解析差速器半轴齿断齿因素与结构改进
1. 某半轴齿制造工艺与失效形式
某差速器半轴齿轮结构设计如图1所示,该齿轮零件通过“下料→磨外圆→车锥度→加热→温锻→正火处理→抛丸处理→磷化/皂化处理→冷校→钻孔→粗车背锥→切边→精车背锥→精车内孔端面倒角→拉花键→渗碳淬火→抛丸处理→精车轴颈平面→产品终验→清洗涂油→包装”工艺制造生产。该半轴齿轮材料为20CrMnTiH,符合GB/T 5216—2004标准,其化学成分如表1所示。
通过上述工艺生产出的半轴齿轮如图2a所示,将其交予用户使用后,用户反馈有部分齿轮出现失效,其中较典型的失效齿轮见图2b、图2c所示。从图2b、图2c中可以判断该失效形式为断齿失效,是齿轮最严重的失效形式,失效后差速器不能实现差速,容易发生事故造成人员伤害。
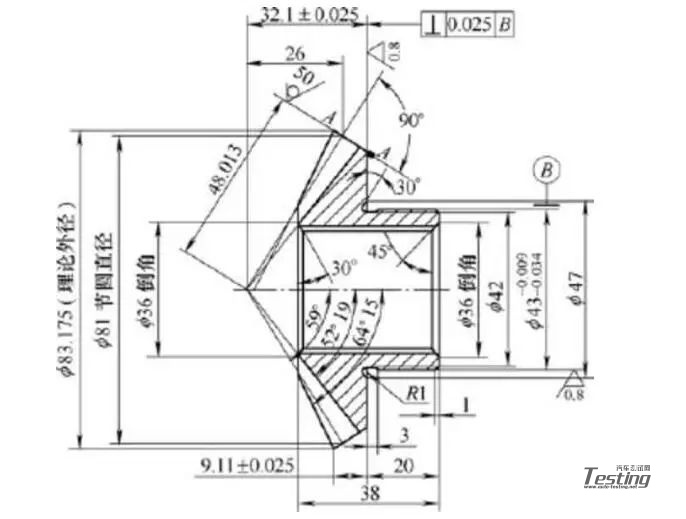
图1 半轴齿轮零件图
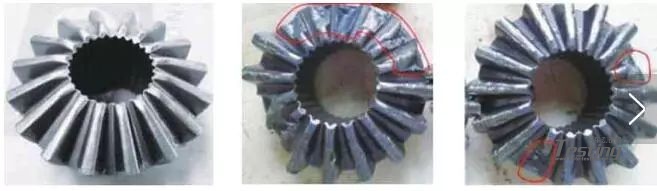
图2 半轴齿轮实物图
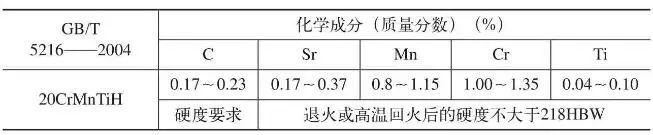
表1 齿轮材料化学成分表
2. 失效原因分析
(1)金相分析。
本文对失效齿轮进行了热处理效果检测,数据如表2所示,该齿轮热处理符合产品技术要求。
为了准确判断断齿原因,本文还对端口进行了金相观察,如图3所示,从图3a、图3b中可以看出,该断口未见疲劳破坏。轮齿断口无宏观可见的塑性变形,放射区占断口的很大部分,微观主要为沿解理面的穿晶断裂,在图3c中可以判断出断口形貌为准解理+撕裂。上述分析表明,该齿轮未见疲劳断裂特征,为一次性断裂,断齿不是因为疲劳强度不足而断齿,无初始裂纹,齿面没有折叠,从而可以判断断齿是因为过载造成的,即齿轮强度不足造成断齿。
(2)故障再现实验及强度校核。
在分析了制造过程与半轴齿轮强度有关的数据都合理的情况下,本文通过故障再现的结果进行分析计算,验证设计强度是否满足相关要求。
驱动桥总成静扭实验的后备系数Kk=2.21;满足QC/T 534—1999驱动桥总成静扭强度后备系数Kk>1.8;实验结果为半轴齿轮断裂,而非半轴。根据驱动桥设计原则,驱动桥传动系统中的薄弱环节应是半轴。实验结果显示半轴齿轮破坏时候的输入转矩1 670N·m,此时差速器壳的转矩为1 670×38/9=7 051.11(N·m),半轴齿轮承受的转矩为7 051.11/2=3 525.56(N·m)。根据设计经验普通的圆锥行星齿轮式差速器的转矩分配系数ε=0.55~0.6,取ε=0.6,则半轴齿轮实际能承受最大转矩为754×38/9×0.6=1 910.33(N·m),那么半轴齿轮的后备系数为3 525.56/1 910.33=1.85。查阅汽车行业标准QC/T 29108—1993,汽车驱动桥差速器行星、半轴齿轮质量分等要求合格品、一等品强度储备系数应≥2.5,因此,可得出造成半轴齿轮强度不足的根本原因在于设计强度不足。
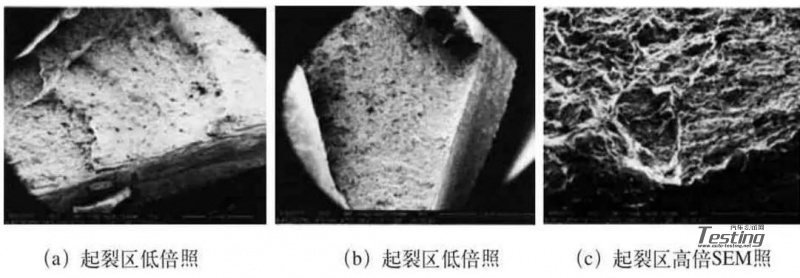
图3 齿轮断口微观组织图

表2 失效齿轮热处理状态检测数据
(3)结构改进及有限元分析。
按驱动桥设计原则最薄弱的部件为半轴,根据与该齿轮相配合的半轴的静扭实验破坏的最大转矩后备系数2.63,那么更改结构后的半轴齿轮的后备系数至少要大于2.63,为了保证齿轮强度后备系数有一定的富余量,因此设计优化时半轴齿轮强度后备系数取K=3,半轴齿轮承受转矩为2 387.676×3=7 162(N·m),此时行星齿轮承受的转矩为7 162×25/40=4 476.25(N·m)。半轴齿轮有限元分析承受的转矩为7 162N·m时,最大应力<980MPa。
本文采用ANSYS分析了半轴齿轮的受力情况,其结果如图4所示,其有限元分析得到的应力集中点和故障件的破坏点位置相同。结合图5所示啮合区位置模拟示意图和红丹粉检测图可以看出,应力集中点和啮合区处于同一区域,导致齿轮承载能力差。
为了提高齿轮强度,本文对齿轮结构进行了改进,如图6所示,在轮齿上下端增加了加强筋结构,并取图6中所示X、Y为控制尺寸,其有限元分析结果如图7所示。
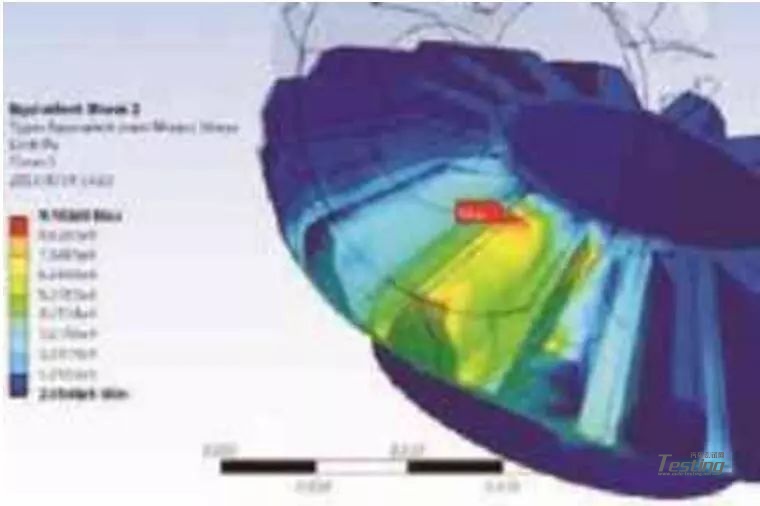
图4 半轴齿轮有限元分析结果
当小端加强筋直径X<44.2mm,大端加强筋厚度Y>14.1mm时,应力点集中在大端齿顶和小端平面与面锥相交处;当小端加强筋直径X=44.2mm、Y=14.1mm时,小端平面与面锥相交处(故障件破坏点)的应力点消失,只存在大端齿顶处的应力点,此时半轴齿轮承受的转矩值为7 162N·m(按设计优化设定的目标加载的转矩),这时的最大应力点的应力值为592.9MPa,小于980MPa,有一定的强度富余量,为了保证强度有足够的富余、便于加工,在材料尽量少的情况下,X取(44.4±0.1)mm, Y取(13.9±0.1)mm。
(4)改进后的齿轮效果验证。改进后的齿轮产品如图8所示,经用户使用后,在服役期内未出现轮齿断裂失效现象,产品达到用户使用要求。
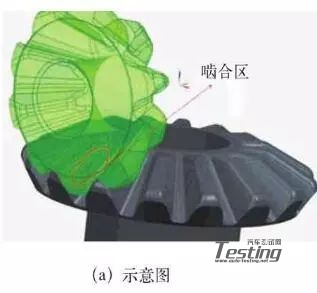
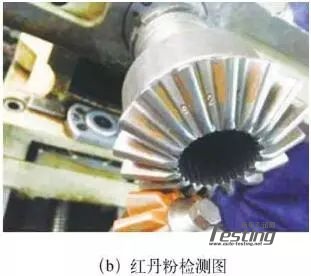
图5 啮合区示意图和红丹检测图
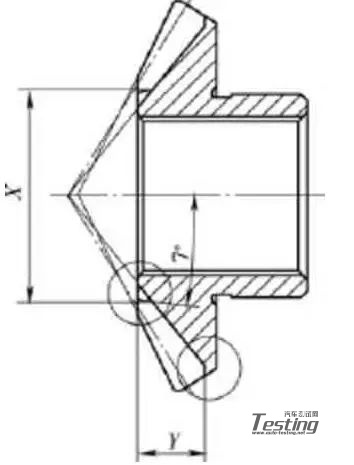
图6 齿轮改进后齿轮零件
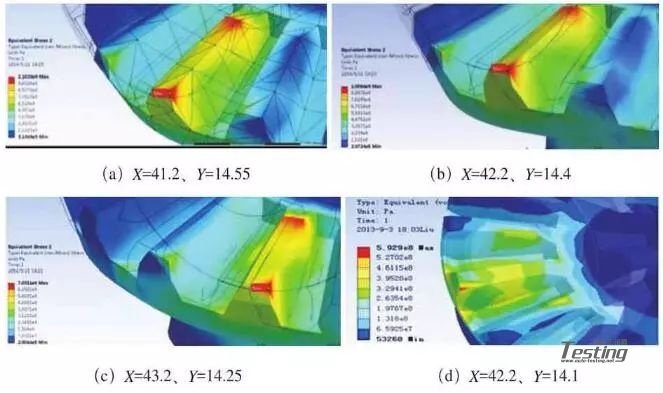
图7 不同参数齿轮有限元分析结果
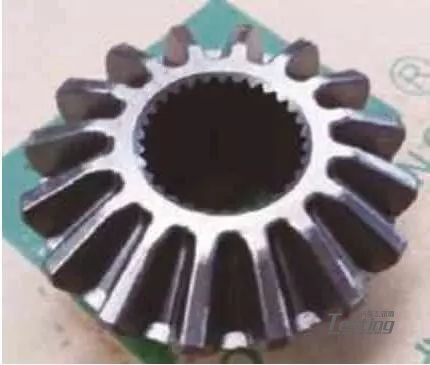
图8 改进后的齿轮实物图
3. 总结
(1)建立仿真模型,设定变量,将模型通过有限元分析,分析得到结果与实验结果基本一致,用于开发新产品时,作强度理论分析,可缩短开发时间,减少实验浪费,提高一次开发成功率。
(2)采用有限元分析验证齿轮设计,能有效地保证半轴齿轮设计强度,避免了变速器因此而产生故障,为今后正确设计、制造汽车变速器具有重要意义。
- 下一篇:MTS 车辆悬挂系统试验解决方案
- 上一篇:简单分析变速器静态换档力影响因素与改善
最新资讯
-
欧洲欲禁碳纤维
2025-04-16 15:47
-
模糊测试究竟在干什么
2025-04-16 15:23
-
越野车辆动力学 —— 越野车辆的平顺性
2025-04-16 14:50
-
Euro 7排放:欧盟委员会匆忙发布轻型车的实
2025-04-16 13:29
-
Applus+ IDIADA宣布采用全频谱碳纤维座舱用
2025-04-16 13:27