简单分析前副车架焊缝疲劳分析及优化
导语
汽车在日常使用中主要载荷来自于动力总成及地面,前副车架直接承担来自动力总成和底盘杆系的载荷,是极易发生疲劳破坏的汽车结构之一。因此,对前副车架进行疲劳性能评估是汽车设计过程中必不可少的过程。现阶段,普遍采用整车耐久试验的方法评估,该方法必须生产多台样车,且每一轮验证耗时长达2-3个月,非常不经济。CAE技术的发展使虚拟样机验证变为可能,疲劳分析技术能大大缩短产品开发周期,节省时间和经济成本。
本文利用CAE方法对某汽车前副车架的疲劳寿命进行了预测,疲劳风险点与耐久试验吻合良好,并优化了该副车架局部结构,后续的耐久试验中未出现开裂现象。
1疲劳分析理论
自19世纪中叶以来,逐渐发展起来的主要疲劳理论有三种:应力寿命相关的S-N理论、应变寿命相关的8-N理论、裂纹扩展理论。相对来说,材料S-N曲线的获得是最容易的,因此,现在工程中应用最广泛、与工程实践结合最好的还是S-N理论瞳。
S-N理论认为:根据材料的S-N曲线,不同的应力对结构产生不同的损伤,在交变载荷作用下,结构的应力也不断变化,损伤不断累计,当结构的总损伤大于1则结构破裂。为了简化计算,工程中通常假定损伤是线性累计(Miner准则)的,与加载顺序无关。
一般地,利用S-N理论做疲劳分析按如下步骤进行:(1)计算结构在单位载荷下的应力;(2)将单位载荷下的应力与各通道的时间历程相乘,并叠加,获得结构的应力历程;(3)对应力历程进行雨流统计,获取应力幅值Ai和载荷循环Ci;(4)与S-N曲线匹配,计算不同幅值的损伤Di;(5)将损伤进行线性累积,计算总损伤D总和寿命1/D总。分析流程如图1所示。
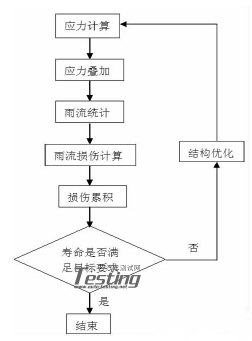
图1 S-N法分析流程图
2前副车架疲劳寿命预测
2.1
有限元模型及网格精度要求
前副车架用螺栓连接在车身上,分析时需考虑安装点的安装刚度,如直接约束副车架与车身的连接点,则车架在受侧向或纵向的拉伸或挤压时会处于过约束状态,会导致与实际不符的分析结果。考虑安装点的安装刚度有两种方法:一种是在安装点建立衬套单元,赋予衬套属性,模拟安装刚度;另一种是搭建部分车身模型,将副车架用梁单元与车身连接,这种方法最接近实际情况。同理,转向机不能用刚性单元模拟,因为刚性单元会加强副车架后横梁的刚度,导致后横梁应力与实际不符。
强度分析采用Nastran求解,分析模型由转向机、前副车架和前部车身组成。壳单元采用CTRIA3及CQUAD4单元模拟;实体单元采用CHEXA及CTETRA单元模拟;螺栓用Cbar单元模拟,模型总计446151个节点,586438个单元,如图2所示。
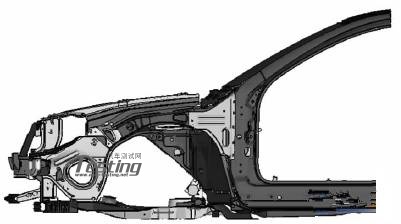
图2 有限元模型
良好的网格模型是有限元分析的基础,不同的分析对网格的要求不同,比如刚度分析不要求网格非常精细,但强度分析需要在关注的地方细化网格,孔周围最好用warsher画法。疲劳分析需要获得结构的应力,因此对网格精度有要求。本文的车身网格模型按一般精度控制,基础尺寸按10mm划分,焊缝处的网格需特殊处理。
以T型焊(T-Joint)和平行焊(Lap-Joint)为例,具体要求有:
(1)紧邻焊缝节点两侧的单元称为焊缝单元,其宽度尺寸严格控制在钣金厚度的2~5倍,如图2所示,a取值为2~5。
(2)焊缝起始节点和终止节点长度尺寸控制在钣金厚度的2~3倍,如图3所示,b取值为2~3。
(3)起始节点和终止节点周围尽量都是焊缝单元。
(4)焊缝单元尽量不要用三角形单元。
(5)平行焊的焊缝连接单元只能定义一层,厚度定义为2个母材的最大厚度。设母材厚度分别为Ti、T2,则焊缝连接单元厚度T=Max{T1,T2},如图4所示。
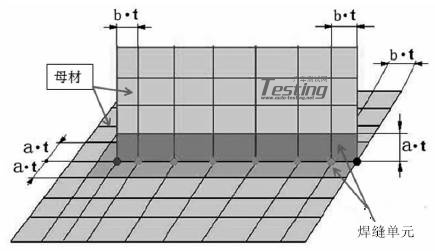
图3 焊缝定义示意图
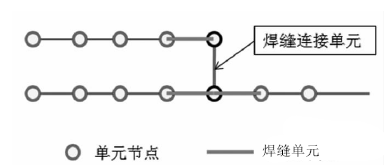
图4 平行焊(Lap-Joint)定义示意图
2.2
强度工况设定
约束车身截断面自由度123,约束前悬架塔座自由度3,保证约束点远离加载点。分别在下摆臂前安装点、下摆臂后安装点、发动机悬置点、稳定杆安装点和转向拉杆连接点施加x、y、z三向单位力和单位扭矩,共计66个工况。分别计算副车架在各工况单位载荷下的应力,各加载点位置如图5所示,除发动机悬置点外,其它点左右对称。
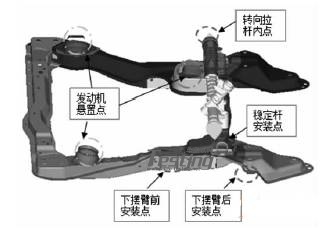
图5 前副车架加载点示意图
2.3
疲劳分析
疲劳分析软件FEMFAT中有丰富的焊缝数据库,在不同的焊缝缺口因子修正下,使焊缝的疲劳分析具有较高的精度。本文中用到的焊缝有平行焊缝(FilletWeld)、V型焊(V-Seam)等,根据副车架的实际焊接情况选择正确的焊缝类型,定义好焊缝节点、起始节点、终止节点及焊缝单元,焊缝的概念模型和实际模型如图6所示,左侧为焊缝的概念模型,右侧为实际模型。
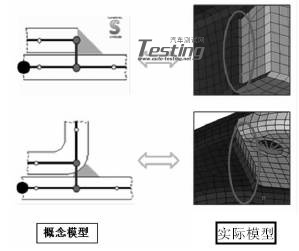
图6 焊缝示意图
底盘件的载荷谱无法直接采集,需依赖多体动力学,采集的车轮六分力通过多体动力学模型分解到各底盘结构件。多体动力学模型中的衬套特性、弹簧特性等直接影响到底盘构件的载荷,建立多体动力学模型时各弹性元件需要经过标定,尽量与实车一致。获得前副车架的载荷后,与2.2中的66个工况一一对应,关联起来,计算前副车架的应力历程,图7所示为下摆臂前安装点的六向载荷,车辆在高强耐久路面上行驶时该点主要承受Y向和Z向载荷。
2.4
结果及优化
计算完成后,输出结果文件,在后处理软件中打开,查看前副车架的寿命分布情况,如图9所示,在副车架后横梁上Pl、P2处焊缝寿命较低,寿命分别为1497Km、5298Km,分析其原因如下:前副车架后横梁为了避让排气管,中部向上凸起,容易上在下摆臂的侧向挤压力或者拉伸力作用下,后横梁中部容易向上或者向下变形,Pl、P2局部焊缝容易应力集中,导致寿命较低。
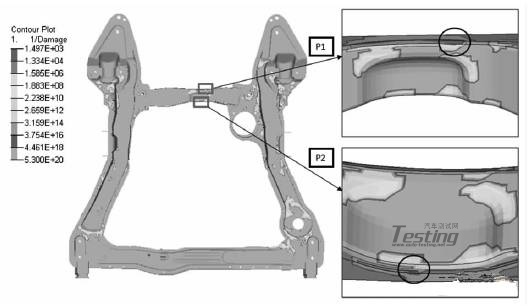
图9 仿真寿命云图(单位:Km)
整车高强耐久试验过程中,1号试验车Pl、P2分别在2542、13085公里出现了裂纹,2号试验车Pl、P2分别在3831、9624公里出现了裂纹。疲劳分析结果及高强耐久试验车的里程如表2所示,试验裂纹如图10所示。由表2及图9、10所知:前;Pl较早出现裂纹,P2次之;同时由于材料、工艺的不一致性,各车架的破裂里程有些不同,但在可接受范围内;总体而言,副车架的破裂位置、趋势及寿命里程都与试验结果吻合较好,可利用本次分析所用的参数及网格处理方式对副车架局部结构进行优化。
根据以上分析结果,在后横梁内部增加一块厚度1.5mm的加强板,该加强板与后横梁底板用焊点连接,同时改进对局部焊缝进行调整,使Pl、P2不再是焊缝的起始点或者终止点,优化方案如图12所示。
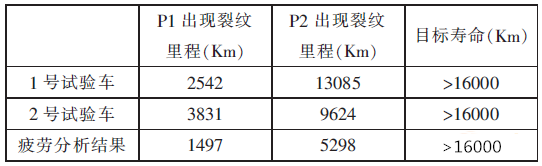
表2 试验与仿真结果对照表
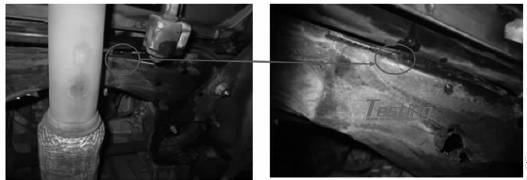
图10 P1试验裂纹图
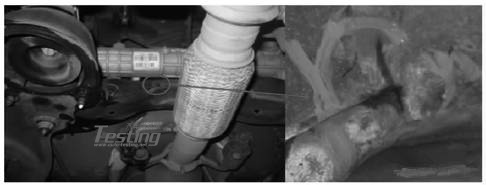
图11 P2试验裂纹图
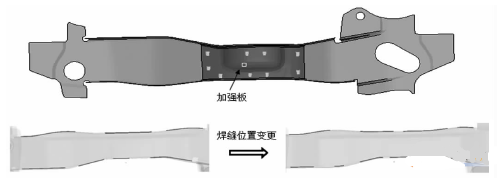
图12 局部结构优化示意图
经优化,Pl、P2局部寿命显著提高,Pl、P2点寿命分别为16629Km、55421Km,满足16000Km的耐久要求,寿命云图如图13所示,设计验证阶段的耐久试验过程中,前副车架后横梁焊缝也未发现开裂。
3结论
基于FEMFAT软件分析了某车型前副车架的疲劳寿命,与试验吻合良好,并对车架进行了优化设计,使车架疲劳寿命满足耐久目标要求,本文方法可应用于后续车型的车架设计及焊缝疲劳寿命预测。
疲劳问题一直是设计开发中的难点问题,影响疲劳寿命的因素较多,且不易控制,甚至经常出现同一部件在同样的工况下寿命存在较大差异的情况,使得疲劳耐久的工程开发有很大困难,但虚拟样机验证取代物理试验验证是耐久开发的是一种趋势。通过精确的焊缝模型、材料对标、参数标定、准确的载荷谱计算及制造工艺控制,能够保证仿真分析结论与试验结论有较高的吻合度。
最新资讯
-
标准解读丨ISO 21111 《道路车辆车载以太网
2025-03-31 19:15
-
清研精准兆瓦级充放电测试设备——重新定义
2025-03-31 19:13
-
强强联合:imc FAMOS内嵌Python接口,提高
2025-03-31 19:12
-
汽车动力电池与发动机系列标准宣贯会在武汉
2025-03-31 16:08
-
氢内燃机2.0-西南研究院(SwRI)启动第二阶
2025-03-31 16:06