纯电动汽车正面碰撞概念设计
纯电动汽车为保证续航里程,搭载了大容量锂离子电池,电池重达数百公斤,因此整车质量较传统燃油车有较大增加,比同级别传统车增重20%以上。这也就意味着正面碰撞(包括正面100%重叠刚性壁障碰撞和正面40%重叠可变形壁障碰撞)时的整车动能增加20%以上。
动力电池受到强烈撞击后易发生渗漏,甚至起火、爆燃,所以碰撞时需要保证对电池充分防护。但因电池体积较大,导致保护难度增加。
对于电动汽车而言,偏置碰是得分难点。所以设计正碰结构耐撞性时,偏置碰工况最值得关注。电动汽车在偏置碰工况下将发生较大的车身变形,可能导致较大的驾驶员伤害值。车体耐撞性开发的重点应该是在布置和结构方面进行优化,以控制偏置碰时的前壁板侵入和乘员舱变形。
电动汽车前舱吸能空间
电动汽车动力总成为驱动电机和减速器,其体积小于传统燃油车动力总成。但是高压配电盒、逆变器、DC-DC和充电器等部件也都布置在前舱内,几乎占满了前舱。为保护内部电子元器件和实现电磁屏蔽,这些部件通常都有刚硬的金属外壳,在碰撞中相当于刚性体,占据了碰撞吸能空间。所以在通常情况下,电动汽车的前舱碰撞吸能空间不会好于传统燃油车。
为在地板下面布置更大的动力电池,现在电动汽车的发展趋势是在整车长度一定时,尽量增加轴距和缩短前后悬。前悬缩短将导致前舱碰撞吸能空间进一步恶化。
要改善前舱吸能空间,需要实现前舱内零部件的高度集成。例如特斯拉Model S 将电机和逆变器集成在一起,如图1所示,这种集成方式节省了大量前舱内空间,所以Model S在保证碰撞吸能空间的同时,前舱内还能再布置一个行李箱。
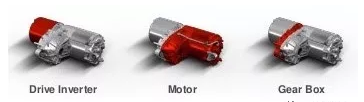
图1 特斯拉Model S集成逆变器的动力总成
动力总成悬置系统对于前舱变形吸能空间也有明显影响,应尽量避免将悬置支架布置在动力总成的前方和后方,悬置支架结构尺寸也要尽量小。图2展示了特斯拉model S的悬置布置方案,采用左前+右前+左后布置方式,而且悬置支架结构本身也比较紧凑,减少了对吸能空间的侵占。
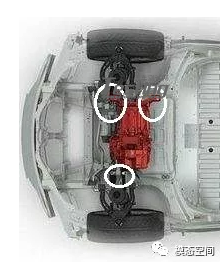
图2 特斯拉model S的动力总成悬置
电动车正面碰撞传力路径
对于传统燃油车,正面碰撞时的传力路径是前端吸能盒—前纵梁—地板纵梁/中通道/门槛梁。如图3所示。来自前纵梁的碰撞力一部分传递到地板纵梁,另外一部分向左右两侧分散到门槛梁和中通道。
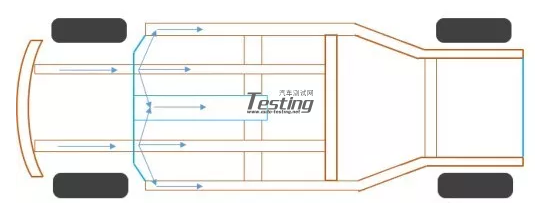
图3 传统车正碰传力路径
对于电动车,因为要在地板底下布置动力电池,需要为电池让出布置空间,所以我们期望传力路径是前端吸能盒—前纵梁—门槛梁,如图4所示。但这种传力路径真正实现起来难度很大,主要原因是前纵梁和门槛梁在Z向和Y向都有很大的间距。
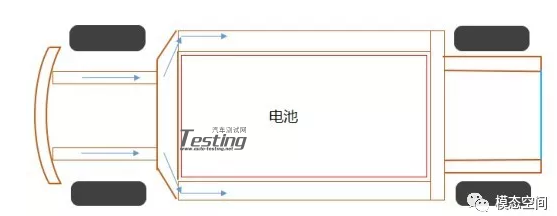
图4 我们期望的电动车正碰传力路径
如果电动车沿用传统车的车身前部架构,则前纵梁下表面和门槛梁下表面之间的Z向距离>200mm,纵梁外侧面和门槛梁外侧面的Y向距离>350mm,如图5所示。这就产生了两个后果,第一个是前纵梁跟门槛梁之间没有任何的重叠量,前纵梁与门槛量连接刚度很低,正碰时无法有效阻挡前纵梁后退;第二个是过大的间距产生了长的力臂,正碰时的纵梁截面力使前纵梁根部承受过大的弯矩。所以正碰时前纵梁尚未来得及充分溃缩吸能,其根部就会发生弯折并向后顶入乘员舱内,产生非常大的前壁板侵入量。

图5 前纵梁和门槛量的Z向和Y向间距
电动车正碰结构概念设计
基于以上分析,电动车正碰结构设计,至少应该在一个方向上解决前纵梁和门槛梁间距过大问题。这样就出现了两种概念方案,分别着眼于Y向间距和Z向间距。
第一种方案以减少Y向间距为目的,如图6所示,沿用传统汽油车传力路径,保留地板纵梁,这种方案我们称之为地板纵梁方案。为布置电池包,地板纵梁向外侧移动,前纵梁根部向外弯以连接到地板纵梁。为保证碰撞力合理传递,前纵梁跟地板纵梁的Y向间距须控制在180mm以内,纵梁弯折角尽量控制在21度以内。
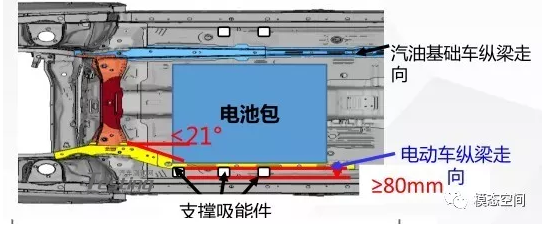
图6 地板纵梁方案
地板纵梁方案的优点是在传统燃油车的基础上实现比较容易,大部分车身结构可以借用,只需做少量的更改和加强。所以国内油改电车型基本上都采用这种方案,国外像雪佛兰Bolt和日产Leaf等传统车企开发的电动车型也都采用此方案。
地板纵梁方案最大的缺点是地板纵梁的存在导致动力电池宽度受限,电池宽度只能达到车身宽度的60%左右,必然影响整车续驶里程。
第二种方案以减少Z向间距为目标,前纵梁尽量向下加大截面高度,这种方案我们称为前纵梁加深方案。前纵梁横截面Z向尺寸相比传统车增加50-80mm,前纵梁下表面与门槛梁下表面的Z向间距减少到170mm以内。
截面高度向下加大后,前纵梁的吸能能力将有明显提升;前纵梁截面力合力点也同时下移,从而缩短了前纵梁根部力矩的力臂;而且前纵梁和门槛梁在Z向将产生一定重叠量。
因为前纵梁和门槛梁只是在Z向有重叠,在Y向仍旧没有重叠,所以前壁板和地板搭接处需要布置一个刚硬的横梁,使前纵梁和门槛梁之间实现足够大的连接刚度,正碰时的碰撞力就能够从前纵梁有效的传递到两侧门槛梁。为承担碰撞力,门槛梁必须设计的非常粗壮。
前纵梁加深方案最大的好处是无需地板纵梁,电池可以充分利用左右门槛梁之间的空间,所以电池的宽度可以达到车身宽度的75%以上,这对于提升整车续驶里程极为有利。
一些新兴电动车企业的产品,例如特斯拉model X和蔚来ES8,都是采用前纵梁加深方案,如图7所示。这种方案导致的一个问题是加深后的前纵梁与驱动半轴干涉,需要在前纵梁上开孔或者开豁口来避让半轴的运动包络。纵梁开孔后容易发生局部应力集中,必须在开孔周围补强处理。
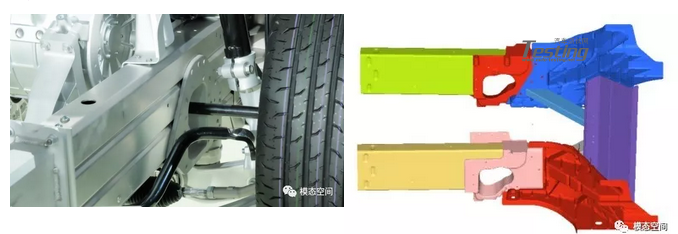
图7 蔚来ES8和特斯拉model X的前纵梁
几点注意事项
对于传统燃油车,我们通常将前纵梁截面的高宽比控制在1.6以内,高宽比太大则Y向容易失稳,导致前纵梁在正碰时弯折变形而不是顺序均匀溃缩,从而降低吸能能力。但这个高宽比限值仅适用于钢板冲压成型的纵梁,并不适用于铝材挤压成型的纵梁。
挤压铝前纵梁的壁厚可以根据需要自由设计,而且截面内部可以设计多条加强筋,即使采用很大的高宽比,也有办法保证Y向的稳定性。例如特斯拉Model X的前纵梁截面,如图8所示,其高宽比已经超过3.0,但它通过合理设计内部加强筋,保证了正碰时的稳定性,无论是100%正碰还是40%偏置碰,都能实现良好的溃缩。
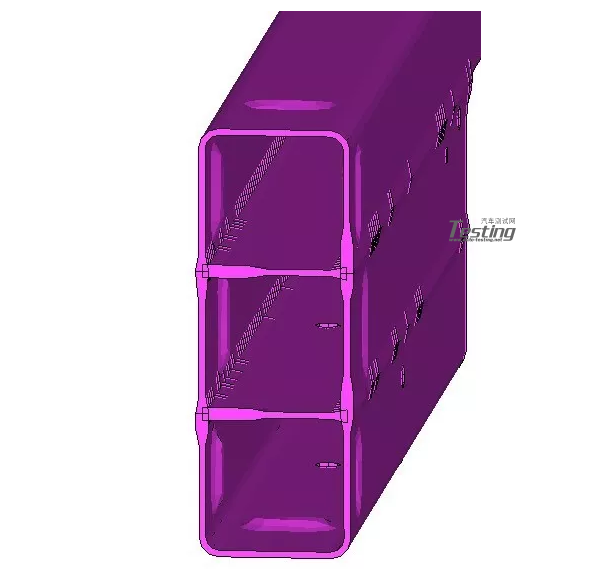
图8 特斯拉model X的前纵梁横截面
无论是地板纵梁方案还是前纵梁加深方案,前纵梁根部都是设计成向外弯曲,区别只是前者连接到地板纵梁,后者连接到门槛梁。所以前纵梁根部是薄弱环节,需要做多重补强。为保证正碰时的前纵梁能够稳定溃缩变形,纵梁根部内侧应增加斜向支撑,如图9所示。斜向支撑件的根部必须稳固支撑到前壁板底部的横梁上。
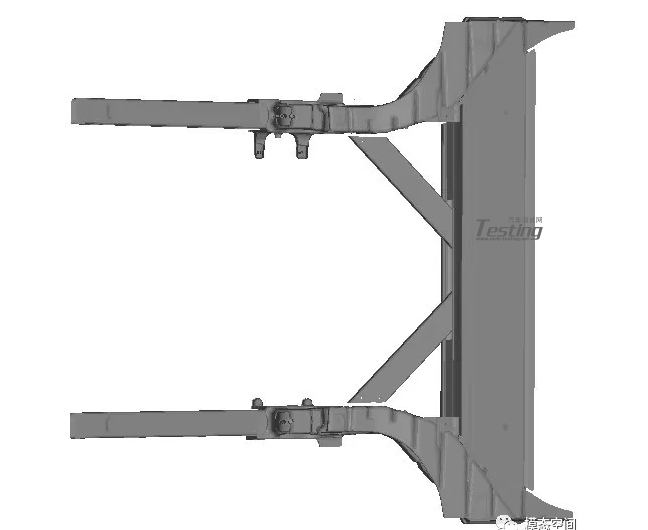
图9 纵梁根部的斜向支撑件
除上述传力路径外,副车架-前纵梁根部-门槛梁为第二条正碰传力路径。如果副车架向前延伸出300mm左右的可溃缩小纵梁,如图10,发生正面碰撞后,延伸梁能够分担一部分截面力,跟前纵梁一起溃缩,使碰撞初期的整车加速度有所提升,因此同样的变形距离下能够吸收更多的能量。
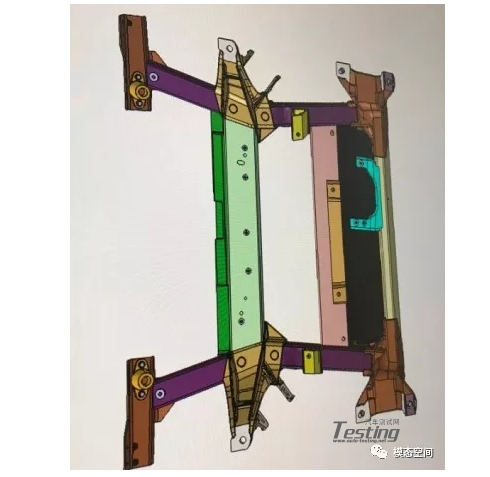
图10 副车架前延伸梁
需要注意的是,第二传力路径吸收的能量有限,通常不超过总动能的10%,所以只能作为第一传力路径的辅助。
如果副车架跟车身是采用软连接,则在正碰时,副车架跟车身之间可能发生较大的相对运动,导致副车架延伸梁无法稳定溃缩。所以采用延伸梁吸能方案时,副车架跟车身之间只能采用硬连接,这对整车NVH性能将有一定影响。
副车架与车身之间的连接螺栓要有足够高的强度,保证在延伸梁完全溃缩之前连接螺栓不发生破坏。
另外,前纵梁前端吸能盒和副车架延伸梁的变形次序必须严格控制,副车架延伸梁的变形应滞后于吸能盒。这样在低速碰撞时仅有吸能盒变形,副车架延伸梁不发生变形,从而保证了低速碰时车辆的可维修性。
小结
通常情况下,电动汽车的前舱吸能空间并不优于传统燃油车。为改善前舱吸能空间,电动汽车前舱内的零部件应进行集成,动力总成悬置应紧凑布置。
纯电动车正碰车体结构概念设计,可选择地板纵梁方案或者前纵梁加深方案,后者能够给动力电池提供更大的空间,所以应该是未来的趋势。
无论是地板纵梁方案还是前纵梁加深方案,前纵梁根部都是最值得关注的部位,应进行多重强化设计,并增加斜向支撑和前壁板底部横梁。
如果在第二传力路径前端增加延伸梁,在正碰时能够溃缩吸能,从而改善整体耐撞性,但第二传力路径吸收的动能极为有限,只能作为第一传力路径的辅助。
特别致谢
本文所用的大部分图片来自卢元甲的大作《纯电动汽车平台与架构》。
作者简介
王朋波,清华大学力学博士,汽车结构CAE分析专家。重庆市科协成员、《计算机辅助工程》期刊审稿人、交通运输部项目评审专家。专业领域为整车疲劳耐久/NVH/碰撞安全性能开发与仿真计算,车体结构优化与轻量化,CAE分析流程自动化等。
本文转自 模态空间公众号,欢迎大家搜索关注
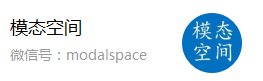
最新资讯
-
中汽中心工程院能量流测试设备上线全新专家
2025-04-03 08:46
-
上新|AutoHawk Extreme 横空出世-新一代实
2025-04-03 08:42
-
「智能座椅」东风日产N7为何敢称“百万级大
2025-04-03 08:31
-
基于加速度计补偿的俯仰角和路面坡度角估计
2025-04-03 08:30
-
《北京市自动驾驶汽车条例》正式实施 L3级
2025-04-02 20:23