简单分析发动机冷试技术优势与经典案例
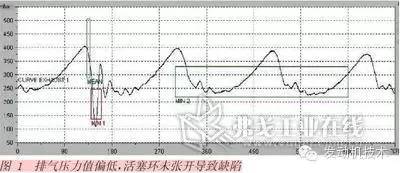
随着相关测试技术的不断进步以及计算机处理能力的迅速提高,目前越来越多的汽车生产厂家开始采用节拍较快、质量检测水平较高及生产成本较低的发动机冷试来进行发动机下线时的高精度检测,以更好地确保产品质量。作为新型的发动机测试技术,冷试通过其独有的测试原理及相关的高精度优势,在发动机质量检测方面迅速占据了整个汽车行业发动机测试的半壁江山。
发动机冷试试验原理
发动机冷试是用来检测内燃机装配质量的一种方法。当采用此技术检测发动机时,发动机不需要燃料来运行,也不需要冷却液进行冷却。被测试的发动机进入测试台,通过气缸或液压缸夹紧发动机的进气、排气口,同时通过专用机油压力适配器连接到设备上,用抱爪或其他夹紧机构自动夹紧发动机的飞轮或适配器,测试台的伺服电动机驱动发动机以不同的速度旋转,与此同时,测试系统通过数据采集卡同时从发动机进气口、出气口和夹紧机构的转矩传感器以及主油道出口的压力传感器上采集测试数据,数据通过测试台专用软件进行分析,然后将分析结果与测试台已设定好的极限值进行比较,从而确定发动机是否被正确装配。另外,设备通过测试程序对发动机上相关传感器发送执行操作的指令,同时发动机各种传感器及执行器也通过CAN-Line或K-Line将反馈信号反馈给测试台,测试台软件对发动机反馈的各种信息进行一系列的分析比较,最终确定发动机各传感器及执行器是否正常工作。
现代冷试技术的发展
冷试试验中,在非常小的误差内保持曲轴转速是检测缺陷和分析问题精确程度的关键。过去一段时间,由于驱动系统很难克服发动机运行过程中产生的剧烈负载变化,从而不能保持发动机的稳定转速,冷试试验系统检测、定位产品组装缺陷问题的能力因此受到了限制。最近几年来,新型伺服电动机驱动技术的应用降低了速度变化,其中专门为试验台设计的专用驱动系统,其试验台架和测功机应用设计的全数字AC通量矢量驱动器,配备全闭环控制系统精确修正位置,电动机速度和转矩通过一个频率为4kHz的增量编码器反馈。这种新型驱动系统同时还配备了基于测量电动机电流和电压的转矩计算器,它可以超过位置编码器的速率高速探测转矩波动。

更值得一提的是数字电流整流器的应用,它可以10kHz的频率工作,大大提高了驱动电动机的反应速度,使其能够对负载波动在非常短的时间内做出反应,这意味着可将单次发动机运转时的速度波动范围控制在±3%。在此基础上,新型冷试试验台在测量精度上有了较大的飞跃,我们可以更精确地检验气门泄漏、轴承间隙过松或过紧以及活塞环的损坏等项目。
试验开发和产品最初试验数据的确定
发动机的测绘是在冷试试验应用开发中一个关键的环节。所谓测绘,就是在特定驱动速度下检测发动机预期的压力、负载等特征。通常我们需要采取一定数量的发动机样本作为试验基础进行测试并采集相关数据,通过对试验数据的分析来优化测试转速及相关的测量参数,例如:进排气系统、单缸测试或者多缸测试,最大探测灵敏度等。同时,通过发动机测试,我们还可以用来确定产品的可变性特征。
测绘通常需要分为两个部分,即:基线测绘与缺陷特征测绘。其中基线测绘是对一批一定数量的合格的发动机产品进行测绘,以确定试验可行性、产品可变性和检测到的信号质量等因素。缺陷特征反馈是在同样的条件下,对同一批发动机装载缺陷后重新进行检测而获得的。信号采集系统的敏感性限制是根据在逐步缩小缺陷尺寸的同时,其反馈信号变化的衰减程度而确定的。随着伺服电动机驱动系统提供连续稳定的转速,冷试台在辨别不同类型的缺陷特征方面具备了很强的能力。最初试验参数和试验软件算法就是根据这些基本测绘数据库而设定的。
新一代冷试台优越的试验性能
1.对发动机排气系统和气缸的检测
新一代冷试试验台可以非常理想地用来检测、评估发动机进排气系统和气缸的完整性,例如当关闭气门检测泄漏时,某气缸的排气压力可以在发动机部分循环运动过程中进行比较。在首次打开气门后,监测排气压力衰减变化和检查排气门打开的实际角度。通常峰值压力反应了气缸的压缩集成性能,而通过峰值压力的衰减变化过程我们可以确定进气门打开的位置。排气压力平均压力值则可以用来参考确定气门的泄漏情况。同时,如排气门打开角度超过3°~40°范围及排气峰值压力过高,则可验证有一个或两个排气门液压挺杆软或者是存在其他缺陷。再有,如排气压力在气缸压缩行程中升高及出现非常高的开启压力,则说明一个排气门面和阀座有泄漏。凸轮轴每前进一个齿,气门在所有气缸上的开启位置会提前最大达22 °,新型驱动系统精确控制、提供连续稳定的速度能有效避免出现速度波动,这些波动产生的影响可能会掩盖许多缺陷信号,特别是在气缸压缩行程中表现更加明显。
图1所示为某发动机排气压力测试缺陷波形,根据图形的缺陷表现以及相关理论分析,我们检测出活塞环未张开或者存在漏装的缺陷,最终拆检后,确认了活塞环未张开的缺陷。
2. 通过对润滑油道压力、流量,油泵压力、流量和油位控制的监测,冷试试验台可以辨别多种典型的机械方面的缺陷,例如:曲轴轴承和连杆的尺寸配套出现故障,或者连杆瓦及主轴瓦发生漏装及错装。
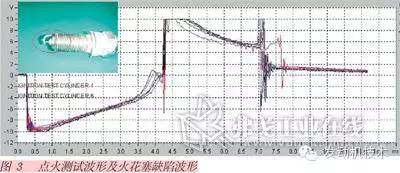
3.对机械缺陷的检测
在热试验中,发动机机油泵在低转速时其效率很低,检测效果不明显;而在高转速时,机油泵上的卸压阀开始起作用,也会对所采集的机油相关信号造成影响,掩盖发动机的部分缺陷信息。而在冷试试验条件下,我们利用不同转速下对机油泵的流量和压力的检测,以及通过对其压力波动值的监测,可以完全避免此类干扰,并更精确地监测出相关缺陷。并且在驱动电动机带动发动机曲轴慢速转动的同时,系统可以在无干扰的条件下采集到高保真信号,这种方式能够实现对机油泵和卸压阀进行高精度的测量。例如:通过发现机油泵压力比正常值过低并且按顺序波动,则可判断曲轴或连杆的轴瓦松动或丢失;如果连杆轴承间隙多出0.01mm,则会检测到在活塞到达上死点前,油道压力有明显的升高。
在发动机整个冷试过程中,设备会有一个监控油压。监控油压主要是为了确保发动机在整个测试循环过程中,机油泵能够持续不断地提供足够充份及足够压力的机油,以保证发动机内部各个相对运动部件之间有足够的润滑,避免因零件故障或装配错误而导致供油不足引起发动机的烧蚀。同时,在发动机起动运转初始阶段,我们必须加入一个步骤以保证机油压力在一个预定的时间内达到一个安全值,这样可以保证发动机有足够的润滑。图2所示为某机型的机油压力测试曲线及两种常见故障缺陷曲线。
4.对点火系统的检测
发动机冷试台控制发动机点火系统工作,并通过传感器感应点火线圈工作过程中周围磁场的变化,间接判断点火系统的好坏。这种测试方法可以检测点火系统中线路的连接、较宽的火花塞间隙以及点火线圈中潜在的问题等多种故障。正常的点火系统工作过程一般都包括充电阶段及放电阶段,通过对充电阶段的电压、充电时间及充电能量的计算,我们可以检测点火线圈内在的故障,而通过放电阶段的放电时间的检测,我们可以检测出火花塞间隙的缺陷、绝缘陶瓷的质量以及装配过程中附着在火花塞表面的杂质情况等。

图3所示为某发动机点火系统测试波形及对应的缺陷火花塞的测试波形图。通过检测,我们发现某个火花塞放电时间过长,怀疑为火花塞间隙过小或者间隙间存在杂质导致放电时间提前,经过拆检我们发现,火花塞电极受到过外部撞击导致间隙过小。
5.燃油轨的测试
图4所示为某机型的某台发动机多次测试,燃油轨的测试曲线叠加图。左侧叠加曲线显示燃油轨首次测试数据与再次重复测试之间,其数据的差异过大,整体离散性过大,缺乏测试结果的一致性,导致在实际生产中难以设定较准确的测试标准,加大了判断发动机故障的难度。
经过分析我们发现,由于零件的长途运输以及我们所需的最低安全库存等缘故,燃油轨从供应商运往公司再到我们正式生产测试,中间需要经历一段比较长的运输与存储等待时间,在此期间,燃油轨运输前所进行的防锈处理的防锈油等物质,会在运输过程中逐渐凝结,导致燃油喷射器的部分堵塞;而在冷试这种快节奏的测试情况下,燃油轨检测时间只有短短的几秒钟,短时间的压缩空气喷射无法将喷油器的凝结防锈油等物质完全清理,而在第二次测试的时候,由于有了第一次测试时的预测试,喷油器基本恢复正常,因此第二次之后的测试结果,基本接近于一条稳定的曲线。
如此,我们进行了各种试验,尝试提高测试气压、延长测试时间等方法,最终确定了一个方案,在测试模块中增加了一个对燃油轨的预测试功能,即在正式检测该测试项目之前,先对燃油轨进行一次充压、开启喷油器的过程,也就完成了对燃油喷嘴的一次清理,这样,后续的检测结果的重复性与离散性大大缩小,提高了检测精度。
图4右图所示即为调整测试程序后,同一台发动机多次测试的曲线叠加情况,从曲线中我们可以看到,其测试结果的一致性有了极大的改善。
5. 电器性能测试
通过对发动机上相关的执行器分时段进行通断电,然后利用相应的反馈信号进行判断,我们可以检测发动机相关电器信号的装配情况。诸如节气门、温度传感器、进气压力传感器、二次空气喷射泵和可变正时调节器等,这些执行原件在相应的运转条件下进行通断电时,其表现出来的电压或电流值是不一样的,这样在设备中通过对其进行检测,便可以检测出相应的缺陷。
总结
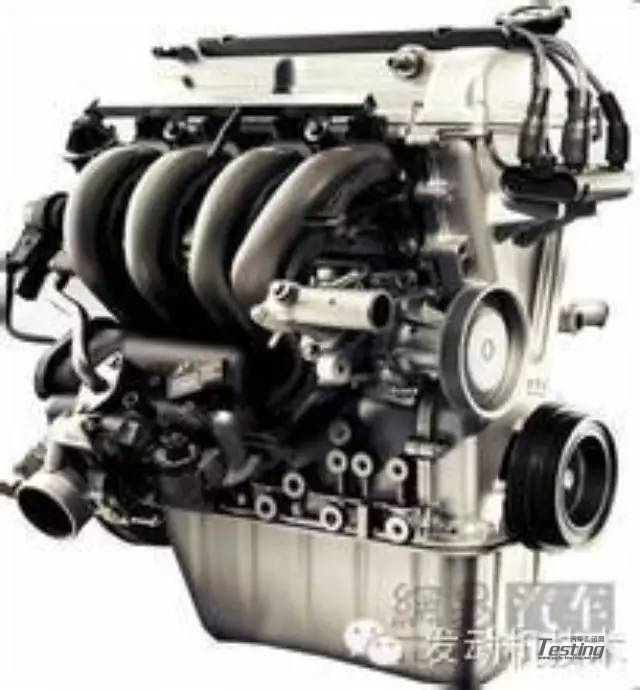
发动机冷试是现代发动机生产中一种较先进的测试方式,它的成功应用可以使用户在组装现场发现缺陷产品,提供生产线实时产品质量控制数据并对装配工艺提供改善依据,有效地降低了发动机生产中产品的缺陷率和生产成本。另外,与传统的热试验相比,它有其独特的优势,能够在快节拍的生产节奏下达到更精确控制发动机产品质量的目的,目前正在被越来越多的发动机生产厂家所采用。
- 下一篇:汽车操纵稳定性的灵魂:汽车悬架
- 上一篇:奇石乐推出DTI汽车安全测试系统
最新资讯
-
全国汽车标准化技术委员会汽车节能分技术委
2025-04-18 17:34
-
我国联合牵头由DC/DC变换器供电的低压电气
2025-04-18 17:33
-
中国汽研牵头的首个ITU-T国际标准正式立项
2025-04-18 17:32
-
为什么要进行汽车以太网接收测试?汽车以太
2025-04-18 17:26
-
产品手册下载 | NI 全新USB数据采集-NI mio
2025-04-18 16:39