱动电机的在性能上追求高功率密度、高转矩密度,在经济上又强调低成本。这导致了设计气隙逐步减小,气隙磁密逐步提高。最终高磁密的问题会反映到电机的噪音和振动水平上。
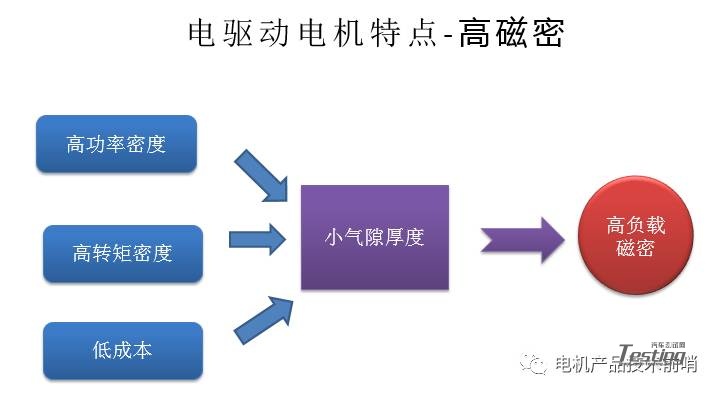
最近几年在低速车微型车领域,出现了许多集中绕组式的电机。集中绕组就是近槽极比配合,绕组跨距为1的电机。这种设计一方面是因为绕组端部小,能减少用铜量,另一方面是为了迎合大规模自动化生产的需要,集中绕组能够直接自动绕线,生产效率极高。但集中绕组却带来了很大的振动噪音挑战。这是因为集中绕组的分数槽结构,产生了大量低阶齿谐波,这些谐波容易和基波相互配对产生低空间次数的电磁力波。而低空间次数电磁力容易在机壳和定子上激励出较大的振动响应,并伴随作噪音问题。
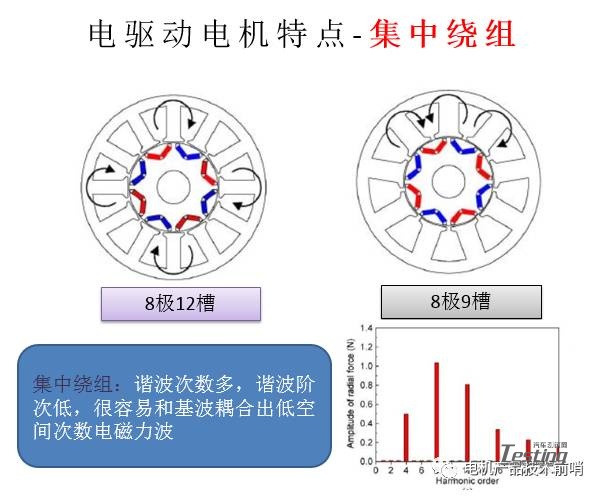
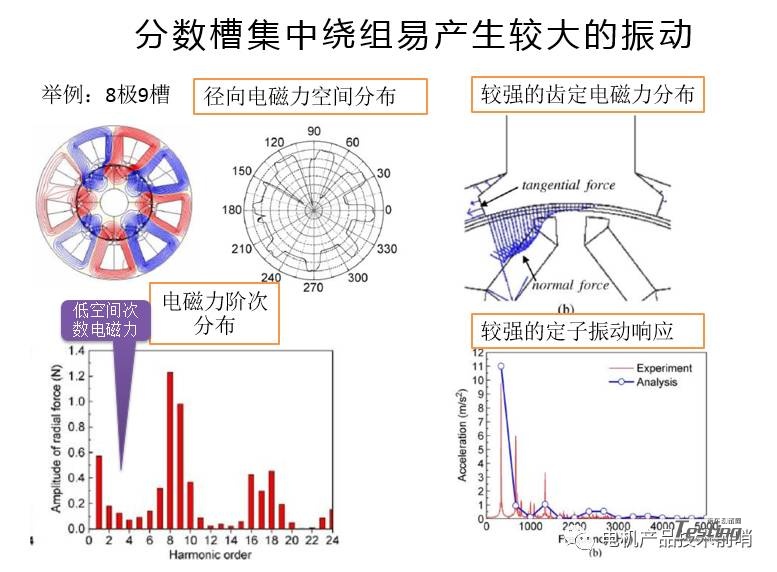
随着对续航里程的要求提高,电动汽车的轻量化趋势明显,一方面电机本体的机壳和定子的厚度再降低,另一方面减速器、车桥、车架的质量也在下降。这导致了无论是本体还是系统的刚度都在下降,相同的电磁力激励会产生更大的振动响应,还可能会引起更大的噪音。
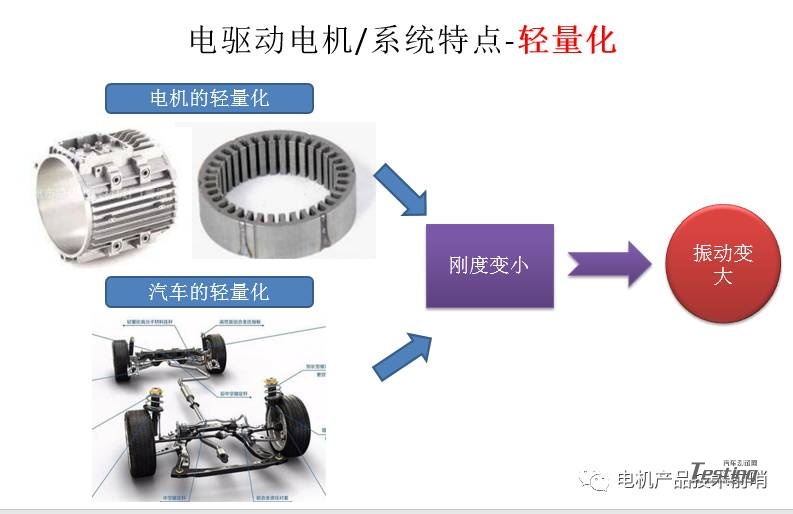
如何分析振动噪音问题?
欲解决振动噪音问题,必先解决如何分析问题。这里就有很多方法和流派,总的来说可以归纳为:自上而下和自下而上两种方法。
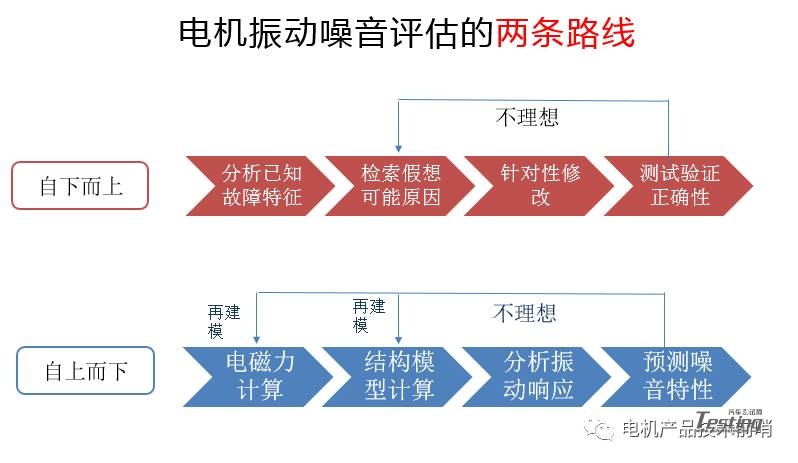
自下而上是经验派的主要工作方法,解决的套路和破案差不多,先到案发现场收集证据,然后分析可能的嫌疑对象,针对嫌疑对象进行调查,然后给出假设逻辑链和证据链。一旦锁定了目标,就做出针对性的修改,重新做一台电机来检验假想是否正确,如果正确了,问题解决,否则推倒重来。
自上而下是学院派的主要工作方法,学院派相信理论,相信方法论,在设计时就通过模型技术分析出了可能的故障特征,如果有问题及时更改设计。如果实测时发现了未预料到的故障特征,也会通过改善模型精度和计算方法来逐步逼近问题。
在实际工作中,我们应该做集大成者,这两种方法要结合起来用,相互配合,从长远来看,应该以学院派为主,经验派为辅助。下面我着重介绍 自上而下的分析过程:
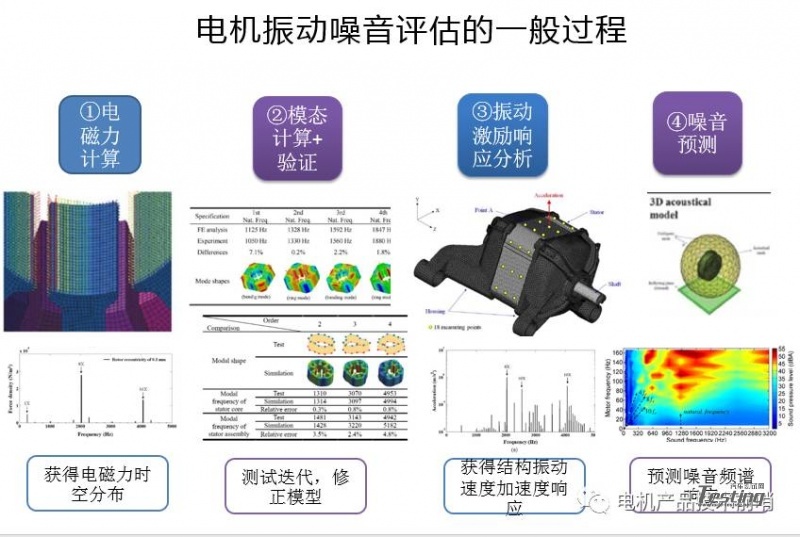
第一步:电磁力计算,一般需要计算出两类电磁力。一类是定子齿顶上每个单元的电磁力,以便后续的结构分析用,这是一种实时的分布力。另外一种是气隙中的电磁力波,即电磁力的波函数,它是用来分析电磁力可能产生的原因。简单的说:前面一种电磁力是用来模型计算用,后面一种电磁力是用来逆向分析用,它们是源同而表达方式不同。
第二步:模态计算和验证。模态计算的精度受约束条件、浸漆、绕组等因素的制约,不太容易一次获得精确解。因此需要通过实际检测的结果来修正各种约束和阻尼的设置。模态的实测方法一般为锤击法。模态分析即是为了修正模型,又可以用来预测共振的风险。
第三步: 振动响应分析,计算第一步的电磁力施加在第二步的模型上,机壳、定子的瞬态响应。获得关注点的加速度和速度振动的幅值和相位。
第四步:噪音分析和预测,通过声学分析软件,计算球面噪音的频率分布和分贝。
如何解决振动噪音问题?
关于这一点,各家都有各家的手段。有的侧重通过工艺来解决问题, 有的侧重电机本体设计,有的侧重从控制器角度来解决问题,更有集大成者 采用综合性策略。
从工艺路线解决,是一种被动解决方案。常用的手段是,改善浸漆质量比如通过二次浸漆提高挂漆量和浸透深度。类似的方法还有改善铁芯叠压质量,降低齿定的弹片量、改善绕组端部长度和绑扎质量等等。这些手段的本质是提高结构系统的刚度和阻尼,从而减弱振动的幅值。
从本体设计路线解决,是一种本质性解决方案,主要的思想是从振动发生的源头出发,能减弱电磁力就减弱电磁力,减弱不了就让问题电磁力的频率避开结构体的固有频率。相应的手段有槽极比选择,它可以明显改变电磁力的频率分布;提高气隙均匀度,能控制电磁力成分,不均匀的气隙会导致额外的谐波并产生额外的电磁力。除此之外还有许多方法,不一一例举。
控制路线解决,在电机本体问题无法排除的情况下,还可以发挥控制器的主观能动性,硬件不行就软件补。常用的方法是谐波管理。它可以从正反两面来解决问题,举个例子:如果已经明确分析出5次电枢谐波是导致振动噪音的主要源头,那么控制时就对5次谐波作单独抑制,从而减弱噪音。如果反过来发现主要噪音是1阶齿谐波引起的,而5次电枢谐波刚好能够抵消掉1阶齿谐波产生的电磁力,那么我们就主动注入5次电枢谐波,就好比以毒攻毒。在国外,从控制侧解决振动噪音问题成为研究热点,因为这种方法机动灵活,不需要增加成本。
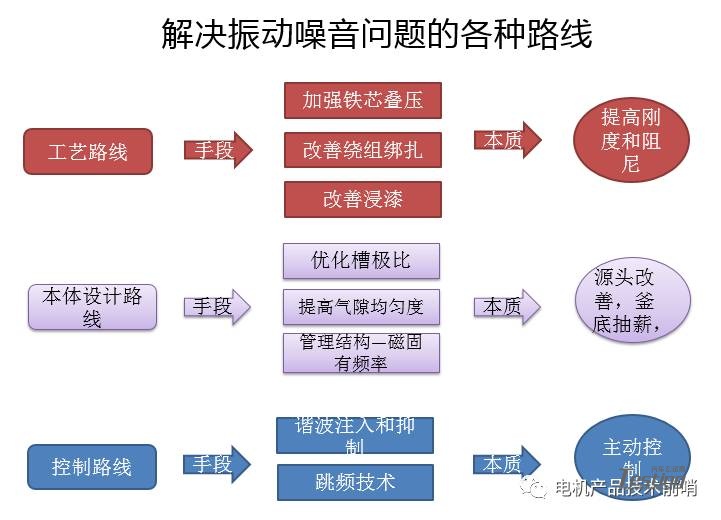
下面我先举三个 国外学者从电机本体解决问题的方法,以便打开思路,启发灵感。
第一个例子是针对集中绕组的齿槽谐波引起的噪音的。有人对定子齿作了如下图的修形处理,将圆弧面修成平面。并以齿顶宽和齿顶高作为可变参数,作了参数化计算。最后优化的结果是能将电机的振动降低7%。
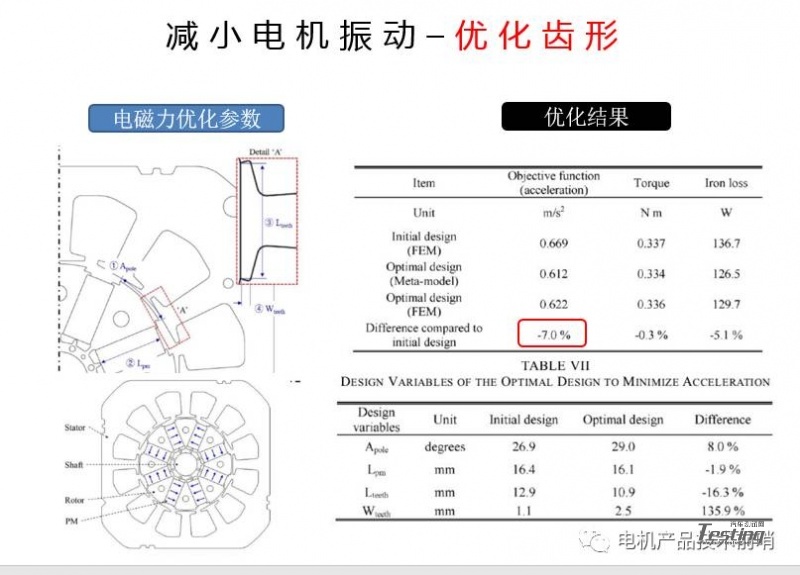
第二个例子是关于扭振和斜极的。这位前辈第一款电机将转子分成两段,两段间斜了半个槽。这样达到了降低转矩脉动,车辆在启动过程中更平稳,但发现电机在3000-4000HZ的噪音特别大。问题出在扭转共振上,该电机定子的第三阶扭转模态频率在3725HZ,振形为上下反向拉伸,上下的相位刚好相反。而两段式斜极导致上下两段的齿槽转矩相位也是相反的。这样就和振型就高度一致 了,在某个转速下必然导致扭转共振现象。解决的方法就是改进斜极方式,如下图两种新的斜极方式,实测下来噪音改善效果都很明显。
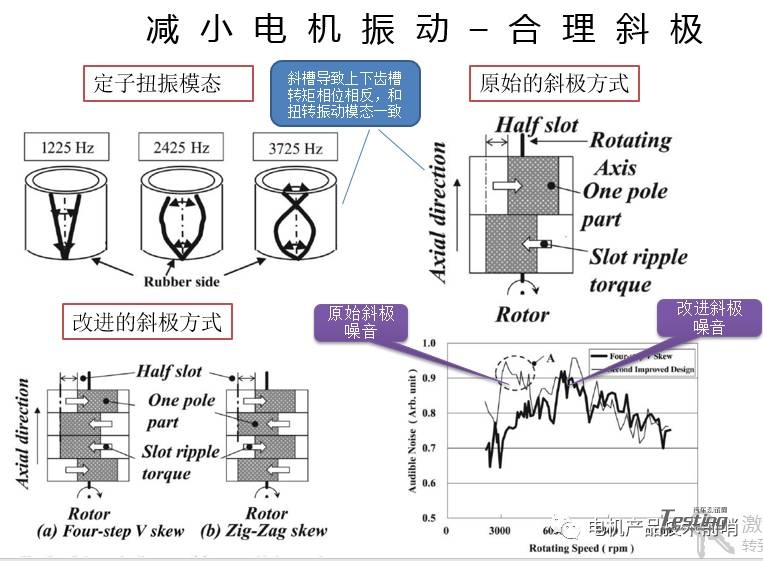
第三个例子 利用转子不对称修形和复合达到类似斜极的效果。如下图所示,有两种转子冲片,A冲片左极弧小于右极弧,B冲片则刚好相反。两种冲片通过A-B-A的方式复合成一个转子,实测后效果很好。不但明显降低了1000-2000HZ噪音,齿槽转矩也有相当比例的下降。
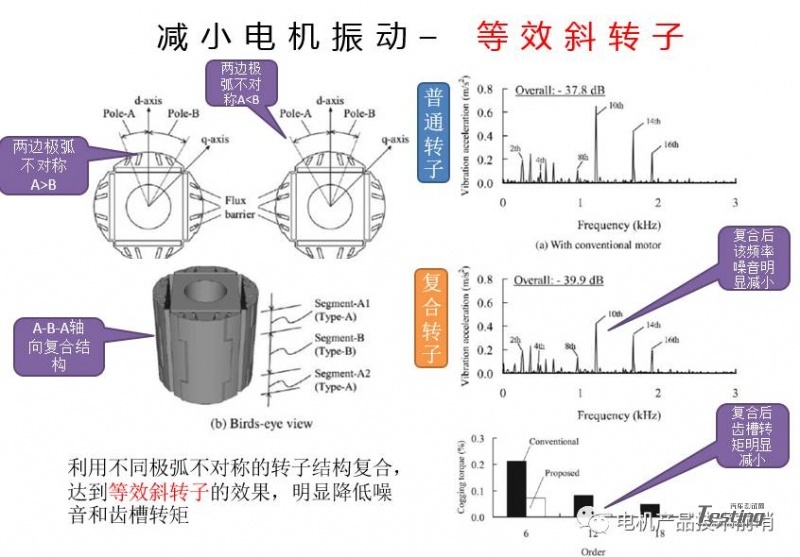
再举两个通过控制侧解决噪音问题的方法:
第一种方法是利用双控制器,降低高频电磁噪音。如下图所示,通过双控制器能明显抑制电机电流的PWM谐波。达到降噪的效果。
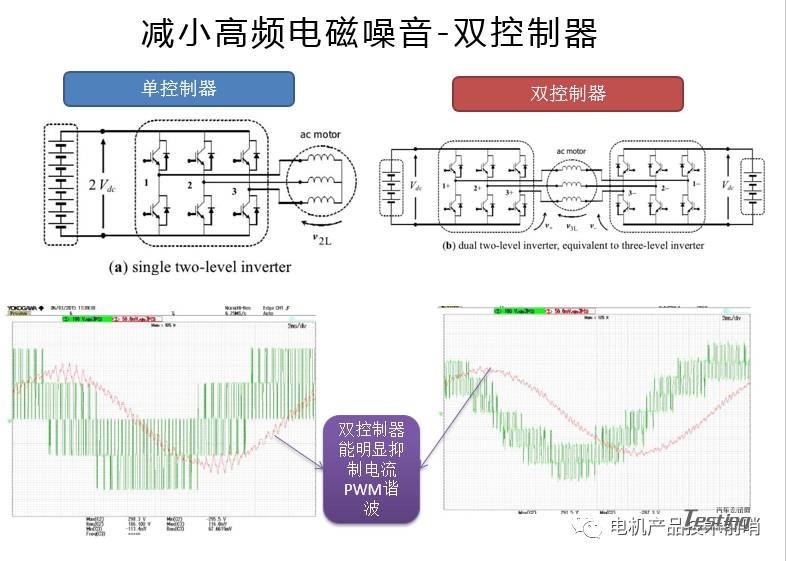
另外一种观点思路比较新颖,有位前辈发现电机的主要振动模态是4阶,而引起该阶振动的电磁力,受交直轴电流影响非常大。他作了仿真和试验,发现不但电动状态和发电状态振动不一致,即便在电动状态的第二相限(Id为负,Iq为正),不同的Id和Iq分配,振动大小也不一样。因此他提出一种观点,就是在电机和控制器耦合设计时,应以优化电磁力为目标,优化电机参数和控制策略,使得电流分配达到最佳噪音效果。但目前还没有看到实际的产品应用。
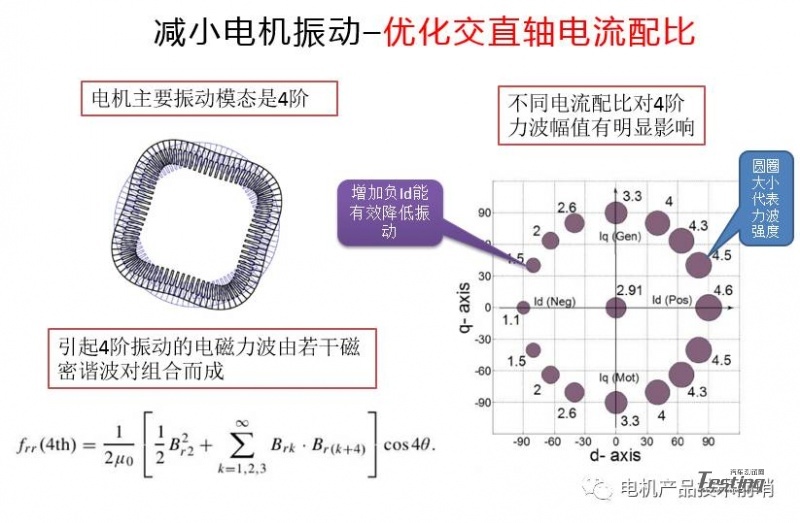
结论
本周我们讨论了三个问题,第一个为什么电动汽车的电机的振动噪音问题突出,这是和轻量化、高密度化、低成本化的需求相关的。第二讨论了分析振噪问题的套路,有自下而上和自上而下两种流派。其中自上而下的分析过程又分成了四步,分别是电磁力分析、模态分析、振动分析、噪音预测。第三讨论了解决振动噪音问题的一系列方法,可以从工艺出发也可以从设计出发,比较新颖的是从控制出发。希望对你有所启发。
最新资讯
-
风噪测试在电动汽车时代的关键作用
2025-04-29 11:34
-
汉航车辆性能测试系列之操纵稳定性测试--汉
2025-04-29 11:09
-
新能源汽车热管理系统验证体系PITMS正式发
2025-04-29 11:09
-
试验载荷谱采集
2025-04-29 11:07
-
APx500 软件演示模式 (Demo Mode) 竟有这些
2025-04-29 08:37